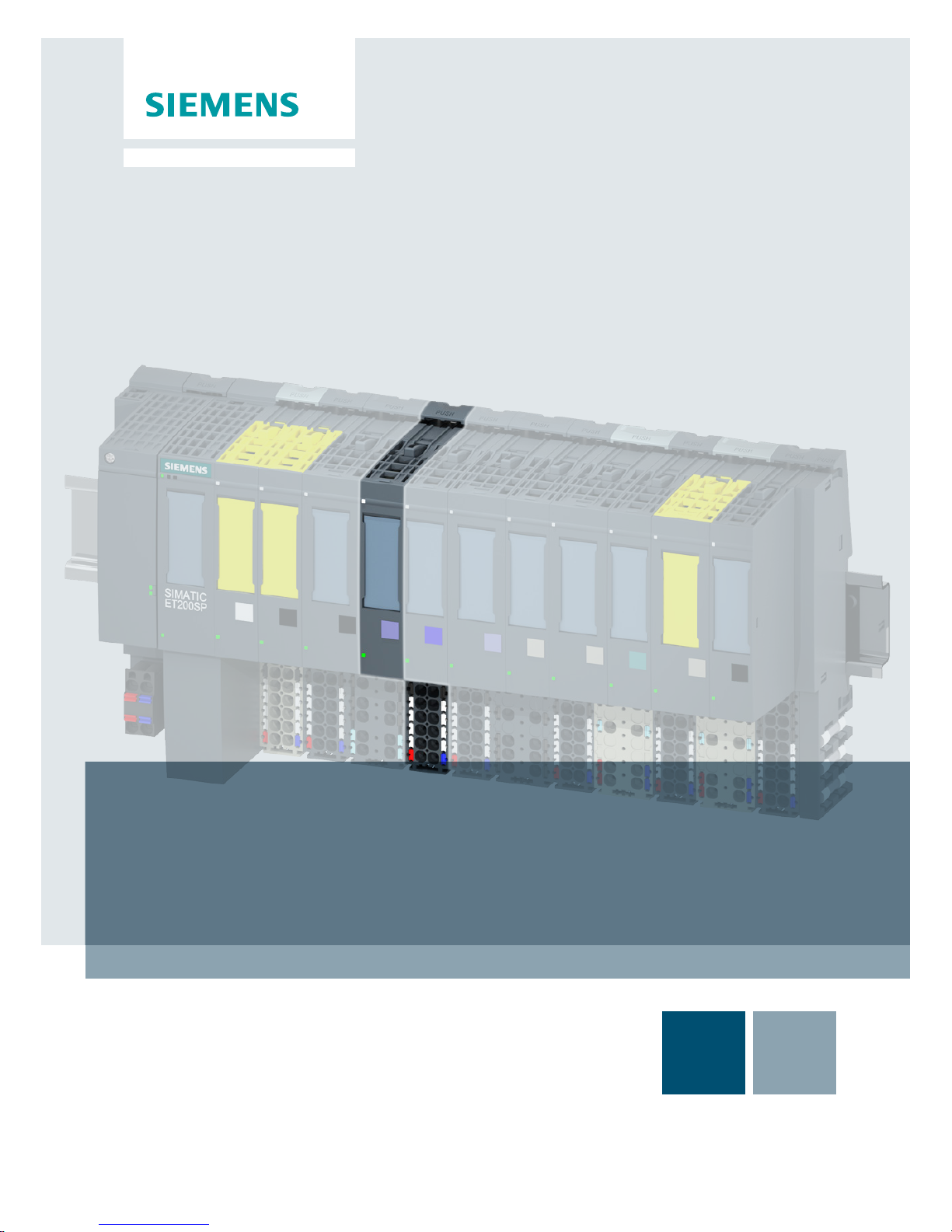
Manual
Analog input module AI 4xRTD/TC 2-/3-/4-wire HF (6ES7134-6JD00-0CA1)
ET 200SP
02/2014Edition
Answers for industry.
SIMATIC
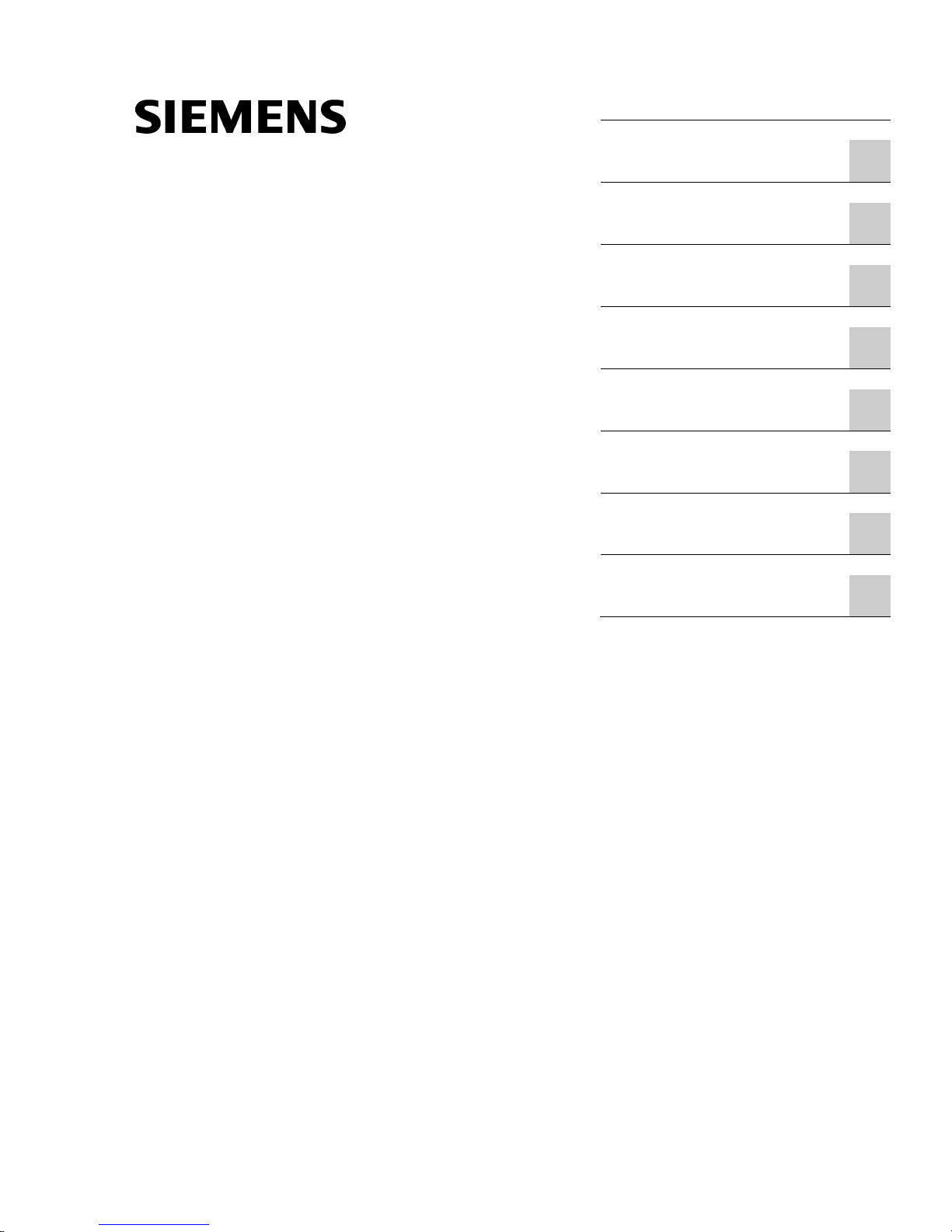
Analog input module AI 4xRTD/TC 2-/3-/4-
wire HF (6ES7134-6JD00-0CA1)
ET 200SP
Analog input module
AI 4xRTD/TC 2-/3-/4-wire HF
(6ES7134-6JD00-0CA1)
Interrupts/diagnostics alarms
Representation of analog
values

Siemens AG
Industry Sector
Postfach 48 48
90026 NÜRNBERG
GERMANY
02/2014 Subject to change
Copyright © Siemens AG 2014.
All rights reserved
Legal information
Warning notice system
This manual contains notices you have to observe in order to ensure your personal safety, as well as to prevent
damage to property. The notices referring to your personal safety are highlighted in the manual by a safety alert
symbol, notices referring only to property damage have no safety alert symbol. These notices shown below are
graded according to the degree of danger.
indicates that death or severe personal injury will result if proper precautions are not taken.
indicates that death or severe personal injury may result if proper precautions are not taken.
indicates that minor personal injury can result if proper precautions are not taken.
indicates that property damage can result if proper precautions are not taken.
If more than one degree of danger is present, the warning notice representing the highest degree of danger will
be used. A notice warning of injury to persons with a safety alert symbol may also include a warning relating to
property damage.
The product/system described in this documentation may be operated only by
for the specific
task in accordance with the relevant documentation, in particular its warning notices and safety instructions.
Qualified personnel are those who, based on their training and experience, are capable of identifying risks and
avoiding potential hazards when working with these products/systems.
Proper use of Siemens products
Siemens products may only be used for the applications described in the catalog and in the relevant technical
documentation. If products and components from other manufacturers are used, these must be recommended
or approved by Siemens. Proper transport, storage, installation, assembly, commissioning, operation and
maintenance are required to ensure that the products operate safely and without any problems. The permissible
ambient conditions must be complied with. The information in the relevant documentation must be observed.
All names identified by ® are registered trademarks of Siemens AG. The remaining trademarks in this publication
may be trademarks whose use by third parties for their own purposes could violate the rights of the owner.
We have reviewed the contents of this publication to ensure consistency with the hardware and software
described. Since variance cannot be precluded entirely, we cannot guarantee full consistency. However, the
information in this publication is reviewed regularly and any necessary corrections are included in subsequent
editions.
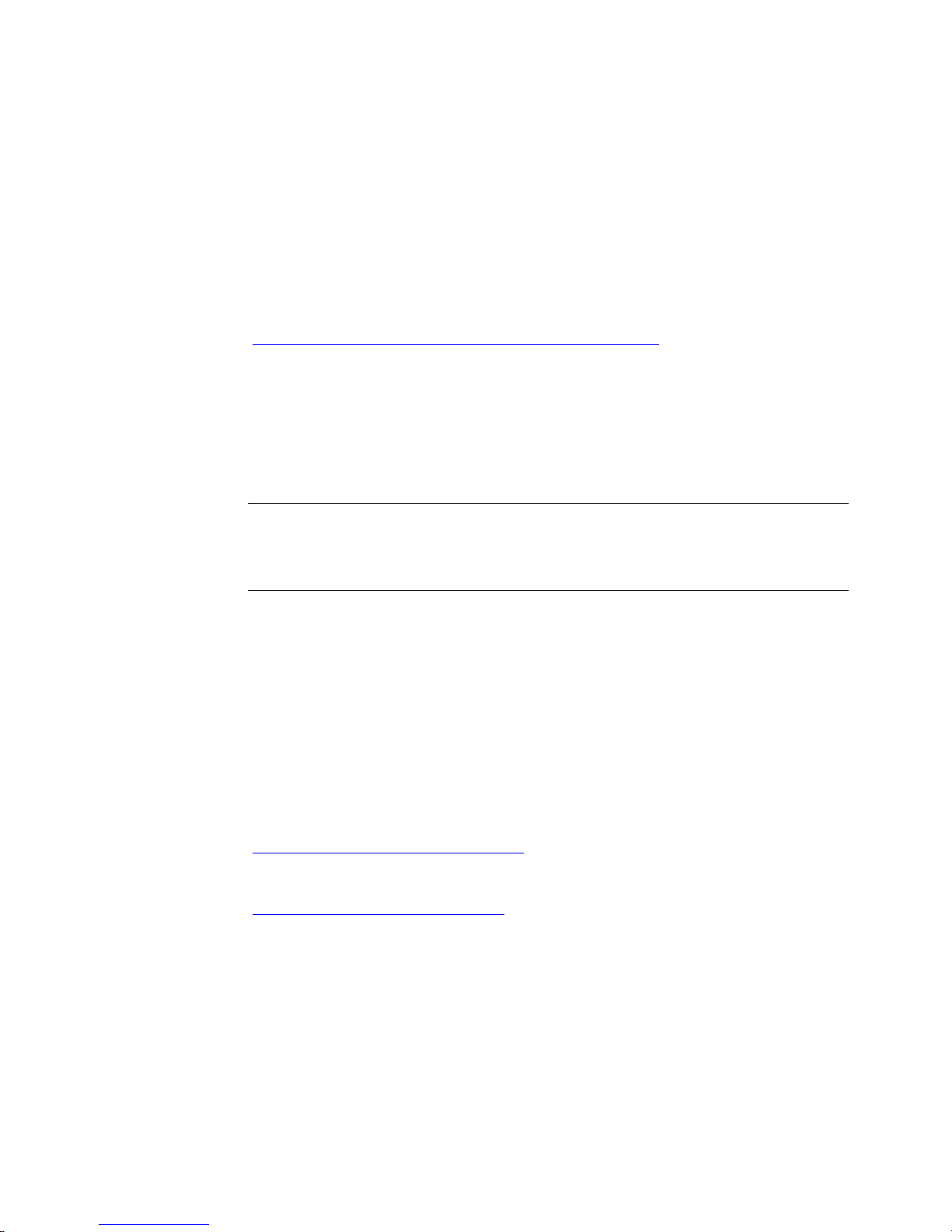
Analog input module AI 4xRTD/TC 2-/3-/4-wire HF (6ES7134-6JD00-0CA1)
Manual, 02/2014, A5E03573289-AD
3
Purpose of the documentation
This device manual complements the system manual ET 200SP distributed I/O system
(http://support.automation.siemens.com/WW/view/en/58649293). Functions that generally
relate to the system are described in this manual.
The information provided in this manual and in the system/function manuals supports you in
commissioning the system.
Please also observe notes marked as follows:
Note
A note contains important information on the product describe
d in the documentation, on the
handling of the product and on the section of the documentation to which particular attention
should be paid.
Siemens provides products and solutions with industrial security functions that support the
secure operation of plants, solutions, machines, equipment and/or networks. They are
important components in a holistic industrial security concept. With this in mind, Siemens’
products and solutions undergo continuous development. Siemens recommends strongly
that you regularly check for product updates.
For the secure operation of Siemens products and solutions, it is necessary to take suitable
preventive action (e.g. cell protection concept) and integrate each component into a holistic,
state-of-the-art industrial security concept. Third-party products that may be in use should
also be considered. You can find more information about industrial security on the Internet
(http://www.siemens.com/industrialsecurity).
To stay informed about product updates as they occur, sign up for a product-specific
newsletter. You can find more information on the Internet
(http://support.automation.siemens.com).
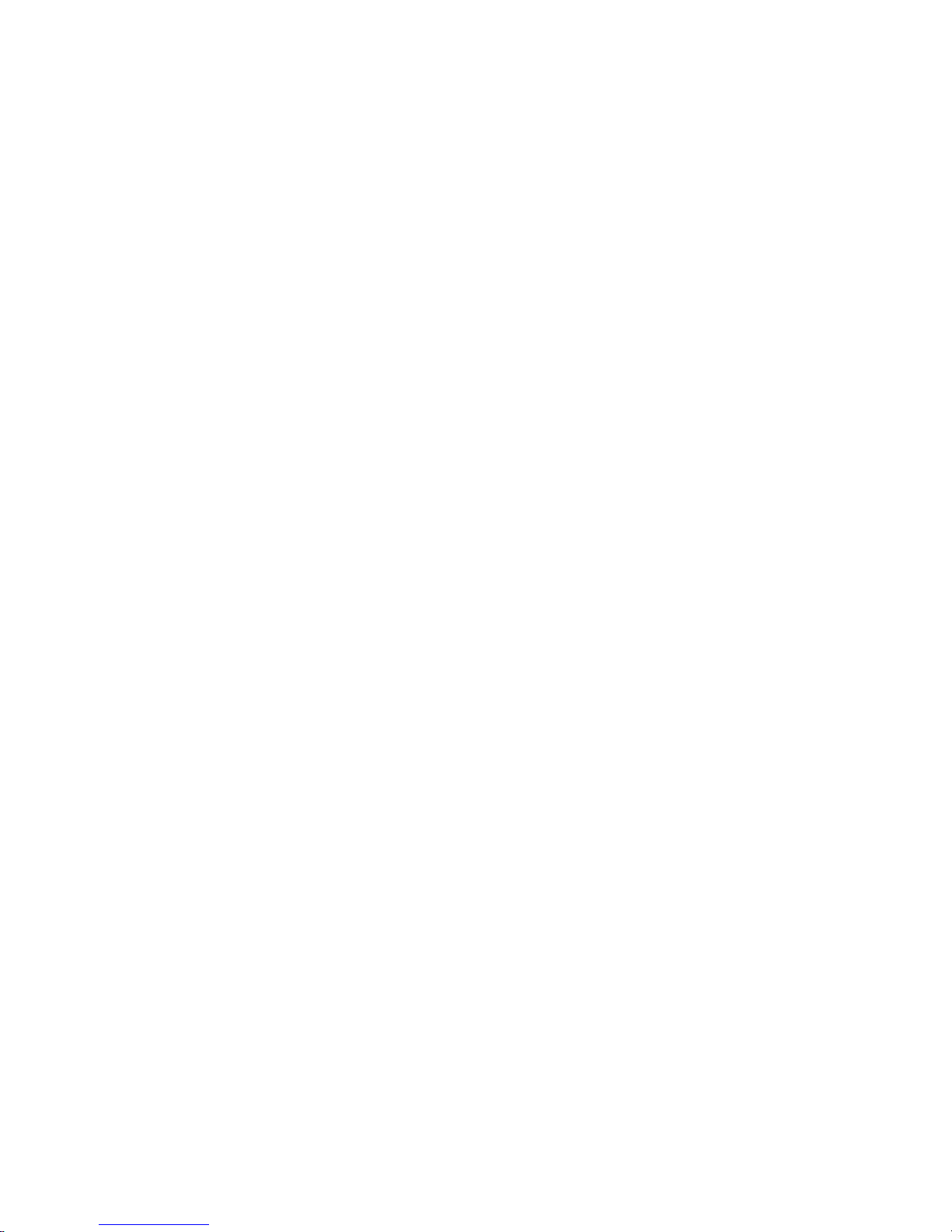
Analog input module AI 4xRTD/TC 2-/3-/4-wire HF (6ES7134-6JD00-0CA1)
4 Manual, 02/2014, A5E03573289-AD
Preface ................................................................................................................................................... 3
1 Guide to documentation .......................................................................................................................... 5
2 Product overview .................................................................................................................................... 7
2.1 Properties ...................................................................................................................................... 7
3 Wiring ................................................................................................................................................... 10
3.1 Pin assignment ............................................................................................................................ 10
3.2 Schematic circuit diagram ........................................................................................................... 12
4 Parameters/address space ................................................................................................................... 13
4.1 Measurement types and measuring ranges................................................................................ 13
4.2 Parameters .................................................................................................................................. 18
4.3 Explanation of parameters .......................................................................................................... 23
4.4 Scalable measuring range .......................................................................................................... 28
4.4.1 Configuration ............................................................................................................................... 30
4.4.2 Evaluating data record 235 ......................................................................................................... 31
4.5 Address space ............................................................................................................................ 34
5 Interrupts/diagnostics alarms................................................................................................................. 35
5.1 Status and error display .............................................................................................................. 35
5.2 Interrupts ..................................................................................................................................... 37
5.3 Diagnostics alarms ...................................................................................................................... 38
6 Technical specifications ........................................................................................................................ 40
6.1 Technical specifications .............................................................................................................. 40
A Parameter data record .......................................................................................................................... 47
A.1 Dependencies when configuring with GSD file ........................................................................... 47
A.2 Parameter assignment and structure of parameter data record ................................................. 52
A.3 Switchable wire break check ....................................................................................................... 61
B Representation of analog values ........................................................................................................... 62
B.1 Representation of input ranges ................................................................................................... 63
B.2 Representation of analog values in voltage measuring ranges .................................................. 64
B.3 Representation of analog values for resistance-type sensors .................................................... 65
B.4 Representation of analog values for thermal resistors ............................................................... 66
B.5 Representation of analog values for thermocouples .................................................................. 69
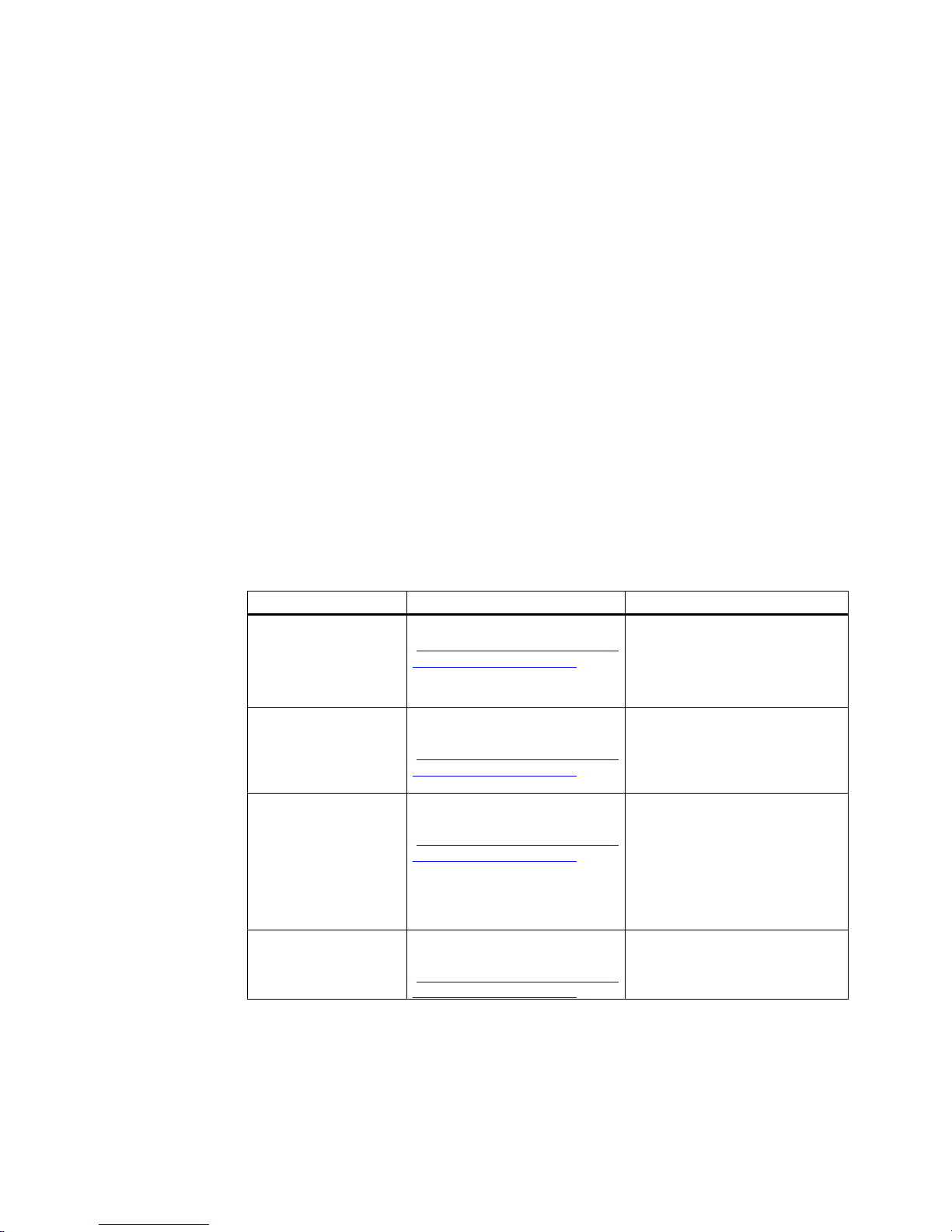
Analog input module AI 4xRTD/TC 2-/3-/4-wire HF (6ES7134-6JD00-0CA1)
Manual, 02/2014, A5E03573289-AD
5
This modular documentation of the SIMATIC products covers diverse topics concerning your
automation system.
The complete documentation for the ET 200SP distributed I/O system consists of a system
manual, function manuals and product manuals.
The STEP 7 information system (online help) also supports you during the configuration and
programming of your automation system.
Overview of documentation for analog input module AI 4×RTD/TC 2-/3-/4-wire HF
The following table shows additional documentation that you need when using the
AI 4×RTD/TC 2-/3-/4-wire HF analog input module.
Table 1- 1 Documentation for analog input module AI 4×RTD/TC 2-/3-/4-wire HF
System description ET 200SP distributed I/O system
(http://support.automation.siemens.
com/WW/view/en/58649293)
system manual
• Application planning
• Installation
• Wiring
• Commissioning
Designing interferencefree controllers
Designing interference-free
controllers
(http://support.automation.siemens.
com/WW/view/en/59193566)
• Basics
• Electromagnetic compatibility
• Lightning protection
Analog value processing Function manual
Analog value processing
(http://support.automation.siemens.
com/WW/view/en/67989094)
• Basics of analog technology
(wiring, processing, installation
technology)
• Description/explanation of
meaning, e.g., conversion and
cycle times, basic error limits,
operational limits
System diagnostics Function manual
System diagnostics
(http://support.automation.siemens.
• Overview
• Diagnostics evaluation of
hardware/software
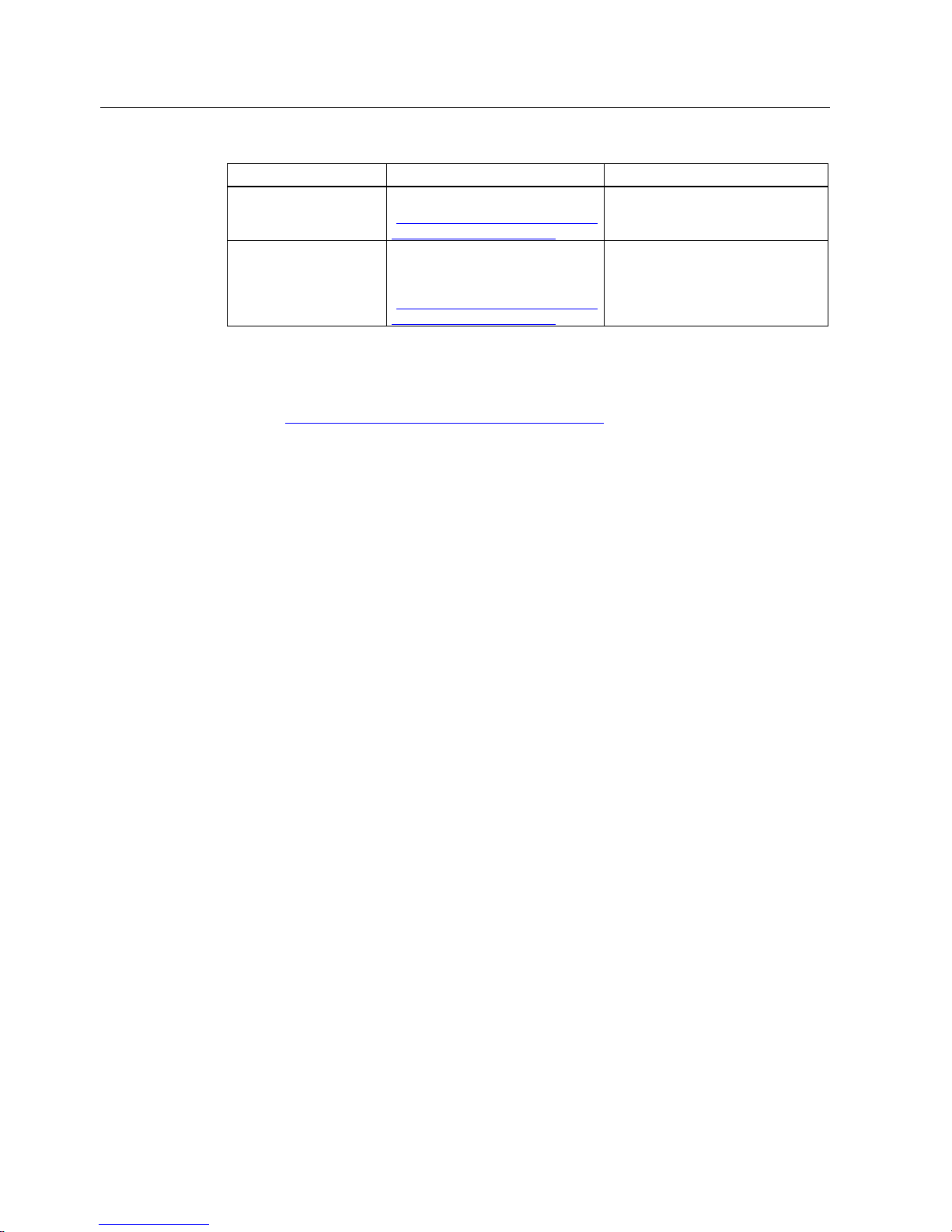
Guide to documentation
Analog input module AI 4xRTD/TC 2-/3-/4-wire HF (6ES7134-6JD00-0CA1)
6 Manual, 02/2014, A5E03573289-AD
BaseUnits Manual ET 200SP BaseUnits
(http://support.automation.siemens.
Technical specifications
Amendments and special
features of the ET 200SP
distributed I/O system
Product information on
documentation of the ET 200SP
distributed I/O system
(http://support.automation.siemens.
Current information not yet
documented in the system manuals,
function manuals, or product
manuals.
All current manuals for SIMATIC products are available to download free of charge on the
Internet (http://www.siemens.com/simatic-tech-doku-portal).
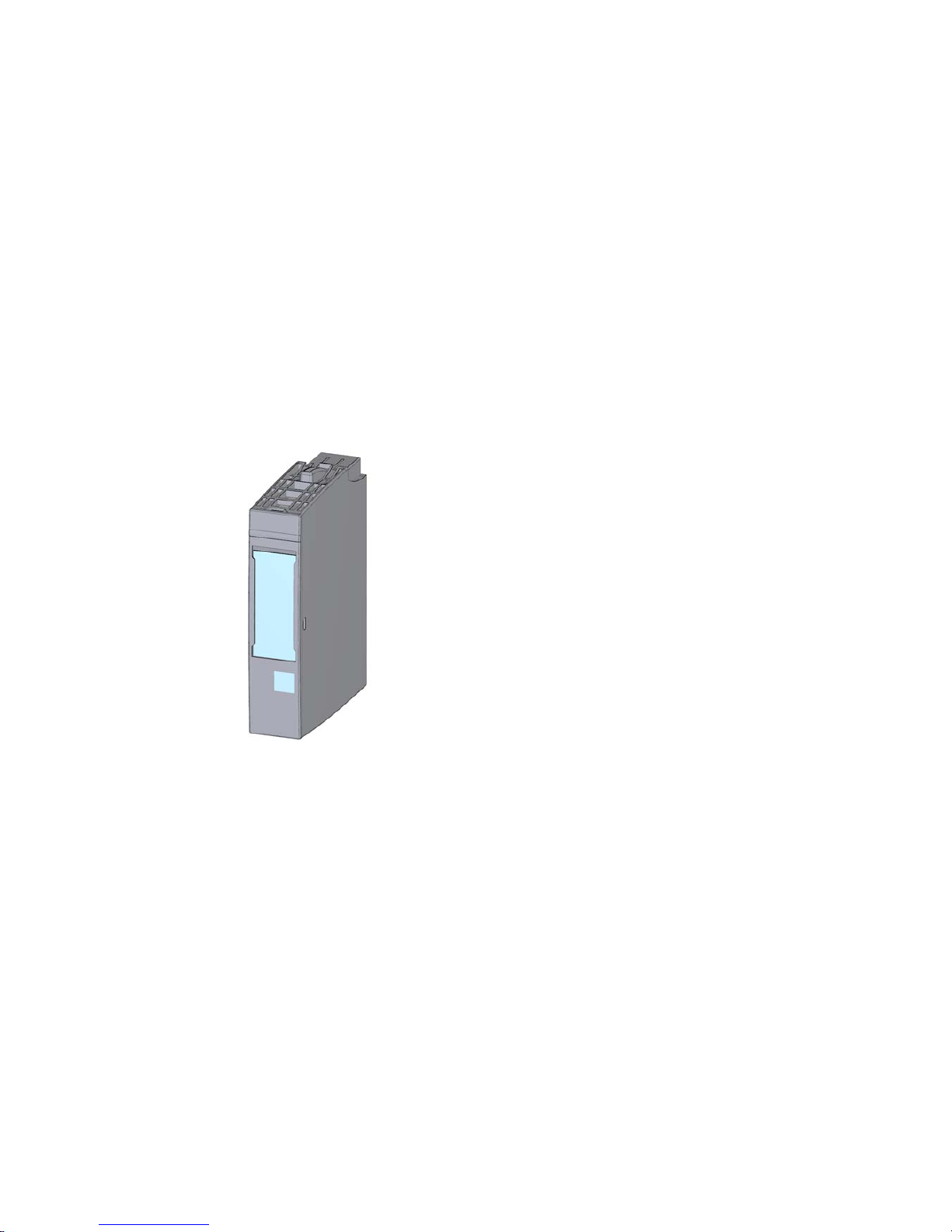
Analog input module AI 4xRTD/TC 2-/3-/4-wire HF (6ES7134-6JD00-0CA1)
Manual, 02/2014, A5E03573289-AD
7
Properties
Article number
Figure 2-1 View of the module AI 4×RTD/TC 2-/3-/4-wire HF
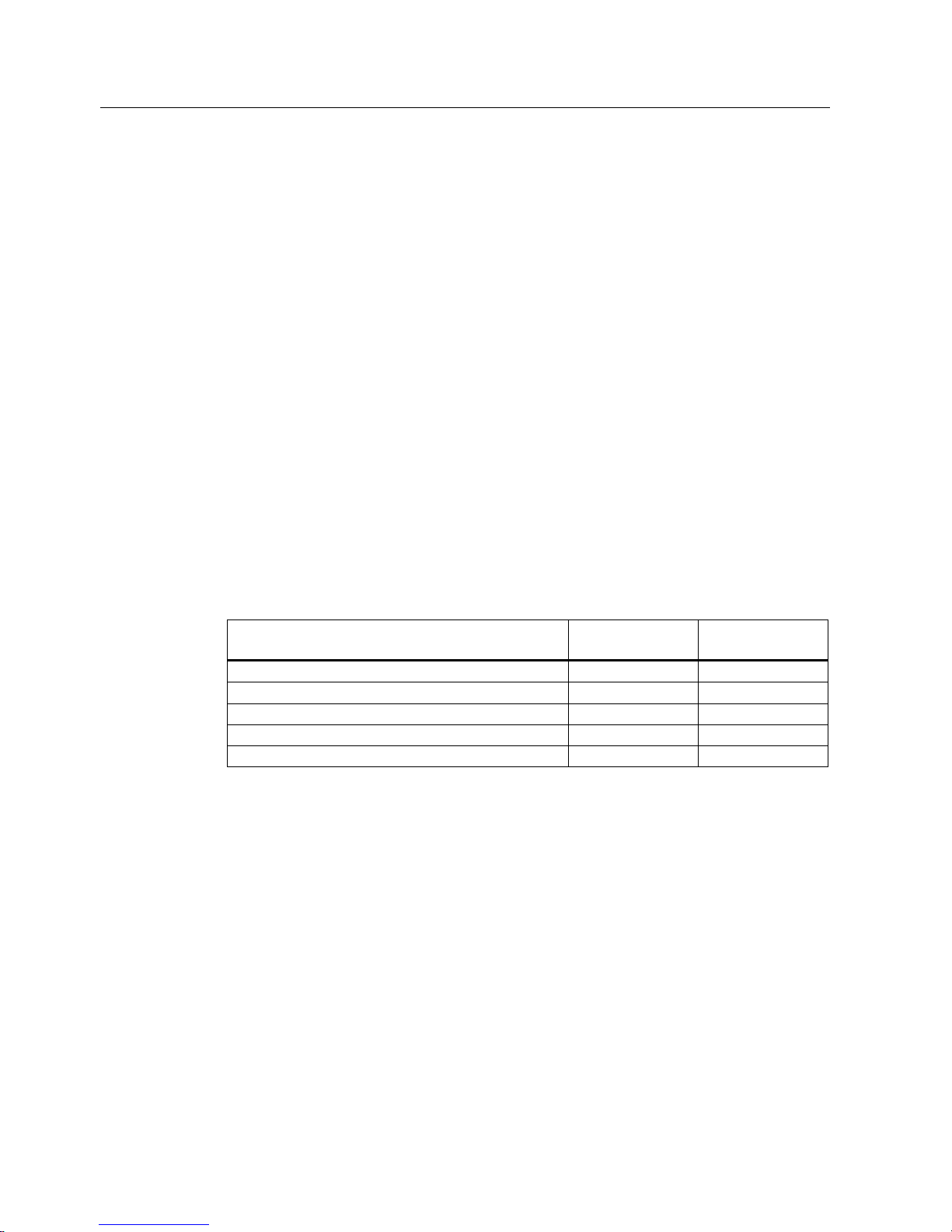
Product overview
2.1 Properties
Analog input module AI 4xRTD/TC 2-/3-/4-wire HF (6ES7134-6JD00-0CA1)
8 Manual, 02/2014, A5E03573289-AD
The module has the following technical properties:
● Analog input module with 4 inputs
● Resolution: Up to 16 bits including sign
● Voltage measurement type can be set per channel
● Resistor measurement type can be set per channel
● Thermal resistor (RTD) measurement type can be set per channel
● Thermocouple (TC) measurement type can be set per channel
● Configurable diagnostics for each channel
● Hardware interrupt on limit violation can be set per channel (two high and two low limits
per channel)
● Automatic compensation of the line resistance with 3-wire connection
The module supports the following functions:
● Firmware update
● I&M identification data
● Reconfiguration in RUN
Table 2- 1 Version dependencies of other module functions
Product version of
the module as of
Firmware version of
the module as of
Value status (PROFINET IO only)
Selectable conductor resistance for 2-wire connection
Switchable wire break check
You can configure the module with STEP 7 (TIA Portal) and with a GSD file.
The following accessories must be ordered separately:
● Labeling strips
● Color identification labels
● Reference identification label
● Shield connection
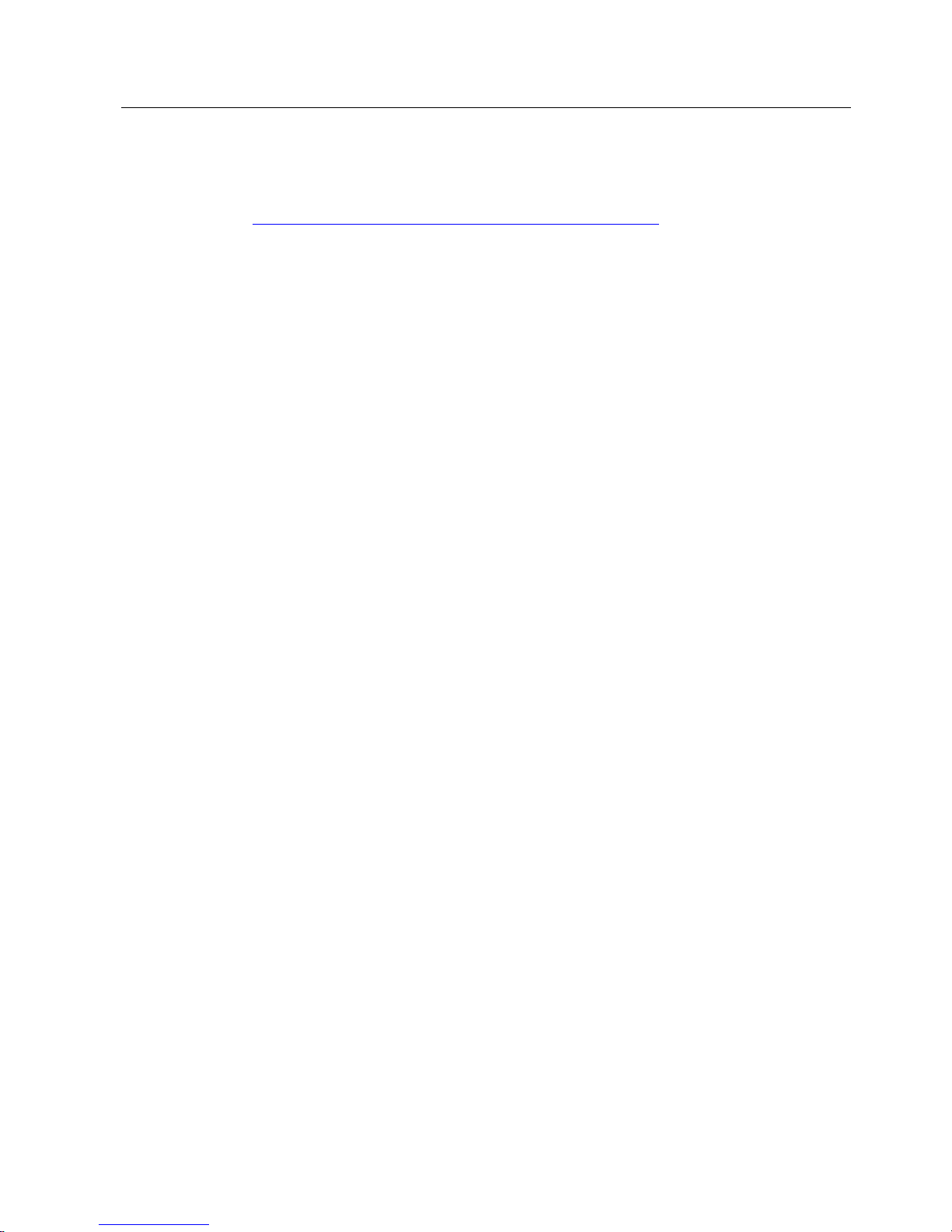
Product overview
2.1 Properties
Analog input module AI 4xRTD/TC 2-/3-/4-wire HF (6ES7134-6JD00-0CA1)
Manual, 02/2014, A5E03573289-AD
9
You can find more information on accessories in the ET 200SP distributed I/O system
(http://support.automation.siemens.com/WW/view/en/58649293) system manual.
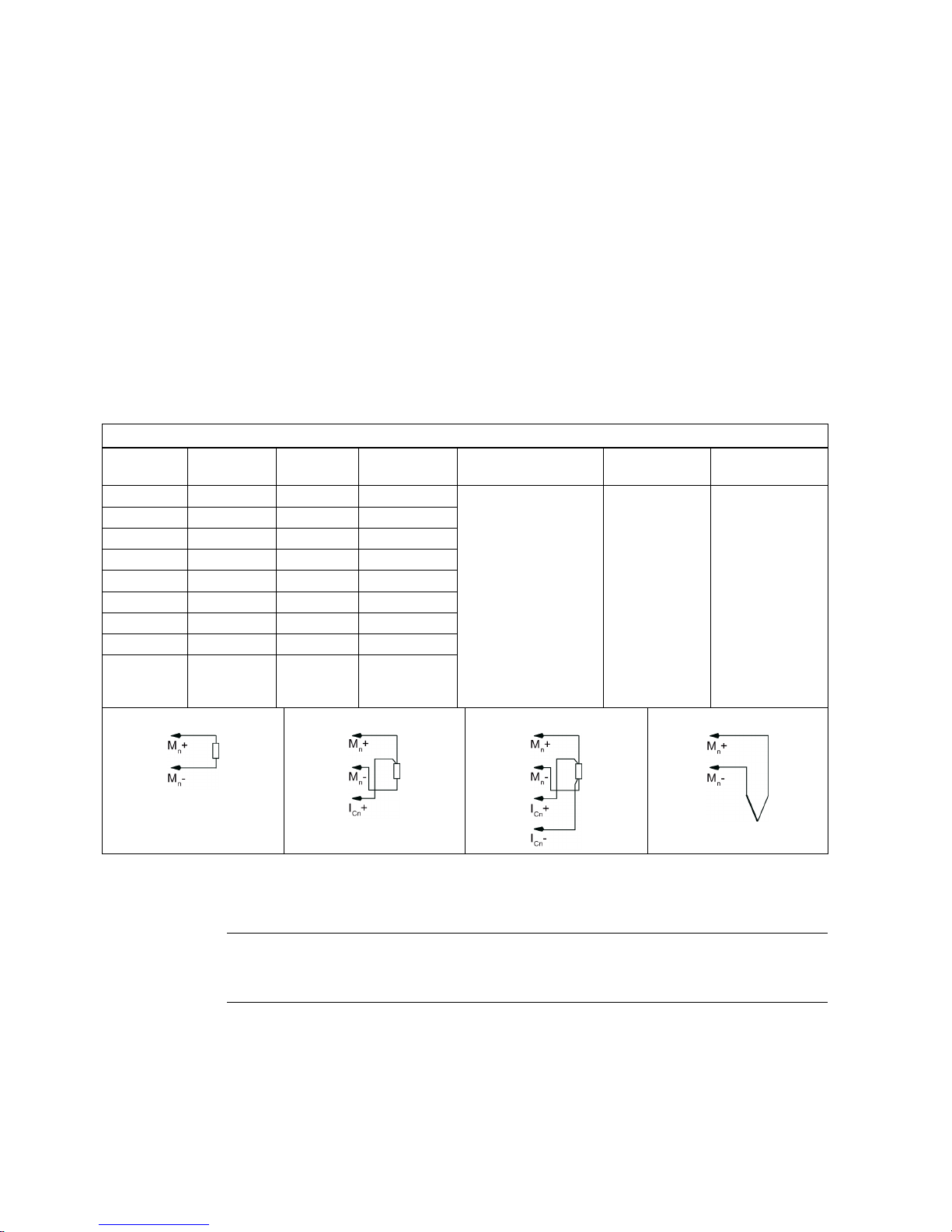
Analog input module AI 4xRTD/TC 2-/3-/4-wire HF (6ES7134-6JD00-0CA1)
10 Manual, 02/2014, A5E03573289-AD
Pin assignment
General pin assignment
Table 3- 1 Pin assignment for AI 4xRTD/TC 2-/3-/4-wire HF
Pin assignment for AI 4×RTD/TC 2-/3-/4-wire HF (6ES7134-6JD00-0CA1)
Color
identification label
• Mn+: Measuring
line positive,
channel n
• M
n
-: Measuring line
negative, channel n
• ICn+: Constant
current line
positive, channel n
• I
Cn
-: Constant
current line
negative, channel n
A0
A1
---
M
RTD 2-wire connection
RTD 3-wire connection
RTD 4-wire connection
Usable BaseUnit types, can be identified by the last two digits of the article number. See also "ET 200SP distributed I/O
Note
The first BaseUnit of a station must be a light
-colored BaseUnit. Keep this in mind also
during the configuration.
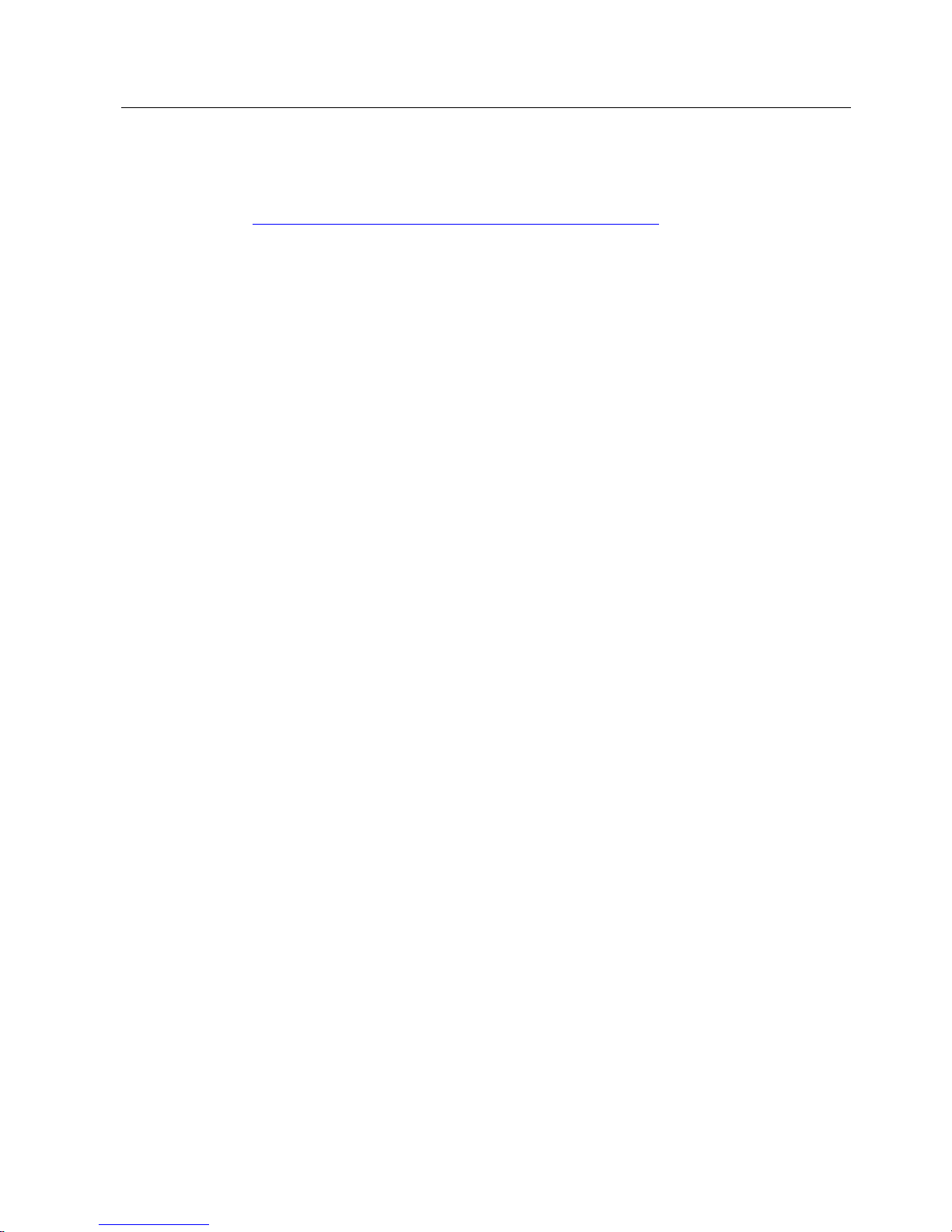
Wiring
3.1 Pin assignment
Analog input module AI 4xRTD/TC 2-/3-/4-wire HF (6ES7134-6JD00-0CA1)
Manual, 02/2014, A5E03573289-AD
11
ET 200SP distributed I/O system
(http://support.automation.siemens.com/WW/view/en/58649293)
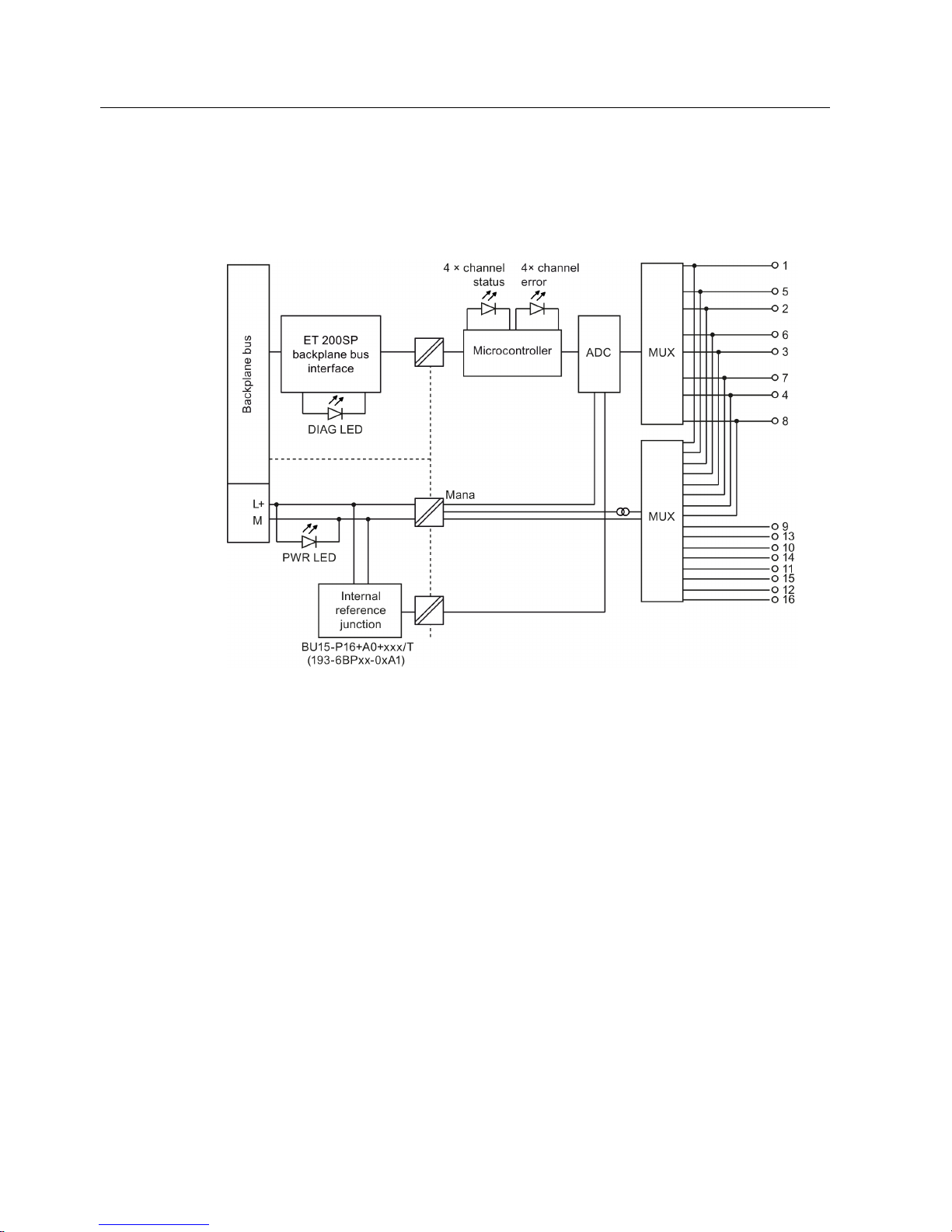
Wiring
3.2 Schematic circuit diagram
Analog input module AI 4xRTD/TC 2-/3-/4-wire HF (6ES7134-6JD00-0CA1)
12 Manual, 02/2014, A5E03573289-AD
Schematic circuit diagram
Schematic circuit diagram
Figure 3-1 Schematic circuit diagram AI 4×RTD/TC 2-/3-/4-wire HF
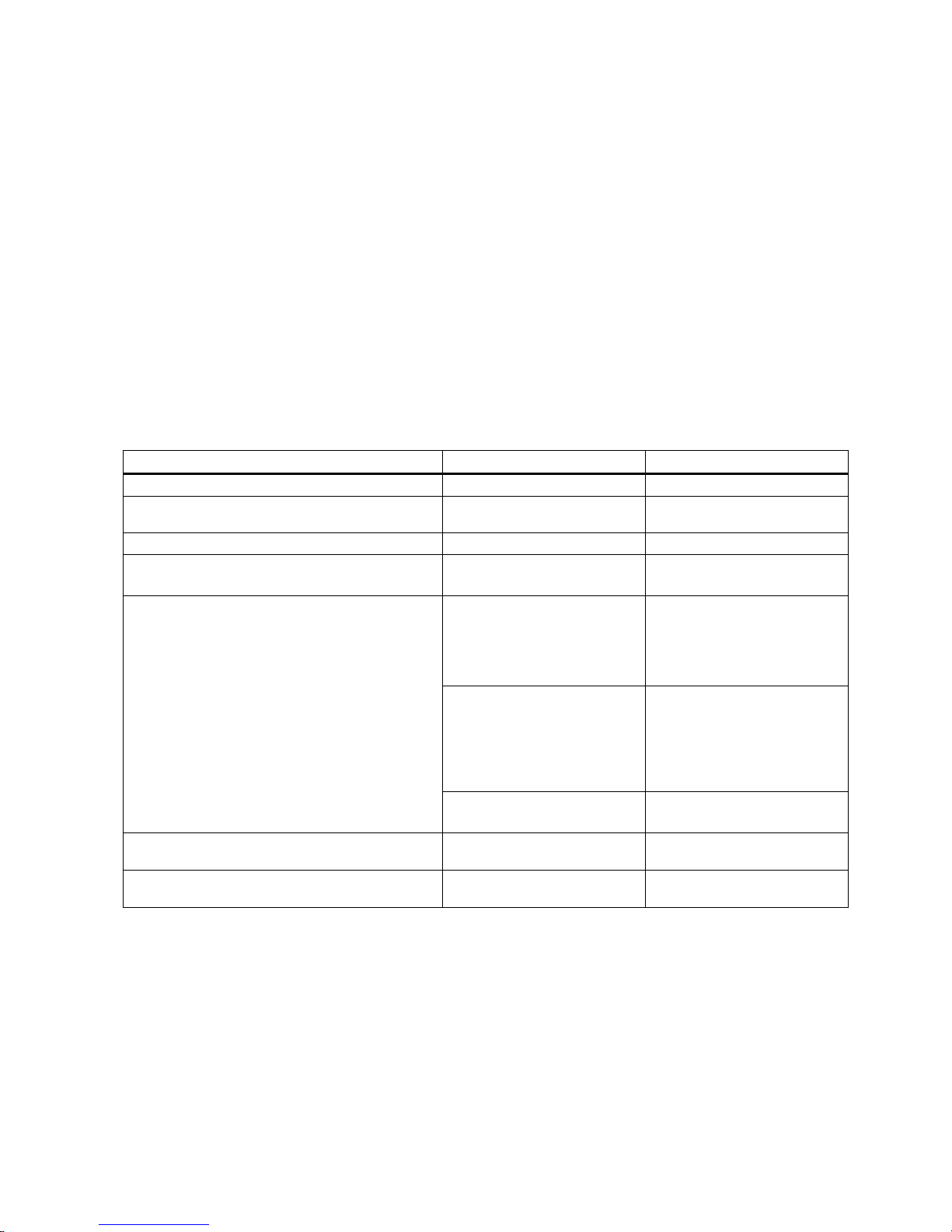
Analog input module AI 4xRTD/TC 2-/3-/4-wire HF (6ES7134-6JD00-0CA1)
Manual, 02/2014, A5E03573289-AD
13
Measurement types and measuring ranges
The following table describes the measuring range and the temperature coefficients you can
configure for each measurement type:
Table 4- 1 Measurement types and measuring ranges
Resistor (2-, 3-, 4-wire connection) 150 Ω / 300 Ω / 600 Ω /
Resistor (2-wire connection)
Thermal resistor RTD
(3-wire connection)
Climatic / Standard
Cu 0.004271
Thermal resistor RTD
(2, 3, 4-wire connection)
Climatic / Standard
Pt 100
Pt 200
Pt 500
Pt 0.00385 /
Pt 0.003916 /
Pt 0.003902 /
Pt 0.00392 /
Pt 0.00385055
Climatic / Standard
Ni 100
Ni 120
Ni 200
Ni 500
Ni 0.00618 /
Ni 0.00672
Climatic2 / Standard2
Ni 0.005
Thermocouple (TC) Type E, N, J, K, L, S, R,
B, T, C, U, TXK (acc. to GOST)
Voltage ±50 mV / ±80 mV /
The preset temperature coefficients are valid for Europe.
2
For sensors LG-Ni 1000 from Siemens Building Ltd (Landis & Stäfa).
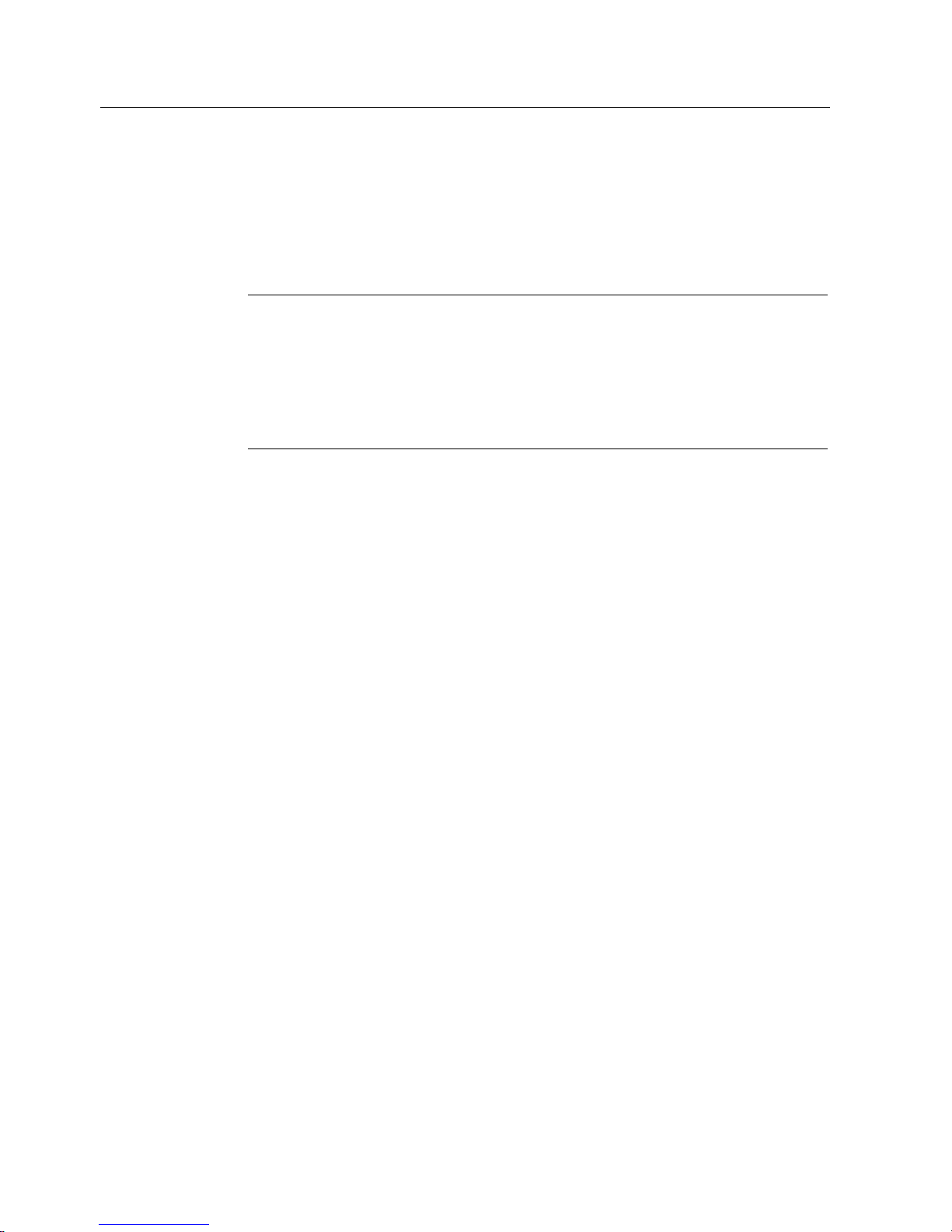
Parameters/address space
4.1 Measurement types and measuring ranges
Analog input module AI 4xRTD/TC 2-/3-/4-wire HF (6ES7134-6JD00-0CA1)
14 Manual, 02/2014, A5E03573289-AD
Special features when using Cu10 sensors
● Choose "Thermal resistor (3-wire connection)" and "Cu10" in the parameter assignment.
● Wire the Cu10 sensor into the 3-wire connection technology.
● During operation, automatic, internal compensation of the line resistance of the missing
measuring line takes place.
Note
To ensure optimum line compensation with Cu10, please observe the following:
• An accurate measured value is only attained if the cable resistance of the positive
const
ant current line to the Cu10 sensor and the cable resistance of the negative
measuring line are identical in value.
• Recommendation: Keep the measuring line as short as possible.
• Different resistance values may also occur due to the connection method used.
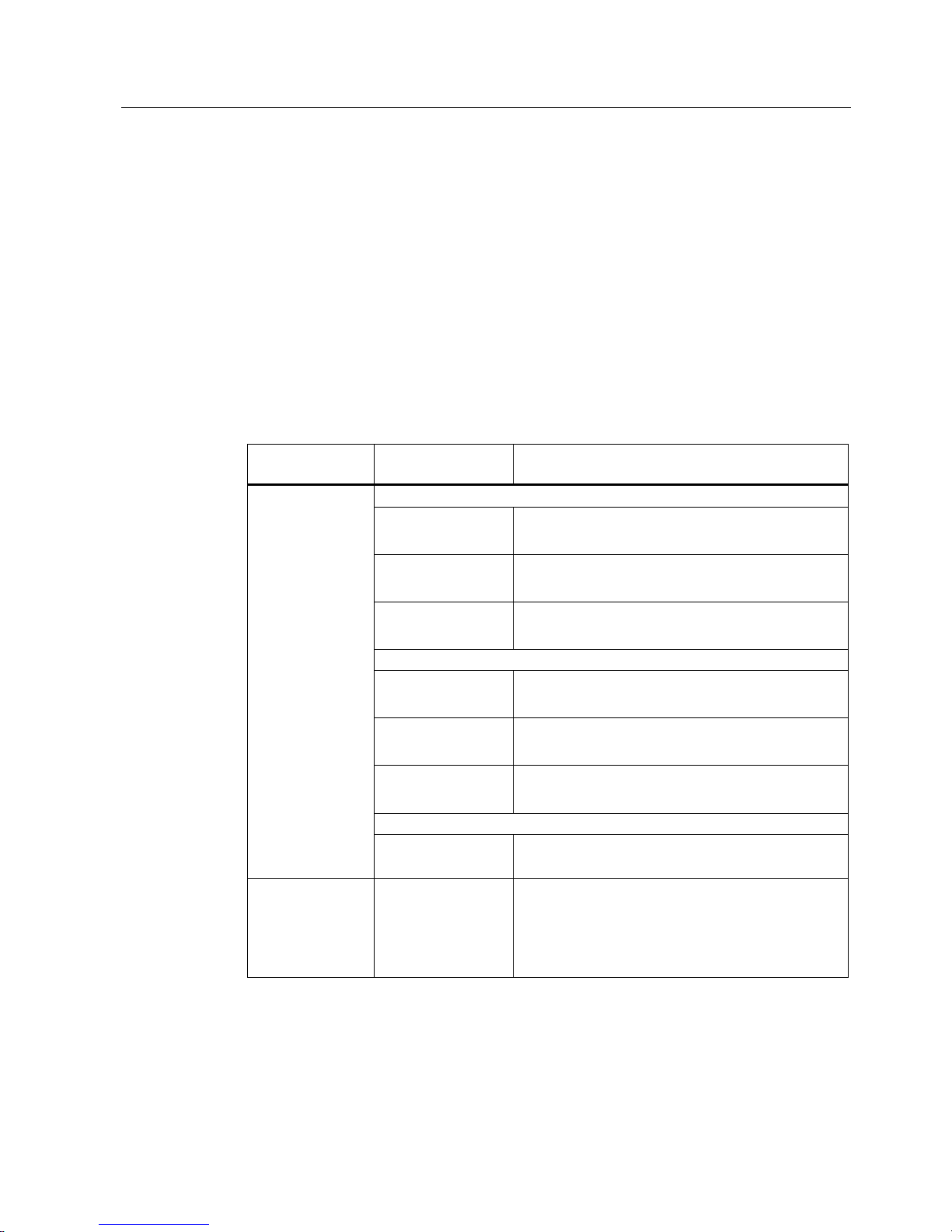
Parameters/address space
4.1 Measurement types and measuring ranges
Analog input module AI 4xRTD/TC 2-/3-/4-wire HF (6ES7134-6JD00-0CA1)
Manual, 02/2014, A5E03573289-AD
15
Special features when using PTC resistors
PTCs are suitable for monitoring temperature and/or as thermal protection devices of
complex drives or transformer windings.
● Choose "Thermal resistor (2-wire)" and "PTC" in the parameter assignment.
● Connect the PTC to the 2-wire connection technology.
● Use the PTC resistors, type A (PTC thermistor) in accordance with DIN/VDE 0660,
part 302.
● If "Underflow" diagnostic is enabled, a "Low limit violated" diagnostic is generated for
resistance values < 18 Ω, indicating a short-circuit.
● Sensor data for the PTC resistor:
Table 4- 2 Using PTC resistors
Property Technical
specifications
Comment
Switching points Behavior with rising temperature
< 550 Ω Normal range:
• SIMATIC S7: Bit 0 = "0", Bit 2 = "0" (in the PII)
550 Ω to 1650 Ω Prewarning range:
• SIMATIC S7: Bit 0 = "0", Bit 2 = "1" (in the PII)
> 1650 Ω Response range:
• SIMATIC S7: Bit 0 = "1", Bit 2 = "0" (in the PII)
Behavior with falling temperature
> 750 Ω Response range:
• SIMATIC S7: Bit 0 = "1", Bit 2 = "0" (in the PII)
750 Ω to 540 Ω Prewarning range:
• SIMATIC S7: Bit 0 = "0", Bit 2 = "1" (in the PII)
< 540 Ω Normal range:
• SIMATIC S7: Bit 0 = "0", Bit 2 = "0" (in the PII)
Reaction to short-circuit
< 18 Ω
• SIMATIC S7: Bit 7 (IB x+1) = "1", Bit 0 = "0" and
Bit 2 = "0"
(RRT-5) °C
(RRT+5) °C
(RRT+15) °C
Measuring voltage/
voltage at the PTC
Max. 550 Ω
min. 1330 Ω
min. 4000 Ω
Max. 7.5 V
1
TNF = Rated response temperature of the sensor
(according to DIN/VDE 0660)
1
Below 23 kΩ
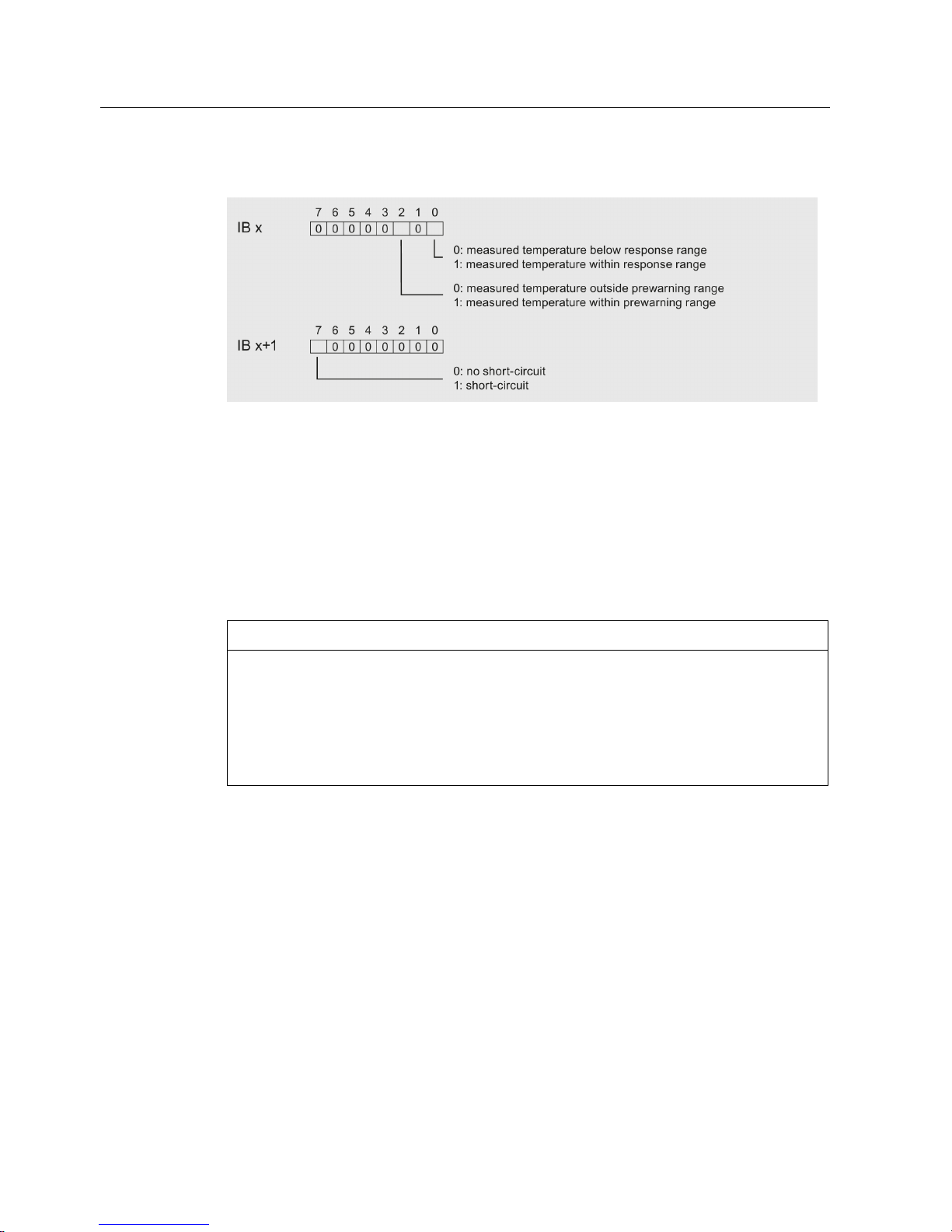
Parameters/address space
4.1 Measurement types and measuring ranges
Analog input module AI 4xRTD/TC 2-/3-/4-wire HF (6ES7134-6JD00-0CA1)
16 Manual, 02/2014, A5E03573289-AD
Assignment in the process image input (PII) with SIMATIC S7
Figure 4-1 Assignment in the process image input (PII)
Notes on programming
● Bits 0+2 are relevant for evaluation in the process image input. You can monitor, for
exampl
e, the temperature of a motor using bits 0+2.
● Bits 0+2 in the process image input cannot be saved. During parameter assignment, take
into consideration that a motor, for example, starts up in a controlled manner (via an
acknowledgment).
● Bits 0+2 can never be set at the same time; they are set one after the other.
NOTICE
No measurement is possible in the following cases:
• When I/O modules are pulled out
• When s
upply voltage to the I/O module fails
• When there is a wire break or short-circuit in the measuring lines
Therefore, always evaluate the diagnostics entries of the AI 4×RTD/TC 2-/3-/4-wire HF for
safety reasons.
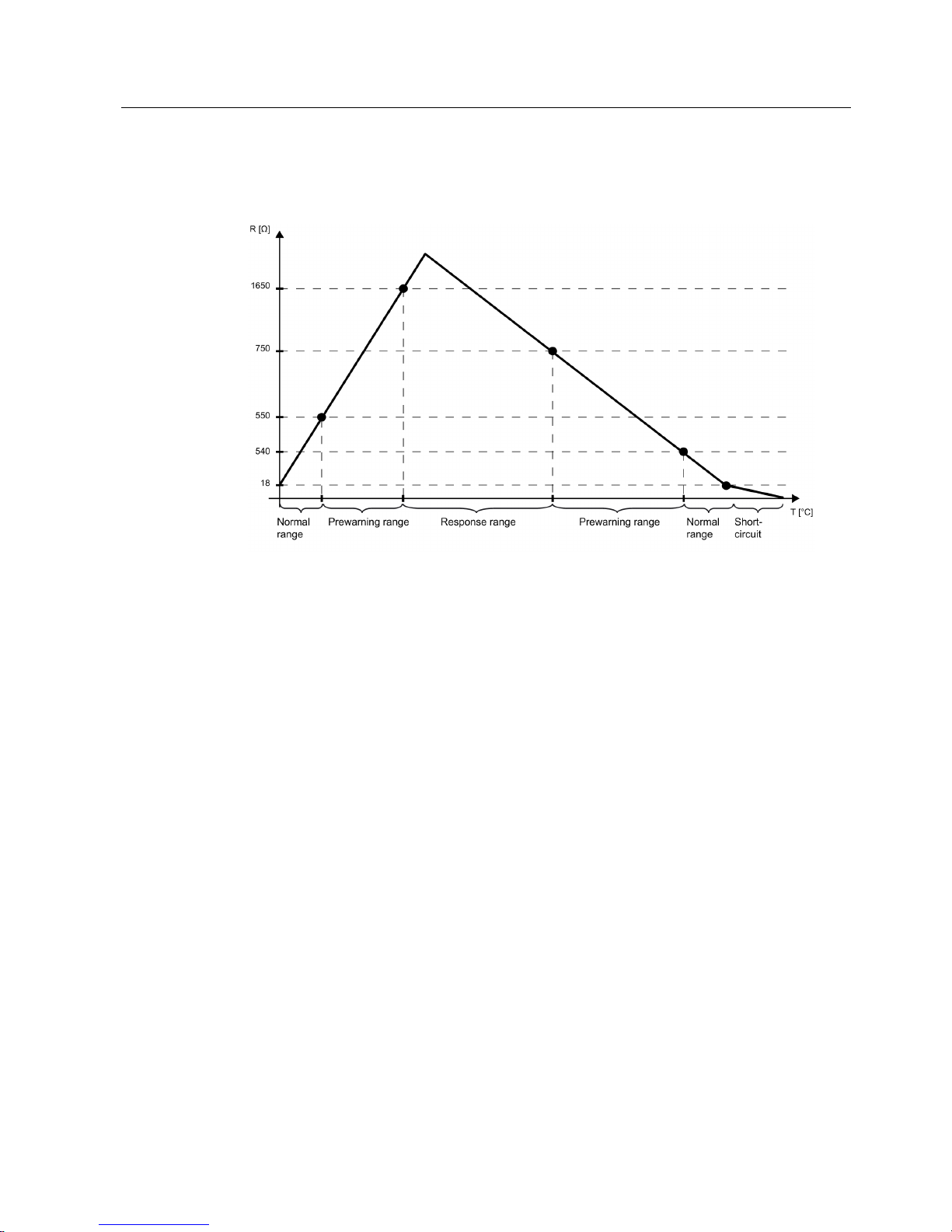
Parameters/address space
4.1 Measurement types and measuring ranges
Analog input module AI 4xRTD/TC 2-/3-/4-wire HF (6ES7134-6JD00-0CA1)
Manual, 02/2014, A5E03573289-AD
17
Example
The diagram shows the temperature curve and the associated switching points.
Figure 4-2 Temperature curve with prewarning range
See also
Technical specifications (Page 40)
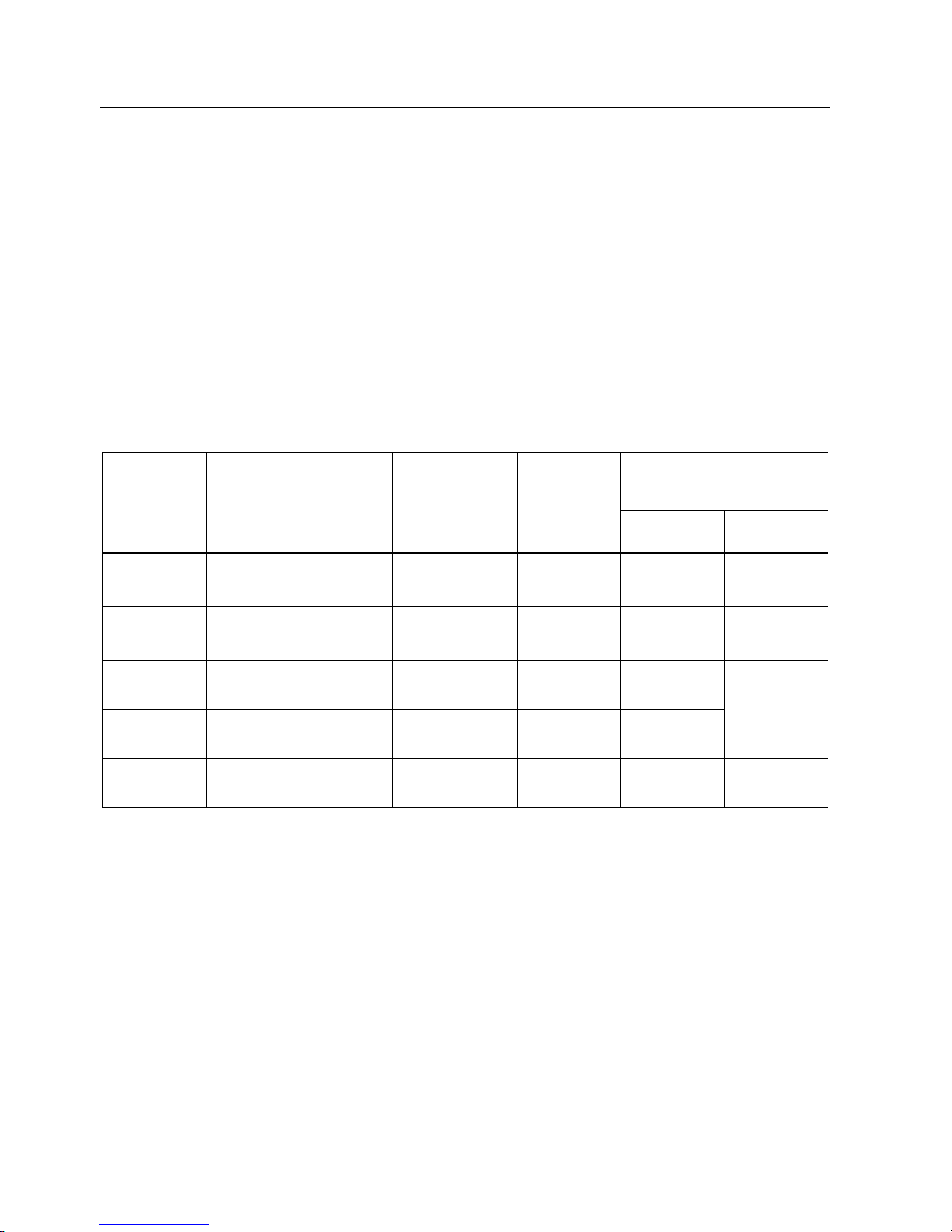
Parameters/address space
4.2 Parameters
Analog input module AI 4xRTD/TC 2-/3-/4-wire HF (6ES7134-6JD00-0CA1)
18 Manual, 02/2014, A5E03573289-AD
4.2 Parameters
Parameters of the AI 4xRTD/TC 2-/3-/4-wire HF
The following table lists the configurable parameters. The effective range of the configurable
parameters depends on the type of configuration. The following configurations are possible:
● Distributed operation on PROFINET IO in an ET 200SP system
● Distributed operation on PROFIBUS DP in an ET 200SP system
When assigning parameters in the user program, use the WRREC instruction to transfer the
parameters to the module by means of data records, see section Parameter assignment and
structure of parameter data record (Page 52). The following parameter settings are possible:
Table 4- 3 Configurable parameters and their defaults (GSD file)
Parameter Value range Default Reconfiguration
in RUN
Scope with configuration
software, e.g.,
STEP 7 (TIA Portal)
GSD file
PROFINET IO
GSD file
PROFIBUS DP
Diagnostics:
Missing supply
voltage L+
• Disable
• Enable
D
isable Yes Channel Channel
1
Diagnostics:
Reference
junction
• Disable
• Enable
D
isable Yes Channel Module
Diagnostics:
Overflow
• Disable
• Enable
Disable Yes Channel Module
Diagnostics:
Underflow
• Disable
• Enable
Disable Yes Channel
Diagnostics:
Wire break
• Disable
• Enable
Disable Yes Channel Channel
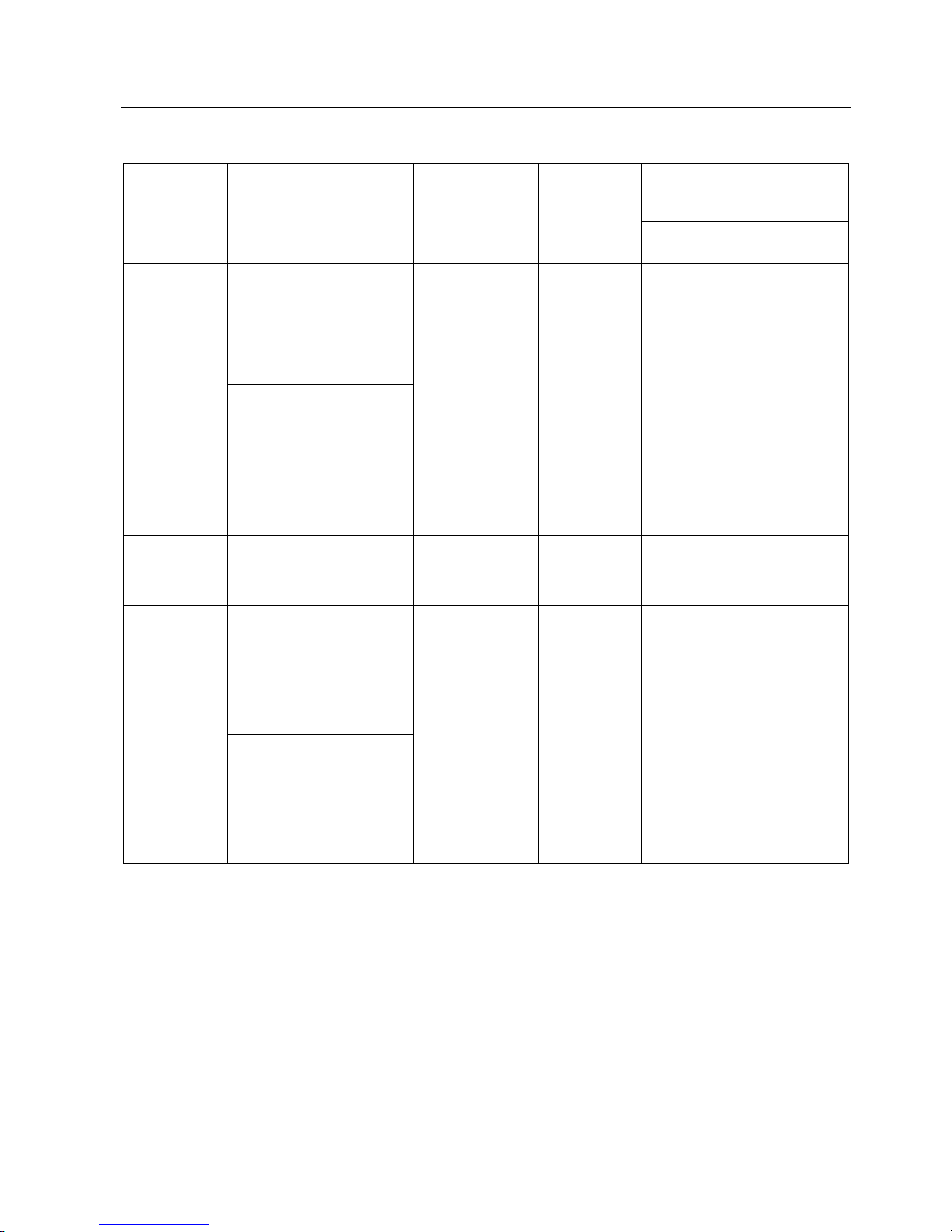
Parameters/address space
4.2 Parameters
Analog input module AI 4xRTD/TC 2-/3-/4-wire HF (6ES7134-6JD00-0CA1)
Manual, 02/2014, A5E03573289-AD
19
Parameter Value range Default Reconfiguration
in RUN
Scope with configuration
software, e.g.,
STEP 7 (TIA Portal)
GSD file
PROFINET IO
GSD file
PROFIBUS DP
Type/range of
measurement
• Deactivated
Thermal resistor
(4-wire connection)
Pt 100 standard
range
Yes Channel Channel
• Voltage ±50 mV
• Voltage ±80 mV
• Voltage ±250 mV
• Voltage ±1 V
Resistor
(2-, 3-, 4-wire connection)
• 150 Ω
• 300 Ω
• 600 Ω
• 3 kΩ
• 6 kΩ
Type/range of
measurement
Resistor (2-wire connection)
PTC
Thermal resistor
(4-wire connection)
Pt 100 standard
range
Yes Channel Channel
Type/range of
measurement
Thermal resistor
(2, 3, 4-wire connection)
• Pt 100 climatic range
• Pt 200 climatic range
• Pt 500 climatic range
• Pt 1000 climatic range
Thermal resistor
(4-wire connection)
Pt 100 standard
range
Yes Channel Channel
Thermal resistor
(2, 3, 4-wire connection)
• Pt 100 standard range
• Pt 200 standard range
• Pt 500 standard range
• Pt 1000 standard range
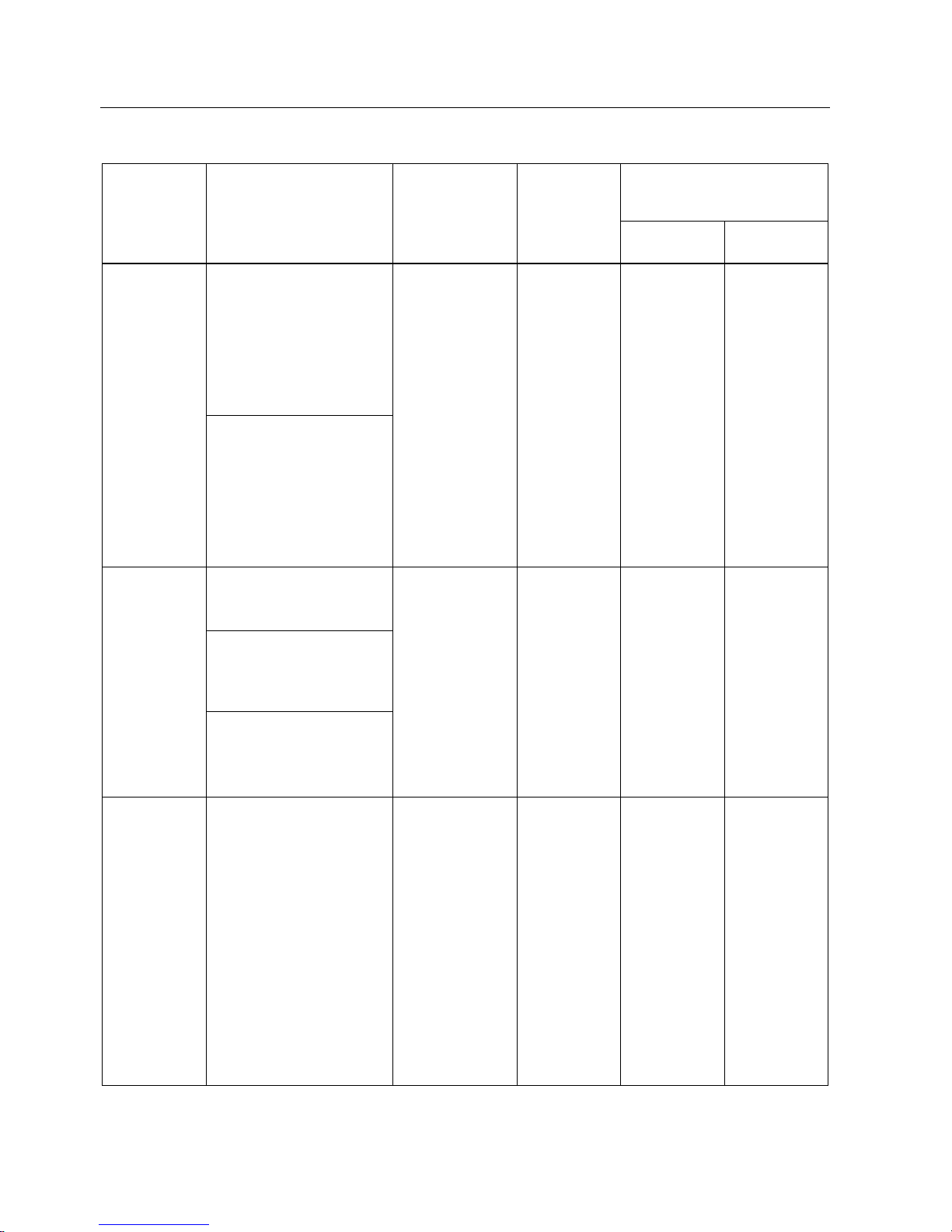
Parameters/address space
4.2 Parameters
Analog input module AI 4xRTD/TC 2-/3-/4-wire HF (6ES7134-6JD00-0CA1)
20 Manual, 02/2014, A5E03573289-AD
Parameter Value range Default Reconfiguration
in RUN
Scope with configuration
software, e.g.,
STEP 7 (TIA Portal)
GSD file
PROFINET IO
GSD file
PROFIBUS DP
Type/range of
measurement
Thermal resistor
(2, 3, 4-wire connection)
• Ni 100 climatic range
• Ni 120 climatic range
• Ni 200 climatic range
• Ni 500 climatic range
• Ni 1000 climatic range
Thermal resistor
(4-wire connection)
Pt 100 standard
range
Yes Channel Channel
Thermal resistor
(2, 3, 4-wire connection)
• Ni 100 standard range
• Ni 120 standard range
• Ni 200 standard range
• Ni 500 standard range
• Ni 1000 standard range
Type/range of
measurement
Thermal resistor
(2, 3, 4-wire connection)
• LG Ni 1000 climatic range
Thermal resistor
(4-wire connection)
Pt 100 standard
range
Yes Channel Channel
Thermal resistor
(2, 3, 4-wire connection)
• LG Ni 1000 standard
range
Thermal resistor (3-wire
connection)
• Cu 10 climatic range
• Cu 10 standard range
Type/range of
measurement
Thermocouple
• Type B (PtRh-PtRh)
• Type N (NiCrSi-NiSi)
• Type E (NiCr-CuNi)
• Type R (PtRh-Pt)
• Type S (PtRh-Pt)
• Type J (Fe-CuNi)
• Type L (Fe-CuNi)
• Type T (Cu-CuNi)
• Type K (NiCr-NiAl)
• Type U (Cu-CuNi)
• Type C (WRe-WRe)
• Type TXK
Thermal resistor
(4-wire connection)
Pt 100 standard
range
Yes Channel Channel
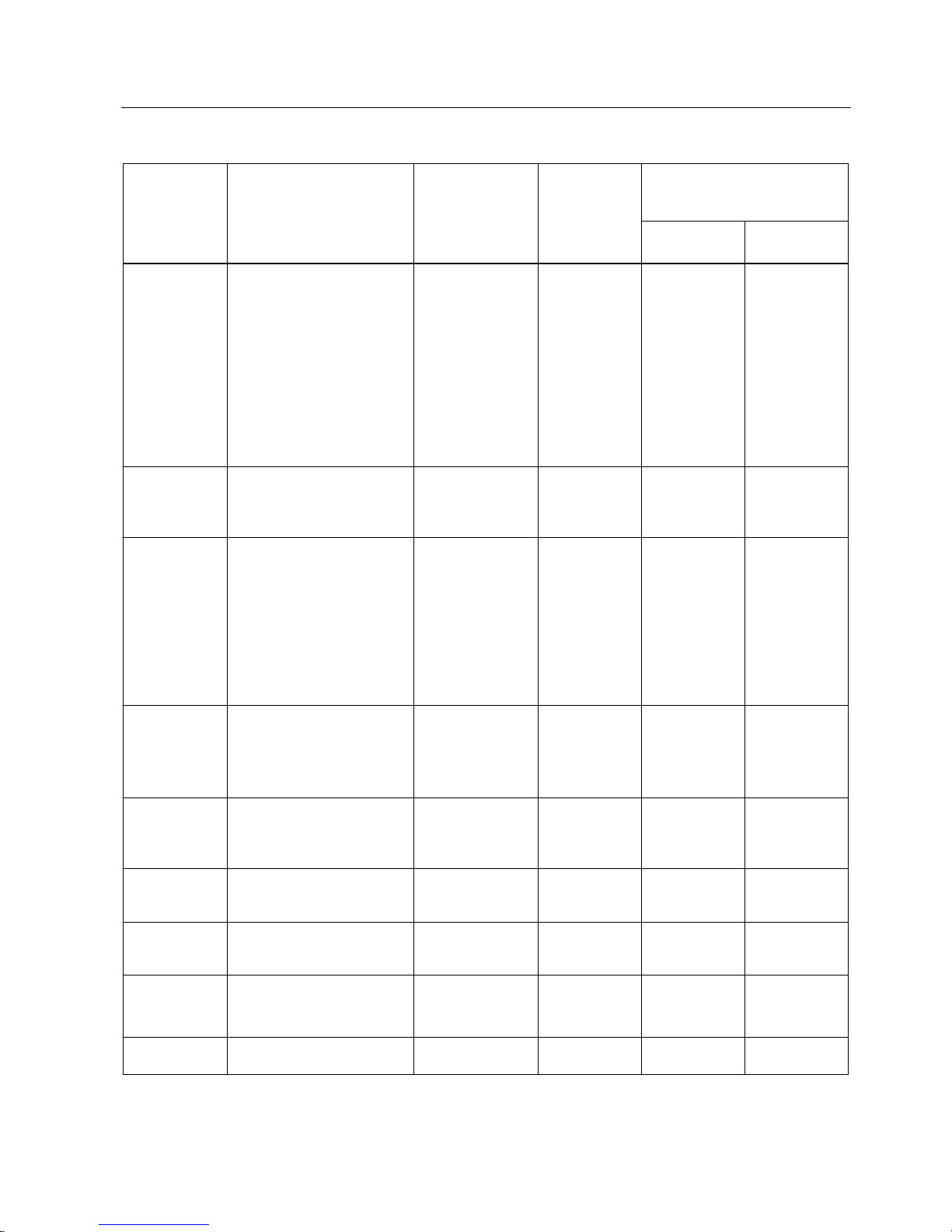
Parameters/address space
4.2 Parameters
Analog input module AI 4xRTD/TC 2-/3-/4-wire HF (6ES7134-6JD00-0CA1)
Manual, 02/2014, A5E03573289-AD
21
Parameter Value range Default Reconfiguration
in RUN
Scope with configuration
software, e.g.,
STEP 7 (TIA Portal)
GSD file
PROFINET IO
GSD file
PROFIBUS DP
Temperature
coefficient
• Pt 0.00385055
• Pt 0.003916
• Pt 0.003902
• Pt 0.00392
• Pt 0.00385
• Ni 0.00618
• Ni 0.00672
• LG-Ni 0.005
• Cu 0.00427
Pt 0.00385055 Yes Channel Channel
Temperature
unit
• Degrees Celsius
• Degrees Fahrenheit
• Kelvin
Degrees Celsius Yes Channel Module
Reference
junction
4
• No reference channel mode
• Reference channel of the
module
• Internal reference junction
• Reference channel of
group 0 to 3
• Fixed reference
temperature
No reference
channel mode
Yes Channel Channel
Smoothing
• None
• Weak
• Medium
• Strong
None Yes Channel Channel
Interference
frequency
suppression 3
• 60 Hz
• 50 Hz
2
• 16.6 Hz
50 Hz Yes Channel Channel
Scalable
measuring
range
• Disable
• Enable
D
isable Yes Channel -
Measuring
range
resolution
• 2 decimal places
• 3 deci
mal places
2 decimal places Yes Channel -
Measuring
range center
• Value within the nominal
range of the measuring
range
0 Yes Channel -
Conductor
resistance
5
0 to 50000 mΩ 0 Yes C
hannel -