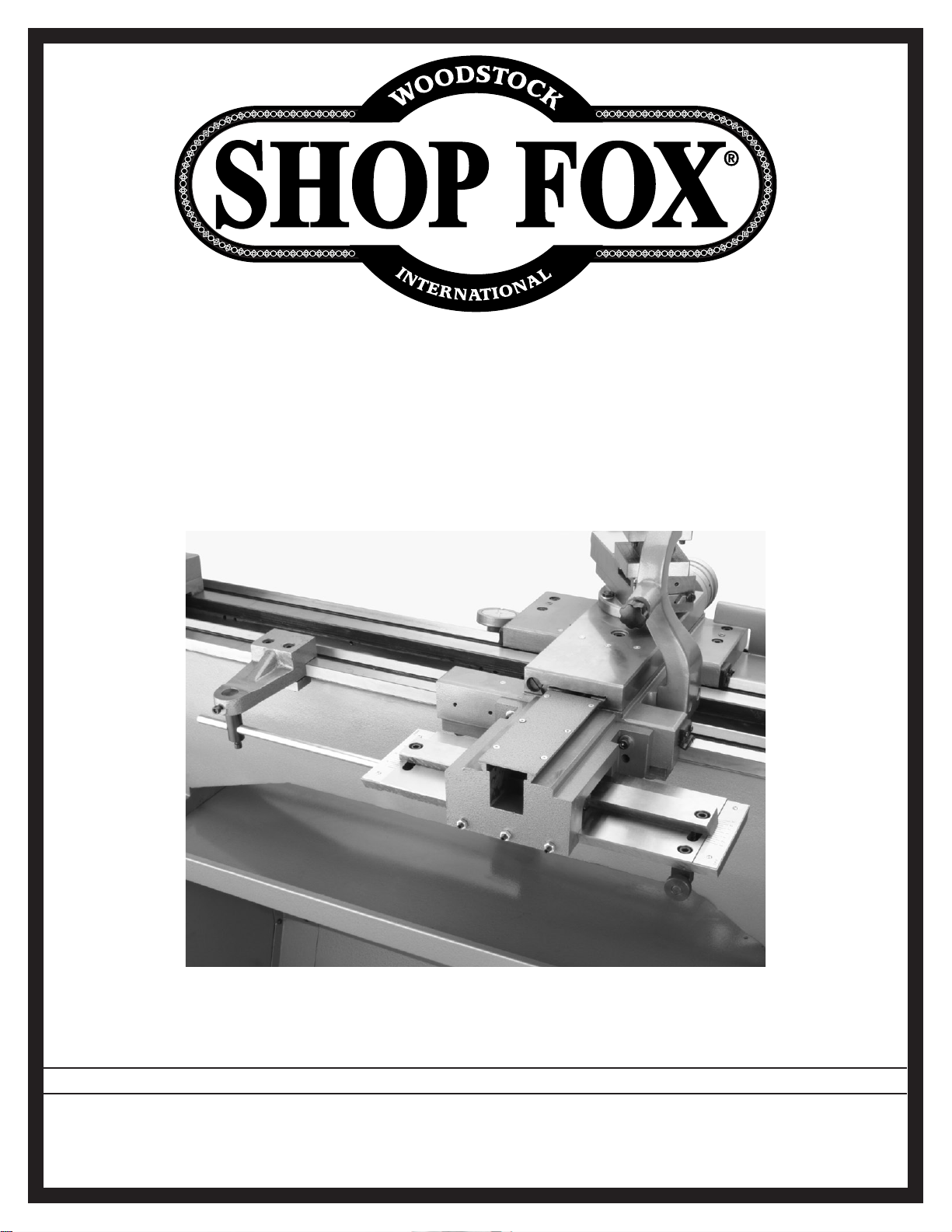
MODEL M1022
TAPER ATTACHMENT
FOR USE WITH MODEL M101 9
#6809 BL
INSTRUCTION MANUAL
Phone: (360) 734-3482 • On-Line Technical Support: tech-support@shopfox.biz
COPYRIGHT © DECEMBER, 2004 BY WOODSTOCK INTERNATIONAL, INC.
WARNI NG: NO PO RTION OF THI S MANUA L MAY B E REPRO DUCED IN ANY S HAPE OR F ORM WITHOU T
THE WRI TTEN AP PROVAL OF WO ODSTO CK INTERNATIONA L, INC.
Print ed in China
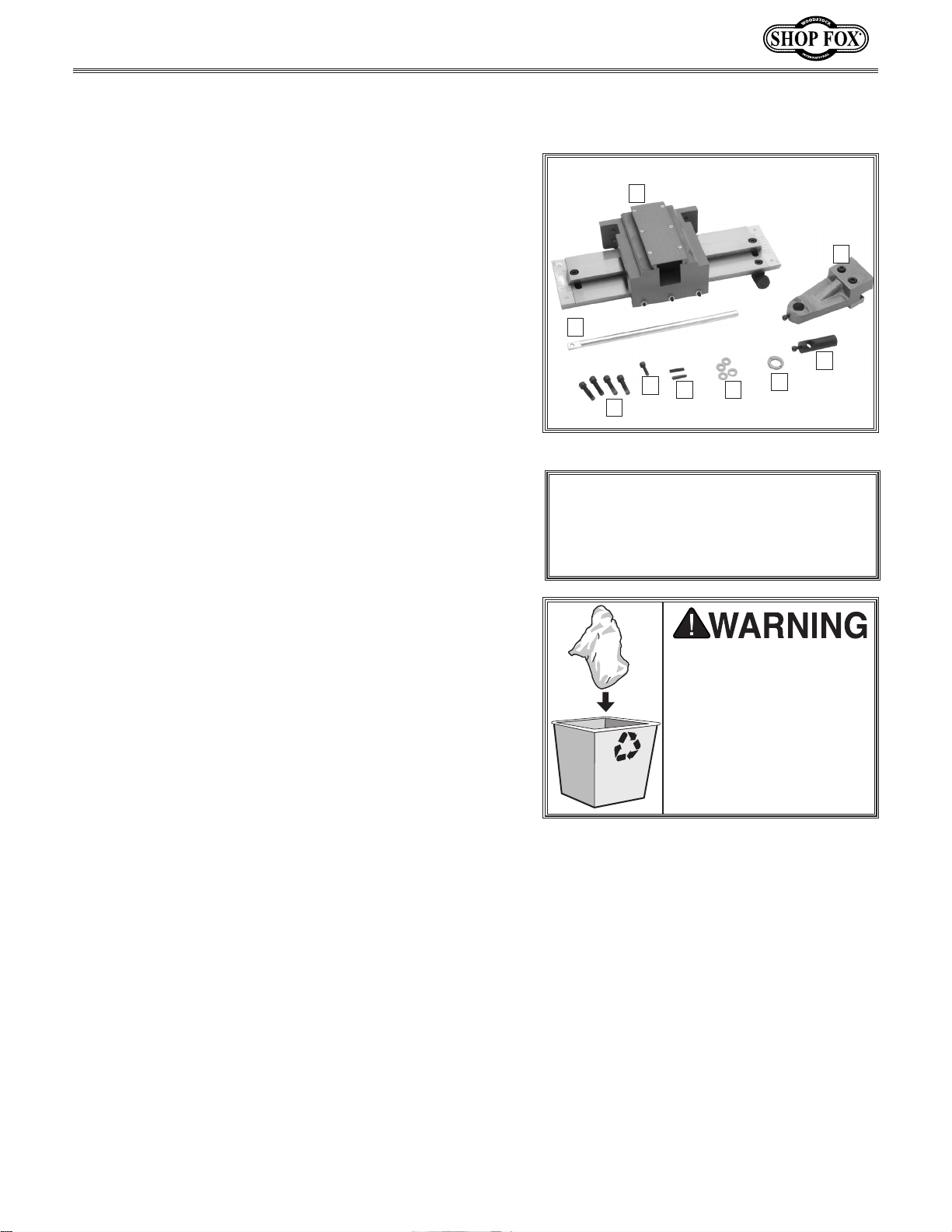
M1022 Taper Attachment
INVENTORY
The following is a description of the main components
shipped with the
Attachment. Lay the components out to inventory them.
Box Contents (Figure
QTY
A. Taper Attachment Body ..................................1
B. Clamping Block ............................................1
C. Support Rod ................................................1
D. Vertical Rod with Cap Screw M6 x 1.0-16 .............1
E. Cap Screws M8-1.25 x 30 ................................4
F. Cap Screw M6-1.0 x 20 ...................................1
G. Roll Pins .....................................................2
H. Washers 8mm ..............................................4
I. Washer 17mm ..............................................1
If any parts appear to be missing, examine the packag
ing carefully to be sure those parts are not among the
packing materials. If any parts are missing, find the
part number in the back of this manual and contact
Woodstock International, Inc. at (360) 734-3482 or at
tech-support@shopfox.biz
SHOP FOX
1)
®
Model M1022 Taper
-
A
B
C
D
F
G
E
Figure 1. Main contents.
H
I
NOTICE
When ordering replacement parts, refer
to the parts list and diagram in the back
of the manual.
SUFFOCATION
HAZARD!
Immediately
discard
all plastic bags and
packing materials to
eliminate choking/suffocation hazards for
children and animals.
-3-
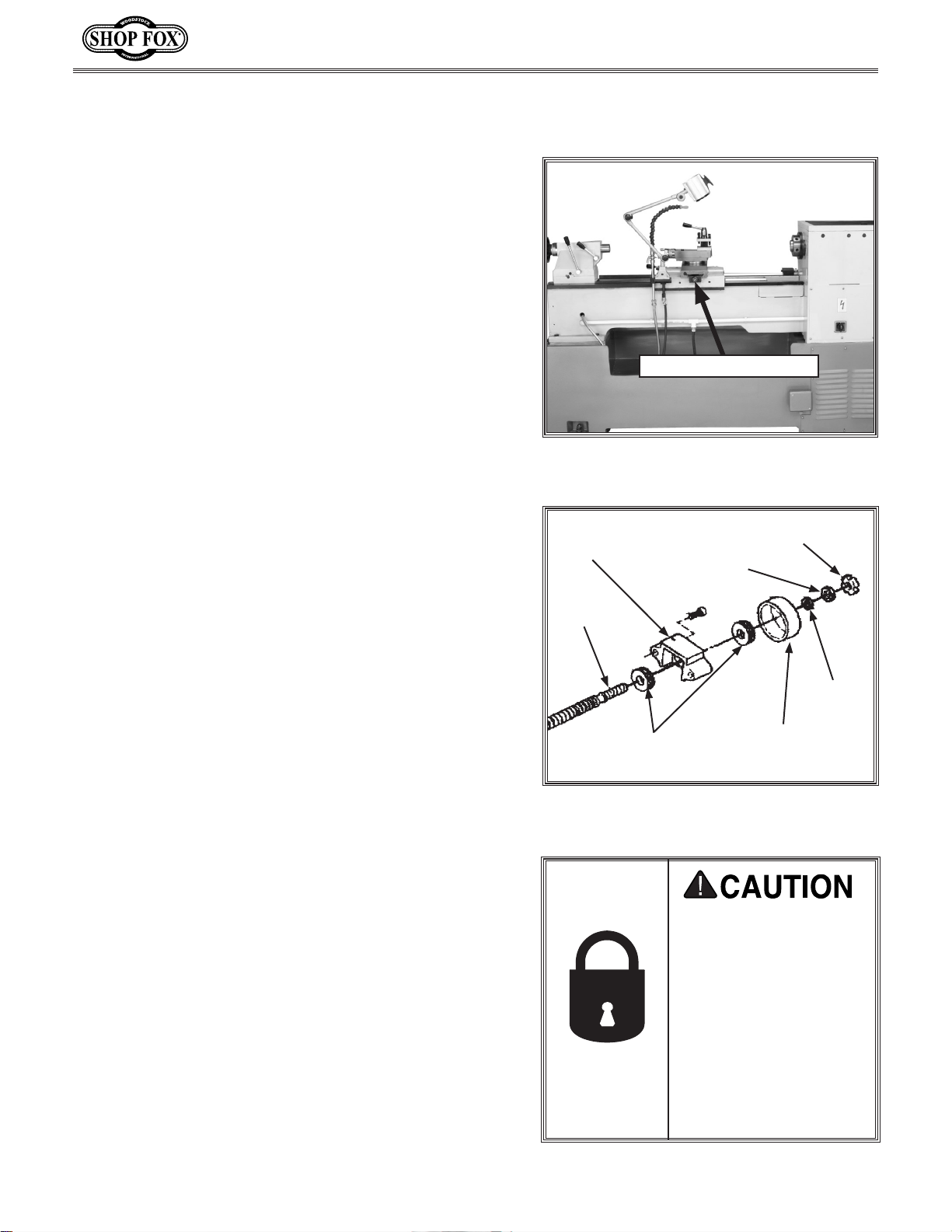
INSTALLATION
The Model M1022 Taper Attachment mounts quickly to
the back of the carriage and bed way of the Model M1019
Gear Head Lathe. Accurate tapers up to 12" can be pro
duced without repositioning the attachment. The Model
M1022 features scales at both ends, reading inches-perfoot and degrees. An angle adjusting screw with fine
threads achieves exacting control when setting tapers.
Another feature is the ability to use it without disengaging
the locking nut. This will allow it to be functional at any
time by simply tightening the clamping block.
The Model M1022 comes carefully packaged and coated
with grease for rust protection. You will need to clean all
pieces thoroughly with a solvent cleaner prior to instal
lation and use. For optimum performance from your
taper attachment, make sure you clean all moving
parts or sliding contact surfaces that are coated. Avoid
chlorine-based solvents as they may damage painted
surfaces should they come in contact. Always follow the
manufacturer’s instructions when using any type of clean
ing product.
Installing the Taper
-
-
-
M1022 Taper Attachment
Cross Slide Lead Screw
Figure 2. Back of lathe with splash guard
removed.
Bearing
Housing
Lead
Screw
External Tooth
Washer
Locking Nut
Attachment
To install the taper attachment, do these steps:
1. Disconnect the lathe from its power source!
2. Remove the splash guard from the back of the lathe
(Figure 2). If the lathe must be moved to allow
access to the splash guard, consult the lathe manual
for safe moving information.
: If you move the lathe, be sure to re-level it
Note
after returning the lathe to its final location.
3. Remove the locking nut that holds the bearings and
spacers in place at the end of the cross slide lead
screw (Figures 2 &
more tangs of the external tooth washer to accom
plish this.
3). You may need to bend one or
-
Spacer
Thrust
Bearings
Figure 3. Cross lead screw components on
lathe.
MAKE your shop “child
safe.” Ensure that your
workplace is inacces
sible to youngsters by
closing and locking all
entrances when you
are away. NEVER allow
untrained visitors in
your shop when assem
bling, adjusting or
operating equipment.
Bearing Dust
Cover
-
-
-4-
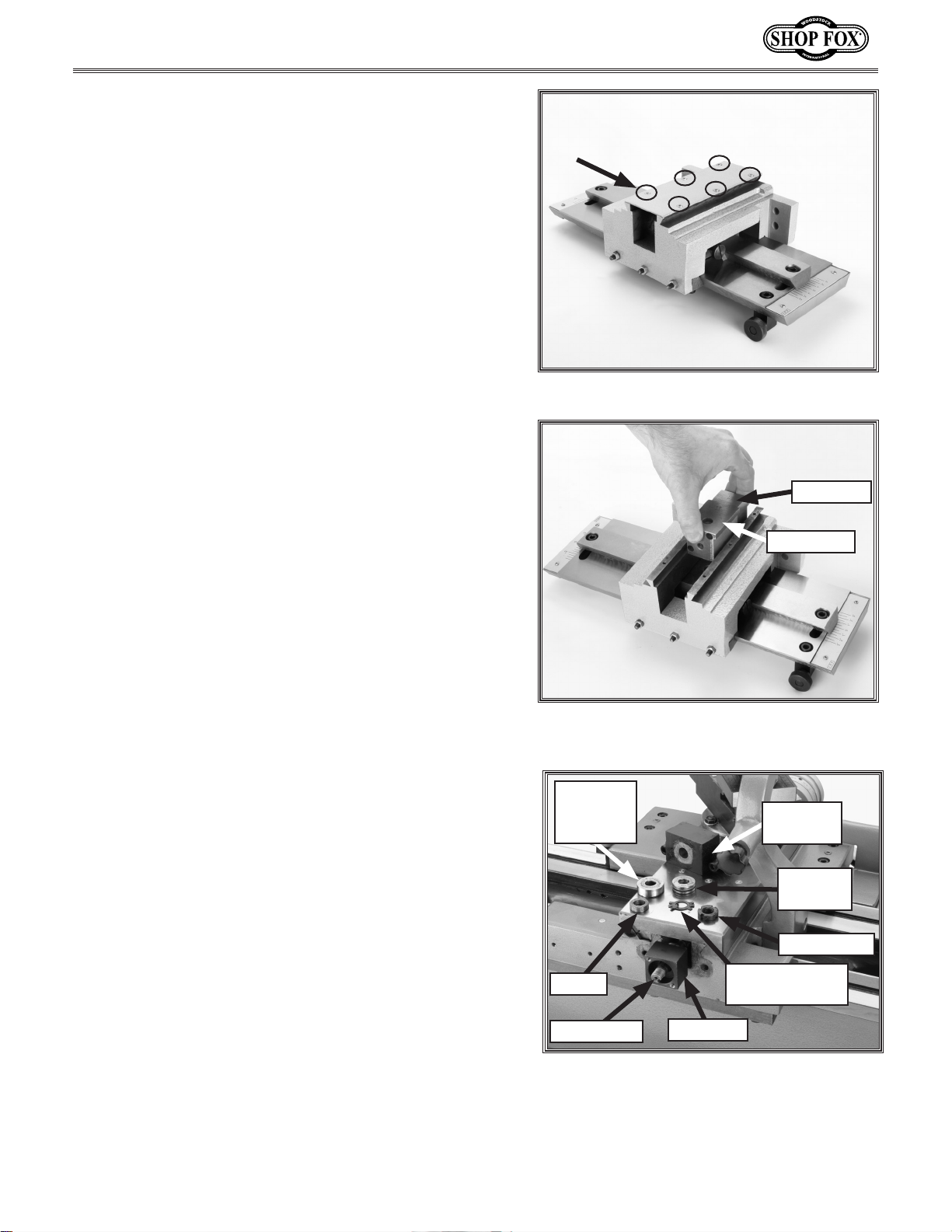
M1022 Taper Attachment
4. Remove the spacer, bearing dust cover, and thrust
bearing (
5. Remove the two cap screws securing the bearing
housing, along with the housing. Leave the remain
ing thrust bearing on the lead screw (
6. Remove the six Phillips head screws from the top
cover plate (
Set the screws and cover aside for later use.
7. Remove the end block and slide block from the taper
attachment body by pulling up, as shown in
These blocks are connected by two cap screws.
Note: The slide block is loosely pinned to a portion of
the cross
aside for future installation or keep the
Figure 6) from the end of the lead screw.
-
Figure 6).
Figure 4) of the taper attachment body.
Figure 5.
slide. Be careful not to lose the pin. Set it
pin in place.
Figure 4. Head screws on cover plate.
8. Separate the end block and slide block by removing
the two cap screws in the slide block. Set the slide
block and cap screws aside for
9. Slide the end block over the lead screw. The end
block bearing pocket and the threaded holes must
face outwards, as shown in
10. Install the thrust bearing, spacer, and external tooth
washer in the same order they were removed into
the opening in the end block. Save the bearing dust
cover in case you want to remove the taper attach
ment.
11. Thread the locking nut (Figure 6) onto the end of
the lead screw and tighten the nut while holding the
cross slide handwheel
ing nut. To check, turn the end block. Only a small
amount of resistance should be felt. Adjust the locking nut as needed.
12. Hold the locking nut in place and bend one or more
tangs of the external tooth washer over the nut.
13. Connect the slide block to the end block using the
two cap screws that were removed in Step 8. The end
block may need to be rotated to line up the holes
. Do not over-tighten the lock-
Step 13.
Figure 6.
-
.
End Block
Slide Block
Figure 5. End block and slide block removed
from taper attachment body.
Bearing
Dust
Cover
Spacer
Lead Screw
End Block
Bearing
Housing
Thrust
Bearing
Locking Nut
External Tooth
Washer
-5-
Figure 6. Lead screw component
identification.