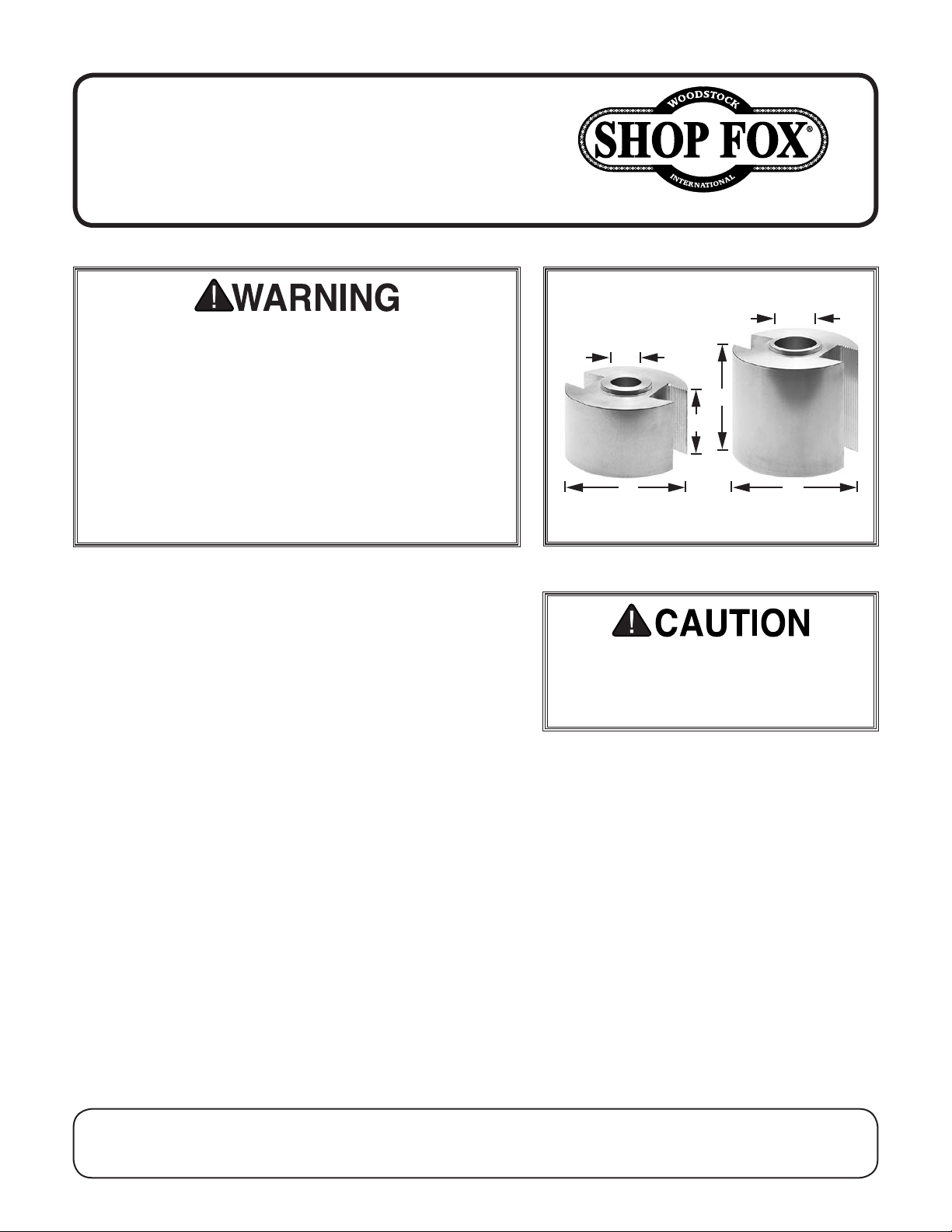
Model D1700/D1701
Moulding Head
Instruction Sheet
Phone #: (360) 734-3482 • Online Tech Support: tech-support@shopfox.biz • Web: www.shopfox.biz
To reduce risk of serious personal injury when using
moulding head:
• Always wear ANSI-approved eye and hearing
protection when using moulding head.
• Never use on
• Never operate with only one knife installed.
• Always ensure BOTH knives are firmly secured in
place BEFORE starting shaper.
• Never feed lumber with rotation of moulding
head.
• Follow safety guidelines of shaper manufacturer.
1
⁄2" spindle.
Introduction
The D1700/D1701 2-Knife Moulding Head (see Figure 1) is
designed to be used on a vertical spindle shaper. It is made
of the highest quality aircraft aluminum and machined to
exact tolerances. The moulding head accepts matched
pairs of interchangeable, corrugated-backed high-speed
knives (not included). The moulding head will use either
60˚ or 90˚–cut corrugations that are spaced
The knives lock into position by wedge-type gibs for maximum safety.
1
⁄16" apart.
1"
¾"
3"
2"
D1700
3"
Figure 1. Moulding head dimensions.
Moulding knives have sharp edges. Use
care while removing them from package.
Remove oily film to help ensure knives
securely mount in moulding head.
D1701
3"
DO NOT use this moulding head on any machine other than
one equipped with a
spindle for the D1701. The shaper should have at least a
1
⁄2 HP motor. We also recommend operating a power
1
feeder when using the moulding head, as it helps feed the
workpiece steadily and consistently for best cutting
results, while at the same time helping you keep your
hands a safe distance away from the cutter.
Important: These instructions and drawings are intended
for explanation and clarification purposes only as they
pertain to the moulding head. You must apply all safety
measures as they relate to shaping operations and your
specific equipment. Review and apply all safety measures
before you use this moulding head.
WARNING: NO PORTION OF THIS MANUAL MAY BE REPRODUCED IN ANY SHAPE OR FORM WITHOUT
3
⁄4" spindle for the D1700, or 1"
COPYRIGHT © SEPTEMBER, 2015 BY WOODSTOCK INTERNATIONAL, INC.
THE WRITTEN APPROVAL OF WOODSTOCK INTERNATIONAL, INC.
Printed in USA#17705BL
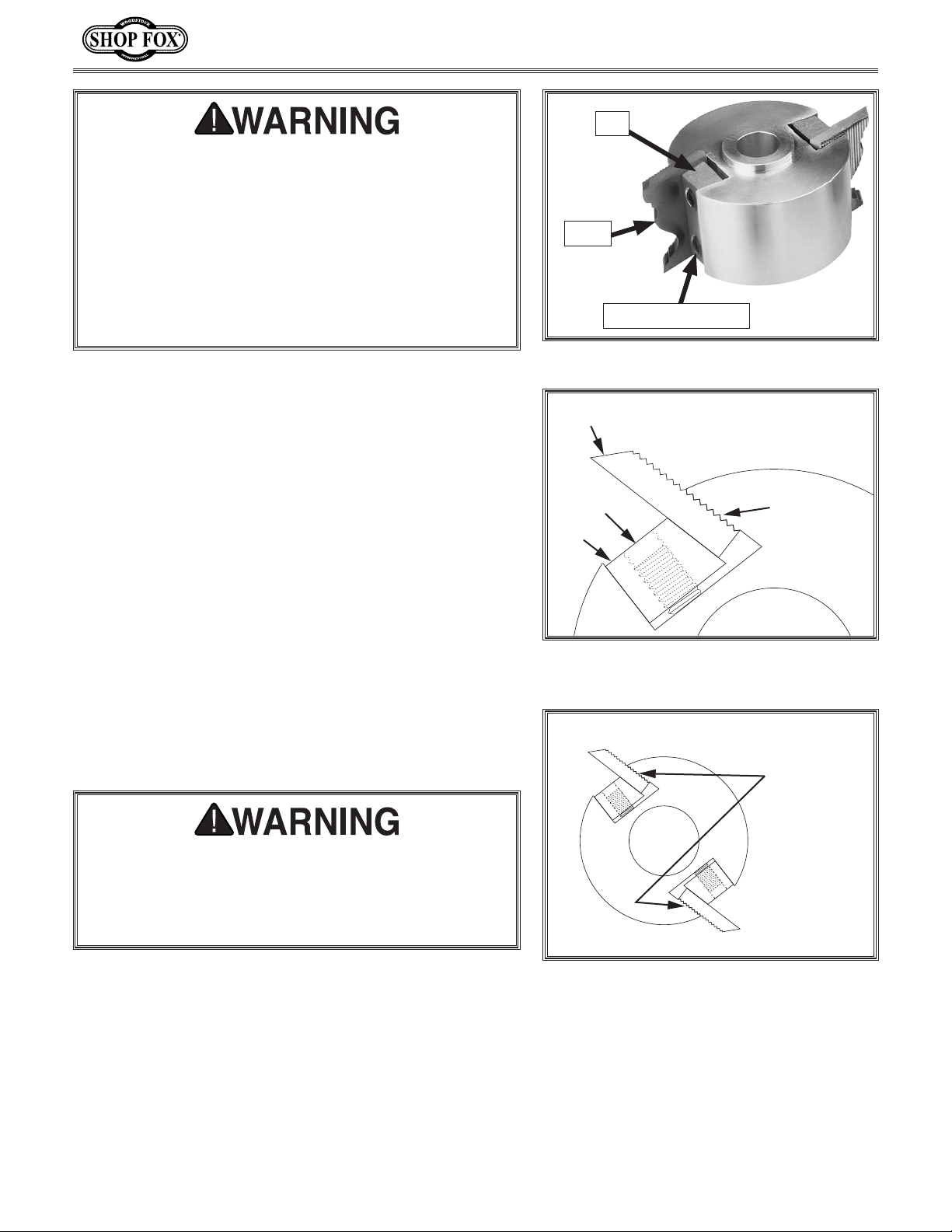
• DISCONNECT SHAPER FROM POWER before
installing or adjusting knife.
• Keep all guards and anti-kickback devices in
place.
• Double-check moulding head to insure it is tight
and secure in spindle.
• Always inspect lumber and other wood materials
for cracks, knots, or other imperfections that
could cause lumber to kick or shatter while
shaping.
Installing Knives
3
1. Thread (2) included
(see Figure 2) so set ends of screws are flush with
bottom of gib.
⁄8"-16 x 1⁄2" set screws into gib
D1700/D1701 Moulding Head (Mfd. Since 10/94)
Gib
Knife
Set Screw (1 of 2)
Figure 2. Knife installed in moulding head.
Knife
(Top View)
2. While holding gib in moulding head, slide knife
corrugations into moulding head corrugations and
center knives on moulding head body. Make sure all
corrugations are engaged (see Figure 3).
3
3. Tighten set screws with a
⁄16" hex wrench, but DO
NOT over-tighten. Use only enough force to secure
knife snugly in position, so you can adjust knives in
next section.
4. Repeat Steps 1–3 to insert second knife in moulding
head. Make sure position of corrugations on first and
second knives is the same (see Figure 4) so both
knives are an equal height.
Improperly secured knives can fly out of moulding
head and hit operator or bystanders, causing
serious personal injury. Recheck all adjustments and
tightening sequences, and ensure both knives are
properly secured before installing moulding head.
Set Screw
Corrugations
Engaged
Gib
Moulding
Head
Figure 3. Moulding head corrugations
engaged.
Corrugations
Match
If you need help with your new moulding head, call our
Technical Support at: (360) 734-3482.
-2-
Figure 4. Position of knife corrugations
match.