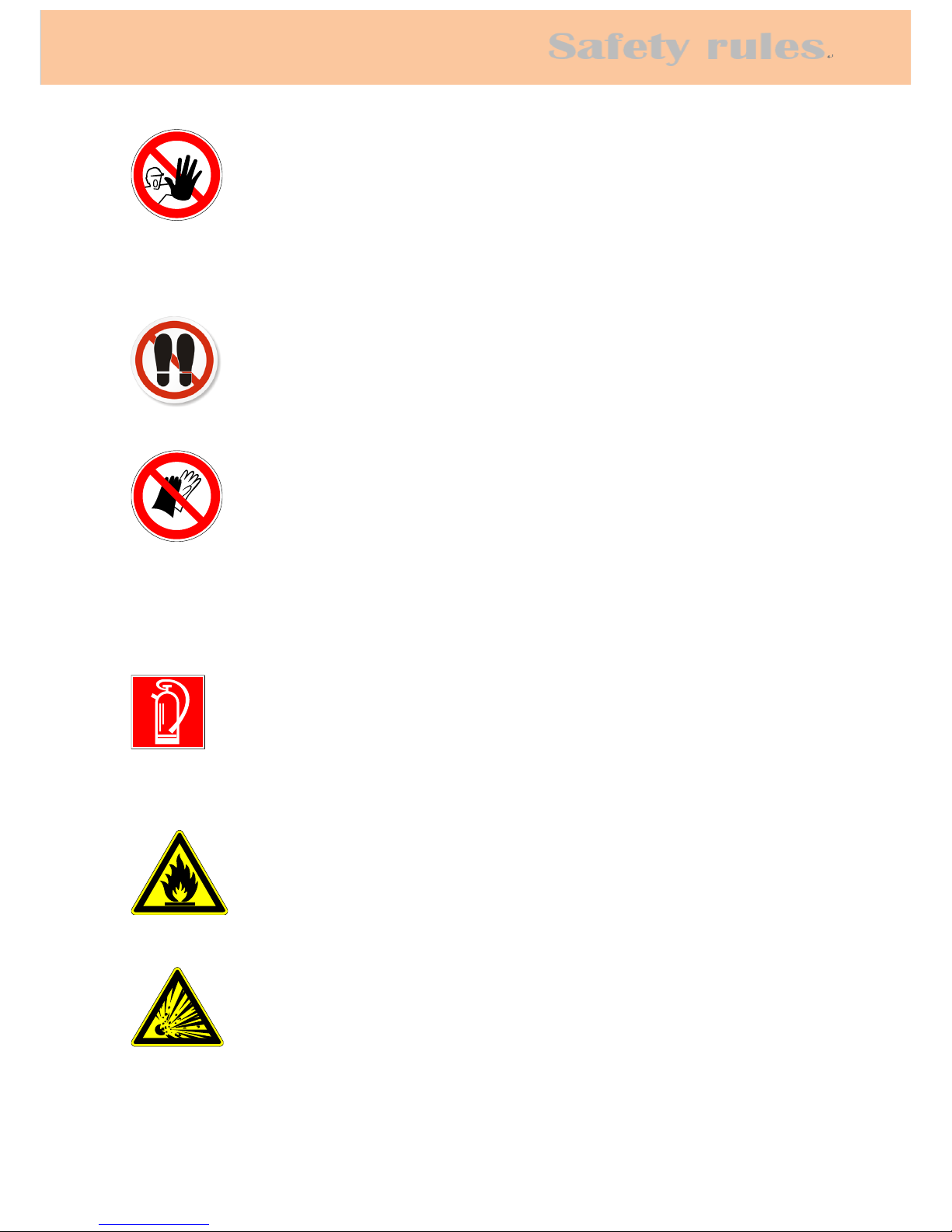
Make sure your work area is cleared of uninvited people and obstacles every
time before you start operating the machine.
Never step or stand on the roller table. Your foot may slip or trip on the rollers
and you will fall.
Never wear gloves or loose clothing when operating the machine. It may lead
to serious injury if they are caught in the running machine. Wrap or cover
long hair.
Never touch the running saw blade with gloves or not. It is dangerous if your
hands, clothing or gloves are caught by the running blade.
Make sure any use of fire is prohibited in the shop and install a fire
extinguisher or other fire control device near the machine when cutting
titanium, magnesium, or any other material that produces flammable chips.
Never leave the machine unattended when cutting flammable materials.
Use a water-soluble cutting fluid on this machine. Oil-based cutting fluids
may emit smoke or catch fire, depending on how they are used.
Never cut carbon or any other material that may produce and disperse
explosive dust. It is possible that sparks from motors and other machine parts
will ignite and explode the air-borne dust.
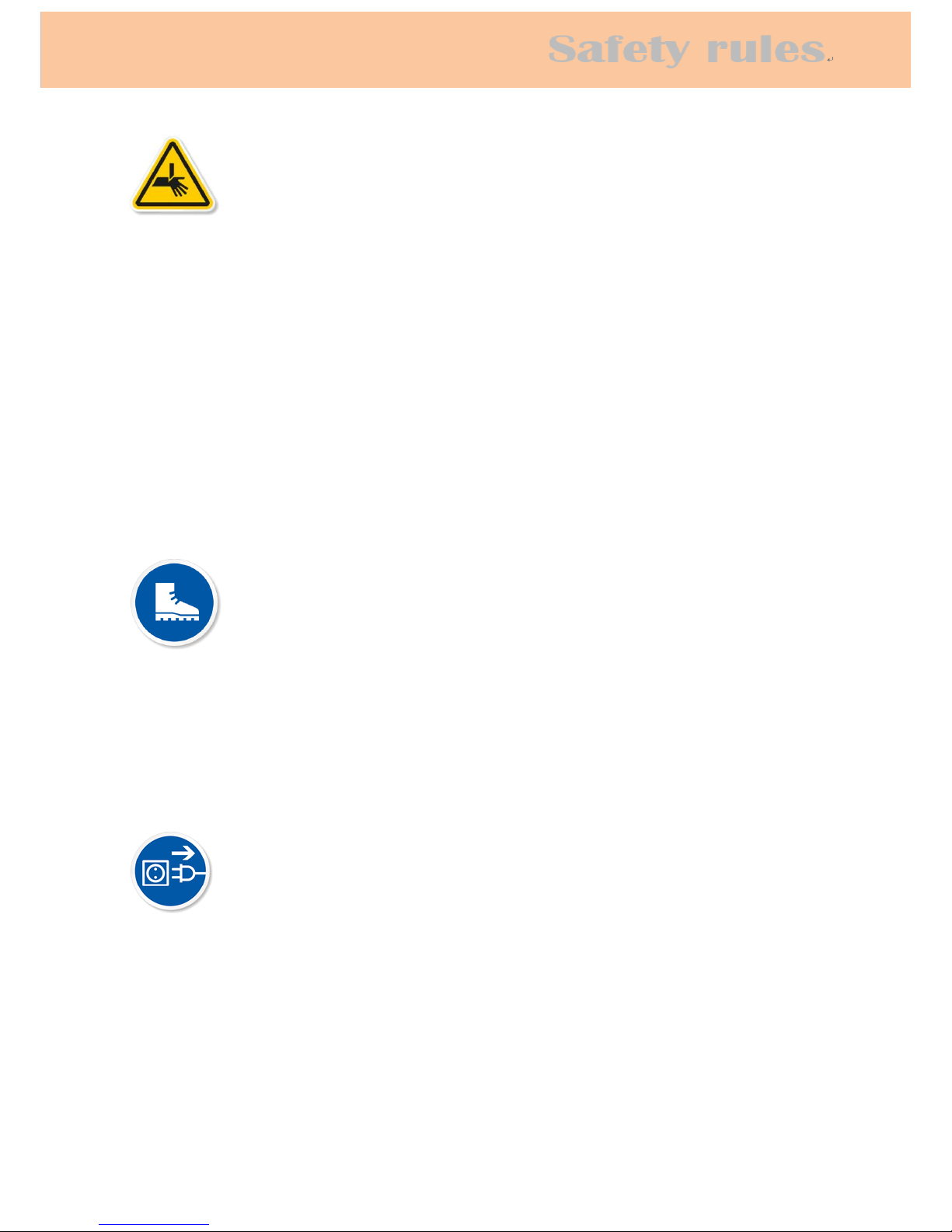
Never adjust the wire brush or remove chips while the saw blade is still
running. It is extremely dangerous if hands or clothing are caught by the
running blade.
Stop the saw blade before you clean the machine. It is dangerous if hands or
clothing are caught by the running blade.
Never start the saw blade unless the workpiece has been clamped firmly. If
the workpiece is not securely clamped, it will be forced out of the vise during
cutting.
Take preventive measures when cutting thin or short pieces from the work to
keep them from falling. It is dangerous if the cut pieces fall.
Use roller tables at the front and rear sides of the machine when cutting long
work. It is dangerous if the work piece falls off the machine.
Turn off the shop circuit breaker switch before performing maintenance on
the machine. Post a sign indicating the machine is under maintenance.
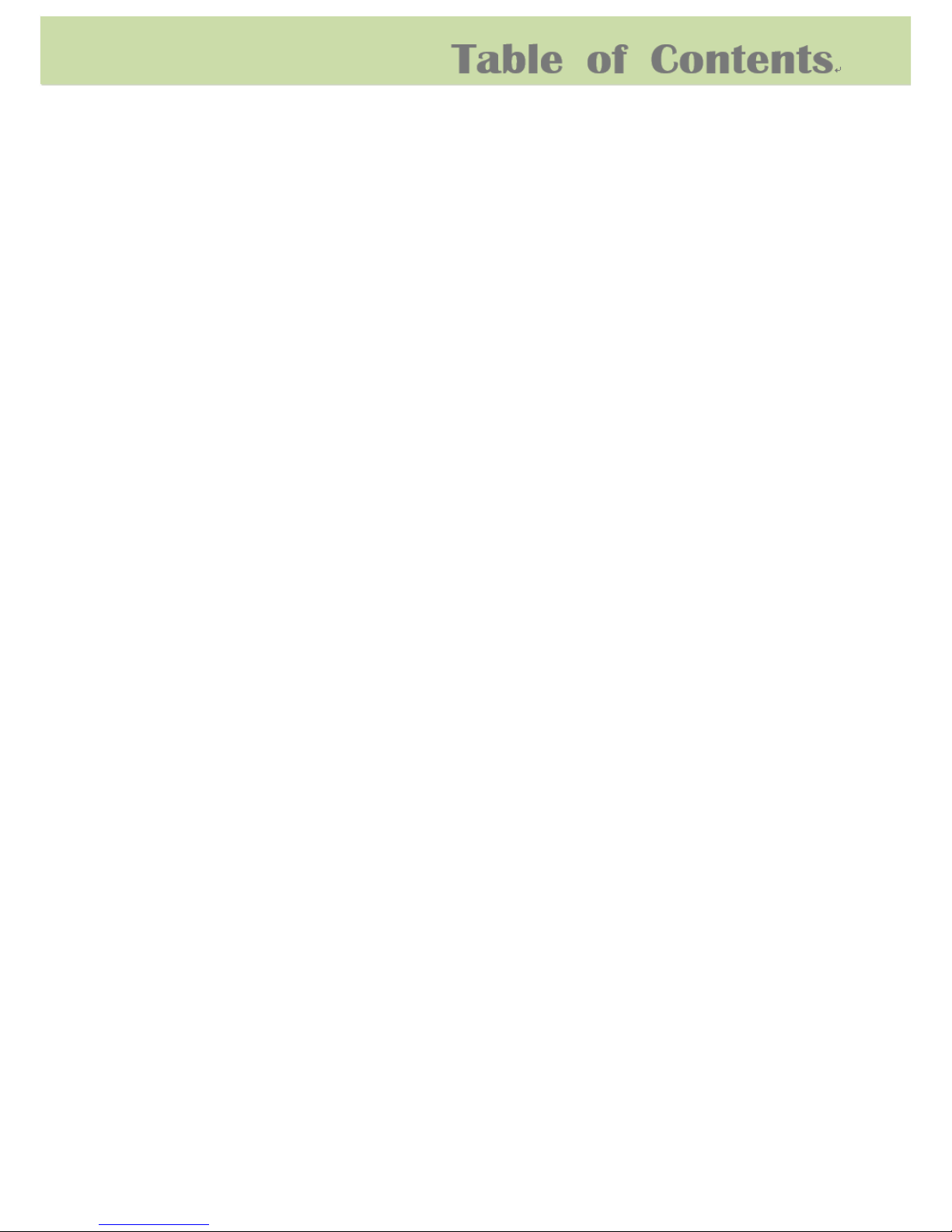
Section 1 – Safety Information
Safety Instructions ……………………………………………………………………………………………………...
1-1 Safeguard Devices ……………………………………………………………………………………………………….
1-3 Emergency Stop ………………………………………………………………………………………………………….
Illustration: Emergency Stop ………………………………………………………………………………………
1-5 Safety Labels ……………………………………………………………………………………………………………….
Illustration: Safety Labels ………………………………………………………………………………………..…
1-9 Hearing Protection ………………………………………………………………………………………………………
CE Compliance …………………………………………………………………………………………………………….
Risk Assessment ………………………………………………………………………………………………………….
Section 2 – General Information
Specification ……………………………………..………………………………………………………………………..
2-2 Machine Parts Identification ……………………………………………………………………………………….
2-3 Floor Plan …………………………………………………………………………………………………..……………….
Section 3 – Moving & Installation
Location & Environment ………………………………..……………………………………………………………
Unpacking & Inspecting ……..……………………………………………………………………………………….
3-2 Lifting …………………………………………..………………………………………………………………….………….
Illustration: Lifting Points ………………………………………………………….……………………….
3-5 Removing Shipping Bracket …………………………..……………………………………………….……………
3-6 Cleaning …………………………………………..…………………………………………………………….……………
3-6 Installing …………………………...………………………………………………………………………….…………….
Supplying Hydraulic Oil …………………………………………………………………….…………….
Supplying Coolant ………..………………………………………………………………….……………..
Connecting Electric Power ……………………………………………………………….……………..
Leveling & Anchoring …………………………………………………………………….……………….
Installing Roller Table (Optional) ………………………………………………….………………….
Installing Fire Control Device……………………………………………………………………………
3-9 Relocating ………………………...…………………………………………………………………….………………….
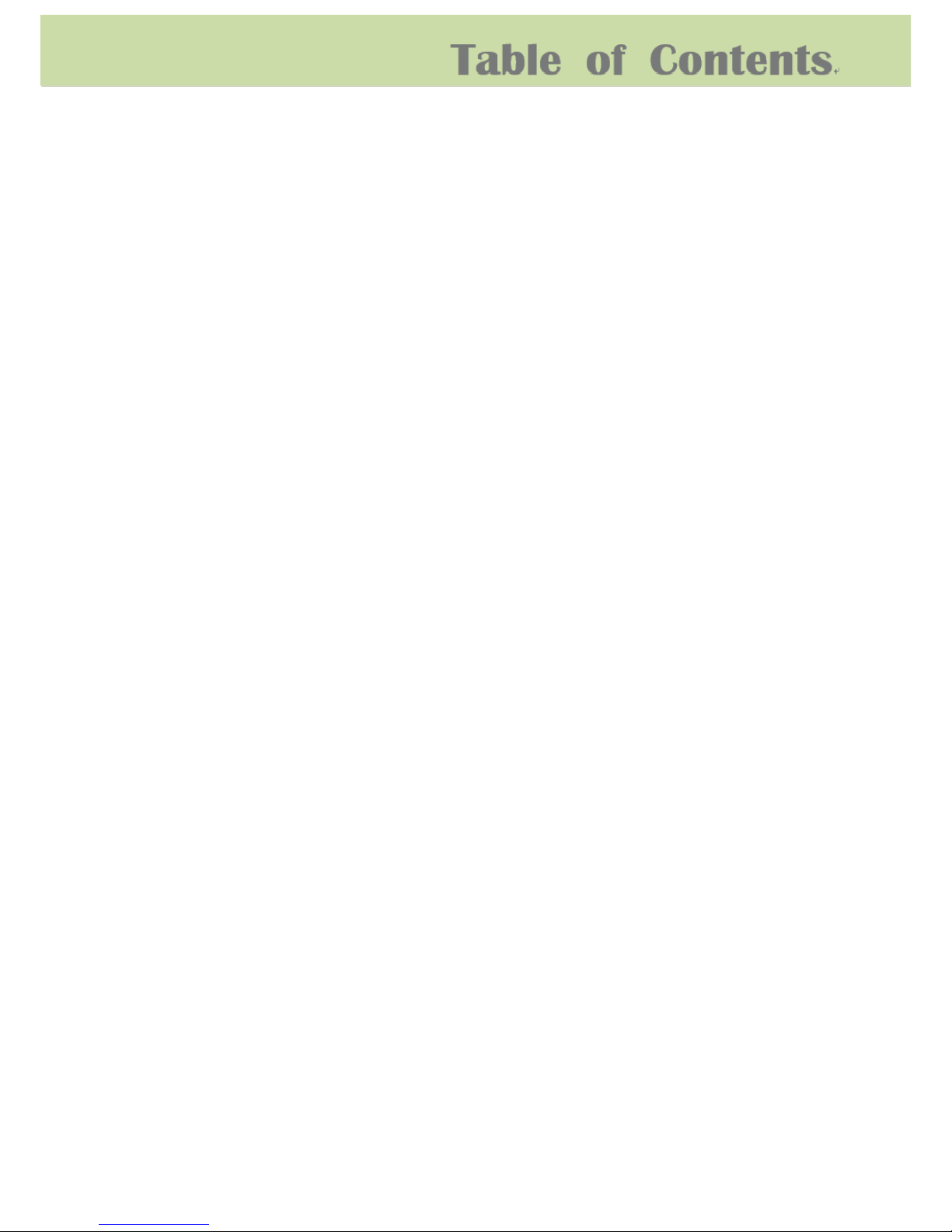
Section 4 – Operating Instructions
Safety Precautions …………………..…………………..……………………………………….…………………….
4-2 Before Operating …………………………..…………………………………………………………………………….
4-3 Control Panel ……..……………………………………..………………………………………….…………………….
Control Panel ………………….………………………………………………………………………..…….
Control Buttons ……………………………………………………………………………………….……..
4-4 Cutting Operation ………..………..……………………………………………..…………………………………….
Selecting Blade Speed …………………………………………………………………………………….
Changing Blade Speed – 4 Speed Step Pulley ………………………………………………….
Selecting Blade ……………………………………………………………………………………………….
Adjusting Feed Rate (Cutting Pressure) ……………………………………………………………
Adjusting Vise …………………………………………………………………………………………………
Angle Cutting ………………………………………………………………………………………………….
4-7 Adjusting Coolant Flow ………..………..…………………………………………………………………..……….
Installing Material Stop Bracket …………………………………………………………………………………..
Unrolling & Installing the Blade …………………………………………………………………….…………….
Adjusting Blade Tension ………..………..…………………………………………………………………………..
Adjusting Wire Brush ………..……………………………………………………………………….……………….
Adjusting Saw Arm……………..……………………………………………………………………….………………
Adjusting Horizontal Stop Spring Cushion ……………………………………………………………………
Section 5 – Electrical System
Electrical Circuit Diagrams ……….…………………..……………………………………………………………..
Section 6 – Hydraulic System
Hydraulic Diagrams ……….…………………..………………………………………………………………………..
Section 7 – Bandsaw Cutting: A Practical Guide
Introduction ……………………….…….…………………..…………………………………………………………….
7-2 Saw Blade Selection ………………….…………………..……………………………………………………………
VISE LOADING …………….…………………..………………………………………….………………………………
BladeBreak -In …………………………………………………………………………………….……………………..
Section 8 – Maintenance & Service
Introduction ……………………….…….…………………..…………………………………………………………….
Basic Maintenance ………………….…………………..…………………………………………….……………….
Maintenance Schedule …………….…………………..…………………………………………………………….
Before Beginning a Day’s Work ……………………………………………………………………….
After Ending a Day’s Work …………………………………………………….………………………..
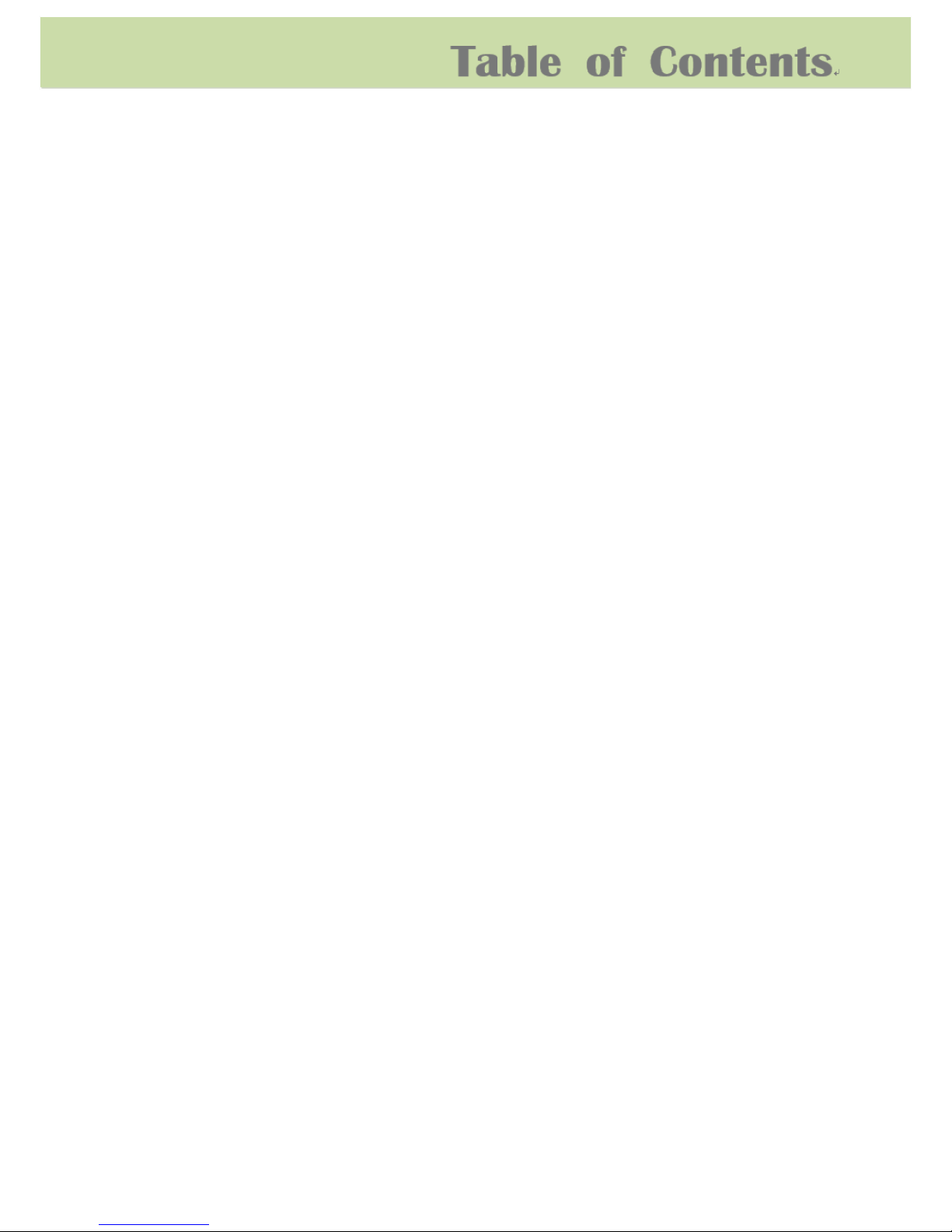
Every 2 weeks …………………………………………………………………….……………………….
First 600hrs for new machine,then every 1200h…………………….……………………….
Every Six Months ……………….………………………………………………….……………………….
8-3 Storage Conditions …………………………....………..……………………………………………………………..
8-3 Terminating the Use of Machine ……..…………..……………………………………………………………..
8-3 Oil Recommendation for Maintenance ……………………………………………………………………….
Section 9 – Troubleshooting
Introduction ……………………….…….…………………..…………………………………………………………….
9-1 Precautions ………………….…………………..…………………………………………………………………….....
9-2 General Troubles & Solutions ………………………..…………………………………………………………….
9-2 Minor Troubles & Solutions ………………………..………………………………………………..…………….
9-3 Motor Troubles & Solutions ………………………..…………………………………………………..………….
9-3 Blade Troubles & Solutions ………………………..………………………………………………………………..
9-4 Sawing Problems & Solutions ………………………..……………………………………………………………
Re-Adjusting the Roller Table ………………………..…………………………………………………………….
Spare Parts Recommendations …………………..……………………………………………………………….
Part List …………………..………………………………………………………………………………………………….
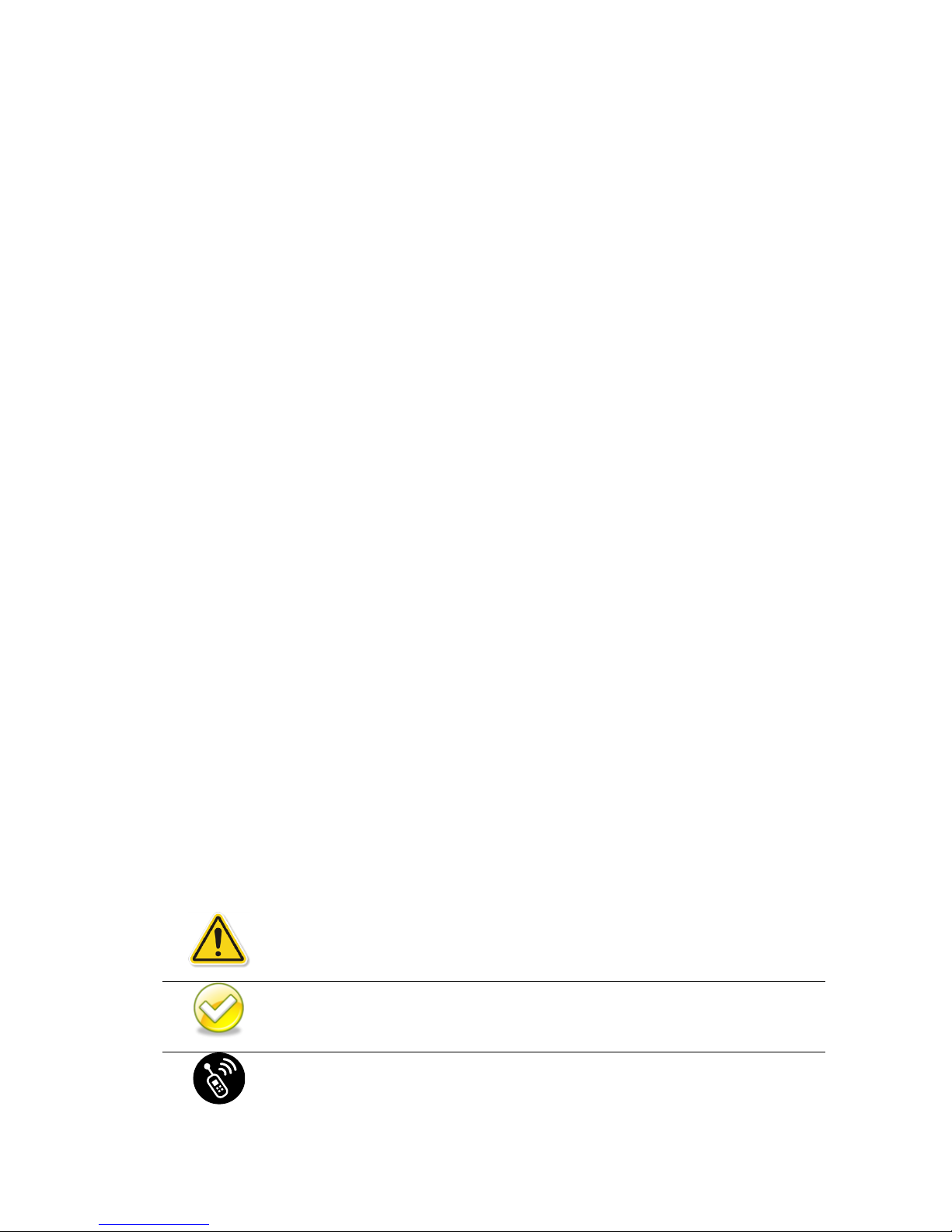
Section 1
SAFETY
INFORMATION
SAFETY INSTRUCTIONS
SAFEGUARD DEVICES
EMERGENCY STOP
SAFETY LABELS
HEARING PROTECTION
CE COMPLIANCE
RISK ASSESSMENT
Safety is a combination of a well-designed machine, operator’s knowledge about the machine and
alertness at all times. This band machine has incorporated many safety measures during the design
process and used protective devices to prevent personal injuries and potential risks. Warning labels also
serve as a reminder to the operator.
Throughout this manual, you will also see various safety-related symbols indicating important
information that you should take note of prior to use of the machine or part of its functions. These
important safety instructions do not cover all possible situations that might occur. It is your responsibility
to take caution and follow procedures stated in this manual when installing, maintaining and operating
your machine.
SAFETY INSTRUCTIONS
What the icons and signs in this user manual mean:
This icon marks WARNING; hazards or unsafe practices that may result in
personal injury or damage to the machine.
Supplementary information to the procedures described in this manual.
Call your local agent or our service center for help.

This manual has important safety
information. Read through it carefully
before operating this machine to prevent
personal injury or machine damage.
Learn the operation, limitation and the
specific potential hazards peculiar to this
band saw. All users must read it before
performing any activity on the machine,
such as replacing the saw band or doing
regular maintenance.
Do not operate this machine unless it is
completely assembled.
Keep all guards and shields in place
before installing or starting up the
machine.
Keep blade protection cover and wheel
covers in place and in working order.
Make sure the power switch is off before
plugging in power cord.
Disconnect the power cord before
making adjustment, maintenance or
blade changes.
Always remember to switch off the
machine when the work is completed.
Keep unauthorized personnel away.
Use recommended accessories.
Improper accessories may be hazardous.
Never hold the material by hand for
cutting. Always use the vise and make
sure the material is clamped securely
before cutting.
When a workpiece is too long or heavy,
make sure it is supported with a roller
table (recommended).
Do not use the machine to cut explosive
material or high pressure vessels as it
will generate great amount of heat
during the sawing process and may
Wear proper apparel during operation
and when servicing the machine. Some
personal protective equipment is
required for the safe use of the machine,
e.g. protection goggles.
Never operate while under the influence
of drugs, alcohol or medication.
Do not reach over or stand on any part
of the machine.
It is dangerous to operate the machine
when the floor is slippery. Keep the floor
clean and dry. Check for ice, moisture, or
grease before entering.
Keep the work environment safe. Do not
use band saw in a damp or wet location.
Keep your work area clean. Cluttered
and slippery floors invite accidents.
Keep your work area well illuminated at
minimum 500 lumen.
Remove adjusting keys, wrenches or any
loose parts or items from the machine
before turning on power.
Moving parts should be kept in proper
alignment and connection with the
machine. Check for breakage, mounting
and any other conditions that may
affect its operation. Any damaged part or
guard should be properly repaired or
replaced.
Use a sharp saw blade and keep the
machine in its best and safest
performance by following a periodical
maintenance schedule.
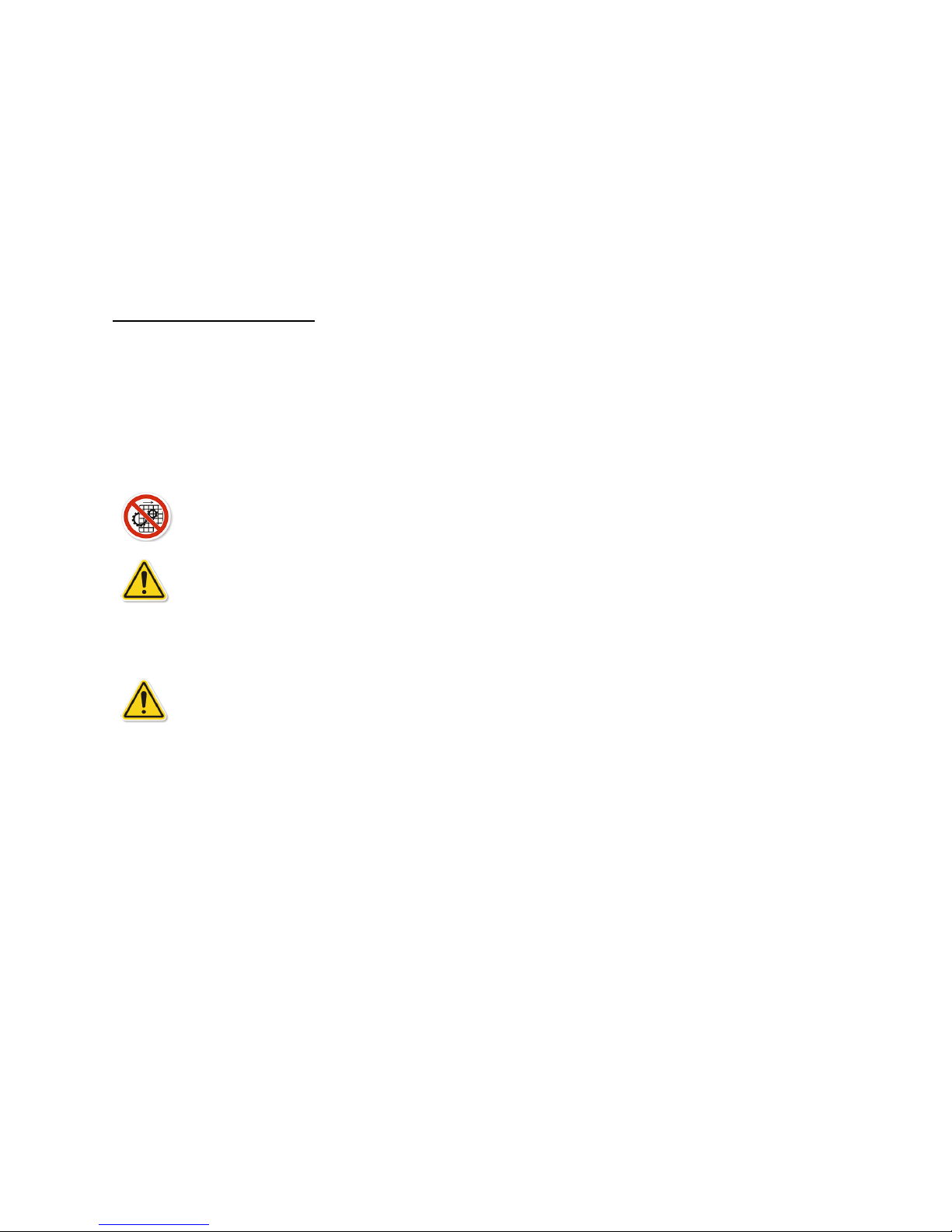
SAFEGUARD DEVICES
The safeguard devices incorporated in this machine include the following two main parts:
1. Protection covers & guards
2. Safety-related switches
Protection Covers & Guards
1. Idle wheel housing cover
2. Drive wheel housing cover
3. Gear reducer cover
4. Wire brush belt cover
5. Blade guard cover (left & right)
The protection devices should always be mounted on the machine whenever the machine is running.
Do not remove any of these safeguard devices under any circumstances except when servicing the
machine. Even skilled service technicians should still take cautions when performing repairs or service on
the machine with any of these protectors removed. It is the responsibility of the user to make sure all
these elements are not lost and damaged.
Take note of the following main moving parts on the machine prior to and during machine operation:
Saw bow assembly
Drive and idle wheels
Blade guide arm
Saw blade guide rollers
Quick approach device (optional)
Wire brush
Chip conveyor (optional)
Workpiece clamping vises
Shuttle vises and workbed rollers
Top clamps (optional)
Gear reducer

Safety Related Switches
To protect the operator, the following safety related switches on the machine are actuated when the
machine is in operation.
This is a proximity sensor used to detect the motion
of the drive wheel. Once the saw blade is broken or
as soon as it starts slipping, the sensor will detect
and stop the drive wheel and the machine.
Located on the cover of electrical cabinet, the power
switch controls the main power of the machine. Up
to your company’s internal rules, this power switch
can be locked with a padlock or a luggage lock to
protect the operator and the machine.
Located on the control panel, the button when
pressed will stop the machine completely.
This switch assures firm clamping of the workpiece. If
the workpiece is not clamped properly, the saw blade
is not allowed to run.
Wheel cover interlock switches
(CE model only)
Located on the two wheel housings, these switches
are used to assure that the machine will stop
whenever the wheel covers are open. This device is
to protect users from being cut by the running saw
blades.
Among all these safety switches, some of them are used to protect the users and some of them are used
to prevent damage to saw blades, the workpiece and the machine itself, etc. We have taken every
precaution to prevent injury or damage and to provide safe and economical operation of the machine.
EMERGENCY STOP
Designed to be easily accessible, the emergency stop button is located on the left bottom corner on the
control panel and is made in red color and rubber material. For CE models, supplementary emergency
stop button may be available at other area(s) of the machine depending on machine type. Please refer
to Illustration: Emergency Stop.
When you press the button, the machine will immediately come to a full stop to avoid injury or damage
when an accident occurs. The button will be locked when you press it. To unlock it, turn the button
clockwise.
You should press it immediately without any hesitation when observing:
An emergency situation that would cause any injury or damage
An abnormal situation or problem such as fire, smoke, abnormal noise and etc.
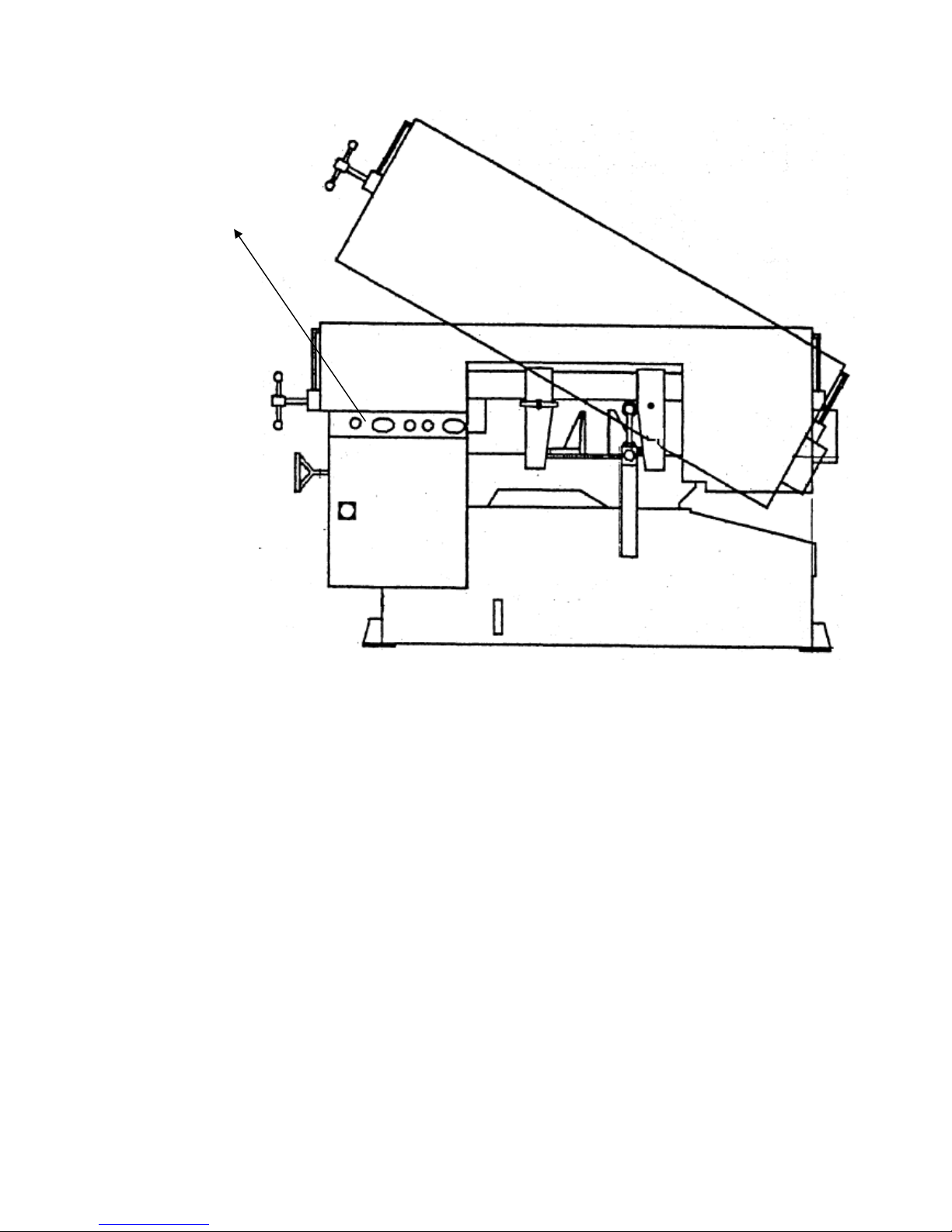
Illustration: Emergency Stop
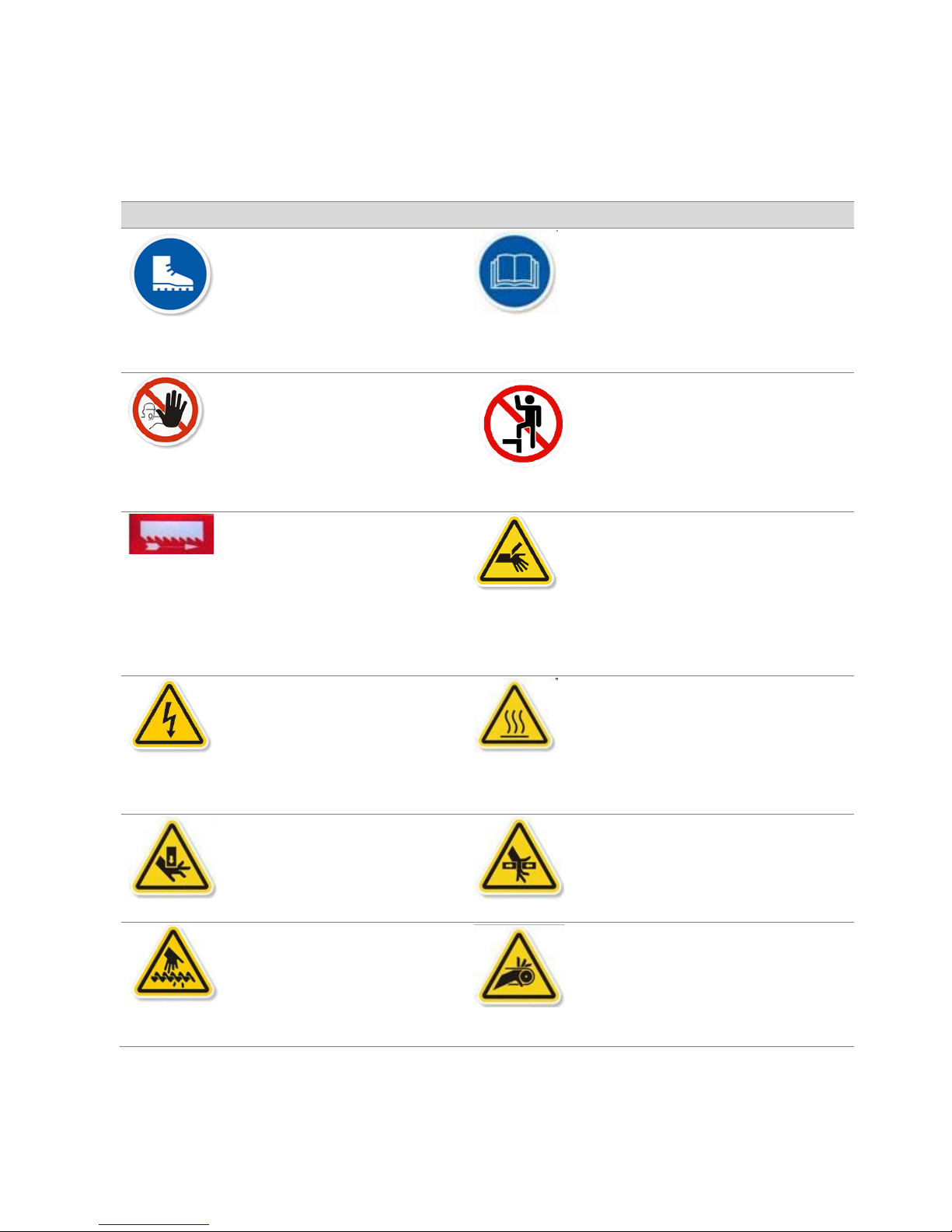
SAFETY LABELS
Please read through and understand them before operating the machine. Refer to Illustration: Safety
Labels.
Impact Hazard
WEAR SAFETY SHOES. Do
not approach dropping area
during operation.
Read Operator’s Manual
This manual has important safety
information. Read through it
carefully before operating this
machine to prevent personal injury
or machine damage.
Keep Unauthorized
Personnel Away
Do not step.
Do not stand on the machine or on
the accessories!
DANGER: Running Blade
Blade runs through this
area. Keep your hands away
from a running blade to
avoid severe injury. The
arrow indicates direction of
the blade.
Cutting Hazard
KEEP COVER CLOSED / KEEP HAND
OFF while the blade is running. Turn
power off before opening cover.
Failure to follow the warning can
result in severe injury.
Hazardous Voltage
TURN POWER OFF before
servicing. Failure to
following the warning can
result in severe injury.
Hand Crush/Force from
Above
Loose Hand Hazard
KEEP HAND OFF. Do not
touch chip conveyor. Failure
to follow the warning can
result in severe injury.
Pinch Point/Hand Entanglement
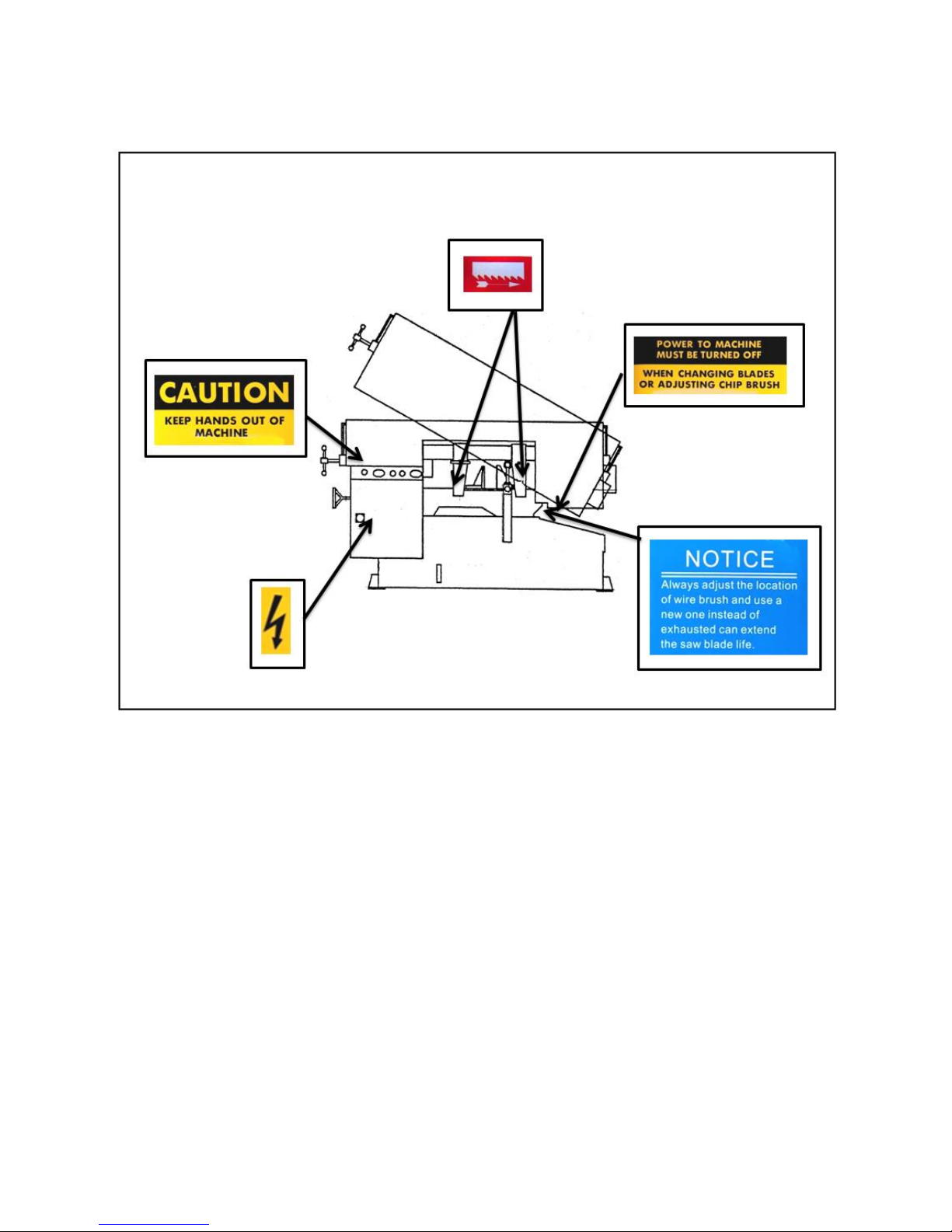
Illustration: Safety Labels
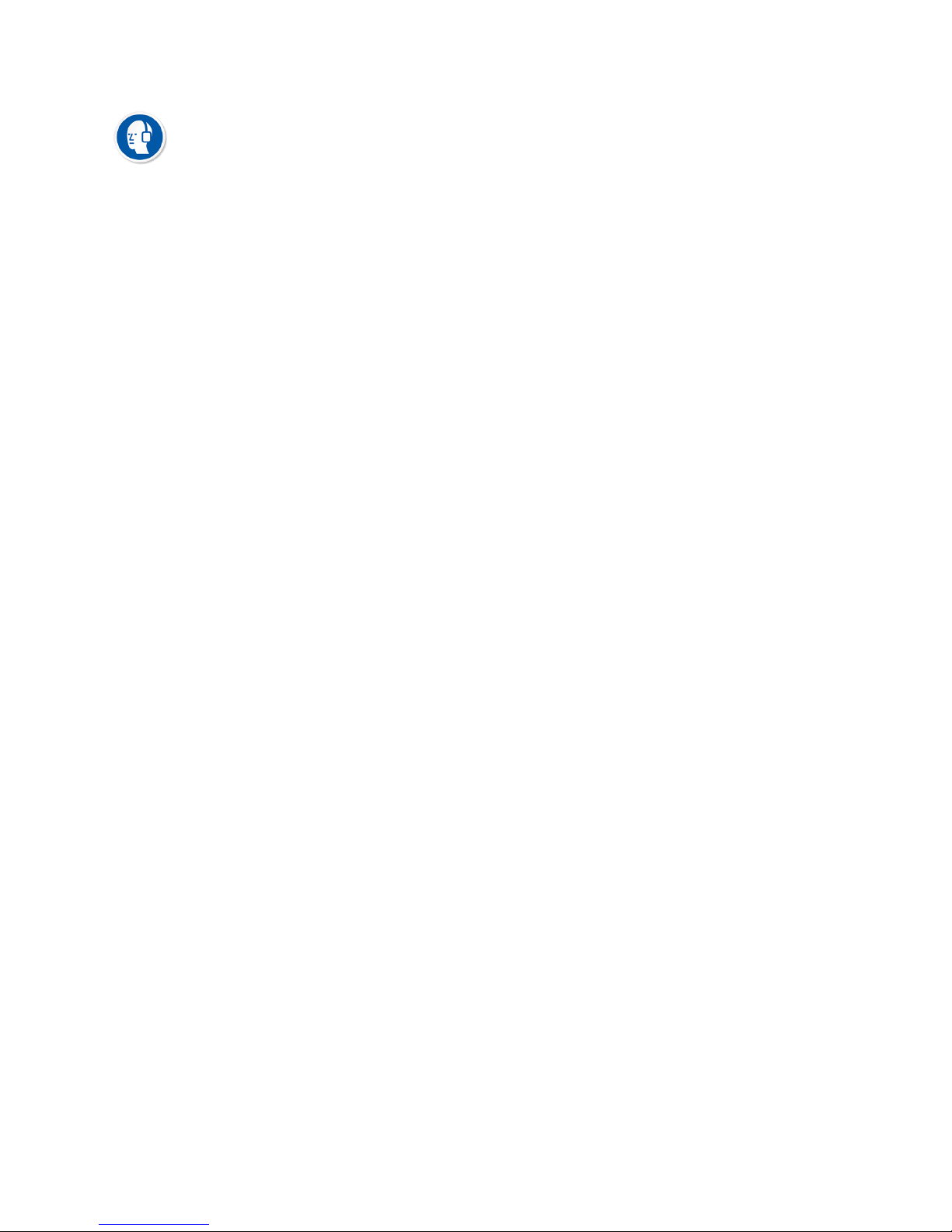
HEARING PROTECTION
Always use ear protection!
When your machine is running, noise generated by the machine may come from the following:
Saw blade during cutting or material feed mechanism
Wire brush unit
Chip conveyor unit
Speed reducer
Hydraulic motor/pump
Belt transmissions variable speed motors
Blade motor
Coolant pump
Drive wheel
Parts not assembled tightly causing mechanical vibration
Our products pass noise testing less than 78 dBA. Noise level vary according to working conditions and
we recommend ear plugs or other hearing protection at all time. If your machine produces an
undesirable noise while it is running, you should:
1. Make sure all maintenance tasks have been performed following the prescribed maintenance
schedule (Refer to Section 6).
2. If maintenance does not seem to solve the problem, follow the troubleshooting procedures under
Section 7.
RISK ASSESSMENT
Risk assessment generally takes account of intended use and foreseeable misuse, including process
control and maintenance requirements. We made every effort to avoid any personal injury or equipment
damage during the machine design stage. However, the operator (or other people) still needs to take
precautions when handling any part of the machine that is unfamiliar and anywhere on the machine
that has potential hazards (e.g. the electrical control box).

Section 2
GENERAL
INFORMATION
SPECIFICATION
MACHINE PARTS IDENTIFICATION
FLOOR PLAN
This band saw machine is designed by our R&D engineers to provide you the following features and
advantages:
Safety
This machine is designed to fully protect the operator from its moving parts during cutting
operation.
The machine and each compoment has passed strict testing (Council Directive on the
approximation of the laws of the Member States relating to Machinery).
The machine will shut off automatically when the saw blade is broken, protecting both the
operator and the machine.
Convenience & High-Performance
The machine is designed in the way that the operation and adjustment can be easily
performed.
The machine will stop automatically when out of stock.
Dual valve system is designed to achieve optimal cutting performance with the simple setting
of feed rate and perspective cutting pressure for different material.
Durability
The intended life-span of the machine is counted based on regular daily operation. It is
calculated with the life expectancy of 10 years under normal operating condition and exact
attention to the maintenance schedule.
8 hours × 5 days × 52 weeks × 10 years = 20,800 hours
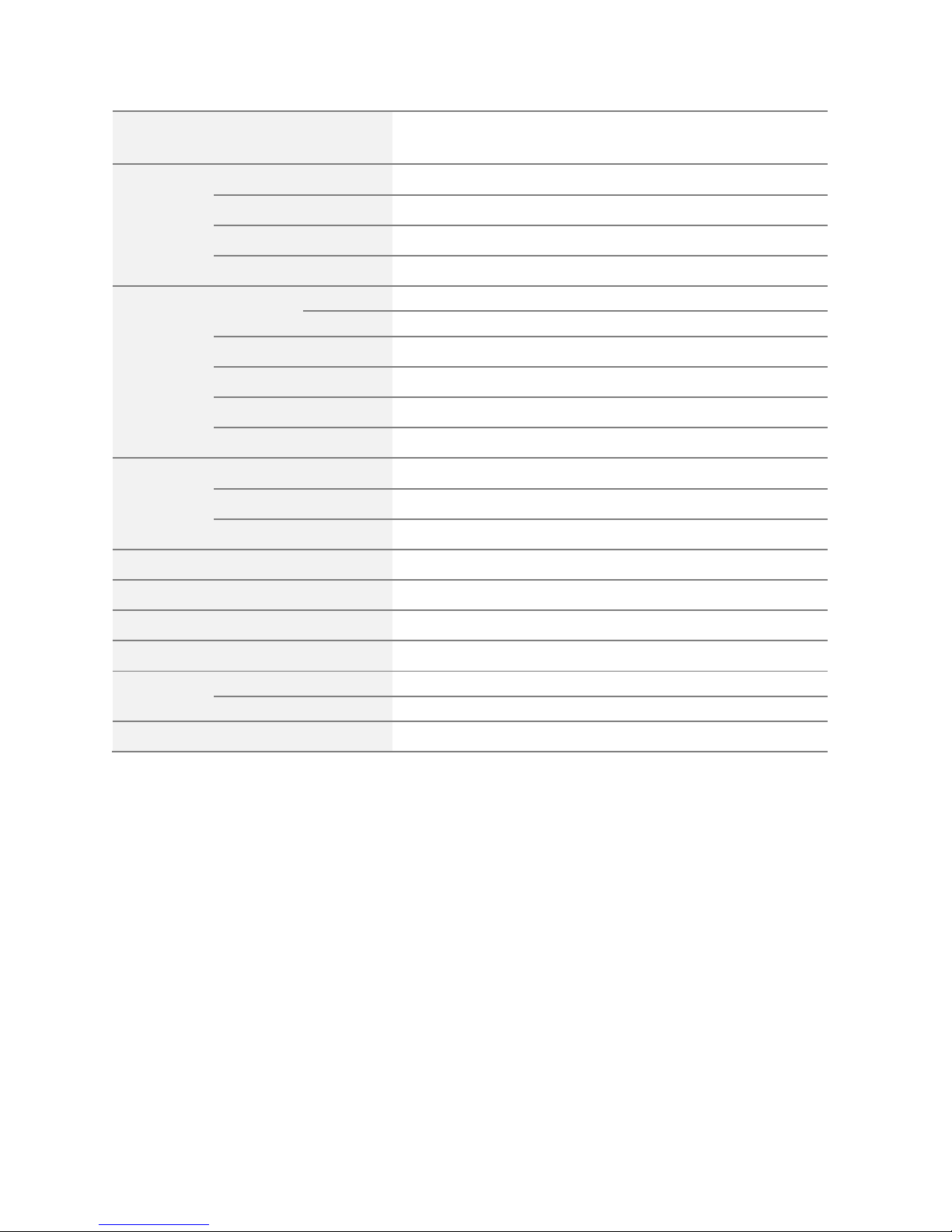
SW-100T
Semi-Automatic Horizontal Bandsaw
230 x 400 mm (9” x 15.7”)
190 x 190 mm (7.5” x 7.5”)
29, 46, 65, 98 m/min (95, 150, 213, 321fpm)
24, 38, 53, 81 m/min (78, 124, 173, 265 fpm)
3,350 x 27 x 0.9 mm (132” x 1.06” x 0.035”)
Hydraulic with automatic blade breakage detection
Interchangeable tungsten carbide
Steel wire brush with flexible drive shaft driven by main motor
1,700 x 1,100 x 1,400 mm (67” x 43.5” x 55.5”)
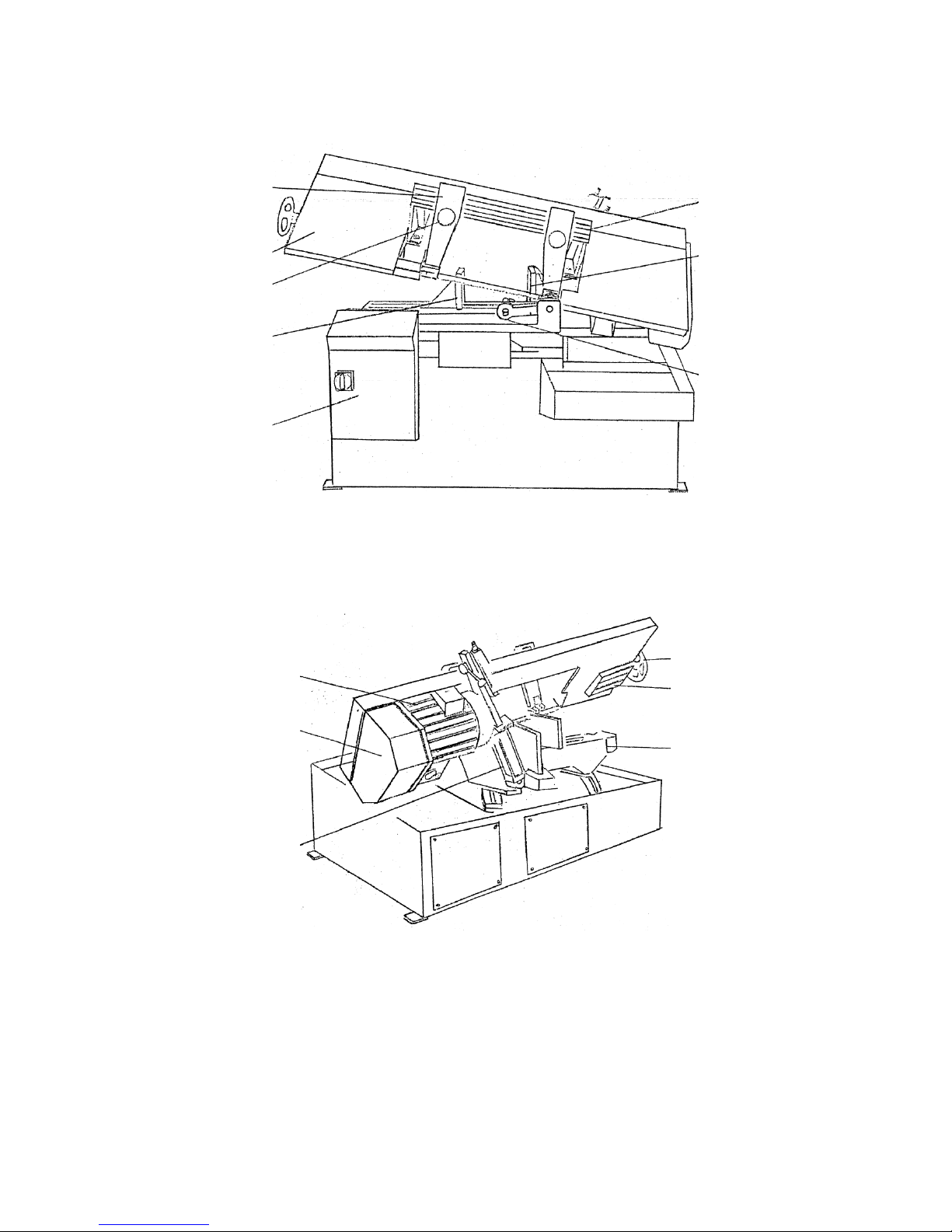
MACHINE PARTS IDENTIFICATION
Guide arm handle
Dovetail slide guide
Variable blade
speed control
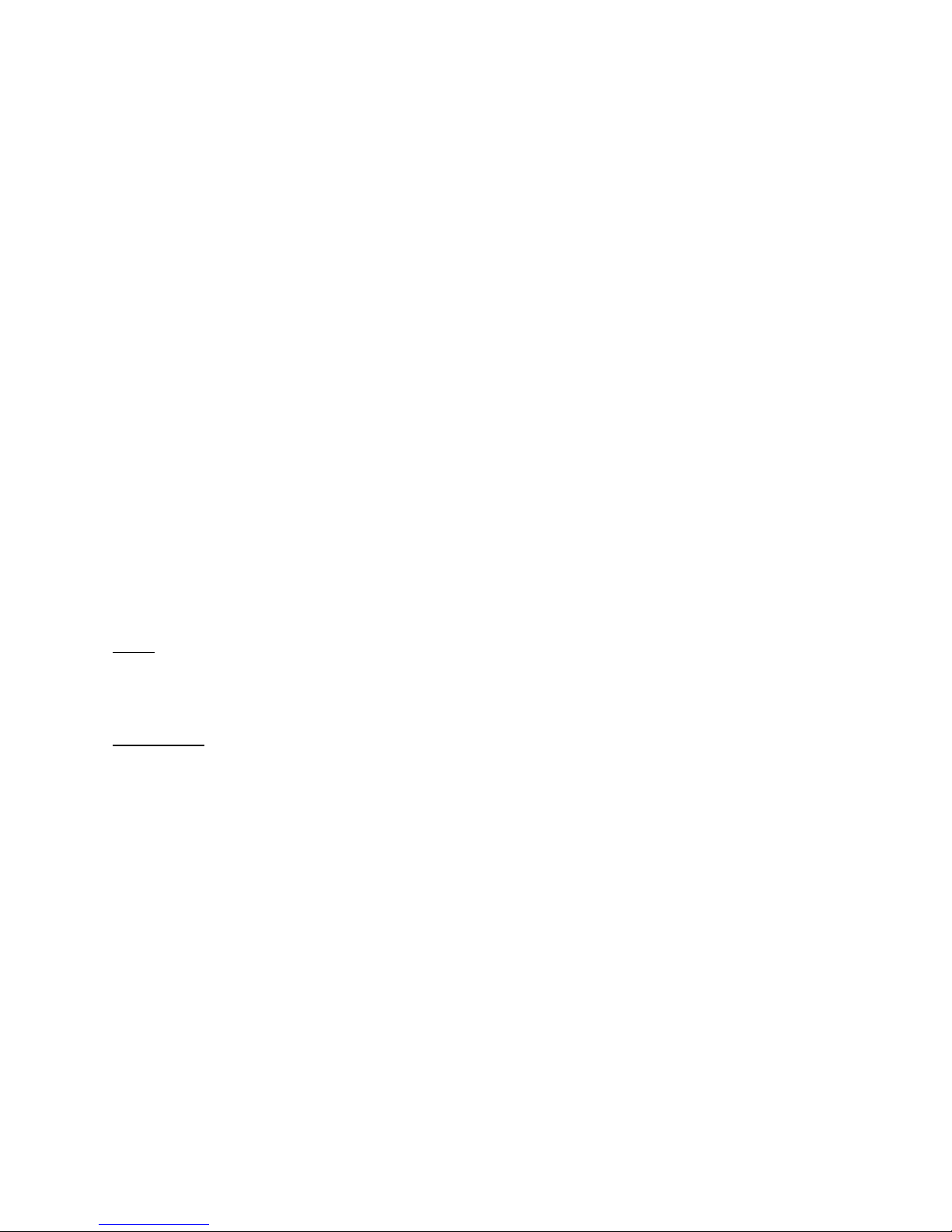
Section 3
MOVING &
INSTALLATION
LOCATION & ENVIRONMENT
UNPACKING & INSPECTING
LIFTING
REMOVING SHIPPING BRACKET
CLEANING
INSTALLING
RELOCATING
LOCATION & ENVIRONMENT
For your safety, please read all information regarding installation before proceeding. Install your machine
in a place satisfying all of the following conditions:
Space:
Leave enough free space around the machine for loading work and unloading cut-off pieces as
well as for maintenance and inspection. Refer to Section 2 General Informattion for machine
dimensions and floor space.
Environment:
Well lighted (500 lumen at minimum).
Floor kept dry at all times in order to prevent operators from slipping.
Away from direct exposure to the sunlight
Room temperature between 5˚C to 40˚C.
Humidity level kept at 30~95%“(without condensation) to avoid dew on electric installation
and machine.
Away from vibration of other machines
Away from powders or dusts emitted from other machines
Avoid uneven ground. Choose a solid level concrete floor which can sustain weight of both
machine and material.
Limit the operation area of the machine to staff only.
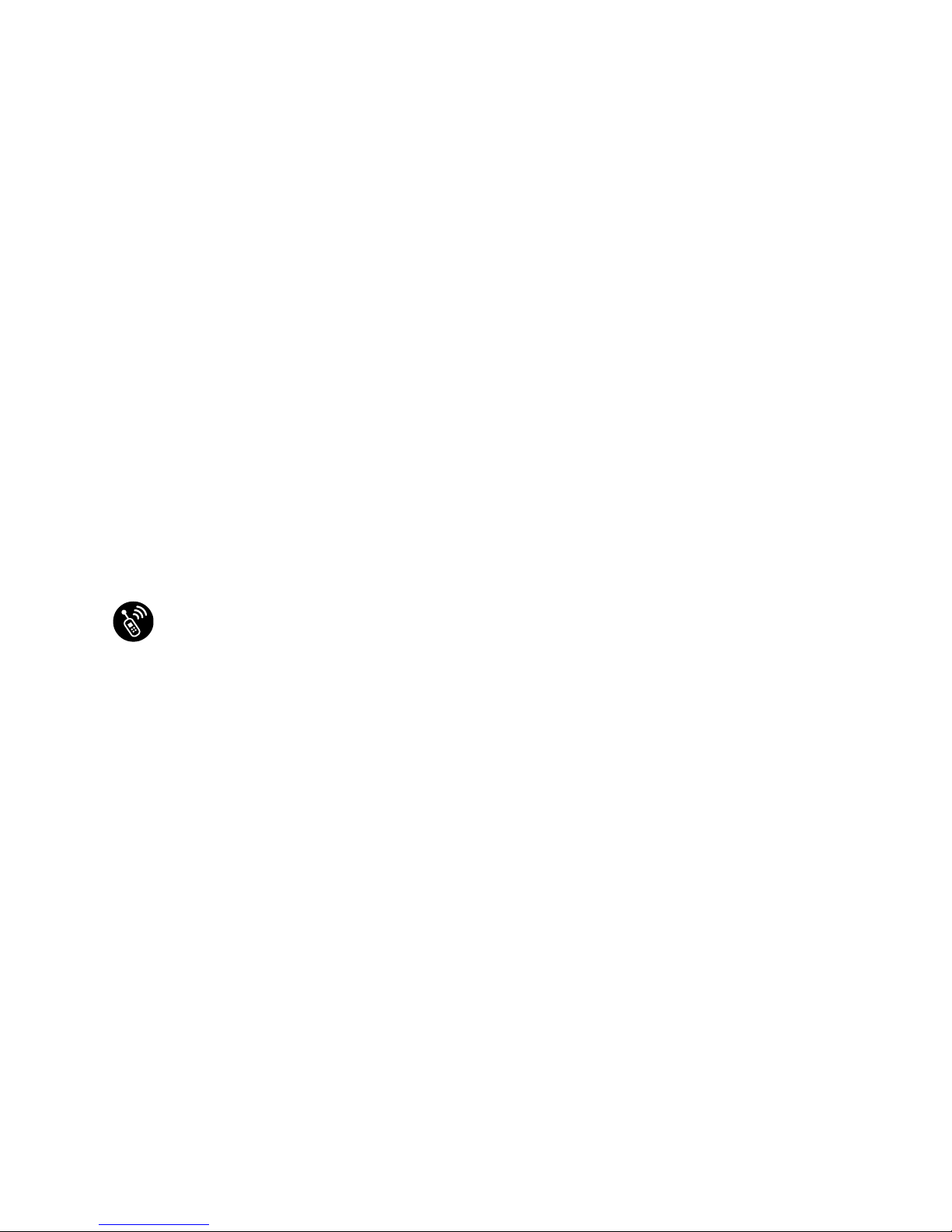
UNPACKING & INSPECTING
Unpack your machine carefully to avoid damage to machine parts or surfaces.
Upon arrival of your new band saw, please confirm that your machine is the correct model and it
comes in the same specification you ordered by checking the model plate on the machine base.
It is also imperative that a thorough inspection be undertaken to check for any damage that could
have occurred during shipping. Pay special attention to machine surface, equipments furnished and
the electrical and hydraulic systems for damaged cords, hoses and fluid leaks.
In the event of damage caused during shipping, please contact your dealer and consult about filing a
damage claim with the carrier.
Your machine comes in with a set of tools for you to maintain the machine. The accessories
furnished are as follows:
Chip spade (only for manual models)
Should you find any missing accessories, please contact your local agent immediately.
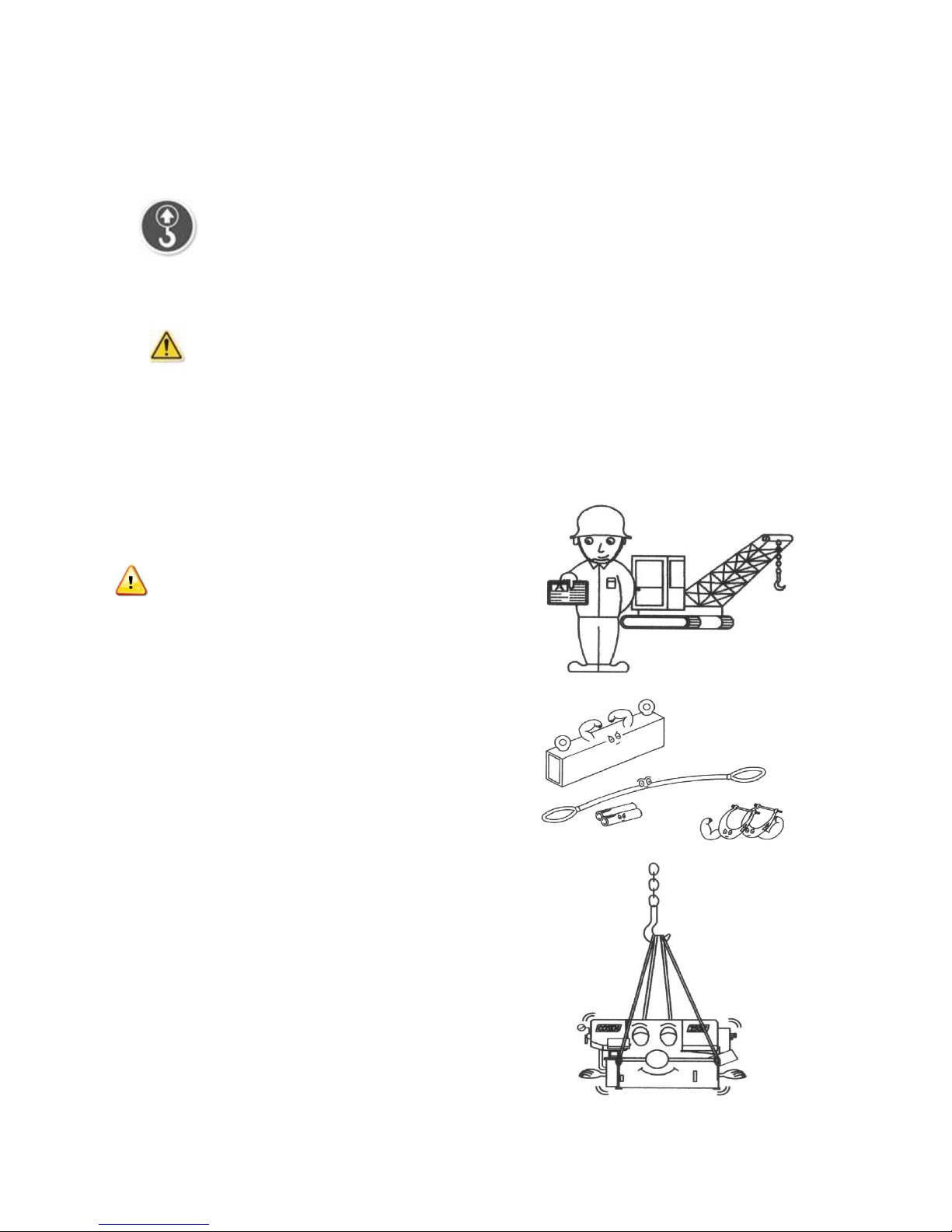
LIFTING
When moving the machine, we strongly suggest you choose any one of the methods described below to
move your machine.
1. (Only applies to the machine with the design of the hanging point.)
Move the machine to its location by using a crane and a wire rope sling that can fully withstand the
weight of the machine (refer to machine specification under Section 2 General Information).
Machine hanging with a crane should be done strictly according to the hanging points
designated by the original manufacturer. If there is any doubt on missing hanging points on your
machine, please consult with the original manufacturer or its qualified agent before hanging the
machine.
Machine lifting is likely to damage the machine
if not performed properly.
Warning: You must have a qualified crane
operator to perform the job.
You must use tools and equipment with the
proper tensile strength and use proper method
when moving your machine.
Apply the wire rope sling to the lifting hooks on
the four ends of the machine. Refer to
Illustration: Lifting Points for exact locations.
Slowly lift the machine. Be sure to protect the
machine from impact or shock during this
procedure. Also watch out your own fingers and
feet to avoid injuries.

Keep the machine well balanced during lifting
process and make sure the wire rope does not
interfere with the saw frame.
When you work together with more than two
people, it is best to keep constant verbal
communication with each other.
2. Use a forklift (Only applies to the machine with the design of the lifting point.)
Make sure that the lifting rod can fully withstand the weight of the machine. (Refer to Section 2 –
General Information for Specifications.)
Machine lifting with a forklift should be done strictly according to the lifting points
designated by the original manufacturer. If there is any doubt on missing lifting points on your machine,
please consult with the original manufacturer or its qualified agent before lifting the machine.
Machine lifting is likely to damage the machine
if not performed properly.
You must have a qualified forklift operator
to perform the job.
You must apply proper forklift technique to
avoid damage to the machine.
Make sure the forks are able to reach in
at least 2/3 of the machine depth.
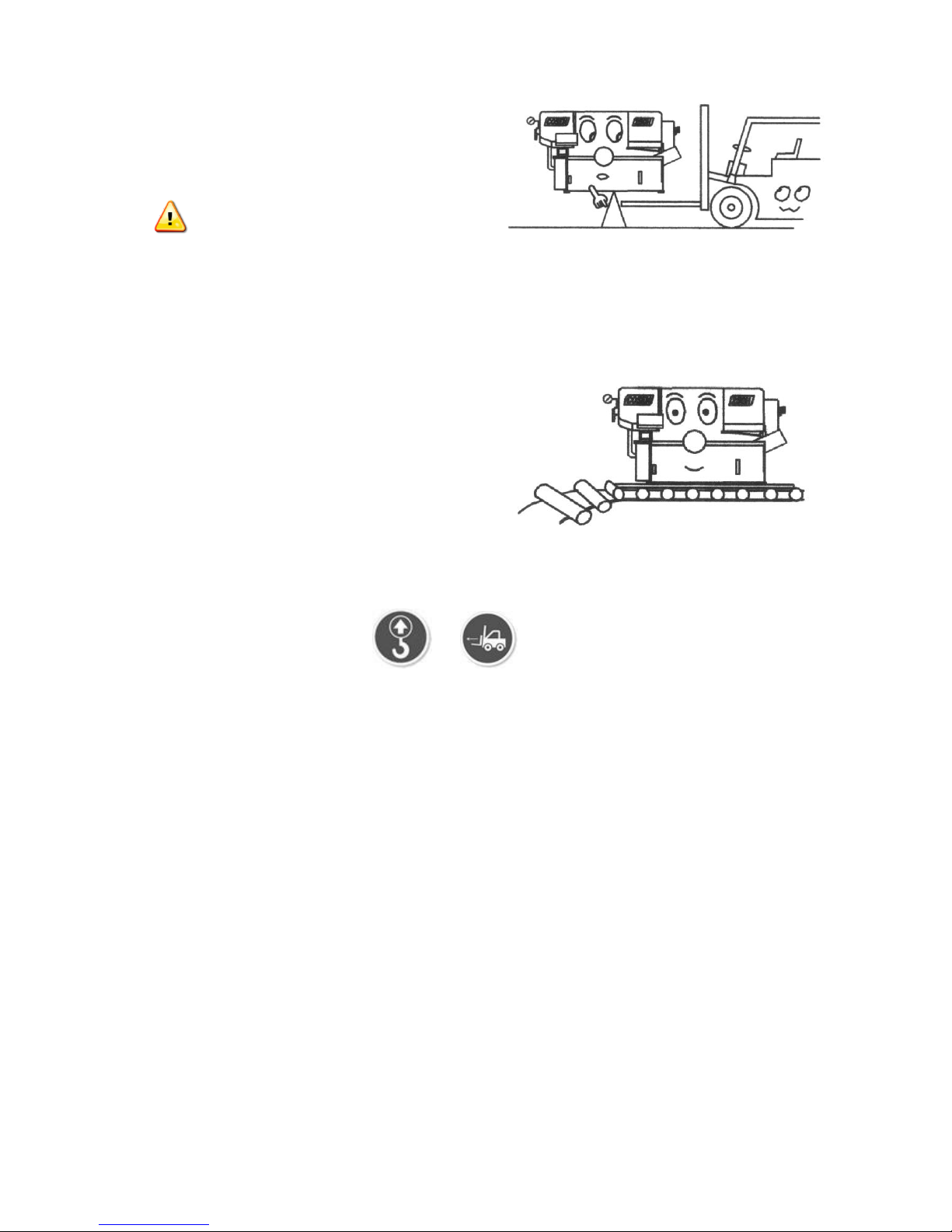
You must keep the machine balanced at all
times.
Make sure the forks are centered before
use.
(Illustration only. Please follow user guide of your forklift.)
3. Use rolling cylinders
You can use rolling cylinders to move your machine in a small machine shop environment.
You must use rolling cylinders made in material
of proper compressive strength.
4. Other ways to move
If the machine does not have or stickers, please contact your local agent
immediately.