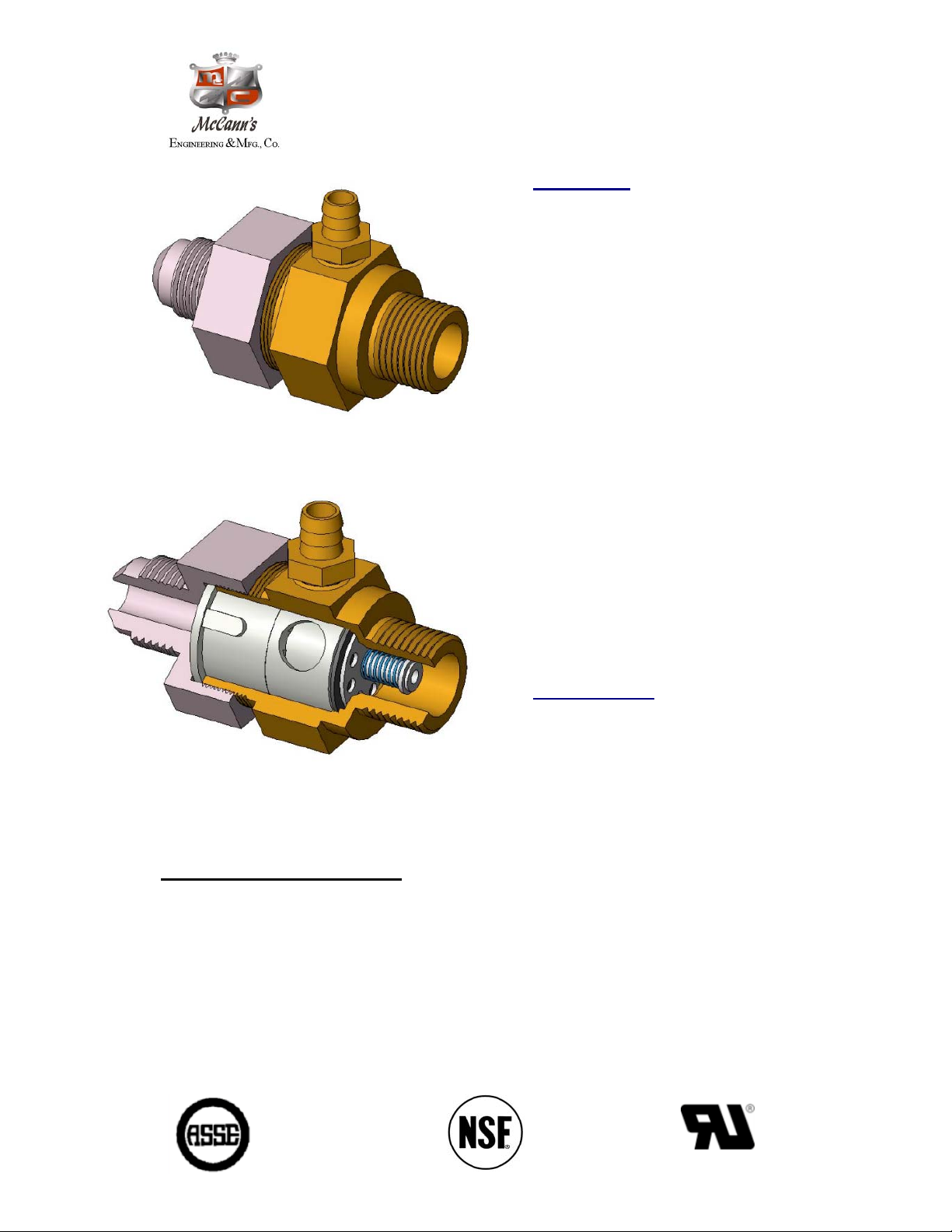
McCann’s ENGINEERING
ASSE 1022 BACKFLOW PREVENT0R
FEATURES:
*
Working pressures from 10-200 psig.
*
Working Temperature up to 130 OF.
*
3/8” Flared x 3/8” NPT connections.
*
Atmospheric Port for Visual Indication of
Secondary Check leakage.
*
Reliable and robust design. Minimized
leak points.
*
Performs and functions better than
other devices in the market.
*
Easy to install. Can be installed in
Vertical or Horizontal position.
*
Easy to service and maintain.
*
Easy to repair, using available repair kit
(16-1585).
APPLICATION:
* ASSE 1022 compliant OEM carbonator.
* Design specific field retrofit kits.
*
ASSE 1022 upgrade kit (16-1522) for
McCann’s carbonators.
APPROVALS / COMPLIANCE:
• ASSE Standard 1022-2003 –Backflow Preventer for Beverage Dispensing Equipment
• NSF/ANSI STD. 18- Manual Food and Beverage Dispensing Equipment
• FDA Food Additive Regulations (rubber compounds)
• UL –File E50184, Vol. 1, Sec. 2, Page 3A, Model E2 Series Fig. 1A (S85-17284)
• SAE J476 Dryseal Pipe Threads
• SAE J513 Refrigeration Tube Fittings
• COCA COLA

WHAT PLUMBING CODES REQUIRE:
Uniform Plumbing Code (UPC) and National Standard Plumbing Code (NSPC) have adopted the
use the American Society of Sanitary Engineering (ASSE) 1022 -Performance Requirements for
Backflow Preventer for Carbonated Beverage Machines.
UPC 603.4.13 Portable Water Supply to Carbonators “shall be protected by either an air gap or a
vented backflow preventer for carbonated beverage dispensers installed within the carbonated beverage
dispenser. The carbonated beverage dispenser shall bear the label of an approved testing agency,
certifying and attesting that such equipment has been tested and inspected, and meets the requirements of
the approved applicable standard. Carbonated beverage dispensers without an approved internal air gap
or vented backflow preventer for carbonated beverage dispensers and carbonated beverage dispensing
systems shall have the water supply protected with a vented backflow preventer for carbonated beverage
dispensers.”
NSPC 10.5.8 Connection to Carbonated Beverage Dispensers “The water supply to a carbonated
beverage dispenser shall be protected against backflow with an integral backflow preventer conforming to
ASSE 1022 or an air gap. Carbonated beverage dispensers and carbonated beverage dispensing systems
without an integral backflow preventer conforming to ASSE 1022 or an air gap shall have the water
supply protected with double check valve and atmospheric vent conforming to ASSE 1022.”
Due to the above codes change, the National Soft Drink Association (NSDA) issued a statement
stating that “…. Under the new code language, the soft drink industry will meet the code requirements by
installing the new backflow preventer meeting the ASSE Standard 1022 during the dispenser
manufacturing process. This change will eliminate the need to install backflow prevention devices on the
permanent dispenser water line after the dispenser is installed in the establishment. Fountain dispensers
that currently use an internal non-vented dual check valve (ASSE 1032), the industry standard for decades,
will be required to have an ASSE 1022 device installed on the dispenser water line.”
UPC being enforce in Alaska, Arizona, California, Colorado, Hawaii, Idaho, Indiana, Iowa,
Montana, New Mexico, Nevada, Oregon, Washington, and Wyoming; while NSPC is used in
Maryland, New Jersey, and South Dakota.
HOW IT WORKS:
ASSE Standard 1022 approved backflow prevention device has two independently acting check
valves in normally closed position. A normally open atmospheric port (vent) is provided between
the check valves.
When there is no flow through the Backflow Preventer, both primary and secondary check valves
remain in closed. When a flow is initiated downstream, both check valves open to allow the liquid
to flow through. Under “backflow” condition or in the event that the primary valve fails to seal, the
secondary valve will remain close. The leaking media (gas and/or liquid) will be relieved through
the vent or atmospheric port, thereby lowering the secondary check valve pressure to a mere
atmospheric (14.7 psi at sea level) condition.
Non-Vented Double-Check valve has no way of relieving the leaking media, thereby subjecting
the secondary check valve to similar condition that caused the primary check valve to fail.