
Quick Start Guide
00825-0100-4016, Rev CB
March 2017
Rosemount™ DP Level Transmitters and
1199 Diaphragm Seal Systems

Quick Start Guide
March 2017
NOTICE
This guide provides basic guidelines for the Rosemount DP Level Transmitters and 1199 Diaphragm Seal
Systems Reference Manual.
service, or troubleshooting. Refer to the appropriate reference manual for more instruction. This guide are
also available electronically on Emerson.com/Rosemount
It does not provide instructions for configuration, diagnostics, maintenance,
.
WARNING
The products described in this document are NOT designed for nuclear-qualified applications. Using
non-nuclear qualified products in applications that require nuclear-qualified hardware or products may
cause inaccurate readings.
For information on Rosemount nuclear-qualified products, contact your local Emerson
Representative.
™
Sales
Contents
Introduction . . . . . . . . . . . . . . . . . . . . . . . . . . . . . 3
Preface . . . . . . . . . . . . . . . . . . . . . . . . . . . . . . . . . . 3
General handling overview . . . . . . . . . . . . . . . . 4
2
Mechanical installation . . . . . . . . . . . . . . . . . . . . 4
Ranging the transmitter . . . . . . . . . . . . . . . . . . . 9
Rosemount 1199 seal types . . . . . . . . . . . . . . . . 9

March 2017
1.0 Introduction
A remote seal system consists of a pressure transmitter, a remote seal, and
either a direct mount or capillary style connection filled with a secondary fill
fluid. During operation, the thin, flexible diaphragm and fill fluid separate the
pressure sensor of the transmitter from the process medium. The capillary
tubing or direct mount flange connects the diaphragm to the transmitter.
When process pressure is applied, the diaphragm is displaced, transferring the
measured pressure through the filled system, by way of the capillary tubing,
to the transmitter. This transferred pressure displaces the sensing diaphragm
in the pressure sensor of the transmitter. This displacement is proportional to
the process pressure and is converted electronically to an appropriate output
current and/or digital protocol.
Figure 1. Path of Pressure in a Standard DP Level Seal System
Quick Start Guide
2.0 Preface
A. Pressure
B. Process isolating diaphragm
C. Transmitter diaphragm
D. Fill fluid
E. Transmitter pressure sensor
This guide is designed to assist with general handling and installation
instructions for the Rosemount DP Level Transmitters and 1199 Diaphragm
Seal Systems. The Rosemount DP Level Transmitters and 1199 Diaphragm Seal
Systems Reference Manual
system assemblies that are not covered in the corresponding transmitter
manuals.
contains supplemental information about the seal
3
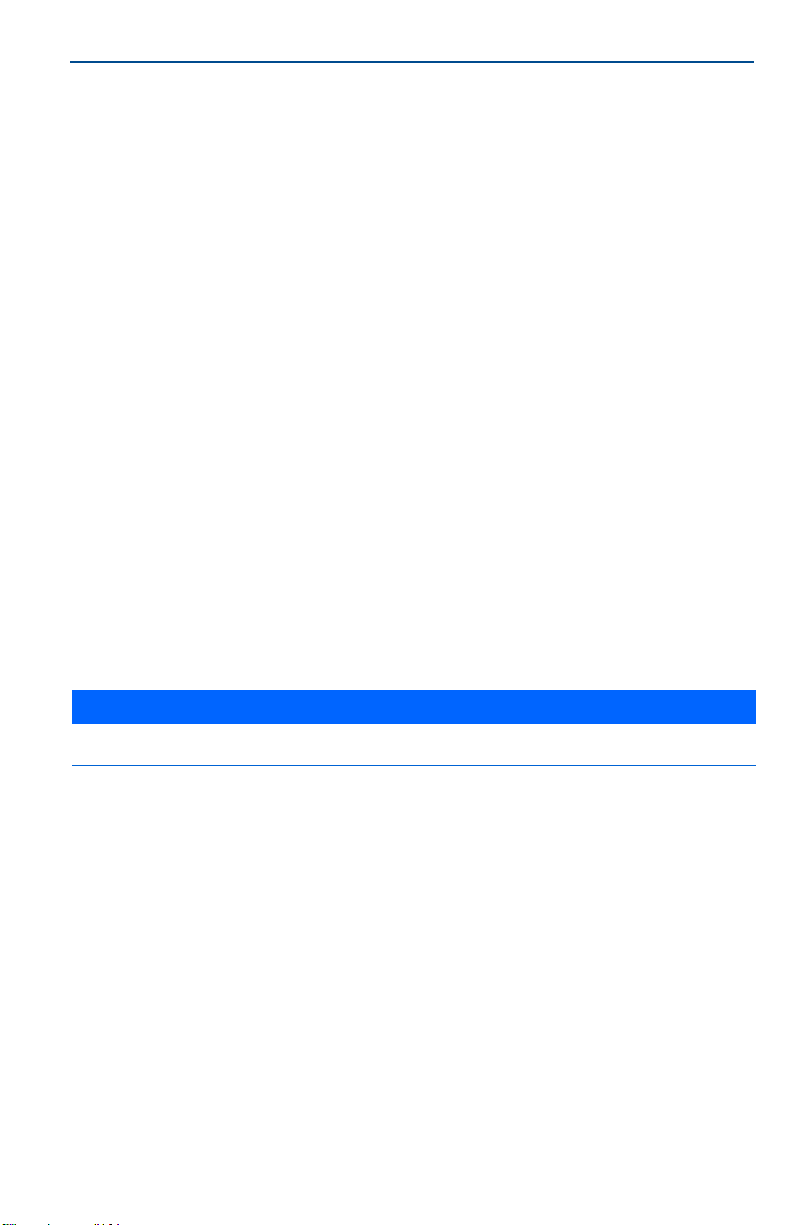
Quick Start Guide
3.0 General handling overview
Check if equipment received conforms to the order. If any issues, contact your
local Emerson sales representative immediately.
When unpacking or handling seal system assemblies, do not lift the seal or
transmitter by gripping the capillaries, doing so could result in disconnecting
the seal and/or capillary from the transmitter, which will void the warranty.
The material of a remote seal is designed to withstand pressure and wear from
process material, but outside of process connection conditions, remote seals
are delicate and should be handled with care.
The protective cover should remain on the seal until the moment before
installation. Try to avoid touching the diaphragm with fingers or objects and
refrain from setting the diaphragm side of the seal down on a hard surface. Even
minor dents or scratches in the diaphragm material may impair the
performance of the seal system assembly.
Avoid sharply bending or crimping the capillary tubing. The minimum bending
radius of the capillary tubing is 3-in. (8 cm).
When using heat or steam tracing, exercise caution if PVC coating is added onto
capillary. The PVC coating on the armor will break down at temperatures around
212 °F (100 °C). Best practice for heat and steam tracing is to regulate the
temperature above the maximum ambient temperature for a consistent result.
To avoid accuracy effects and thermal stress, the capillary should not be partially
heated.
March 2017
4.0 Mechanical installation
NOTICE
Never attempt to disconnect the seals or capillaries from the transmitter or loosen bolts. Doing so will result in
loss of fill fluid and will void the product warranty.
4.1 Mounting the seal system in vacuum applications
Mounting the pressure transmitter at or below the bottom vessel tap is an
important factor to ensure a stable measurement with vacuum applications.
The static pressure limit for a differential pressure transmitter is 0.5 psia
(25 mmHgA), which ensures the transmitter sensor module fill fluid remains
within the liquid phase of the vapor pressure curve.
If the vessel static limit is below 0.5 psia, mounting the transmitter below the
bottom tap provides a capillary fill fluid head pressure on the module. A general
rule in vacuum applications is to mount the transmitter approximately 3 ft.
(1 m) below the bottom tap of the vessel.
Capillaries are to be securely fastened in order to avoid false readings.
4