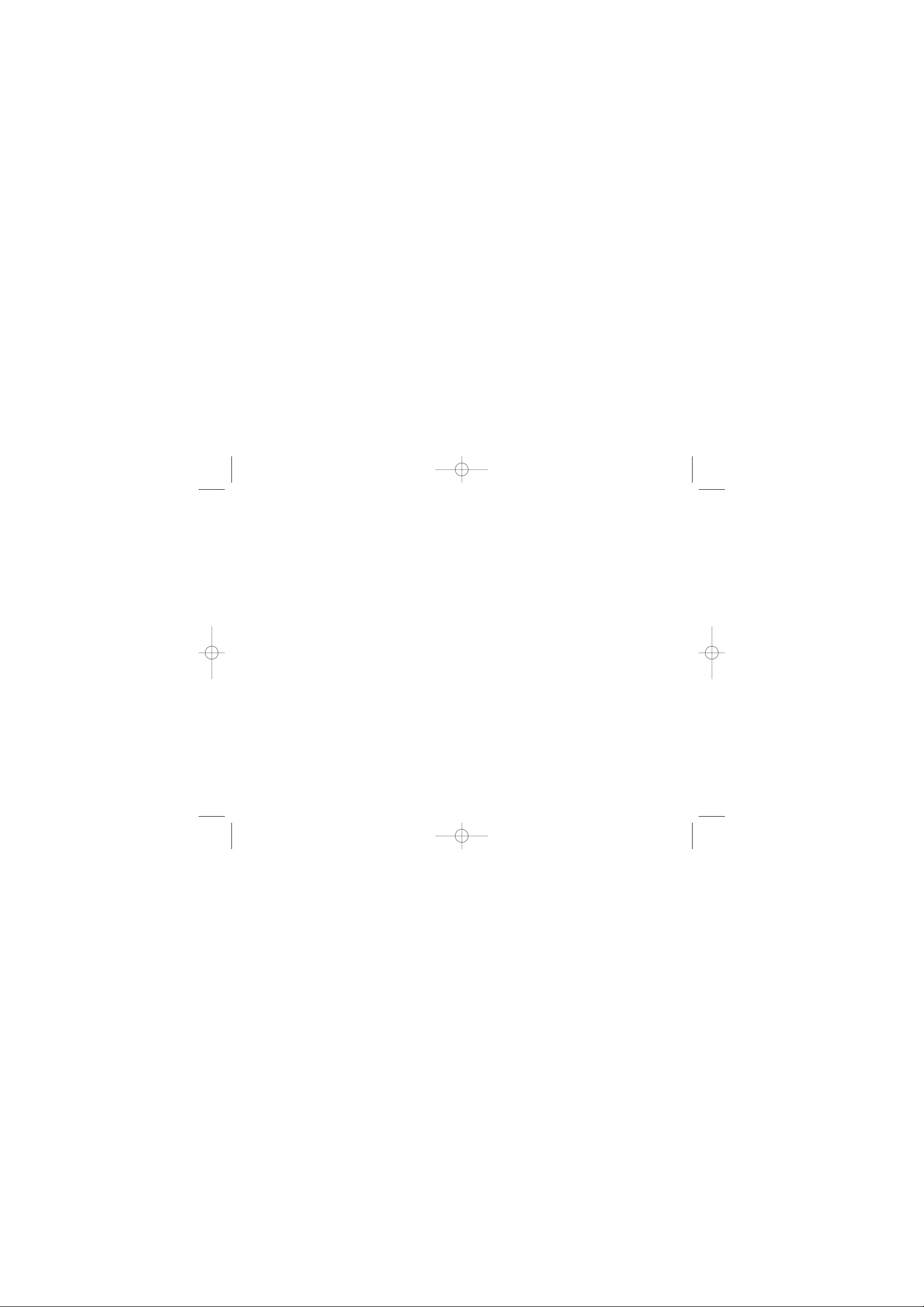
Introduction...........................................1
Assembly...............................................2
Testing...................................................3
Fitting Your RB1000..............................4
Preparing the T urnt able.....................5-6
Arm Height Adjustment.........................7
Cartridge Alignment...........................8-9
Anti-Skating...........................................9
Further Adjustments......................10-11
Contents
RB1000 Booklet.qxd 09/11/2005 10:15 Page 1
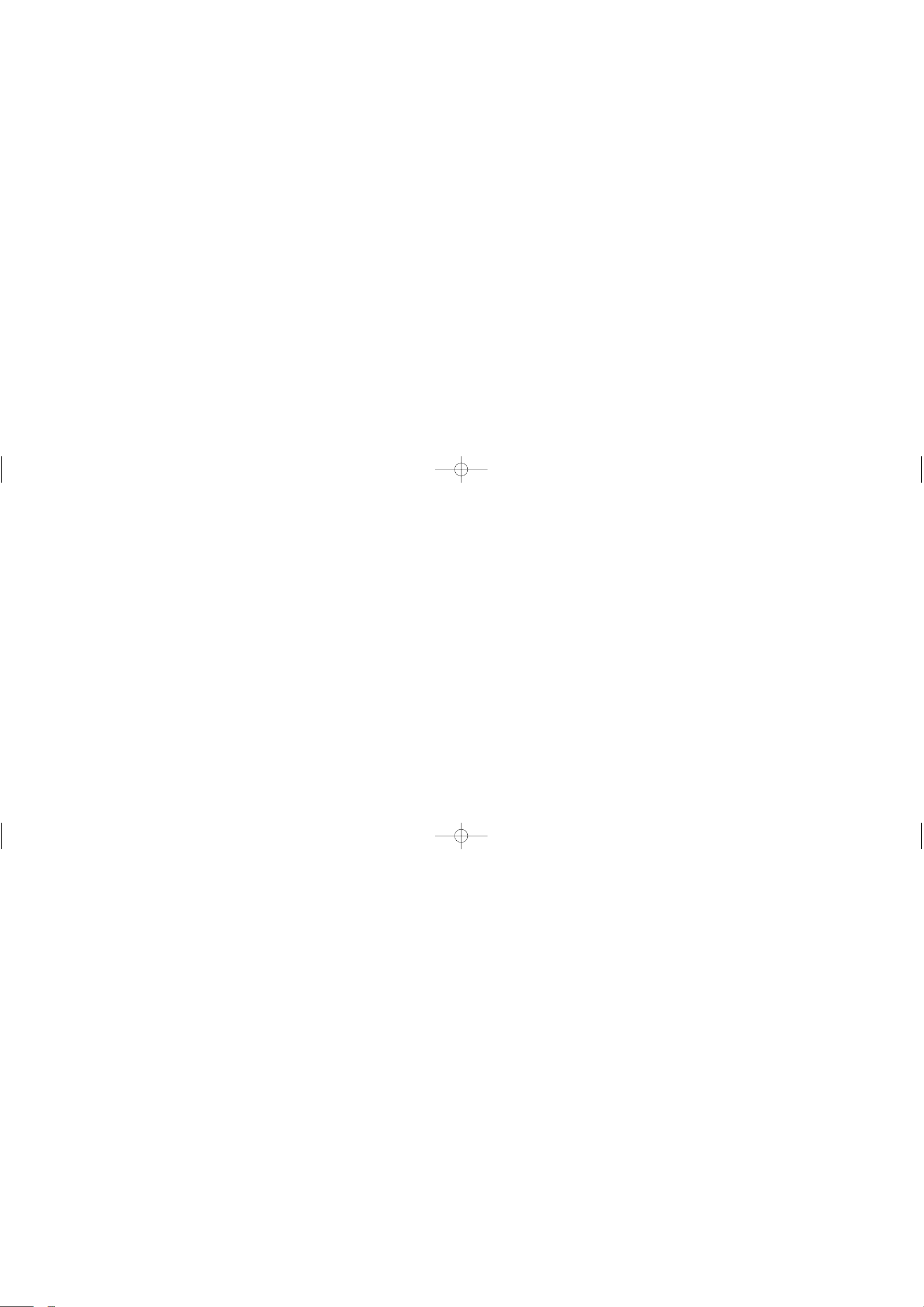
The precision stainless steel shaft onto which these bearings fit is
ground to a tolerance of within 5 microns (one micron being 1/1000
of a millimetre). The bearings are then selected and fitted onto
shaft s by hand. This is a highly skilled and time consuming process
which results in the fit between the shaft, bearing and one piece arm
tube being all interference fit s with zero tolerance. The arm tube,
after being cast, will be cleaned, inspected, highly polished then
inspected again. The three mounting point vertical bearing housing is
CNC machined from solid stainless steel into which the second set of
bearings are hand fitted, and into which the vertical shaft is fitted.
Again these are interference fits and so, are tolerance free.
Meanwhile, the arm tube assembly will have been fitted into the
carrier and then the two sub-assemblies come together with the arm
lead, which become a tonearm.
Assembly
2
Congratulations... You have purchased probably the highest
performance tonearm produced by mankind.
The Rega RB1000 is created using state of the art computerised
CNC engineering centres. The arm is then hand assembled and
checked by a small highly experienced dedicated team who draw on
the experience of having produced high quality tonearms for thirty
years.
Being designed to extract the most information from vinyl recordings
as is possible the RB1000 must hold the cartridge body both
accurately and rigidly whilst having bearing friction levels which are
extremely low. This is achieved by using the highest quality bearings
available, which are ordinarily found in navigational gyroscopes.
They are then graded both by hand and by aural examination.
This ensures that we have the smoothest and quietest ball races in
existence.
Incorporating the above design and engineering ideals the tonearm
will then track the spiral p ath of the record groove making the
cantilever of the cartridge move further in the cartridge body.
The result being the most musical information you will have ever
heard extracted from your record collection!
Introduction
1
RB1000 Booklet.qxd 09/11/2005 10:15 Page 2
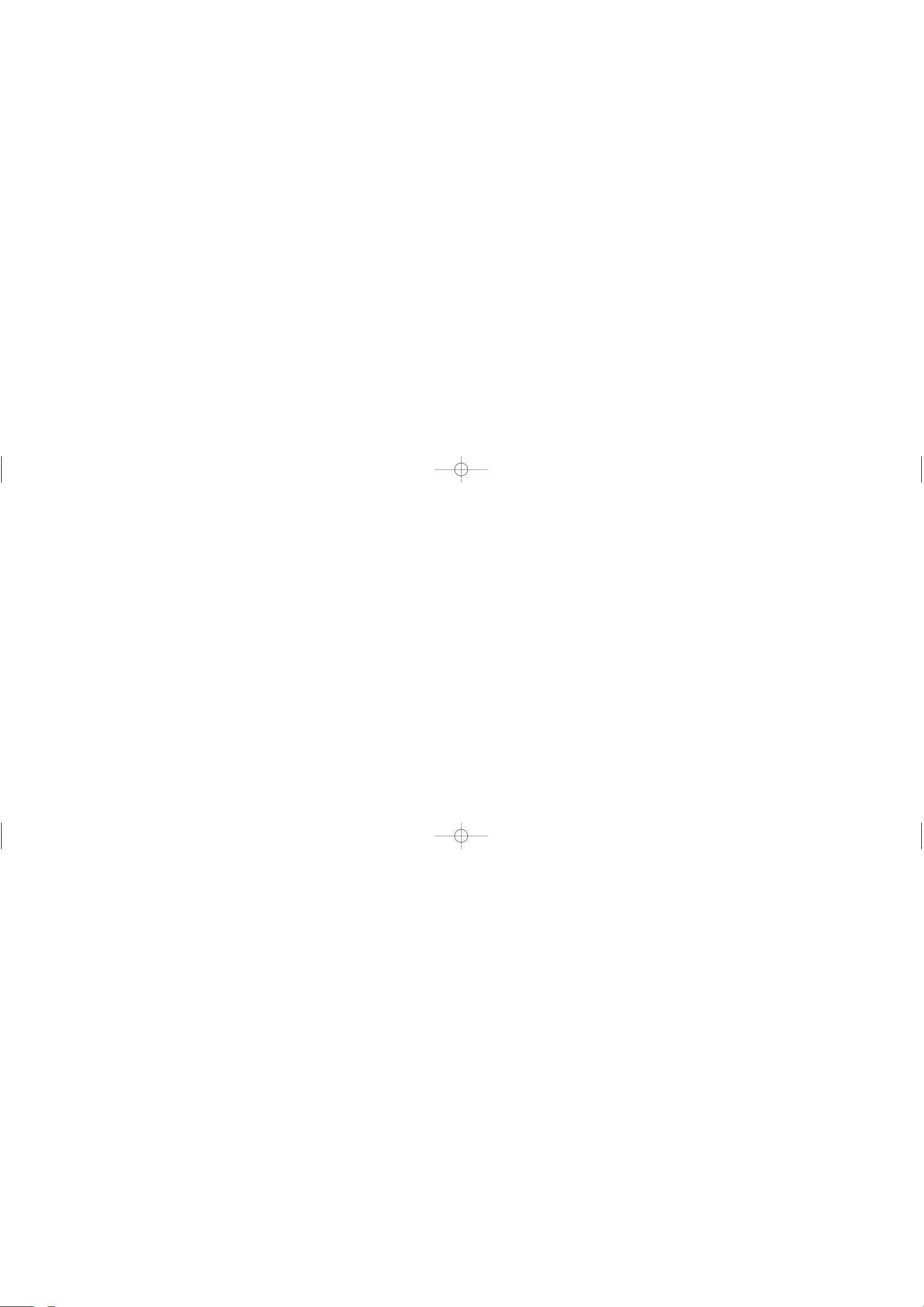
rejected by any member of sta ff involved. The entire process of
producing this arm is "time is no object", where perfection of the
process is.
Fitting your RB1000
The Rega RB1000 tonearm is a precision crafted product. To create
the low friction levels and meet the required mass, many pa rt s of the
arm are delicate and require careful handling. The arm should
always be treated with respect and under no circumstances should
any part be removed or t ampered with.
In most cases, it is advisable that the dealer fit s this arm to your
turnt able. If the user fit s the arm and causes any damage to the arm,
cartridge or turnt able, then it is their responsibility. The dealer should
also be able to advise should there be any subsequent problems
with the rest of the system.
Fitting Your RB1000
4
The testing of the completed product consists o f five separate
st ages. Firstly there is a horizont al bearing test, (also at this stage,
headshell azimuth is checked) this is in two part s, the first of which
involves a test of the action. This can only be done by hand/eye
coordination of highly skilled st a ff as there is no machine which could
work to the required accuracy.
W ith the first test completed the second p art may proceed; this is the
friction level test. This consist s of a 20mg weight placed on the
headshell of the balanced out arm to see how fast it falls. Following
this, vertical bearings undergo exactly the same test as the horizonta l
components, after which the tracking pressure assembly is tested for
accuracy by using an extremely sensitive stylus pressure gauge.
The fourth test is to access the magnetic bias assembly; this is done
on a purpose built jig using a test recording we have created
exclusively for the job. The arm is then tested to see that, at the
correct bias setting for the cartridge, the output from both channels is
identical. Then, by adjusting the bias slider , the change in output
levels can be observed visually on a twin needle moving coil meter.
Assuming all is well, the arm will go onto its final test, which is the
electrical continuity testing to make sure there is no crosstalk, and
that the earthing is present and correct. At any one of the previous
st ages, the whole assembly can (and are actively encouraged to) be
Testing
3
RB1000 Booklet.qxd 09/11/2005 10:15 Page 4