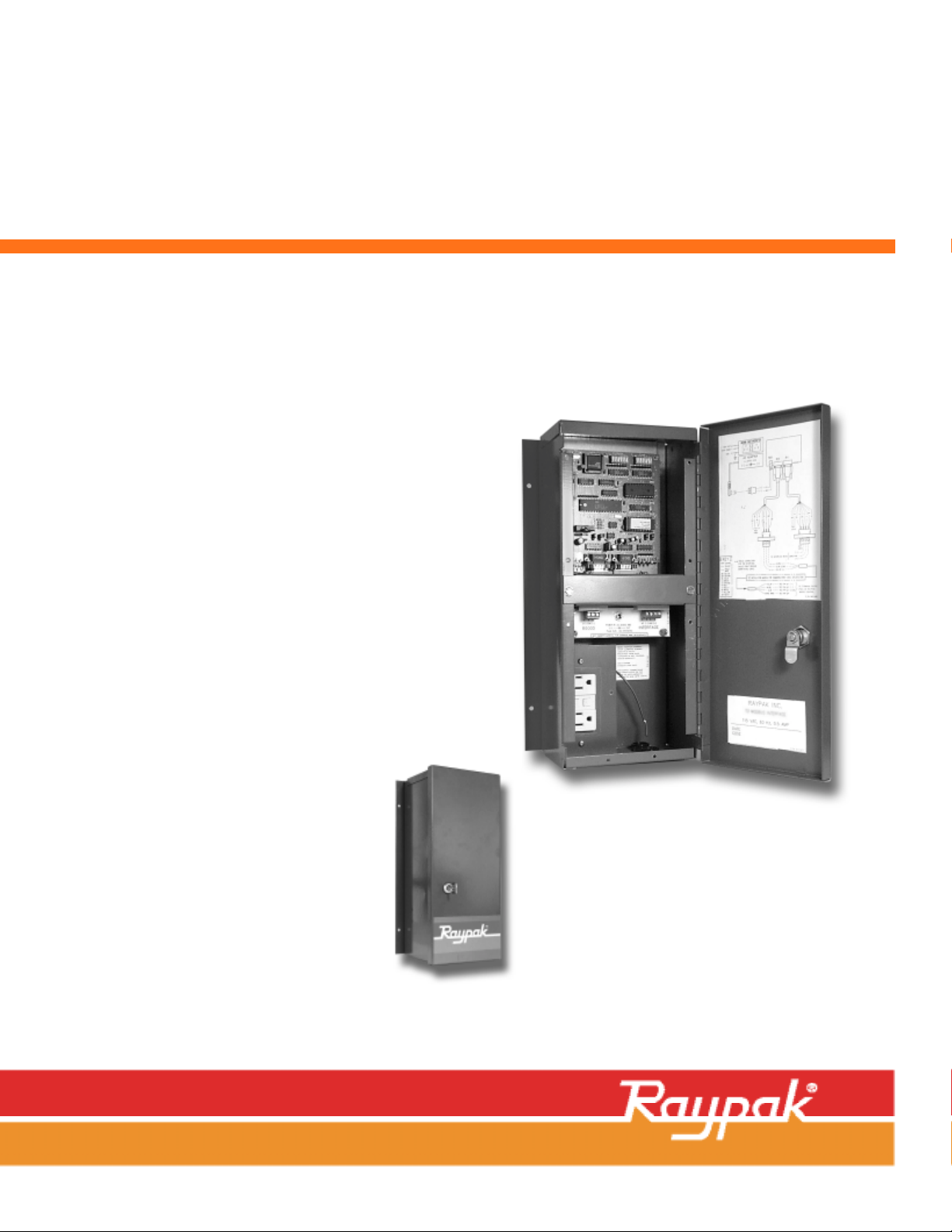
T-3 MODBUS
INTERFACE
B6000 BMS Modbus System Control Interface
The T-3 Modbus Interface provides certified compatibility for data sharing and program access
between the Raypak B6000 Boiler Management System and a host of other Building Management Systems. The T-3 utilizes a ProSoft 1500 series communications interface to facilitate low
level translation between the proprietary Raypak RS-485 protocol and other Manufacturers Modbus
protocols. The Raypak B6000 and Modbus systems fuse to provide a level of boiler control and
monitoring capability unparalleled by any other system at any price.
Features
• Certified Modbus Compatibility
• Total B6000 BMS Program Access
• Boiler Activation/Shutdown
• Outdoor Reset Adjustment
• Setback Control
• Lead/Lag Scheduling
• Boiler Fault Annunciation
• Complete Boiler Diagnostics
• Remote Troubleshooting
• All Attribute Read/Write Support
• Diagnostic LED Indicators
• Data Integrity Assurance
• Data Transfer Rate: 9600 Baud
• Single Source Responsibility
DOOR OPEN
DOOR CLOSED
Raypak, Inc. reserves the right to make product changes or improvements at any time without notification.
Catalog No. 5100.16 Effective: 9-01-98 Replaces: NEW
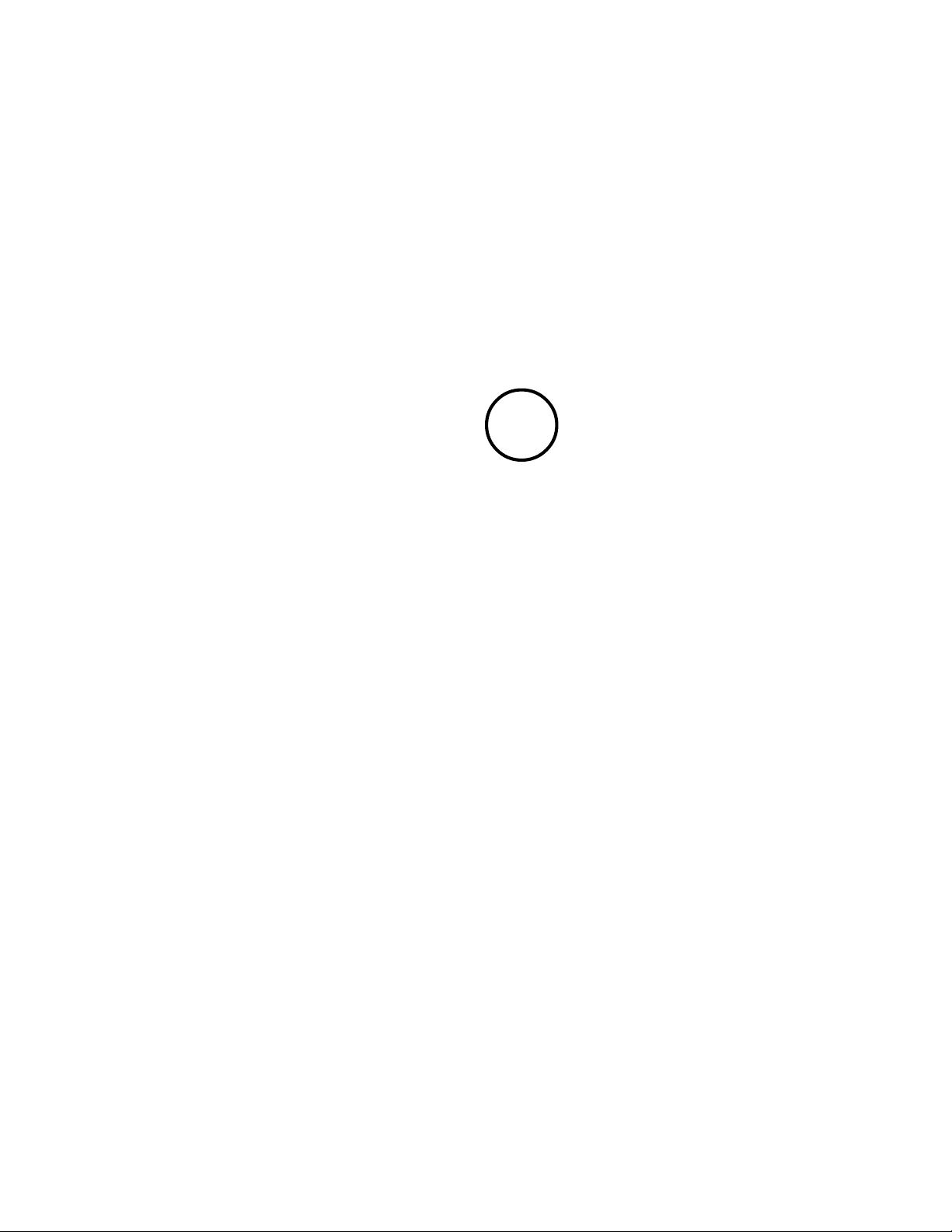
T-3 Modbus Interface
Interface Board
Certified Modbus Compatibility
ProSoft Series 1500 Translator
RS-485 to N2 Gateway
Transfer Rate: 9600 Baud
Read/Write Attributes
Analog/Binary
Total B6000 BMS Program Access
Data Integrity Protocol
Summation/Modulus Error Checking
Auto Command Error Feedback
LED Diagnostic Indicators
Port 1 Active
Port 2 Active
Port 1 Error
Port 2 Error
− Green
− Green
− Red
− Red
Electrical Characteristics
120 VAC, 0.25A, 60 Hz
Ambient Conditions
Temperature: -40 to 175
°F
Humidity: 90% RH Non-condensing
Enclosure
Heavy Gauge Steel
Lockable Access Door
Tamper Resistant Design
15 3/16L x 8 W x 4 3/4D
Boiler or Remote Mounted
Limited One Year Warranty
U
®
L
Sample Specification
Section I: General Requirements
1. Provide a Raypak T-3 Modbus Interface that shall facilitate low level data translation between the Raypak B6000 Boiler
Management System and Modbus compatible Building Management Systems.
2. The interface shall be microprocessor based.
3. The interface shall be UL Listed.
4. The interface shall carry a one year limited warranty against failure caused by defective workmanship or material.
5. The interface and boiler control system shall be manufactured by the same company and shall carry single source
responsibility.
Section II: Equipment Enclosure
1. The interface enclosure shall be constructed of heavy gauge steel and shall be protected with a baked-on UV inhibited
Polytuff powdercoat finish.
2. The front access door of the interface enclosure shall be lockable and the enclosure shall be tamper resistant.
Section III: Control Functions
1. The interface shall provide seamless communications integration between the Raypak B6000 RS-485 and Modbus
communications protocols.
2. The interface shall utilize summation/modulus error checking and auto command error feedback to ensure data integrity.
3. The interface shall allow analog and binary multi-level read/write Modbus capabilities for the following B6000 functions:
a) Reset parameters including: Setpoint, Reset Ratio, Temperature Rise and Control Band.
b) Outdoor cutoff parameters including: Outdoor Cutoff Temperature and Outdoor Cutoff Deadband.
c) Secondary operating parameters including: Firing Step Increment, Pump Turn-Off Delay and Ignition Lockout Time.
d) Setback parameters including: Setback Period Scheduling and Setback Activation.
e) Lead-lag parameters including: Lead Boiler Assignment and Time Rotation Interval.
Section IV: Display Functions
1. The interface shall have port active and error diagnostic lights for both interface ports.
2. The interface shall allow analog and binary multi-level read-only Modbus capabilities for the following B6000 functions:
a) Current temperatures including: Water Temperature, Outdoor Air Temperature, and Target Temperature.
b) Boiler operating status including: Valve Position, and Current Firing Rate.
c) Fault indication including: Low Water, Low Gas Pressure, High Gas Pressure, High Temp, Low Water Pressure, Low
Flow, No Pilot and Manual Override Status.
d) Secondary operating parameters including: Time Remaining Till Lead Boiler Rotation and Valve Operating Times.
Raypak, Inc., 2151 Eastman Avenue, Oxnard, CA 93030 (805) 278-5300 FAX (800) 872-9725 www.raypak.com
Litho in U.S.A.