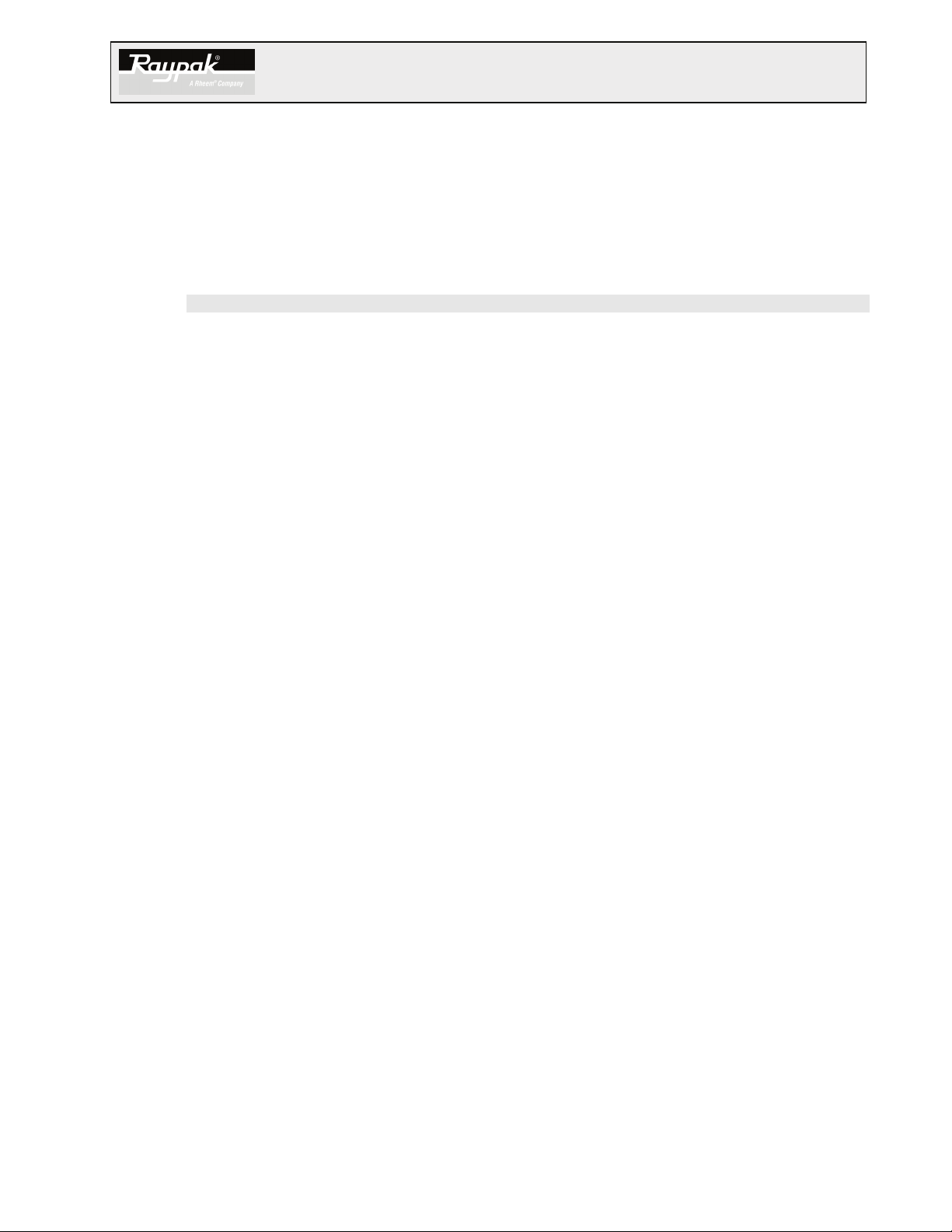
PART 1 - GENERAL
1.1 SUMMARY
A. Section includes gas-fired, copper finned-tube hydronic heating boilers
B. Related Sections
Specifier Note: Use as needed
1. Building Services Piping – Division 23 21 00
2. Breeching, Chimneys, and Stacks (Venting) – Division 23 51 00
3. HVAC Instrumentation and Controls – Division 23 09 00
4. Electrical – Division 23 09 33
1.2 REFERENCES
A. ANSI Z21.13/CSA 4.9
B. ASME, BPV Section IV
C. 2006 UMC, Section 1107.6
D. ANSI/ASHRAE 15-1994, Section 8.13.6
E. National Fuel Gas Code, ANSI Z223.1/NFPA 54
F. I=B=R
G. National Electrical Code
H. ASME CSD-1, 2009 (when required)
®
HI DELTA
, TYPE H - MODELS 302BE-902BE
SUGGESTED SPECIFICATIONS
DIVISION 23 52 33.13
FINNED WATER-TUBE BOILERS
Catalog No.: 2000.942E
Effective: 12-28-09
Replaces: 9-01-09
1.3 SUBMITTALS
A. Product data sheet (including dimensions, rated capacities, shipping weights, accessories)
B. Wiring diagram
C. Warranty information
D. Installation and operating instructions
1.4 QUALITY ASSURANCE
A. Regulatory Requirements
1. ANSI Z21.13/CSA 4.9
2. Local and national air quality regulations for low NOx (< 20 PPM NOx emissions) boilers
B. Certifications
1. CSA
2. ASME H Stamp and National Board Listed
1.5 WARRANTY
A. Limited one-year warranty from date of installation
B. Limited twenty-year thermal shock warranty
C. Limited ten-year closed-system heat exchanger warranty
PART 2 - PRODUCTS
2.1 MANUFACTURER
A. Raypak, Inc.
1. Contact: 2151 Eastman Ave., Oxnard, CA 93030; Telephone: (805) 278-5300;
Fax: (800) 872-9725; Web site: www.raypak.com
Project Name / Date Division 23 52 33.13 - 1
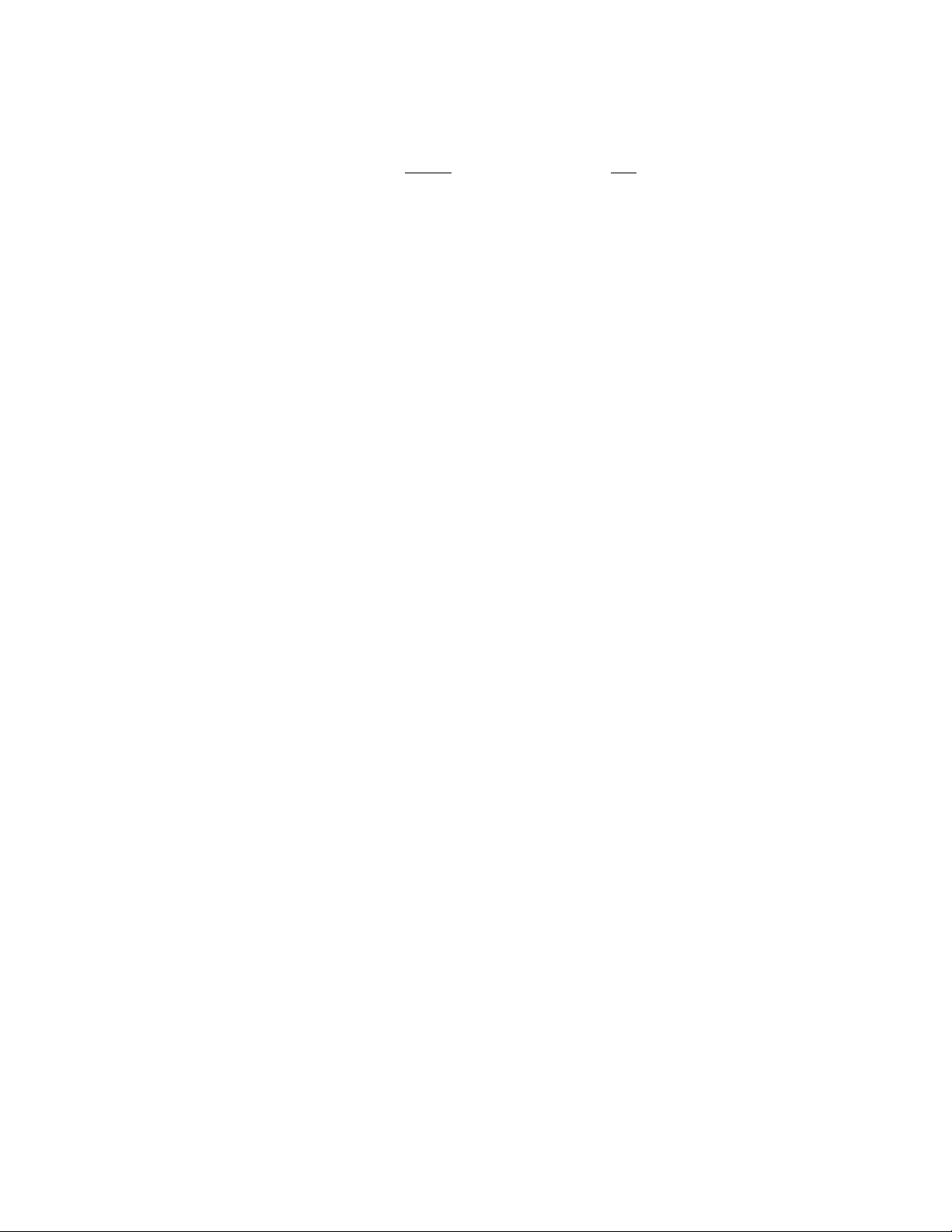
2. Product: Hi Delta® copper finned-tube hydronic boiler(s)
2.2 BOILERS
A. General
1. The boiler(s) shall be fired with
2. The boiler(s) shall be CSA tested and certified with a minimum thermal efficiency of 87 percent
at full fire.
3. The boiler(s) shall be ASME inspected and stamped and National Board registered for 160
PSIG working pressure, complete with a Manufacturer's Data Report.
4. The boiler(s) shall have a floor loading of 65 lbs. /square foot or less.
B. Heat Exchanger
1. The heat exchanger shall be of a single-bank, horizontal-grid design with eight integral copperfinned tubes, each end of which is rolled into an ASME boiler-quality steel tube sheet.
2. The heat exchanger shall be sealed to 160 PSIG rated cast-iron glass-lined headers with high
temperature silicone "O" rings.
3. The low water volume heat exchanger shall be explosion-proof on the water side and shall
carry a twenty-year warranty against thermal shock.
4. The headers shall be secured to the tube sheet by stud bolts with flange nuts to permit
inspection and maintenance without removal of external piping connections.
5. The heat exchanger shall incorporate “V” baffles between the tubes to ensure complete
contact of the external tube surfaces with the products of combustion.
6. The boiler(s) shall be capable of operating at inlet water temperatures as low as 120°F without
condensation.
7. The boiler(s) shall be designed to accommodate field changes of either left or right hand
plumbing and electrical while leaving the tube bundle in place.
C. Burners
1. The tubular burners shall have multiport radial gas orifices, punched ports and slots, be
capable of quiet ignition and extinction without flashback at the orifice, and be manufactured
from corrosion-resistant, titanium-stabilized stainless steel with low expansion coefficient.
2. The burners will be supplied with a fan-assisted, clean burning, and highly efficient fuel-air
mixture.
D. Ignition Control System
1. The boiler(s) shall be equipped with a 100 percent safety shutdown system.
2. The ignition shall be Hot Surface Ignition type with full flame rectification by remote sensing
separate from the ignition source, with a three-try-for-ignition sequence, to ensure consistent
operation.
3. The igniter will be located away from the water inlet to protect the device from condensation
during startup.
4. The ignition control module shall include an LED that indicates six (6) individual diagnostic
flash codes.
5. Two external viewing ports shall be provided, permitting visual observation of burner
operation.
E. Gas Train
1. The boiler(s) shall have a firing/leak test valve and pressure test valve as required by CSD-1.
2. The boiler(s) shall have dual-seated main gas valve(s).
3. Gas control trains shall have a redundant safety shut-off feature, main gas regulator, shut-off
cock and plugged pressure tapping to meet the requirements of ANSI Z21.13/CSA 4.9.
F. Boiler Control
1. The following safety controls shall be provided:
a. High limit control
b. Flow switch, mounted and wired
c. ____PSIG ASME pressure relief valve, piped by the installer to an approved drain
d. Temperature and pressure gauge
gas at a rated input of BTU/hr.
Project Name / Date Division 23 52 33.13 - 2