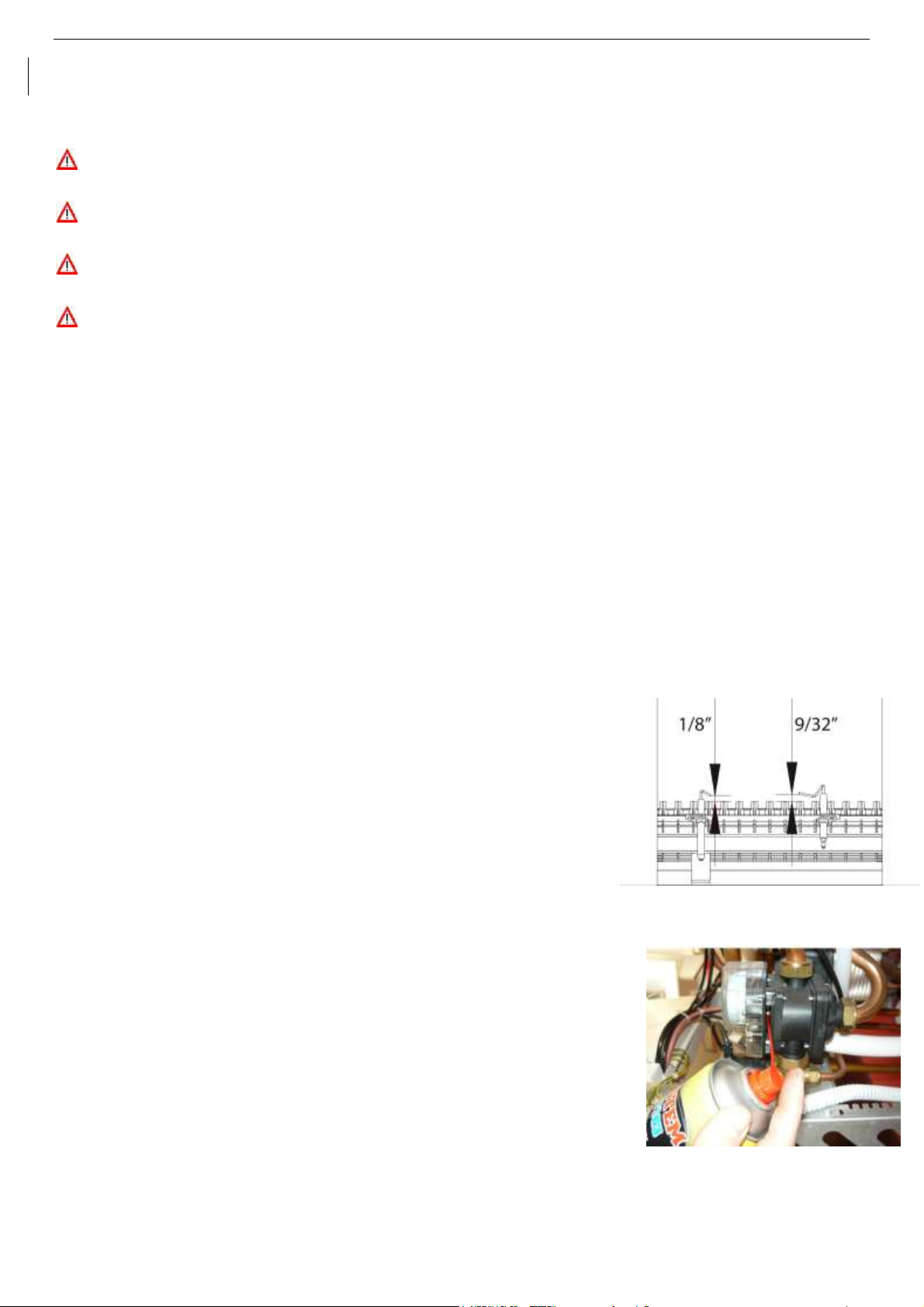
INSTALLATION INSTRUCTIONS
6. MAINTENANCE (authorized personnel)
6.1 General Warnings
All maintenance operations must be carried out by professionally qualified personnel, authorised by
Granby/Pensotti LLC.
The frequency of boiler maintenance must comply with current law and, nevertheless, should be carried
out once a year.
In order to guarantee the long life of the appliance and in accordance with the current gas safety
regulations, only use original spare parts
Before carrying out any type of maintenance operation, disconnect the appliance from the mains
electricity supply and close the gas valve.
6.2 Boiler inspection
In order to ensure that the boiler operates efficiently and safely, it is required that the appliance is inspected by a
suitably competent technician at least once a year.
The following is a minimum recommendation of service that should be carried out annually
■ Check the condition of the gas seals and replace where necessary.
■ Check the condition of the water seals and replace where necessary.
■ Visually inspect the condition of the combustion chamber and flame.
■ Remove and clean any oxidation from the burner.
■ Check that the seal of the room-sealed chamber is undamaged and positioned correctly.
■ Check the primary heat exchanger and clean if necessary using a soft nylon brush and subitle vacum
■ Check the condition and operation of the ignition and gas safety systems.
■ Remove and clean the scaling from the ignition and flame detection
electrodes, paying particular attention to place them at the correct distance
from the burner. Fig 1.
■ Check the pre-fill pressure of the integral expansion tank
■ Check the presence of air intake/permanent ventilation openings correctly
sized according to the boiler installed and in respect with current law.
■ Check the integrity and operation of the flue gas exhaust system.
■ Check the integrity of the gas piping system.
■ Check that the connection to the electricity supply complies with that reported
in the boiler’s instruction manual.
■ Check the electrical connections inside the control panel.
■ Check Fernox inhibitor integrity
■ Check and clean if necessary the dirt separator
■ Check for and remove any combustible or flammable materials that are in the
vicinity of the boiler
■ Lubricate the 3-way valve using a TPFE aersol lubricant. Fig 2
■ Check Relief Valve or proper operation
■ Check the maximum and minimum modulation pressures and the modulation
itself.
■ Check that the combustion is correctly regulated and if necessary make
adjustments according to section 4.4 “Starting the boiler”.
■ Check all heating safety systems. Ex; termpeature saeftly limit, air pressure switch, flame failure, etc.
65
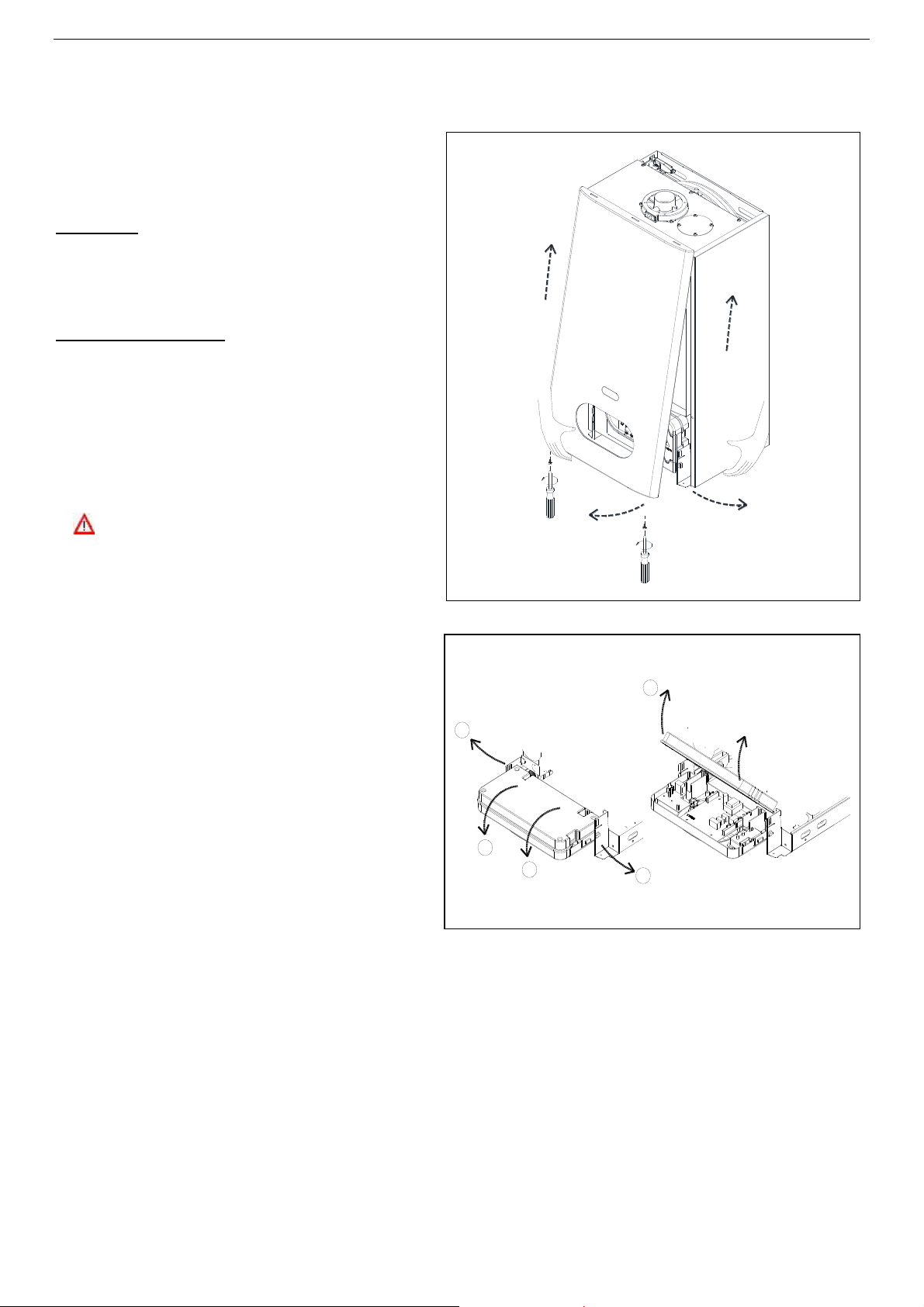
INSTALLATION INSTRUCTIONS
6.3 Accessing the boiler
All maintenance operations require one or more of the
boiler casing panels to be removed.
The side panels can only be removed after the front
panel has been removed.
Front panel:
Remove the fixing screws at the lower edge of the
front panel.
Grasp the lower part of the panel and pull it
outwards (see fig. 1) and then up (see fig. 2).
Left and right side panel:
Remove the fixing screws at the front and lower
edge of the side panel to remove.
Grasp the bottom of the panel, move it sideways
and then upwards to remove it.
To access the electrical connections of the control
panel, proceed as follows:
Switch off the power supply at the main switch.
Remove the front panel (see fig. 1 and fig. 2).
Grasp the left and right control panel support
brackets (see fig. 5) and pull them outwards, at the
same time rotating the panel downwards.
Unscrew the four fixing screws (see fig. 6) and
remove the panel back piece.
6.4 Flushing out the primary side
Fill the boiler as per the filling instructions.
Using a drain off cock on the lowest point of
the system allow the water to drain from the
system and boiler.
In order to flush the system correctly, turn off
all radiators or fan coils. Open the filling loop
and drain cock simultaneously and allow the water to flow through the boiler.
Open each individual radiator or fan coil, allowing water to flow through. Then turn that radiator or fan coil
off and repeat for all radiators or fan coil on the system.
Turn off the filling loop and close the drain cock open all radiators and open the filling valve to fill the
system. Continue to fill the system until the pressure gauge reads in the Green section of the gauge 14.5
psi.
In order to safeguard all waterside components the supplied Fernox Commissioning Kit must be used in its
entirety.
66
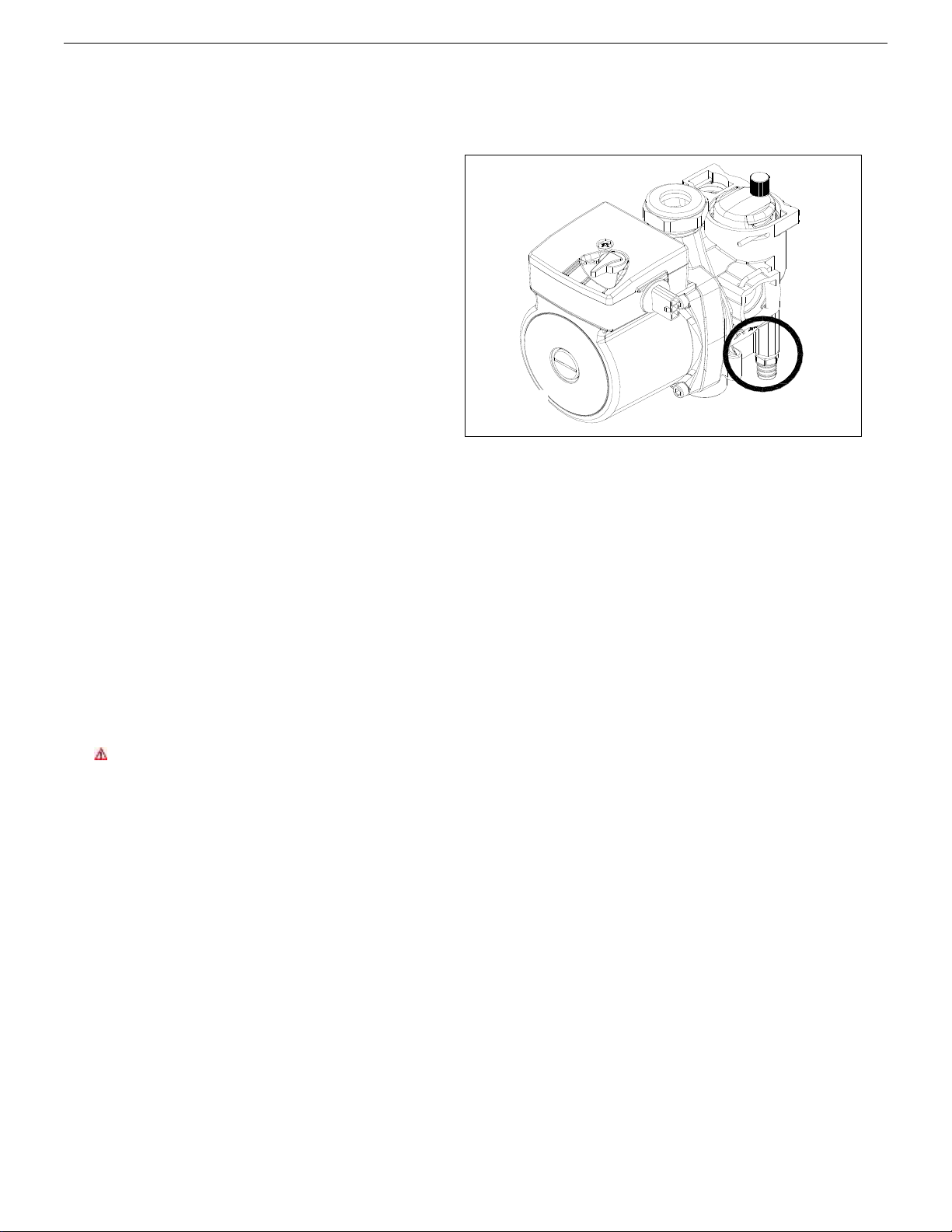
INSTALLATION INSTRUCTIONS
6.5 Draining the central heating system
If the need arises to drain the system, this can be done
as follows:
Switch the system to “HEAT” mode and ignite the
boiler.
Switch off the power supply to the boiler.
Wait for the appliance to cool down.
Connect a hose to the system drain point R and
locate the other end of the hose in a suitable
drainage system.
Open the system drain valve (fig. 1).
Open the air vents on the radiators, starting with the
highest and moving down the system to the lowest.
When the system has been drained, close the
radiator air vents and the drain valve.
Draining the domestic hot water system
If there is a danger of freezing, the domestic hot water system should be drained. This can be done as follows:
Close the main water supply valve.
Open all the hot and cold water taps.
Drain the water from the system. Used compressed air to evacuate the pipes of any remaining water.
Use non-toxic antifreeze to protect the DHW system.
On completion, close all the previously opened taps.
Freeze Protection
Glycol must not be used in Domestic Hot Water applications.
System winterization (non-operative system)
Because it may be impossible to completely drain the boilers heating circuit, D.H.W circuit and distribution system.
Pensotti recommends the introduction of the proper type antifreeze to protect these systems from freezing damage.
System winterization (operating system)
Pensotti boilers are certified for indoor use ONLY. Proper precautions for freeze protection are
recommended for boilers and associated piping in areas where the danger of freezing exists. Do not use
automotive antifreeze. Pensotti recommends the use of inhibited glycol concentrations between 20-35%
glycol. Glycol products must be maintained properly so they do not become inactive or corrosive, consult
glycol specifications for more information.
67