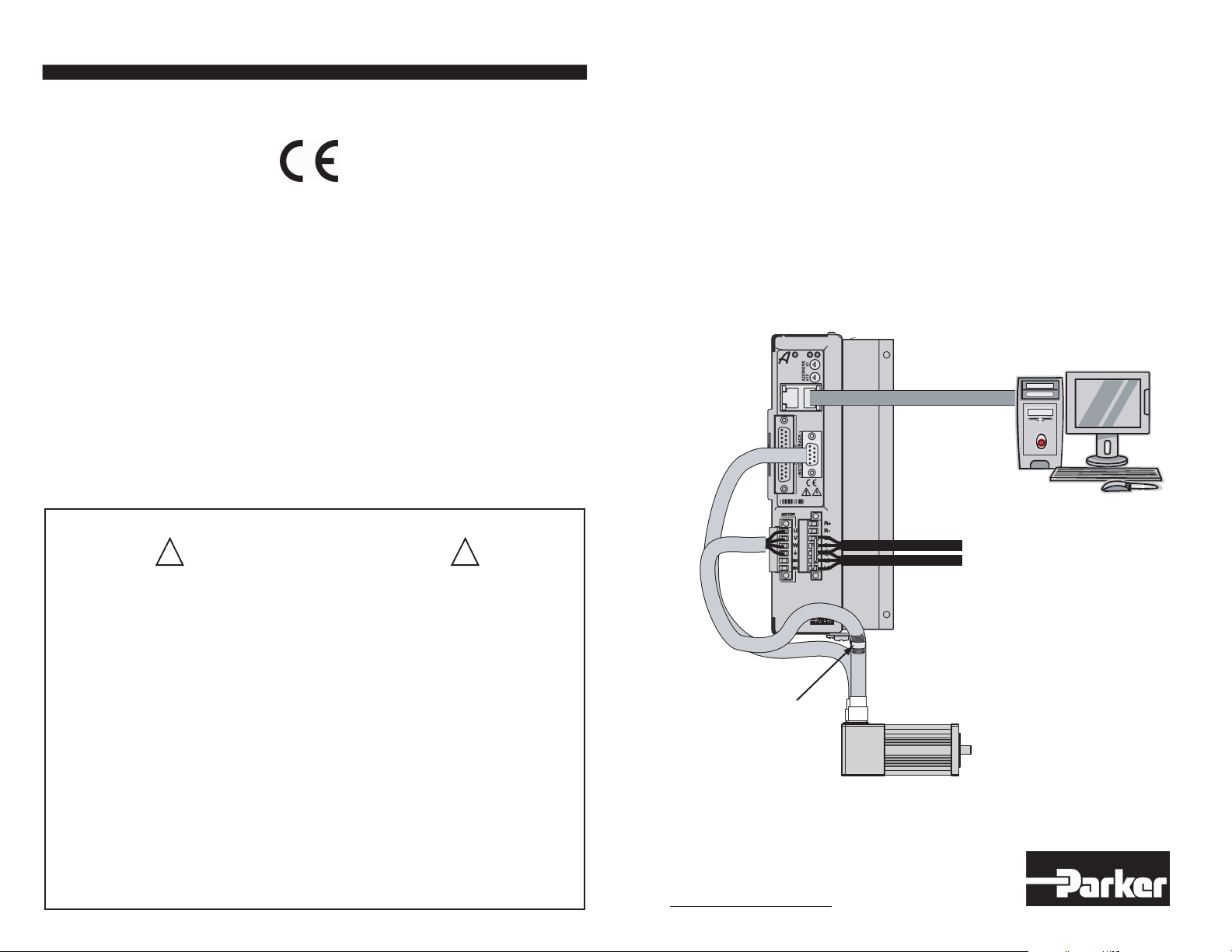
Compliance
UL Recognized Component, 508c
Product Type . . . . . . . . . . . . . . . . . Aries AR-04CE, AR-08CE, and AR-13CE
The above equipment conforms with the protection requirements of Council Directive
89/336/EEC (EMC Directive) as amended by Directive 92/31/EEC on the approximation of the
laws of the Member States relating to Electromagnetic Compatibility when installed, operated,
and maintained as intended. Also, the above equipment conforms with the requirements of
Council Directive 73/23/EEC (Low Voltage Directive) as amended by 92/59/EEC, and CE
Marking Directive 93/68/EEC, provided the installation requirements described in the
Aries-ACR Drive/Controller Hardware Installation Guide are met, when installed, operated,
and maintained as intended.
In accordance with IEC 61800-3:1997 (adjustable-speed electrical power drive systems) this
product is of the restricted sales distribution class which meets the needs of an industrial
environment when installed as directed. However, further measures may need to be taken for
use of the product in a domestic environment.
The installation requirements are detailed in the Information supplied with the equipment. The
equipment is sold only to competent system builders.
Safety Warning!
High-performance motion control equipment is capable of producing rapid movement and
very high forces. Unexpected motion may occur especially during the development of controller
programs. KEEP WELL CLEAR of any machinery driven by servo motors. Never touch any part
of the equipment while it is in operation.
!!
Aries
Controller
Quick Reference Guide
Aries AR-04CE, AR-08CE, and AR-13CE Servo Drive/Controllers
Aries Controller
Ethernet Cable
Motor Feedback
Cable
Control Power
Cable
Motor Power
Motor
Cable
Mains Cable
Customer PC
This product is sold as a motion control component to be installed in a complete system
using good engineering practice. Care must be taken to ensure that the product is installed and
used in a safe manner according to local safety laws and regulations. In particular, the product
must be positioned so that no part is accessible while power may be applied.
This and other information from Parker Hannifin Corporation, its subsidiaries, and authorized
distributors provides product or system options for further investigation by users having technical expertise. Before you select or use any product or system, it is important that you analyze
all aspects of your application and review the information concerning the product in the current
product catalog. The user, through its own analysis and testing, is solely responsible for making
the final selection of the system and components and assuring that all performance, safety, and
warning requirements of the application are met.
If the equipment is used in any manner that does not conform to the instructions given in this
user guide, then the protection provided by the equipment may be impaired.
R-Clamp snugly
attached to braided
shield
Electromechanical Division
Parker Hannifin Corporation
p/n 88-028905-01A
Effective: October 2007
http://www.parkermotion.com
Motor
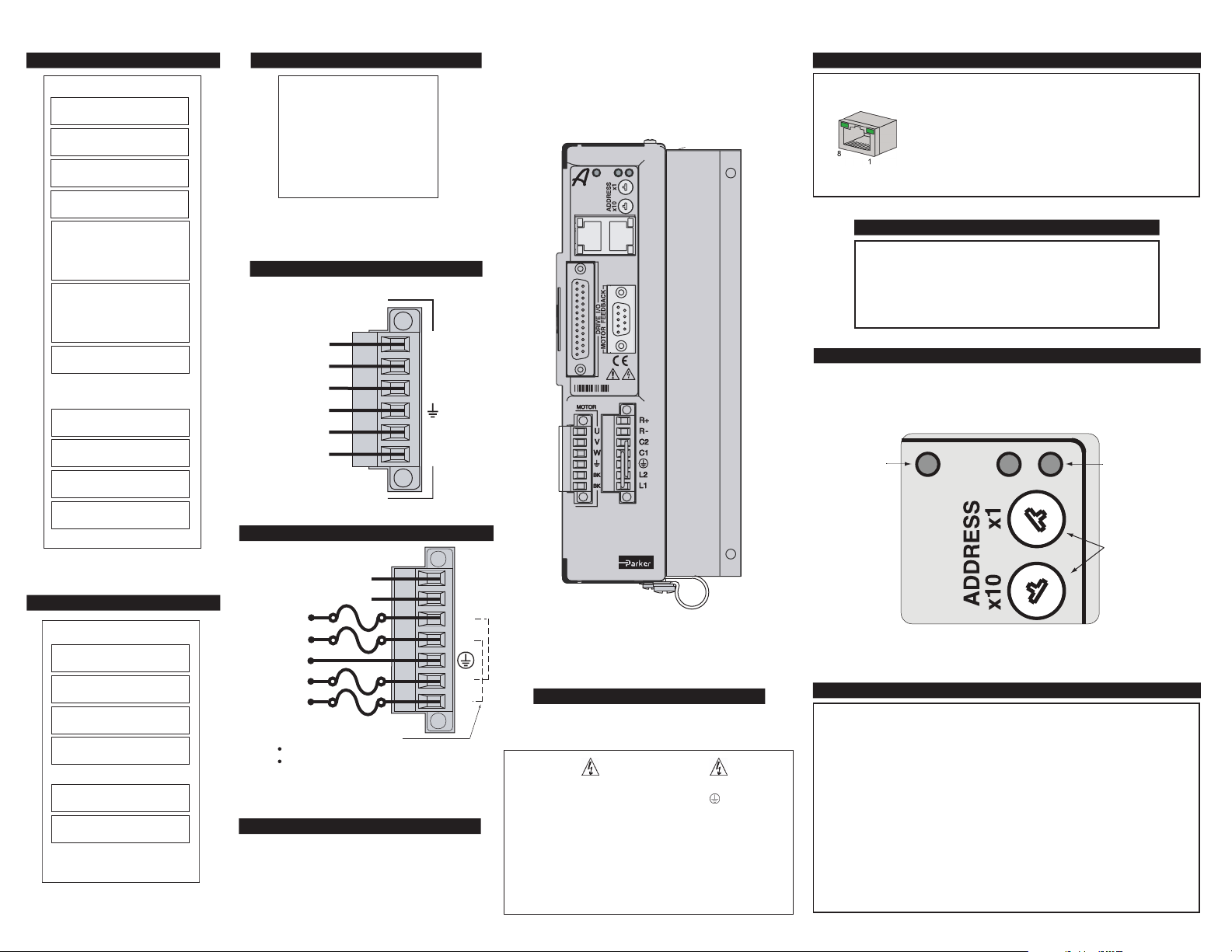
I/O Connector
Signal
Input 0+
Input 0– 14
Input 1+
Input 1– 15
Input 2+
Input 2– 16
High-Speed Input 4+ 4
High-Speed Input 4– 17
High-Speed Input 5+ 5
(or Aux Enc A+)
High-Speed Input 5– 18
(or Aux Enc A-)
High-Speed Input 6+ 6
(or Aux Enc B+)
High-Speed Input 6– 19
(or Aux Enc B-)
Input 3+ 7
Input 3– 20
Reserved (future 5V) 8
Reserved (future GND) 21
Output 32+ 9
Output 32– 22
Output 33+ 10
Output 33– 23
Output 34+ 11
Output 34– 24
Output 35+ 12
Output 35– 25
Not used 13
NOTE: Box surrounding pins indicates
a requirement for twisted-pair wiring.
1
2
3
Pin
Motor Feedback Connector
Signal Pin
ENC Z+/DATA+ 1
ENC Z–/DATA– 2
DGND 3
+5 VDC (250mA max) 4
+5 VDC (250mA max) 5
DGND 6
ENC A–/SIN– 7
ENC A+/SIN+ 8
Hall 1/SCLK+ * 9
Thermal+ 10
Thermal– 15
ENC B–/COS– 11
ENC B+/COS+ 12
Hall 2/SCLK– * 13
Hall 3 14
*When using the SinCos protocol, pins
9 and 13 require twisted pair wiring.
Ethernet Connector
Signal
RX+ 1
RX– 2
TX+ 3
Not used 4
Not used 5
TX– 6
Not used 7
Not used 8
Ethernet Cable: Use braid over foil twisted-pair
wiring (straight or crossover).
Pin
Output Power Connector
MOTOR
Motor Phase
Motor Phase
Motor Phase
Motor Safety Earth
Motor Brake Relay
Motor Brake Relay
U
V
W
BK
BK
Mains Power Connector
External Regeneration Resistor
External Regeneration Resistor
Control Input Power
Control Input Power
Protective Earth GND
Motor Input Power
Motor Input Power
Factory installed jumpers
C1 to L1
C2 to L2
Remove jumpers to use separate control
and motor mains AC power input.
R+
R-
C2
C1
L2
L1
Fuse Information
Aries Controller has no internal fuses. For safety,
you must provide a fuse in each of the AC input
lines. See the installation guide for detailed fuse
information.
Aries
Controller
Power Supply
120/240 VAC, 50-60Hz, single phase
Warning!
•
You must connect the unit’s protective conductor
terminal, marked with the earth symbol , to a reliable
system Protective Earth.
•
The unit’s connector strip terminals are at hazardous
voltages when power is applied to the Aries Controller,
and up to several minutes after power is removed.
Lower voltages may still be present for several minutes
after power is removed.
•
During normal operation, these high voltage terminals
must not be accessible to the user.
Ethernet Status LEDs
LED
State What it means
Ethernet Link/Activity
Ethernet Speed
Off
Yellow
Yellow, flashing
Off
Green
No Ethernet link detected
Ethernet link established;
no activity
Ethernet link established
and active
Ethernet 10Mbps
Ethernet 100Mbps
Ethernet Network Status LED
LED State
Off
Green
Red
Red/Green
What it means
Reset or not active
TCP connection on Port 5002 or 5006
UDP connection on Port 5003
Alternating; UDP & TCP connection active
IP Address Switches
The unit’s IP address is 192.168.100.xx, with the last octet xx set with the rotary
decimal switches. For example: to set to 14, rotate x10 switch to 1 and x1 switch
to 4. Valid range is 01 to 99; 00 is not valid. (Set the IP address of your PC to
192.168.100.yyy, where yyy ≠ xx.)
Ethernet
Network
Status
3
2
4
1
5
0
6
9
7
8
Drive
Controller
Status
Address
Switches
3
2
4
1
5
0
6
9
7
8
See the Aries Controller Hardware Installation Guide, Chapter 4, for more
information on how to set IP addresses for the Aries Controller and PC.
Drive Controller Status LEDs
LED State
Drive Enabled
Off
Yellow (flashes in Regen)
Yellow/Green (alternating)
Drive Disabled
Off
Yellow
Yellow
Yellow & 1 Green flash
Yellow & 2 Green flashes
Yellow & 3 Green flashes
Yellow & 4 Green flashes
—
Left
Right What it means
Green
Green
Green
Red
Off
Red
Red
Red
Red
Red
Enabled
Regeneration active
Autorun mode
No faults, or Ethernet boot (8 sec)
Motor control boot (4 sec
No bridge power
Bridge fault
Feedback fault
Thermal fault
Other fault
)