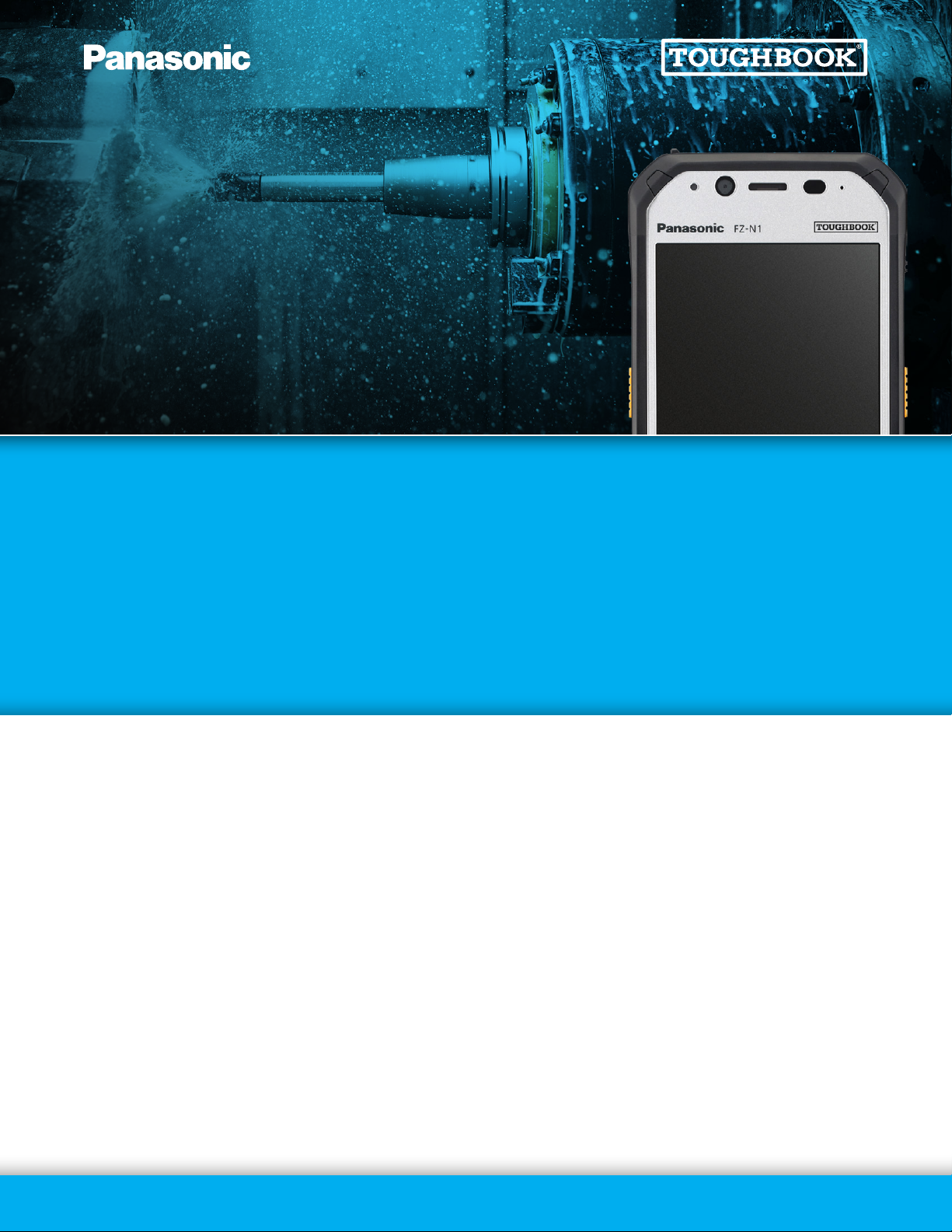
INDUSTRY 4.0:
A MOBILITY CHECKLIST
FOR MANUFACTURERS
THE SMART FACTORY
Today’s era of manufacturing automation is creating what is referred to as “the
smart factory.” A smart factory is described as a highly digitized and connected
manufacturing facility that relies on technologies like cloud computing, the
Internet of Things (IoT), robotics, big data and analytics, mobile technology, and
eventually artificial intelligence to streamline and improve operations.
Smart factories are the culmination of the Fourth
Industrial Revolution, referred to as Industry
4.0. In a smart factory, production processes are
flexible and run almost autonomously with the
ability to self-correct in real time. As a result,
employees are no longer focused on repetitive,
labor-intensive tasks but rather on handling
exceptions and higher-level work.
A 2017 CapGemini study found that early
adopters of Industry 4.0 have realized production
gains of 20 percent in their smart factories with
improvements in on-time delivery, productivity
and labor costs. With such impressive business
results, it’s no surprise that manufacturers are
INDUSTRY 4.0: A MOBILITY CHECKLIST FOR MANUFACTURERS
embracing the trend. The same study reports that
76 percent of manufacturers either have a smart
factory initiative in place or are in the process of
planning one.
MOBILE SOLUTIONS ENABLE INDUSTRY 4.0
Mobile devices connected to cloud-based
applications become the conduit through which
plant managers and workers access and act on
information across all areas of the plant, from the
warehouse to the shop floor. Employees work in
an agile, responsive environment that streamlines
operations and maximizes uptime with distributed
intelligence and insight delivered directly to their
devices and in real time.
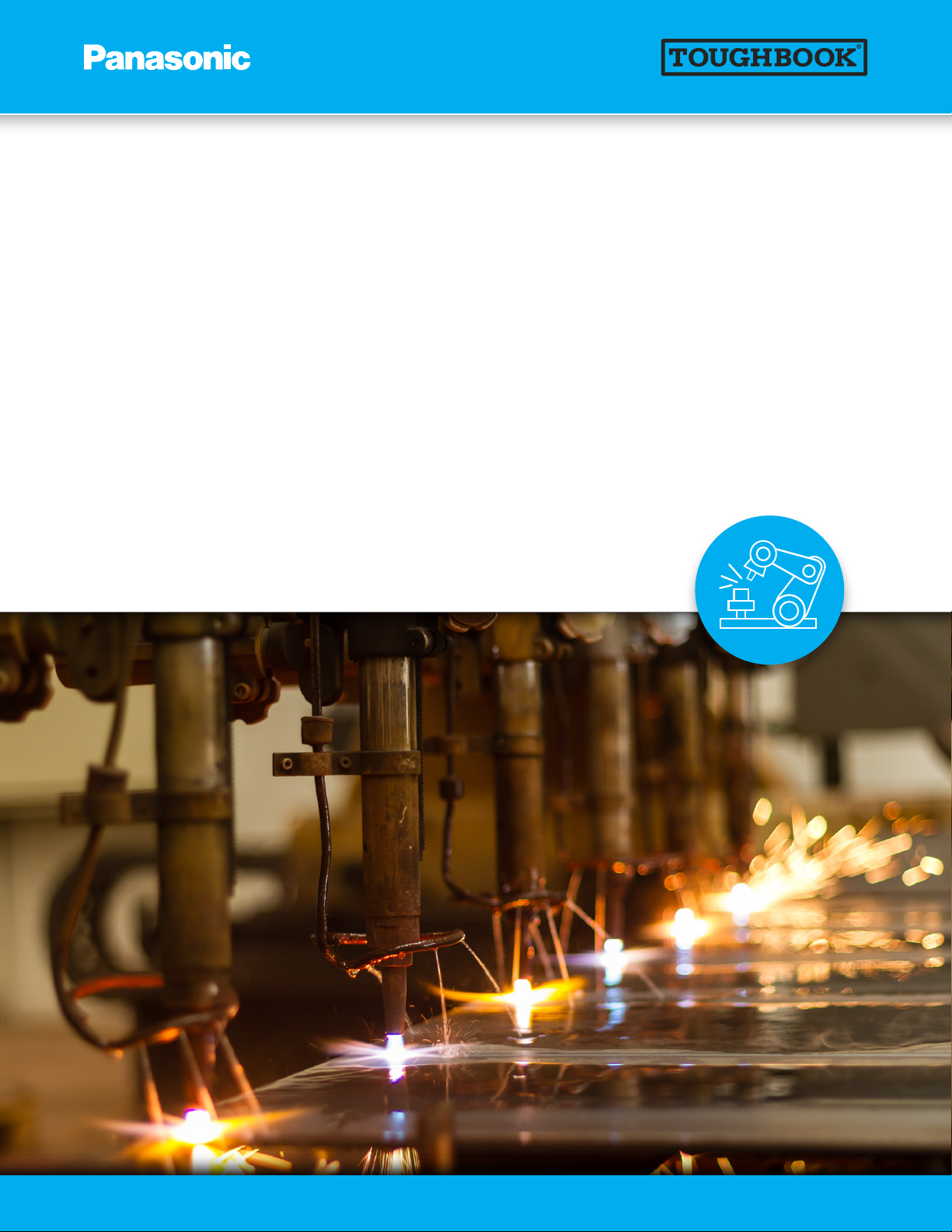
Achieving Industry 4.0 requires a complete digital
transformation of the factory environment with
Industrial Internet of Things (IIoT)-embedded
machines, cloud computing and big data
analytics, and machine-learning algorithms to
keep production on track. While the business
value may be clear, most factories still aspire
to be smart factories. Forrester reports 58
percent of manufacturers have launched digital
transformation initiatives while only 19 percent
have completed their journey. Mobile solutions
that connect workers and physical systems are
a crucial first step.
Early mobility initiatives can dramatically
improve worker productivity with better task
management. Companies further along will
be able to gain additional benefits by using
high-performing enterprise mobile devices
as powerful edge computing machines that
decrease latency by processing data closer
to the source.
The purpose of this guide is to help companies
select an enterprise mobile solution that
connects workers and plant managers to
production systems and the supply chain for
improved operational efficiency, increased
visibility and better decision-making across
manufacturing operations.
INDUSTRY 4.0: A MOBILITY CHECKLIST FOR MANUFACTURERS
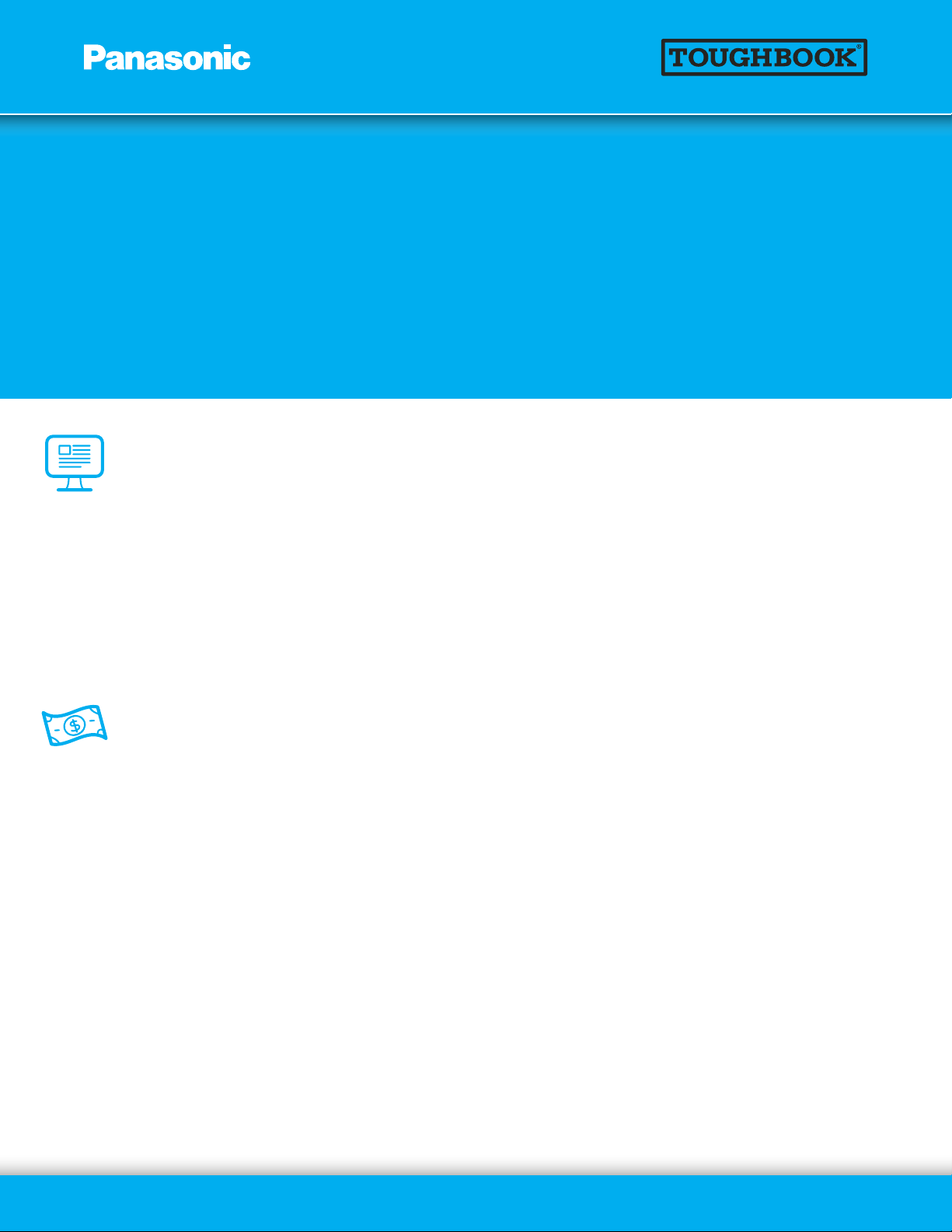
WHAT’S HOLDING MANUFACTURERS BACK?
Today many manufacturers are in the early stages of digitalization and still utilize
manual, paper-based processes across areas of operations. While most plants
are using mobile solutions for communications and notifications, they may have a
long way to go before they are fully mobile within a smart factory environment.
Some reasons for these delays include legacy equipment, the cost to upgrade
and challenging plant conditions.
LEGACY EQUIPMENT
Much factory equipment and systems are rooted in legacy technologies that don’t easily
connect to modern networking systems or take advantage of today’s powerful mobile devices.
While factory machinery continues to function as specified, the electronic interfaces built into
them may be technologically dated. For example, many of them require mobile devices that
connect to serial ports (RS-232) for data collection and control. Consumer-grade systems are
not equipped with these interface options, whereas enterprise-grade, rugged devices can be
equipped with these interface options.
For example, the Panasonic TOUGHBOOK 20, a fully rugged 2-in-1 laptop, and the
TOUGHPAD FZ-G1 tablet can be configured with serial, Ethernet, HDMI and USB connections.
COSTS TO UPGRADE
When evaluating the costs to upgrade to mobile technologies, manufacturers may be tempted
to first consider consumer devices and protective cases because of the perceived cost savings.
However, analyst data shows that rugged laptops and tablets deliver a higher return on
investment than consumer-grade devices, contributing to a lower total cost of ownership
(TCO). And while a price gap exists between consumer-grade mobile devices and
enterprise-grade rugged devices, the difference is shrinking.
The price differential is even smaller when decision makers consider the features and device
performance that manufacturers need to operate over full shifts or around-the-clock
operations. Rugged enterprise-grade devices, even at the higher price point, make even more
sense when you look at the true cost of a device over its lifetime—its TCO. Rugged devices are
more durable and better suited for the harsh manufacturing conditions, even over a consumer
device in a protective case.
TOUGHBOOK laptops, tablets and handhelds, for example, have a longer expected life cycle
than consumer devices and boast the lowest failure rate in the industry, even among other
rugged hardware. In situations where failure is not an option, TOUGHBOOK devices are more
INDUSTRY 4.0: A MOBILITY CHECKLIST FOR MANUFACTURERS