
AB (Fine Art) Airbrush
Customer Note: New “AB” Airbrushes are factory inspected for
immediate use.
The “A B ” A i rbru s h m aint e nance an d r e p lace m ent part s
instructions are for Airbrushes that have been used extensively
and require refurbishing.
HOW THE AB WORKS:
The illustration below gives you an idea what is going
on inside your AB. As the finger lever is pressed down, air
from your compressor is channeled from the air valve
through the body of the airbrush. The airstream then
splits, and part of the air is pushed across the edge of the
power wheel ( A ) while the rest goes through the airblast
tube ( B ). The edge of the power wheel is serrated, so
that the air pushing against it causes the power wheel to
spin. You will notice that the shaft on which the power
wheel rotates passes through a slot in the walking arm.
Actually, the portion of the shaft which rides in the slot is
offset from center, so that with a cam like action the
spinning of the power wheel causes the walking arm (and
thus the needle) to oscillate back and forth. The speed
regulator screw controls the speed of the power wheel
(and thus the walking arm and needle) by regulating the
volume of air pushing against the power wheel.
When you press down on the finger lever, you let air
into the airbrush and start the needle moving back and
forth. Then as you pull back on the finger lever, the
walking arm is pushed forward, and in turn the oscillating
needle is pushed into the stream of air coming from the
airblast tube. Thousands of times per minute, the needle
retracts into the needle bearing, picks up a coating of color
and then moves forward, drawing the color out of the
bearing and into the airstream, where the color is blown off
the needle and onto the surface you are painting. The
needle is tapered, so that as you pull back farther on the
finger lever, a thicker portion of the needle is exposed to
the airstream and a wider band of color is formed.
A line is thus formed by the action of the needle passing
back and forth in front of the stream of air coming from the
airblast jet, and you control the thickness of that line with
the finger lever. But the quality of that line and the ease
with which you can control it are affected by three other
INSTRUCTIONS AND PARTS LIST AB-8/31/2011
Supersedes Instructions & Parts List AB-10/29/2008
WARNING: Spray materials may be harmful if inhaled or
allowed to come into contact with the skin or eyes. Consult
the product label and Material Safety Data Sheet supplied
for the spray m aterial. Follow all safety precautions.
CAUTION: We ll Ventil at ed Area Required to rem ove
fumes, dust or overspray. Secu re ai rhose to A irbrush
with V-62 Wrench for safety a nd to prevent air leaks.
M a x i m u m A i r P r e s s u r e 5 0 P . S . I .
controls, all of which regulate the volume or the pressure
of the air passing through the airbrush.
METHODS OF CONTROL:
As menti o ned b efore , the speed regul a tor s crew
controls the volume of air hitting the power wheel, and so
controls the speed of the needle. The faster the needle
moves, the more color is being blown onto the surface you
are painting during a given length of time. If you want to
form a thin line, you can do so by having the needle
moving at a high speed and sweeping the airbrush very
quickly over your work, or by having the needle oscillating
much s lower and movi ng t he a irbru sh more slowl y.
Obviously the second method offers the most control and
is a major advantage of using the Paasche AB.
There is another method of controlling the speed of the
needle, however, and that is by adjusting the pressure of
the air coming into the airbrush. In this case, if you have
the speed regulator screw turned wide open (counterclockwise) with low air pressure (8-15 P.S.I.) from your air
source, the power wheel and needle will move slowly. But
the needle will also move slowly using a high air pressure
(25-35 P.S.I.) with the speed screw turned almost closed
(clockwise).
A comparable situation exists for the flow of air through
the airblast tube. The stipple adjuster screw restricts the
airflow through the airblast jet and across the needle.
When the air is almost closed off, a grainy or stippling
effect is created. But the same effect happens with the
stipple adjuster wide open using a very low air pressure.
As you can see, there are many different combinations
of settings for these three controls (the speed regulator,
the stipple a d juster, a n d the air p r e s s u r e ) e a c h
combination producing a characteristic effect, both in spray
pattern and handling of the airbrush.
Paasche Airbrush Company
4311 North Normandy Avenue
Chicago, IL 60634-1395
Phone: 773-867-9191 • Fax: 773-867-9198
Website: paascheairbrush.com
E-Mail: info@paascheairbrush.com
All AB needles should have a bow in them in
order t o be held securely by the needle
guide and enter the needle bearing properly.
Printed in the U.S.A.
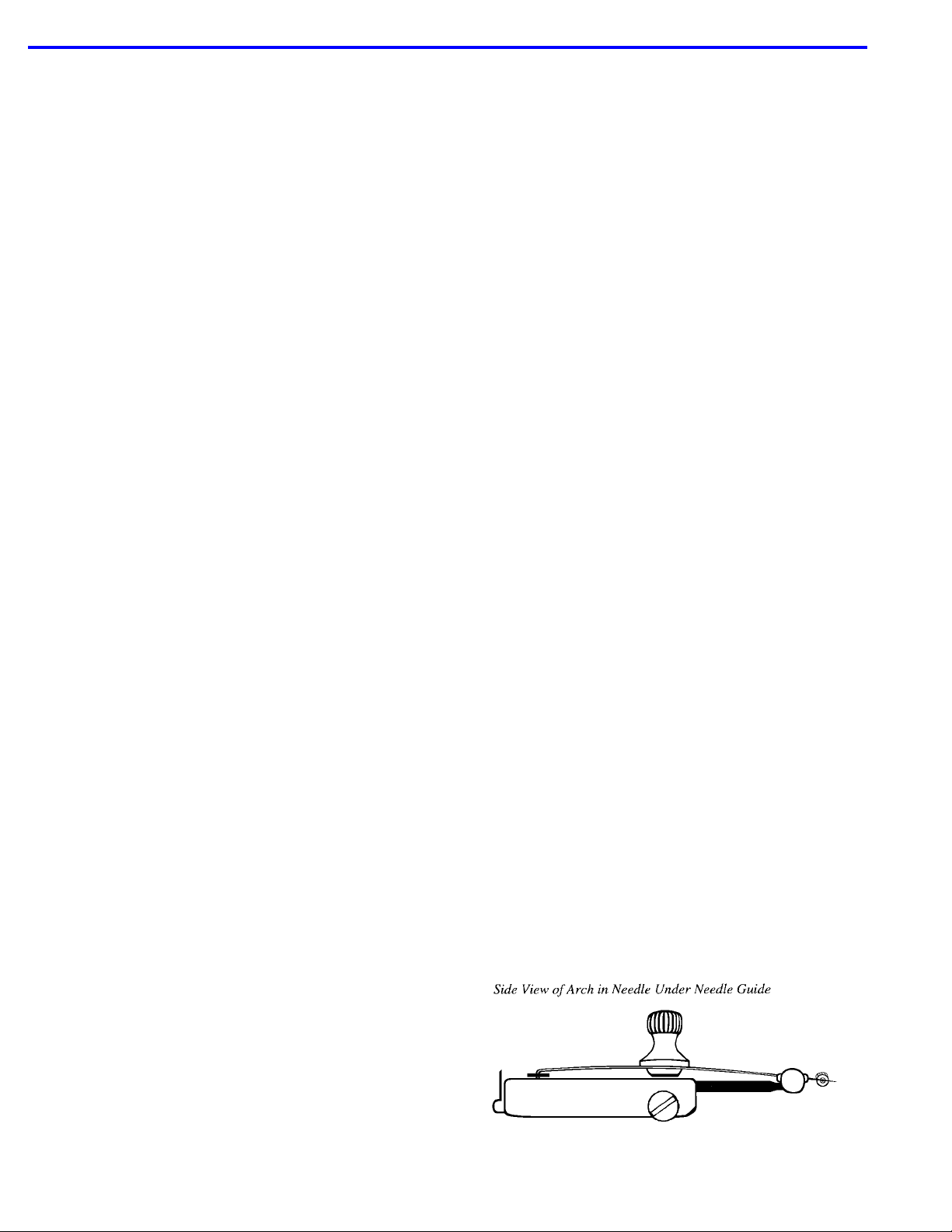
Page 2 Paasche AB (Fine Art) Airbrush Instructions and Parts List
BASIC PRECAUTIONS:
Before starting any adjustments or parts replacements,
a couple of precautions should be observed. The fine tip of
the needle is very delicate, and once damaged it is difficult
to straighten again. Remove the needle before beginning a
repair, or if necessary use an old needle. Secondly, most
of the threaded parts are made of brass, and the threads
are easily stripped. Do not force the parts to do what they
don’t want to do.
(See section “Speed Regulator Screw” for specific
example of this problem.)
ADJUSTING STIPPLE ADJUSTER & AIRBLAST JET:
The stipple adjuster is the screw at the elbow of the
airblast tube. It controls the airflow through the airblast
tube. By turning this screw in (clockwise), you restrict the
volume of air blown out the airblast jet and across the
needle. When the air is almost shut off you create a grainy,
stippling effect.
The threads of the stipple screw can become so loose
that it will not hold its position in the airblast tube and will
gradually turn out as you use the airbrush. As a preventive
measure, we suggest you avoid excessive turning in and
out of this screw. From the fully closed position, you only
need to turn the screw two full turns to fully open this little
valve.
If the screw is too loose, you can tighten the threads’ fit
by pressing a dab of beeswax onto the threads and rolling
the screw between your thumb and forefinger to work the
beeswax into the threads. Only a thin coating is needed.
Then pass the screw very briefly over a match flame,
melting the beeswax into the threads. The wax will adhere
better as you insert the screw back into the airblast tube.
SPEED REGULATOR SCREW:
This s crew w o r k s much the same as the s tipple
adjuster. It controls airflow and thus the speed of the
power wheel and the needle. Again, all the adjustments
happen within a range of two turns of the screw. As noted
before, do not try to force the screw tighter than it wants to
go. You can shear the head of the screw right off, leaving
the screw firmly embedded in the body of the airbrush,
impossible to remove.
POWER WHEEL TOP SHAFT BEARING ADJUSTING:
Adjusting shaft bearings is a procedure that should be
done only if the power wheel is sluggish, is intermittently
binding, or is completely stuck. To check this, remove the
needle, then try to operate the power wheel and walking
arm, pressing down the finger lever and moving it back
and forth. If the power wheel runs smoothly now, the
problem i s with your needle, not with the bearing
adjustments. If the problem continues, however, you will
need to adjust the bearings. If the power wheel is sluggish
or will not move at all, it could be that you simply need to
loosen the top bearing a little. Remove the top grease cap,
exposing the top shaft bearing. You will find the bearing
covered with grease, which you may want to remove in
order to see the slot in the top of the bearing better. To
adjust the bearing, use a screwdriver with a blade as wide
as the ope ning int o wh ich the bearing fits . A larg er
screwdriver can be filed down to fit exactly the slot in the
bearing. While pressing down on the finger lever for air,
slowly loosen the top bearing (turn counter-clockwise). If
the power wheel frees itself and begins to run smoothly,
yo u hav e fo und the prob lem. To adjus t th e bea ring
accurately, tighten it again until the power wheel stops,
then loosen it just until the power wheel runs smoothly.
This is a matter of 1/16 to 1/8 turn, never more than 1/4
turn. Do not loosen the bearing beyond the point where the
power wheel frees itself and runs smoothly. Beyond this
point the power wheel will begin to vibrate in the bearing. It
will appear to be running smoothly but then will suddenly
bog down. If this happens, tighten the bearing a little. You
will find the power wheel returns to normal speed.
If you find that the power wheel runs smoothly for a
while then freezes up ag ain, the problem is that the
threads in the power wheel cover have become too worn
to hold the bearing snugly in place. The power wheel
happens to spin in the same direction needed to tighten
the top shaft bearing. If the bearing does not fit snugly in
the power wheel cover, the power wheel will actually drag
the bearing until it stops the power wheel! The remedy for
this situation is the same as for the loose stipple adjuster
or speed control—work beeswax into the threads of the
bearing. Over a long time period, the beeswax will wear
out and this repair will have to be done again.
FINGER LEVER ADJUSTING SCREW:
This screw is located at the back of the finger lever, in
the lever fork, and adjusts the “rest position” of the finger
lever. When you turn the adjusting screw in, the walking
arm is pushed farther into the stream of air from the
airblast jet. By adjusting this screw you set the width of the
line created when the finger lever is simply depressed, but
not pulled back (the “rest position” spray width.) Note: In
the “farthest forward rest position” you get no spray if the
color cup is properly positioned.
Be careful with the two extremes of this adjustment. If
you t u r n t he adjusting s c r e w t o o far out ( c o u n t e r clockwise), the needle moves to the very end of the slot in
the walking arm, and the needle binds between this slot
and the slot in the color cup support. Always check that the
needle is at least a “hair’s breadth” from the very end of
the walking arm slot.
On some ABs, if you turn the adjusting screw too far in
(clockwise), the walking arm will be pushed too far forward
and will hit the front of the opening in the power wheel
cover through which it extends.
SHAPING THE NEEDLE:
In general an AB needle should be curved in two
directions. Viewed from the side the needle should have a
slight arch, so that the needle guide can hold it firmly in the
slot in the needle bearing. Viewed from the top, the needle
should curve underneath the lip of the needle guide screw.
Both arch and curve should be gradual bends along the
length of the needle, with no sudden bends or angles.
About 3/8 inch at the tip of the needle—that portion which
rides in and out of the needle bearing—should be left
straight. In fact, try not to touch the tip at all as you are
arching and curving the needle, for fear of distorting the
needle. Remember that you are shaping the needle to fit
your particular airbrush.
The arch (side view) of the needle does not need to be
too great—just enough to give a little tension when the
needle guide is screwed all the way down. With a more
extreme arch the tip of the needle rides in the bearing at
too great an angle. In addition, the motion of the needle is
not as smooth, because the crest of the arch is passing in
and out from under the needle guide.
Continued on page 3