
JUSP-NS500
PROFIBUS-DP unit
PROFIBUS-DP connectivity with positioning
functionality.
• Connects directly to the Sigma-II series drive
• Simplifies distributed control and information
management
• No programming languages are required.
• Various positioning functions including point-topoint mode (with multi-step speed positioning available) and station number mode (indexing function)
• All parameters are set and maintained by a
PLC or PC.
• Up to 126 servos can be connected to the
PROFIBUS-DP network
System configuration
Limit switches
contact sensors
Cable connection
NS500
JUSP-NS500
PROFIBUS-DP
6
(CN11) Computer connecting cable
(CN6) PROFIBUS-DP network
(CN4) External I/O or fully-closed encoder signal
CJ1 series
PROFIBUS-DP
master
SGDH-
Ver.
CHARGE POWER
CN3
CN1
CN2
SERVOPACK
Sigma-II
200V
series
Servo Drive
(CN10)
PROFIBUS-DP
SERVOPACK
SGDH-
Sigma-II
200V
Ver.
series
CHARGE POWER
Servo Drive
CN3
CN1
CN2
NS500
JUSP-NS500
PROFIBUS-DP
6
unit
Sigma-II series
Servo Motor
SERVOPACK
NS500
SGDH-
200V
Ver.
6
CHARGE POWER
CN3
CN1
CN2
SERVOPACK
NS500
SGDH-
200V
Ver.
CHARGE POWER
6
CN3
CN1
CN2
SERVOPACK
NS500
SGDH-
200V
Ver.
6
CHARGE POWER
CN3
CN1
Sigma-II series
CN2
Linear Motor
105PROFIBUS-DP unit
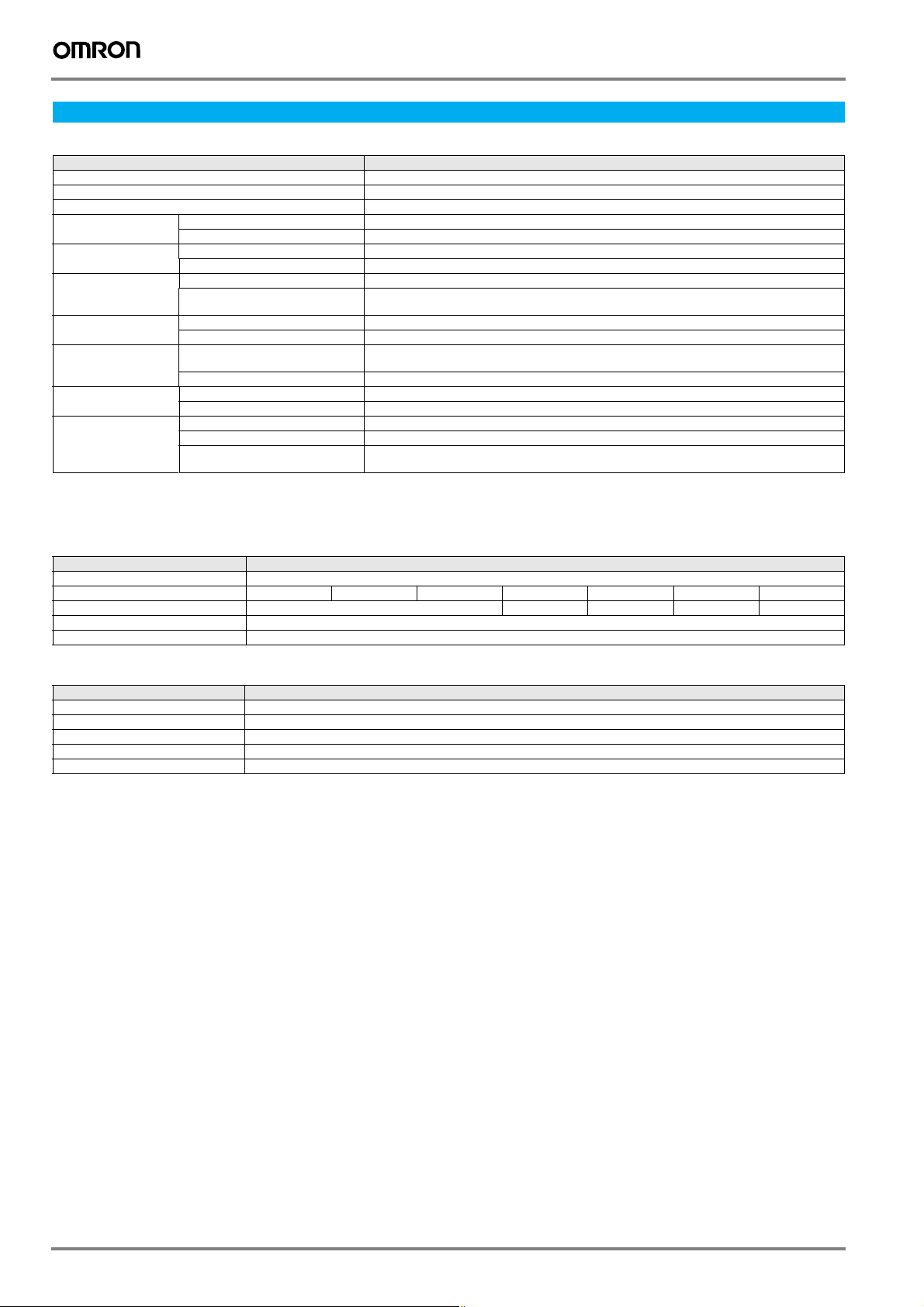
Specifications
JUSP-NS500 - PROFIBUS-DP interface unit
Item Details
Type JUSP-NS500
Applicable servo drive All SGDH-@@@E models
Installation method Mounted on the SGDH servo drive side: CN10.
Basic
specifications
PROFIBUS-DP
communications
Command format Operation specifications Positioning using PROFIBUS-DP communications
Position control
functions
Input signals Fixed allocation to SERVOPACK CN1
Output signals Servo drive CN1 connector
Internal functions Position data latch function Position data latching is possible using phase C, zero point signals, and external signals.
Note: *The allocation of the output signals for brake interlock, servo ready, or positioning completion can be changed using parameter settings.
Transmission specifications
Item Specifications
Communication format Conforms to PROFIBUS-DP
Transmission speed (kbps) 9.6 19.2 93.75 187.5 500 1500 12000
Transmission distance (m) 1200 1000 400 200 100
Transmission media STP cable
Number of stations 32 stations (can be extended to 126 stations using repeater.)
Power supply method Supplied from the servo drive control power supply.
Power consumption 1.3 W
Baud rate setting The baud rate is automatically set by the master between 9.6 kbps and 12 Mbps.
Station address setting Select the address from 0 to 7D (0 to 125) using the rotary switches.
Reference input PROFIBUS-DP communications
Acceleration/deceleration method Linear first/second-step, asymmetric, exponential, S-curve
Fully-closed control Possible
connector
NS500 unit Emergency stop signal
NS500 unit P1, P2 (area signals)
Protection Parameters damage, parameter setting errors, communications errors, etc.
LED indicators ERR: Module error
∗
Commands: motion commands (position, speed), parameter read/write
Forward/reverse run prohibited, zero point return deceleration LS, zero point signal,
external positioning signal
Servo alarm, brake interlock, servo ready, positioning completion
COMM: Communications status
Cable
Item Specifications
Cable type impedance Shielded twisted-pair wire type A 135 to 165 Ω
Capacity < 30 pf/m
Loop resistance 110 Ω/km
Wire gage 0.64 mm
Conductor area > 0.34 mm
2
Connector
9-pin D-sub connectors are used.
106 Motion controllers