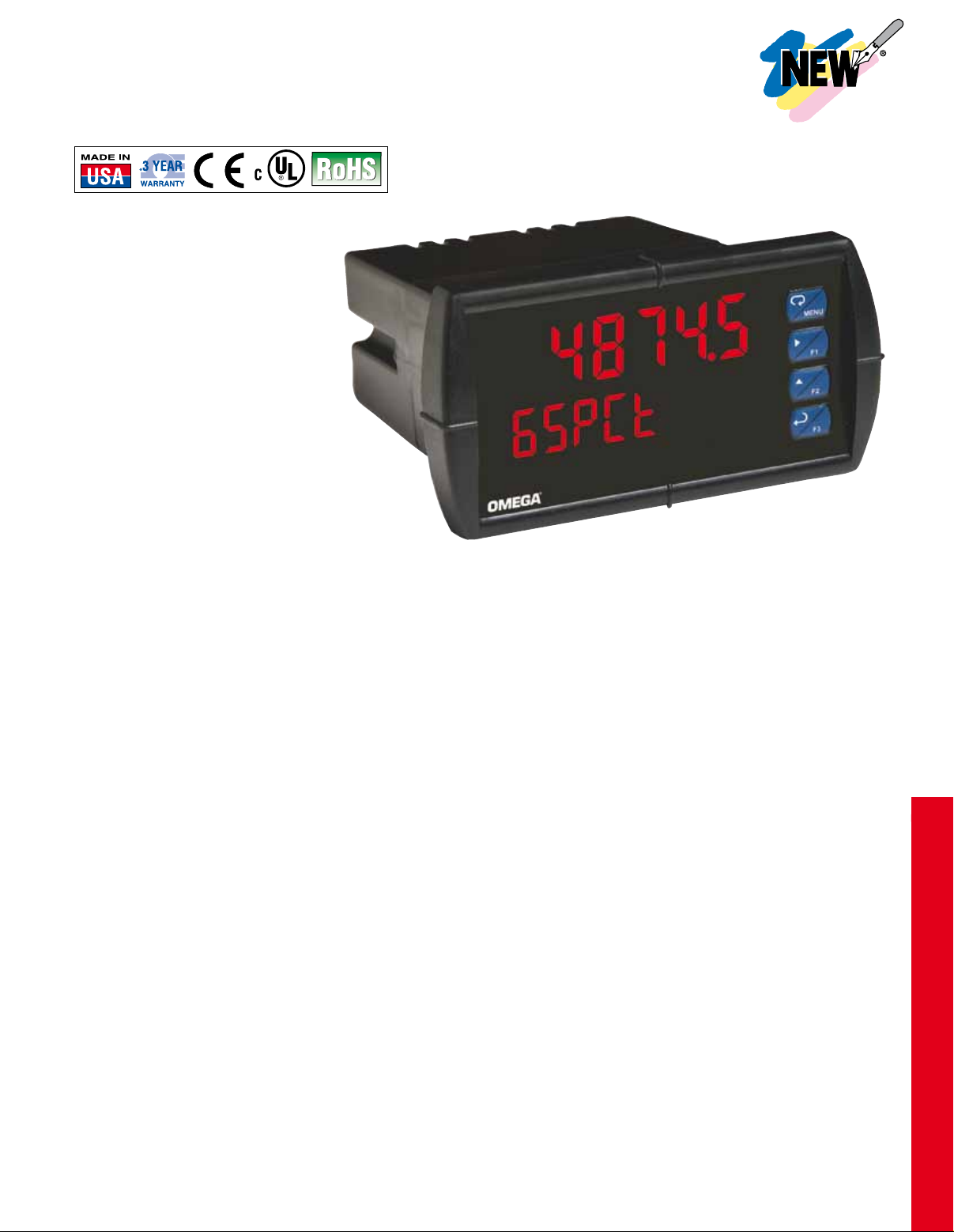
1
⁄8 DIN Process Panel Meter
With Optional USB Communications
DP6000 Series
U Modular USB,
RS232, RS485 Serial
Communication Options
and Relays
U 0 to 20 mA, 4 to 20 mA,
0 to 5V, 1 to 5V, and
±10V Inputs
U NEMA 4X (IP65) Front
U Universal 85 to 265 Vac
or 12/24 Vdc Input Power
U Large Dual-Line
6-Character Display,
15 and 12 mm
(0.60 and 0.46")
U Sunlight Readable
Display Models
U Isolated 24 Vdc @
200 mA Transmitter
Power Supply Standard
U Programmable Displays
and Function Keys
U 32-Point, Square
Root, or Exponential
Linearization
U MODBUS® RTU
Communication
Protocol Standard
U Free Software for
Operation, Monitoring
and Programming
The DP6000 Series meter boasts
specifications and functionality
that clearly make it one of the
most advanced process meters
available. Its dual-line 6-digit
display (999,999), advanced
signal input conditioning functions,
function keys, MODBUS RTU
serial communications, and
optional expansion modules
are only a few of the features
found on the DP6000. Sunlight
readable display models have an
extraordinarily bright LED display.
They are perfect for applications
where the meter is in direct
sunlight or in applications where
visibility may be impaired by
smoke, fog, dust, or distance.
The upper display can be
programmed to indicate PV,
maximum (peak), minimum
(valley), alternating maximum/
minimum, one of eight alarm
set points, or MODBUS input.
The lower display can also be
configured to display engineering
units, set points, user defined
legends, or simply turned off. The
user friendly dual-line display
makes the DP6000 easy to set
up and program. No jumpers to
set for input selection. All setup
and programming are done via
the front panel. Three levels of
password protection help maintain
the reliability of the programming.
The Copy feature is used to copy
(or clone) all the settings from
one DP6000 to other meters in
about 20 seconds! The Copy
function is a standard feature on
all meters. It does not require a
communications adaptor, only an
optional cable assembly.
General Specifications
Display: Both displays are 6 digits
(-99999 to 999999), red LEDs with
leading zero blanking
Upper Display: 15 mm (0.60") high
Lower Display: 12 mm (0.46") high
Display Intensity: 8 intensity levels
Display Update Rate: 5/second
(200 ms)
Overrange: Display flashes 999999
Underrange: Display flashes -99999
M-1
Display Assignment: The upper
and lower displays may be assigned
to PV1, PV2, PCT (percent),
max/min, alternate max and min,
set points, units (lower display only),
or MODBUS input
Front Panel: NEMA 4X (IP65)
Programming Methods: 4 front
panel buttons, digital inputs, PC and
software, MODBUS registers, or
cloning using copy function
Noise Filter: Programmable from
2 to 199 (0 will disable filter)
Filter Bypass: Programmable from
0.1 to 99.9% of calibrated span
Recalibration: Calibrated at the
factory. Recalibration is recommended
at least every 12 months
Max/Min Display: Max (peak)/
min (valley) readings reached by
the process are stored until reset
by the user or until power to the
meter is cycled
Password: 3 programmable
passwords restrict modification of
programmed settings; Pass 1: Allows
use of function keys and digital
inputs; Pass 2: Allows use of function
keys, digital inputs and editing set/
reset points; Pass 3: Restricts all
programming, function keys, and
digital inputs
DP6000 shown smaller
than actual size.
M
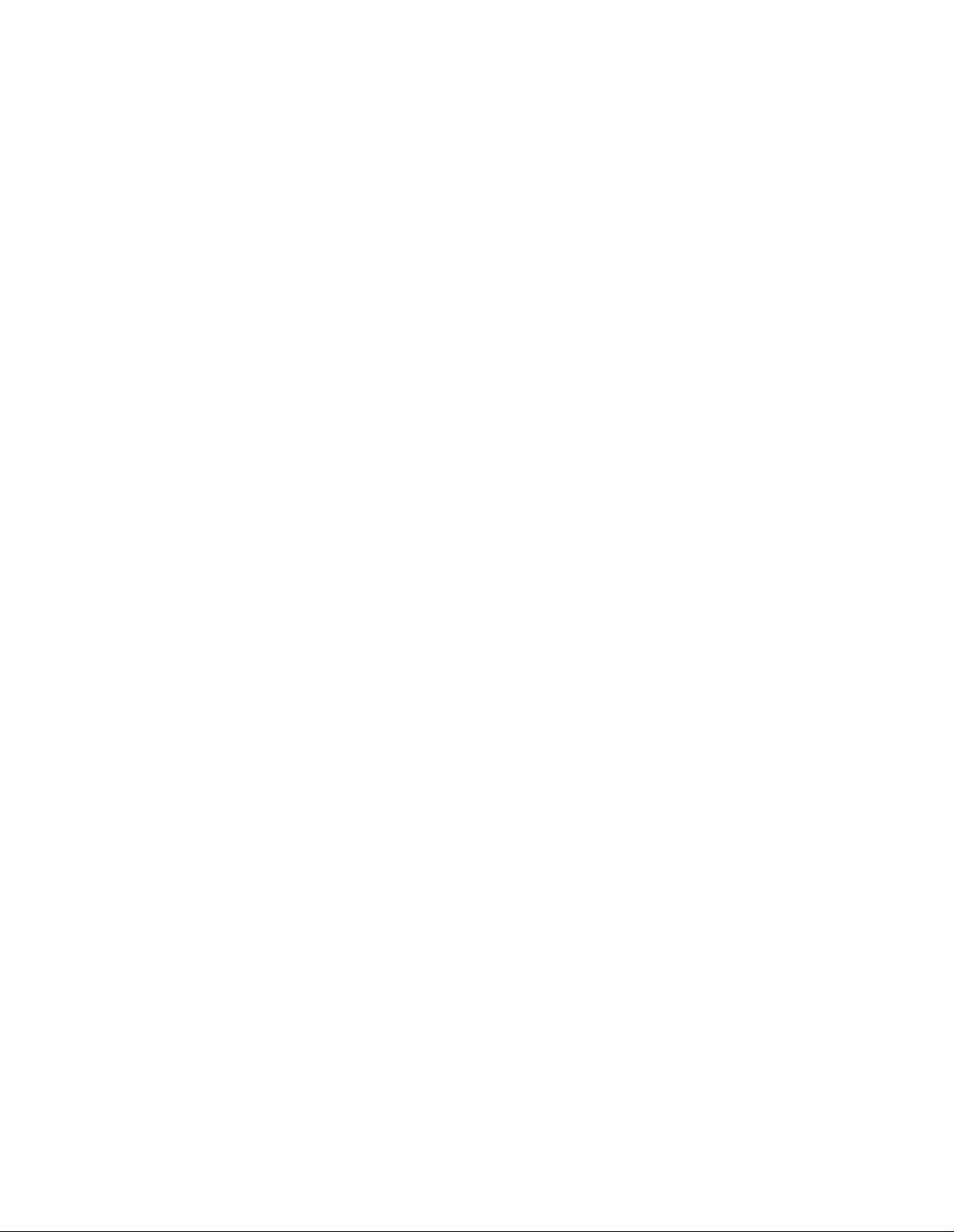
Non-Volatile Memory: All
programmed settings are stored in
non-volatile memory for a minimum of
ten years if power is lost
Power Options: 85 to 265 Vac
50/60 Hz, 90 to 265 Vdc, 20 W max,
or jumper selectable 12/24 Vdc ±10%,
15 W max
Fuse (External, Required): UL
recognized, 5 A max, slow blow; up
to 6 meters may share one 5 A fuse
Isolated Transmitter Power
Supply: 24 Vdc ±5% @ 200 mA
max (standard), (12/24 Vdc powered
models rated @ 100 mA max); 5 or
10 Vdc @ 50 mA max, selectable with
internal jumper J4
Normal Mode Rejection: Greater
than 60 dB at 50/60 Hz
Isolation: 4 kV input/output-to-power
line; 500 V input-to-output or
output-to-P+ supply
Overvoltage Category: Installation
overvoltage category II; local level
with smaller transient overvoltages
than installation overvoltage
category III
Operating Temperature Range:
-40 to 65°C (-40 to 149°F)
Storage Temperature Range:
-40 to 85°C (-40 to 185°F)
Relative Humidity: 0 to 90%
non-condensing
Connections: Removable screw
terminal blocks accept 12 to 22
AWG wire, RJ45 for external relays,
digital I/O, and serial communication
adaptors
Enclosure:
plastic, UL 94V-0, color: black
Mounting:
required: 92 x 45 mm (3.622 x
1.772"); two panel mounting bracket
assemblies are provided
Tightening Torque: Screw terminal
connectors: 5 lb-in (0.56 Nm)
Overall Dimensions:
119 W x 62 H x 143 mm D
(4.68 x 2.45 x 5.64")
Weight: 269 g (9.5 oz)
1
⁄8 DIN, high impact
1
⁄8 DIN panel cutout
Process Input
Input: Field selectable: 0 to 20 mA,
4 to 20 mA, ±10 Vdc (0 to 5, 1 to 5,
0 to 10V), MODBUS PV (slave)
Accuracy: ±0.03% of calibrated
span ±1 count, square root and
programmable exponent accuracy
range: 10 to 100% of calibrated span
Temperature Drift: 0.005% of
calibrated span/°C max from 0 to 65°C
ambient, 0.01% of calibrated span/°C
max from -40 to 0°C ambient
Signal Input Conditioning Function:
Linear, square root, programmable
exponent, or round horizontal tank
volume calculation
Multi-Point Linearization:
2 to 32 points for PV or PV1;
2 to 8 points for PV2 (dual-scale
level feature)
Programmable Exponent:
1.0001 to 2.9999
Low-Flow Cutoff: 0 to 999999
(0 disables cutoff function)
Decimal Point: Up to 5 decimal
places or none: d.ddddd, dd.dddd,
ddd.ddd, dddd.dd, ddddd.d, or dddddd
Calibration Range:
4 to 20 mA: Minimum span;
input 1 and Input 2: 0.15 mA
±10 V: Minimum span;
input 1 and 2: 0.10 V
An Error message will appear if input
1 and input 2 signals are too close
together
Input Impedance:
Voltage Ranges: Greater than
1 MΩ
Current Ranges: 50 to 100 Ω
(depending on resettable fuse
impedance)
Input Overload: Current input
protected by resettable fuse, 30 Vdc
max; fuse resets automatically after
fault is removed
Relays
Rating: 2 or 4 SPDT (Form C) internal
and/or 4 SPST (Form A) external;
rated 3 A @ 30 Vdc and 125/250 Vac
resistive load; 1/14 HP (≈ 50 W)
@ 125/250 Vac for inductive loads
such as contactors, solenoids, etc.
Noise Suppression:
Recommended for each relay
contact switching inductive loads
Deadband: 0 to 100% of span, user
programmable
High or Low Alarm: User may
program any alarm for high or low trip
point; unused alarm LEDs and relays
may be disabled (turned off)
Relay Operation: Automatic (nonlatching), latching (requires manual
acknowledge), sampling (based on
time), pump alternation control
(2 to 8 relays), off (disable unused
relays and enable interlock feature,
manual on/off control mode)
Time Delay: 0 to 999.9 seconds,
on and off relay time delays;
programmable and independent for
each relay
Fail-Safe Operation: Programmable
and independent for each relay
Note: Relay coil is energized in non-alarm
condition. In case of power failure, relay
will go to alarm state.
Auto Initialization: When power is
applied to the meter, relays will reflect
the state of the input to the meter
Serial Communications
Protocol: MODBUS RTU
Meter Address/Slave ID: 1 - 247
Baud Rate: 300 to 19,200 bps
Transmit Time Delay: Programmable
between 0 and 199 ms
Data: 8 bit (1 start bit, 1 or 2 stop bits)
Parity: Even, odd, or none with 1 or 2
stop bits
Byte-to-Byte Timeout:
0.01 to 2.54 seconds
Turn Around Delay:
Less than 2 ms (fixed)
Isolated 4 to 20 mA
Transmitter Output
Output Source:
max, min, set points 1 through 8,
manual control setting, or
MODBUS input
Scaling Range: 1.000 to 23.000 mA
for any display range
Factory Calibration: 4.000 to
20.000 = 4 to 20 mA output
Analog Output Programming:
23.000 mA maximum for all
parameters: overrange, underrange,
max, min, and break
Accuracy: ± 0.1% of span ± 0.004 mA
Temperature Drift: 0.4 µA/°C
maximum from 0 to 65°C ambient,
0.8 µA/°C maximum from -40 to
0°C ambient
Note: Analog output drift is separate from
input drift.
Isolated Transmitter Power Supply:
Terminals I+ & R: 24 Vdc ± 5% @
40 mA maximum, may be used to power
the 4 to 20 mA output or other devices
External Loop Power Supply:
35 Vdc maximum
Output Loop Resistance:
24 Vdc Power Supply:
10 Ω minimum, 700 Ω maximum
35 Vdc (External) Power Supply:
100 Ω minimum, 1200 Ω maximum
Process variable (PV),
Digital I/O Expansion
Module
Channels: 4 digital inputs and
4 digital outputs per module
System: Up to 2 modules for a total of
8 inputs and 8 outputs
Digital Input Logic:
High: 3 to 5 Vdc
Low: 0 to 1.25 Vdc
Digital Output Logic:
High: 3.1 to 3.3 Vdc
Low: 0 to 0.4 Vdc
Source Current: 10 mA maximum
Sink Current: 1.5 mA minimum
+5 V Terminal: To be used as pull-up
for digital inputs only
4-Relay Expansion Module
Relays: 4 Form A (SPST) rated 3 A @
30 Vdc and 125/250 Vac resistive load;
1/14 HP (≈ 50 W) @ 125/250 Vac for
inductive loads
M-2

Meter Copy
The Copy feature is used to copy (or
clone) all the settings from one DP6000
to other DP6000 meters in about
20 seconds! The Copy function is a
standard feature on all meters. It does
not require a communications adapter,
only an optional cable assembly, model
number DPA1200. See the ordering
information for complete details
NEMA 4X Field Enclosures
Thermoplastic NEMA 4X
enclosures are constructed for
either indoor or outdoor use.
DP6000 with DPA2812 NEMA 4X
field enclosure, shown smaller
than actual size.
Accessories
Model No. Description
DPA1004
DPA1044
DPA1232
DPA1485
DPA8008
DPA7485-I
DPA7485-N
DPA8232-N
DPA8485-I
DPA8485-N
DPA1002
DPA1200
DPA2811
DPA2812
Comes complete with 2 side mounting brackets, software, and operator’s manual.
Ordering Example: DP6000-6R2, process panel meter with 2 relays, and DPA8008, USB serial adaptor.
OCW-2, OMEGACARESM extends standard 3-year warranty to a total of 5 years.
4-relay expansion module - field installable
4 digital inputs and 4 digital outputs module - field installable
RS232 serial adaptor - field installable
RS485 serial adaptor - field installable
USB serial adaptor - field installable
RS232 to RS422/485 isolated converter - field installable
RS232 to RS422/485 non-isolated converter - field installable
USB to RS232 non-isolated converter - field installable
USB to RS422/485 isolated converter - field installable
USB to RS422/485 isolated converter - field installable
DIN rail mounting kit for 2 expansion modules
Meter copy cable
Plastic NEMA 4X enclosure for one DP6070 temperature meter
Plastic NEMA 4X enclosure for two DP6070 temperature meters
Model No. Description
Standard 85 to 265 Vac Models
DP6000-6R0
DP6000-6R2
DP6000-6R3
DP6000-6R4
DP6000-6R5
DP6000-6R7
Standard 12/24 Vdc Low Voltage Models
DP6000-7R0
DP6000-7R2
DP6000-7R3
Sunlight Readable Models, 85 to 265 Vac
DP6000-6H0
DP6000-6H2
DP6000-6H3
Sunlight Readable Models, 12/24 Vdc Low Voltage
DP6000-7H0
DP6000-7H2
DP6000-7H3
Process panel meter
Process panel meter with 2 relays
Process panel meter with 4 to 20 mA output
Process panel meter with 4 relays
Process
Process
Process panel meter
Process panel meter with 2 relays
Process panel meter with 4 to 20 mA output
Process panel meter
Process panel meter with 2 relays
Process panel meter with 4 to 20 mA output
Process panel meter
Process panel meter with 2 relays
Process panel meter with 4 to 20 mA output
M-3
panel meter with 2 relays and 4 to 20 mA output
panel meter with 4 relays and 4 to 20 mA output
To Order Visit omega.com/dp6000 for Pricing and Details
M