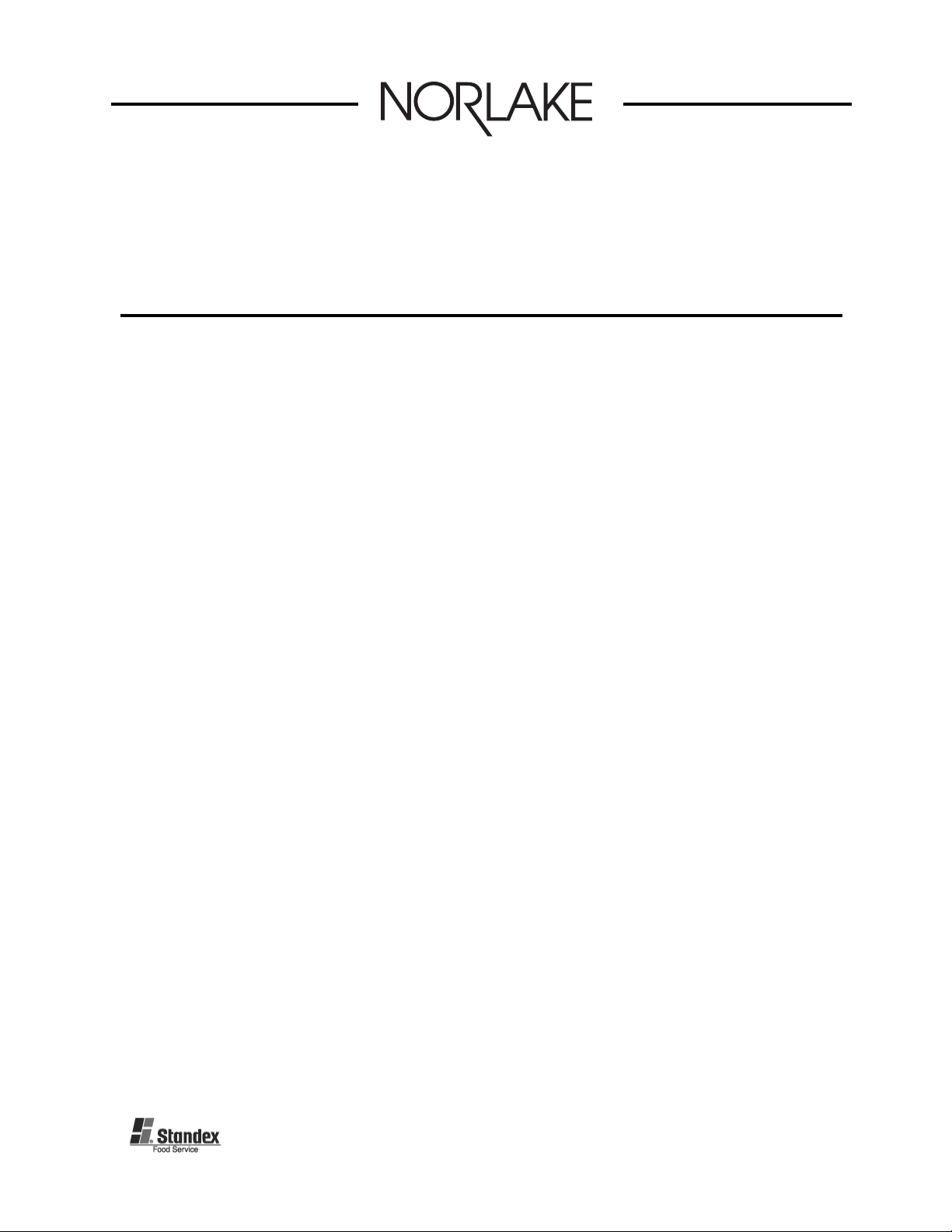
®
DAIRY QUEEN
BLIZZARD STATION™
Installation, Operation and
Maintenance Instructions
INSPECTION
When the equipment is received, all items should be carefully checked against the bill of
lading to insure all crates and cartons have been received. All units should be inspected
for concealed damage by uncrating the units immediately. If any damage is found, it
should be reported to the carrier at once, and a claim should be filed with the carrier. This
equipment has been inspected and tested in the Nor-Lake Manufacturing Facility and
has been crated in accordance with transportation rules and guidelines. Manufacturer is
not responsible for freight loss or damage.
INSTALLATION
GENERAL
After the unit crate and crate base have been removed, locate the casters found inside
the cabinet. Attach the casters to the base of the unit by screwing them into the same
threaded fittings that were used to secure the crate base to the cabinet. Insure that the
casters are screwed all the way into the base.
LOCATION
The refrigeration system of the cabinet requires free air access for proper operation.
Bumpers have been attached to the back of the cabinet to allow for the appropriate
clearance from a wall. Once the cabinet is placed in its permanent location it should be
leveled from side to side and front to back. Fresh water and drain connections must be
made in accordance with Federal, State, and Local code requirements.
© 2005 Nor-Lake, Inc. 11/05 110199
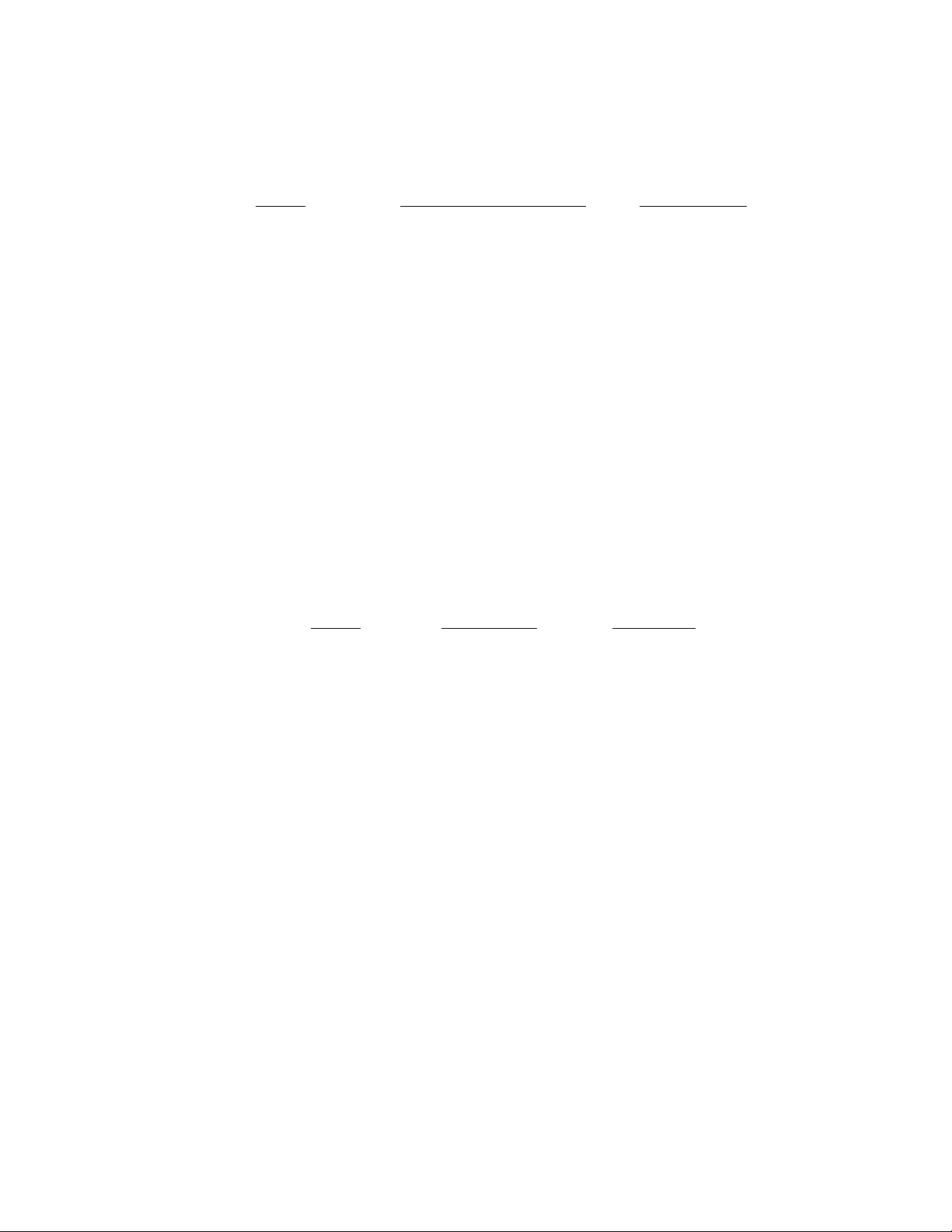
Physical Specifications
Unit Exterior Dimensions Refrigerant
Model Width x Depth x Height
ZR112 54" x 32" x 44-3/4" See Serial Tag
ELECTRICAL
Check the proposed outlet to be used to insure that the voltage, phase, and current
carrying capacity of the circuit from the electrical panel correspond to the requirements of
the cabinet. Never use an extension cord to run power to the unit. Refer to the serial tag
for all pertinent electrical information.
Observe all Warning Labels. Disconnect power supply to eliminate electrical shock
and injury from moving parts when servicing equipment.
Type/Amount
Electrical Data
Unit Type of
Model Connection
ZR112 Cord 115/60/1
Volt/Hz/Ph
OPERATION
The Blizzard Merchandising Cabinet employs a cold wall evaporator located inside the
topping rail. During the refrigeration process, heat is removed through the evaporator
tubing and expelled through the condensing unit. In order to assure proper airflow, make
certain the flow of air behind the cabinet and through the front louver is not restricted.
The refrigeration system on this cabinet uses a temperature thermostat that senses the
cut-in and cut-out temperatures of the cold wall evaporator coil. The topping rail
temperature can be adjusted by turning the thermostat control knob that is located on the
inside of the cabinet on the condenser cover.
2
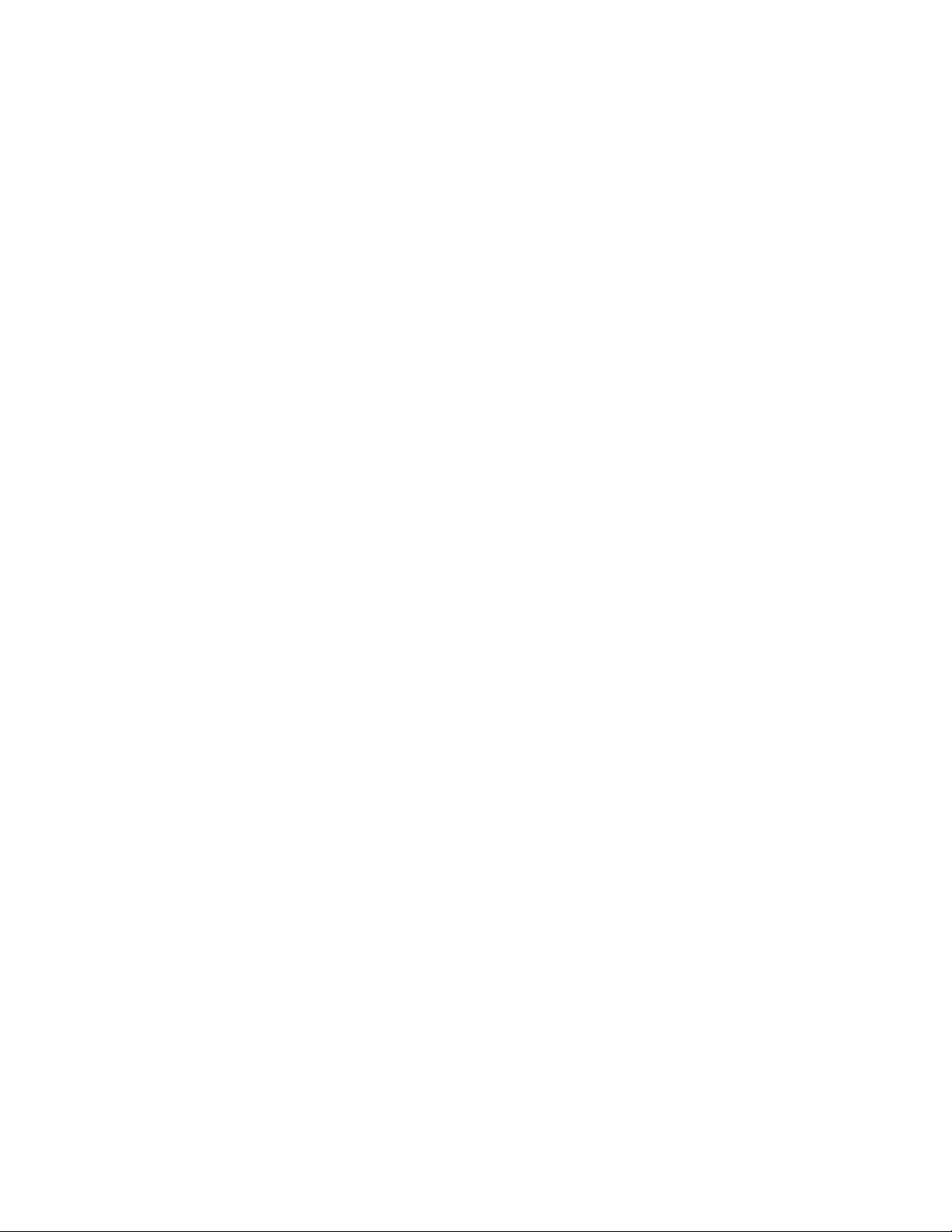
MAINTENANCE
PERIODIC CLEANING
Beginning with the initial installation, the interior surfaces of the cabinet and topping well
should be periodically wiped down with a solution of warm water and baking soda. This
solution will remove any odors that may occur as a result of spillage. The exterior of the
cabinet should also be cleaned frequently with a commercial grade of glass cleaner. The
plastic "safe edging" material should be removed periodically and cleaned in a sink with
soap and water, dried, and replaced on the unit. Caution: Do not use any abrasive or
alkaline solutions to clean the cabinet.
Important: Monthly cleaning of the condenser coil will aid the heat transfer characteristics
of the refrigeration system and keep it operating at top efficiency. The condenser coil is
located inside the cabinet and can be accessed by removing the condenser cover. The
condenser cover has a label identifying it and reminding the user to clean the condenser
coil monthly. Failure to keep the condenser coil clean could result in temperature loss
and damage to the compressor.
Disconnect the power before cleaning the condenser coil to prevent injury. Remove the
condenser cover and use a soft brush to loosen the lint and dirt attached to the fins. After
this has been accomplished, use a vacuum cleaner to remove the loosened particles.
All moving parts have been permanently lubricated and will generally require no
maintenance.
SERVICE
Any correspondence pertaining to this cabinet should be directed to the Service
Department of Nor-Lake, Incorporated. Be sure to include the cabinet model number and
serial number with any correspondence.
800-388-5253 Parts/Service
Nor-Lake, Incorporated 800-388-5253 Parts/Service
727 Second Street 800-955-5253 Sales
P.O. Box 248 715-386-2323
Hudson, Wisconsin 54016 715-386-6149 FAX
3
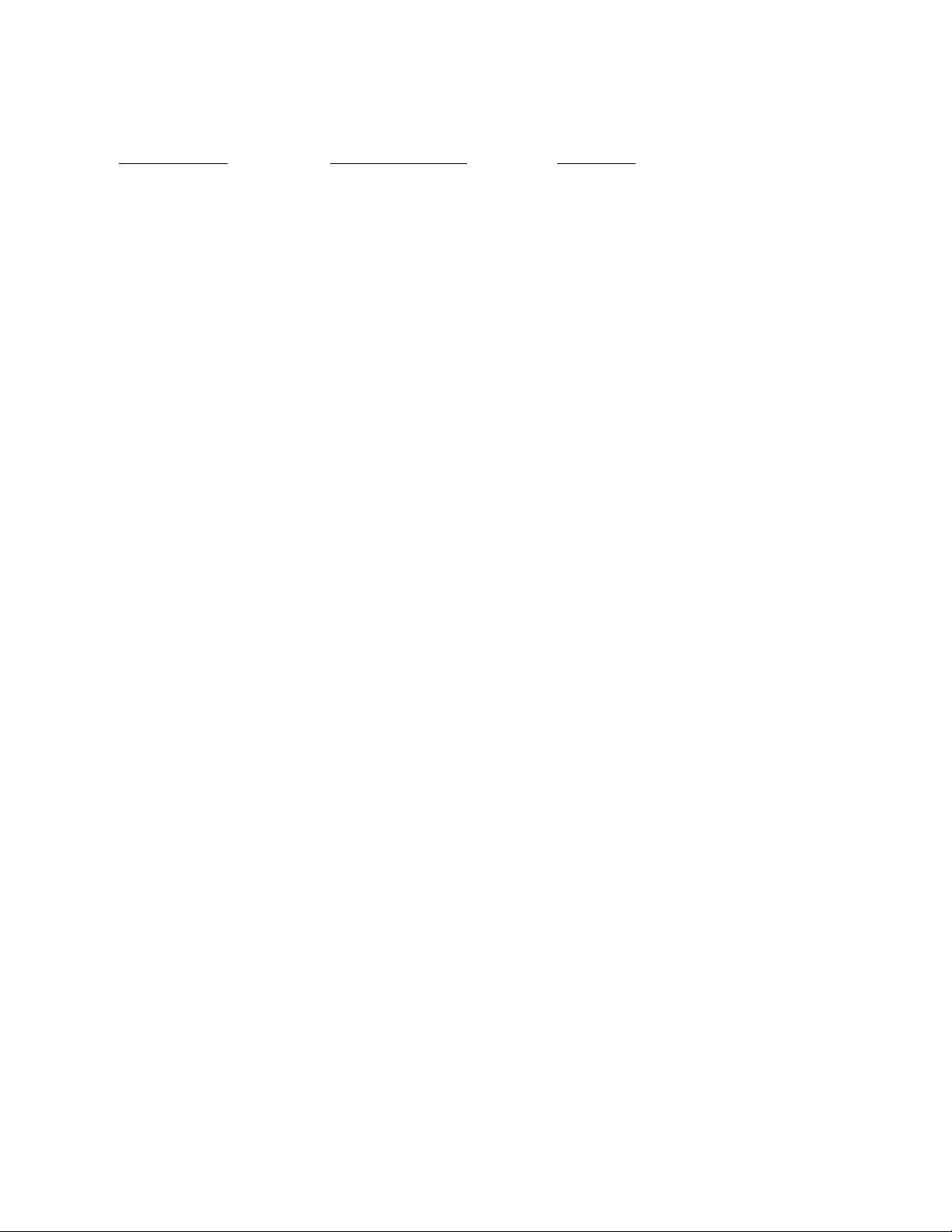
MAINTENANCE SERVICE AND ANALYSIS GUIDE
REFRIGERATION SYSTEMS - ALL MODELS
MALFUNCTION POSSIBLE CAUSE
Compressor will not start - 1. Service cord unplugged 1. Plug in service cord
no hum 2. Fuse blown or removed 2. Replace fuse
3. Overload tripped 3. Determine reasons and correct
4. Control stuck open 4. Repair or replace
5. Wiring incorrect 5. Check wiring against the diagram
Compressor will not start - 1. Improperly wired 1. Check wiring against the diagram
hums but trips on overload 2. Low voltage to unit 2. Determine reason and correct
protector 3. Starting capacitor defective 3. Determine reason and replace
4. Relay failing to close 4. Determine reason, correct or replace
Compressor starts and runs, 1. Low voltage to unit 1. Determine reason and correct
but short cycles on overload 2. Overload defective 2. Check current, replace overload protector
protector 3. Excessive head pressure 3. Check ventilation or restriction in
refrigeration system
4. Compressor hot-return gas hot 4. Check refrigerant charge, fix leak if
Compressor operates long 1. Short of refrigerant 1. Fix leak, add refrigerant
or continuously 2. Control contact stuck 2. Repair or replace
3. Evaporator coil iced 3. Determine cause, defrost manually
4. Restriction in refrigeration 4. Determine location and remove restriction
system
5. Dirty condenser 5. Clean condenser
Compressor runs fine, but 1. Overload protector 1. Check wiring diagram
short cycles 2. Cold control 2. Differential too close - widen
3. Overcharge 3. Reduce charge
4. Air in system 4. Purge and recharge
5. Undercharge 5. Fix leak, add refrigerant
SOLUTION
necessary
Starting capacitor open, 1. Relay contacts stuck 1. Clean contacts or replace relay
shorted or blown 2. Low voltage to unit 2. Determine reason and correct
Relay defective or burned out 1. Incorrect relay 1. Check and replace
Refrigerated space too warm 1. Control setting too high 1. Reset control
Standard temperature system 1. Control setting is too low 1. Reset the control
freezes the product 2. Control points stuck 2. Replace the control
Objectionable noise 1. Fan blade hitting fan shroud 1. Reform or cut away small section of shroud
Pan Area 1. No cooling 1. Make sure switch is in the "on" position
3. Improper relay 3. Replace
2. Voltage too high or too low 2. Determine reason and correct
2. Refrigerant overcharge 2. Purge refrigerant
3. Dirty condenser 3. Clean condenser
4. Evaporator coil iced 4. Determine reason and defrost
5. Not operating 5. Determine reason, replace if necessary
2. Tubing rattle 2. Locate and reform
3. Vibrating fan blade 3. Replace fan blade
4. Condenser fan motor rattles 4. Check motor bracket mounting, tighten
5. General vibration 5. Compressor suspension bolts not loosened
on applicable models - loosen them
6. Worn fan motor bearings 6. Replace fan motor
2. Too cold 2. Adjust temperature control - see instructions
under pan area
3. Too warm 3. Adjust temperature control - see instructions
under pan area
Nor-Lake, Inc. • PO Box 248 • Hudson, WI 54016 • 800-388-5253 Service • 715-386-2323 Sales • 715-386-6149 FAX
4