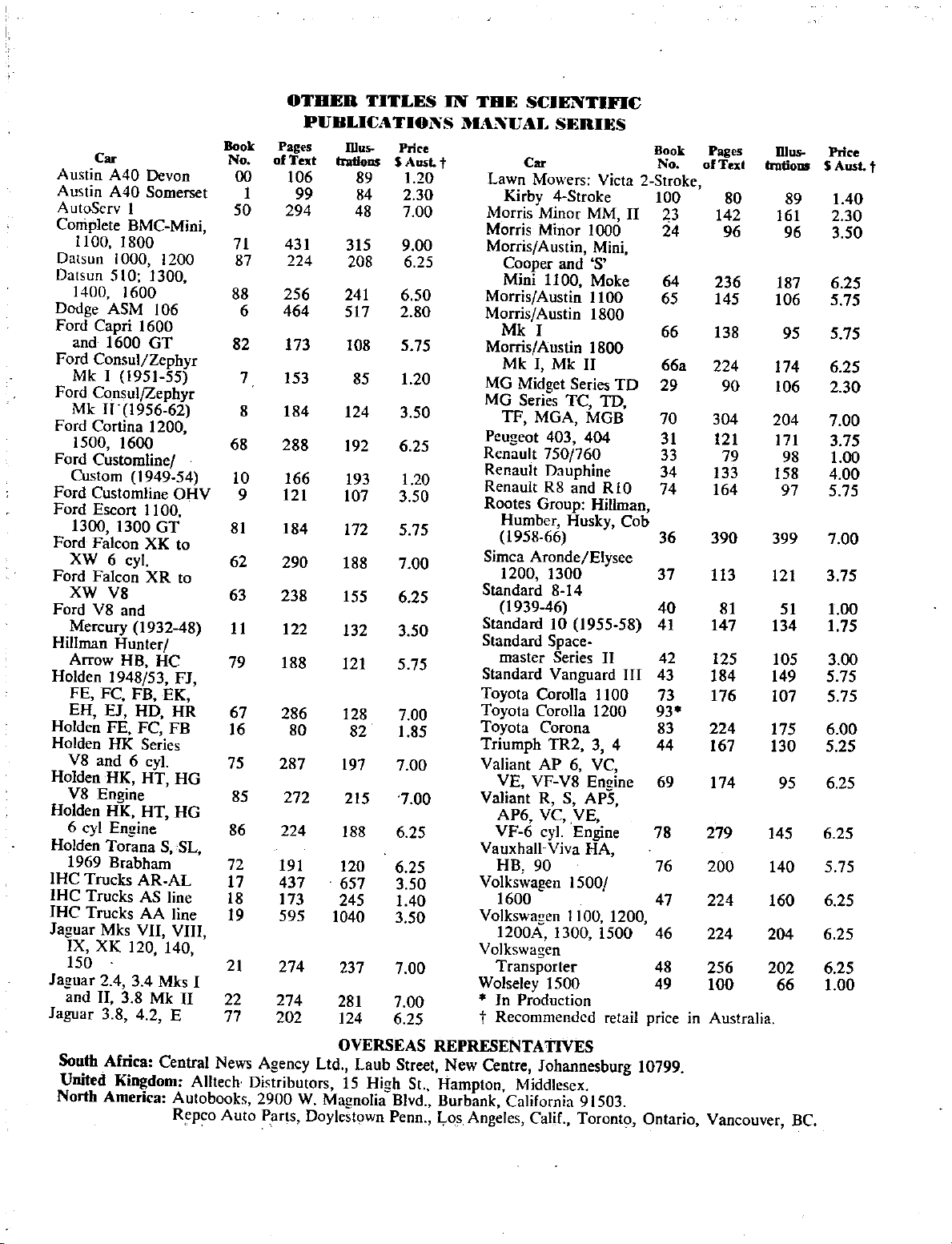
Car
Austin
Austin
A
Complete
Datsun
Datsun
Dodge
Ford
Ford
Ford
Ford
Ford
Ford
Ford
Ford
Ford
Ford
A40
A40
utoServ
1100 1800
1000
510
1400
ASM
Capri
and
1600
Consul
Mk
I
1951
Mk
II
Cortina
1500
Customline
Custom
Customline
EscortI100
BOO 1300
Falcon
XW
6
Falcon
XW
V8
V8
I
BMC
1600
1956
1600
and
Mercury
Hillman
Holden
Holden
Holden
Holden
Holden
Holden Torana
HC
IHC
IHC
Jaguar
Jaguar
Jaguar
North
Arrow
FE
EH
V8
V8
6
cyl
1969
Trucks
Trucks
Trucks
IX XK
150
and
South
United
Hunler
HB
1948
FC
EJ
FE
HI
and
HK
Engine
HK
Engine
Brabham
Mks
24 34
II
3 842
Africa
Kingdom
America
Devon
Somerset
1300
1600
GT
Zephyr
ConsulZephyr
1949
XK
cyl
XR
1932
FB
HD
FC
Series
6
HT
HT
AR
AS
AA
VII
20
3 8
1200
106
1200
GT
HC
53
cyt
Mk
Mini
55
62
54
OHV
to
to
48
FJ
EK
HR
FB
HG
HG
S
SL
AL
line
line
VIII
140
Mks
E
Central
Autobooks
Repco
II
Bool
No
I
Alltech
00
1
50
7L
87
88
6
82
7
8
68
10
9
81
62
63
11
79
67
16
75
85
86
72
17
18
19
21
22
77
News
Auto
OTHER
PUBUCATIONS
s
Pag
of
Text
106
99
294
431
224
256
464
173 108
153
184
288
166
121 107
184
290
238
122 132
188
286
80 82
287
272 215
224
191 120
437 657
173
595
274
274
202
Agency
Distributors
2900
Parts
TITLES
IDo
Indiom
89
84
48
315
208
241
517
85
124
192
193
172
188
155
121
128
197
188
245
1040
237
281
124
OVERSF
Ltd
15
W
Magnolia
Doylestown
Laub
High
Price
Aus
1
2
7
9
6
6
2
5
1
6
3
5
7
6
3
5
Penn
IN
THE
B
t
20
30
00
00
25
50
80
75
20
3
50
25
1
20
50
75
00
25
50
75
7
00
85
1
7
00
7
00
25
6
6
25
3
50
1
40
3
50
7
00
00
7
6
25
AS
REPRESENTATIVES
Street
New
St
Hampton
Burbank
Blvd
os
I
SCIENTIFIC
NUAI
Lawn
Kirby
Morris
Morris
Morris Austin
SERIES
Car
Mowers
4
Minor
Minor
Cooper
Mini
1100
Morris Austin
Morris
Morris Austin
MG
MG
Peugeot
Renault
Renault
Renault
Rootes
Standard
Toyota
Toyota
Mk
Mk
Midget
Series
TF
Humber
1958
Simca
1200
1939
Standard
Standard
master
Standard
Toyota
Austin
I
I
Mk
MGA
403 404
750f760
Dauphine
R8
Group
66
Aronde
1300
46 40
Corolla
Corolla
Corona
Triumph
VE
AP6
VF
HB
AP
VF
R
VC VE
6
cy
90
Valiant
Valiant
Vauxhall Viva
Volkswagen
1600
Volkswagen
1200A 1300
Volkswagen
Transporter
Wolseley
Production
In
t
Recommended
Centre
Angeles
Johannesburg
Middlesex
California
Calif
Vieta2Stroke
Stroke
MM
1000
Mini
and
S
Moke
1100
1800
1800
II
Series
TC TD
MGB
and
Hillman
Husky
Elysee
8
14
10
1955
Space
Series
Vanguard
11
1200
TR2
3
6
VC
V8
Engine
AP5
S
Engine
HA
1500
1100
1500
91503
Toronto
RIO
11
1500
Book
No
100
II
23
24
64
65
66
66a 224
29
TO
70
31
33 79 98
34
74
Cob
36
37
41
58
42
III
43
73
00
93
83
4
44
69
78
76
47
1200
46
48
49
retail
price
10799
Ontario
Pages
of
Text
80
142
96 96
236
145
138
90
304 204
121
133
164
390
113
81 51
147
125
184
176
224
167
174
279
200
224 160
224 204
256 202
100
in Australia
Vancouver
trntiollS
89
161
187
106
95
174
106
171
158
399
121
134
105
149
107
175
130
145
140
Dlu
s
Price
AusLt
1
40
2
30
3
50
6
25
75
5
75
5
25
6
2
30
7
00
75
3
1
00
4
00
97
5
75
00
7
75
3
00
1
1
75
3
00
5
75
5
75
00
6
5
25
95
6
25
25
6
75
5
25
6
6
25
25
6
66
Be
1
00

fJngi
12
EN
INE
MOUNTINGS
19
TO
REMOVE
I
chassis
2
brackets
3
sump
assembly
4
the
engif
bracket
5
Installation
Allow
mountings
TO
REMOVE
I
chassis
I
Engine
a
b
c
d
e
t
g
h
i
0
k
Raise
stands
Remove
the
to
Interpose
a
and
Remove
e
to
the
Remove
the
full
before
Raise
stands
wm
Dirty
Carburettor
Moisture
distributor
Dirt
Incorrectly
Faulty
Faulty
Fuel
Faulty
Incorrectly
Broken
distributo
AND
INSTAL
the
front
the
front
a
and
jack
the
ounting
crossmemher
both
isareversal
weight
tightening
AND
INSTAL
the
front
not
start
or
corroded
nooding
on
cap
or water
set
coil
or
low
or
lock
vapor
fuel
pump
set
or
points
of
bolt
nuts
crossmember
wooden
jack
nuts
securing
brackets
front
mountings
of
the
engine
the
of
normal
by
Possible
distributor
high
in
carburettor
spark
capacitor
tension
high
ignition
short
circuited
FRONT
the vehicle
fixing
block
the
up
each
and
of
the
assembly
securing
REAR
the
vehicle
cranking
cause
tension
and
plug
gaps
wires
timing
the
between
front
engine
the
from
removal
bolts
I
J
points
wires
fuel
low
and
engine
of
bolts
the
to
and
and
ENGINE
and
system
tension
support
mounting
the
engine
the
engine
mounting
from
brackets
procedure
bear
on
nuts
support
or
lead
inside
on
to
the
the
on
FA1JLT
to
2
weight
3
mounting
4
transmission
crossmember
the
5
mounting
remove
E
and
tiansm
finally
NOTE
renewed
normq
DIA
Clean
Check
Dry
Clean
Reset
Test
Test
Check
Test
Check
Test
Place
the
of
Remove
securing
Remove
Undo
to
the
mounting
that
nsure
tigjItening
Engine
and
l
working
or
needle
out
out
spark
and
and
source
and
and
and
a
jack
e
engi
the
bolts
the
crossmember
the
the
Installation
is
a
the
sion
weight
the
mountings
the
cause
flfe
for
NOSIS
renew
and
valve
tension
high
carburettor
plug
renew
renew
of
overhaul
retime
renew
lead
under
the
and
transmission
two
transmission
bolts which
to
bolts
transmission
connecting
reversalofthe
mounting
i
is
aken
mounting
that
the
oil
of
the
mounting
Remedv
adjust
points
and
noat
wires
fuel
and
to
gaps
faulty
faulty
vapo
fuel
specification
components
wires
lock
pump
ignition
transmission
assembly
rear
attach
the
uf
derbody
the
extension
removal
procedure
centralized
on
the
mounting
securingbolis
are
oil
soaked
lea
rectified
concerned
clean
out
fuel
and
cap
system
and
insulate
take
to
crossmember
the
an
remove
rear
housing
that
and
should
to
ensure
system
a
inst
the
to
rear
engine
and
eflgine
bef9re
be
a
heat
2
3
Engine
a
b Fault
c
Engine
a
Idling
b
Idling
c
Carburettor
wm
Weak
Faulty
stalls
not
or
faulty
in
starter
starter
speed
mixture
start
Possible
battery
lead
Possible
set
too
too
nooding
weakorerratic
cause
or
solenoid
cause
slow
lean
or
rich
noat
or
level
cranking
incorrectly
set
Continued
neXl
Recharge
Test
and
Test
and
Readjust
Readjust
Check
p
1ge
renew
overhaul
idling
needle
or
idling
renew
valve
faulty
starter
speed
mixtur
Remedv
battery
components
Remedy
stop
r
reset noat
s
screw
rew
and
level
idling
speed
screw
25

or
foreign
sideofthe
3
With
down
through
tubes
If
impregnated
the
upper
the
tubes
operation
necessary
work
TO
INSTAL
Position
1
opening
between
grease
and
2
Connect
between
the
matter
core
the aid
the
it
is
with
and
lower
thoroughly
carried
be
specialised
the
instal
radiator
the
that
of
radiator
apparent
flakes
tanks
cleaned
out
equipment
radiator
and
tighten
the
and
hoses
may
by
upper
a
of
the
and
have
flash
fill
that
rust
un
sweated
It
a radiator
assembly
the
and
engine
pipes
accumulated
makeavisual check
light
onto
point
the
tubes
it
will
be
necessary
from
is
recommended
specialist
to
four
carry
securing
lower
Use
out
in
the
radiator
a
light
on
the
are
the
who
this
front
bolts
the
front
radiator
severely
to
core
that
has
type
panel
hoses
smear
have
and
this
the
cooling
the
level
50 in
proves
and
drain
water
engine
slowly
and
2
or
in
of
or
Cooling
NOTE
Inspect
perishing
to
be
unserviceable
3
On
where
applicable
at
4
at
instal
5
radiator
bottom
at
operating
allow
6
the
Close
the
Start
Use
pressure
With
pipes
plug
and
of
the
the
NOTE
is
to
of
temperature
transmission
and
vehicles
lower
cylinder
the
of
renew
pressure
the
is
care
fluid
all
hoses
any
fitted
connect
radiator
the
radiator
block
cap
engine
approximately
the
filler
neck
to
avoid
temperature
to
escape
the
engine
check
thoroughly
leaks
before
hose
with
up
tank
Fill
and
the
before
that
the
drain
check
within
risk
remuve
running
installing
upon
automatic
torque
tap
the
system
of
the
removing
that
impection
transmission
converter
and
with
the
12
7
mm
scalding
radiator
and
for
System
for
cracking
instal
clean
water
0
the
If
cap
the
cap
at
water
operating
TO
REMOVE
Remove
1
water
from
2
3
to
4
tank
Disconnect
Remove
the
Detach
radiator
elbow
withdraw
head
NOTE
determine
further
open
and
A
testing
when
should
Installation
Ensure
Fill
approximately
neck
and
check
the
front
the
visual
its
removed
be
that
the
AND
INSTAL
the
cooling
and
the
portion
the
water
thermostat
examination
serviceability
Fur
instance
from
discarded
reversal
is
a
a
new
cooling
12
7
mm
for
water
radiator
system
remove
two
and
gasket
system
leaks
bolts
of
the
outlet
from
and
a
cold
a
new
of
the
is
050in
pressure
the
of
a
via
the
top
securing
cylinder
elbow
the
recess
the
thermostat
obviate
thermostat
cap
tap
radiator
the
head
and
in
the
engineisobviously
unit
fitted
removal
fitted
with
below
when
procedure
assembling
clean
the
J
and
the
on
hose
water
gasket
the
will
necessity
with
water to
radiator
drain
outlet
cylinder
its
faultv
T
the
lower
and
often
for
valve
filler
ERMOSTAT
that neither
sidesorbottom
temperature
valve
and
valve
and
valve
a
See
valve
A
new
3
Progressively
commences
4
Continue
then
measure
Specification
opening
thermostat
lift
not
unit
fitted
the
of
reading
within
the
vessel
heat
the
on
to
open
heating
the
temperature
with
opening
specifications
thermosta
until
maximum
section
or
thermometer
the
thermometer
the
valve
fo
temperature
should
water
lift
maximum
is
touching
noting
the
as
is
completely
the
of
and
be
discarded
thermostat
open
thermostat
valve
maximum
the
the
lift
and
TO
a
CHECK
1
2
reliable
Gleck
Suspend
thermometer
that
and
the
immerse
thermostat
in
v
a
is
closed
the
thermostat
esselofcold
when
together
water
it
is
cold
ensuring
with
29
Thermostat
and
Housing
Compartments