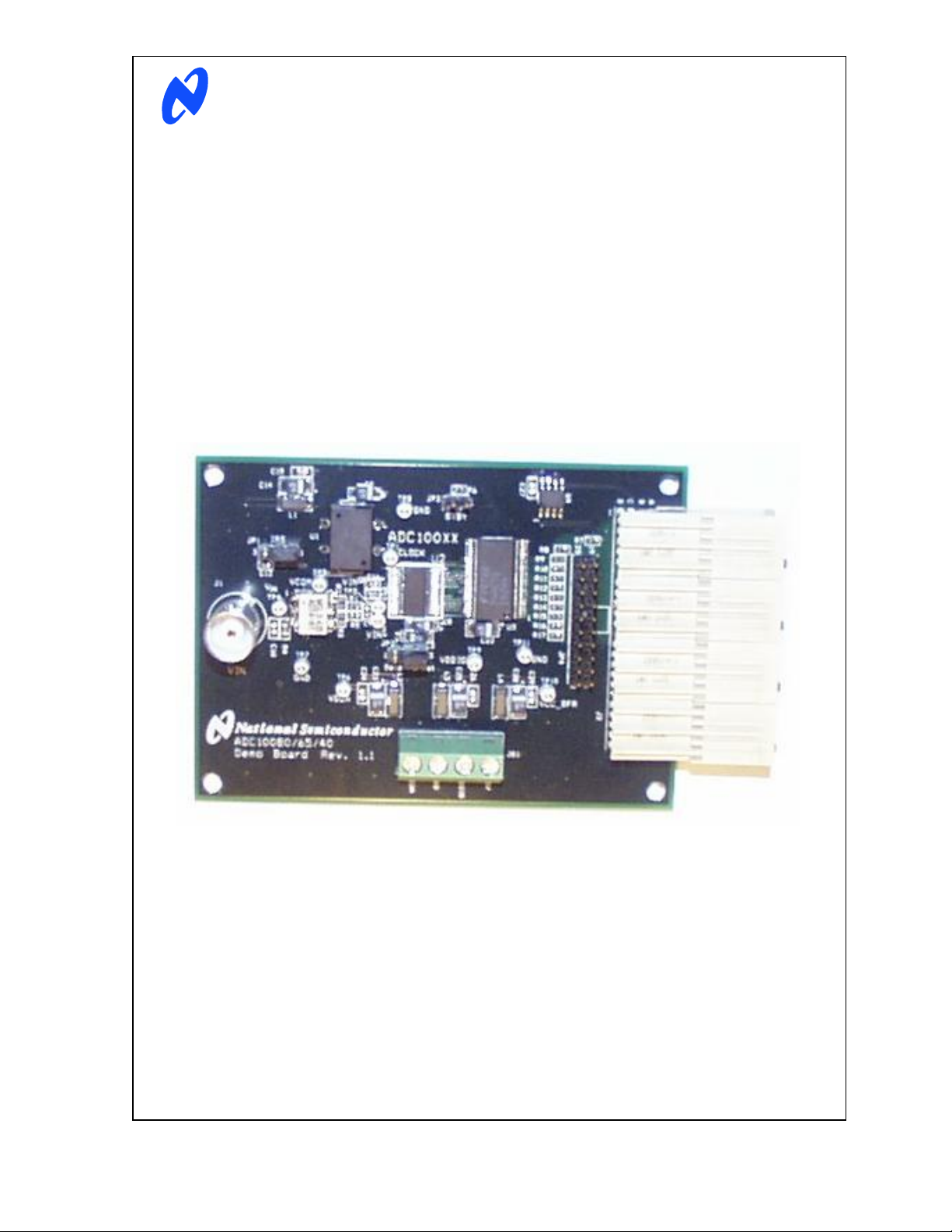
National Semiconductor
Rev 1.3
May 9, 2005
Evaluation Board User’s Guide
ADC10040 10-Bit, 40 MSPS, 3 Volt, 55.5 mW A/D Converter
ADC10065 10-Bit, 65 MSPS, 3 Volt, 68.5 mW A/D Converter
ADC10080 10-Bit, 80 MSPS, 3 Volt, 78.6 mW A/D Converter
© 2005 National Semiconductor Corporation.
1 http://www.national.com
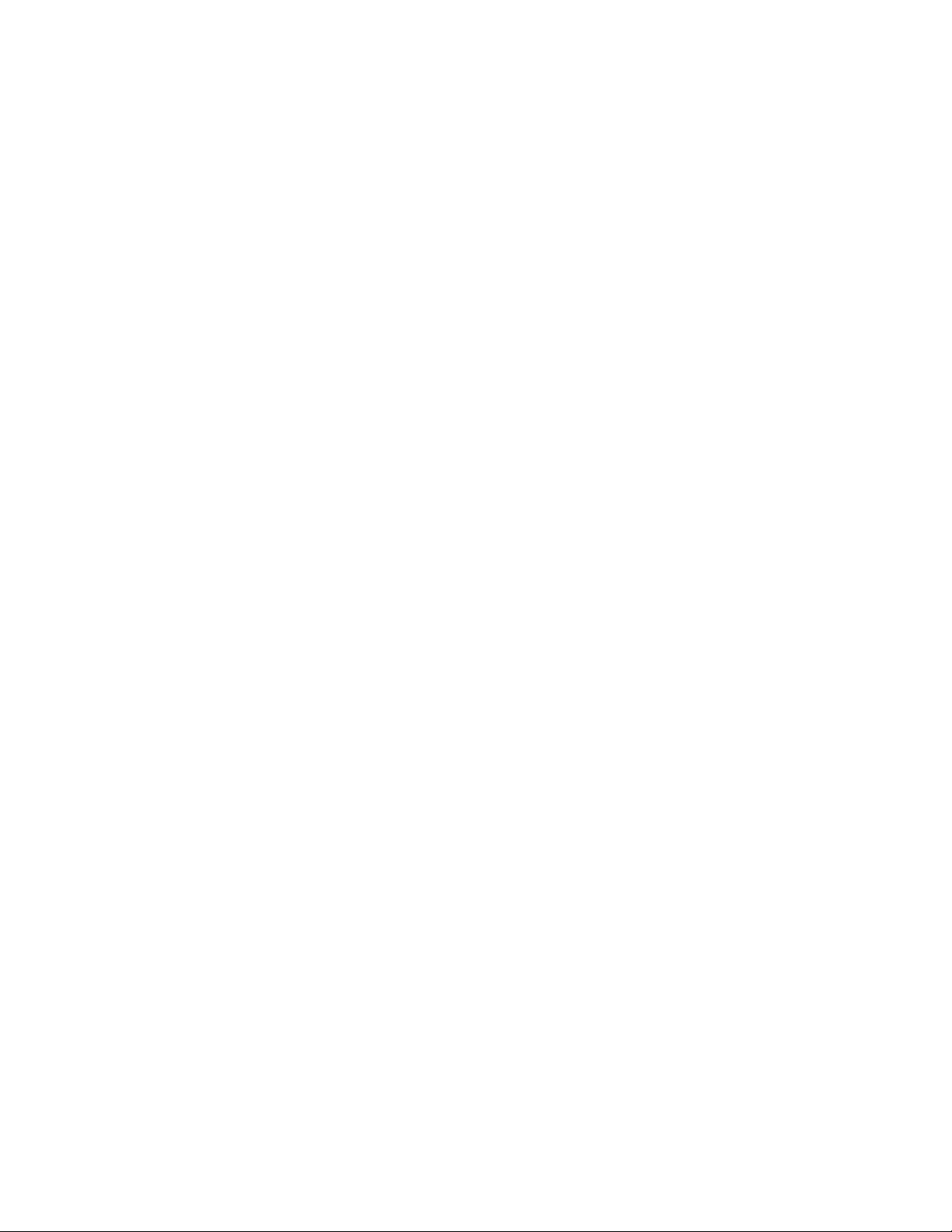
Table of Contents
1.0 Introduction
2.0 Quick Start
3.0 Functional Description
4.0 Obtaining Best Results
............................................................................................................................................ 3
............................................................................................................................................. 3
............................................................................................................................. 3
3.1 The Signal Input
3.2 Digital Data Output.
3.3 ADC10080 Control Pins.
3.3.1 The Standby (STBY) Pin
3.3.2 The Data Format (DF) pin
3.3.3 The Input Range Select (IRS) Pin
3.3.4 Power Supply Connections
4.1 Clock Timing
4.2 Coherent Sampling
4.3 FFT Windowing Technique
....................................................................................................................... 3
............................................................................................................................. 4
........................................................................................................................... 4
.................................................................................................................... 4
5.0 Hardware Documentation
.................................................................................................................. 3
........................................................................................................... 3
..................................................................................... 3
.................................................................................... 3
............................................................................... 4
........................................................................................................... 4
....................................................................................................... 4
............................................................................................................... 6
2 http://www.national.com
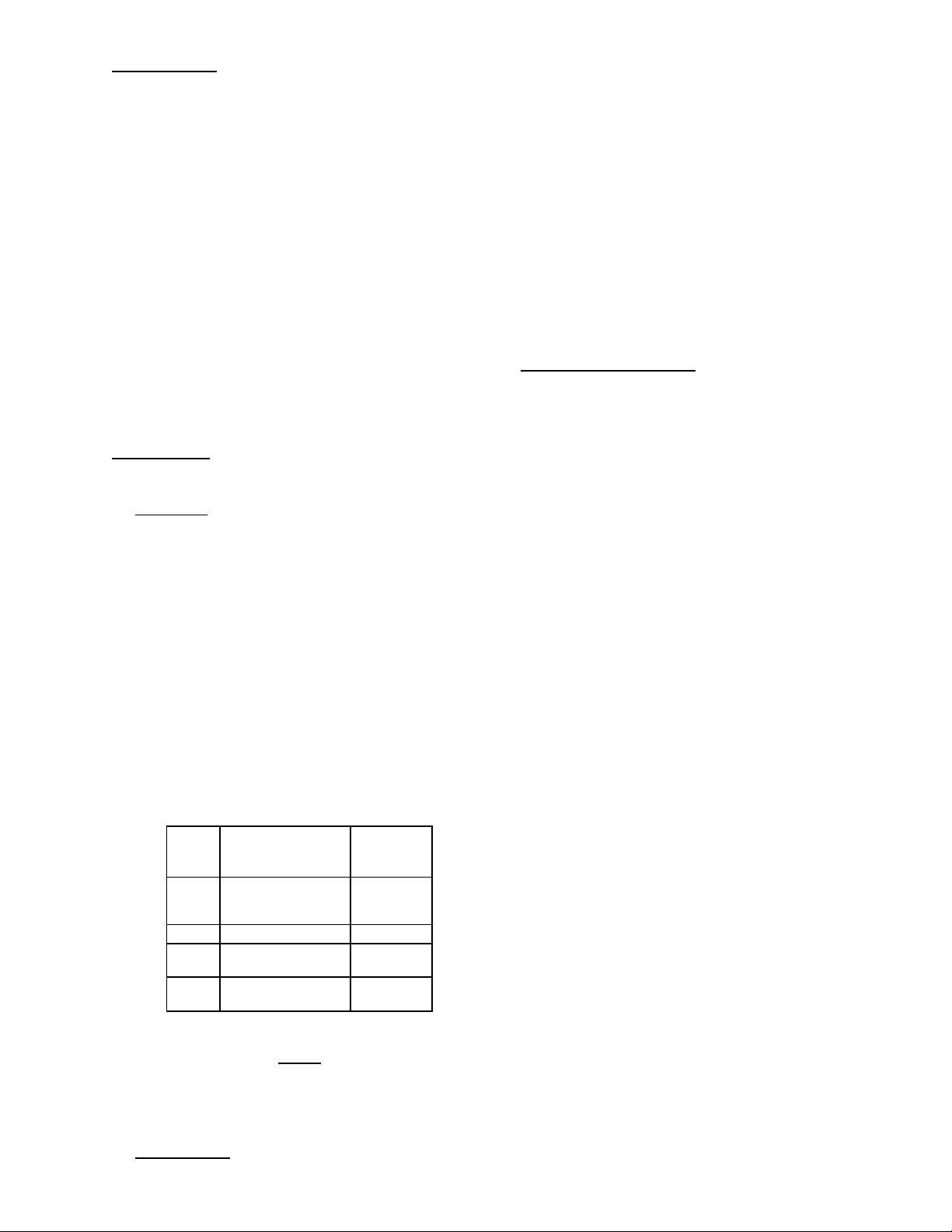
1.0 Introduction
The ADC10080EVAL Design Kit (consisting of the Evaluation Board
and this manual) is designed to ease evaluation and design-in of
National's ADC10040, ADC10065, or ADC10080 10-bit Analog-toDigital Converters, which operate at speeds up to 40, 65, and 80
MSPS. Further reference in this manual to the ADC10080 is meant
to also include the ADC10040 and the ADC10065 unless otherwise
specified. The latest datasheet for these products can be obtained
from http://www.national.com.
The evaluation board can be used in either of two modes. In the
Manual mode, suitable test equipment, such as a logic analyzer,
can be used with the board to evaluate the ADC10080 performance.
In the Computer mode, evaluation is simplified by connecting the
board to the WaveVision™ Digital Interface Board (order number
WAVEVSN BRD 4.0). It is connected to a personal computer
through a USB port and running WaveVision™ software, operating
under Microsoft Windows 95 or later. The WaveVision™ software
can perform an FFT on the captured data upon command and, with
the frequency domain plot, shows dynamic performance in the form
of SNR, SINAD, THD and SFDR.
The signal at J1, the Analog Input to the board, is digitized and is
available at pins B4 through B13 of J2 and pins 10 through 19 of
JP4. See the board schematic for more details.
2.0 Quick Start
Refer to the board layout for locations of test points and major
components.
For Stand-Alone
operation:
1. Select the input voltage range by inserting a jumper into JP1.
Set the jumper on pins 1&2 for 2.0 Vpp. Set the jumper on pins
2&3 for 1.5 Vpp. If no jumper is inserted, 1.0 Vpp is assumed.
2. To make the ADC10080 active, insure there is no jumper on
JP3.
3. Select the output data format using JP2. When the jumper is
on pins 1&2, 2’s complement data format is selected. If the
jumper is on pins 2&3, offset binary is selected.
4. Connect a clean power supply to Power Connector JS1. Refer
to Table 1 for power supply description and requirements.
5. Connect a signal of the selected amplitude (see step 1) from a
50-Ohm source to Analog Input BNC J1. Insure that the signal
is not over-ranged, by examining a histogram. (Either by using
WaveVision
tm
, or the logic analyzer being used.) Over-range
signals will dramatically increase the THD.
6. The digitized signal is available at pins B4 through B13 of J2
and pins 10 through 19 of JP4.
JS1 pin
number
1 Vcc for Crystal and
Description Voltage
Range
2.7 - 3.3 V
VDDA for
ADC10080
2 Ground 0V
3 VDDIO 2.5 – 3.3 V
4 Output Buffer VCC 4.9 – 5.1 V
Table 1
For Computer mode
operation:
tm
1. Connect the evaluation board to the WaveVision
Interface Board. See the instruction manual supplied with the
WaveVision
tm
kit. The latest WaveVisiontm software can be
Digital
obtained from http://www.national.com.
2. Select the input voltage range by inserting a jumper into JP1.
Set the jumper on pins 1&2 for 2.0 Vpp. Set the jumper on pins
2&3 for 1.5 Vpp. If no jumper is inserted, 1.0 Vpp is assumed.
3. To make the ADC10080 active, insure there is no jumper on
JP3.
4. Select pins 2&3 on JP2 so that the output data is offset binary.
5. Connect a clean power supply to Power Connector JS1. Refer
to Table 1 for power supply description and requirements.
6. If the output level goes over range as seen on the data
captured through WaveVision™, reduce the output level from
the signal generator and capture data again. If the output level
does not reach codes of 25 and 1000, increase the output level
from the signal generator and capture data again.
3.0 Functional Description
The ADC10080 Evaluation Board schematic is shown in Section 5.
3.1 The Signal Input
The signal transformer T1 provides single-ended to differential
conversion. The common mode voltage VCOM provided by the
chip, sets the common mode of the input signal by biasing the
center tap of T1.
The differential signal present on the secondary side of the
transformer is then sent through a low pass filter set up by R1, R5 &
C9.
It is important when evaluating the dynamic performance of the
ADC10080 (or any A/D converter), that a clean sine wave be
presented to the converter. To do this it is necessary to use a
bandpass or a low pass filter between the signal source and the
ADC10080 evaluation board input J1. Even the best signal
generators available do not provide adequate noise and distortion
performance for proper evaluation of a 10-bit ADC. A high-quality
bandpass filter with better than 12-bit equivalent noise
characteristics and at least 80dB stop band attenuation is ideal. No
scope or other test equipment should be connected to any input
circuitry while gathering data.
3.2 Digital Data Output.
The digital output data from the ADC10080 is available at the 96-pin
Euro connector J2 and header JP4. Series resistors R7 – R17
provide data line dampening that may occur with long cables. U3
provides buffering to drive the cable. U3’s VCC may be adjusted for
various output levels. Refer to Table 1 for voltage range.
3.3 ADC10080 Control Pins.
The ADC10080 has three control pins, making it a very versatile
converter. They are Standby (Pin 28 – STBY), Data Format (Pin 15
– DF) and Input Range Select (Pin 5 – IRS).
3.3.1 The Standby (STBY) Pin
When this pin is pulled high (pins 1&2 of JP3 are connected), the
converter is put into ‘standby’ mode. The converter consumes only
13.5 mW of power. When STBY is tied to VSSA (JP3 is open), the
ADC is in full operation.
3.3.2 The Data Format (DF) pin
This pin sets the output data format of the ADC10080. When this
pin is pulled to VDDA (pins 1&2 of JP2 are connected), the output is
2’s complement. When pulled down to VSSA (pins 2&3 of JP2 are
connected), the data output is offset binary.
3 http://www.national.com
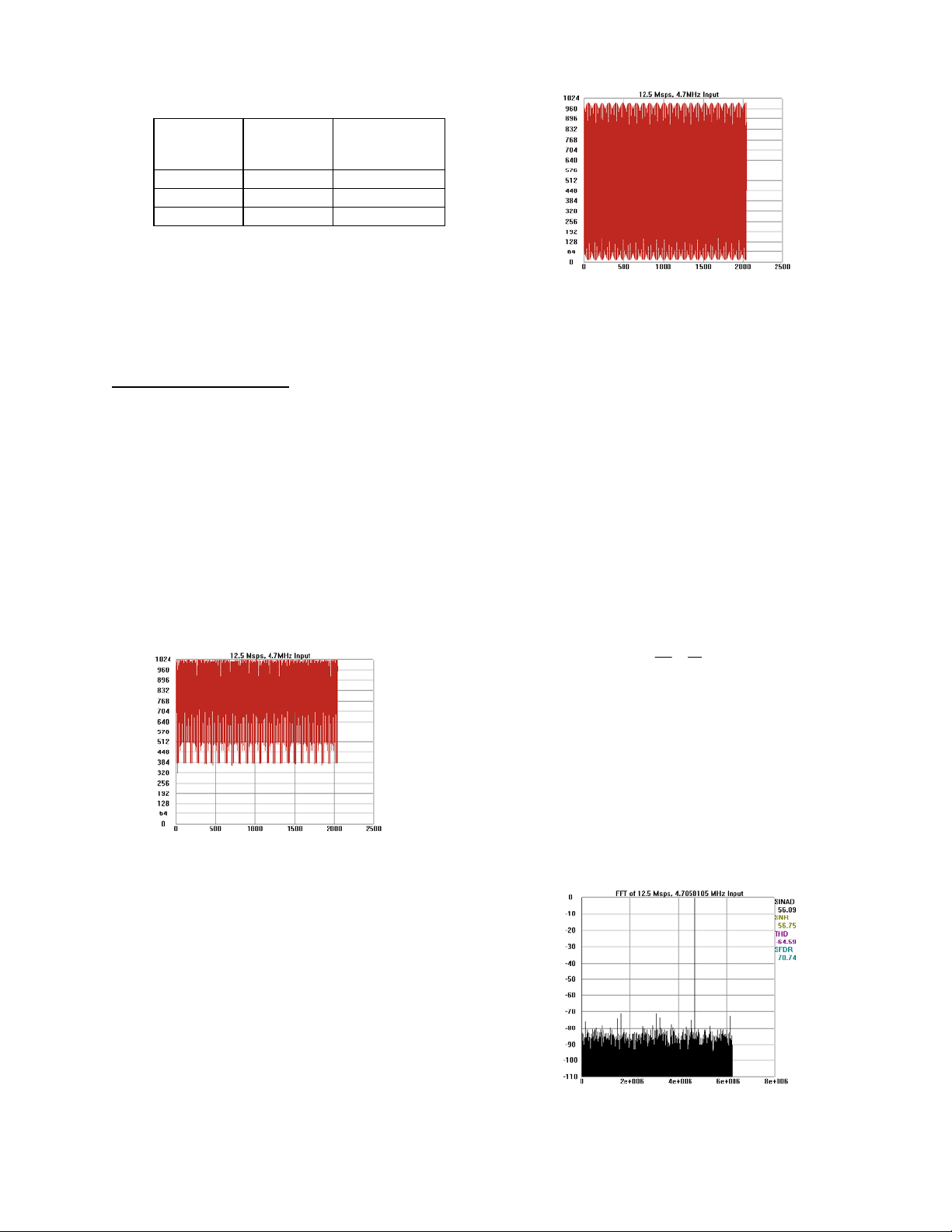
3.3.3 The Input Range Select (IRS) Pin
This pin has three states which the following table summarizes:
JP1 Jumper
setting
IRS State
Input Voltage
Range
(differential)
Pins 1&2 VDDA 2Vpp
Pins 3&4 VSSA 1.5Vpp
Open Floating 1.0Vpp
Figure 3. A good data capture of a 4.7MHz input
3.3.4 Power Supply Connections
Power to this board is supplied through power connector JS1. Table
1 describes the pin out, and the allowed voltage ranges
signal at 12.5Msps
4.2 Coherent Sampling
4.0 Obtaining Best Results
Many factors go into reasonable data capture when evaluating an
ADC. These include, but are not limited to, such things as PCB
layout, clock timing, the ratio between the input frequency and
sample rate and the FFT windowing technique.
Here we include very brief discussions on clock timing adjustments
as it relates to the ADC10080 and of sampling and FFT windowing.
4.1 Clock Timing
Because of differing delays in the clock signal and the data from the
ADC, at some sample rates the data from the ADC may be latched
as it is changing, leading to corrupted data, one example of which is
seen in Figure 2, which shows the poor data capture of a 4.7MHz
signal at 12.5Msps that results from poor timing of the clock and
external latch signals relative to each other.
Figure 2. Bad data capture of a 4.7MHz input signal at
12.5Msps due to attempted capture at data transition.
Figure 3 shows a successful data capture of a 4.7MHz input signal
at 12.5Msps with a shorting jumper on JS1.
4 http://www.national.com
Artifacts can result when we perform an FFT on a digitized
waveform, producing inconsistent results when performing repeated
testing. The presence of these artifacts means that the ADC under
test may perform better than the measurements would indicate.
We can eliminate the need for windowing and get more consistent
results if we observe the proper ratios between the input and
sampling frequencies. This greatly increases the spectral resolution
of the FFT, allowing us to more accurately evaluate the spectral
response of the A/D converter. When we do this, however, we must
be sure that the input signal has high spectral purity and stability
and that the sampling clock signal is extremely stable with minimal
jitter.
Coherent sampling of a periodic waveform occurs when a prime
integer number of cycles exists in the sample window. The
relationship between the number of cycles sampled (CY), the
number of samples taken (SS), the signal input frequency (fin) and
the sample rate (fs), for coherent sampling, is
f
CY
in
=
f
SS
s
CY, the number of cycles in the data record, must be a prime
integer number and SS, the number of samples in the data record,
must be a factor of 2 integer.
Further, fin (signal input frequency) and fs (sampling rate) should be
locked to each other. If these frequencies are locked to each other,
whatever frequency instability (jitter) is present in one of the signal
is present in the other signal and these jitter terms will cancel each
other.
Windowing (an FFT Option under WaveVision™) should be turned
off for coherent sampling. The results of coherent sampling can be
seen in the FFT plot seen in Figure 4. Note how narrow is the bin
(how fine are the lines) in this plot as compared with the plots of
Figures 5 through 7.
Figure 4. Coherent sampling will indicate accurate
dynamic performance of the ADC
4.3 FFT Windowing Technique