
Installation and Operating Instructions
Moniteur
Series 40 Positioners
INSTALLATION & OPERATING INSTRUCTIONS
SERIES 40 Positioners
Form IO2-0406

Installation and Operating Instructions
Moniteur
Description of Device
Moniteur's Series 40 pneumatic (3-15psi) and electropneumatic (4-20mA) positioners are advanced control
devices for rotary or linear valves which provide
unparalleled stability in difficult environments.
! Rugged Aluminum Housing With a Triple Corrosion-
Resistant Interior and Exterior Coating stands up to
harsh environments
! Reduced Bleed Pilot Valve reduces air consumption by
more than 50%
! Precise Calibration with simple SPAN and ZERO
adjustments.
! Magnetic 4-20 mA I/P Converter provides automatic
compensation for supply pressure, atmospheric
pressure and ambient temperature changes, and is
unaffected by EMF.
! Zero-Hysteresis Coupling System provides superior
accuracy and repeatability by eliminating "slop".
! Vibration Resistant Design maintains consistent
performance in poor conditions - no resonance effects
from 5 - 200Hz
! Stainless Steel Gauges
Series 40 Positioners
CAUTION: To reduce the risk of ignition of
hazardous atmospheres, disconnect the
device from the supply circuit before
opening. Keep assembly tightly closed
during operation.
Positioning
Moniteur Series 40 positioners can be mounted in any
position.
Mounting Brackets
For the installation of the rotary positioner, a mounting
bracket has been designed for actuators with the 80 x
30 mm NAMUR accessory pattern. For the 130 x 30
pattern, the block-type mounting bracket is available.
See diagrams below:
Bracket for the 80 x 30 NAMUR pattern
! Optional Limit Switches and 4-20mA Feedback
! Each Positoner Performance Tested - Test results are
included with each positioner
Bracket for the 130 x 30 NAMUR pattern
Part Number System
The series and part number are located on the nameplate. The part number can be deciphered in the table below.
4 N1
Series 40 Shaft Rating Pilot Feedback Gauges Indicator
Description
Series:
Pneumatic
Electro-Pneumatic
Shaft
Rotary NAMUR
Linear 10-80mm
Linear 80-150 mm
Code
40
41
N
L
S
-
E 1 S
Description
Electrical Ratings
Standard / None
Ex md IIT6
Intrinsically Safe
Pilot Valve
Standard Orifice
Small Orifice
Extra-Small Orifice
N
Code
S
E
I
1
2
3
-
F
Description
Position Feedback
None
4-20 mA
2 SPDT Limit Switches
Gauges
None
Standard
Indication
Flat Dial
Dome
Code
N
T
S
N
S
F
D
MONITEUR DEVICES INCORPORATED
36 Commerce Road, Cedar Grove, NJ 07009 Tel. (973) 857-1600 Fax (973) 857-7289
www.moniteurdevices.com
Page 1
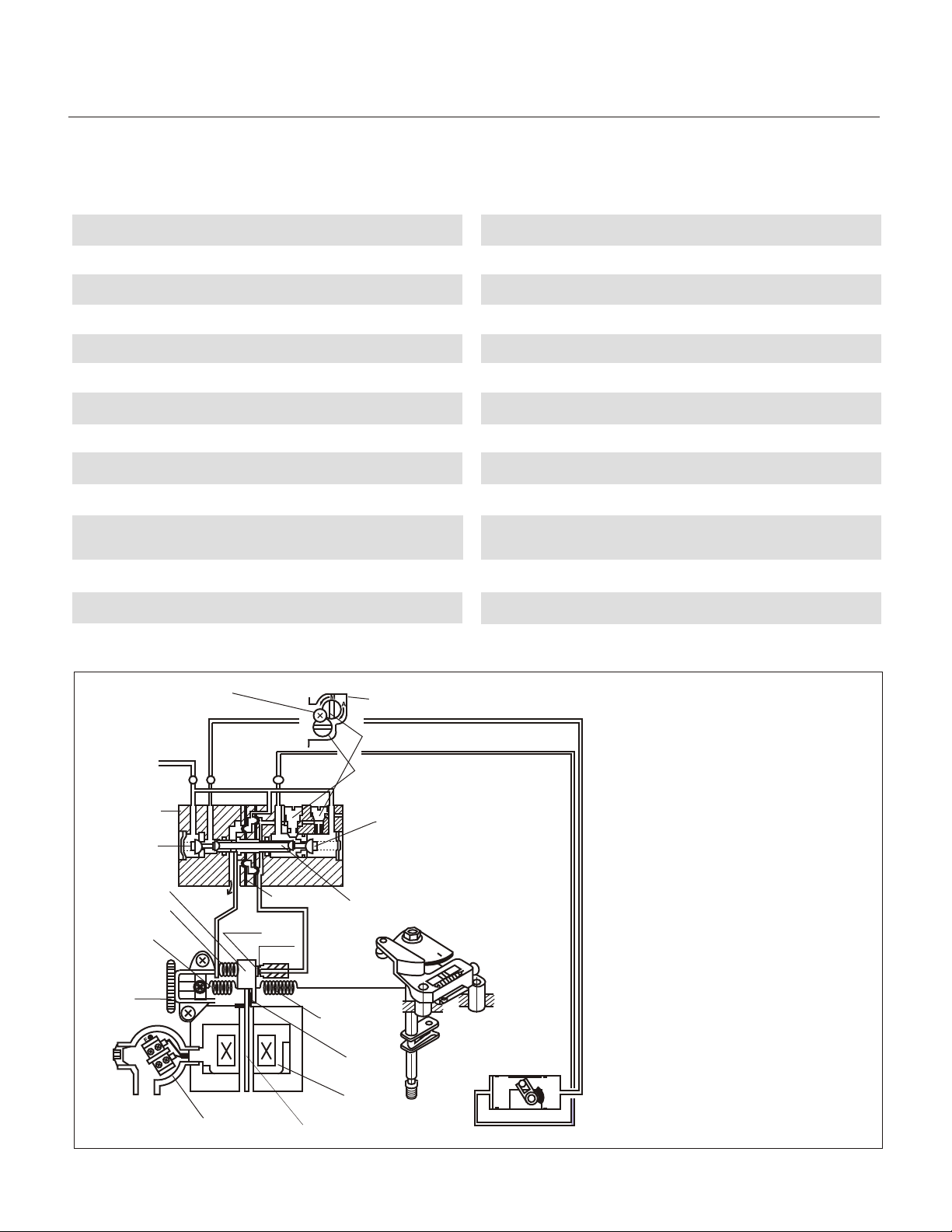
Installation and Operating Instructions
Moniteur
Specifications -3-15 psi Pneumatic
Input Signal 3 - 15 psig
Split Range Available
Impedance N/A
Stroke Range: 0 - 90°
Supply Range: 20 to 100 PSIG
Air Delivery: 7 SCFM
Air Consumption: 0.26 SCFM
Operating Temperature: -4° to +158° F
Linearity +/- 1%
Hysteresis 1% max.
Sensitivity +/- 0.5%
Repeatability +/- 0.5%
Pneumatic Connections: 1/8 NPT - Gauge Ports
1/4 NPT - Supply / Outlet
Series 40 Positioners
Specifications - 4-20 mA Electro-Pneumatic
Input Signal 4 - 20 mA @ 24 VDC
Split Range Available
Impedance 250 +/- 15 ohms
Stroke Range: 0 - 90°
Supply Range: 20 to 100 PSIG
Air Delivery: 7 SCFM
Air Consumption: 0.15 SCFM
Operating Temperature: -4° to +158° F
Linearity +/- 1%
Hysteresis 1% max.
Sensitivity +/- 0.5%
Repeatability +/- 0.5%
Pneumatic Connections: 1/8 NPT - Gauge Ports
1/4 NPT - Supply / Outlet
Enclosure: Designed to NEMA 4, 4X
Enclosure Weight: Approx. 4.8 lbs.
Principle Of Operation
Automatic
Manual
Change-over screw
(Built-in bleed restriction)
Sensitivity adjusting screw
(Adjusts GAIN)
Inlet Valve A
Exhaust Valve
Plate
Spring
Torque
Motor
Air Supply
Pilot Valve
Inlet Valve B
Counter Weight
Compensation
Spring
Zero
adjusting
Spring
Zero
adjusting
Screw
Stopper Screw
Do not move
Terminal Box
Flapper
Diaphragm
Nozzle
Feedback
Spring
Armature
Enclosure: Designed to NEMA 4, 4X
Enclosure Weight: Approx. 6.5 lbs.
OUT 1
As the signal current from the controller
increases, the plate spring of the torque
motor works as a pivot. As the armature
receives the rotary torque in the counter-
OUT 2
clockwise direction, the counter-weight
is pushed to the left, the clearance
between the nozzle and the flapper will
increase, and the nozzle back pressure
will decrease. As a result, the exhaust
valve of the pilot valve moves to the
right, and the output pressure of OUT1
increases (as OUT 2 decreases) to
move the actuator.
The movement of the actuator in turn
rotates the feedback shaft and spring.
The actuator stays in the position where
the spring force is balanced with the
force generated by the input current in
the torque motor. The compensation
spring is for direct feedback of the
Actuator
motion of the exhaust valve, and is
connected to the counter weight to
enhance the stability of the loop. The
zero point is adjusted by changing the
zero adjustment spring tension.
Page 2
MONITEUR DEVICES INCORPORATED
36 Commerce Road, Cedar Grove, NJ 07009 Tel. (973) 857-1600 Fax (973) 857-7289
www.moniteurdevices.com