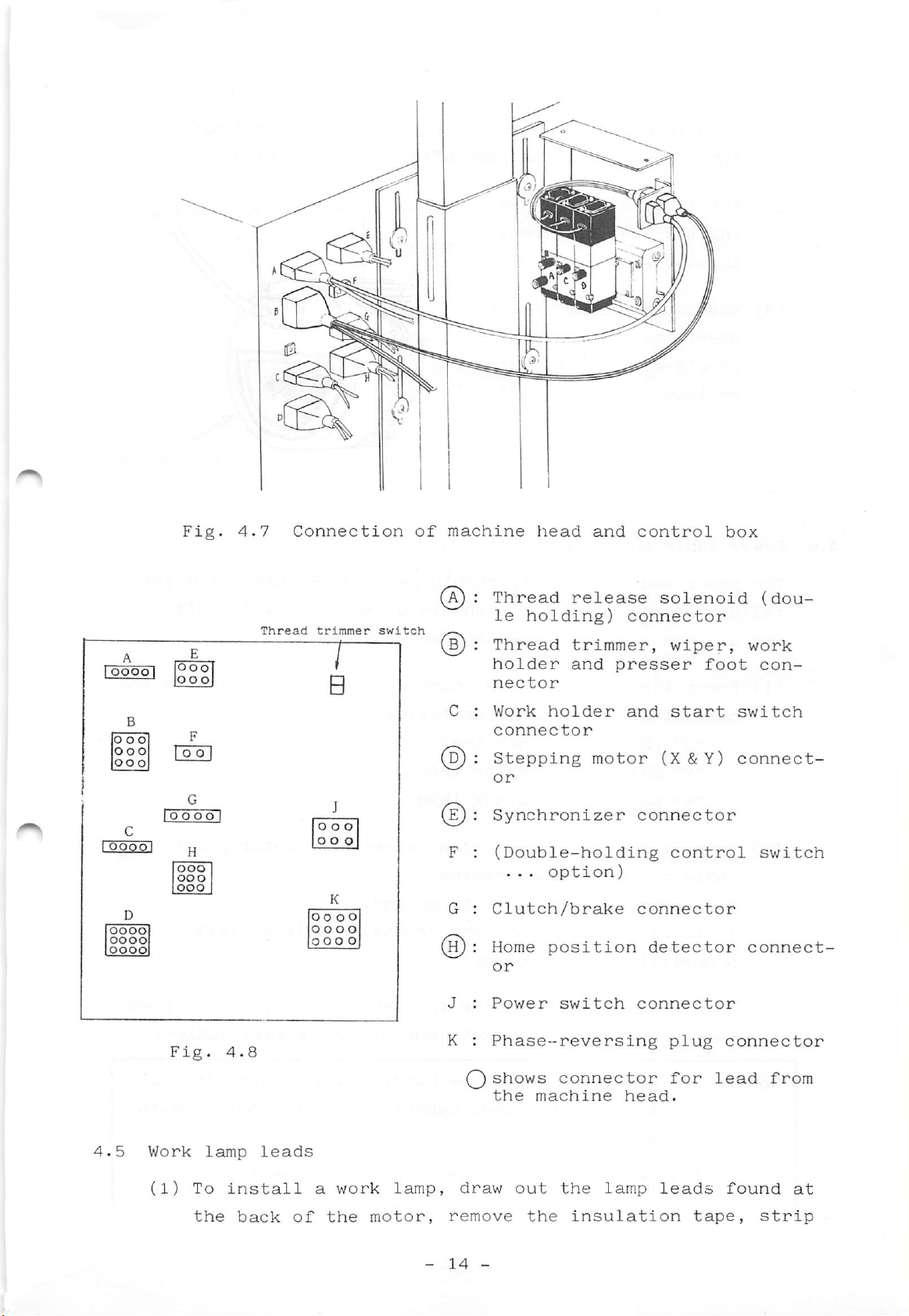
Fig.
4.7
Connection
of
machine
head
and
control
box
oooo
^ :
Thread
trimmer
switch
^ : Thread trimmer, wiper,
A
G
oooo
Fig.
oooo
oooo
oooo
4
^:
Thread
le
holder
nector
C :
Work
connector
D) :
Stepping
Synchronizer
F :
(Double-holding
G :
Clutch/brake
H):
Home
J :
Power
K :
Phase-reversing
Qshows
the
holding)
...
machine
release
and
holder
motor
option)
position
switch
connector
solenoid
connector
presser
and
(X&Y)
connector
connector
detector
connector
head.
foot
start
control
plug
for
(dou-
work
con
switch
connect-
switch
connect-
connector
lead
from
4.5
Work
(1)
To
the
lamp
leads
install
back
of
a
work
the
lamp,
motor,
-
draw
remove
14
-
out
the
the
insulation
lamp
leads
tape,
found
at
strip
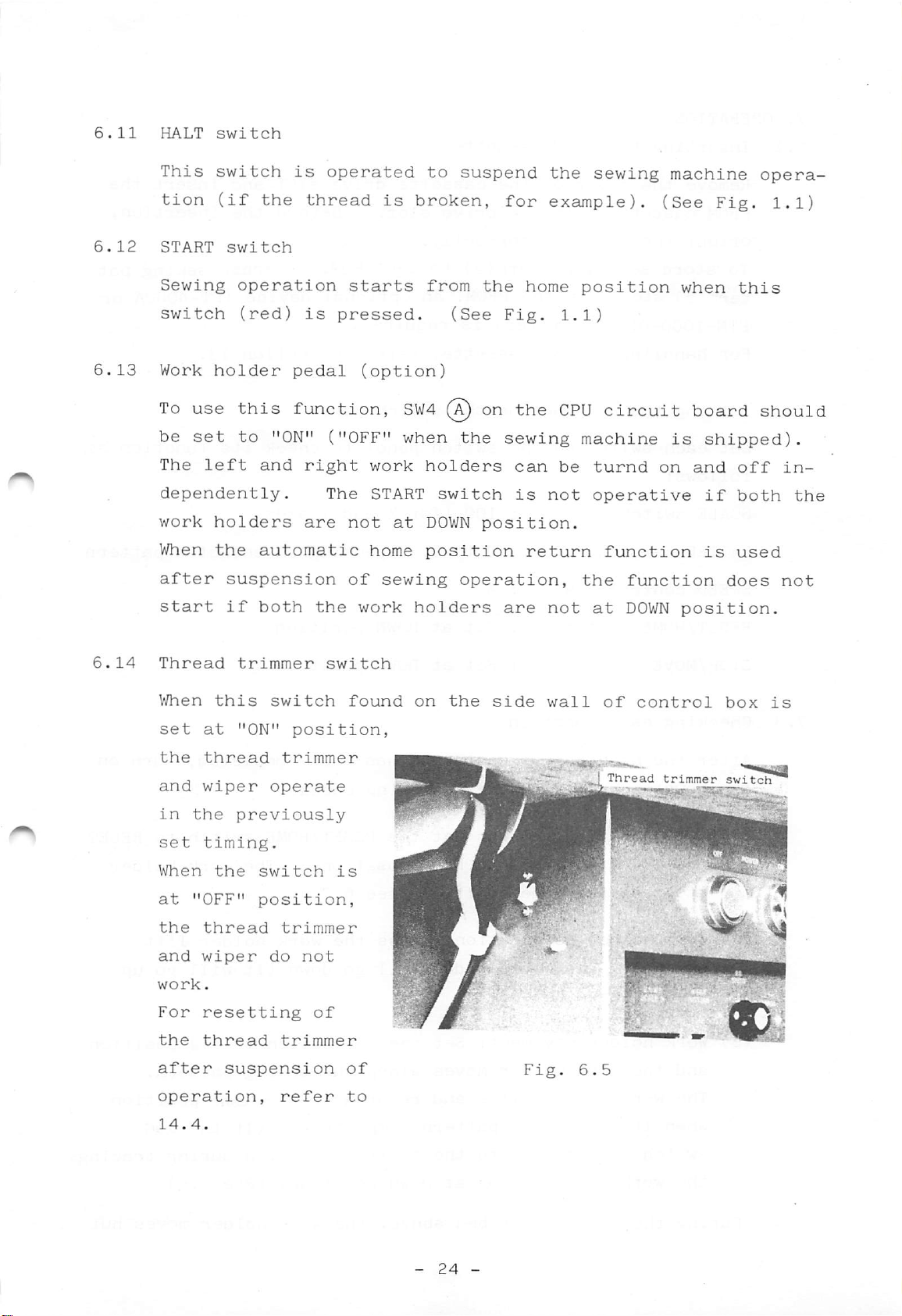
5.11
HALT
switch
6.12
6.13
This
tion
START
Sewing
switch
(if
switch
operation
switch
Work
To
be
The
dependently.
work
When
after
start
holder
use
set
left
holders
the
this
to
suspension
if
the
(red)
"ON"
and
automatic
both
is
operated
thread
starts
is
pressed.
pedal
(option)
function,
("OFF"
right
The
are
not
of
the
work
is
SW4
when
work
START
at
home
sewing
to
suspend
broken,
from
(See
(A) on
the
holders
switch
DOWN
position
operation,
holders
for
the
home
Fig.
the
sewing
can
is
position.
return
are
the
sewing
example).
position
1.1)
CPU
circuit
machine
be
turnd
not
operative
function
the
not
at
machine
(See
is
on
function
DOWN
Fig.
when
board
shipped).
and
if
is
does
position.
opera
this
should
off
both
used
1.1)
in
the
not
6.14
Thread
When
set
at
the
thread
and
wiper
in
the
set
timing.
When
at
"OFF"
the
thread
and
wiper
work.
For
resetting
the
thread
after
operation,
trimmer
this
"ON"
previously
the
switch
position,
suspension
switch
position,
trimmer
operate
trimmer
do
not
trimmer
refer
of
switch
found
is
of
to
on
the
side
Fig.
wall
.*•
of
,_1Thread
6.5
control
trimmer
box
switch
is
v
-41!
14.4.
-
24
-

7.6
Operating
The
sewing
procedure
machine
and
should
checking
be
operated
and
checked
in
accor
dance
Checking
before
operation:
with
the
following
flow
1) Checkif the power cable is plugged into
the
power source
2) Checkifthe other
3) Check if the
installed.
outlet.
cables
PROM
cassette is correctly
correctly connected.
4) Check if the fuses are not blown.
Start
preparation
Press
the
pushbutton
Does
motor
POWER
the
rotate?
main
ON
NO
Press
OFF
chart:
Check
source
the
pushbutton
power
wiring
POWER
>
CZ)
Reference
Operation
Preparation
Judgement
item
Check
rotational
direction.
Press
pushbutton.
Change
tion
or
reversing
the
(any
inverse
power
POWER
twoofthree
settingofphase
plug.
cable
ON
connec
Set
switchtoSTOP
Press
lift
the
START
wires)
Does
the
holder
home
the
holdergodown?
Depress
work
return
position?
STOP/MOVE
the
work
switchtolet
work
holder.
Does
the
work
the
switch
oes
the
sewing
achine
start?
to
holder
down
Set
switchtoHOME
Set
switchtoRESET
NO
the
RESET/HOME
the
RESET/HOME
Press
the
the
work
POWER
switchtolift
holder.
Press
pushbutton.
the
holder
work
OFF
lift
Adjust
mechanism.
Check
of
the
connector.
the
the
main
work
connection
motor
holder
To
the
next
page
-
27
-

@
To
adjust knife
engagement
pressure, loosen the lock
11.9
(4)
Installing
Put
movable
in
movable
Fig.
Adjusting
(1)
When
noide
discs
nut
screw
the
position
11.12(2).
the
the
is
should
(B) shown
(A).
the
protector
knife
knife,
tension
actuated,
and
together
needle
open
in
knife
as
thread
release
Fig.
under
secure
shown
the
about
11.10
protector
the
it
with
the
in
tension
sole-
tension
1.0mm
and
release
turn
Fig.
the
Max.
Center
11.12(2)
adjusting
Set
Movable
Protector
O.Smin
of
needle
screw
knife
(2)
NOTE:
(3)
as
shown
To
adjust,
shown
the
wire
Opening
increases
is
moved
If
needle
to
ever,
If
opening
loosen
in
of
opening
the
may
the
in
loosen
Fig.
tube.
the
when
to
thread
needle
cannot
screw
Fig.
11.14
the
of
cause
11.13.
the
tension
the
left.
the
may
thread.
loose
be
(A)
and
wire
tension
be
adjusted
and
nut
move
discs
tube
broken
stitch.
(C)
Too
pull
discs
due
by
the
loose
aushing
is
to
tension
moving
wire
About
Fig.
too
small,
excessive
the
to
11.13
discs,
wire
adjust.
1mm
the
tension
how
tube,
-
68
-

When
thread
trimming
signal
and
HALT
signal
are
given
at
the
14.5
same
set
at
stops
Sewing
with
Adjusting
Fabric
SW2
switches.
In
Table
When
feed
shaft
position
If
the
starts
time
"ON",
at
operation
the
feed
the
starts
rotates
switch
after
from
the
work
the
14.1,
switch
is
external
thread
DOWN
holder
fabric
timing
the
when
5.6°
detected
(C)
the
position.
can
can
initial
settings
rotation
per
is
arm
signal
trimming
be
resumed
at
the
feed
be
pulse)
by
the
set
shaft
occurs
DOWN
timing
changed
switch
are
of
synchronizer.
at
"OFF",
rotates
sources
as
the
is
and
by
pressing
position.
by
chaning
settings
shown
arm
shaft
completed
for
for
with
the
in
Table
example,
10
the
work
the
settings
are
for
after
pulses
switch
holder
START
listed.
14.1,
8
pulses
needle
fabric
(i.e.,
(D)
switch
of
fabric
(arm
DOWN
feed
8 + 2
pulses).
Fabric
checked
(1)
With
UP
power.
(2)
Press
switch
holder.
(3)
Start
(4)
While
feed
position,
fabric
remove
as
the
the
the
the
timing
follows:
needle
work
to
lower
sewing
feed
operation
the
starts.
rear
turn
can
at
holder
the
machine
cover
on
be
the
the
work
is
lift
in
(Fig.
and
press
suspension
4.2)
Switch
(A)
(B)
(C)
(D)
Table
the
and
OFF
ON 4
ON 2
ON 1
14.1
HALT
(HALT
the
V-belt.
Timing
8
pulses
pulses
pulses
pulse
switch
condition),
after
(5)
(6)
With
Turn
foot
the
the
will
V-belt
pulley
be
driven
removed,
(balance
by
-
79
wheel)
the
press
stepping
-
the
by
START
hand
motor.
switch.
and
the
presser
/

Connection
of
flat
cables
PLK-4C-CPU
50-circuit
CPU
1 A
2 A
3 A D 4
4 A
5 A
6 A
7 A
8 A D 1 8 A
9 A D 7 9 A
1 0 A D 0 1 0 A
J 1 A
1 2 A
1 3 A A 1 0
1 4 A
1 5 A
1 6 A A 4
1 7 A
] 8 A A 9
1 9 A A 6 1 9 A
2 0 A A 8
2 1 A A 7
2 2 A
2 3 A 2 3 A
2 4 A
2 5 A
~
Signal
G N D
CST-CHECK
C S 1
. C S 2
+ 5 V
connector
D 3
D 5
D 2
D 6 .
A 1
A 2
A 3
A 5
PLK-2-CST
GST
1 A
2 A
3 A
4 A
5 A
6 A
7 A
1 1 A
1 2 A
1 3 A
1 4 A
1 5 A
1 6 A
1 7 A
1 8 A
20
2 1 A
22
24
25
Table
CPU
1 B
2 B
3 B
4 B
5 B
6 B
7 B
8 B
9 B
1 0 B
1 1 B
1 2 B
1 3 B
1 4 B
1 5 B
1 6 B
1 7 B
1 8 B
1 9 B
A
20
B
2 1 B
A
A
A
2 2 B
23
24
25
B
B
B
Signal
G N D
C S 0
C S 3
C S 4
C S 5
C S 6
C S 7
W R
A 0
. R D
I 0 / M
A 1 2
A 1 1
+ 5 V
15.3
C S T
1 B
2 B
3 B
4 B
5 B
6 B
7 B
8 B
9 B
1 0 B
1 1 B
1 2 B
1 3 B
1 4 B
1 5 B
1 6 B
1 7 B
1 8 B
1 9 B
20
21
22
23
24
25
B
B
B
6
B
B
PLK-4C-CPU
CPU
1 A
2 A
3 A
4 A
5 A
6 A
7 A
8 A
9 A
I 0 A
1 1 A
1 2 A
1 3 A
1 4 A
1 5 A
1 6 A
1 7 A
1 8 A
1 9 A
2 0 A
PLK-llPAL
Signal
G N D
E R R 4
E R R 2
.1
0 G ( - )
X S C L S
Y S C L S
V S C A L E 8
" 4
1 0
20
40
8 0
X S C A L E 8
X S C A L E 1
Tab]
Le
15.4
PAL
1 A
2 A
3 A
4 A
5 A
6 A
7 A
8 A
9 A
1 0 A
2
1
t 1 A
1 2 A
1 3 A
1 4 A
1 5 A
1 6 A
1 7 A
4
2
1 8 A
1 9 A
2 0 A
CPU
1 B
2 B
3 B
4 B
5 B
6 B
7 B
8 B
9 B
1 0 B
1 1 B » 4
] 2 B
1 3 B
1 4 B
1 5 B
1 6 B
1 7 B
1 8 B
1 9 B
20
B
Signal
G N D
E R R 3
E R R 1
JOG
RESET/HOME
STOP/MOVE
P S E 1
S P M A X 1
" 4
XSCALE
XSCALE
( + )
C S T
1 B
2 B
3 6
4 B
5 B
6 B
7 B
8 B
9 B
2
8
2
8
80
4 0
2 0
10
1 0 B
1 1 B
1 2 B
1 3 B
1 4 B
1 5 B
1 6 B
1 7 B
I 8 B
1 9 B
20
B
-
84
-

A
MITSUBISHI ELECTRIC CORPORATION
HEAD
OFFICE:
MITSUBISHI
DENKI
BLDG.
MARUNOUCHI
TOKYO
100
TELEX:
J24532
CABLE
MELCO
TOKYO
{8902)ROD
Printed in Japan