
ro
name
model
Ion
Opt
card
RF-312
KF-312
RF-332
RF-332
Unit
Motor
abaft
detector
0SE5K-
6-12-
108
(0SE5K)
0SE5K-
6-12108
(0SE5K)
0SE5K-
6-12-
108
(06E5K)
0AKR5K
-1X-3-
-8-108
(QAKR5K
-IX)
0SE5K-
6-12-
108
(0KE5K)
Machine
end
/ball
end
0SE5KN-ET
ctt,
9.52-0]
Connector
direction
Various
scales
pulse
outputs
1
0.5
cification
can
connected.
ad
screw
detector
of
F/B
of
p
and
p
spe¬
be
0AER5K-1X
-9.52-0
Connector
direction
forna
Unit
Can-
System
O.
0
o
H
•U
u*.
o
O
B
U
0>
0
<
«/>
•
u
u
4J
u
Cl
X)
C
I
•
K
t:
«
B
o
n
<j
-H
O
U)
a
P
v
u
41
r-i
u
U
r-i
<U
i:
<4
i
»
tons
IX
o
o
o
M
I
to
o>
o
H
cn
u
£
"J
u
tn
o.
|
H
r-
•a
o
m
»i
U
O
O
3
f
<2
u
i
01
-X)
1
B
(A
O
U
m
•u
a
O
o
i
u
O
••
-O
M
O
*
c
O'H
02
V)
uo
U
«
O
Q
r-i
a
V
H
U
r-i
u
System
structural
drawing
Maximum
C
o
i
-
u
!
*—
>oci
•U
—
°
Minimum
°
Maximum
°
The
motor
maximum
being
Special
(4.1
•MM
i:
o
I.
U
3
H
o
a
H
M#
»
•
!
ini
JT
itn
(ÿ
n
IJHE'
--3
ion
-
U
1
•a4
4«t.«a.r
h>uu
•i
kill
a*
UltllM*
1
atall
-
C_
-
*c
-
-
kr>
aoi
-
C3
—
__
-
Maximum
°
1
Minimum
•
Maximum
°
LJ
The
maximum
motor
belnx
Special
Maximum
•
Minimum
°
Maximum
°
System
performance
and
motor
Optional
Maximum
sKeli
N*t«f
4<i««ur
•e4
§
I
u
H
rH
u
‘
*
i
M
Ml
MKM
Ull
•
Minimum
°
L.J
Maximum
•
The
maximum
being
motor
Optional
Maximum
HM««
«4«II
n4
<
«••«!•«
(or»
a
o
»-<
U
I
ti
•H
W
MM
•
Minimum
•
»
Maximum
The
motor
1
maximum
belnR
System
Standard
follow-up
resolution
speed
speed
used.
follow-up
Mpps
resolution
speed
speed
used.
follow-up
resolution
speed
scale
follow-up
resolution
speed
speed
used.
follow-up
Mpps
resolution
speed
speed
used.
performance
type
performance:
(Motor
depends
specification
performance:
(Ball
screw
(Ball
6crew
(Ball
screw
depends
_
specification
performance:
depends
being
specification
performance:
(Motor
depends
specification
performance:
(Ball
screw
(Ball
screw
(Ball
screw
depends
_
shaft
used.
shaft
:
:
:
:
:
:
:
:
:
:
0.018
3000
on
end)
0.018
end)
3000
end)
on
1pm
0.5pm
3000
on
0.018
3000
on
end)
0.018
end)
3000
end)
on
end)
the
the
end)
the
the
Servo
amplifier
model
1
Mpps
MR-S2-
o/p
rpms
MR-S2-
o/p
Q-E31
rpm
1
Mpps
MR-S2-
or
rpm
the
1
Mpps
MR-S2-
o/p
rpm
o/p
MR-S2-
rpm
1
Amp
if
nntor
shaft
detector
CN2KO
t
Axis
nuiher
7
L
.
<
N541C583
.
L
7
>
N54
1C582
CN2KO
CN2KO
CN33KO
CN2KO
Cable
ler-
5m-
5m-
cable
AIIÿJ
ad
ad
ad
ball
lit
Lei
screw
-
detector-machine
detector
cable
CN31NRO
MO
CM
31
CN33RO
Remarks
r
(/>
H
O
"T1
(/)
ro
C/>
m
30
m
w
(D
m
30
<
O
w
•<
C/>
H
m
2
<0
M
tv)
wrwa
M
co co
HHOH
O
CO
tv)
CO
Q
M
w
CO
CO
M
w
<
o
CO
5*J
<
CO
K
CO
s
h-*
o
H
M
o
CO
tv)
CO
r*i
&
M
w
to
>
o
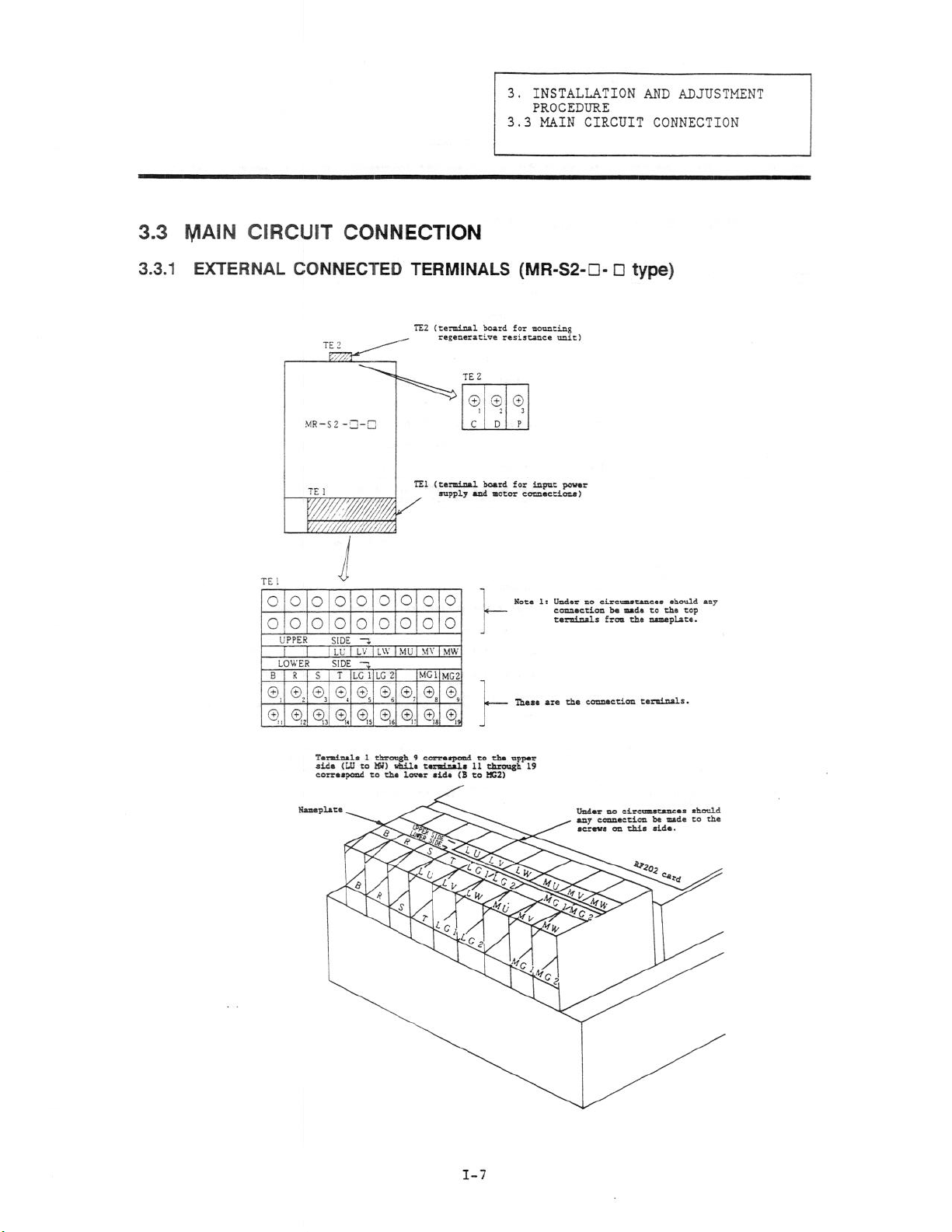
3.
INSTALLATION
PROCEDURE
3.3
MAIN
CIRCUIT
ADJUSTMENT
AND
CONNECTION
3.3
3.3.1
MAIN
CIRCUIT
EXTERNAL
CONNECTED
TE
MR-S2
l
TE
V
TE
i
|o
o
o
o
olo
UPPER
LOWER
B
©,
<3.1
R
®2
I
S
®3
2),
CONNECTION
TERMINALS
(terminal
TE2
ol
000
|
MU
®.
<9,
TE1
1
MCI
o
MV
®„
SI,
regenerative
(terminal
supply
o
fMW
©,
G>,
2
_
_
o
o
SIDE
LU
SIDE
T
©4
<3.
o
olo
—«ÿ
LV1LW
I
—
LC
®s
©„
o
2
1
LC
©.
©„
2
TE
© ©
I
and
(MR-S2-D-
board
for
mounting
unit)
©
3
P
for
input
power
connections
Kota1:Undernocircumstances
These
)
connectionbemadetothe
terminals
the
are
board
motor
resistance
2
D
from
connection
type)
the
nameplate.
terminals.
should
any
top
Terminals
side
correspond
Haseplate
1
(LUtoMV)
to
B
through
the
t
while
s
lower
correspond
9
terminals
side
j-
•ky
(B
1-7
11
to
to
the
through
2)
MG
Hi-
upper
19
Under
any
screws
circumstances
no
connection
on
this
be
side.
mads
should
to
the
Hu
Hy
He

3.
INSTALLATION
PROCEDURE
3.3
MAIN
CIRCUIT
AND
ADJUSTMENT
CONNECTION
3.3.2
Terminal
board
TE1
TE2
TERMINAL
Terminal
board
No.
1
2
3
4
5
6
7
8
9
11
12
13
14
15
16
17
18
19
1
2
3
BOARD
Terminal
position
Upper
side
Lower
side
CONNECTIONS
Terminal
name
No
No
No
LU
LV
LW
MU
MV
MW
B
R
S
T
LG1
LG2
MCI
MG2
C
D
P
E
Connect
Connect
Connect
Connect
Connect
Connect
When
remove
Connect
Connect
Connect
No
Connect
Connect
When
between
terminals
Connect
connection
connection
connection
the
phase
the
phase
the
phase
the
phase
the
phase
the
phase
making
the
shorting
3-phase
thermal
thermal
EMR
the
the
the
the
connection
the
thermal
the
thermal
the
using
regenerative
terminalsDandPand
between
the
chassis
Details
U
V
W
U
V
W
terminalsCand
of
terminal
terminal
terminal
terminal
terminal
terminal
connection
bar
from
AC
200/220V
relay
terminal
relay
terminal
relay
terminal
relay
terminal
ground
connection
of
of
of
of
of
of
the
unit,
connect
and
the
the
the
the
the
the
(external
R
power
motor
L
L
L
M
M
M
terminal.
1
of
of
2
of
1
of
2
remove
P.
ground.
axis
axis
axis
axis
axis
axis
emergency
supply.
the
the
theMaxis
theMaxis
the
the
regenerative
motor.
motor.
motor.
motor.
motor.
motor.
L
L
axis
axis
shorting
stop),
motor.
motor.
motor.
motor.
bar
unit
Note:
The
connections
Specifications
differ
Manual.
slightly
for
the
MR-S2S-0-0
1-8
type
and
so
reference
should
be
madetothe
MR-S2

3.
INSTALLATION
PR
F
nr*
3.3
MAIN
run?
F
CIRCUIT
ADJUSTMENT
AND
CONNECTION
3.3.5
Motor
CANNON
type
HA23C
HA33C
HA40C
HA43C
HA80C
HA83C
HA100C
HA23CB
HA33CB
PLUGS
Motor
connector
end
r.
§°6°o
°cDoc
MS3102A18-12P
I
H
O
Oc
i
Oil
60
MS3102A22-23P
fFO0OA
Eo
bo
MS3102A24-10P
k°66o
op
r
o
.
B
°oDoc
MS3102A18-12P
MS3102A10SL-4P
USED
KS3108A18-12S
KS3206A18-
(Straight
MS3108B22-23S
MS3106B22-23S
(Straight
KS3108B24-10S
MS3106B24-10S
WS31081I8-12S
MS3106A18-12S
(Straight
KS3
108B10SL-4S
KS3106B10SL-4S
(Straight
The
figure
*
07F-
-DC
12S
type)
s
status.
type)
shove
or
or
type)
type)
or
the
or
or
BRAKE
HH
Cannon
MOTOR
tj
CD
MOTOR
nr
Cb
MOTOR
in
Cb
MOTOR
bb
plug
Z3
XX
used
To
4
To
To
mu
To
amplifer
Powar
for
fH
To
amplifier
amplifier
amplifer
amplifier
rupply
braka
J
Note:
HA40CB
HA8CCB
HA100CB
(1)
Select
cable
(2)
The
the
in
MS3102A22-23P
o,o
MS3102A24-10P
MS3102A10SL-4P1
MS3108
the
(MS3057)
clamp
motor
of
flange
position
5
0
fs6
°o°o
'
O
O
M
o
o
o
0
angular
a
or
Cannon
the
direction.
plug,
piping
connector
*
MS3106
connector.
KS3108B22-23S
MS3106B22-23S
(Straight
The
re
f
status.
0
-DC
£
MS3108B24-10S
MS3106B24-10S
(Straight
MS3108B10SL-4S
MS3106B10SL-4S
(Straight
straight
should
key
1-13
shows
type)
plug
be
Wÿ
or
type)
the
or
type)
or
set
MOTOR
BRAKE
MOTOR
DRAM.
HtZT
cS
Zl
A
To
iM
O
Power
I
supply
braka
for
excitation
amplifier
Powar
supply
I
braka
for
excitation
je-ie-di