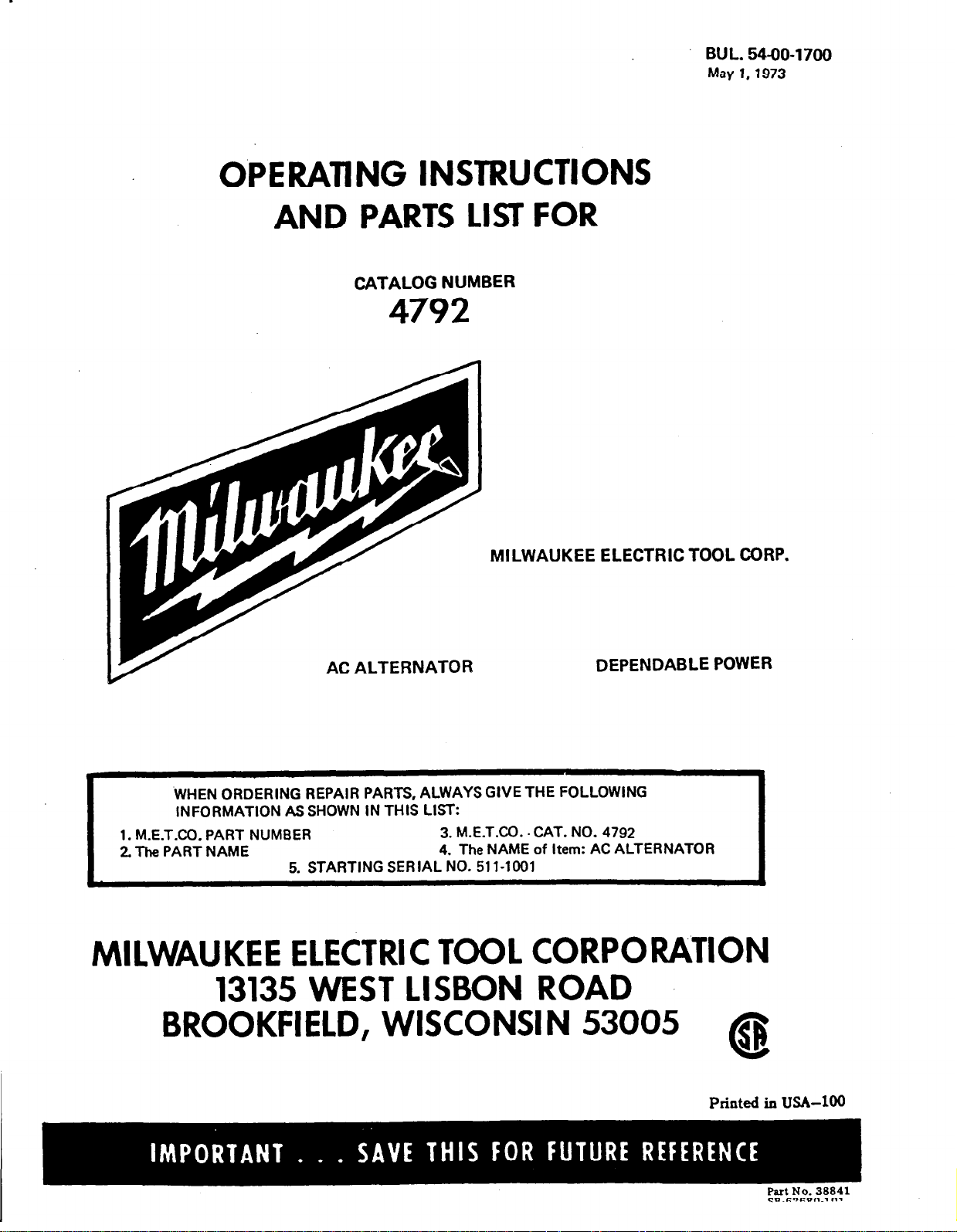
OPERAl’lNG INSTRUCTIONS
AND PARTS LIST FOR
CATALOG NUMBER
4792
BUL. 54-00-1700
May 1.1973
MILWAUKEE ELECTRIC TOOL CORP.
DEPENDABLE POWER
WHEN ORDERING REPAIR PARTS, ALWAYS GIVE THE FOLLOWING
INFORMATION AS SHOWN IN THIS LIST:
1. M.E.T.CO. PART NUMBER
2 The PART NAME
5. STARTING SERIAL NO. 51 l-1001
AC ALTERNATOR
3. M.E.T.CO. . CAT. NO. 4792
4. The NAME of Item: AC ALTERNATOR
MILWAUKEE ELECTRIC TOOL CORPORATION
13135 WEST LISBON ROAD
BROOKFIELD, WISCONSIN 53005
a
Printed in USA-100
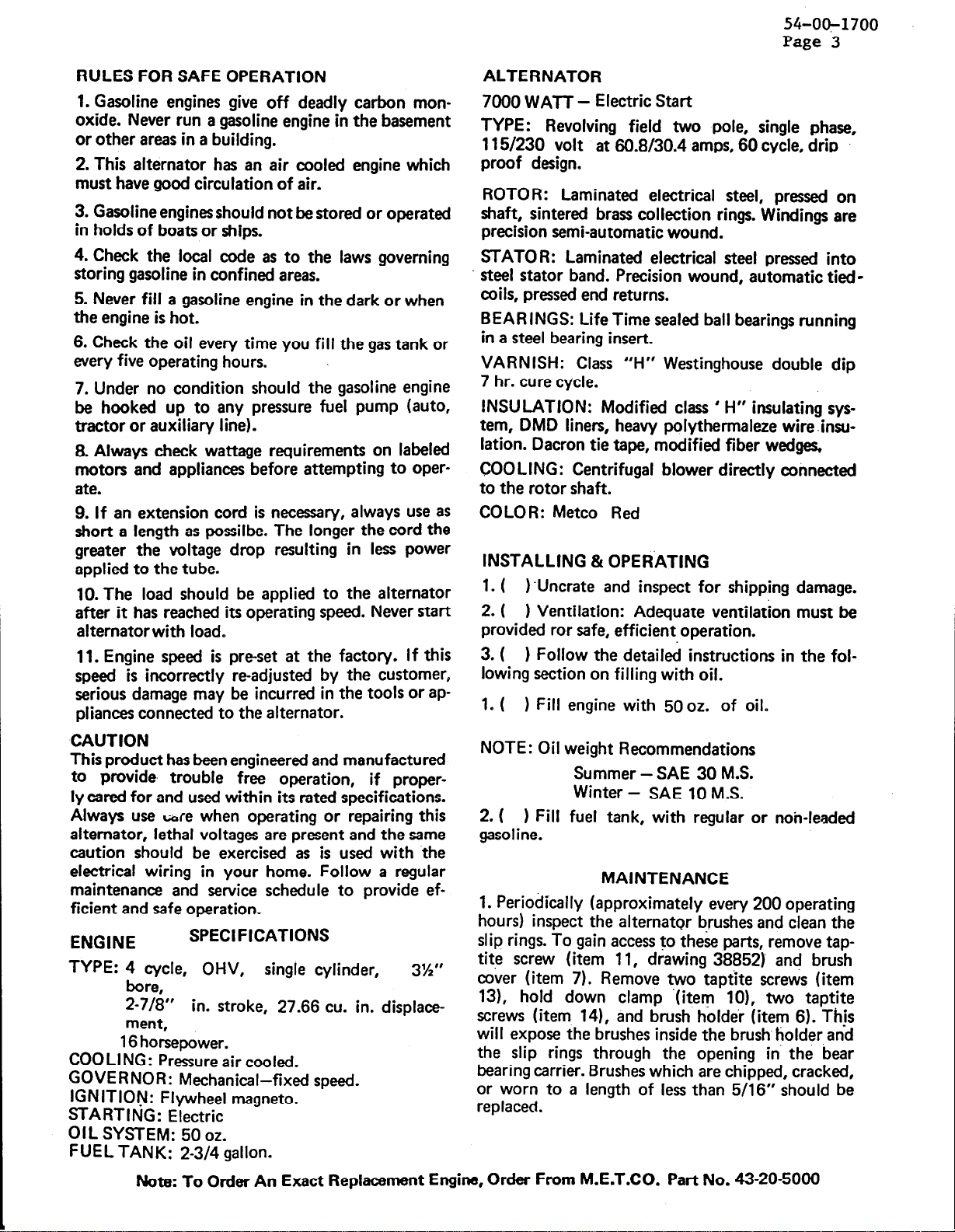
54-00_1700
Page 3
RULES FOR SAFE OPERATION
1. Gasoline engines give off deadly carbon monoxide. Never run a gasoline engine in the basement
or other areas in a building.
2. This alternator has an air cooled engine which
must have good circulation of air.
3. Gasoline engines should not be stored or operated
in holds of boats or ships.
4. Check the local code as to the laws governing
storing gasoline in confined areas.
5. Never fill a gasoline engine in the dark or when
the engine is hot.
6. Check the oil every time you fill the gas tank or
every five operating hours.
7. Under no condition should the gasoline engine
be hooked up to any pressure fuel pump (auto,
tractor or auxiliary line).
8. Always check wattage requirements on labeled
motors and appliances before attempting to oper-
ate.
9. If an extension cord is necessary, always use as
short a length as possilbe. The longer the cord the
greater the voltage drop resulting in less power
applied to the tube.
10. The load should be applied to the alternator
after it has reached its operating speed. Never start
alternatorwith load.
11. Engine speed is preset at the factory. If this
speed is incorrectly readjusted by the customer,
serious damage may be incurred in the tools or appliances connected to the alternator.
ALTERNATOR
7000 WATT - Electric Start
TYPE: Revolving field two pole, single phase,
115/230 volt at 66.8/30.4 amps, 60 cycle, drip
proof design.
ROTOR: Laminated electrical steel, pressed on
shaft, sintered brass collection rings. Windings are
precision semi-automatic wound.
STATOR: Laminated electrical steel pressed into
steel stator band. Precision wound, automatic tiedcoils, pressed end returns.
BEARINGS: Life Time sealed ball bearings running
in a steel bearing insert.
VARNISH: Class “H” Westinghouse double dip
7 hr. cure cycle.
INSULATION: Modified class ’ H” insulating system, DMD liners, heavy polythermalete wire.insulation. Dacron tie tape, modified fiber wedges,
COOLING: Centrifugal blower directly connected
to the rotor shaft.
COLOR: Metco Red
INSTALLING & OPERATING
1. ( 1 ‘Uncrate and inspect for shipping damage.
2. ( ) Ventilation: Adequate ventilation must be
provided ror safe, efficient operation.
3. ( 1 Follow the detailed instructions in the following section on filling with oil.
1. ( 1 Fill engine with 50 oz. of oil.
CAUTION
This product has been engineered and manufactured
to provide- trouble free operation, if properly cared for and used within its rated specifications.
Always use r;afe when operating or repairing this
alternator, lethal voltages are present and the same
caution should be exercised as is used with the
electrical wiring in your home. Follow a regular
maintenance and service schedule to provide efficient and safe operation.
ENGINE
TYPE: 4 cycle, OHV, single cylinder,
bore,
2-7/8” in. stroke, 27.66 cu. in. displacement,
16 horsepower.
COOLING: Pressure air cooled.
GOVERNOR: Mechanical-fixed speed.
IGNITION: Flywheel magneto.
STARTING: Electric
01 L SYSTEM: 50 oz.
FUEL TANK: 2-3/4 gallon.
Note: To Order An Exact Replacement Engine, Order From M.E.T.CO. Part No. 43-20-5008
SPECIFICATIONS
3%”
NOTE: Oil weight Recommendations
Summer - SAE 30 M.S.
Winter -
2. ( 1 Fill fuel tank, with regular
gasoline.
MAINTENANCE
1. Periodically (approximately every 200 operating
hours) inspect the alternator brushes and clean the
slip rings. To gain access to these parts, remove taptite screw (item 11, drawing 38852) and brush
cover (item 7). Remove two tapdte screws (item
131, hold down clamp ‘(item lo), two taptite
screws (item 141, and brush holder (item 6). This
will expose the brushes inside the brush.holder and
the slip rings through the opening in the bear
bearing carrier. Brushes which are chipped, cracked,
or worn to a length of less than 5/16” should be
replaced.
SAE 10 M.S.
or non-leaded