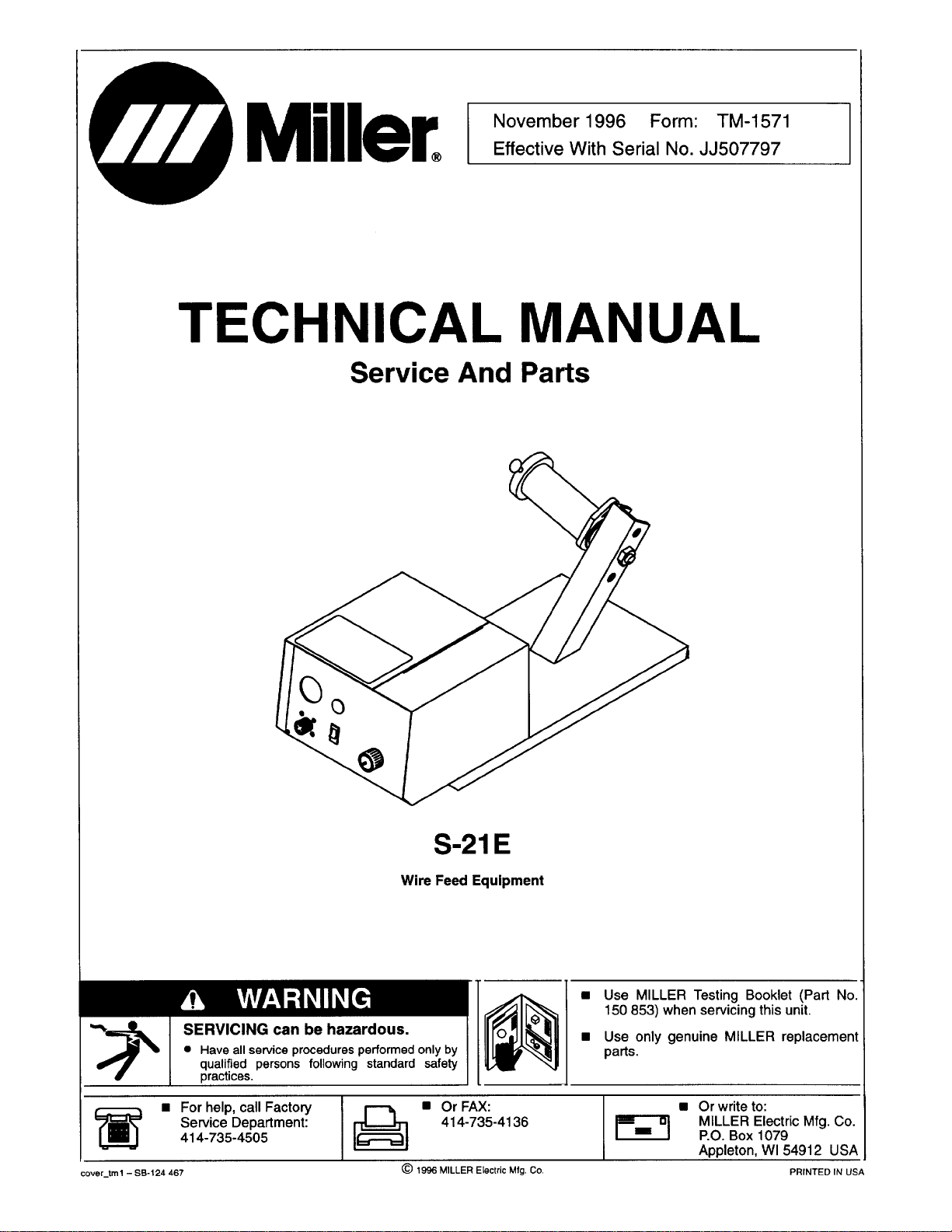
MiIIe~
November1996
Effective
With Serial
Form:
No.
TM-1571
JJ507797
TECHNICAL
Service
And
MANUAL
Parts
coverjml—SB-124
A
SERVICING
•
Have
qualified
practices.
U
For
help,
Service
414-735-4505
467
WARNING
canbehazardous.
all
service
procedures
persons
call
Factory
Department:
following
performed only
~U~r
Wire
standard
©
S-21E
Feed
Equipment
by
safety
FAX:
14-735-4136
1996
MILLER Electric
Mfg.
Co.
Use
MILLER
150
853)
Use
only genuine
parts.
L................J
Testing Booklet
when
servicing
MILLER
U
Or
write
MILLER
RO.
Box
Appleton,WI54912
this
unit.
replacement
to:
Electric
1079
PRINTEDINUSA
(Part
Mfg.
No.
Co.
USA

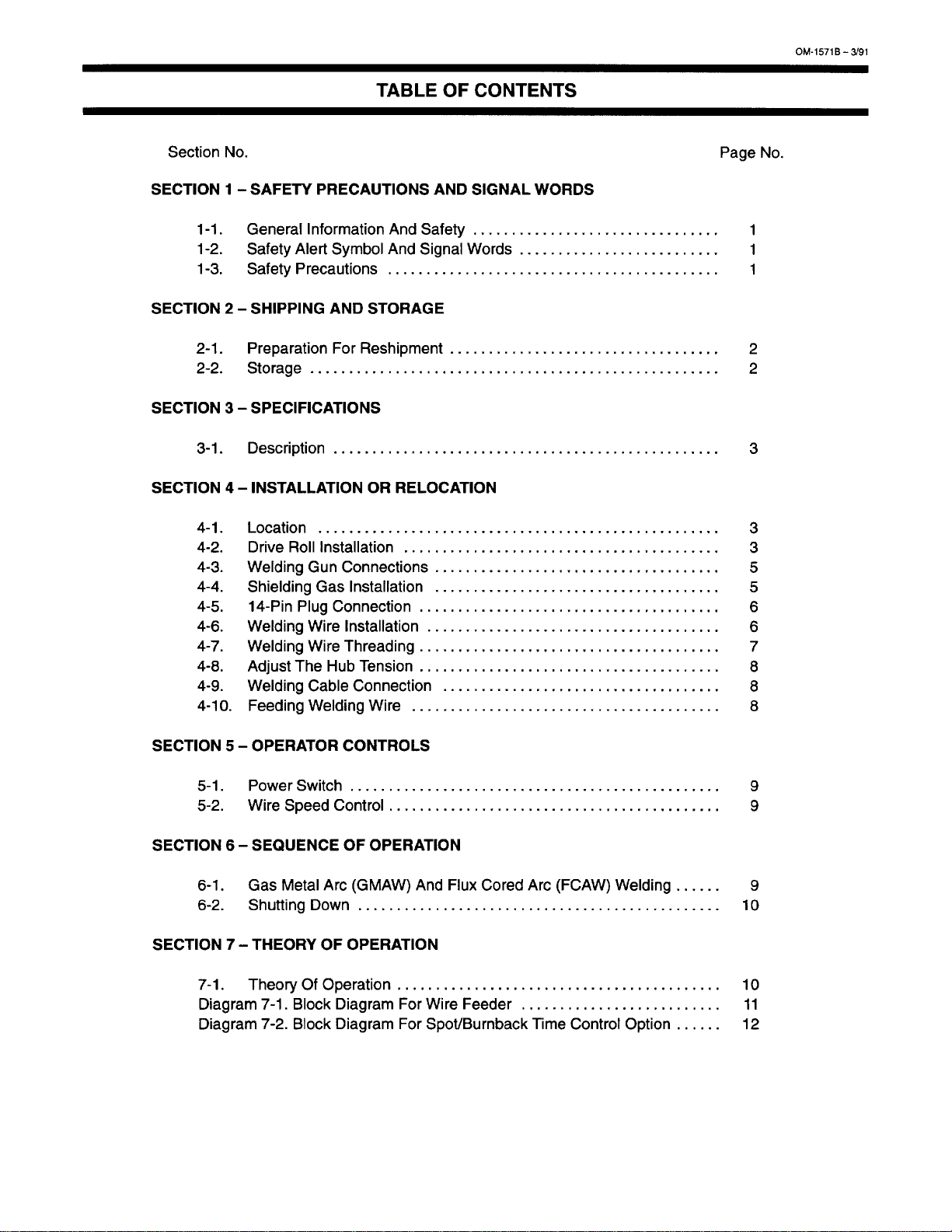
TABLEOFCONTENTS
OM-1571B—3/91
Section
SECTION
SECTION2-SHIPPING
No.
1-SAFETY
1-1.
1-2.
1-3.
General
Safety
Safety
PRECAUTIONS AND
Information And
Alert
Precautions
2-1. Preparation
Symbol And
AND
STORAGE
For
Reshipment
Safety
Signal
SIGNAL
Words
2-2. Storage
SECTION3—SPECIFICATIONS
3-1.
Description
SECTION4-INSTALLATIONORRELOCATION
4-1.
4-2.
4-3.
4-4. Shielding
4-5.
4-6.
4-7.
4-8.
4-9.
4-10.
Location
Drive
Roll
Installation
Welding Gun Connections
Gas
Installation
14-Pin
Welding
Welding
Adjust
Welding
Feeding Welding
Plug
Wire
Wire
The
Cable
Hub
Connection
Installation
Threading
Tension
Connection
Wire
WORDS
Page
No.
1
1
1
2
2
3
3
3
5
5
6
6
7
8
8
8
SECTION
5-OPERATOR
5-1.
5-2.
Power
Wire
Switch
Speed
CONTROLS
Control
SECTION6—SEQUENCEOFOPERATION
6-1.
6-2.
Gas
Metal Arc (GMAW)
Shutting
Down
And
Flux Cored
SECTION7-THEORYOFOPERATION
7-1.
Diagram
Diagram
Theory Of
7-1.
Block
7-2.
Block
Operation
Diagram
Diagram
For
Wire Feeder
For
SpotlBurnback
Arc
(FCAW) Welding
Time
Control
Option
9
9
9
10
10
11
12
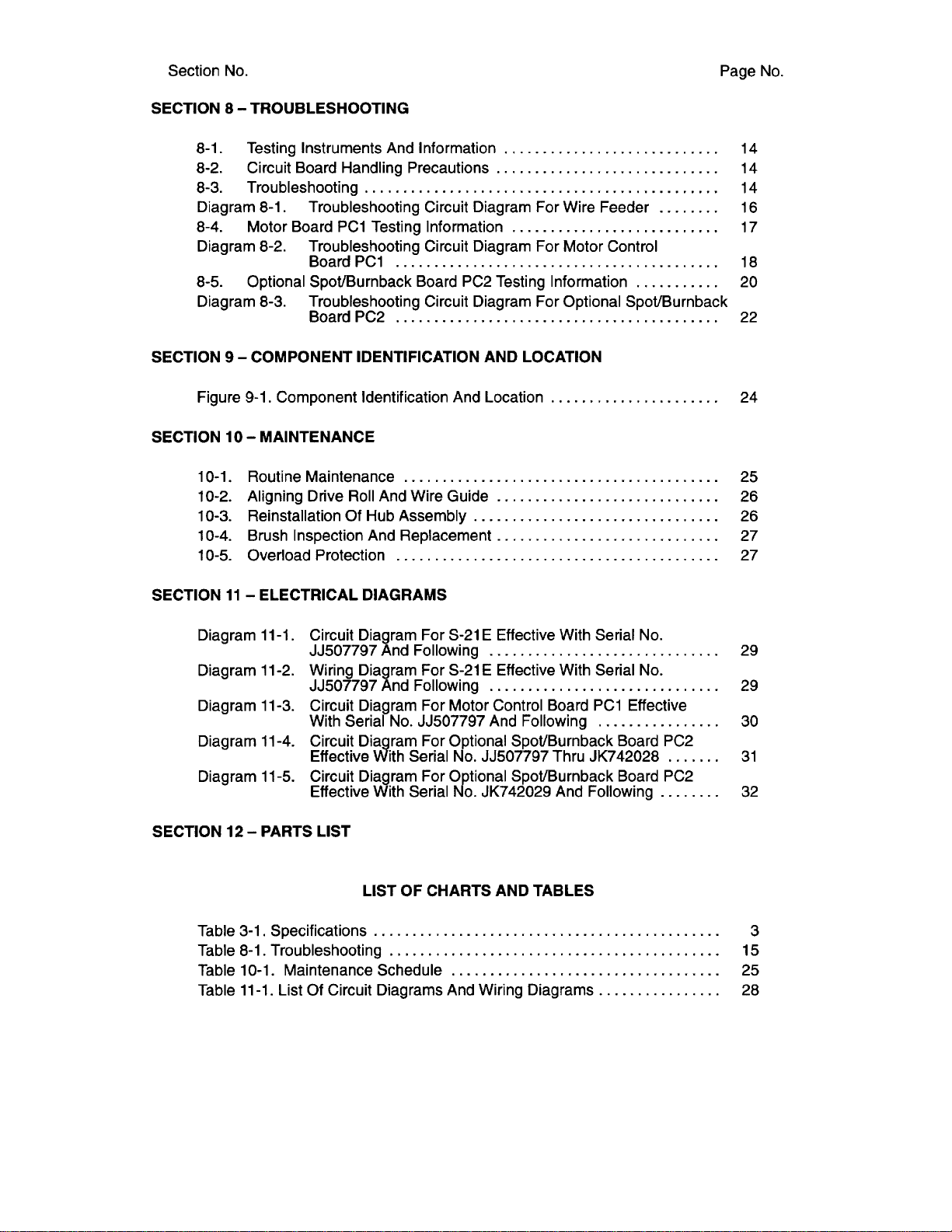
Section
SECTION8-TROUBLESHOOTING
No.
Page
No.
8-1.
8-2.
8-3.
Diagram
8-4. Motor
Diagram
8-5.
Diagram
SECTION9-COMPONENT
Figure
SECTION
10-1.
10-2.
10-3.
10-4.
10-5.
SECTION
Testing
Circuit
Troubleshooting
Optional
9-1.
10—
Routine
Aligning
ReinstallationOfHub
Brush
Overload
11-ELECTRICAL
Instruments And Information
Board
Handling
8-1.
8-2.
8-3.
MAINTENANCE
Troubleshooting
Board
PCi
Troubleshooting
Board
SpotlBurnback
Troubleshooting
Board PC2
Component
Maintenance
Drive
Roll And
Inspection
Protection
Precautions
Circuit
Testing
Circuit
PCi
Board PC2 Testing
Circuit
IDENTIFICATION
Identification And
Wire
Assembly
And
Replacement
DIAGRAMS
Diagram For
Information
Diagram For
Diagram For
Guide
AND
LOCATION
Location
Wire Feeder
Motor Control
Information
Optional Spot/Burnback
14
14
14
16
17
18
20
22
24
25
26
26
27
27
Diagram
Diagram
Diagram
Diagram
Diagram
SECTION
Table 3-1.
Table 8-1.
Table
Table
11-1.
11-2.
11-3.
11-4.
11-5.
12—
PARTS
Specifications
Troubleshooting
10-1.
Maintenance
11-1.
ListOfCircuit Diagrams
Circuit
JJ507797
Wiring
JJ507797
Circuit
With Serial
Circuit
Effective
Circuit
Effective
Diagram For
Diagram
Diagram For
Diagram
With Serial
Diagram For
With Serial
LIST
LISTOFCHARTS AND
S-21EEffective
And Following
For
S-21EEffective
And Following
No.
Schedule
Motor Control
JJ507797 And Following
For
Optional
No.
JJ507797
Optional Spot/Burnback
No.
JK742029
And
Wiring
With Serial
With
Serial
Board
PCi
SpotlBurnback
Thru
JK742028
And Following
TABLES
Diagrams
No.
29
No.
29
Effective
30
Board PC2
31
Board PC2
32
3
15
25
28

SECTION
1-SAFETY
PRECAUTIONS
AND
SIGNAL WORDS
1-1.
This
specific
dures.Italso includes
vanttothese
tive toolinthe
ever,itdoes
training
arises
sented,orif
manual,
proceeding
1-2.
The
used
identify
tions.
A
A
A
IMPORTANT
GENERAL
manual
about
following safety alert
throughout
provides
operating,
procedures.
handsofa
not
nor
safety-conscious service
the
problems
contact
further.
SAFETY
WORDS
different
This safety alert
words
WARNING and
tionto
the
WARNING statements identify
practices which
ous personal injury
CAUTION
practices which
personal injuryordamagetothis
statements identify special
necessary
for
the
INFORMATION
testing, and
and
cannot
specific
arise
the
factory
ALERT
this
levels of
safety
statements identify procedures
most efficient
ment.
1-3.
SAFETY
PRECAUTIONS
AND SAFETY
theoryofoperation
troubleshooting
precautionary information
This
manual
trained
application
which
symbol
manual to
hazard
symbolisused
statements.
mustbefollowedtoavoid
mustbefollowedtoavoid
serviceperson.
take
the
work.Ifany
of procedures
are
not
Service Department
SYMBOL AND
and signal
call
and
CAUTIONtocall
or loss of
along
can
be an
placeofprevious
covered
SIGNAL
words
attention
special
with
the
procedures
life.
equipment.
instructions
operationofthis
with
proce-
rele-
effec
How-
doubt
pre
in this
before
are
to and
instruc
signal
atten
or
seri
or
minor
equip
•
Shut
down
unit
and
disconnect
when
servicing
cally
requiresanenergized
•
Do
not
leave
-
-
ARC
RAYS,
can
burn eyes
hearing.
•
Wear
FUMES
your
health.
•
Keep
•
Ventilate to
correct
AND
your
unless
live
SPARKS,
and
eye,
GASES can
the
unit
unattended.
AND HOT
skin; NOISE
ear,
and body
head outofthe
keep
from
breathing
input
procedure
unit.
SURFACES
can
damage
protection.
seriously
fumes.
fumes
power
specifi
harm
and
-
gases.
•Ifventilationisinadequate,
breathing
•
-
Read Material
and
materials
-
WELDING
wounds.
•
Do
any
-
HOT
cause
•
Watch
•
Haveafire
howtouse
•
Do
•
-
Allow
device.
Safety
manufacturer’s
used.
WIRE
not
point
gun towardany
conductive
METAL,
fire
and
for
surface,orother
SPATrER,
burns.
fire.
extinguisher
it.
not
use
near
flammable
work
and
Data
instructions
can
equipmenttocool
use
Sheets
cause
part of
AND
nearby
material.
approved
(MSDSs)
for
any
puncture
the
body,
personnel.
SLAG
and
can
know
before
handling.
MOVING
•
Keep
PARTS
away
can
from
cause
moving
serious
parts.
injury.
A
5-21E
W
ARNING: ELECTRIC
S
Do
not
touch
live
•
Protect
and
•
Insulate
rubber9loves
power is
yourself
clothing.
yourself
and
appliedtothe
SHOCK
electrical
with
dry
from
groundbyusing
insulating
unit.
can kill.
parts.
insulating
floormats
gloves
when
HOT
SURFACES
•
Allow
cooling
MAGNETIC
can
affect
pacemaker
•
Wearers
going near
mentorany
can
period
FIELDS
should
consult
the
servicingofarc
arc
welding
cause
before
FROM
HIGH CURRENTS
operation.
their
operations.
severe
burns.
servicing.
doctor
welding
TM-1571
before
equip
Page
1
-
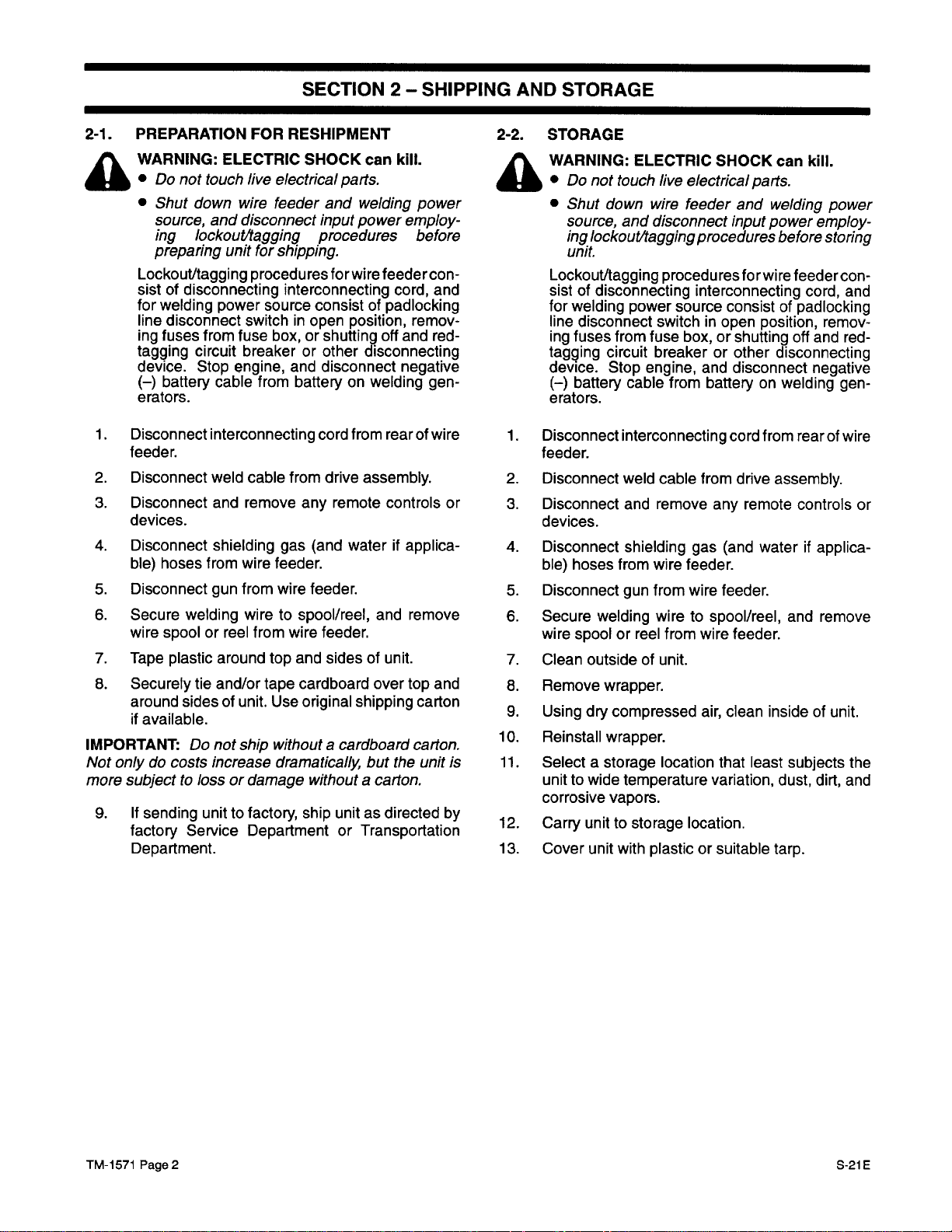
SECTION2-SHIPPING
AND
STORAGE
PREPARATION
WARNING:
•
Do
not
A
•
Shut
source,
ing
touch
down wire
and
lockout/tagging
preparing unit
Lockout/tagging
sistofdisconnecting
for
welding
line
disconnect switch
ing
fuses
from
tagging circuit breaker or
device.
(—)
erators.
1.
Disconnect
feeder.
2.
Disconnect
3.
Disconnect and remove
devices.
4.
Disconnect
ble)
5.
Disconnect gun
6.
Secure
wire
7.
Tape
8.
Securely
around
if
available.
IMPORTANT:
Not
onlydocosts increase
more
subjecttolossordamage
9.
If
sending
factory
Department.
Stop
battery
hoses from
spoolorreel
cable
interconnecting
weld
shielding
welding
plastic
tie
sidesofunit.
Do
not
unittofactory,
Service
FOR
RESHIPMENT
ELECTRIC
live
disconnect
SHOCK
electrical
feeder
and
input
can
parts.
welding
power
procedures
for
shipping.
procedures
power
source
fuse
box,
engine, and
from
cable
gas
wire
feeder.
from
wire
wiretospool/reel,
from
around
and/or tape cardboard over
top
Use
ship without
dramatically
forwire
interconnecting
consistofpadlocking
in open
or shutting
other
disconnect
batteryonwelding
cord
from drive
any
remote
(and
feeder.
wire
feeder.
and
sidesofunit.
original
feedercon
position,
off
disconnecting
from
rearofwire
assembly.
controls
waterifapplica
and
shipping carton
a cardboard
but
cord,
the
withoutacarton.
ship
unitasdirected
DepartmentorTransportation
kill.
power
employ
before
and
remov-
and rednegative
gen
remove
top
and
carton.
unit
or
by
is
STORAGE
WARNING:
•
A
-
Do
•
Shut
source,
ing
ELECTRIC
not
touch
live
electrical
down
wire
feeder
and
disconnectinput power
lockout/tagging
procedures
SHOCK
parts.
and
can
kill.
welding
employ
before
power
-
storing
unit.
-
-
-
10.
11.
12.
13.
Lockout/tagging
sistofdisconnecting
for
welding
line
disconnect switch
ing
fuses
tagging circuit
device. Stop
(—)
battery
erators.
1.
Disconnect
feeder.
2.
Disconnect weld
3.
Disconnect and remove
devices.
4.
Disconnect
ble)
hoses
5.
Disconnect gun
6.
Secure
wire
spoolorreel
7.
Clean outside of
8.
Remove
9.
Using
Reinstall wrapper.
Selectastorage
unittowide
corrosive
Carry
Cover
power
from
cable
interconnecting
shielding
from
welding
wrapper.
dry
compressed
temperature
vapors.
unit
to storage
unit
with
procedures
source consistofpadlocking
fuse box,
breakerorother
engine, and
from
cable
gas
wire
feeder.
from
wire
wiretospool/reel,
from
unit.
location that
location.
plastic
forwirefeedercon
interconnecting
in open
or shutting
disconnect negative
batteryonwelding
cord
from drive
any
remote
(and
feeder.
wire
feeder.
air,
clean
least
variation,
or suitable
cord,
position,
off and
disconnecting
from
rearofwire
assembly.
controls
waterifapplica-
and remove
inside of
subjects
dust,
tarp.
and
remov-
red-
gen
unit.
the
dirt,
and
-
-
or
TM-1571
Page
2
5-21E
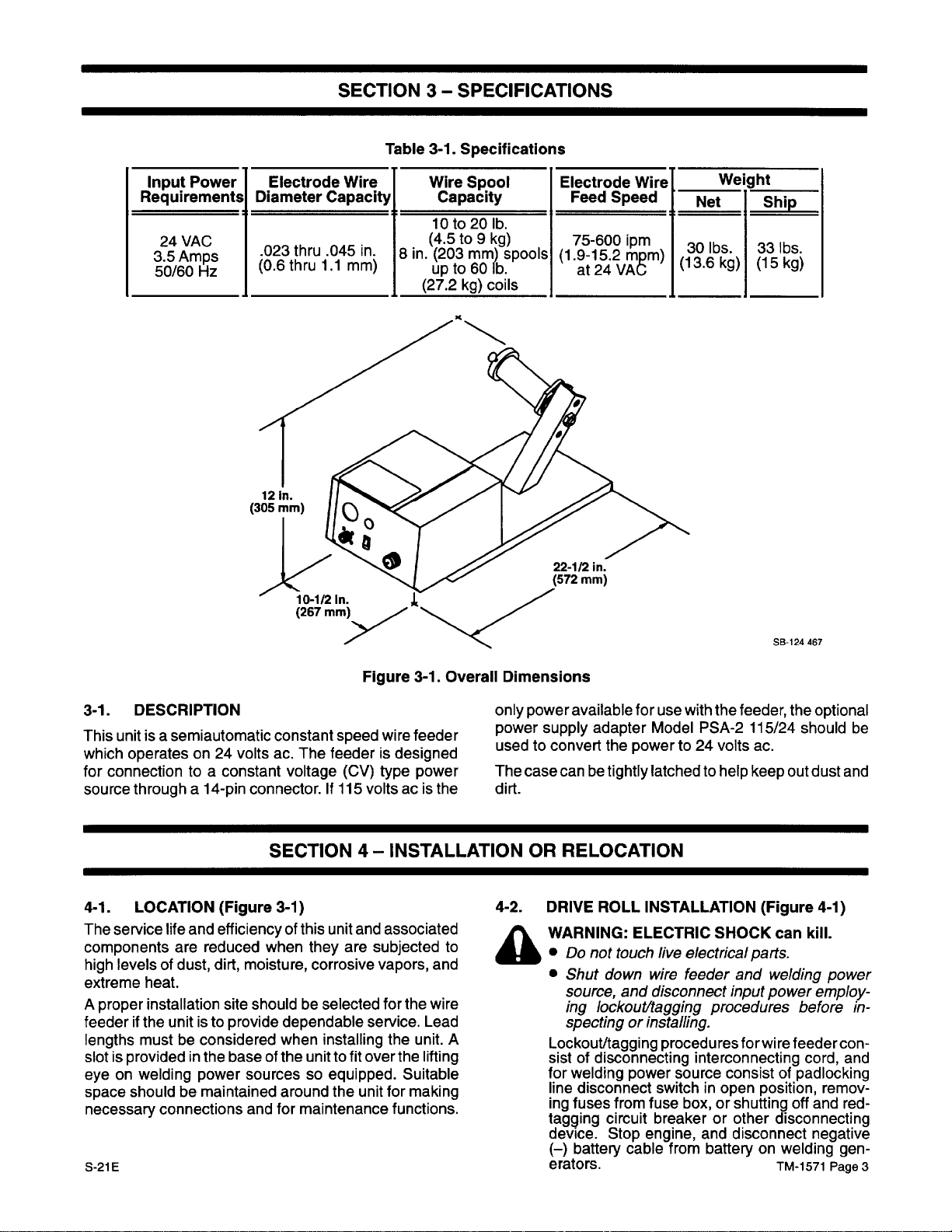
SECTION3-SPECIFICATIONS
Input
Power
Requirements
24
VAC
3.5
Amps
50/60
Hz
Electrode
Diameter
.O23thru
(0.6 thru
10-112
(267
Wire
Capacity
.045
in.
1.1
mm)
In.
mm)
Table 3-1.
Wire
Capacity
10to20
(4.5 to9kg)
8
in.
(203mm)
upto60
(27.2
Specifications
Spool
lb.
spools
lb.
kg)_coils
Electrode
(1.9-15.2
22-1(2
(572
Wire
Feed Speed
75-600 ipm
mom)
at24VA~
in.
mm)
Net
30
(13.6
Weight
lbs.
kg)
Ship
33
lbs.
(15 kg)
3-1. DESCRIPTION
This
unitisa
which
for
connection toaconstant
source
4-1.
The
service
components
high
levels of
extreme
A
proper installation
feederifthe
lengths
slotisprovided in
eyeonwelding
space
necessary
S-21E
semiautomatic
operates
througha14-pin
LOCATION
heat.
mustbeconsidered
shouldbemaintained
on 24
volts
(Figure 3-1)
life
and
efficiencyofthis unit
are
reduced
dust,
dirt, moisture,
site shouldbeselected
unitisto provide
the
baseofthe
power
connections
Figure
constant speed wire feeder
ac.
The
feederisdesigned
voltage (CV)
connector.If115
volts acisthe
3-1. Overall Dimensions
only
power supply
used
type
power
The
dirt.
SECTION4-INSTALLATION OR
4-2.
and
associated
when
they
are
subjected to
corrosive
dependable
when
installing
unittofit
sourcessoequipped. Suitable
around
and
for
maintenance
the
vapors, and
for
the
service.
the
over
the
unit
for
making
functions.
wire
Lead
unit.
lifting
A
A
power
available
to convert
case
canbetightly
for
adapter
the
powerto24
use
Model
latched to
RELOCATION
DRIVE
WARNING: ELECTRIC
•
•
Lockout/tagging
sistofdisconnecting
for
line
ing
tagging
device.
(—)
erators.
ROLL
INSTALLATION (Figure 4-1)
Do
not
touch
live
Shut
down
wire
source,
ing
and
disconnect
lockout/tagging
spectingorinstalling.
welding
disconnect switch
fuses
battery
power
from
circuit
Stop
cable
fuse
breakerorother
engine, and
SB-124
467
with
the
feeder,
PSA-2
volts
help
SHOCK
electrical
feeder and
input
procedures
procedures
source consistofpadlocking
box,
from
for
interconnecting
in open
or shutting
disconnect negative
batteryonwelding
the
optional
115/24 should
ac.
keep
out
dust
can kill.
parts.
welding
power
power
employ
beforein-
wire feeder
cord,
position,
remov-
off
and
disconnecting
TM-1571
Page
be
and
con
and
red-
gen
-
-
-
3

Wire
•
Spring
Hub
Pressure
(ShownInOpen
9
Roll
Assembly
PosItion)
Retaining
Ring
•
OPTIONAL
Itisnecessarytoinstall
tingupthis unit
IMPORTANT:
Base drive
and
the
also
recommendations:
The
dual-grooved drive
commodates
wire.
This
knurled
.030
in.
groove
wire.
The
sideofthe
feeder,
visible.
The50Series wire feeder
with
this feeder,
used,aknurled
.035
and
A
.023
drive
groove.
(0.6 and
for
feeding
wire
drive
the
wire
.045
(.089
W
ARNING:
Do
not
ment. The
cally
Use
size
roll.
size
drive
hot
roll
through
roll
has
the “V”
0.76
mm)
.035
and
for
each
When
stamp
but,
due to
roll is
and
ELECTRIC
store metallic
motor
whenever
gized.
TM-1571
Page
4
Ret.
50497
Figure
required
when
roll
provided
.045
both
groove
the
for
style
recommended
1.1
drive
changing
selectiononthe
with
in.
(0.6 through
a
“‘I”
groove
for
wire.
Use
.045
in.
(0.89
grooveisstampedonthe
drive
roll is
the
unused
drive
rolls
the flat
mm)
idler pressure
wire.
SHOCK
4-1.
rolls
when
wire
the
feederac-
and
feeding
the
“V”
and
installedinthe
groove
maybeused
when
can
objectsinthis
drive
assemblyiselectri
the
welding
circuitisener
Wire
set
sizes.
following
1.1
mm)
a
“‘I”
.023
and
knurled
1.1
mm)
will
be
roll
feeding
kill.
compart
Feeder
-
IMPORTANT:
can
verse
The
be
1.
2.
3.
4.
-
-
-
Components
Loose
createanelectrical
put
nents
metal
circuit and
resulting in
Both
be reversed
for
rollstoposition
dual-grooved
reversed,
a.
b.
c.
d.
but
Unlatch
Loosen
knob
Pivot
carrier.
For
and
pressure
free of
pressure
dual-grooved
Choose
Slide
drive
chosen
wire
size
after
installation.
Align
the
Insert
securing
the
groove
objects
path
any
metal
electric
typesof50
reuse
when
unused
drive
roll
pro
onlytofeed a
open
left
case
adjustment
pressure
proper
roll onto
for
the
drive
arm.
arm
away
roll
supplied
groove.
drive
toward
unused
roll
with
screws, and tighten.
GunlFeeder
connector
Securing
Ref.
in this
compartment
between
surfacesorcompo-
shock.
Series
they
the
style
become
groove(s)tofeed
vided
with
this
feedercan
different
inside of machine.
holes.
size
access
to expose
roll
groove
door.
knob,
with
feeder:
mounting hub with
willbevisible
Knob
SB-125
923
may
weld
out
drive
rolls
worn.Re-
wire.
wire.
and
pivot
drive
roll
The
5-21E
-
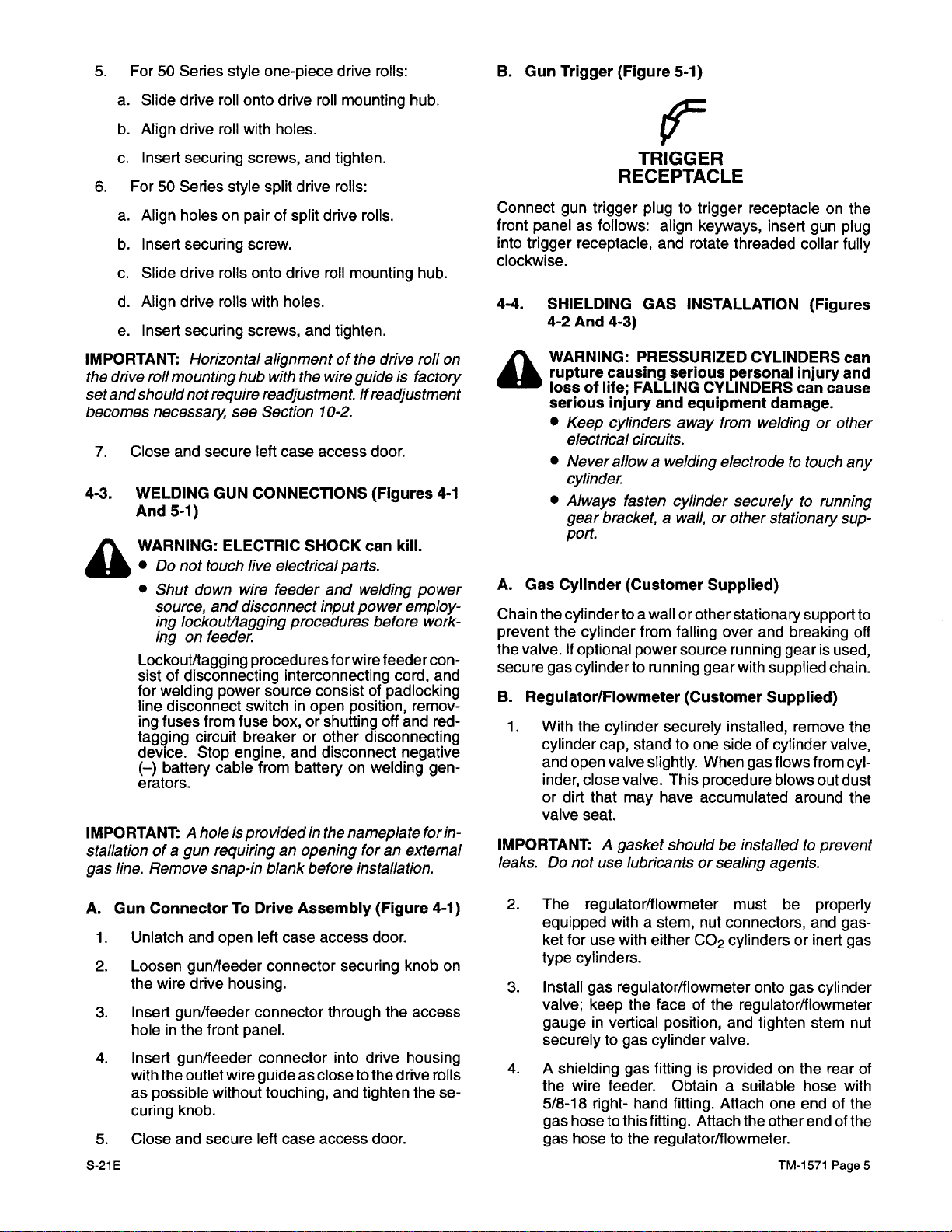
5.
For50Series
a.
Slide
b.
Align
c.
Insert
6.
For50Series
a.
Align holesonpair of split
b.
Insert
c.
Slide
d.
Align
e.
Insert
IMPORTANT:
the drive
set
becomes
7.
4-3.
A
roll
and
should
necessary,
Close
WELDING
And
WARNING:
•
Do
•
Shut
mounting
and
5-1)
source,
ing
ingonfeeder.
Lockout/tagging
sistofdisconnecting
for
welding
line
disconnect switch
ing
fuses
tagging circuit
device.
(—)
battery
erators.
IMPORTANT:
stallationofa
gas
line.
Remove snap-in
style
one-piece
drive
roll
onto
drive
drive
roll
with
holes.
securing
securing
drive
drive
securing
Horizontal
not
not
down
lockout/tagging
Stop
A
gun
screws, and tighten.
style
screw.
rolls
onto
rolls
with
screws, and tighten.
hub
require
secure
GUN
touch
readjustment.Ifreadjustment
see
Section 10-2.
left
CONNECTIONS
ELECTRIC
live
wire
and
disconnect
procedures
power
from
fuse box,
breakerorother
engine, and
cable
from
hole
ispro
requiring an
split
drive
holes.
alignmentofthe drive
with
case
electrical
feeder
procedures
interconnecting
source consistofpadlocking
videdinthe
blank
drive
rolls:
roll
drive
rolls:
drive
roll
the
wire
access
SHOCK
mounting
rolls.
mounting
guideisfactory
hub.
door.
(Figures
can kill.
parts.
and
welding
input
power
employ
before
for
wire feeder
cord,
in open
batteryonwelding
position,
or shutting
disconnecting
disconnect
remov-
off
and red-
negative
nameplate
opening
before
foranexternal
installation.
hub.
roll
on
4-1
power
work
con
and
gen
form-
B.
Connect
front
into
clockwise.
4-4.
A
A.
-
Chain
-
prevent
the
-
secure gas
B.
1.
-
IMPORTANT:
leaks.Donot
Gun
Trigger (Figure 5-1)
‘9=
TRIGGER
RECEPTACLE
gun
trigger plugtotrigger receptacleonthe
panelasfollows:
trigger
receptacle,
SHIELDING
4-2
And
4-3)
WARNING:
rupture
lossoflife;
serious
•
causing serious
injury
Keep
cylinders
electrical circuits.
•
Never
allow
cylinder.
•
Always fasten
gear
bracket,awall,orother
port.
Gas
Cylinder (Customer
the
cylindertoa
the
cylinder
valve.Ifoptional
cylinder
Regulator/Flowmeter
With
the
cylinder
cylinder
and
inder,
or
valve
open
dirt
cap,
valve
close
that
seat.
A
use
align
and
GAS
PRESSURIZED
FALLING
and
a welding
wall or
from
power
to running
stand
slightly.
valve.
may
have
gasket shouldbeinstalledtoprevent
lubricantsorsealing
keyways,
rotate
threaded
INSTALLATION
CYLINDERS can
personal
CYLINDERS
equipment
away
from
electrodetotouch
cylinder
falling
source
(Customer
securely
to one
This procedure
securelytorunning
Supplied)
other
stationary
over
running
gear
with
installed,
sideofcylinder
When
gas
accumulated
insert
gun
plug
collar
fully
(Figures
injury
and
can
cause
damage.
weldingorother
any
stationary
and
breaking
gear is
supplied
Supplied)
remove
flows
blows
support
used,
chain.
valve,
from
out
around
sup-
to
off
the
cyl
dust
the
agents.
-
A.
1.
2.
3.
4.
5.
S-21E
Gun
ConnectorToDrive
Unlatch and
Loosen
the
wire
Insert
holeinthe
Insert
with
the
as
possible
curing
Close and
open
gun/feeder
drive
housing.
gun/feeder connector
front
panel.
gun/feeder
outlet
wire
without touching,
knob.
secure
Assembly
left
case
access
connector securing
through
connector
guideasclosetothe
left
case
access
into
and
tighten
(Figure 4-1)
door.
drive
door.
knob
the
housing
drive
on
access
rolls
these-
2.
The
regulator/flowmeter
equipped withastem,
ket
for
use
type
cylinders.
3.
Install
gas
regulator/flowmeter onto
valve;
securelytogas
4.
A
the
keep
gaugeinvertical
shielding
wire
feeder.
5/8-18
gas
gas
right- hand
hosetothis
hosetothe
must
nut
connectors,
with
either
CO
2
cylindersorinert
the
faceofthe
position,
cylinder
gas fittingisprovidedonthe
Obtainasuitable
fitting.
fitting.
regulator/flowmeter.
and
valve.
Attach
Attach the
be
gas
regulator/flowmeter
tighten
one end of
other
TM-1571
properly
and
cylinder
stem
rear of
hose
end of
Page
gas
gas
nut
with
the
the
-
5

Flow
Adjustment
CO
2
Washer
CO2
Installation
Figure
CO2
cylinder
4-2. Typical
Argon
RegulatorlFlowmeter
Installation
Installation
Gas
cylinder
Valve
ArgonorArgon
Mix
cylinder
SB-109
492
4-5.
The
ing
wire
provides24voltacpower,
used
14-pin
insert
The
the
source
pins
PinA:Upto10
specttosocket
welding
PinB:24
tactor.
contact closure
PinG:24
welding
IMPORTANT:
not
14-PIN
4-4)
14-pin
cord,
feedertoa
withaconstant
receptacle.Tomake
plug,
pinsonplug
power
are
The
usedbythe
Shielding
valve
PLUG CONNECTION
plug
PLG1
providesajunction
welding
and
rotate
PLG
source
provides
designated as
power
volts ac
volts ac
power
and
six
amperesof24
G (circuit
source.
input
feeder
sends
from pin Atopin
circuit common;
source
The
remaining
feeder.
Gas
Fitting,
00,onthe
power
voltage
threaded
100
wire
functionstothe
follows:
common);
powertoenergize
back24volts ac by
chassis.
(Figures
end of
the
interconnect
point
for
connecting
source.
and
contactor
(CV)
connections,
are
definedinrelationtoboth
feeder.
volts
pinsinthe
This
control when
power
source
align
collar
fully
The
welding
wire
feeder.
ac,60Hz,
protected by
the
B.
also connected
receptacle are
Wire
Feed
connection
clockwise.
weld
meansofa
4-3
And
the
with
a
keyway,
power
The
withre-
fuse
in
con
to
-
Ref.
S-0004
Figure
4-6.
A
-
4-4. Front
WELDING
WARNING: ELECTRIC
•
Do
not
•
Shut
source,
ing
lockout/tagging
ViewOf14-Pin
Locations
WIRE
INSTALLATION
touch
live
down
wire
and
disconnect
electrical
feeder and
procedures
Plug
SHOCK
parts.
input
With
Pin
(Figure
can kill.
welding
4-5)
power
poweremploy
before
work
-
-
ingonfeeder.
A
Lockout/tagging
sistofdisconnecting
for
welding
line
disconnect
ing
fuses
tagging
device.
(—)
erators.
CAUTION: LOOSE
cause
•
Spooled wire
when
circuit
Stop
battery cable
Injury.
Keepafirm
tion,
removal,
loosened
procedures
power
source consistofpadlocking
switch
from
fuse
box,
breakerorother
engine, and
from batteryonwelding
holdonthe
and
hasatendencytounravel
from
forwire
interconnecting
in open
or shutting
disconnect
WELDING
wire
threading
the
spool.
feeder
cord,
position,
during
remov-
off and
disconnecting
negative
WIRE can
installa
operations.
rapidly
con
and
red-
gen
-
-
-
14-Pin
Plug
TM-1571
Page
Figure
6
4-3.
Rear
Weld
Cable
Connection
Opening
Panel
View
SA-125
924
IMPORTANT:
any
part of
If
it should become
the
hub
assembly
stallation instructioninSection
necessarytoreplace
see
hub
assembly
10-3.
rein
5-21E
-
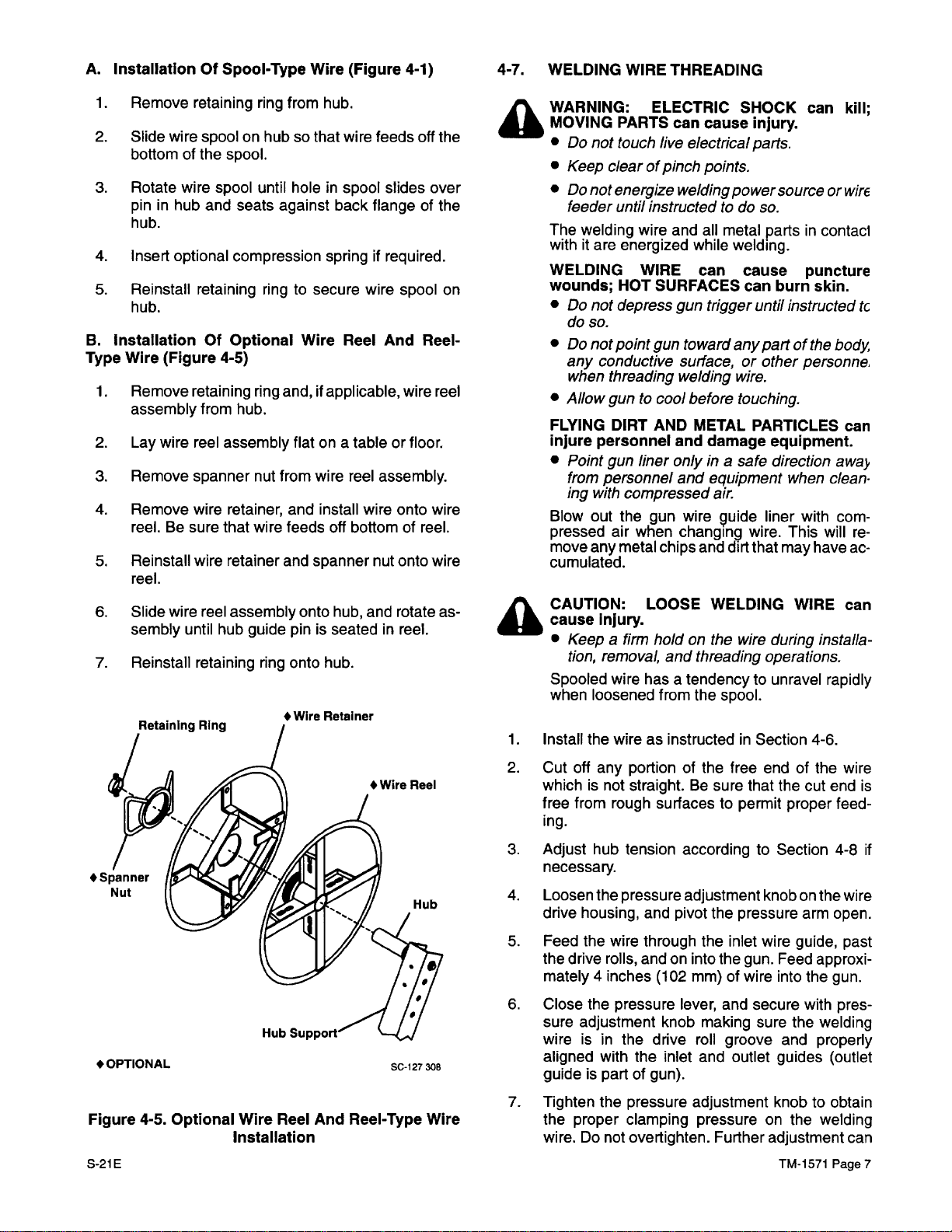
A.
InstallationOfSpool-Type
1.
Remove
2.
Slide
bottomofthe
3.
Rotate
pininhub and
hub.
4.
Insert optional
5.
Reinstall retaining
hub.
B.
InstallationOfOptional
Type
Wire
1.
Remove
assembly
2.
Lay
3.
Remove
4.
Remove wire
reel.Besure
5.
Reinstall
reel.
6.
Slide
sembly
7.
Reinstall retaining
retaining
wire
spoolonhubsothat
spool.
wire
spool
seats
compression springifrequired.
(Figure 4-5)
retaining
from hub.
wire
reel
assembly
spanner
retainer,
that
wire
retainer and
wire
reel
assembly
until
hub
Wire
ring
from
hub.
until
hole
in spool
against back
ringtosecure
Wire
ring
and,ifapplicable,
flat
on a
nut
from
wire
and
install
wire
feeds
spanner
onto
guide
pin is
ring
onto
hub.
•Wlre
Retainer
(Figure 4-1)
wire
feeds
slides
flangeofthe
wire
spool
Reel
And
tableorfloor.
reel
assembly.
wire onto wire
off
bottomofreel.
nut
onto wire
hub,
and
rotateas-
seated in
reel.
off
wire
the
over
on
Reel-
reel
4-7.
A
A
WELDING
WARNING:
MOVING
•
Do
•
Keep
•
Do
feeder
The welding
withitare
WELDING
Wounds;
•
Do
do
•
Do
any
WIRE
ELECTRIC
PARTS
not
touch
clearofpinch
not
energize welding
until
instructedtodo
wire
energized
WIRE can
HOT
not
depress
so.
not
point
gun towardany
conductive
when threading
•
Allow
guntocool before
FLYING
injure personnel
•
Blow
pressed
move
cumulated.
CAUTION:
cause
•
Spooled wire
when
1.Install
DIRT
Point
gun
from
personnel
ing with
compressed
out the
air
when
any
metal
Injury.
Keepafirm
tion,
removal,
loosened
the
wireasinstructedinSection 4-6.
AND
liner onlyina
gun
LOOSE
hasatendencytounravel
THREADING
SHOCK
can
live
electrical
cause
injury.
parts.
points.
power
sourceorwirE
so.
and
all
metal
partsincontaci
while
welding.
cause puncture
SURFACES
gun
can
trigger
burn skin.
untll
part of
surface,orother
welding
wire.
touching.
METAL PARTICLES can
and
damage equipment.
safe direction
and
equipment when
air.
wire
9uide
liner
changing
chips
and
holdonthe wire
and
threading
from
the
wire.
dirt
that
WELDING
during
operations.
spool.
may
can
kill;
instructed
the
body
personne.
awaj~
clean~
with
com
This
willre-
haveac-
WIRE
can
installa
rapidly
tc
-
-
•
Spanner
Nut
•
OPTIONAL
Figure
S-21E
4-5.
Optional Wire
Reel
Installation
And
Reel-Type
SC-127
306
Wire
2.
Cut
off
any
portionofthe
whichisnot straight.Besure
free
from
rough
surfacestopermit
ing.
3.
Adjust
necessary.
4.
Loosen
drive
5.
Feed
the
mately4inches
6.
Close
sure
wireisin
aligned with
guideispart of
7.
Tighten
the
wire.Donot
hub
tension according to Section
the
pressure
housing,
the
drive
the
adjustment knob
proper
and
wire
through
rolls,
andoninto
(102
pressure
the
drive
the
gun).
the
pressure
clamping
overtighten. Further
free
endofthe
that
the
cut
proper
adjustment knobonthe
pivot
the
pressure
the
inlet
the
gun.
mm)ofwire
lever,
and
secure
making
roll
groove
inlet
and
outlet
adjustment knobtoobtain
pressureonthe
arm open.
wire
guide, past
Feed
into
the
with
sure
the
and
guides
adjustment
TM-1571
wire
end
is
feed
4-8
wire
approxi
gun.
pres
welding
properly
(outlet
welding
can
Page
-
if
-
-
7
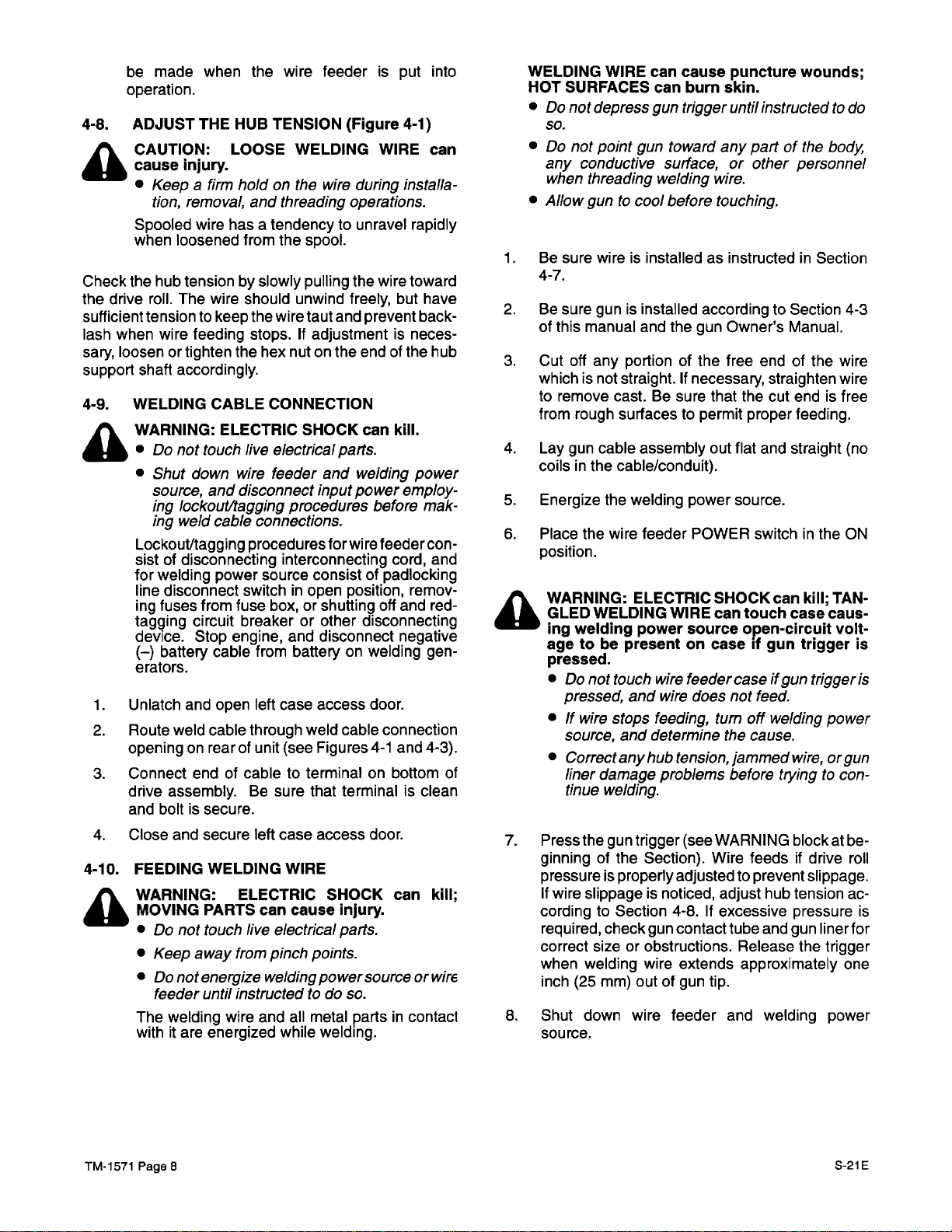
be
operation.
4-8.
A
Check
the
sufficient
lash
sary,
support
4-9.
A
4-10.
A
ADJUST
CAUTION: LOOSE
:ause
Spooled
when
the
drive
when
loosen or
shaft
WELDING
WARNING: ELECTRIC
•
•
Lockout/tagging
sistofdisconnecting
for
line
ing
tagging
device.
(—)
erators.
1.
Unlatch and
2.
Route
openingonrearofunit
3.
Connect
drive
and
4.
Close and
FEEDING WELDING
WARNING: ELECTRIC
MOVING
•
•
•
The
withitare
made
Keepafirm
tion,
hub
roll.
tensiontokeep the
Do
Shut
source,
ing
ing
Do
Keep
Do
feeder
when
THE
Injury.
removal,
wire
loosened from
tensionbyslowly
The
wire
feeding
tighten
accordingly.
not
touch
down
lockout/tagging
weld
welding
disconnect switchinopen
fuses
from
circuit
Stop
battery
weld
end of
assembly.Besure
boltissecure.
secure
PARTS
not
touch
away
not
energize
until
welding
the
wire
HUB
TENSION
WELDING
holdonthe wire
and
threading
hasatendencytounravel
the
wire
should
the
CABLE
live
wire
and
disconnect
cable
power
fuse box,orshutting
breakerorother
engine,
cable
open
cable
cabletoterminalonbottom
live
from
instructedtodo
wire
energized
unwind
wire
stops.Ifadjustmentisneces
hex
nutonthe
CONNECTION
SHOCK
electrical
feeder and
procedures
connections.
procedures
interconnecting
source
and
from
batteryonwelding
left
case
through weld
(see
left
case
WIRE
can
cause
electrical
pinch
welding
and
all
while
feederisput
(Figure 4-1)
WIRE can
during
operations.
spool.
pulling
the
wire
freely,
taut and
consistofpadlocking
that
points.
metal
prevent
end of
can
parts.
welding
input
power
before
forwire
disconnect negative
access
Figures
access
SHOCK
powersourceorwirE
welding.
feedercon
position,
off
disconnecting
door.
cable
connection
4-1
terminalisclean
door.
Injury.
parts.
so.
partsincontaci
into
installa
rapidly
toward
but have
back
the
hub
kill.
power
employ
mak
cord,
and
remov
and
red-
gen
and
4-3).
can kill;
of
WELDING
HOT
•
Do
so.
•
Do
any
-
-
-
-
-
-
-
A
-
when threading
•
Allow
1.
Be
4-7.
2.
Be
of
this
3.
Cut
whichisnot straight.Ifnecessary,
to remove cast.Besure
from
4.
Lay
coilsinthe
5.
Energize the
6.
Place
position.
WARNING: ELECTRIC
GLED
ing Welding power
agetobe
pressed.
•
•Ifwire
•
7.
Press
ginningofthe Section).
pressureisproperly
If
wire
cordingtoSection
required,
correct
when
inch
8.
Shut
source.
WIRE
can
cause
SURFACES
not
depress
not
point
conductive
guntocool
sure
wireisinstalledasinstructedinSection
sure
gunisinstalled
manual
off
any
rough
gun
cable
the
WELDING
Do
not
pressed,
source,
Correctanyhub
liner
damage
tinue
welding.
the
gun
slippageisnoticed,
check
sizeorobstructions.
welding
(25
mm)
down
can
gun
gun
toward
surface,orother personnel
welding
before
and
the
portionofthe
surfacestopermit proper
assembly
cable/conduit).
welding
wire
feeder POWER switchinthe
WIRE can
presentoncaseifgun
touch
wire
and
wire does
stops
feeding,
and
determine
tension,
problems
trigger
adjustedtoprevent
4-8.Ifexcessive
gun
contact
wire extends
outofgun tip.
wire
feeder
puncture
burn skin.
trigger until
according
gun
that
out flat
power
source
feeder
(see
Wire feedsifdrive
instructedtodo
any
part of
wire.
touching.
to Section
Owner’s
free
source.
SHOCK
caseifgun
not
tum
the
jammed
before
WARNING blockatbe
adjust
tube
Release
approximately
and
Manual.
end of
straighten
the
cut
and
can kill;
touch
open-circuit
feed.
off
welding
cause.
tryingtocon-
hub
and gun
welding
endisfree
feeding.
straight
case
wire,orgun
tensionacpressure
Wounds;
the
body
4-3
the
wire
wire
(no
ON
TAN
caus-
volt
trigger
slippage.
the
trigger
power
roll
liner
for
trigger
one
power
is
is
is
-
-
-
TM-1571 Page
8
S-21E

SECTION5-OPERATOR
CONTROLS
Access
Gun/Feeder
Gun
Trigger
Receptacle
6-1.
A
GAS
CORED
WARNING: ELECTRIC
MOVING
EXPOSURETOENVIRONMENT
internal parts.
•
•
Warrantyisvoidifthe
with
removed.
ARC
can
•
FUMES
your
•
•Ifventilationisinadequate,
HOT
cause
•
•
•
MAGNETIC
can
•
5-21
E
Hole
For
Connector
Wire
Figure
Do
Keep
Wear
5-1.
Control
METAL
ARC
not
case
any
portionofthe
RAYS
damage hearing.
correct
AND
health.
ARC
(FCAW)
PARTS
touch
live
closed
can
eye,
GASES can
burn
Ventilatetokeep
gases.
breathing
Watch
Keepafire
howtouse
Allow
device.
METAL,
fire
and
for
fire.
work
SPATrER,
burns.
extinguisher
it.
and
handling.
FIELDS
affect
pacemaker operation.
Wearers
going
welding
should
near
arc
operations.
Speed
Control
Panel
View
SECTION
(GMAW)
WELDING
can
cause
electrical
while operating.
wire
outer
eyes
ear,
and body
from
breathing
equipmenttocool
FROM
consult
welding
AND
SHOCK
serious
can
parts.
feederisoperated
enclosure open
and
skin; NOISE
seriously
use
AND
nearby
HIGH
CURRENTS
their
doctor
gouging,orspot
5-1.
The
the
5-2. WIRE SPEED
The
88-124
467
in
ing
feed
6—
SEQUENCEOFOPERATION
FLUX
can kill;
injury;
damage
POWER
POWER switch
wire
feeder.
WIRE
SPEED
inches per
the WIRE
speed.
minute
The
WELDING
Wounds.
•
Do
any
1.
Install
2.
Wear
dry
3.
Connect
SPEED
not
conductive
and
piece.
or
protection.
harm
4.
A
Rotate
(see
WIRE
Section
WARNING:
•
Do
not
•
Do
not
contact
fumes
and
The
welding
withitcarry
approved
SLAG
and
know
can
source
5.
Energize
6.
Place
the
7.
Turnonshielding
8.
Wear
welding
accordingtoANSI Z49.1.
before
before
9.
Hold
from
flows,
is
Section 4-7.
tip
workpiece,
gas
noticed,
SWITCH
(Figure 5-1)
POWER
functions as
CONTROL
the
ON/OFF switch
(Figure 5-1)
WIRE SPEED
ojo
control
scaleiscalibratedininches per
point
connect
insulating gloves
work
touch
touch welding
withitwhile
weld
contactorisenergized.
the
welding
POWER switchintheONposition
of gun
flows,
adjust drive
adjusts
within
the
control
WIRE can
gun
wire
clockwise
toward
surface,orother
unit
according
clamptoclean,
SPEED
controltodesired
5-2).
ELECTRIC
live
SHOCK
electrical
wireorany
welding.
wire
and all
metal
output when
power
gasatthe
helmet with
approximately
and
depress
and
wire
feeds.Ifwire
roll
pressure
the
wire
feed
speed
range.
increases
minute.
cause
any
part of
puncture
the
personnel.
to Section
and
clothing.
bare metalatwork-
position
can kill.
parts.
metal
partsincontact
the
welding
sourceorgenerator.
source,ifapplicable.
proper filter lens
1/2 in.
gun
(13
trigger.
Current
slippage
according
TM-1571
for
speed
Rotat
wire
body
4.
part
in
power
mm)
to
Page
9
-
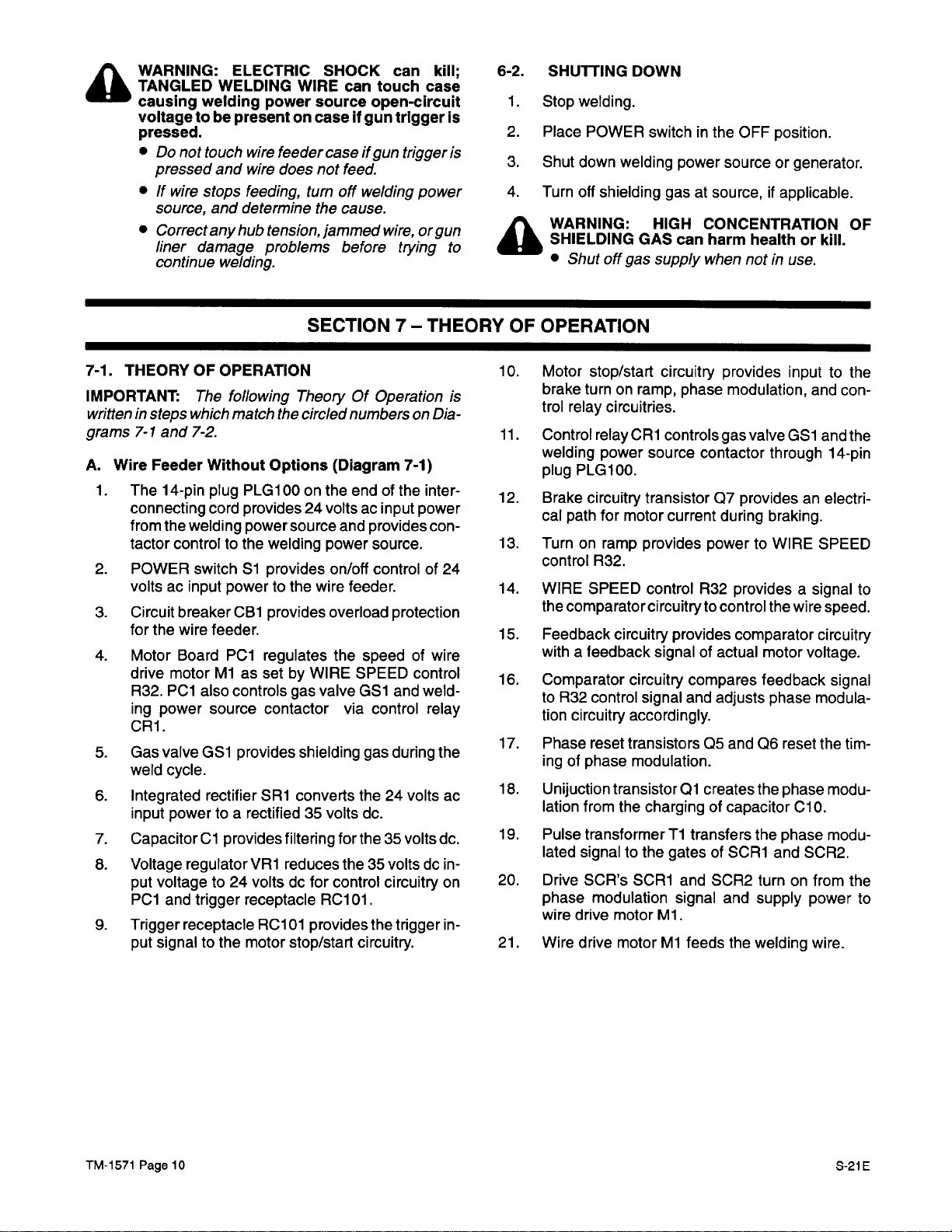
WARNING: ELECTRIC
A
7-1.
IMPORTANT:
writteninsteps
grams
A.
TANGLED
causing
voltagetobe
pressed.
•
Do
pressed
•Ifwire
source,
•
Correctanyhub
liner
continue
THEORYOFOPERATION
7-1
and
Wire
Feeder
The
1.
2.
3.
4.
5.
6.
7.
8.
9.
14-pin
connecting cord
from
the
tactor
POWER switch51provides
volts ac
Circuit
for
the
Motor
drive
R32.
PCi
ing
power
CR1.
Gas
valve
weld
cycle.
Integrated
input
CapacitorClprovides
Voltage regulator
put
voltageto24
PCi
and
Trigger receptacle
put signaltothe
WELDING
welding
presentoncaseifgun
not
touch
and
stops
and
damage
welding.
The
following
which
match
7-2.
Without
plug PLG100onthe
welding
controltothe
input
powertothe
breaker
wire
Board
motorMlas
powertoa
CB1
feeder.
PCi
also
controls
source
051
rectifier
trigger
provides
SHOCK
WIRE can
power
wire
wire does
feeding,
determine
tension,jammed
problems
source
feeder
not
turn
the
caseifgun
feed.
off
welding
cause.
before
SECTION7-THEORYOFOPERATION
TheoryOfOperation
the
circled
Options
provides24volts ac
power
source
welding
provides
regulates
setbyWIRE
gas
contactor
shielding
SRi
converts
rectified35volts
filtering
VR1
reduces the35volts dcin-
volts dc
receptacle
RC101provides
motor
stop/start
numbersonDia-
(Diagram 7-1)
end of
and
power
on/oft
wire
feeder.
overload
the speedofwire
SPEED
valve
051
via
gas
the24volts ac
dc.
for
the35volts
for
control
RC1
01.
circuitry.
can kill;
touch
open-circuit
provides
source.
controlof24
control relay
the
case
trigger
wire,orgun
trying
the
input
protection
and
during
circuitry
triggerin-
trigger
power
inter
power
con-
control
weld-
the
dc.
is
is
to
is
on
6-2.
A
-
SHUTTING
1.
Stop
welding.
2.
Place
3.
Shut
down
4.
Turn
off
WARNING: HIGH
SHIELDING
•
Shut
10.
Motor
brake turnonramp,
trol relay circuitries.
11.
Control
welding
plug
PLG100.
12.
Brake
cal
path
13.
Turnonramp
control
14.
WIRE
the
comparator circuitrytocontrol the
15.
Feedback circuitry
with
a feedback
16.
Comparator circuitry compares feedback
to
R32
tion
circuitry
17.
Phase
ingofphase modulation.
18.
Unijuction
lation
19.
Pulse
lated
signaltothe
20.
Drive
phase
wire
drive
21.
Wire
drive
DOWN
POWER switchinthe
welding
shielding
off
gas
stop/start
relay
power
circuitry
for
motor
R32.
SPEED
control signal
reset
transistorsQ5and
transistorQicreates
from
the
transformerTitransfers
SCR’s
modulation
motor
motorMlfeeds
power
gasatsource,ifapplicable.
GAS
can
supply
circuitry
phase modulation,
CR1
controls
source
transistorQ7providesanelectri
current
provides
control
provides
signalofactual
and
accordingly.
charging of
gatesofSCRi
SCRi
and
signal
Mi.
OFF
sourceorgenerator.
CONCENTRATION
harm healthorkill.
when
provides
gas
contactor
during
powertoWIRE
R32
providesasignal
comparator circuitry
adjusts
capacitor ClO.
SCR2
and
the
position.
notinuse.
inputtothe
and
valve
051
through
braking.
wire
motor
voltage.
phase
Q6 reset the
the phase
the phase
and SCR2.
turnonfrom
supply
welding
power
wire.
OF
con-
and
the
14-pin
SPEED
to
speed.
signal
modula
tim
modu
modu
the
to
-
-
-
-
-
TM-1571
Page
10
S-21E
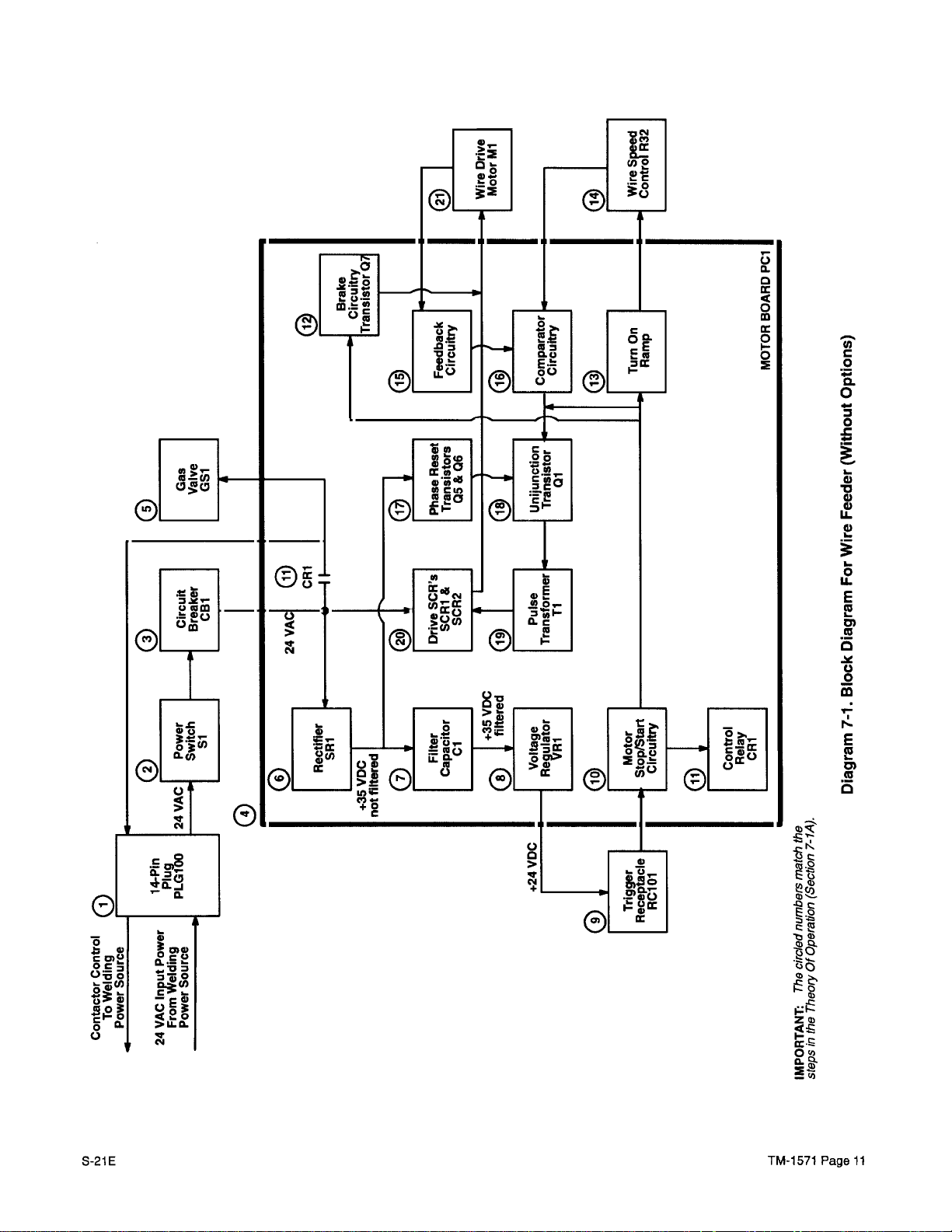
0
4-
0.
0
•1~
0
4-
1~
4)
4)
LI
-
4)
I
-
0
U
-
E
(U
I
-
0)
(U
0
0
1~
E
(U
0)
(U
0
S-21E
-A
c~
.~
~(i)
.~Q)
tb~.
~3O
c~o
I—0
ZQ)
TM-1571
Page
11