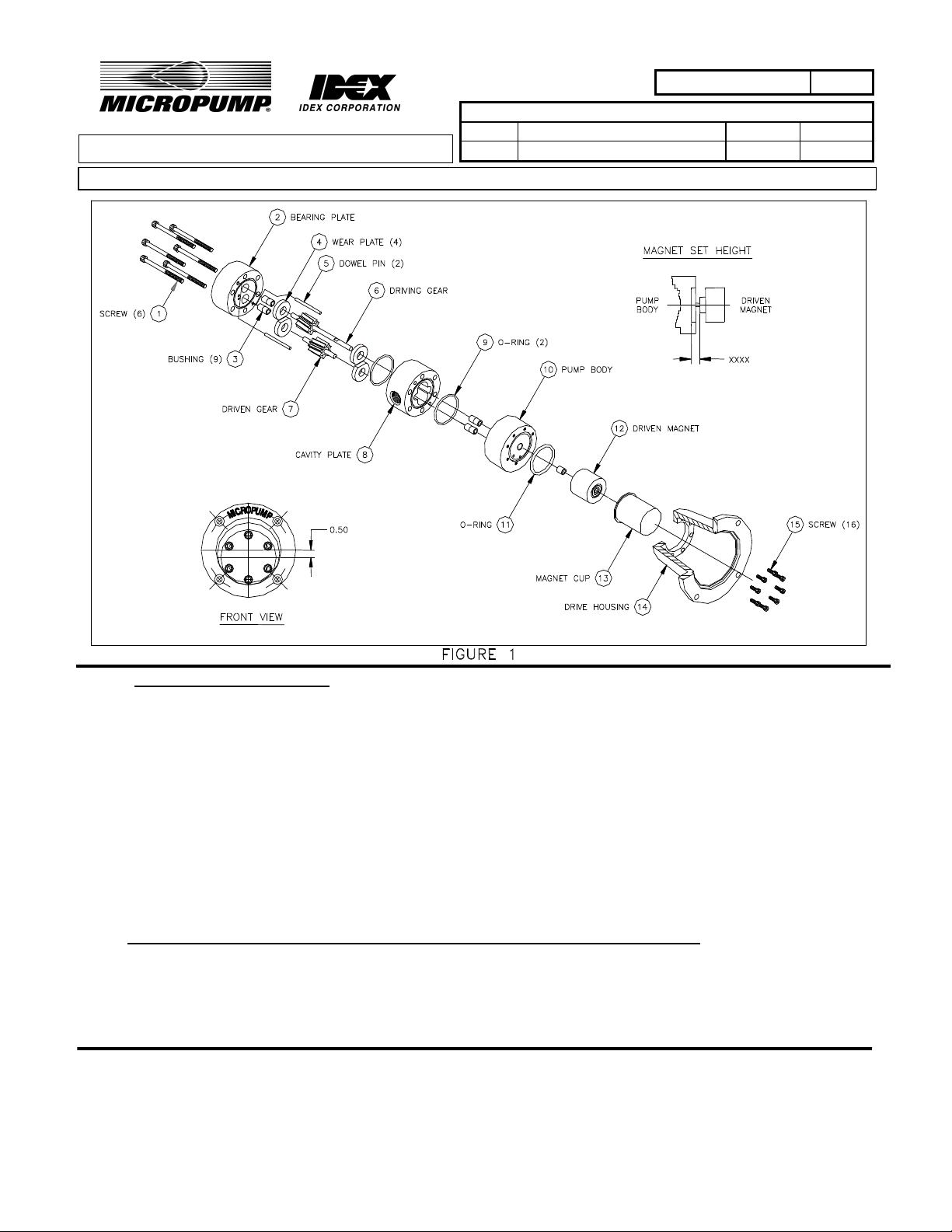
SERVICE INSTRUCTIONS: L23154
MODEL: 5500/56C
PART NUMBER:
REVISION
LTR. DESCRIPTION DATE BY
A ORIGINATED PER E14164 1/28/04 CMA
L23154
1. Description and Operation
1.1 The Model 5500 pump is a positive displacement gear pump constructed of 316 stainless steel, PEEK
or Teflon, and Viton.
Special pumps may be constructed of alternate materials. The pump is magnetically driven and is therefore
leak-proof and contamination free. The pump is self priming under normal conditions.
1.2 Drive power for the pump is provided by the motor via the magnetic coupling. An exploded view is
shown in Figure 1. Fluid is drawn into the pump due to the negative pressure created by the gear
rotation in the cavity plate. The fluid is contained by the gear teeth, cavity walls, and gear mesh to
create fluid transfer and pressure.
2. Tools and materials required for Disassembly, Repair, and Assembly of Pump
2.1 Hex Keys (9/64”, 3/16”, and 5/16”)
2.2 X-Acto knife (or equivalent)
2.3 Masking Tape
MICROPUMP, INC.
A Unit of IDEX Corporation
PO Box 8975, Vancouver, WA 98668-8975 • Phone: 360/253-2008 • Fax: 360/253-8294
Howard Road, Eaton Socon, St.
MICROPUMP
A Subsidiary of Micropump, Inc.
Neots, Cambridgeshire, PE 19 8ET England, • Phone: (44) (0) 1480-356600• Fax: (44) (0) 1480-35630
Page 1 of 9
LIMITED
0
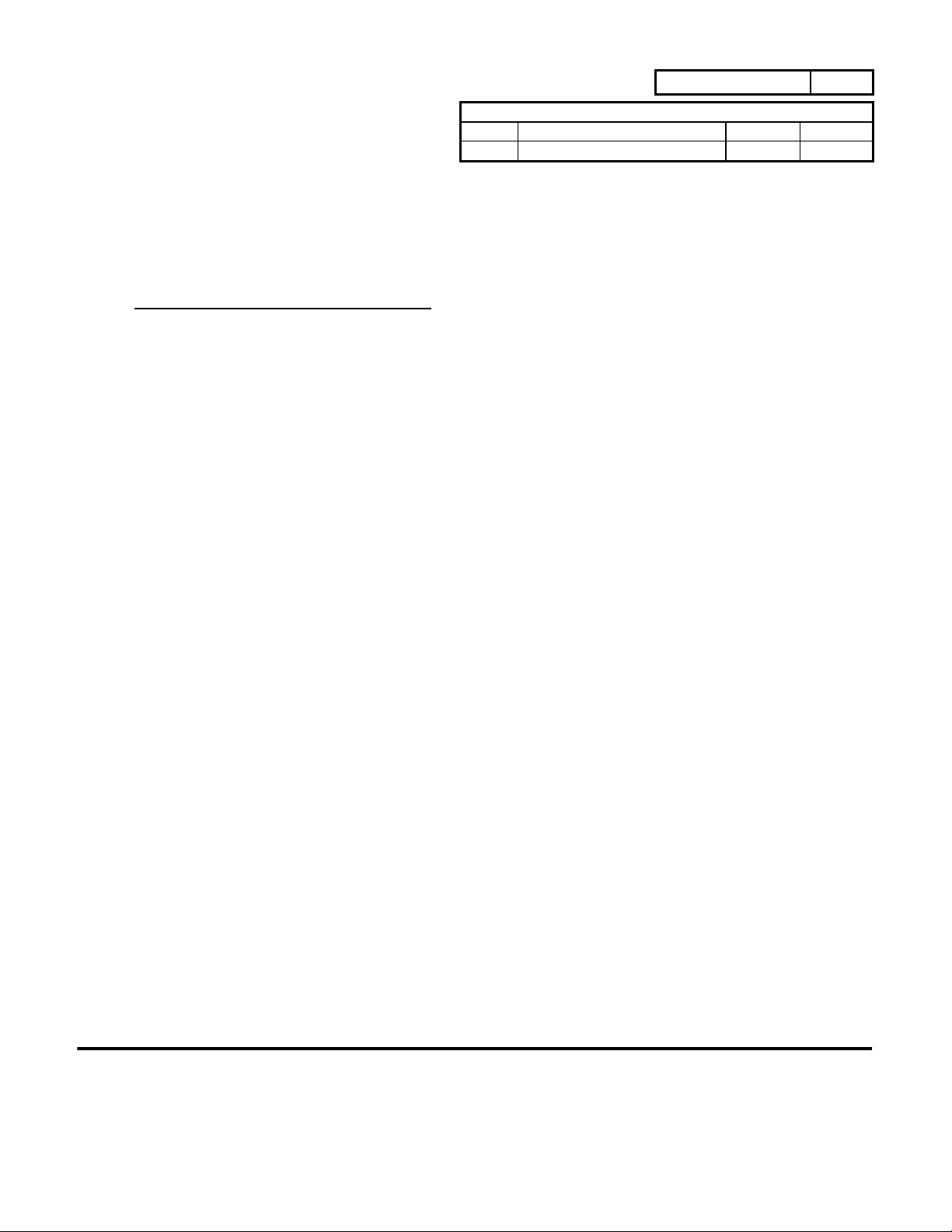
PART NUMBER:
L23154
2.4 Surface plate or equivalent flat
surface
2.5 Bushing insertion tool (or arbor press)
2.6 Reamer for bushings
2.7 Silicone vacuum Grease
2.8 Stoddard Solvent or liquid detergent
3. Disassembly of Pump (Refer to Figure 1)
Note: Prepare a clean, flat area, free of metal particles.
3.1 Place pumphead on surface with housing facing up.
NOTE: EXERCISE CAUTION IN THE FOLLOWING STEP.
ENTRAPPED FLUID WILL BE RELEASED WHEN PUMP BODY
AND MAGNET CUP ARE SEPARATED.
3.2 Remove the screws (15), qty 16 (Qty 8 for low pressure version), and pull the drive housing (14) and
magnet cup (13) from the pump body (10).
3.3 Separate magnet cup (13) and drive housing (14).
LTR. DESCRIPTION DATE BY
A ORIGINATED PER E14164 1/28/04 CMA
REVISION
3.4 Loosen the setscrew on the driven magnet (12) and remove magnet from
driving gear (6) shaft.
Note: Store the driven magnet (12) in a clean bag and keep away
from other magnets and sensitive electronic equipment.
3.5 Remove screws (1), qty 6, and pull bearing plate (2), cavity plate (8), and
two of the dowel pins (5) straight away from pump body (10).
3.6 Separate bearing plate (2), cavity plate (8), and two dowel pins (5) from each other. Gently
lift the wear plates (4) (if used), qty 4, out of the cavity plate (8), taking care to pull them
straight out.
Note: If dowel pins are difficult to remove, protect pins with a soft
material (i.e. plastic or rubber) and remove them with pliers.
Replace pins if damaged.
3.7 Remove driving gear (6) and driven gear (7) from pump body (10).
3.8 See repair instructions, section 6.5.1 regarding bushing (3), qty 9, removal.
MICROPUMP, INC.
A Unit of IDEX Corporation
PO Box 8975, Vancouver, WA 98668-8975 • Phone: 360/253-2008 • Fax: 360/253-8294
Howard Road, Eaton Socon, St.
MICROPUMP
A Subsidiary of Micropump, Inc.
Neots, Cambridgeshire, PE 19 8ET England, • Phone: (44) (0) 1480-356600• Fax: (44) (0) 1480-35630
Page 2 of 9
LIMITED
0

PART NUMBER:
L23154
LTR. DESCRIPTION DATE BY
A ORIGINATED PER E14164 1/28/04 CMA
REVISION
Note: Remove bushings and O-
rings ONLY if replacement is necessary.
4. Inspection of Pump Components
4.1 Magnet Cup (10)
4.1.1 Visually check the outside of the magnet cup (13) for rub marks on the
back and sides. Marks on the back indicate that the hub assembly is
misaligned axially. Marks on the sides indicate radial misalignment.
4.1.2 Visually check the inside surfaces of the magnet cup (13) for rub marks. Marks on
the bottom surface indicate that either the driven magnet (12) or hub assembly is
misaligned. See section 7.12 for driven magnet (12) installation. See section
8.1 for hub assembly installation. Marks on the insides of the magnet cup (13)
indicate radial misalignment of the driven magnet (12), refer to section 6.2.
4.2 Driven Magnet (12)
4.2.1 Visually check the driven magnet (12) for wear on the outside shell; refer to section
6.2.
4.2.2 Visually check the driven magnet (12) for metal particles. See cleaning instructions,
section 5.
4.3 Driving gear (6) and driven gear (7)
4.3.1 Visually check the gear teeth on both gears for pits, wear, or damage.
Replace both gears if either gear is damaged or worn.
4.3.2 Visually check gear shafts for wear, pits, scoring, or corrosion. Light wear marks on
shaft circumference will not normally impede the operation of the pump. Replace
both gears if either gear shafts are scored or damaged.
Note: ALWAYS replace all bushings if either gear shaft is worn or damaged.
4.4 Bearing plate (2) (Section 4.4.1 applies when wear plates not used)
4.4.1 Visually check the bearing plate (2) surface that contacts the gears for scoring. Refer
to section 6.4.
4.4.2 Visually check the bearing plate lube holes for debris. See cleaning instructions,
section 5.
PO Box 8975, Vancouver, WA 98668-8975 • Phone: 360/253-2008 • Fax: 360/253-8294
Howard Road, Eaton Socon, St.
MICROPUMP, INC.
A Unit of IDEX Corporation
MICROPUMP
A Subsidiary of Micropump, Inc.
Neots, Cambridgeshire, PE 19 8ET England, • Phone: (44) (0) 1480-356600• Fax: (44) (0) 1480-35630
Page 3 of 9
LIMITED
0