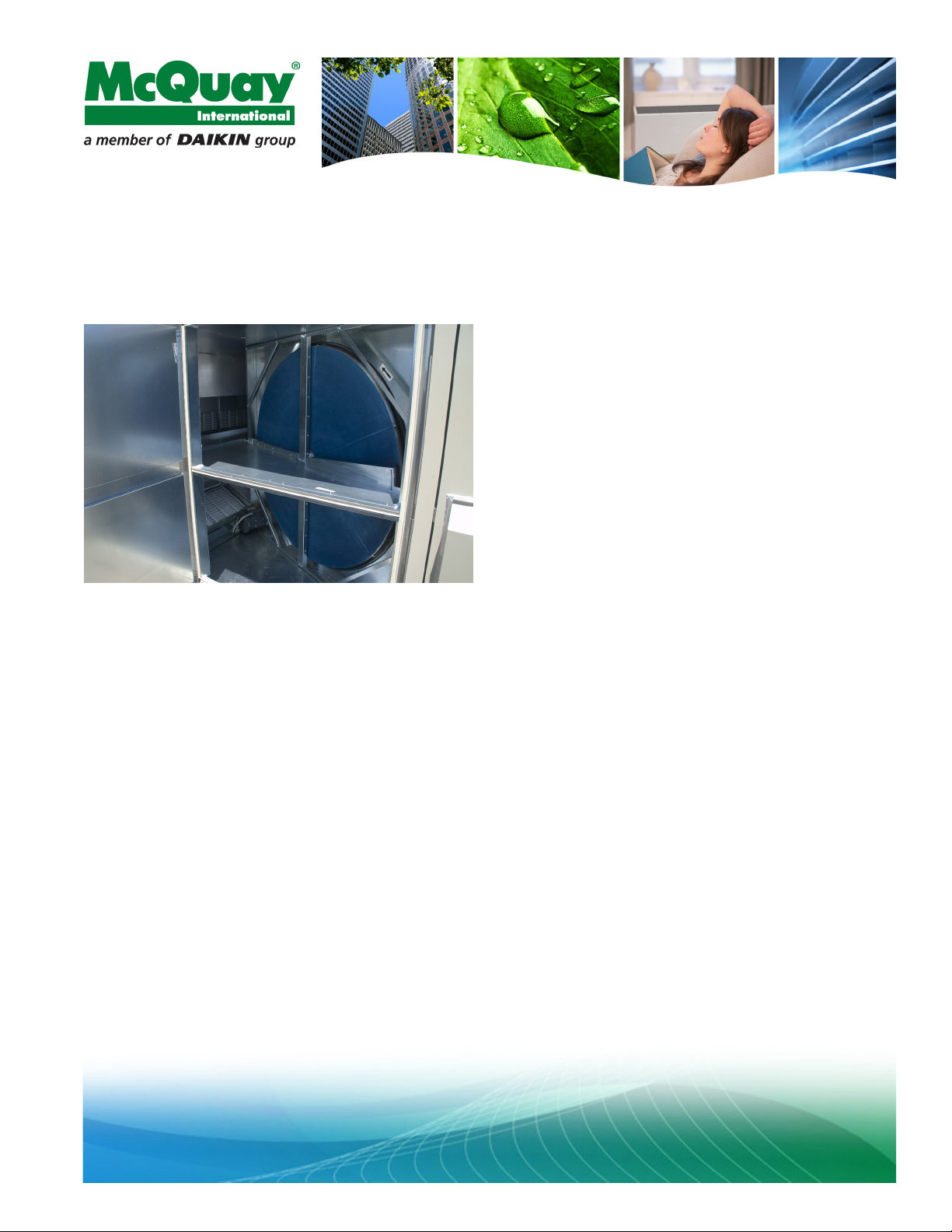
RoofPak™ Energy Recovery Solutions from
McQuay
Controlling Energy Costs and ASHRAE
Standard 62.1 Compliance
The energy cost to condition ventilation air is a major part
of total building energy costs. Ventilation air can account for
30% of the total cooling load and 50% of the total heating
load for a school building. Because proper ventilation is a
necessity – not an option – a method of conserving energy,
while simultaneously meeting the current requirements of
ASHRAE Standard 62.1 is essential.
The solution is a factory-installed and tested energy recovery system available only in McQuay RoofPak™ applied
rooftop systems and rooftop air handlers.
McQuay Energy Recovery Systems
Our energy recovery device transfers both heat and moisture energy between the exhaust and ventilation air. In doing
so, it conditions the incoming ventilation air. This total
energy device offers a cost-effective and efficient method
for containing energy costs while meeting the ventilation
requirements of ASHRAE Standard 62.1.
Factory-Installed and Tested Package
McQuay energy recovery systems (with an ARI certified
wheel, exhaust fan, optional bypass dampers and controls)
are provided as a one-piece, factory-installed and tested
package. This eliminates field coordination and leakage
problems associated with field installation.
The outdoor and exhaust air flows are arranged in counterflow for better efficiency, and to reduce field cleaning
requirements. Exhaust contaminants cannot enter the ventilation air because the exhaust air static pressure is always
less than the ventilation air static pressure. Frost protection
and purge options are also available.
Factory-installed and tested controls provide proper operation for:
Integrated cooling, heating and recovery control –
Mechanical heating and cooling are supplied as necessary to
supplement the wheel and maintain space conditions.
Free cooling – Units with economizers include bypass
dampers that are opened when “free cooling” is available.
The wheel is simultaneously turned off.
Proper exhaust – Exhaust fan speed is controlled using a
factory-installed Variable Frequency Drive (VFD) and space
building pressure sensor for proper exhaust.
Features
• Recovers both heat and moisture energy
• Factory-installed and tested prior to shipment
• Available in 100% outdoor air (OA) or economizer con-
figurations, both with exhaust fans
• ARI-certified and UL-recognized wheel
Engineered for flexibility and performance
™

Benefits
• Recovers approximately 75% of the energy from
exhaust air stream
• Allows mechanical refrigeration, heating, and humidify-
ing capacities to be reduced, offsetting the initial cost of
the energy recovery wheel
• Cuts winter humidification energy costs by up to 60%
• Provides 100% more summer energy recovery than
sensible-only energy recovery devices
• Helps provide a comfortable and affordable indoor envi-
ronment
• Satisfies ASHRAE Standard 90.1 requirements for ener-
gy recovery on applications involving more than 70%
minimum outdoor air and 5000 total cfm.
Advantages of Enthalpy Wheel Design
Not only is our energy recovery wheel ARI-certified and
UL-recognized, its unique composition also provides significant advantages. Composed of synthetic fiber, our wheel
allows moisture-absorbing desiccant to be uniformly and
permanently dispersed throughout the wheel, maximizing
its life expectancy.
The desiccant forms a 4-Angstrom molecular sieve that
attracts water and minimizes contamination. Unlike other
energy recovery wheels that can separate or be spread apart
by air flow and risk contamination of ventilation air from
the exhaust air, the honeycombed design and small aperture
sizes of our wheel provides even air flow and minimizes
internal wheel bypass.
Efficient Winter Humidification
significantly raising the humidity level of outdoor air in the
winter. Not only can this have a dramatic impact on the first
cost and operating cost of an HVAC system, it can also dramatically improve indoor air quality and level of comfort
for building occupants.
Winter Performance: Beating “Jack
Frost”
Frost build up can occur whenever the exhaust air stream
is near 100% relative humidity (RH) and the wheel surface
temperature is below 32°F. Optional factory-installed and
tested controls help prevent frost by measuring the exhaust
air temperature and humidity, slowing down the rotation of
the wheel as required.
Summer Performance: It’s Not Just the
Heat, It’s the Humidity
Enthalpy wheels provide twice as much summer energy
recovery as sensible devices because summer ventilation
air involves as much latent load as sensible load. In fact,
our wheel normally cools outdoor air down to 67°F wet
bulb as normally required by dedicated outdoor air systems
(DOAS). Therefore, terminal unit systems like fan coils and
heat pumps can be used in combination with our energy
recovery rooftop units to provide excellent dehumidification
on the most demanding applications.
First Cost and Operating Cost
Reductions
The charts below illustrate typical energy cost savings from
the McQuay RoofPak Energy Recovery System.
Low space humidity is a common problem in the winter
and can cause both discomfort and health problems for tenants. It also leads to increased static electricity, which can
be damaging to computer equipment. However, mechanical
humidification requires 1,100 Btu per pound of humidity.
Our energy recovery system provides the added benefit of
Typical Annual Energy Savings per 10,000 CFM of Ventilation Air with McQuay Energy Recovery Wheel
Minneapolis Phoenix Miami Dallas N.Y.C. Atlanta Chicago
With Winter
Humidication
Without Winter
Humidication
Typical Payback (In Years) with McQuay Energy Recovery Wheel
With Winter
Humidication
Without Winter
Humidication
$6,609.00 $4,605.00 $8,048.00 $5,545.00 $5,374.00 $4,738.00 $6,010.00
$5,359.00 $4,579.00 $8,048.00 $5,381.00 $4,625.00 $4,363.00 $5,041.00
Minneapolis Phoenix Miami Dallas N.Y.C. Atlanta Chicago
1.2-2.6 2.6-7.4 0.7-2.7 1.8-5.2 2.0-6.1 2.6-7.1 1.5-4.1
1.9-4.9 2.6-7.4 0.7-2.7 1.9-5.4 2.6-7.1 2.9-7.3 2.1-6.0
First cost savings result because the system is factoryinstalled and tested, eliminating the need for field design,
installation and coordination. Because less mechanical
cooling is needed, the cooling system can be downsized for
additional first cost savings. This also can reduce the unit’s
electrical requirement, further reducing installed costs.
© 2010 McQuay International • (800) 432-1342 • www.mcquay.com A/SP 31-161 (06/10)