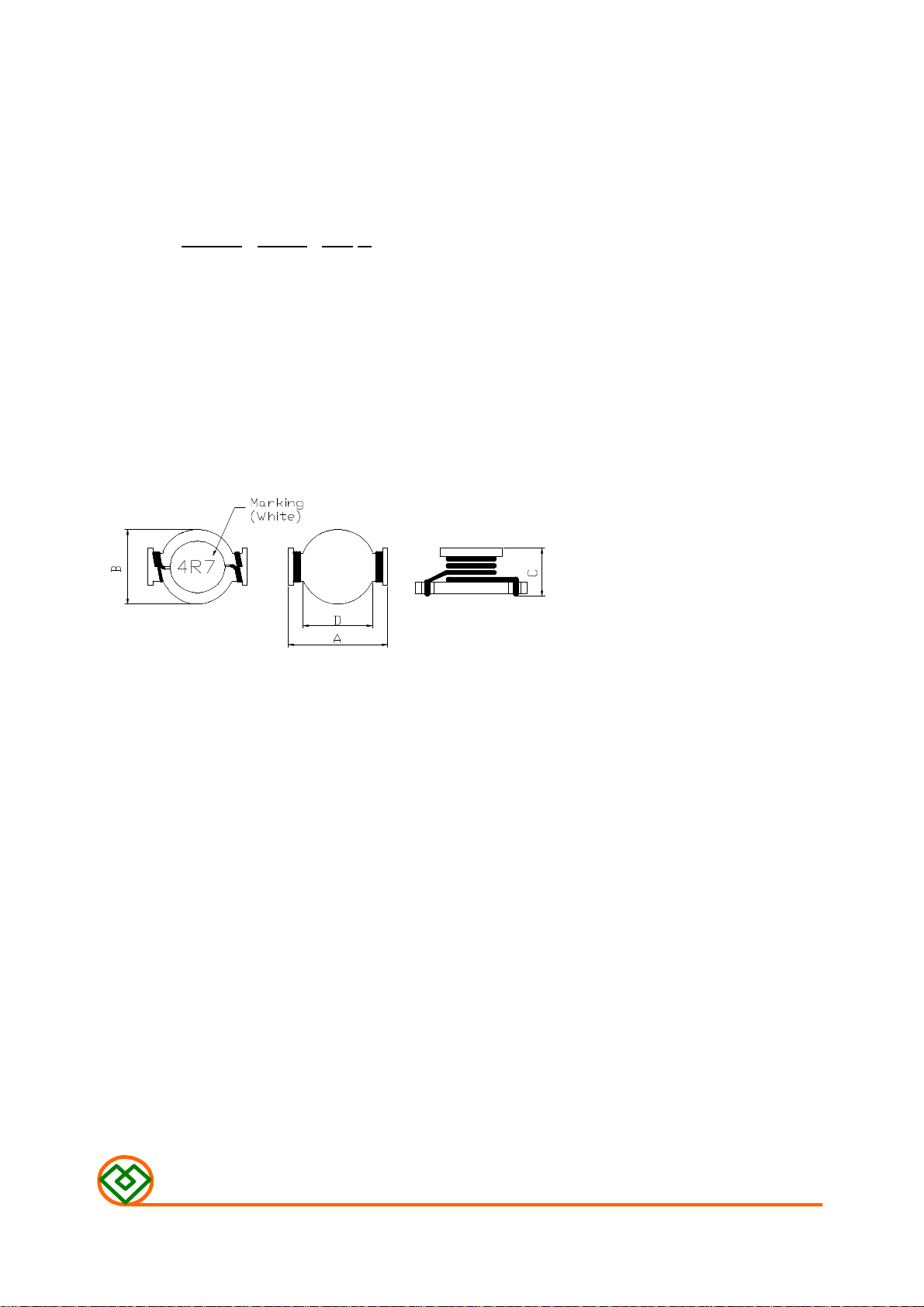
:
(1) SHAPES AND DIMENSIONS
(2) ELECTRICAL SPECIFICATIONS
This specification applies to the Pb Free high current type SMD inductors for
MSCDB-2206H-SERIES
PRODUCT INDENTIFICATION
MSCDB - 2206H - 4R7 M
① ② ③ ④
① Product Code
② Dimensions Code
③ Inductance Code
④ Tolerance Code
A: 22.3Max. mm
B: 16.2Max. mm
C: 7.40Max. mm
D: 14.5Typ. mm
SEE TABLE 1
TEST INSTRUMENTS
L : HP 4284A PRECISION LCR METER (or equivalent)
RDC : CHROMA MODEL 16502 MILLIOHMMETER (or equivalent)
(3)-1 Ambient temperature ……......... +60℃ Max.
(3)-2 Operate temperature range ...... -40℃~+125℃
(Including self temp. rise)
(3)-3 Storage temperature range ...... -40℃~+125℃
MAG.LAYERS
MSCDB-2206H-SERIES Page 1/8
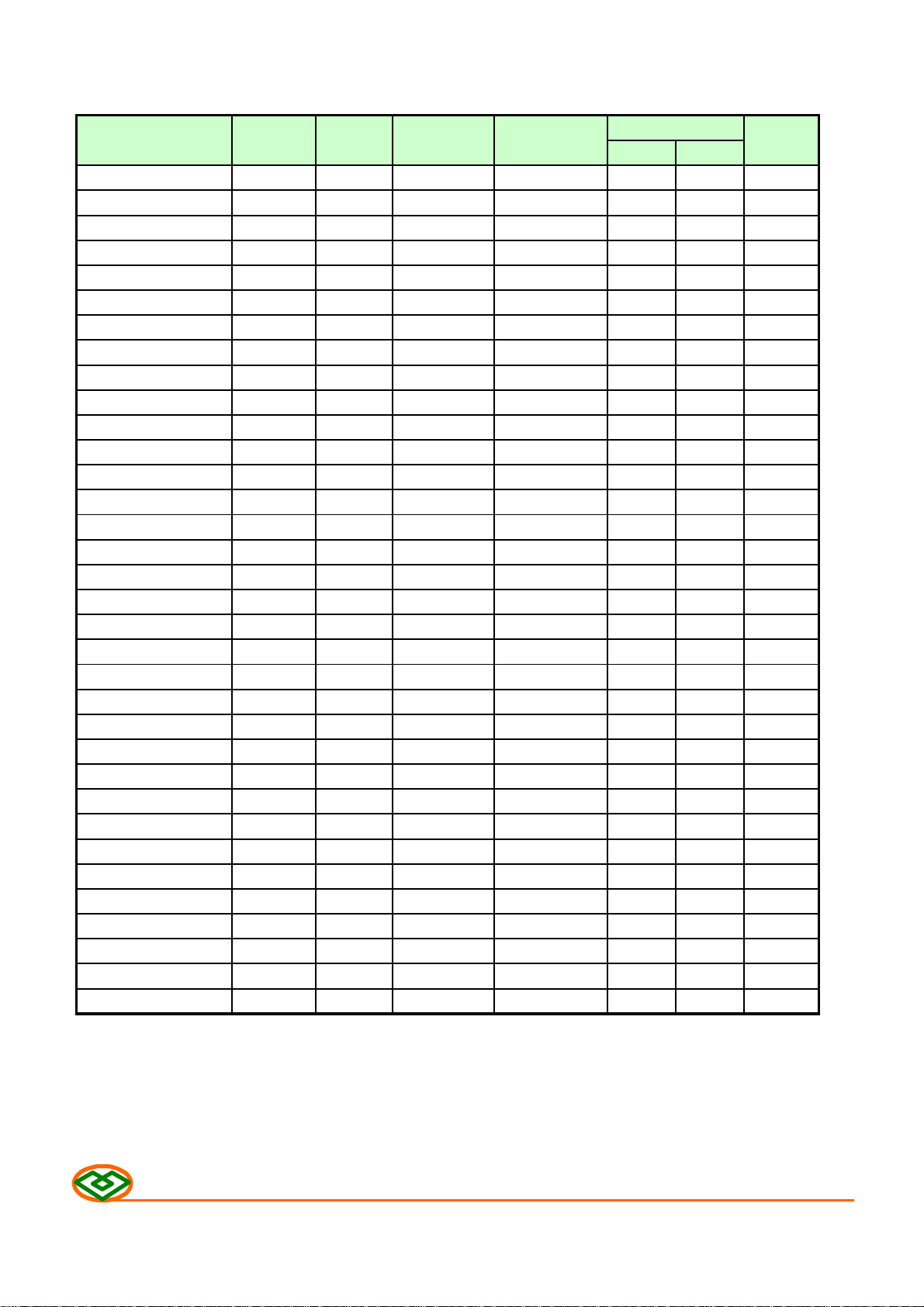
MAGLAYERS
PT/NO.
MSCDB-2206H-R80□
MSCDB-2206H-1R2□
MSCDB-2206H-1R8□
MSCDB-2206H-2R7□
MSCDB-2206H-3R3□
MSCDB-2206H-4R7□
MSCDB-2206H-5R6□
MSCDB-2206H-6R8□
MSCDB-2206H-8R2□
MSCDB-2206H-100□
MSCDB-2206H-120□
MSCDB-2206H-150□
MSCDB-2206H-180□
MSCDB-2206H-220□
MSCDB-2206H-270□
MSCDB-2206H-330□
MSCDB-2206H-390□
MSCDB-2206H-470□
MSCDB-2206H-560□
MSCDB-2206H-680□
MSCDB-2206H-820□
MSCDB-2206H-101□
MSCDB-2206H-121□
MSCDB-2206H-151□
MSCDB-2206H-181□
MSCDB-2206H-221□
MSCDB-2206H-271□
MSCDB-2206H-331□
MSCDB-2206H-391□
MSCDB-2206H-471□
MSCDB-2206H-561□
MSCDB-2206H-681□
MSCDB-2206H-821□
MSCDB-2206H-102□
Inductance Percent Test Resistance Rated DC Current
L(μH) Tolerance Frequency RDC(Ω)Max. IDC1(A) IDC2(A)
0.8 M,N 100kHz/0.25V 2.76m 35.0 16.0 R80
1.2 M,N 100kHz/0.25V 4.20m 30.0 15.0 1R2
1.8 M,N 100kHz/0.25V 5.40m 25.0 13.0 1R8
2.7 M,N 100kHz/0.25V 8.40m 20.0 10.0 2R7
3.3 M,N 100kHz/0.25V 9.36m 17.0 9.0 3R3
4.7 M,N 100kHz/0.25V 10.6m 15.0 8.5 4R7
5.6 M,N 100kHz/0.25V 14.9m 14.0 7.8 5R6
6.8 M,N 100kHz/0.25V 17.0m 12.0 7.5 6R8
8.2 M,N 100kHz/0.25V 18.6m 11.0 7.0 8R2
10 M,N 100kHz/0.25V 20.6m 10.0 6.5 100
12 L,M 100kHz/0.25V 28.3m 9.5 5.5 120
15 L,M 100kHz/0.25V 33.6m 9.0 5.0 150
18 L,M 100kHz/0.25V 39.6m 8.0 4.6 180
22 L,M 100kHz/0.25V 47.3m 6.5 4.0 220
27 L,M 100kHz/0.25V 52.2m 6.0 3.8 270
33 L,M 100kHz/0.25V 70.1m 5.5 3.4 330
39 K,M 100kHz/0.25V 78.0m 5.2 3.2 390
47 K,M 100kHz/0.25V 0.109 5.0 2.8 470
56 K,M 100kHz/0.25V 0.116 4.5 2.6 560
68 K,M 100kHz/0.25V 0.134 4.0 2.4 680
82 K,M 100kHz/0.25V 0.173 3.5 2.2 820
100 K,M 100kHz/0.25V 0.202 3.0 2.0 101
120 K,M 100kHz/0.25V 0.230 3.0 1.6 121
150 K,M 100kHz/0.25V 0.250 2.6 1.5 151
180 K,M 100kHz/0.25V 0.300 2.5 1.3 181
220 K,M 100kHz/0.25V 0.380 2.4 1.2 221
270 K,M 100kHz/0.25V 0.470 2.2 1.1 271
330 K,M 100kHz/0.25V 0.560 1.9 1.0 331
390 K,M 100kHz/0.25V 0.680 1.7 0.9 391
470 K,M 100kHz/0.25V 0.850 1.4 0.82 471
560 K,M 100kHz/0.25V 1.00 1.3 0.78 561
680 K,M 100kHz/0.25V 1.10 1.2 0.72 681
820 K,M 100kHz/0.25V 1.40 1.1 0.64 821
1000 K,M 100kHz/0.25V 1.80 1.0 0.56 102
Marking
※ □ specify the inductance tolerance,K(±10%),L(±15%),M(±20%),N(±30%)
※ IDC1: Based on inductance change (△L/Lo: ≦ drop 10% Typ.)@ ambient temp. 25℃
IDC2: Based on temperature rise (△T: 40℃ Typ.)
Rated DC Current: The less value which is IDC1 or IDC2.
MAG.LAYERS
MSCDB-2206H-SERIES Page-2/8
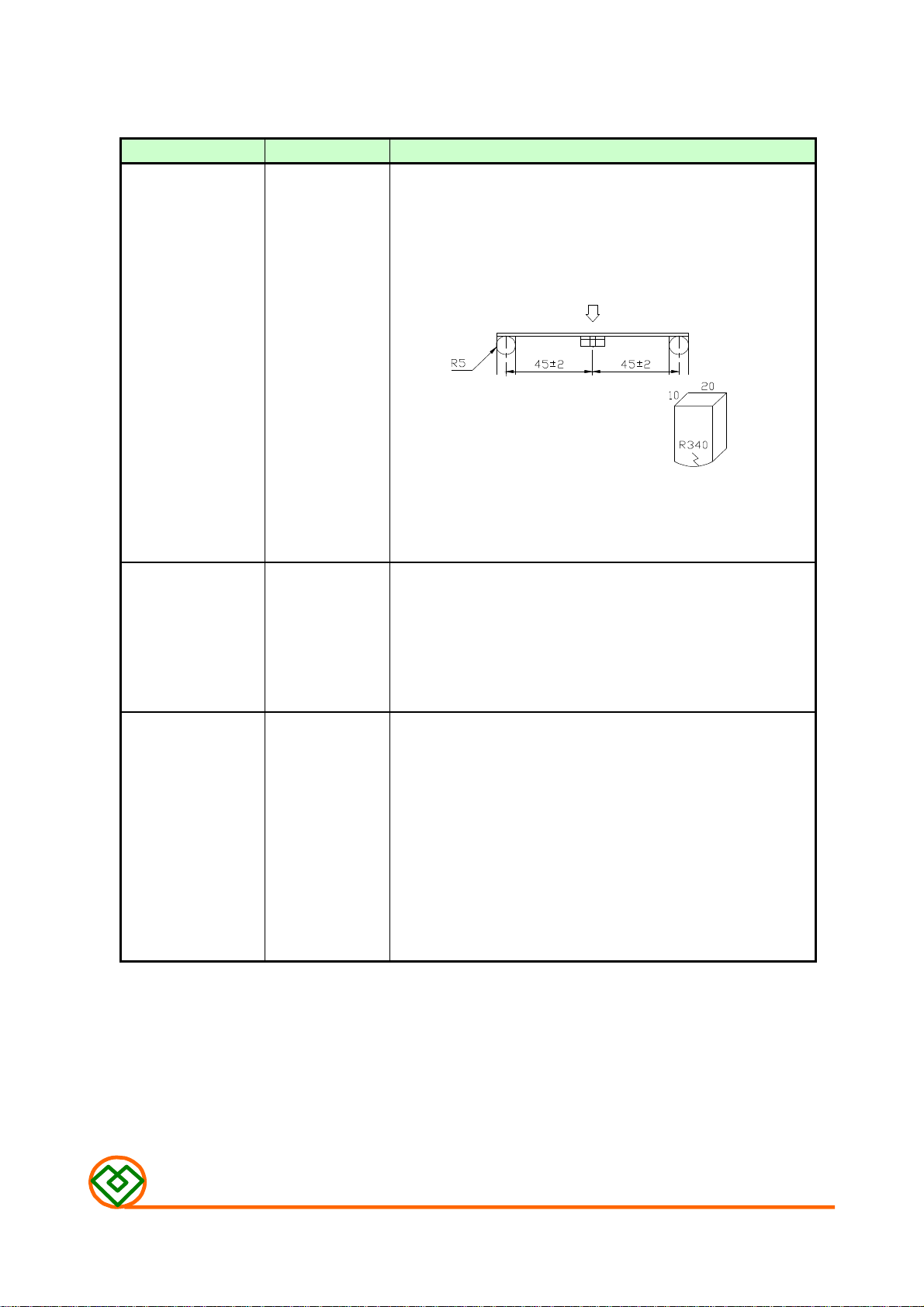
(4) RELIABILITY TEST METHOD
MECHANICAL
TEST ITEM SPECIFICATION TEST DETAILS
Substrate bending
△L/Lo≦±5%
There shall be direction is made approximately 3mm.(keep time 30 seconds)
no mechanical PCB dimension shall the page 7/9
damage or elec- F(Pressurization)
trical damege.
The sample shall be soldered onto the printed circuit board
in figure 1 and a load applied unitil the figure in the arrow
PRESSURE ROD
figure-1
Vibration
Solderability
△L/Lo≦ ±5%
There shall be and a frequency of from 10 to 55Hz/1 minute repeated should
no mechanical be applied to the 3 directions (X,Y,Z) for 2 hours each.
damage. (A total of 6 hours)
New solder Flux (rosin, isopropyl alcohol{JIS-K-1522}) shall be coated
More than 90% over the whole of the sample before hard, the sample shall
The sample shall be soldered onto the printed circuit board
and when a vibration having an amplitude of 1.52mm
then be preheated for about 2 minutes in a temperature of
130~150℃ and after it has been immersed to a depth 0.5mm
below for 3±0.2 seconds fully in molten solder M705 with
a temperature of 245±5℃.
More than 90% of the electrode sections shall be couered
with new solder smoothly when the sample is taken out of
the solder bath.
MAG.LAYERS
MSCDB-2206H-SERIES
Page-3/8