
LCB-I-O Rev B
MULTI-TEMPERATURE
LOOP CONTROL BOARD
INSTRUCTIONS
Models: KB 81 - 286, KBXL 400 -
801, WB 51 - 211, and
WH 55 - 399
WARNING
IMG00116
This manual must only be used
by a qualifi ed heating installer /
service technician. Read all
instructions, including this manual,
the Installation and Operation
Manual, and the Service Manual,
before installing. Perform steps in
the order given. Failure to comply
could result in severe personal
injury, death, or substantial property
damage.
Save this manual for future reference.
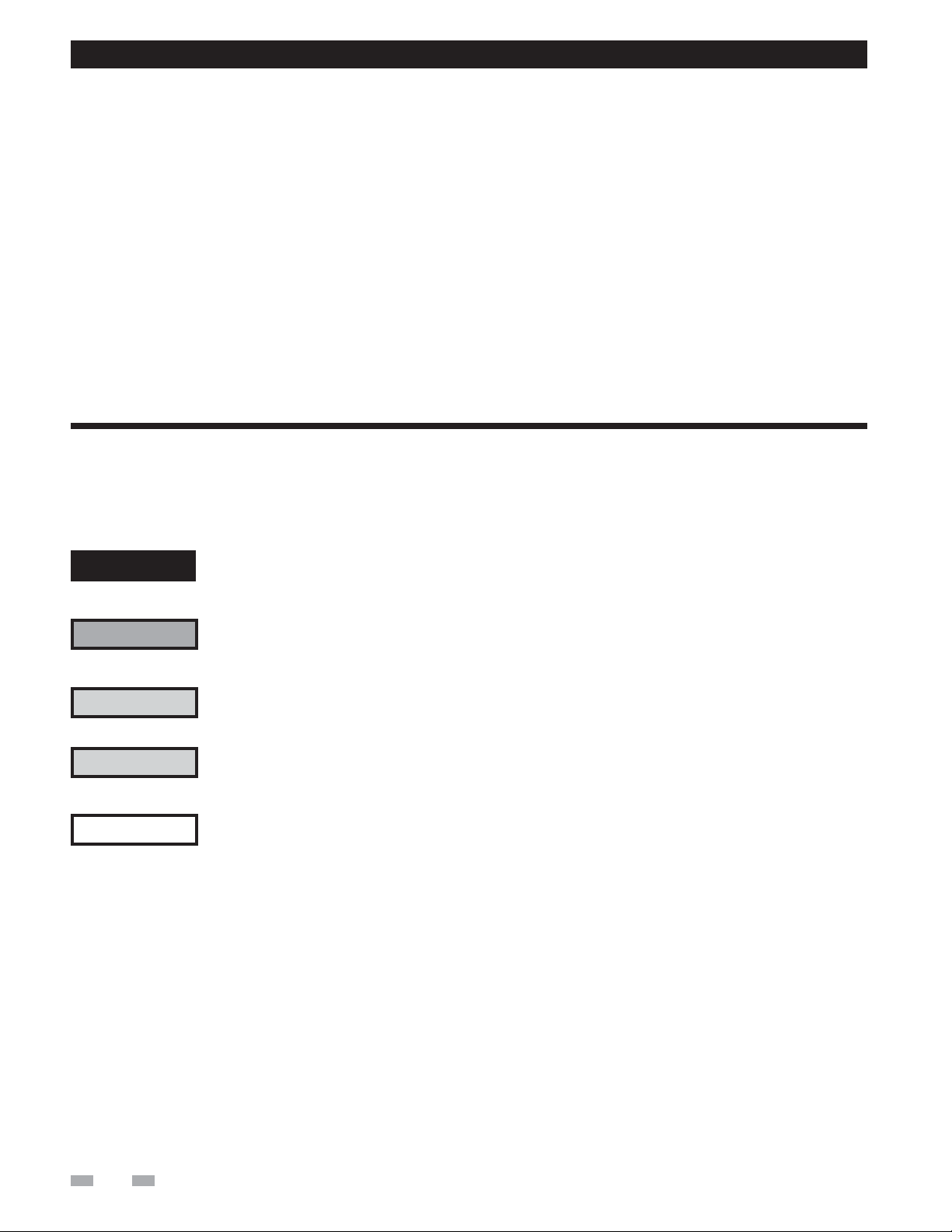
Contents
1. INTRODUCTION ......................................................... 3
2. COMPONENTS AND HYDRONIC PIPING ................. 4-6
3. WIRING REQUIREMENTS
Line Voltage Connections ............................................ 7
Loop Sensors .............................................................. 7
Mixing Valves .............................................................. 7
Wiring of the Cascade ................................................. 7
4. BOILER PARAMETERS SETUP
Cascade Communication Setup ................................... 10
To Access Cascade Address ....................................... 10
3-Way Valve Setup ....................................................... 10
24-Hour Pump In-Activity Operation ............................. 11
To Set Time for SYS Pump Delay ................................ 11
5. BASIC OPERATION ..................................................... 12
Protections .................................................................. 12
Initial ...................................................................... 12
Error Mode ............................................................ 12
Forced Change ..................................................... 13
Revision Notes ................................................... Back Cover
Hazard defi nitions
The following defi ned terms are used throughout this manual to bring attention to the presence of hazards of various risk levels
or to important information concerning the life of the product.
DANGER
WARNING
CAUTION
CAUTION
NOTICE
DANGER indicates an imminently hazardous situation which, if not avoided, will result in death or serious
injury.
WARNING indicates a potentially hazardous situation which, if not avoided, could result in death or
serious injury.
CAUTION indicates a potentially hazardous situation which, if not avoided, may result in minor or
moderate injury.
CAUTION used without the safety alert symbol indicates a potentially hazardous situation which, if not
avoided, may result in property damage.
NOTICE indicates special instructions on installation, operation, or maintenance that are important but
not related to personal injury or property damage.
2

Loop Control Board Instructions
1 Introduction
The information contained in this manual provides installation and operation instructions for the addition of the MultiTemperature Loop Control Board in conjunction with the Lochinvar Knight (KB(N/L) 81-286), Knight XL (KB(N/L) 400 -801),
Wall Mount (WB(N/L) 51-211, WH(N/L) 55-399) boilers.
When connected on the Cascade communication bus to the boiler control, the Multi-Temperature Loop Control Board
(MTLCB) will actively control the water temperature supplied, up to three (3) loops. The MTLCB will control the 3-way mixing
valves and pumps for each of these loops, and provide the actual loop temperatures to the boiler for display.
The MTLCB has been tested, and is in compliance with the following standards:
• CSA Standard C22.2 No 0 - General Requirements - Canadian Electrical Code, Part II
• CSA Standard C22.2 No 24 - Temperature-Indicating & Regulating Equipment
• ANSI/UL 873 - Temperature Indicating and Regulating Equipment
3

2 Components and Hydronic Piping
Components
Loop Control Board Instructions
The multi-temperature loop control consists of four (4)
major components in conjunction with the boiler system.
These components are as follows:
• Multi-Temperature Loop Control Board
• Loop Temperature Sensors
• Mixing Valves
• Loop Pumps
In order for the system to work properly the components
listed above must be installed correctly. Reference the
piping illustrations included in this section (FIG.’s 2-1 and
2-2) for suggested guidelines in piping.
NOTICE
1. Multi-Temperature Loop Control Board (MTLCB):
The MTLCB communicates with the boiler’s SMART
SYSTEM control for operation of the mixing valves and
loop pumps to regulate each loop temperature. The
power supply required for the MTLCB is 120 V/60 Hz
at less than 12 amps.
Please note that the piping illustrations
(FIG.’s 2-1 and 2-2) are meant to show
system piping concept only, the installer
is responsible for all equipment and
detailing required by local codes.
Table 2A 3-Way Valve Requirements
3-Way Valve Requirements
Item Description Limit
Power Supply 24 VAC
Maximum Load .25 Amps
Control Signal 3-Point (Open, Close, Com)
Action Type Floating / Modulating
4. Loop Pumps:
Field supplied. The MTLCB provides 120 VAC power to
operate three (3) loop pumps. The maximum current rating
for each pump cannot exceed 1.8 amps.
2. Loop Temperature Sensors:
The loop temperature sensors measure the temperature
of each loop. Each sensor should be placed on the
discharge side of the loop pump as shown in FIG.’s
2-1 and 2-2 on pages 5 and 6 of this manual. Use
only the three (3) NTC thermistor sensors supplied. If a
replacement sensor is needed, order Lochinvar part
number TST2032. For the best reading, the sensor
should be securely fastened to the pipe and insulated.
3. Mixing Valves:
Field supplied. The MTLCB is designed to control
24 VAC fl oating 3-way mixing valves with open and
close signals. These valves have an actuator (motor)
time from full open to full close. The time in seconds
must be consistent across all 3-way valves installed. For
information on programming the mixing valve time
into the boiler, reference Section 4 , Boiler Parameter
Setup. For 3-way valve requirements, reference Table
2A.
4

Loop Control Board Instructions
2 Components and Hydronic Piping (continued)
Figure 2-1_Single Boiler Multi-Temperature
PRESSURE
REDUCING VALVE
BACKFLOW
PREVENTER
MAKE
UP
WATER
AIR SEPARATOR
BALL VALVE
(TYPICAL)
DRAIN POINT
(TYPICAL)
LOOP
SENSOR
(TYPICAL)
PRESSURE
GAUGE
SYSTEM
SUPPLY
SENSOR
EXPANSION
TANK
MAY SUBSTITUTE
LOW LOSS HEADER
TEMPERATURE
LOOP #1
NOT TO EXCEED 4 PIPE DIA.
OR MAX. OF 12" APART
Y-STRAINER
(RECOMMENDED)
BOILER
CIRCULATOR
FLOW CHECK
VALVE
TEMPERATURE
LOOP #2
TEMPERATURE
LOOP #3
DOMESTIC
HOT WATER
CIRCULATOR
MIXING VALVES
(TYPICAL)
HOT
WATER
OUT
ANTI-SCALD
MIXING VALVE
COLD
WATER
IN
NOTICE
NOTICE
UNION
(TYPICAL)
TEMPERATURE /
PRESSURE
GAUGE
DRAIN
BOILER
BOILER
INDIRECT
DHW TANK
INDIRECT
DHW
Please note that these illustrations are meant to show system piping concept only, the installer is responsible
for all equipment and detailing required by local codes.
A system supply sensor MUST BE installed for proper boiler operation to occur.
5