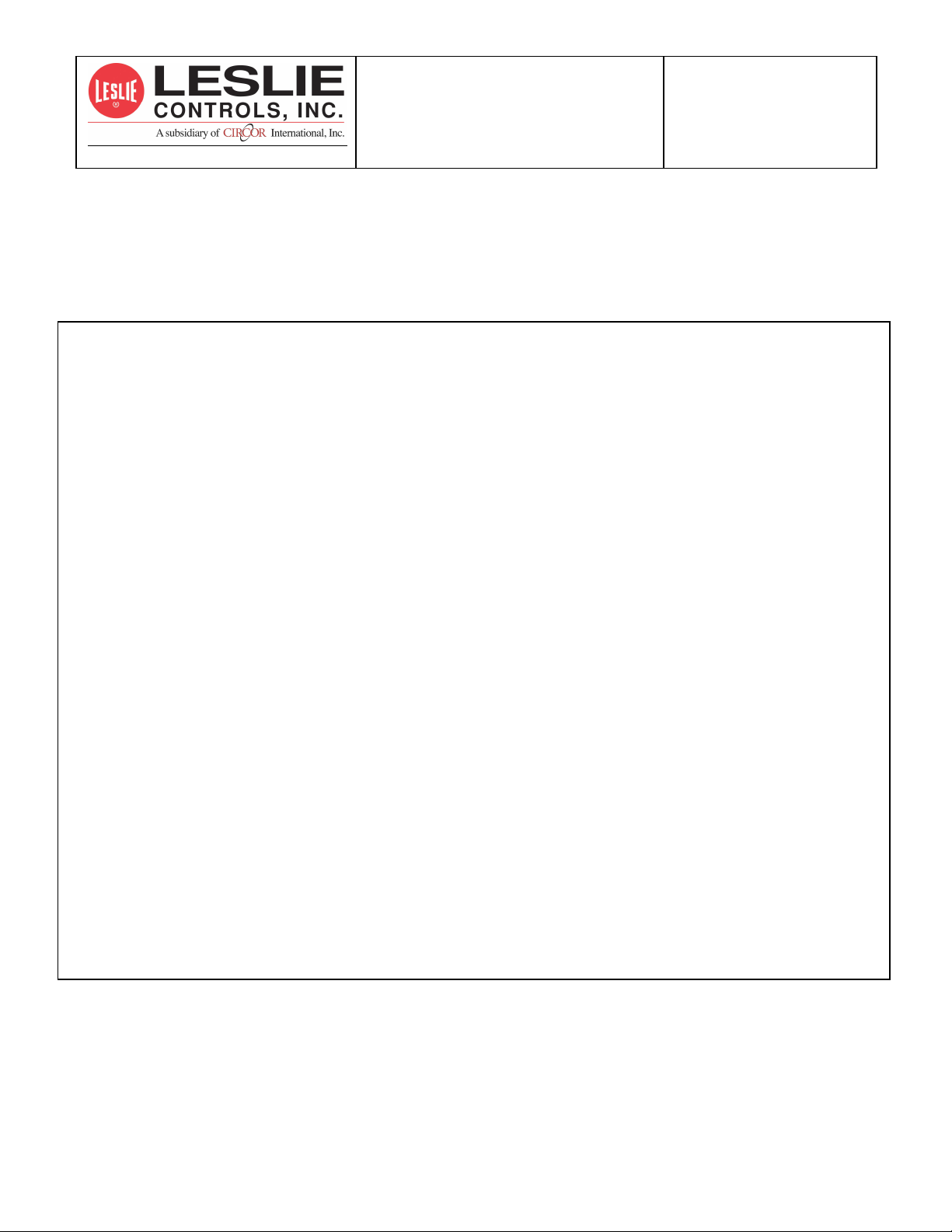
12501 Telecom Drive, Tampa Florida 33637
Installation, Operating and
Maintenance Instructions
Supplement
AEROFLOW SUPPLEMENT
ANSI 4500 Aeroflow
10/2.5.1.F
Rev. 2
TABLE OF CONTENTS
INSTALLATION & OPERATION
MAINTENANCE
VALVE ASSEMBLY................................................................................................................................2
.....................................................................................................................2
INSPECTION AND CLEANING
...................................................................2
........................................................................2
ILLUSTRATION INDEX
F
IGURE 1 –
4500 A
EROFLOW WITH SPECIAL THERMAL GROWTH TRIM
..........................................................3
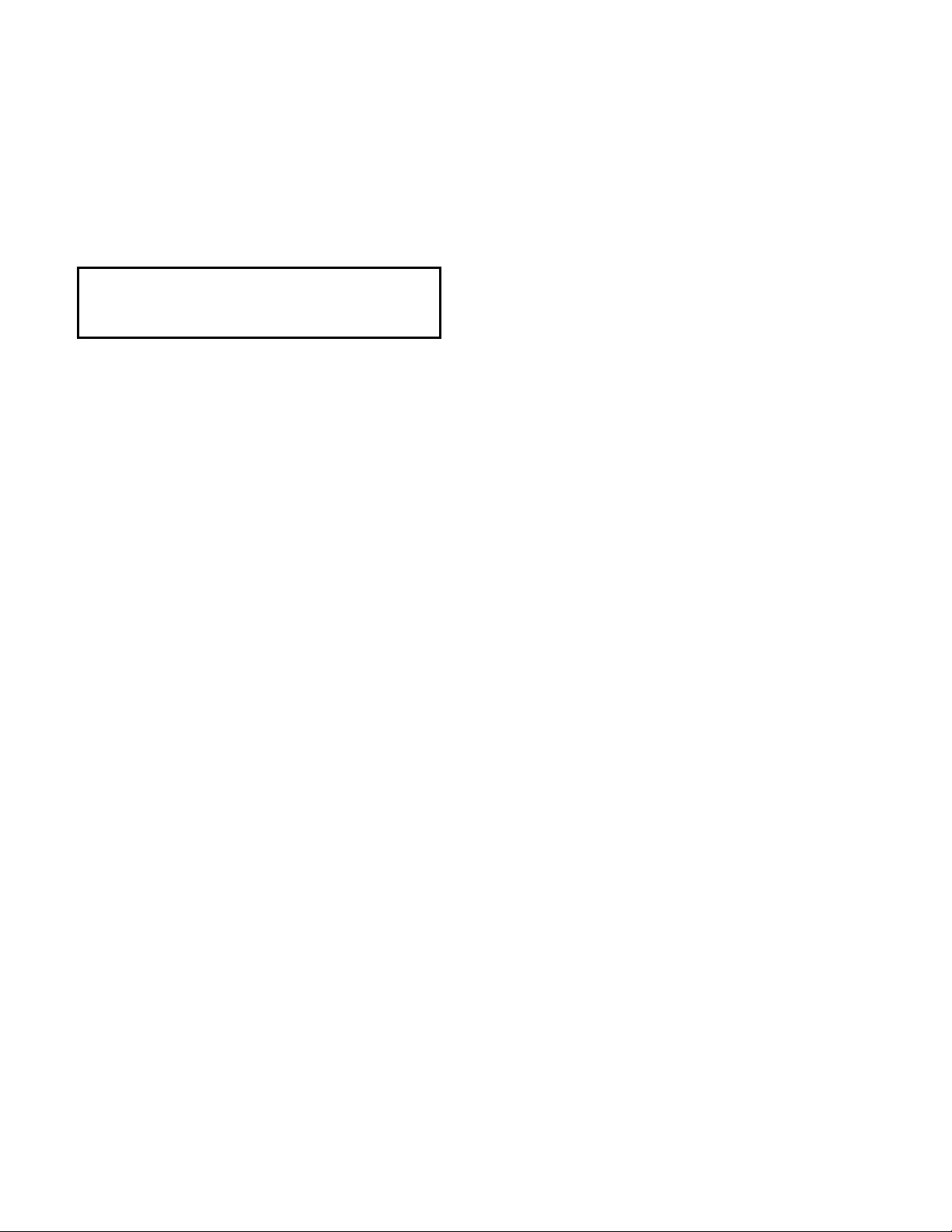
INSTALLATION &
OPERATION
Refer to standard IOM 10/2.5.1for installation &
operation.
All warnings from standard valve IOM must be
NOTE: Refer to Fig. 1 for assembly.
MAINTENANCE
VALVE ASSEMBLY
1. Carefully position a new seat ring gasket (511) in the
body (303) recess. Install seat ring (510) with seating
surface upward.
2. Install load ring (504) on top of seat ring (510).
3. Before installing seat ring retainer (505) in valve,
lubricate silver plated set screws (503) with a nickel
based anti-seize compound (Never-Seez, Jet Lube,
Nickel or equiv.) then screw sliver plated set screws
(503) into seat ring retainer (505) with cup point end
of set screw flush with bottom surface of retainer.
4. Position the seat ring retainer (505) on top of seat ring
flange. (Bolts may be used as handles in two setscrew
holes to aid in installing seat ring retainer.) When
retainer is in place, remove bolts and insert setscrews.
Grip one end of spiral retaining ring (505), pull
through top body diameter and insert one end into
body groove. Insert ring into groove until the full ring
is installed. To compress the seat ring gasket and load
seat ring, tighten setscrews according to the following
procedure to ensure that gasket is fully compressed
and evenly loaded:
a) Initially tighten setscrews finger tight (2-3 ft-
lbs).
b) Develop the required screw torque by moving
around the ring in a screw-to-screw sequence to
ensure all screws are equally stressed. Apply
the torque in three steps according to the
following table:
5. Step Torque, ft lbs
1 15
2 30
3 35
6. Assemble the pilot plug assembly per standard
IOM 10/2.5.1.
7. Attach the cage (600) and cage O-ring (602) to
the bonnet (302) using (601) screws (tight to 3035 ft-lbs) and slide into valve body (303) over the
plug assembly.
8. Assemble the pressure seal (307), backing ring
(308), split ring (310) and bonnet retainer (309).
9. Snug the nuts (305/306) up using studs (304) until
bonnet is fully seated against the pressure seal
then tighten an additional 2 turns.
10. Pressurize valve to the Cold Working Pressure
(CWP) or the Production Hydro Pressure, which
ever is appropriate, to seat the pressure seal
gasket (307).
11. Depressurize the valve.
12. Snug nuts to 10-20 ft-lbs.
INSPECTION AND
CLEANING
The standard valve IOM should be followed for all
inspection and cleaning procedures.
2

Figure 1 – 4500 Aeroflow with Special Thermal Growth Trim
It is solely responsibility of system designer and user to select products and materials suitable for their specific
application requirements and to ensure proper installation, operation and maintenance of these products. Assistance
shall be afforded with selection of materials based on technical information supplied to Leslie Controls Inc.; however,
system designer and user retain final responsibility. Designer should consider applicable Codes, material
compatibility, product ratings and application details in selection and application. Improper selection, application or
use of products described herein can cause personal injury or property damage. If designer or user intends to use
product for an application or use other than originally specified, he must reconfirm tat selection is suitable for new
operating conditions. Life expectancy for this product defaults to warranty period of sales contract.
3