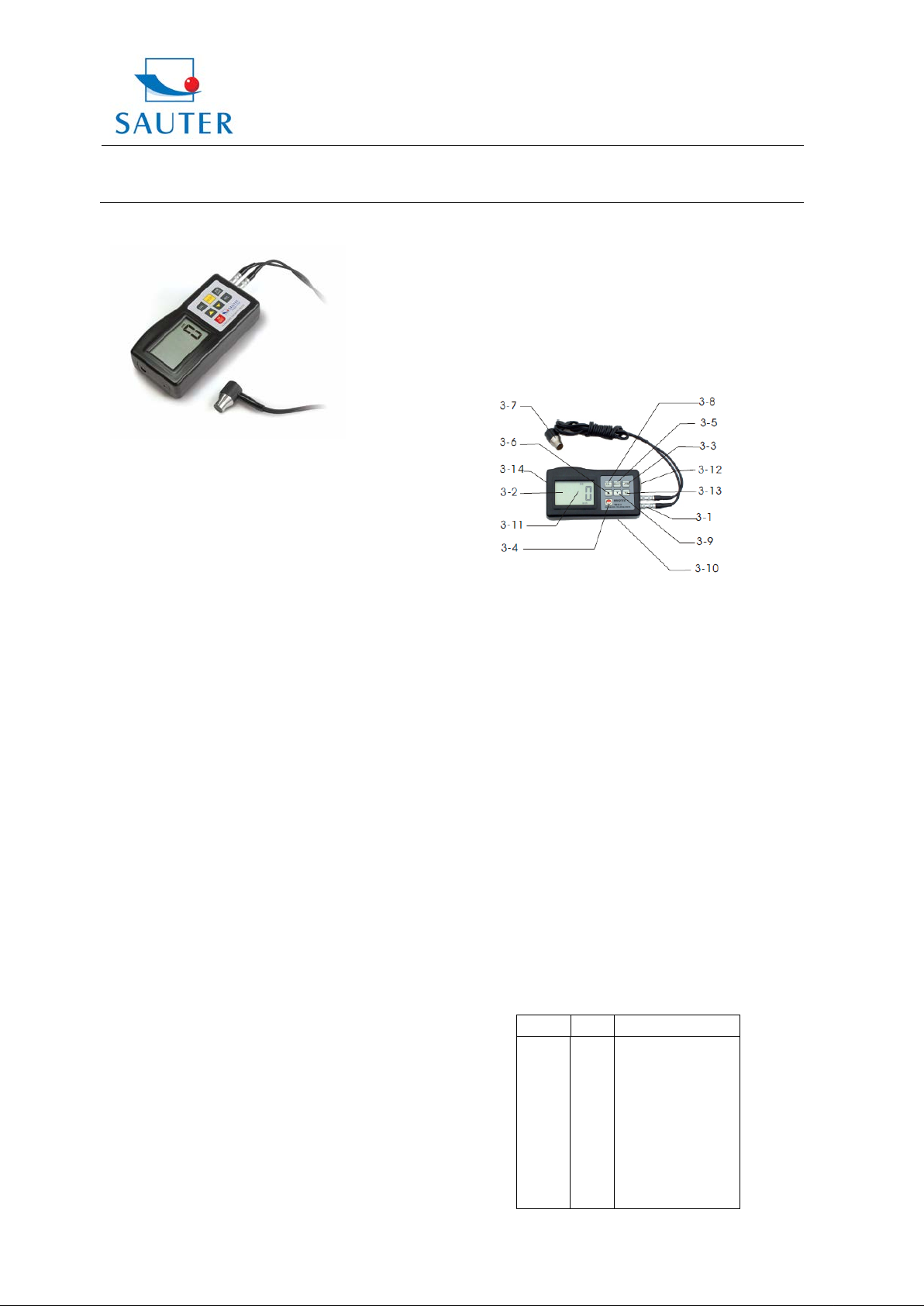
Ziegelei 1
D-72336 Balingen
E-Mail: info@sauter.eu
Instruction Manual
DIGITAL THICKNESS GAUGE
Tel: +49-[0]7433- 9933-199
Fax: +49-[0]7433-9933-149
Internet: www.kern-sohn.com
Humid i ty: <80%
Size: 120 x 62 x 30mm (4.7 x 2.4 x 1.2 inch)
Weight: about 164g (not including batteries)
Accessories: Carrying case
Operation manual
Ultrasonic sensor
3. Front panel description
Model: TD 225-0.1 US
Table of contents
1. Features
2. Specifications
3. Front panel description
4. Material selection
5. Calibration
6. Measuring procedure
7. Measuring by velocity setting
8. Battery replacement
9. Declaration of conformity
Annotation: It is strongly recommended to calibrate
the new instrument before the first use, as
described in paragraph 5. By doing this it
will be achieved a much better measure ment result right from the start.
1. Features
* The exclusive Micro- computer LSI offers high
measurement accuracy.
* The instrument offers high power of emission and a
wide spectrum of receiving sensitivity.
Sensors of different frequencies can be identified.
Rough surfaces, even cast iron, can be measured.
It is used in alm ost all kinds of industries.
* Convenient to measure the thickness of many materials,
e.g. steel, cast iron, aluminium, red copper, brass, zinc,
quarz glass, Polyethylen, PVC, grey cast iron, nodular
cast iron.
* Automatic power-off to preserve batteries.
* Date transfer to PC possible. Cable and software can be
obtained as optional accessory.
2. Specifications
Display: 4 digits, 10mm LCD
Range: 1.0 to 200mm (45# steel)
Resolution: 0.1mm / 0.001 inch
Accuracy: ± (0.5%n+0.1)
Sound velocity: 500 to 9000m/s
Power supply: 4×1.5V AAA (UM-4) battery
Operating conditions: Temperature: 0 to 50°C
3- 1 Sensor plug
3- 2 Display
3- 3 mm/ inch key
3- 4 Power- key
3- 5 Material selection key
3- 6 Plus- key
3- 7 Ultrasonic sensor
3- 8 Calibration key
3- 9 Minus- key
3-10 Battery compartment/ cover
3-11 Coupling indicator
3-12 Base plate
3-13 Velocity key
3-14 RS-232C interface
4. Material selection
4.1 The instrument has to be switched on by the
Power- key 3-4.
4.2 The Material selection key 3-5 has to be pressed and
the display 3-2 will show the code `cdxx` or `xxxx`.
`cd` is the abbreviation for `code` and `xx` is a
number among 0.1 and 11 that stands for the material
to be measured as shown in the scale below.
. `xxxx` is a 4-digit number describing
the sound velocity of the material defined by the user.
The `cdxx` material relationship is as follows:
1
2
3
4
5
6
7
8
9
10
11
cd01
cd02
cd03
cd04
cd05
cd06
cd07
cd08
cd09
cd10
cd11
Steel
Cast iron
Aluminium
Red copper
Brass
Zinc
Quarz glass
Polyethylen
PVC
Grey cast iron
Nodular cast iron
TD_US-BA-e-1310 1
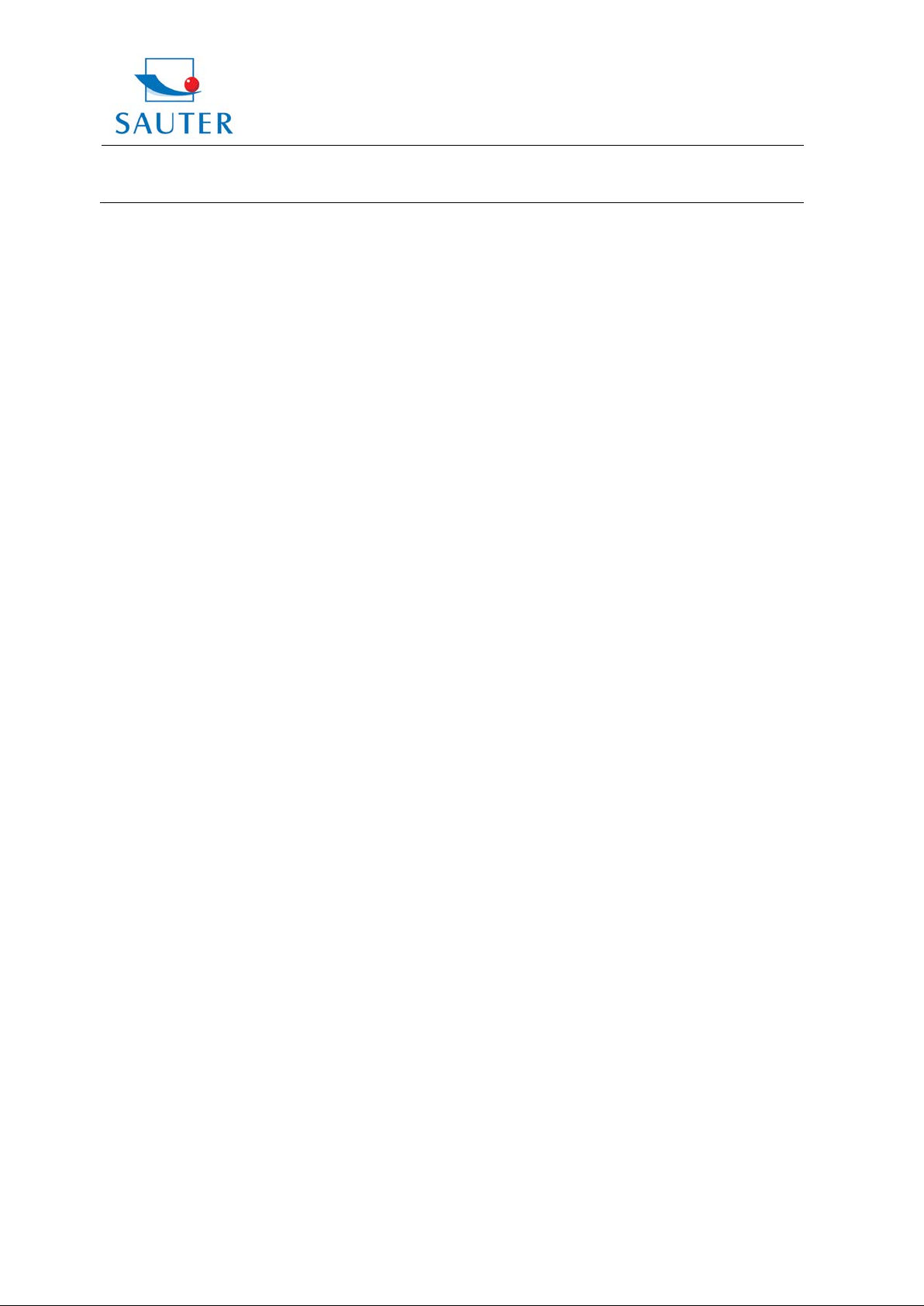
Ziegelei 1
D-72336 Balingen
E-Mail: info@sauter.eu
Instruction Manual
4.3 The Plus key 3-6 or the Minus key 3-9 is to be pressed
to select the material code to measure. Then the
Material selection key 3-5 is to be pressed to confirm.
The instrument changes into the measuring mode and
on the display occurs `0`.
If a material code is selected without confirming this
selection, the instrument will automatically change
back into the measuring mode after a few seconds.
In this case the primary material code will still be
stored before switching off.
4.4 A 4-digit number will be shown on the display by
pressing the Plus key 3-6 when displaying `cd11`or the
Minus key 3-9 is to be pressed when displaying `cd01`.
The 4-digit number is the last sound velocity being de fined by the user. By changing the velocity, varying
qualities of materials can be compensated.
4.5 If the material code has once been selected and saved
it is stored in the memory of the instrument. As long
as no modification is done, the instrument will always
raise (use) this material code.
4.6 To get into the menu selection of the material code, the
Material selection key 3-5 is to be pressed. To quit the
menu the material selection key is to be pressed again
or it has to be waited until the instrument- after a few
seconds- changes back into the measuring mode.
On the display appears `0`.
5. Calibration
5.1 A little oil is to be dropped on the base plate 3-12.
5.2 The calibration key 3-8 is to be pressed and `CAL`
appears on the display.
`CAL` is the abbreviation for calibration.
5.3 The sensor 3-7 is to be pressed on the base plate. The
coupling symbol ((•)) (measurement in action) occurs if
the measuring procedure has been established
successfully by the process of sound sending and
receiving.
On the display appears`5.0mm` or 0.197 inch
(debit thickness of the base plate) and `CAL` in turn.
As soon as the value is stabilized, the `CAL` key 3-8 is
to be pressed to confirm. Then the instrument
changes back into the measuring mode.
5.4 The calibration has been finished and automatically
saved in the instrument.
6. Measuring procedure
6.1 The Power key 3-4 is to be pressed to switch on the
instrument.
6.2 The mm/ inch key 3-3 is to be pressed to select the
correct measurement unit.
6.3 The sensor 3-7 is to be placed onto the material
surface to be measured, provided that the material
code has been selected correctly.
Assure yourself that coupling is fine and the symbol
((•)) 3-11 is active. The measurement result is to be
shown on the display.
Tel: +49-[0]7433- 9933-199
Fax: +49-[0]7433-9933-149
Internet: www.kern-sohn.com
6.4 The measurement result is saved until a new measure ment is performed. The last value is conserved on the
display until the instrument is switched off.
6.5 The instrument can be switched off by the Power- on/
Power- off key or by Auto-Power off function, one
minute from last key operation.
7. Measuring by velocity setting
7.1 By pressing the VEL- key 3-13, on the display appears
last saved velocity.
7.2 Measuring of coatings & materials by a known
thickness:
Velocity can be adjusted by pressing the Plus- or the
Minus- key. By doing this, the value shown on the
display is changed higher or lower. First the increase
is 10m/ s . If th e P lus- or Minus- key is pressed for
longer than 4 seconds, the increase is 100m/ s.
7.3 A little oil is to be dropped onto the material to be
measured. Now the sensor 3-7 is pressed onto the
surface to be measured. The reading on the display
is the thickness, assumed that coupling is well.
If velocity of a special material is known, it is easy to
measure the thickness with the help of step 7.2.
7.4 Measuring of coatings & materials with an
unknown thickness:
A test material of known thickness is to be selected.
Step 7.2 (vel.setting) and 7.3 is to be repeated until the
measured value is exactly the same as the known
thickness. In this case the set value is the velocity of
the material to be measured.
With this, any number of unknown thicknesses of the
same material can now be measured.
7.5 To change velocity, VEL- key 3-13 is to be pressed.
To return into the measuring mode, this key is to be
pressed again or it has to be waited until the instru ment automatically shows `0`.
7.6 By using velocity measurement, the coating thickness
or the thickness of any hard materials can easily be
measured.
8. Battery replacement
8.1 If the battery symbol appears on the display,
batteries should be replaced.
8.2 The battery cover is to be removed from the instrument
and the batteries are to be taken off.
8.3 Batteries are to be installed, paying carefully attention
to polarity.
TD_US-BA-e-1310 2

9. Declaration of conformity
Ziegelei 1
D-72336 Balingen
E-Mail: info@sauter.eu
Instruction Manual
Tel: +49-[0]7433- 9933-199
Fax: +49-[0]7433-9933-149
Internet: www.kern-sohn.com
TD_US-BA-e-1310 3