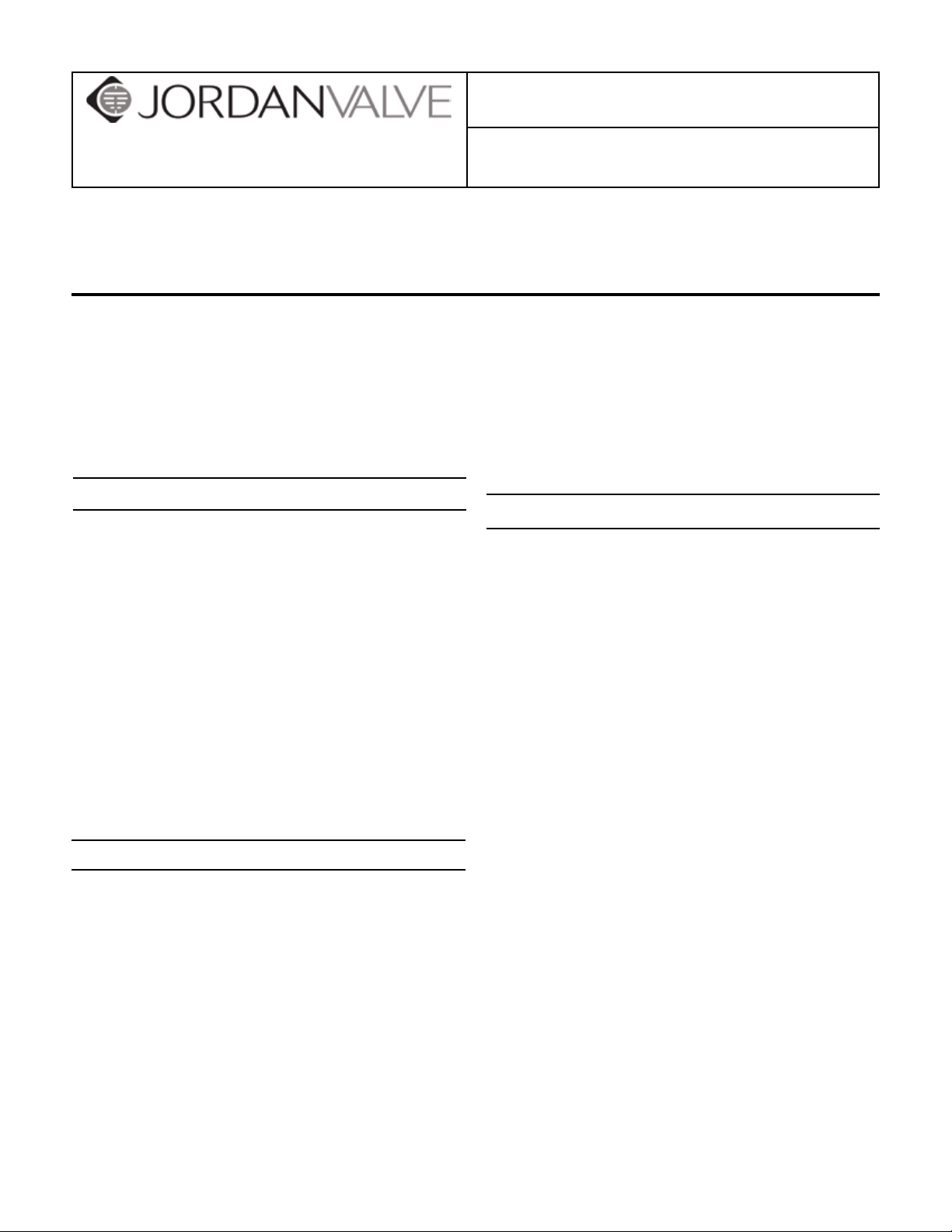
I & M Mark 86
3170 Wasson Road • Cincinnati, OH 45209 USA
Phone 513-533-5600 • Fax 513-871-0105
info@richardsind.com • www.jordanvalve.com
Warning: Jordan Valve Temperature Regulators must only be used, installed and repaired in accordance with these
Installation & Maintenance Instructions. Observe all applicable public and company codes and regulations. In the
event of leakage or other malfunction, call a qualied service person; continued operation may cause system failure
or a general hazard. Before servicing any valve, disconnect, shut off, or bypass all pressurized uid. Before disassembling a valve, be sure to release all spring tension.
Please read these instructions carefully!
Your Jordan Valve product will provide you with long,
trouble-free service if it is correctly installed and maintained. Spending a few minutes now reading these instructions can save hours of trouble and downtime later.
When making repairs, use only genuine Jordan Valve
parts, available for immediate shipment from the factory.
Installation & Maintenance Instructions for
Mark 86 Temperature Regulator
underside of the actuator.
The temperature at which the valve is fully open,
as indicated on the Set Point Indicator, can be
changed by turning the adjusting wheel under the
spring. Turn the wheel to compress the spring to
increase the setting. Turn the wheel downwards to
release compression on the spring to decrease the
temperature setting. The limits of adjustment are
indicated on the nameplate under “Range”.
Introduction
Field & Shop Testing Procedures
The Mark 86 AMBITEMP II Ambient Temperature Sensing
Control Valve, our AMBITEMP II, responds to temperature
changes of the air surrounding the actuator. The most
common application for the Mark 86 is the automatic
control of tracing steam or other hot uids, to prevent
freezing of process piping. As the temperature of the
area in which the valve is installed decreases to near
the freezing point, the valve opens. As the temperature
increases to a safe level the valve will close and thereby
conserve the heat energy lost on manually controlled
constantly owing systems.
The Mark 86 is identical to the Mark 80 Temperature
Regulator except that the Mark 86 requires no capillary
or sensing bulb. The actuator on the Mark 86 serves as
both the sensing element and the power element.
Installation
All of the Installation and Maintenance instructions for
the Mark 80 apply also to the Mark 86 except for the instructions which pertain specically to the sensing bulb.
Additional instructions regarding the installation of a
Mark 86 are as follows:
Field Testing (Valve Closed):
Observe that Stem Position Indicator points to 1.
“CLOSED”.
Observe SET POINT on the Set Point Scale. This 2.
indicates the temperature at which the Mark 86
will be fully open. (See Temp. Span Chart on P.2
Ambitemp II Bulletin to nd temperature at which
regulator is fully closed.)
By spraying the top of the SST Diaphragm Actuator 3.
(Thermal Head) with Freon-22, thus simulating lowering ambient temperature, the valve stem position
indicator will move to the “Open” position (in about
15-20 seconds) showing the valve is functioning.
ALTERNATE TEST METHOD: Tape a piece of a.
cardboard or sheet metal around the circumference of the actuator so that it extends about
two inches above the edge. Place ice, cubes or
crushed, on the top of the actuator to cover as
much surface as possible. The valve will stroke
within ve minutes and should indicate full
open on the STEM POSITION INDICATOR.
Shop Calibration and Setting (For 32°F Set Point):
Do not install the valve so that the actuator is near
a source of heat, such as another steam or hot oil
line.
Insulate the piping adjacent to the Mark 86 to pre-
vent radiant heating of the actuator.
Install the valve upright in the line on outdoor appli-
cations so that precipitation does not collect in the
Place entire SST Diaphragm actuator (Thermal 1.
Head) in ice water. Wait approximately ve minutes.
Now turn the adjusting wheel until seats are com-2.
pletely open.
If necessary, reposition seat point scale so that set 3.
point indicator points to 32°F.
If a different “wide open” set point is desired, turn 4.
the adjusting wheel until the set point indicator
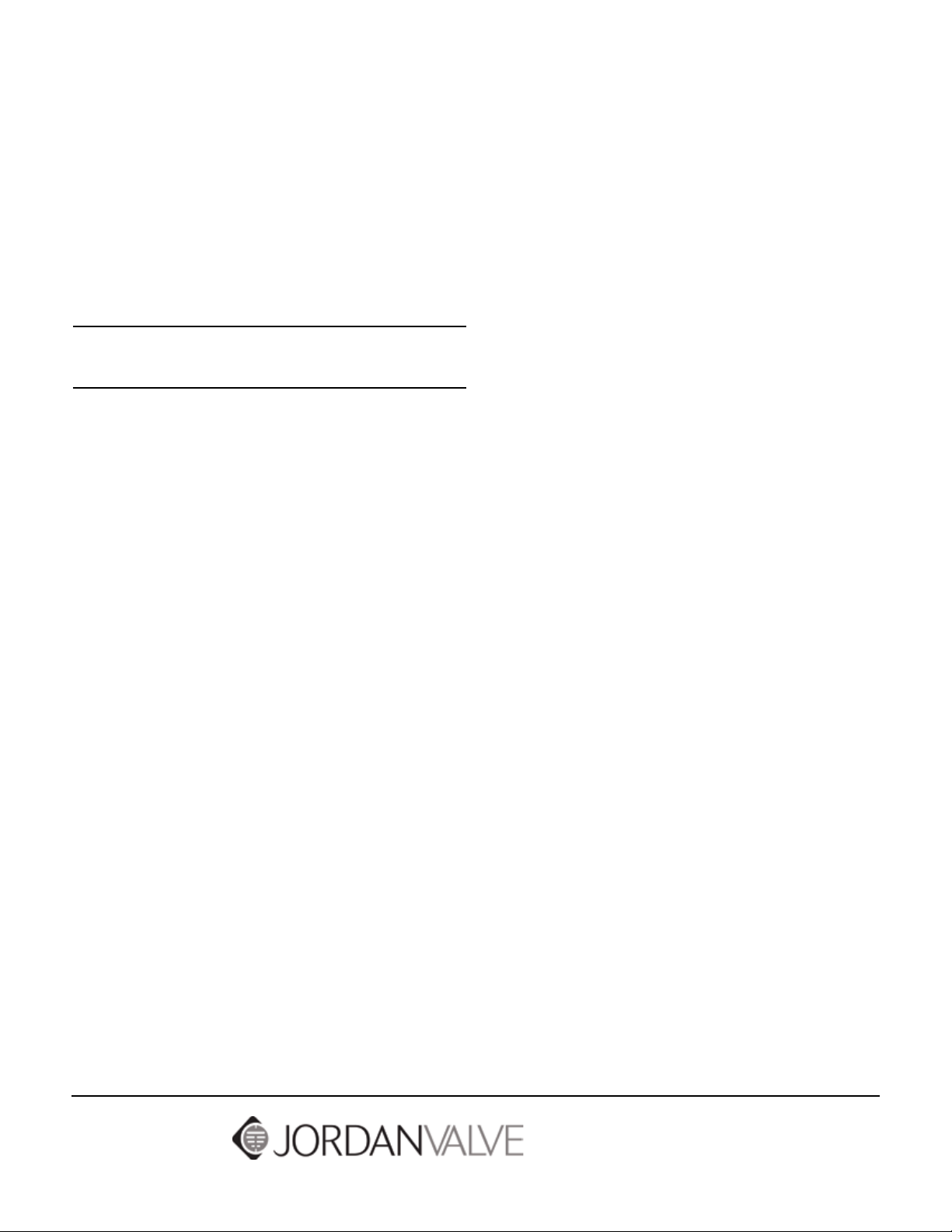
point to the desired temperature on the temperature set point scale. (This method of setting the
Ambitemp II is quite accurate ± 2-3°.)
For precise setting at temperatures other than 32°F, the
actuator must be enclosed by an insulated housing (such
as a split box). A thermometer is inserted to indicate
the temperature inside this enclosure. By using a Vortex
Tube arrangement, the desired “Ambient” Temperature
(at which the Ambitemp II is to be wide open) can now
be simulated. Once stabilized, turn adjusting wheel until
seats are wide open; then reset set point indicator scale
as previously described.
Factory Test Procedure For
MK86 Ambitemp
First the body and cap are hydrostatically tested at a
pressure of 1½ times the maximum working pressure of
the valve.
The valve is then assembled and sent to the nal test department where it is tested as follows:
NOTE 1: To stroke the Mark 86 the actuator must be
cooled to below the valve set point. To do this we use a
vortex and insulated housing around the actuator. This
vortex tube is capable of cooling the entire actuator assembly to approximately 0º F.
NOTE 2: To set the Mark 86, the probe from the digital
thermometer is inserted into the insulated housing surround the actuator assembly. The actuator assembly is
brought to the temperature required by the set point.
When this temperature is reached, the adjustment screw
is turned so that the valve is fully open.
All nuts and bolts are checked for tightness.1.
The valve is checked against the written order to 2.
assure the proper size, action, range, and Cv.
The valve is then clamped in a test xture and 100 3.
psi of air pressure is applied to the inlet side of the
valve.
With 100 psi of inlet air pressure and the outlet 4.
open to atmosphere, the valve is stroked (see note
1) several times.
The valve is then stroked to the closed potion, 5.
the outlet of the test xture is closed and the seat
leakage is checked. Seat leakage is measured by
means of a ow meter calibrated in standard cubic
feet per hour (SCFH). All Jordan Valves have a leakage rate of .01 percent of the rated ow capacity or
less per class IV of ANSI B16.104.
The valve being tested is then stroked to the open 6.
position allowing both the cap and the body to be
pressurized.
All pressure containing areas are checked with a 7.
soap solution for external leakage.
The valve is then set to the customer specied set 8.
point (see note 2).
The set point indicator is now installed. Because 9.
the set point indicator is installed after the valve is
tested and set, we are insured of the correct calibration for this particular valve.
Bulletin IM-MK86-0210
3170 Wasson Road • Cincinnati, OH 45209 USA
Phone 513-533-5600 • Fax 513-871-0105
info@richardsind.com • www.jordanvalve.com