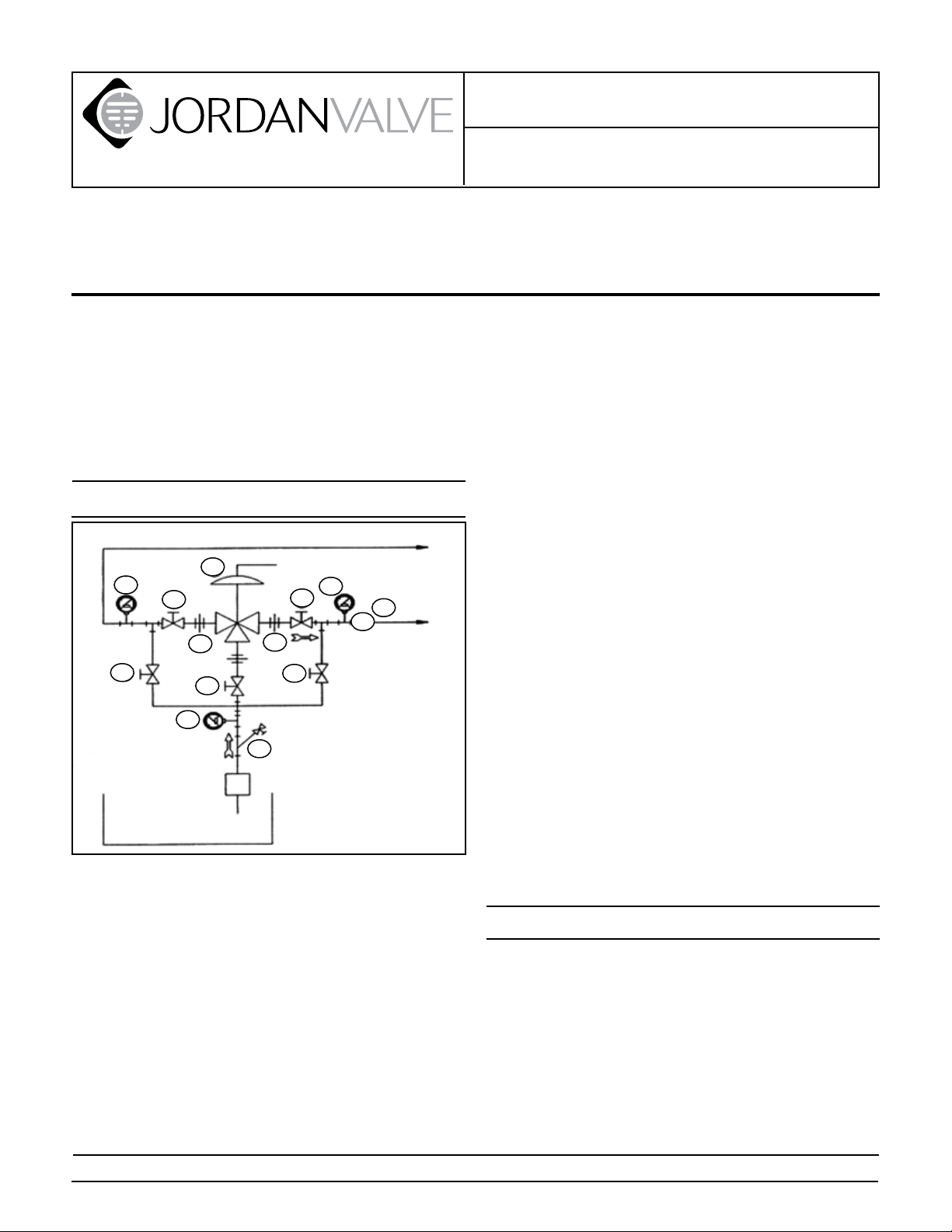
I & M Mark 79/79MX
3170 Wasson Road • Cincinnati, OH 45209 USA
Phone 513-533-5600 • Fax 513-871-0105
info@richardsind.com • www.jordanvalve.com
Installation & Maintenance Instructions for
Mark 79 Three Way Control Valves (1/4” - 2”)
Warning: Jordan Valve Control Valves must only be used, installed and repaired in accordance with these Installation & Maintenance Instructions. Observe all applicable public and company codes and regulations. In the event
of leakage or other malfunction, call a qualied service person; continued operation may cause system failure or a
general hazard. Before servicing any valve, disconnect, shut off, or bypass all pressurized uid. Before disassembling
a valve, be sure to release all spring tension.
Please read these instructions carefully!
sealer Teon ribbon.
A line strainer should be installed on the inlet side 4.
Your Jordan Valve product will provide you with long,
trouble-free service if it is correctly installed and maintained. Spending a few minutes now reading these instructions can save hours of trouble and downtime later.
When making repairs, use only genuine Jordan Valve
parts, available for immediate shipment from the factory.
of the valve. A 0.033 perforated screen is usually
suitable. Line strainers are available from Jordan
Valve.
Install the valve in the highest horizontal line of 5.
piping to provide drainage for inlet and outlet piping, to prevent water hammer and to obtain faster
response.
The ow arrow on the valve body must be pointed 6.
Main Line
4
1
Ideal Installation
Control Valve
4
1
1
1. Shut off Valve
2. Pipe Union
3. Strainer and Drain Valve
4. Pressure Gauge
5. Jordan Series 790 DCV
6. Relief Valve
1
2
1
4
Pump
Reservoir
5
2
3
6
R
in the direction of ow. The valve may be installed
vertically or horizontally without affecting its operation.
For best control, 3’ 0” straight sections of pipe 7.
should be installed on either side of the valve.
In hot vapor lines, upstream and downstream pip-8.
ing near the valve should be insulated to minimize
condensation.
If possible, install a relief valve downstream from 9.
the valve. Set at 15 psi above the control point of
the valve.
Expand the outlet piping at least one pipe size if 10.
the controlled pressure (downstream) is 25% of
the inlet pressure or less. A standard tapered expander connected to the outlet of the valve is recommended.
Where surges are severe, a piping accumulator is 11.
recommended.
The air piping or tubing to the diaphragm case 12.
should be 1/4” or 3/8”. The length of tubing should
To protect the valve from grit, scale, thread chips 1.
be less than 150 feet.
and other foreign matter, ALL pipelines and piping
components should be blown out and thoroughly
Start Up
cleaned before the installation process begins.
Shutoff valves, pressure gauges and by-pass piping 2.
should be installed as indicated in the Ideal Installation Schematic to provide easier adjustment, operation, and testing.
In preparing threaded pipe connections, care 3.
should be exercised to prevent pipe-sealing compound from getting into the pipe lines. Pipe sealing compound should be used sparingly, on male
threads only, leaving the two lead threads clean.
Jordan uses and recommends Seyco #2415 thread
The MK79 Control Valve has been pre-set by 1.
Jordan; however, ner adjustments may be
required to compensate for pressure drops of
the application. See the “Spring Pre-Loaded
Adjustment” section.
Close all inlet, outlet and by-pass shut-off valves. 2.
Remove all pressure from downstream lines.
Fully open the outlet shut-off valves. Slowly open 3.
the inlet shut-off valve just enough to start ow
through the control valve. Increase the ow
PROTECT VALVES WITH LINE STRAINERS
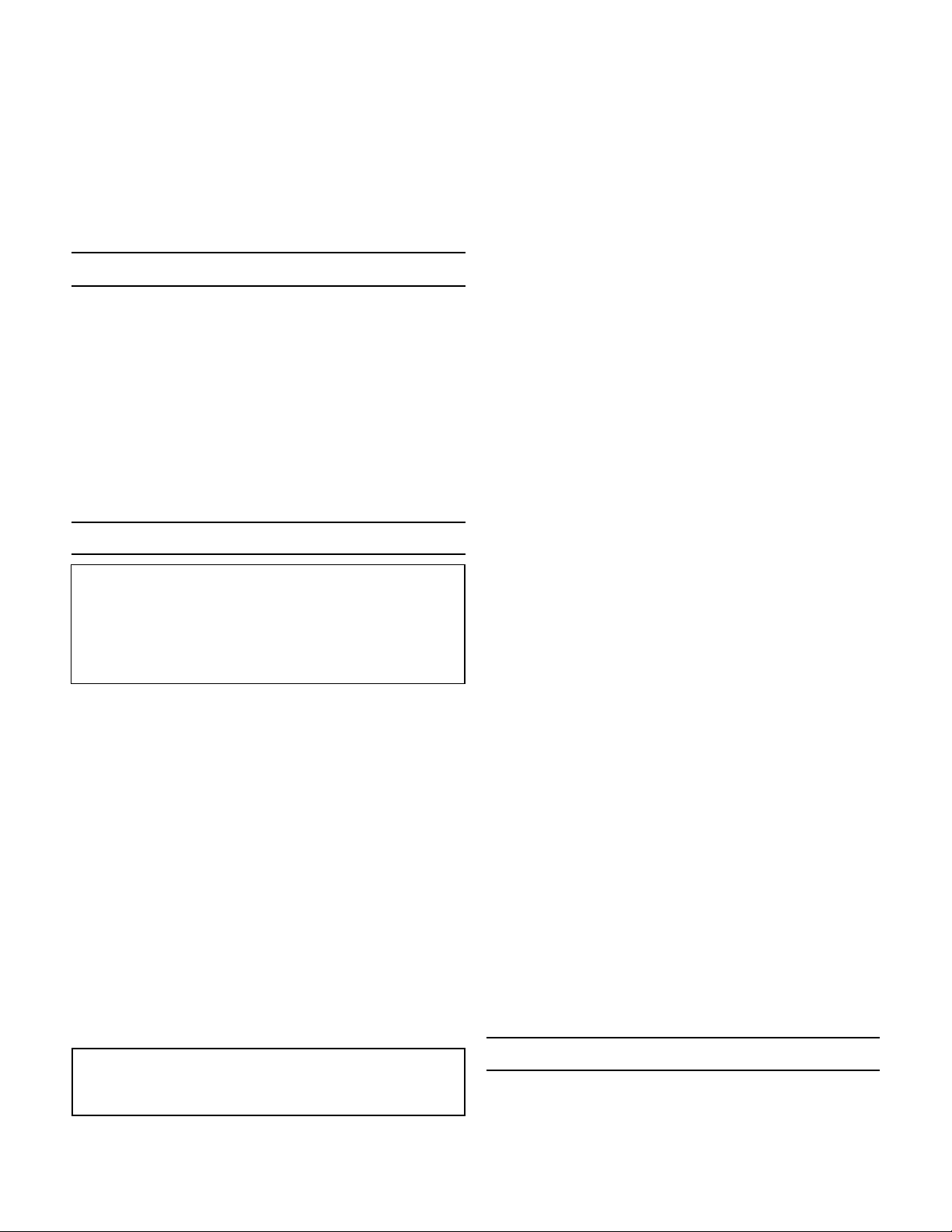
gradually by slowly opening the inlet shut-off valve.
DO NOT fully open the inlet shut-off valve until you
are sure that the controller and control valve have
control of the system.
To shut off the line uid, close the inlet shut-off 4.
valve rst, then the outlet shut-off valves.
Body and cap bolts should be re-tightened per 5.
torque procedures after valve reaches operating
temperature.
Maintenance
Caution: Be sure that there is no pressure in the valve
before loosening any ttings or joints. The following
steps are recommended:
Close inlet shut-off valve.1.
Allow pressure to bleed off through downstream 2.
piping. Do not cause a reverse ow through valve
by bleeding pressure from the upstream side of
valve.
Shut off air supply to controller and remove control 3.
air line from the valve.
Valve Seats
The valve seats in all Jordan valves are lapped to
a critical atness. Maintaining such tolerances is
of paramount importance for your assurance of
excellent control and tight shut-off. Do not use
metallic objects in removing the seats. Care in
handling is imperative.
A. DISASSEMBLY
Shut off pressure to the valve. See caution above.1.
Remove the valve from the line.2.
Note the scribed line on the side of valve body and 3.
caps. Secure one of the outlet cap hexes (1) in a
vise. Remove the cap screws (2) from the other cap
and lift the cap straight up.
Next remove the valve plate (3) and place it on the 4.
bench with the lapped surface up. You will notice
that there is a locating pin which aligns the valve
plate with the disc guide (5). The scribe line on the
outside of the valve cap and valve body indicates
that this locating pin should be on this side.
Now remove the valve disc (4) and the disc guide 5.
(5), placing the valve disc on the bench with the
lapped surface up. Fingertip pressure should be
sufcient to remove these parts.
leakage or improper control.
Clean all parts of the body and cap with a good 6.
quality solvent. The valve disc and the valve plate
then may be cleaned. Place a piece of 4/0 polishing cloth or jeweler’s cloth on a smooth, at surface, and polish the lapped surfaces. If the parts
are badly scarred, DO NOT attempt to re-lap them,
but return to the factory for repair or replacement.
USE ONLY JORDAN REPLACEMENT PARTS. The
use of other than genuine Jordan parts may impair
their ability to serve you.
B. REASSEMBLY
On the normally open side, place the disc guide in 1.
the body bore with the index pin on the same side
as the scribe line on the valve body. Apply a small
amount of anti-seize compound to the body bore.
Place the disc in the aperture of the disc guide and 2.
engage the disc pin.
In placing the plate in the body, notice that the 3.
index pin hole in the lapped surface of the plate
engages the index pin of the disc guide.
On Normally Open Side4. : with no pressure on the
actuator, the disc and plate should have the orices
in perfect alignment, with the slots at 90° to the
stem. It may be necessary to move the seat set in
the bore to obtain this critical positioning. On Nor-
mally Closed Side: apply 20-25 psi to the actuator
to assure the valve is stroked fully. Follow alignment
instructions for Normally Open Side.
Apply a small amount of anti-seize compound to 5.
the cap bore and set the cap onto the plate, being
careful not to move the position of the plate.
Tighten the cap screws uniformly, being cautious 6.
not to apply too much torque. See table on page 4
for torque recommendations. Repeat disassembly
and reassembly per “A” and “B” above for second
set of seats.
Special Instructions for Mark 79MX:
All instructions for the MX version are the same as above
with the following modications:
The disc pin protrudes through the plate, with the 1.
disc and disc guide located on top.
Upon start-up, it is important to simultaneously 2.
open both inlets slowly. If only one can be done at
a time, open the normally closed side rst.
It is imperative that the disc pin is not rotated in
disassembly, cleaning, or reassembly, since this
affects the stroke adjustment of the valve.
Improper handling of the seats will result in
Disc Pin
Remove the valve disc and plate (3, 4) following the 1.
procedure outlined under “VALVE SEATS” above.
Loosen the stem connector nut and bolt (19, 20) 2.
and remove connector assembly (18).
-2-