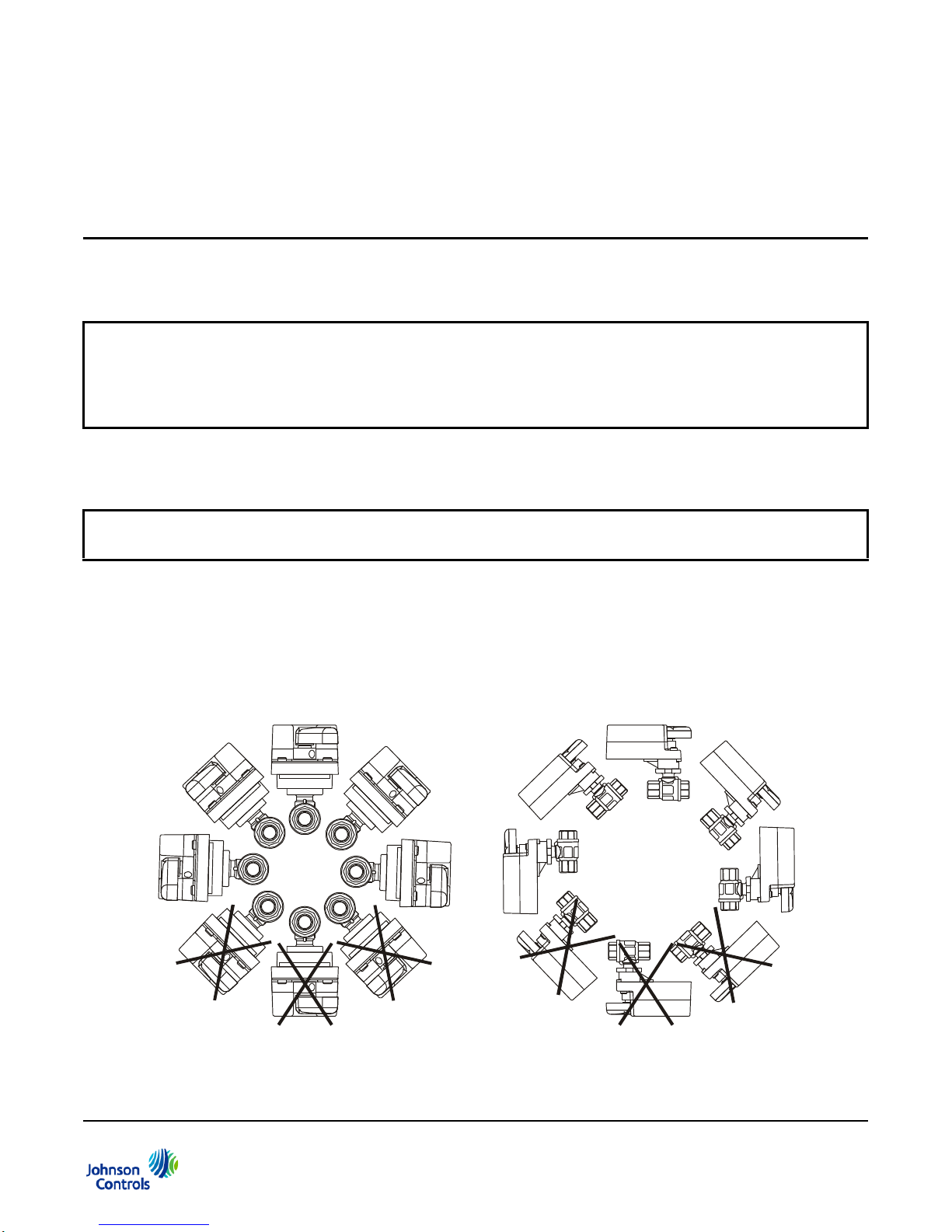
Figure 1: Mounting Positions for Chilled Water and Condensing Atmosphere Applications
*1412015RevX*
14-1201-5 Rev. X
VG1000 Series Forged Brass Ball Valves
Installation Instructions
Part No. 14-1201-5, Rev. X
Issued December 2018
Refer to the QuickLIT website for the most up-to-date version of this document.
Applications
The VG1000 Series Ball V alves are designed to regulate the flow of hot or chilled water (and for some models, low
pressure steam) in response to the demand of a controller in HVAC systems.
IMPORTANT: Use the VG1000 Series Valves as an operating control. Where failure or malfunction of the
VG1000 Series Valve could lead to personal injury or property damage to the controlled equipment or other
property, additional precautions must be designed into the system. Incorporate and maintain other devices, such
as supervisory or alarm systems or safety or limit controls, intended to warn of or protect against failure or
malfunction of the VG1000 Series Valve.
Installation
Install VG1000 Series Ball Valves with the actuator at or above the centerline of the horizontal piping, as shown in
Figure 1.
IMPORTANT: In steam applications, install the valve with the stem horizontal to the piping. Failure to follow
these guidelines may shorten the life of the actu at or.
To minimize heat transfer in steam applications, wrap the valve and piping with insulation. Allow sufficient
clearance to remove the actuator (as illustrated in the dimension drawings, Figure 6 through Figure 11).
When mounting the actuator in the field (befo re installation ), use an adjustab le wrench to manu ally rotate the valve
stem several times. This rotation breaks the torque that may have built up during long-term storage.
For the valve to move in the proper direction, wire the input lines to the electric actuator correctly.
VG1000 Series Forged Brass Ball Valves Installation Instructions
s
o
p
t
n
m
:
G
I
F
1
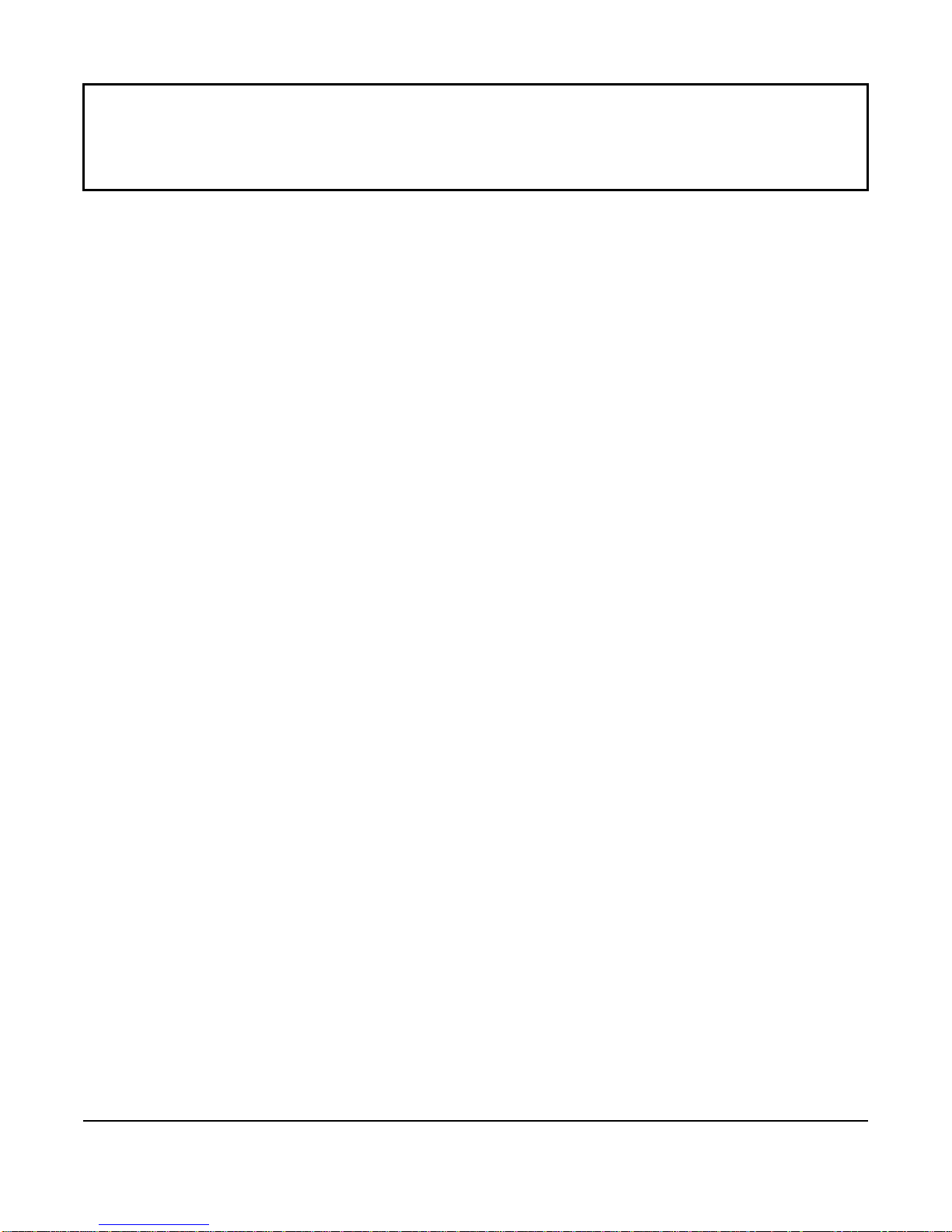
IMPORTANT: Take care to prevent foreign material such as weld slag, thread burrs, metal chips, and scale
from entering the piping system. This debris can damage or severely impede the operation of the valve by
embedding itself in the seats, scoring the valve, and ultim at ely resu ltin g in se at leaka g e. If the debr is be co me s
embedded in the seats, subsequent flushing and filtering of the piping system with the valve installed does not
remedy the problem.
For more detailed installation information about the specific equipment used, refer to the appropriate document
from the following list:
• VA9104-xGA-2S Series Electric Non-Spring Return Valve Actuators Installation Instructions
(Part No. 14-1336-15)
• VA9104-xGA-3S Series Electric Non-Spring Return Valve Actuators Installation Instructions
(Part No. 14-1336-23)
• M9102-AGA-2S and M9104-xGA-2S Series Electric Non-Spr ing Return Actuators Installation Instructions (Part
No. 34-636-1220)
• M9102-AGA-3S and M9104-xGA-3S Series Electric Non-Spr ing Return Actuators Installation Instructions (Part
No. 34-636-1433)
• VA9300 Series Electric Non-Spring Return Valve Actuators Installation Instructions
(Part No. 34-636-2421)
• VA9203 -AGx-2Z Series On/Off and Floating Point Electric Spring Return Valve Actuators Installation
Instructions (Part No. 14-1380-8)
• VA9203-Bxx-2 Series On/Off Spring Return Valve Actuators Installation Instructions
(Part No. 14-1380-16)
• VA9203-GGx-2Z Series Proportional Spring Return Valve Actuators Installation Instructions
(Part No. 14-1380-24)
• VA9208-AGx-x Series On/Off and Floating Point Electric Spring Return Valve Actuators Installation Instructions
(Part No. 14-1379-5)
• VA9208-Bxx-x Series On/Off Spring Return Valve Actuators Installation Instructions
(Part No. 14-1379-13)
• VA9208-GGx-x Series Proportional Spring Return Valve Actuators Installation Instructions
(Part No. 14-1379-21)
• M9000-560 Ball Valve Linkage Kit and M9000-561 Thermal Barrier Installation Instructions
(Part No. 34-636-2227)
• M9000-342 Series Weather Shield Enclosures Installation Instructions (Part No. 34-636 -2499)
• M9000-551 Ball Valve Linkage Kit Installation Instructions (Part No. 34-636-1816)
Note: To avoid excessive wear or drive time on the motor for VA9104 and M9104 models, use a controller or
software that provides a time-out funct ion to re mo ve the signal at the end of rotation (stall). The IGx and GGx
models have an auto shutoff to avoid excessive wear or drive time on the motor.
On models with the flow-characterizing disk, the disk is located in Port A. Port A must be the inlet. On three-way
models, use Port A as the coil inlet and Port B as the bypass inlet.
VG1000 Series Forged Brass Ball Valves Installation Instructions
2
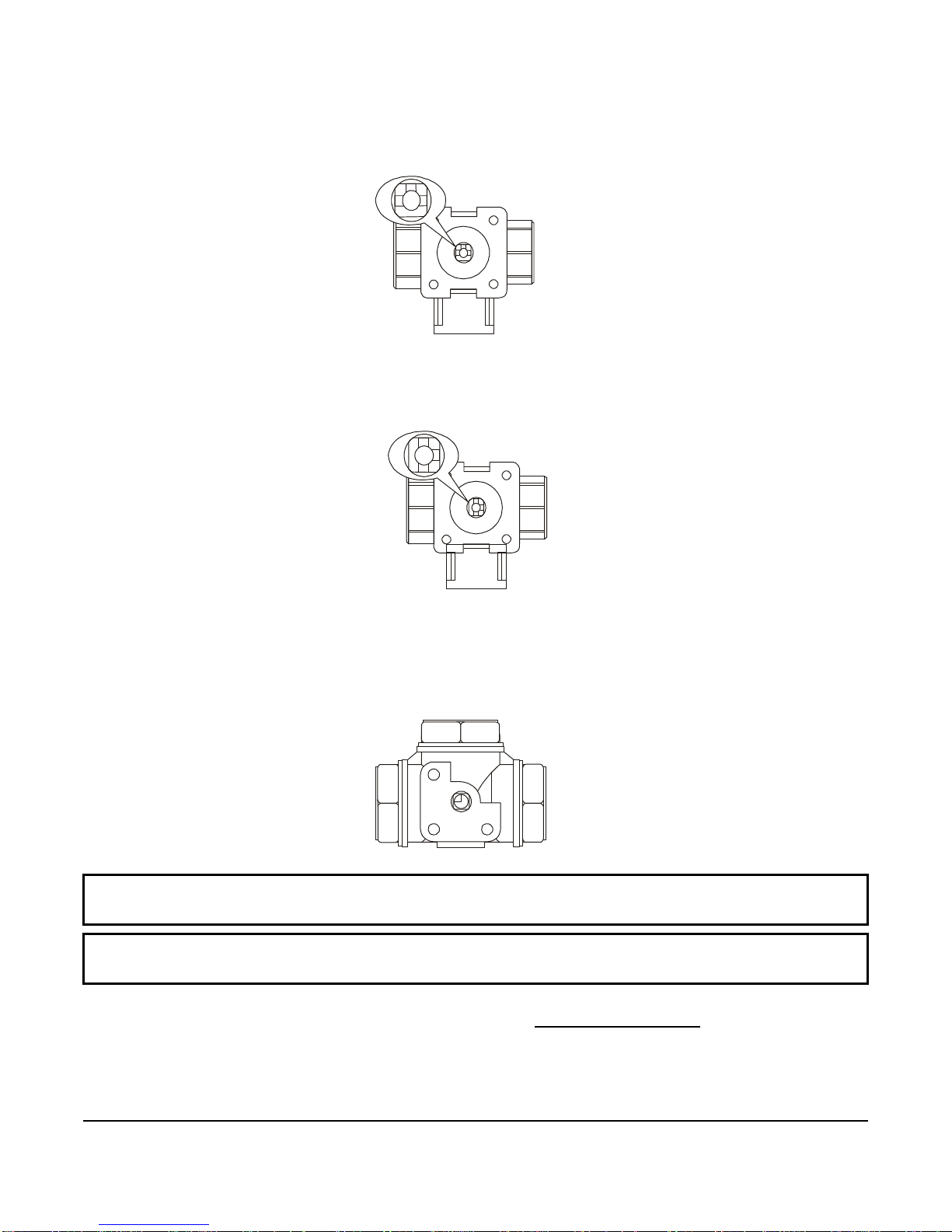
VG1841 and VG1845 Series Three-W ay Ball Valves have a different port configuration from VG1644 Series Three-
Figure 2: VG1841 or VG1845 Series ThreeWay Ball Valve (Port A Connected to Port C)
Figure 3: VG1841 or VG1845 Series ThreeWay Ball Valve (Port B Connected to Port C)
Port
Normally
Open Port
Normally
F
I
G
:
v
g
1
6
4
4
c
c
w
Figure 4: Top View of VG1644 Series Three-
Way Ball Valve (Actuator Fully
Way valves. See Figure 2, Figure 3, and Figure 4 for details.
Port C
Common
C
o
t
A
G
V
:
G
Port B Bypass
I
F
Port C
Common
IMPORTANT: Protect the actuator from dripping water, condensation, and other moisture. Water or moisture
could result in an electrical short, which may damage or affect the operation of the actuator.
IMPORTANT: Do not cover the actuator with thermal insulating material. High ambient temperatures may
damage the actuator, and a hot water pipe, steam pipe, or other heat source may overheat it.
Contact your local Johnson Controls® representative for compatibility concerns before using VG1000 Series Ball
Valves to control the flow of fluids other than those outlined in the Technical Specifications
Port B Bypass
Common
Closed Port
table in this document.
VG1000 Series Forged Brass Ball Valves Installation Instructions
3
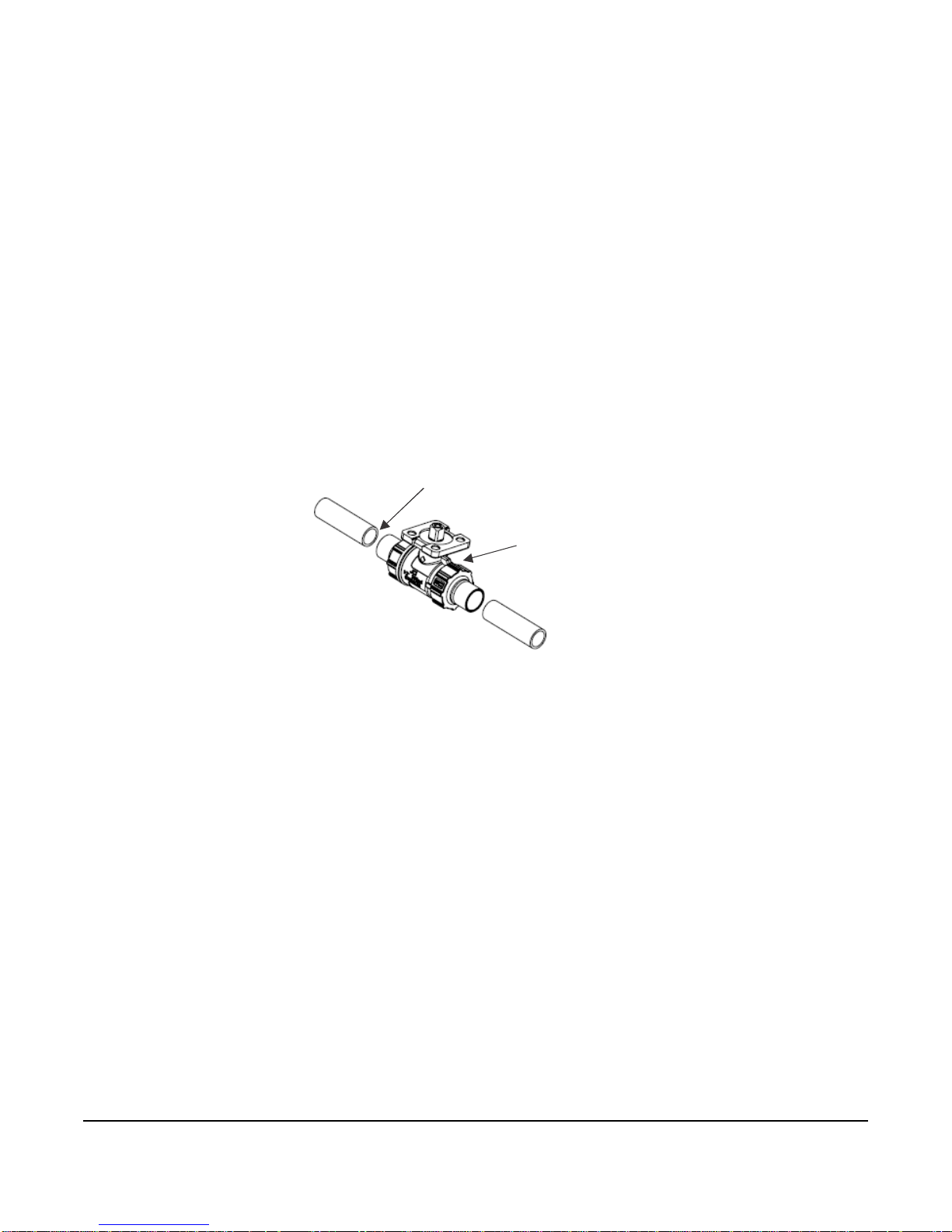
Press Valve Installation
Figure 5: Sweat Valve Installation
tempera tu r e soft solder.
the neck of th e valve.
FIG:sv_ins
VG1000 press end connection valves are installed using RIDGID® press tools. Always refer to the operator’s
manual supplied with the RIDGID press tool that is used to make the valve end connections. The manual should
provide proper instructions for the safe operation of the tool, proper crimping procedures, and methods of
inspecting the finished connection. If you use a battery-operated press tool, ensure its proper operation by fully
charging the unit. To avoid damage to the integral O-ring, never use sealant or pipe dope with a press connection.
Always inspect the end connections of the valve before making the connection. The end connection should not be
deformed, and the internal, integral O-ring must be in place for a proper seal.
Sweat Valve Installation
When soft soldering sweat ball valves, be sure to use a low temperature solder with a melting point that does not
exceed 450°F (232°C). For lead-free RoHS compliance, a 96.5% tin/3.5% silver solder is recommended. Never
install the actuator on the valve until you have completed the soldering operation and the valve body has cooled.
Before soldering, minimize the risk of damage to the ball seals by positioning the ball so that Port A is fully open.
When soldering, always apply a wet rag around the valve’s neck and cover as much of the valve body with the rag
as possible. Direct the tip of the flame away from the valve and always heat the copper tubing directly, but never
the valve body. Solder Port A first, then the remaining ports. These steps provide maximum protection to the
internal valve components. See Figure 5 for details.
Use only low meltin
Place a wet r ag around
t
VG1000 Series Forged Brass Ball Valves Installation Instructions
4