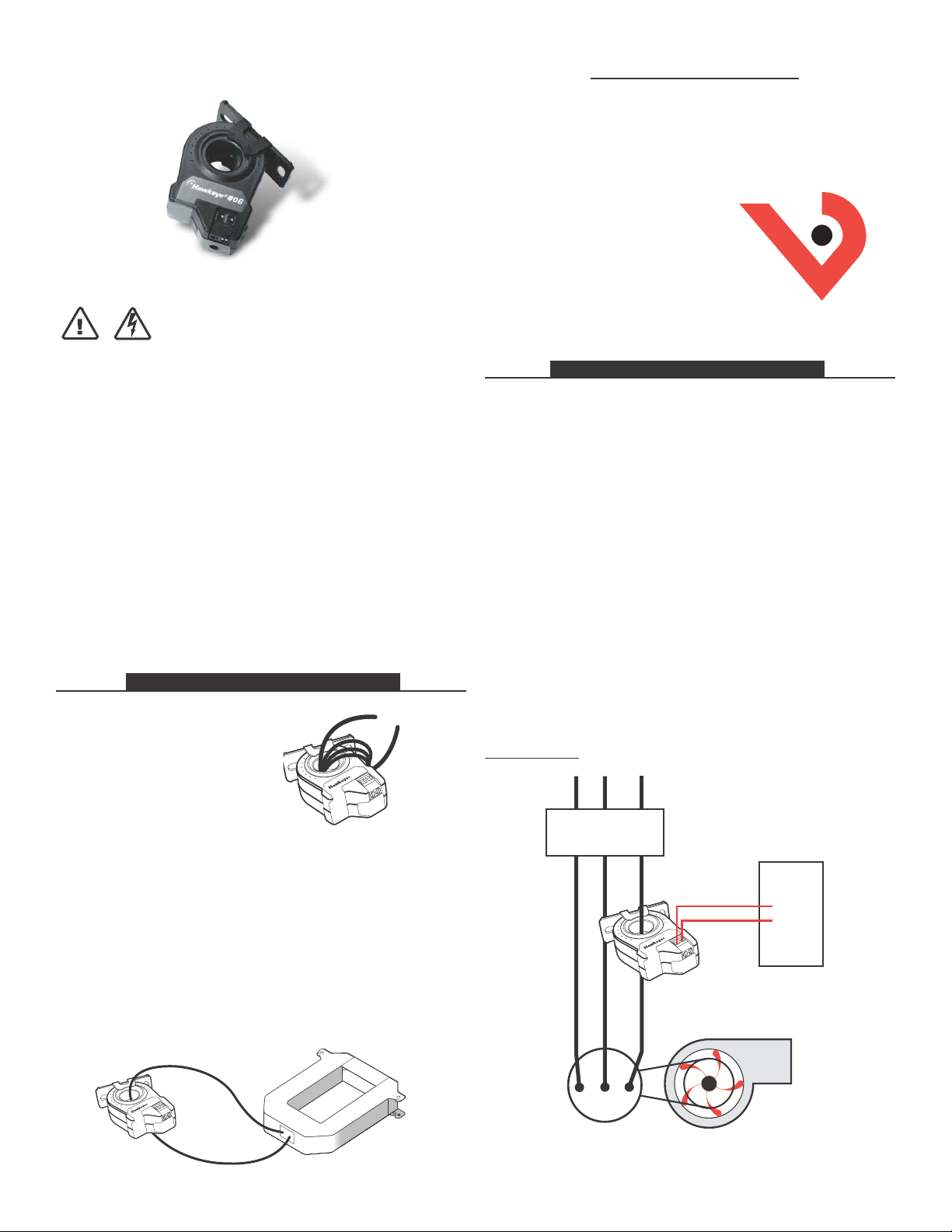
PORTLAND, OREGON USA
(503) 598-4564 FAX (503) 598-4664
1-800-354-8556
VERIS INDUSTRIES
http://www.veris.com email:sales@veris.com
®
Motor
Fan or Pump
DDC CONTROLLE
H806
Installation Instructions
H806
Mini Solid-Core Adjustable Current Switch
• This product is not intended for life or safety applications.
This product is not intended for installation in hazardous or classied
locations.
• Potential electrocution hazard exists. Installing sensors in an energized
motor control center or on any energized conductor can be hazardous.
• Read instructions thoroughly prior to installation.
Severe injury or death can result from electrical shock during contact with
high voltage conductors or related equipment. Disconnect and lock-out
all power sources during installation and service. Applications shown are
suggested means of installing sensors, but it is the responsibility of the
installer to ensure that the installation is in compliance with all national and
local codes. Installation should be attempted only by individuals familiar with
codes, standards, and proper safety procedures for high-voltage installations.
INSTALLATION
1. For currents less than .75 Amp:
To provide adequate current, wrap the
conductor through the center hole and
around the sensor body to produce multiple
passes and increase measured current.
• Measured current = Actual current times
the number of passes.
example: 4 passes
INSTALLATION
1. Ensure power conductor to be monitored is disconnected and locked out
from the power source!
2. Install the removable mounting bracket to the back of the electrical
enclosure.
3. Thread the monitored conductor through the sensor opening
and terminate.
Additional Information:
• To monitor current under .75 Amp please see installation note #1.
• To monitor current above 50 Amps please see installation note #2.
4. Connect current switch output to DDC controller or switched load.
Additional Information:
A. 5 VDC or more are required for the contact to be in the Normally
Closed position.
5. Calibrate the sensor (see calibration section)
WIRING EXAMPLE
2. For currents greater than 50 Amps:
In order to monitor currents greater than 50 Amps, a 5 Amp current
transformer may be used. Run the CT secondary wire through the current
sensor. Terminate the two secondary wires of the 5 Amp CT to each other.
Then install the 5 Amp CT (H6800 Series) on the conductor being monitored.
CAUTION: CT’s can contain hazardous voltages. Install CT’s in accordance
to manufacturers specications and instructions. (Terminate the
secondary CT before applying current through it.)
Z101762-0D
H6800-5A CT
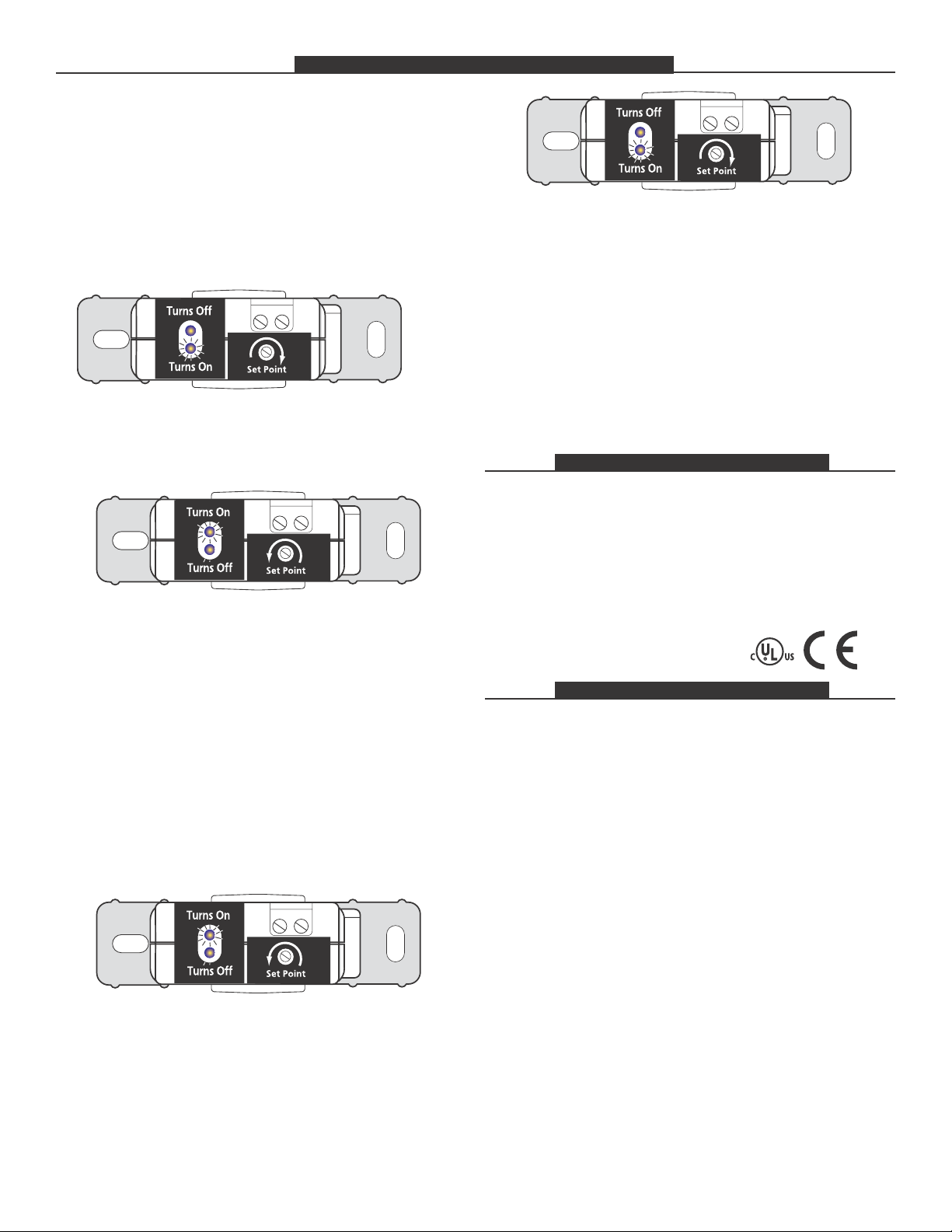
CALIBRATION AFTER INSTALLATION
Orient the current switch so the status output terminal is facing you and
follow method (A) (undercurrent) or (B) (over-current), below. The monitored
motor must be running normally.
A. For under current status indication: (Belt loss, coupling shear, fan &
pump status)
STEP 1: Turn the setpoint screw clockwise until the Status Open LED turns
o and the Status Closed LED turns on.
STEP 2: Slowly turn the setpoint screw counter-clockwise until the Status
Closed LED turns o and the Status Open LED turns on.
STEP 3: Turn the setpoint screw counter-clockwise 1/4 turn more to create
a grace margin.
STEP 2: Turn the setpoint screw clockwise until the Status Open LED turns
o and the Status Closed LED turns on.
STEP 3: Turn the setpoint screw clockwise 1/4 turn more to create a grace
margin.
The sensor is now calibrated to provide indication of current ows above
normal full load amps
Output Status:
Normal: Output Closed
Alarm: Output Open
SPECIFICATIONS
Amperage Range.......................... .75-50A Continuous
Sensor Supply Voltage.................. Induced from monitored conduc tor
Isolation........................................ 600VAC rms. (max. voltage when monitoring an
uninsulated conductor)
Temperature Range...................... -15º to 50ºC
Humidity Range ........................... 0-95% non-condensing
Status Output Ratings .................. N.C. 0.1A@5-30VDC polarit y sensitive
O-state Leakage (max.) .............. 24ua@5VDC, 143ua@30VDC
Onstate Voltage Drop ................... 1.7VDC (max.)@0.1A
Listings ......................................... UL508 E150462
The sensor is now calibrated to provide indication of current ows below
normal full load amps.
Output Status:
Normal: Output Open
Alarm: Output Closed
B. For over current status indication: (Locked rotor, seized impeller)
STEP 1: Turn the setpoint screw counter-clockwise until
the Status Closed LED turns o and the Status Open LED turns on.
TROUBLESHOOTING
1. The unit will not come on at all.
A. Check to be sure that no more than 30VDC or 0.2A has passed through
the contact. Voltages or currents above these levels will damage the unit.
B. Verify that the conductor you are monitoring is carrying at least 1.0
Amps. If the sensor is monitoring less than .75 Amp, employ installation
note #1 (pg. 1)
C. Verify that the setpoint is not above operating amps by turning screw
counter-clockwise (up to 20 full turns) until the contacts close (status
closed LED turns on).
D. Verify that at least 5VDC are across the contacts. The device will be
Normally Closed only if at least 5VDC are present.
E. Verify that polarity is correct.
2. Set-point screw has no stops. Keeps turning.
A. The 20 turn set-point screw has a slip clutch which prevents damage
at either end. To start the calibration process over again turn the screw 20
full turns counter-clockwise. This sets the device in its original and most
sensitive position. Resume calibration from the beginning.
3. Both LED’s are lit.
A. If the setpoint screw has been turned too far to the right the user will
be notied that the current switch is out of calibration by seeing both
LED’s lit. To correct this, turn the set-point screw 20 full turns
counter-clockwise and resume calibration from the beginning.