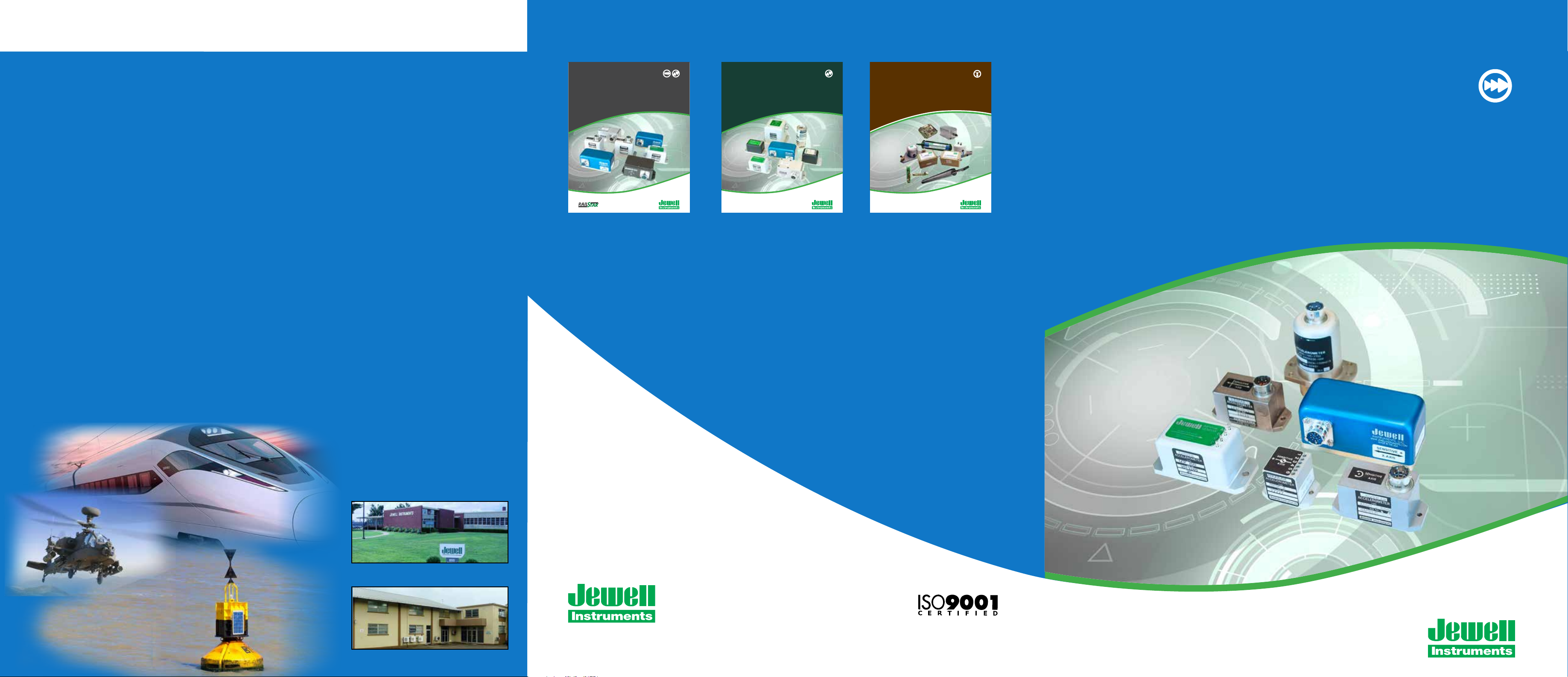
Reliable, HigH PeRfoRmance PRoducts — excePtional seRvice
FEATURING: Precision Linear & Angular Accelerometers
All Jewell force-balanced (servo) precision accelerometers are fully self-contained. They connect to a DC power source
and a readout or control device for a complete operating system. The output is a high-level DC signal proportional to
acceleration and tilt angle sine from as little as ±0.010g to ±20g full range. Jewell precision accelerometers respond
to change in velocity as small as 1µg. Hysteresis is less than 0.0005% of full range output and vibration rectication
is less than 50µG/G2 are available. Review the products in this guide for more information.
Other Product Groups Available:
Force-Balanced Precision Accelerometer & Inclinometer
Rail Transportation Selector Guide
Force-Balanced Precision Inclinometer
Selector Guide
Electrolytic Tilt Sensors and Accessories
Selector Guide
Force-Balanced Precision Accelerometer
Selector Guide
Custom ApplicationSpecific Solutions
Jewell Instruments provides both
standard and custom solutions
for a diverse group of industries,
such as aerospace, medical,
industrial, telecommunications, and
rail markets. We manufacture our
components completely in-house
and work directly with our clients,
maintaining control over the entire
development processes. Our legacy
of experience and success, and
the expertise of our engineering
team, mean customers benet
from extensive resources at their
disposal.
Connecting Experience,
Quality & Expertise
For over 60 years, Jewell
Instruments has provided
commercial and industrial sensors
and controls, meters and avionics,
and industrial test equipment
solutions to a range of global
markets. Our ISO 9001:2008
certication ensures that our
customers receive products and
systems with the dependability and
reliability that their applications
demand. Jewell Instruments’
experienced engineering team
works with customers to produce
high quality, reliable products that
meet or exceed their requirements.
Exceptional
Customer Service
We specialize in reliability, value
and responsiveness. Cooperation
and joint planning between
our engineering groups and
our clients drive our customer
care experience. We work as
an extension of our customers’
engineering and manufacturing
teams to solve problems, improve
applications, shorten leadtimes and bring more value to
their products and services.
Superb customer support is
the cornerstone of our many
successful, long-term customer
relationships.
Rail Transportation
Selector Guide
Force-Balanced Precision
Inclinometer Selector
Guide
Jewell Instruments is a world leader in the manufacture and
distribution of panel meters, avionics components, inertial
sensors, and precision solenoids. From sales and design,
manufacturing and testing, and delivery and support, Jewell
Instruments offers complete customer care and engineering
expertise. We also offer two, fully modernized manufacturing
facilities, one in Manchester, New Hampshire and one in
Barbados, West Indies to handle the most stringent manufacturing
requirements with a cost-competitive advantage.
Electrolytic Tilt Sensors
and Accessories Selector
Guide
Jewell Facilities
Jewell offers two, fully modernized
manufacturing facilities, one in
Manchester, New Hampshire and
one in Barbados, West Indies.
Manchester Facility
Barbados Facility
Distributed By:
www.jewellinstruments.com
© 2013 Jewell Instruments LLC | 850 Perimeter Road | Manchester, NH 03103 | 603-669-6400
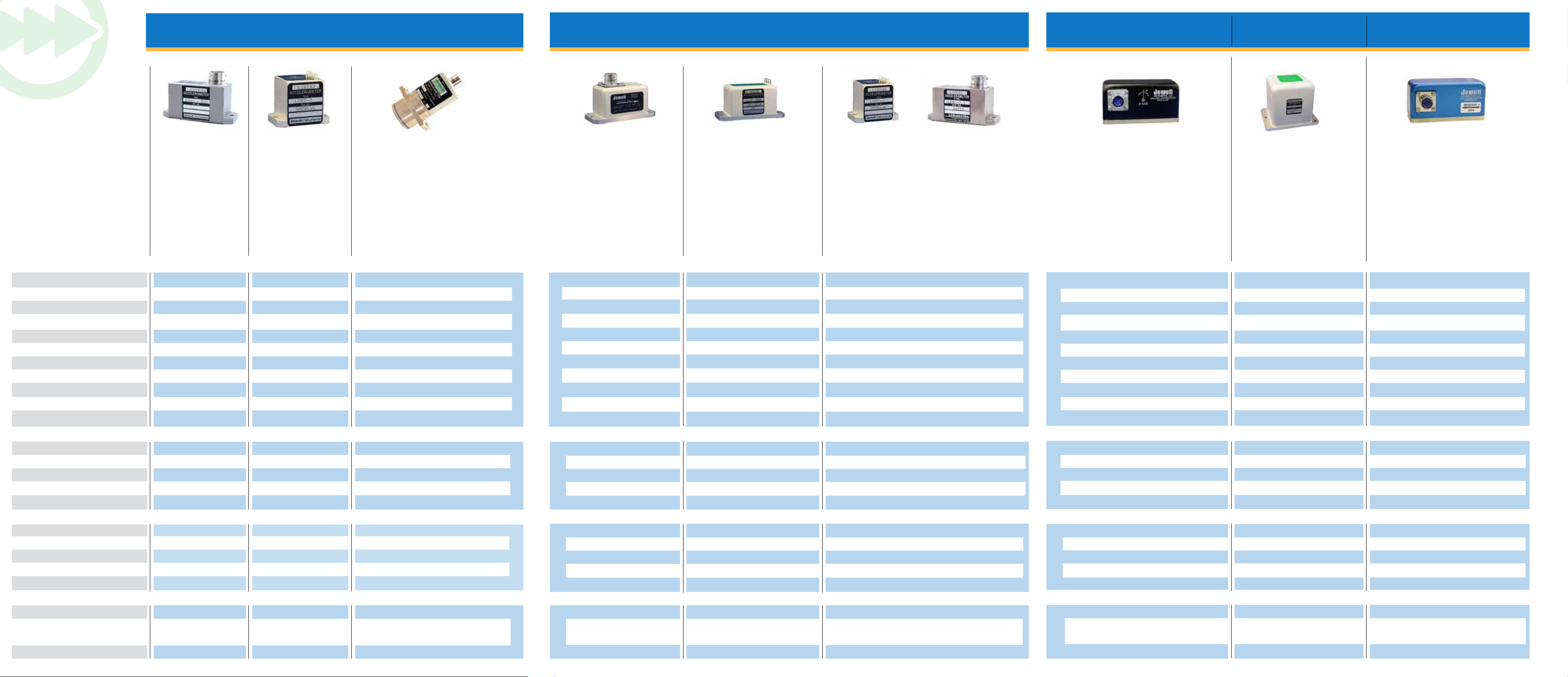
Angular Accelerometers
Linear Accelerometers
Dual Axis
Accelerometers
Triple Axis
Accelerometers
Digital
Accelerometers
Features & Benets
Applications
ASB Series
• Bandwidths to 200 Hz
• IP68 Seals
• Available 28V Aircraft Input
• Connector or Pin Cong
• Aerospace Quality and
Reliability
• Antenna Stabilization
• Motor Torque Measurement & Control
• Vehicle Ride Analysis
• Autopilot System Input
• Optical System Stablization
ASMP Series ASXC Series
• Bandwidths to 200 Hz
• 1.05" Cube Housing Size
• ±15 Standard Input Voltage
• Aerospace Quality &
Reliability
• Motor Torque Measurement & Control
• Automotive Angular
Acceleration Testing
• Autopilot System Input
• Optical System Stablization
• Standard Ranges 2 to 100 rad/sec2
• Resolution Better than 0.001 rad/sec2
• Very High Output to Size Ratio
• Self-test for Greater than 95% Fail Detect
• -30°C to 70°C Operating Temperature
Range
• Aircraft Stability Augmentation
• Racecar Performance Testing
• Camera Angular Motion Stabilization
• Autopilot System Input
• Rotating System Performance Testing
• Weapons Control Targeting
Performance Specs
Input Range (Ang: rads/sec2, Lin: g) ±200 ±500 ±1000 ±200 ±500 ±1000 ±2 ±10 ±20 ±50 ±100
Full Range Output (FRO V± 1.0%) ±5.0 ±5.0 ±5.0 ±5.0 ±5.0 ±5.0 ±5.0 ±5.0 ±5.0 ±5.0 ±5.0
Non Linearity (%FRO’ Max.) 0.5 0.2 0.1 0.5 0.2 0.1 1.0 1.0 1.0 1.0 1.0
2,
Scale Factor (Ang: V/rad/sec
Scale Factor Temp Sens (% reading, PPM/°C, Max.) 0.09 0.09 0.09 0.09 0.09 0.09 0.09 0.09 0.09 0.09 0.09
Bias (Ang: rad/sec², Lin: g, Dig: g, Max.) ±1.0 ±4.0 ±4.0 ±1.0 ±4.0 ±4.0 ±.005 ±.020 ±.030 ±.080 ±.100
Bias Temp Sens (FRO, PPM/°C, mg, Max.) ±0.05 ±0.05 ±0.10 ±0.40 ±0.40 ±0.40 ±0.001 ±0.001 ±0.001 ±0.001 ±0.001
Bandwidth (-3db) (Hz, Nom.) 70 100 120 70 100 120 100 150 200 17 0 170
Damping Ratio (Nom) 0.6 0.6 0.6 0.6 0.6 0.6 0.9 0.9 0.9 0.9 0.9
Transverse Axis Misalignment (°, Max.) ±1.0 ±1.0 ±1.0 ±1.0 ±1.0 ±1.0 ±0.025 ±0.025 ±0.025 ±0.025 ±0.025
Resolution and Threshold (rad/sec
Lin: V/g, Nom.) 0.025 0.010 0.005 0.025 0.010 0.005 5.000 1.000 0.500 0.200 0.100
2
, µg, Max.) 0.005 0.005 0.005 0.004 0.010 0.020 0.001 0.001 0.002 0.005 0.010
LCA-100 Series
• Built-in Output Filter
• DO-160 Quality Versions
• Available 28V Aircraft Input
• Connector or Pin Cong
• 0.20% 10-year Scale Factor
• Aircraft Flight Controls
• Aircraft Fatigue Monitoring
• Aircraft Autopilot System Input
• Aircraft Wind-shear Detect
• Double Integrated Railcar Pos
• Train Performance Testing
±0.5 ±1.0 ±2.0 ±5.0 ±0.5 ±1.0 ±2.0 ±5.0 ±0.5 ±1.0 ±2.0 ±5.0 ±10.0 ±20.0
±5.0 ±5.0 ±5.0 ±5.0 ±5.0 ±5.0 ±5.0 ±5.0 ±5.0 ±5.0 ±5.0 ±5.0 ±5.0 ±5.0
0.05 0.05 0.05 0.02 0.05 0.05 0.05 0.02 0.05 0.05 0.05 0.10 0.50 0.25
10.0 5.0 2.5 1.0 10.0 5.0 2.5 1.0 10.0 5.0 2.5 1.0 0.5 0.25
180 180 180 180 100 100 100 100 200 200 200 200 200 200
±0.01 ±0.01 ±0.01 ±0.01 ±0.005 ±0.005 ±0.005 ±0.005 ±0.050 ±0.010 ±0.010 ±0.010 ±0.020 ±0.050
100.0 100.0 100.0 100.0 50.0 50.0 50.0 50.0 50.0 50.0 50.0 100.0 100.0 100.0
60 60 60 60 30 30 30 30 70 100 140 100 140 160
- - - - - - - - 0.5 to 0.9
±0.71 ±0. 71 ±0.71 ±0.71 ±0.71 ±0.71 ±0. 71 ±0.71 ±0.71 ±0. 71 ±0.71 ±0. 71 ±0. 71 ±0. 71
10.0 10.0 10.0 10.0 1.0 1.0 1.0 1.0 10.0 10.0 10.0 10.0 20.0 50.0
LCF-200 Series LSM Series LSB Series
• ±0.5g to ±5.0g Full Range
• Filtering 5 to 100 Hz Bandwidth
• Exceptional Bias and
Scale Factor
• High Level ±V dc Output
• 1,500g Shock Capability
• Geophysical Testing
• Railcar Accel/Decel Control
• Ocean Buoy Accel Sensing
• Aircraft Stability Control
• Aircraft Flight Testing
• Vehicle Roadway Proling
• ±0.5g to 20g Full Range
• Filtering to 200 Hz Bandwidth w/0.6 Damping
• Satellite Application Reliability
• Better than 20µg Resolution at 10g Full Scale
• -55ºC to +95ºC Operating Temperature Range
• Satellite Nutation Sensing
• Radar Leveling
• Fire Control
• AHRS System Input
• Attitude Heading and
Reference System
• Train Braking & Banking
• Missile Orientation
• Autopilot Systems
• Train Performance Testing
• Performance Testing
LCF-2530
• ± 0.25 g to ± 5.0 g Full Range
• Dual Axis Version of LCF-Series
• High Accuracy and Superior Repeatability
• -40°C to +80° C Operating Temp Range
• Satellite Nutation Sensing
• Train Braking and Banking
• Performance Testing
• Attitude Heading and Reference Systems
• Autopilot
± 0.25 ± 0.50 ± 1.00 ± 2.00 ± 5.00 ±0.5 ±2.0 ±5.0 ± 0.25 ± 0.50 ±.87 ± 1.00 ± 2.00
± 5.0 ± 5.0 ± 5.0 ± 5.0 ± 5.0 ±5.0 ±5.0 ±5.0 ± 0.25 ± 0.50 ±.87 ± 1.00 ± 2.00
0.02 0.02 0.02 0.05 0.10 0.05 0.05 0.05 0.02 0.02 0.03 0.05
20.00 10.00 5.00 2.50 1.00 10 2.50 1.00 0.05 0.05 0.05 0.05 0.05
100 60 60 100 100 100 100 100 100 100 100 100 100
±0.001 ±0.002 ±0.004 ±0.005 ±0.005 ±0.005 ±0.005 ± .005 ±.0008 ±.0008 ±.0008 ±.0008 ±.0008
0.001 0.0005 0.0003 0.0003 0.0003 100.0 100.0 100.0 90.0 90.0 90.0 90.0 90.0
30 30 30 30 30 30 30 30 30 30 30 30 30
- - - - - 30.0 30.0 30.0 - - -
±0.50 ± 1.00 ± 1.00 ± 1.00 ± 1.00 ±1.0 ±1.0 ±1.0 ±0.15 ±0.15 ±0.15 ±0.15 ±0.15
1.0 1.0 1.0 1.0 1.0 10.0 10.0 10.0 8.0 8.0 8.0 8.0 8.0
• ±0.5g to ±5.0g Full Range
• Filtering 5 to 100 Hz Bandwidth
• Exceptional Bias & Scale Factor
• High Level ± Vdc Output
• 1,500 Shock Capability
• Tri-Axis
• Geophysical Testing
• Railcar Acceleration
• Ocean Buoy Acel Sensing
• Aircraft Stability Control
• Vehicle Roadway Proling
• Tri-Axis Acceleration Applications
LCF-3500
& Deceleration Control
DXA-100/200 Series
• Digital Output
• Resolution 8 µg
• Mechanical Shock 1500 g 1msec ½ sine
• Industry Standard RS485 & RS422 Output
• High Precision and Performance
• Low Noise
• Radar/Antenna Control
• Structural Monitoring
• Linear Acceleration/Deceleration
Measuring
• Automatic Train Position Control
• Seismic Monitoring
• Track Leveling
Test Case
- -
Electrical
Number of Axis 1 1 1
Input Voltage (Vdc) ±15 to ±10
Input Current (mA, Nom.) ±10 ±10 ±25
Output Impedence (Ohms, Nom.) 10.0K 4.0K 5.0K 4.0K 4.0K 4.0K 100.0
Noise (Vms, Max.) 5.00 5.00 5.00 0.005 0.005 0.005 0.030 0.030 0.050 0.050 0.050
±12 to ±18 ±15 to ±10
Environmental
Operating Temperature Range -55°C to +95°C -55°C to +95°C -30°C to +70°C
Survival Temperature Range -65°C to +105°C -65°C to +105°C -40°C to +70°C
Vibration - - -
Shock 100g, 11msec, 1/2 sine 100 g 100g, 11msec, 1/2 sine
Seal MIL-STD-202, Method 112 MIL-STD-202, Method 112 MIL-STD-202, Method 112
Mechanical
Weight 3.0 oz. 2.0 oz. 8.5 oz.
Dimensions 1.10" W x 2.60" L x 1.235" H 1.05" W x 1.50" L x 1.235" H 1.40" Dia x 2.97" L x 2.50" Flange W
1.657" Over Connector 1.39” Over Terminal Pins 3.44" Over Connector
Custom Ability Yes No Yes
1 1 1
±12 to ±18 ±12 to ±18 ±12 to ±18
±25 ±15 ±10
100.0 100.0 10.0K 5.0K 2.5K 5.0K 2.5K 2.5K
0.005 0.001 5.000
-55°C to +85°C -40°C to +80°C -55°C to +95°C
-60°C to +90°C --40°C to +90°C -65°C to +105°C
0 g 20 g 20 g
100 g 1000g, 1 msec, 1/2 sine 100 g, 0.011 sec, ½ sine
MIL-STD-202, Method 112 MIL-STD-202, Method 112 MIL-STD-202, Method 112
5.0 oz. 4.0 oz. LSB - 5.0 oz., LSB - 2.0 oz.
1.38" W x 3.10" L x 1.50" H 1.38" W x 3.10" L x 1.50" H 1.10" W x 2.60" L x 1.225" H (1.857" over connector)
1.05" W x 1.50" L (1.05" body) x 1.235" H (1.39" over pins)
No No LSM - Yes, LSB - No
2
±12 to ±18
±50
100.0
0.002
-40°C to +80°C
-60°C to +90°C
20 g
1000g, 1msec, 1/2 sine
MIL-STD-202, Mtd 112
8.0 oz.
3.609" L x 1.62" W x 1.83" H
Yes
3
±12 to ±18
±15
100.0
0.002
-40°C to +80°C
-60°C to +90°C
20 g
1000g, 1msec, 1/2 sine
MIL-STD-202, Mtd 112
16 oz.
3.25" L x 2.75" W x 2.75" H
Yes
1 or 2
±10 to ±30
DXA-100 ±80 mA/DXA-200 ±70 mA
-
0.005
-40°C to +70°C
-40°C to +75°C
20 g
1500g, 1msec, 1/2 sine
MIL-STD-202, Mtd 112
DXA-100 8 oz./DXA-200 10 oz.
3.609" L x 1.62" W x 1.83" H
Accelerometer Selector Guide
Yes