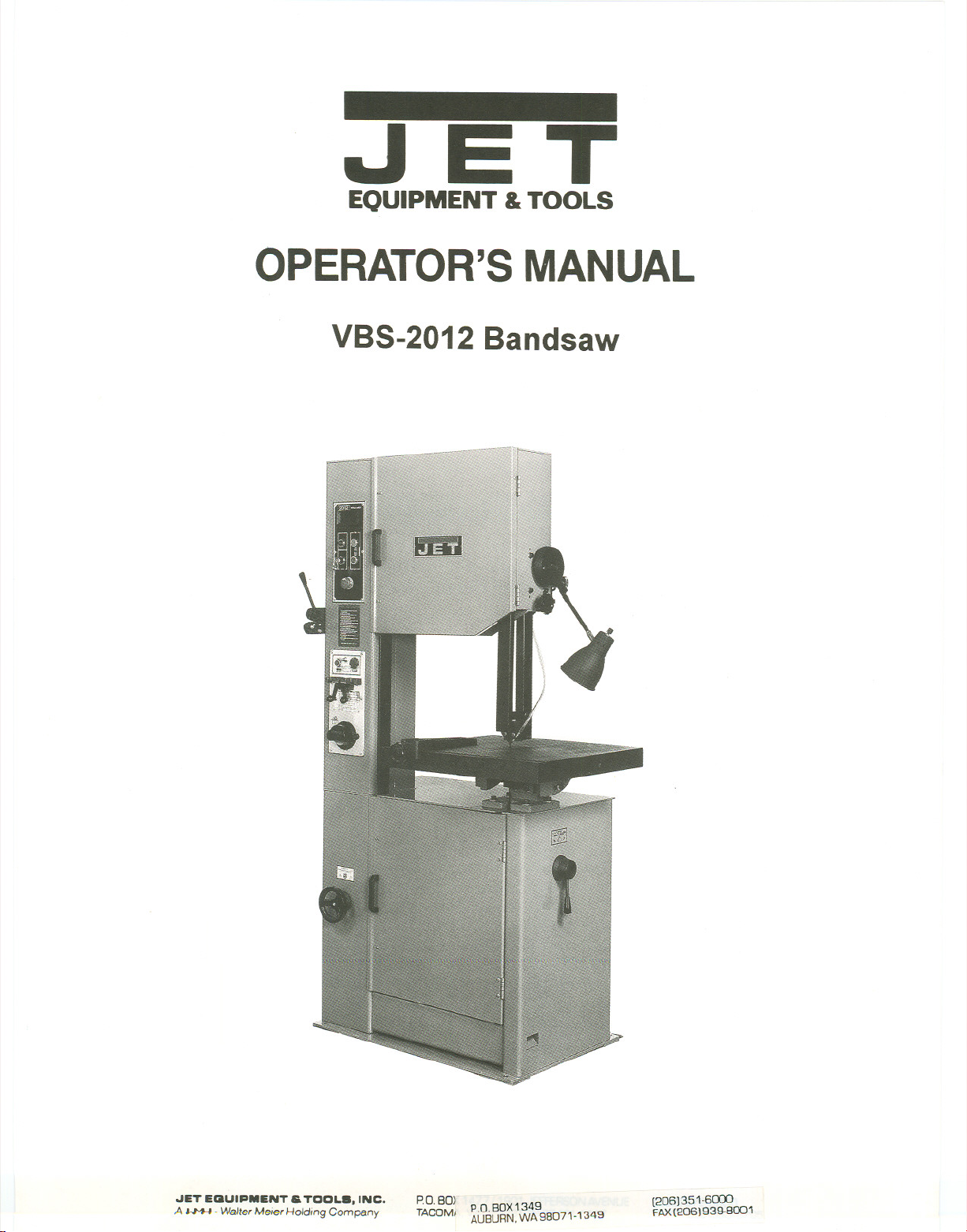
.JET
EQUIPMENT& TOOLS
OPERATOR'S MANUAL
VBS-2012 Bandsaw
..lETEcaUIPMENT a TOOLS, INC.
A ~ -WalterMeterHoldingCompany
po. 80)
TACOMI P.D.BOX1349
AUBURN.WA9B071-1349
(206) 351-6COJ
FA)«(206) 939-8001
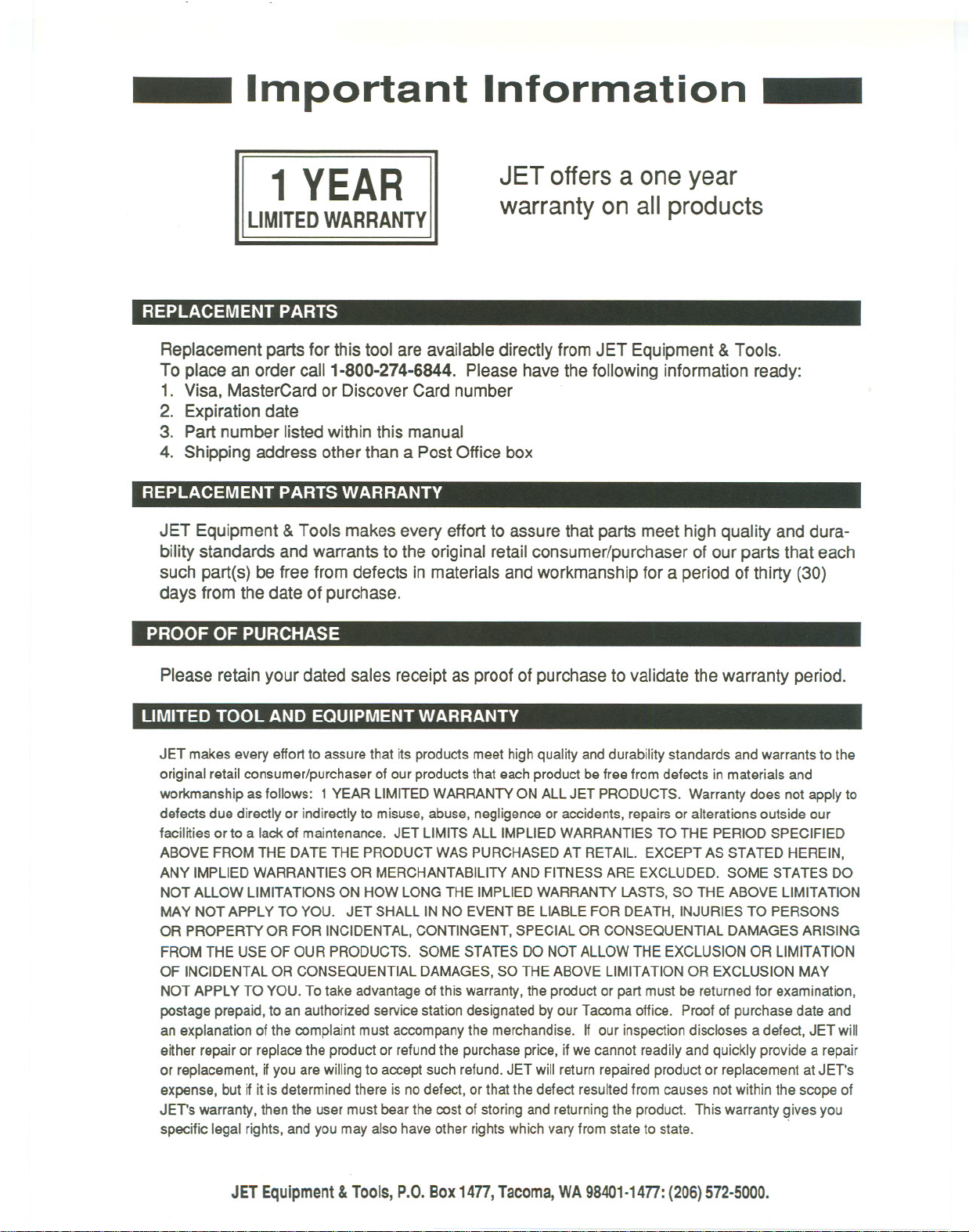
Il11portant Inforl11ation
1 YEAR
LIMITEDWARRANTY
JET offers a one year
warranty on all products
REPLACEMENT PARTS
Replacement partsfor this tool are available directly from JET Equipment & Tools.
To place an order call 1-800-274-6844. Please have the following information ready:
1. Visa, MasterCard or Discover Card number
2. Expiration date
3. Part number listed within this manual
4. Shipping address other than a Post Office box
REPLACEMENT PARTS WARRANTY
JET Equipment & Tools makes every effort to assure that parts meet high quality and dura-
bility standards and warrants to the original retail consumer/purchaser of our parts that each
such part(s) be free from defects in materials and workmanship for a period of thirty (30)
days from the date of purchase.
PROOF OF PURCHASE
Please retain your dated sales receipt as proof of purchase to validate the warranty period.
LIMITED TOOL AND EQUIPMENT WARRANTY
JET makes every effort to assure that its products meet high quality and durability standards and warrants to the
original retail consumer/purchaser of our products that each product be free from defects in materials and
workmanship as follows: 1 YEAR LIMITED WARRANTY ON ALL JET PRODUCTS. Warranty does not apply to
defects due directly or indirectly to misuse, abuse, negligence or accidents, repairs or alterations outside our
facilities or to a lack of maintenance. JET LIMITS ALL IMPLIED WARRANTIES TO THE PERIOD SPECIFIED
ABOVE FROM THE DATE THE PRODUCT WAS PURCHASED AT RETAIL. EXCEPT AS STATED HEREIN,
ANY IMPLIED WARRANTIES OR MERCHANTABILITY AND FITNESS ARE EXCLUDED. SOME STATES DO
NOT ALLOW LIMITATIONS ON HOW LONG THE IMPLIED WARRANTY LASTS, SO THE ABOVE LIMITATION
MAY NOT APPLY TO YOU. JET SHALL IN NO EVENT BE LIABLE FOR DEATH, INJURIES TO PERSONS
OR PROPERTY OR FOR INCIDENTAL, CONTINGENT, SPECIAL OR CONSEQUENTIAL DAMAGES ARISING
FROM THE USE OF OUR PRODUCTS. SOME STATES DO NOT ALLOW THE EXCLUSION OR LIMITATION
OF INCIDENTAL OR CONSEQUENTIAL DAMAGES, SO THE ABOVE LIMITATION OR EXCLUSION MAY
NOT APPLY TO YOU. To take advantage of this warranty, the product or part must be returned for examination,
postage prepaid, to an authorized service station designated by our Tacoma office. Proof of purchase date and
an explanation of the complaint must accompany the merchandise. If our inspection discloses a defect, JET will
either repair or replace the product or refund the purchase price, if we cannot readily and quickly provide a repair
or replacement, if you are willing to accept such refund. JET will return repaired product or replacement at JET's
expense, but if it is determined there is no defect, or that the defect resulted from causes not within the scope of
JET's warranty, then the user must bear the cost of storing and returning the product. This warranty gives you
specific legal rights, and you may also have other rights which vary from state to state. .
JETEquipment&Tools, P.O.Box1477,Tacoma,WA98401.1477:(206)572.5000.
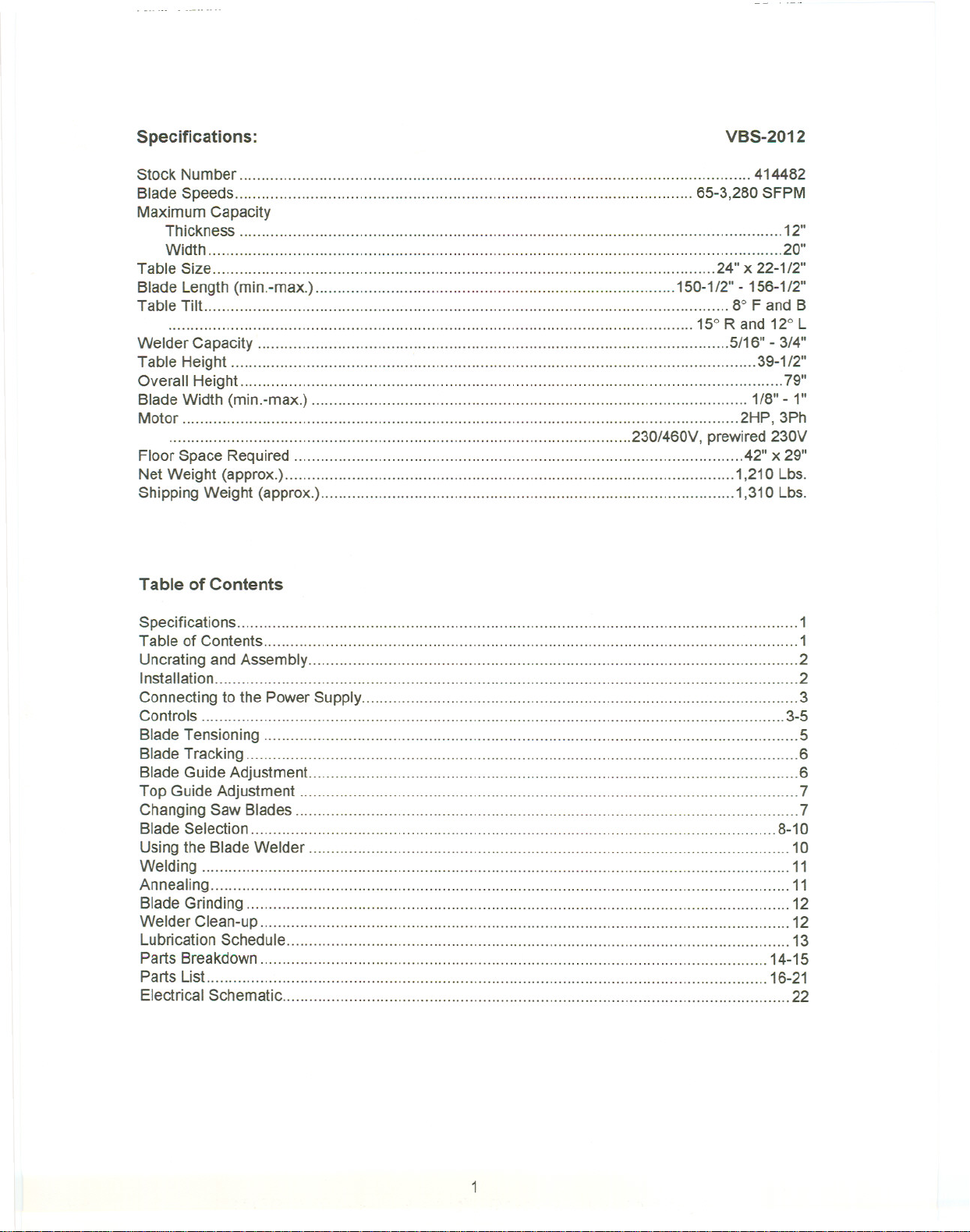
Specifications:
Stock Number.. 414482
Blade Speeds , 65-3,280 SFPM
Maximum Capacity
Thickness .12"
Width 20"
Table Size 24" x 22-1/2"
Blade Length (min.-max.) 150-1/2"- 156-112"
Table Tilt 8° F and B
, 15°Rand 12°L
Welder Capacity .5/16"- 3/4"
Table Height 39-1/2"
Overall Height ..79"
Blade Width (min.-max.) 1/8" - 1"
Motor 2HP, 3Ph
.230/460V, prewired 230V
Floor Space Required 42" x 29"
Net Weight (approx.) 1,210 Lbs.
Shipping Weight (approx.) 1,310 Lbs.
VBS-2012
Table of Contents
Specifications 1
Table of Contents 1
Uncrating and Assembly ., 2
Installation 2
Connecting to the Power Supply. ..., 3
Controls 3-5
Blade Tensioning ... ""'" 5
Blade Tracking 6
Blade Guide Adjustment 6
Top Guide Adjustment 7
Changing Saw Blades 7
Blade Selection .8-10
Using the Blade Welder. 10
Welding 11
Annealing 11
Blade Grinding ..12
Welder Clean-up .12
Lubrication Schedule 13
Parts Breakdown. 14-15
Parts List "'"'''''''''''''''''''''''''''''''''''''''''''''''''''''''''''''''''''''' 16-21
Electrical Schematic 22
1
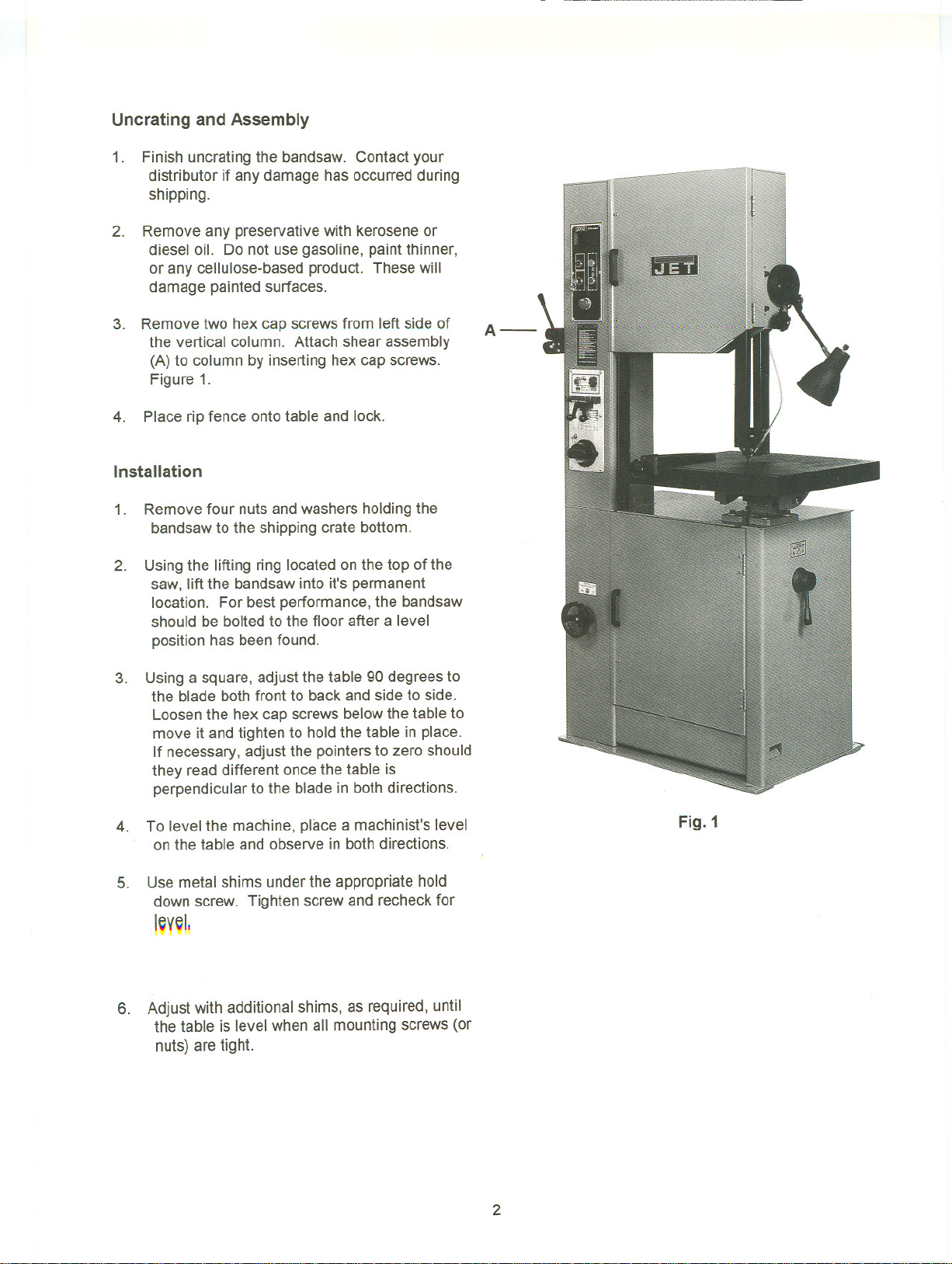
Uncrating and Assembly
1. Finish uncrating the bandsaw. Contact your
distributor if any damage has occurred during
shipping.
2.
Remove any preservative with kerosene or
diesel oil. Do not use gasoline, paint thinner,
or any cellulose-based product. These will
damage painted surfaces.
3. Remove two hex cap screwsfrom left side of
the vertical column. Attach shear assembly
(A) to column by inserting hex cap screws.
Figure 1.
4. Place rip fence onto table and lock.
Installation
1. Remove four nuts and washers holdingthe
bandsawto the shipping crate bottom.
2. Usingthe lifting ring located onthe top of the
saw, lift the bandsawinto it's permanent
location. For best performance, the bandsaw
should be bolted to the floor after a level
position has been found.
3. Using a square, adjust the table 90 degrees to
the blade both front to back and side to side.
Loosenthe hex cap screws belowthe table to
move it andtighten to hold the table in place.
If necessary, adjust the pointers to zero should
they read different oncethe table is
perpendicular to the blade in both directions.
A-
4. To level the machine, place a machinist's level
on the table and observe in both directions.
5. Use metal shims underthe appropriate hold
down screw. Tighten screw and recheck for
leveL
6. Adjust with additional shims, as required, until
the table is level when all mounting screws (or
nuts) aretight.
Fig. 1
2
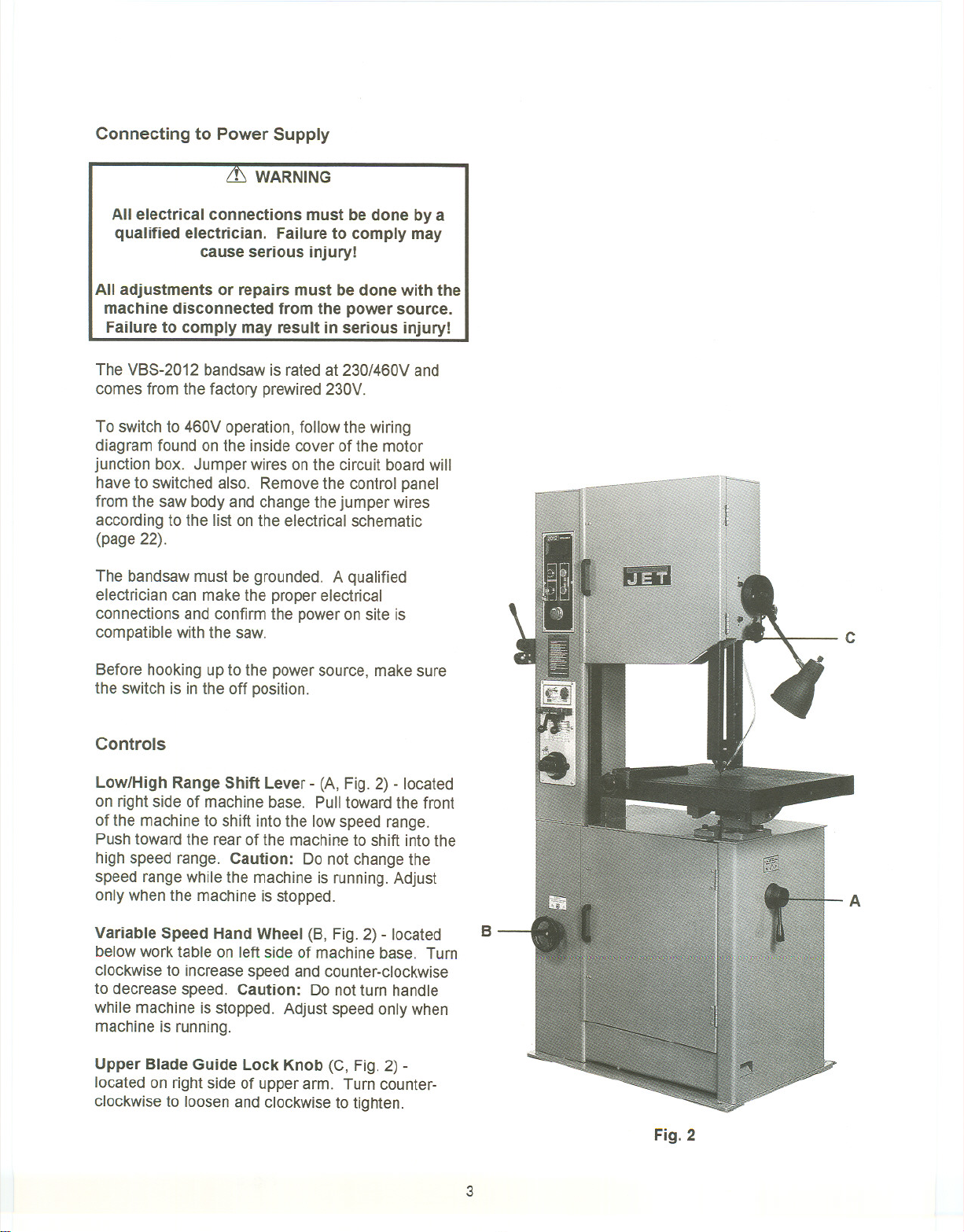
Connecting to Power Supply
fL WARNING
All electrical connections must be done by a
qualified electrician. Failure to comply may
cause serious injury!
All adjustments or repairs must be done with the
machine disconnected from the power source.
Failure to comply may result in serious injury!
The VBS-2012 bandsaw is rated at 230/460V and
comes from the factory prewired 230V.
To switch to 460V operation, follow the wiring
diagram found on the inside cover of the motor
junction box. Jumper wires onthe circuit board will
have to switched also. Remove the control panel
from the saw body and changethejumper wires
according to the list on the electrical schematic
(page 22).
The bandsaw must be grounded. A qualified
electrician can make the proper electrical
connections and confirm the power onsite is
compatible with the saw.
c
Before hooking up to the powersource, make sure
the switch is in the off position.
Controls
Low/High Range Shift Lever -(A,Fig.2) - located
on right side of machine base. Pull toward the front
of the machine to shift into the low speed range.
Push towardthe rear of the machine to shift into the
high speed range. Caution: Do not change the
speed range while the machine is running. Adjust
only when the machine is stopped.
Variable Speed Hand Wheel (B, Fig. 2) - located
below worktable on left side of machine base. Turn
clockwise to increase speed and counter-clockwise
to decrease speed. Caution: Do not turn handle
while machine is stopped. Adjust speed only when
machine is running.
Upper Blade Guide Lock Knob (C, Fig. 2)-
located on right side of upper arm. Turn counter-
clockwise to loosen and clockwise to tighten.
B
Fig. 2
3
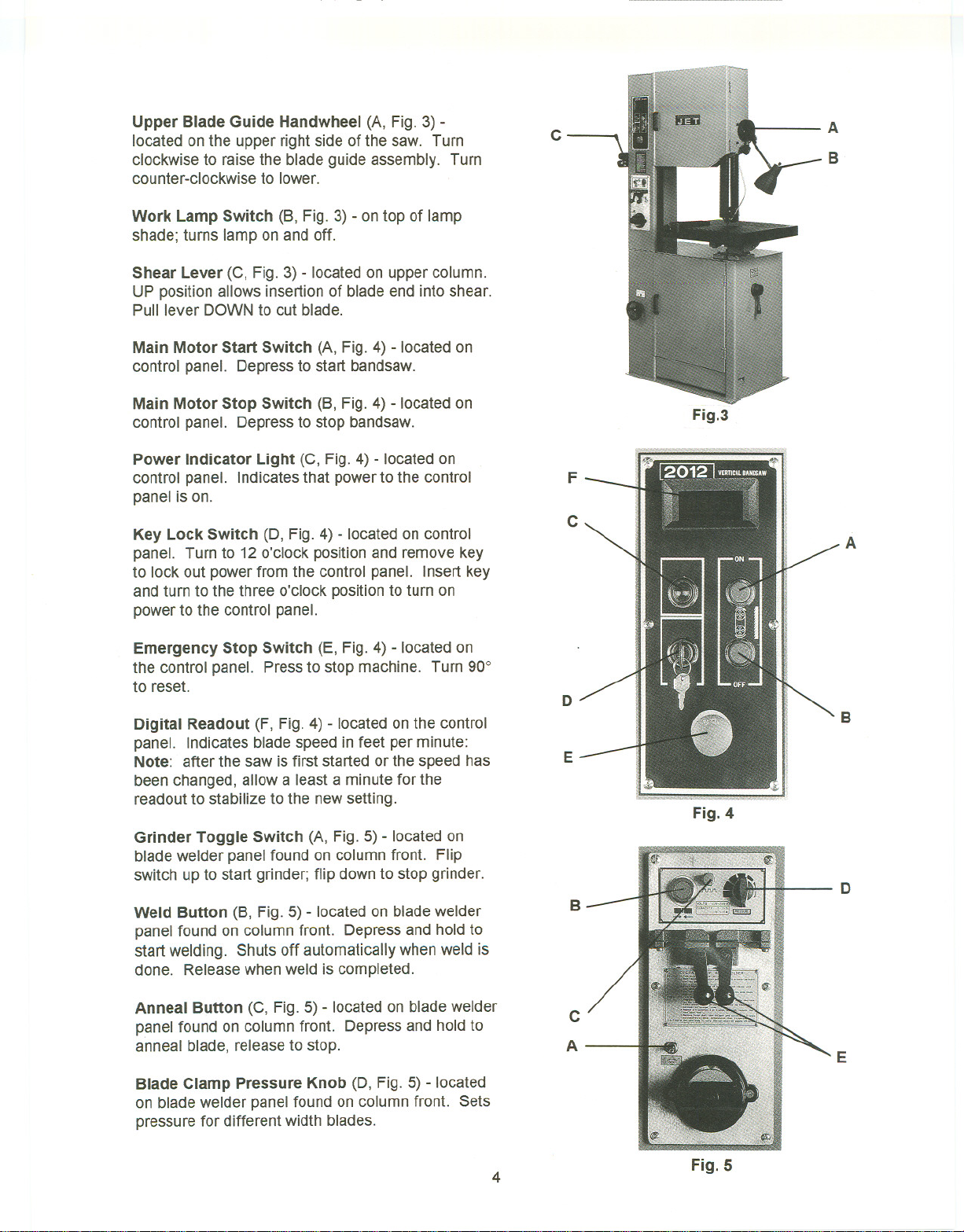
Upper Blade Guide Handwheel (A, Fig. 3) -
located on the upper right side of the saw. Turn
clockwise to raisethe bladeguide assembly. Turn
counter-clockwise to lower.
Work Lamp Switch (8, Fig. 3) - on top of lamp
shade; turns lamp on and off.
Shear Lever (C, Fig. 3) - located on upper column.
UP position allows insertionof blade end into shear.
Pull lever DOWN to cut blade.
Main Motor Start Switch (A, Fig. 4) - located on
control panel. Depressto start bandsaw.
C
A
B
Main Motor Stop Switch (8, Fig. 4) - located on
control panel. Depress to stop bandsaw.
Power Indicator Light (C, Fig. 4) - located on
control panel. Indicates that power to the control
panel is on.
Key Lock Switch (0, Fig. 4) - located on control
panel. Turn to 12 o'clock position and remove key
to lock out power from the control panel. Insert key
andturn to the three o'clock positionto turn on
powerto the control panel.
Emergency Stop Switch (E,Fig.4)- locatedon
thecontrolpanel. Pressto stopmachine.Turn90°
to reset.
Digital Readout (F, Fig.4) - located
panel. Indicates blade speed in feet per minute:
Note: after the saw is first started or the speed has
been changed, allow a least a minute for the
readoutto stabilize to the new setting.
on the control
Grinder Toggle Switch (A, Fig. 5) - located on
blade welder panel found on column front. Flip
switch up to start grinder; flip down to stop grinder.
Weld Button (8, Fig. 5) - located on bladewelder
panel found on column front. Depress and hold to
start welding. Shuts off automatically whenweldis
done. Releasewhen weld is completed.
Fig.3
F
C
A
D
B
E
Fig. 4
D
B
Anneal Button (C, Fig. 5)- located on blade welder
panel found on column front. Depress and hold to
anneal blade, release to stop.
Blade Clamp Pressure Knob (0, Fig.5) - located
onbladewelderpanelfoundoncolumnfront. Sets
pressurefordifferentwidthblades.
C
A
4
Fig. 5
E
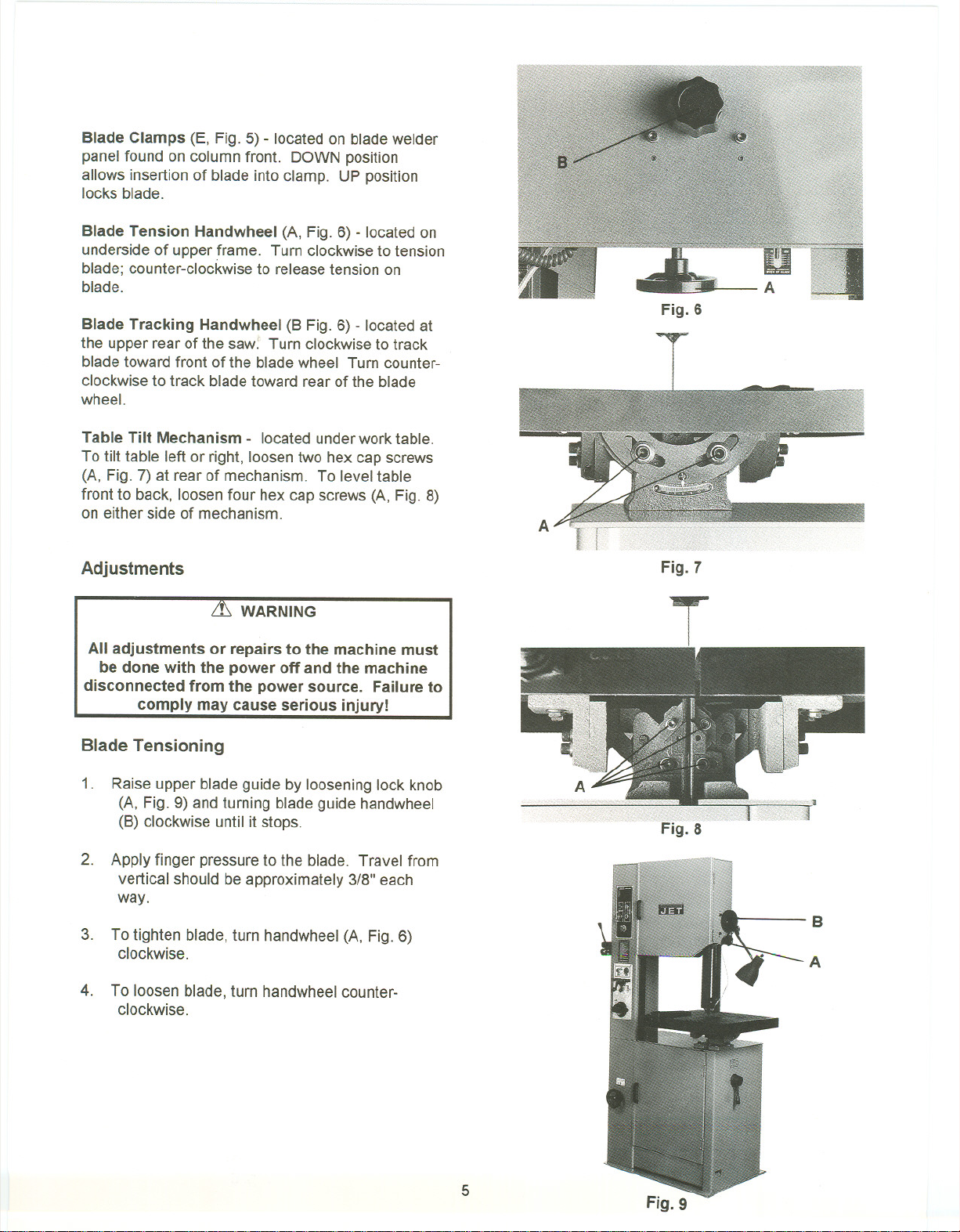
Blade Clamps (E, Fig. 5) - located on blade welder
panel found on column front. DOWN position
allows insertion of blade into clamp. UP position
locks blade.
Blade Tension Handwheel (A, Fig. 6) - located on
underside of upper frame. Turn clockwise to tension
blade; counter-clockwise to release tension on
blade.
Blade Tracking Handwheel (8 Fig.6) -locatedat
the upper rear of the saw~Turn clockwiseto track
blade toward front of the blade wheel Turn counter-
clockwise to track bladetoward rear of the blade
wheel.
Table Tilt Mechanism - located underworktable.
To tilt table left or right, loosentwo hex cap screws
(A, Fig. 7) at rear of mechanism. To level table
front to back, loosen four hex cap screws (A, Fig. 8)
on either side of mechanism.
Fig. 6
Adjustments
Lf'-, WARNING
All adjustments or repairs to the machine must
be done with the power off and the machine
disconnected from the power source. Failure to
comply may cause serious injury!
Blade Tensioning
1. Raise upper blade guide by loosening lock knob
(A, Fig. 9) andturning blade guide handwheel
(8) clockwise until it stops.
2. Apply finger pressure to the blade. Travel from
vertical should be approximately 3/8" each
way.
3. To tighten blade, turn handwheel (A, Fig. 6)
clockwise.
4. To loosen blade, turn handwheelcounter-
clockwise.
Fig. 7
B
A
5

5. Use the blade tension indicator (B, Fig. 10) as
reference only. Blade should betensioned
usingthe finger pressure method.
Blade Tracking
Blade tracking may be required from time to time
depending on the blade size and tension. The blade
must betensioned as outlined on page 5 under
"Blade Tensioning". Disconnectthe machine from
the power source and open both blade wheel doors.
Shift the high-low gear box lever into the neutral
position. Turn the upper bladewheel by hand while
observing blade position onthe upper bladewheel.
If adjustment is necessary:
1. Turn blade tracking knob (A, Fig. 10) clockwise
to track blade toward front of blade wheel.
2. Turn counter-clockwise to track blade toward
rear of blade wheel. Blade should betracked
as close to the center of the top blade wheel as
possible.
Note: Upper and lower blade guidesshould be
moved away and left loose from the blade
while tracking adjustments are being made.
Fig. 10
Blade Guide Adjustment
Lt CAUTION
Blade guides must be properly adjusted or
damage may occur to the blade and/or the
guides.
Lt WARNING
Air nozzle has been removed to show detail.
Always operate saw with the air nozzle in place
and properly adjusted. Failure to comply may
cause serious injury!
1. Loosen lock knob (A, Fig. 9) and turn blade
guide handwheel (B, Fig. 9) until blade guide
assembly is half way betweentable and head,
then tighten lock knob (A, Fig. 9).
2. Loosen screw (A, Fig. 11) andslide blade guide
assembly away from the blade until it stops.
Fig. 11
6
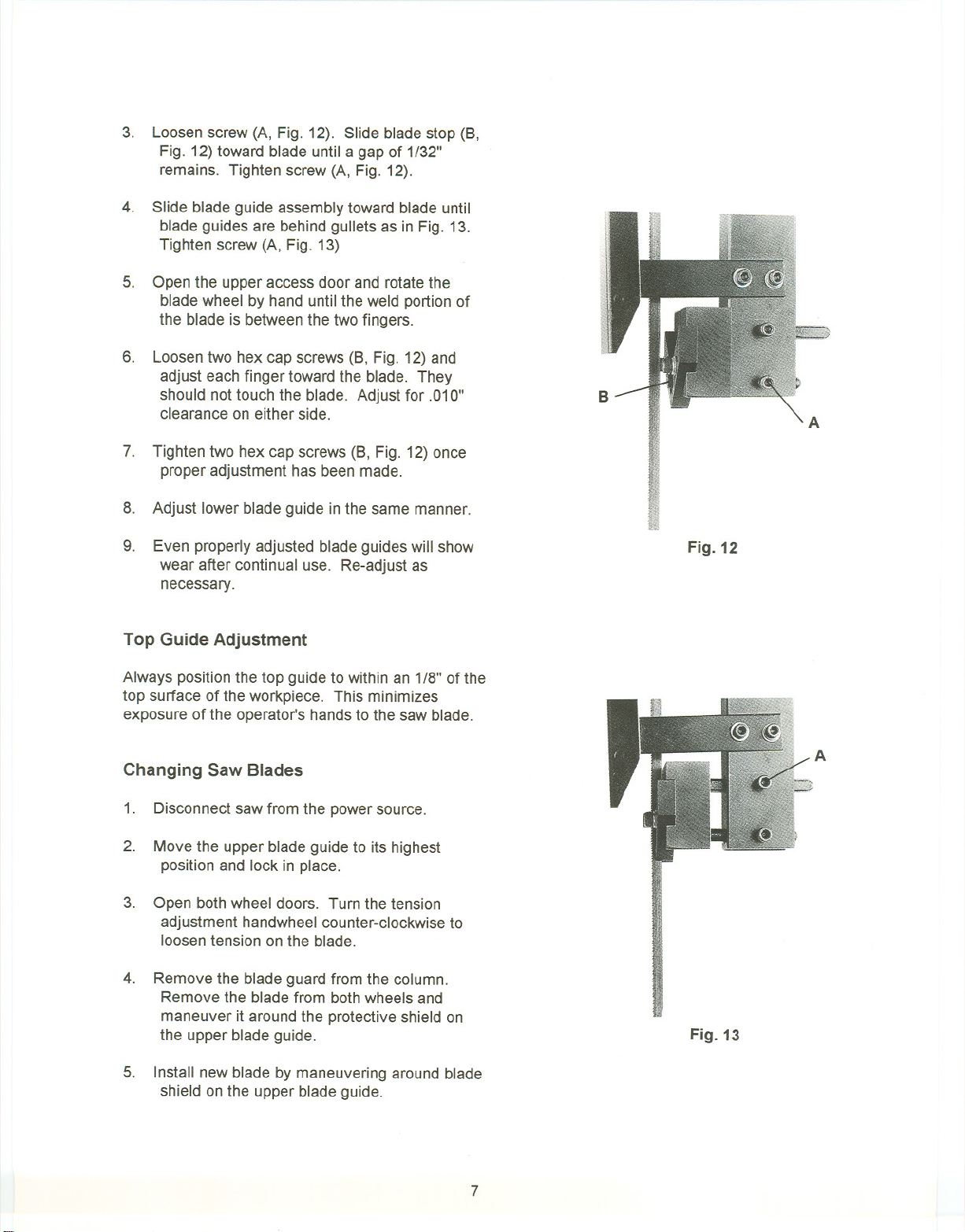
3. Loosenscrew (A, Fig. 12). Slide blade stop (B,
Fig. 12)toward blade until a gap of 1/32"
remains. Tighten screw (A, Fig. 12).
4. Slide blade guide assembly toward blade until
blade guides are behind gullets as in Fig. 13.
Tighten screw (A, Fig. 13)
5. Open the upper access door and rotatethe
blade wheel by hand until the weld portionof
the blade is betweenthe two fingers.
6.
Loosentwo hex cap screws (B, Fig. 12) and
adjust each finger toward the blade. They
should not touch the blade. Adjust for .010"
clearance on either side.
7. Tighten two hex cap screws (B, Fig. 12) once
proper adjustment has been made.
8. Adjust lower blade guide in the same manner.
9.
Even properly adjusted blade guideswill show
wear after continual use. Re-adjust as
necessary.
B
Fig. 12
Top Guide Adjustment
Always positionthe top guide to within an 1/8" of the
top surface of the workpiece. This minimizes
exposure of the operator's hands to the saw blade.
Changing Saw Blades
1. Disconnect saw from the power source.
2. Move the upper blade guide to its highest
position and lock in place.
3. Open both wheel doors. Turn the tension
adjustment handwheel counter-clockwiseto
loosen tension on the blade.
4. Remove the blade guard from the column.
Remove the blade from bothwheelsand
maneuver it aroundthe protective shield on
the upper bladeguide. Fig. 13
5.
Install new blade by maneuvering around blade
shield on the upper blade guide.
A
7

6. Place it betweenthe fingers of both blade
guides and onto both wheels. Position next to
both wheel flanges. Make sureteeth point
downtowardthe table.
7.
Be sure that blade rests against ball bearing (A,
Fig. 13), not behind it.
8. Replace blade guard on column.
9. Tension the saw blade by turning tension hand
wheel. Rotate the wheel by hand and make
sure the blade is properly seated in the blade
guides. Blade guides will have to be adjusted
if the replacement blade is a different type and
width.
Blade Selection
Proper blade selection isjust as important to band
saw operation as is blade speed and material feed.
Proper blade selection will impact blade life,
straightness of cut, cut finish, and efficiency of
operation. Excess blade breakage, stripping of
teeth, and waviness of cut are some of the results of
improper blade selection.
Fig. 13
Blades are classified by material composition, tooth
shape, pitch of teeth, and type of set, gage of the
band material, and kerf of the set (width of cut).
Material Composition
Carbon Steel - low cost, for use with non-ferrous
materials, wood, and plastics.
High Speed Steel - resists heat generated by dry
cutting. Used for ferrous metals and are more
expensive than carbon steel blades;
Alloy Steel - tough and wear resistant, cuts faster
with longer blade life. Used on hard materials.
More expensive than carbon or high speedsteel.
Carbide Tipped - for cutting unusual materials such
as uranium, titanium, or beryllium.
8

Tooth Shape
Note: When cutting thin materials, the rule for blade
pitch is to have a minimum of two teeth engaging
the material being cut at all times.
Standard Tooth - generally usedto cut ferrous
metals, hard bronze, hard brass, andthin metals.
Skip Tooth - have better chip clearance (larger
gullet) and are used on softer, non-ferrous materials
such as aluminum, copper, magnesium, and soft
brass.
Hook Tooth - provides a chip breaker and has less
tendency to gum up in softer materials. Used in the
same materials as skip tooth but can be fed faster
than standard or skip tooth blades.
Set Type
Straight Set - used for free cutting non-ferrous
materials; i.e., aluminum, magnesium, plastics, and
wood.
Wavy Set - used on materials of varying thickness
(pipe, tubing, and structural shapes).
RakerSet - used in large cuts on thick plate and bar
stock where finish of cut is not as important as
speed.
Gage
Blade gage is the thickness of material from which
the blade is produced. The thicker the material, the
stronger the blade will be.
Kerf
Kerf isthe width of a cut. Kerf will vary according to
set of bladeteeth.
Blade Width
The narrowerthe blade,the tighter the minimum
radius of cut will be. Always use the widest blade
possible for the job.
9

General rulesfor blade selection:
1.
Select coarser pitch blades for thicker or softer
material.
2.
Select finer pitch blades for thinner or harder
material.
3.
Use fine pitch blades to obtain a smooth finish.
4.
Use coarse pitch bladesto obtain faster cutting
speeds (thick material).
5.
To prevent premature blade wear, usethe
fastest practical speed.
6.
Adjust the feed rate to ensure continuous
cutting action.
Run the bandsawwith the blade centered in the
7.
upper and lower guides andthe gui<;lefingers
adjusted as close as possiblewithout touching
the blade or weldjoint.
LfS: WARNING
Po"t'on of Cut Rolot'vo
to Tho Gullot of tho
Tooth Tooth G,ound Moo Con,umOd
'/2 TO°
h 112 Tooth
. --- . ~---~00.A.I)
" 'LL-J ~
[jtj
Po,it'on of Cut Rolotivo 4 Pitch
i~o;~o GUII~ tho '-'/2 Tooth Goound A,oo Con,umed
3/4T°Ftrfioth ~ ~ '" r.'ByWolding.
, ~', ---I_jJ LJ - - -1'nM
po,it'on of Cut " 'n 6 Pitch
Tho Canto, of tho
Gullet. -.. 2 Toeth G'ound A,oo Consumed
'TOO~O:_~~ :~ByWolding.
. I';::°ff ~ I-By Walding.
d
,
LJJU uu--CJI[J
~~'~~o;3~,Te~t07~~O:iVo~ BP'tch
Teoth "- 2-'/2 Teeth G,ound A'oo Consumod
'-'/4T~
LlJ~---CDLU-- LULJ
Follow these cutting and grinding Instructions and the teeth will be uniformly
spaced after the weld.
CLEAN BLADE ENDS
WHICH CONTACT WELDER JAWS.
REMOVE DIRT. OIL. S4ALE
AND OXIDE-
'-'/4Tooth :-:1 ~Off ~WOlding.
.
'0 Pitch
/' GRIND OFF TEETH
~
A WITHIN WELDING AREA
Neveradjust guide fingers while blade is
running! Failure to comply may cause
serious injury!
Blade Shear and Blade Preparation
1.
Blade should be cut to the longest lengththat
machine will accept.
2.
Put handle in the upright position.
3.
Place blade againstthe back of the square
cutting guide of the shear.
4.
Bring handle down firmly to cut blade.
5.
Usethe blade grinder to assurethe blade ends
areflat, square, and smooth.
6.
With fine pitched blades, one or moreteeth
from each sidewill have to be removed by
grinding so that the cross section of the weld
area is unjform.
Points to remember in preparing the blade for welding
GRIND HERE
y
/
/
/
:f
~
~
WELD NOT IN CENTER OF GULLET
If snips are used
to cut blade,
grind ends square
as shown.
GOOO WELD
'NCORRECT T09TH SPACING
1. TOOTH WHICH WAS NOT
~
,~REMOVED HAS JAMMED IN WELD
Welder Preparation
1.
Clean the welder jaws and the lowerjaw inserts.
10
WEAK. INCOMPLETE WELD
(BLOW-OUT HOLES!
~~---
J

Welding
it:, CAUTION
The welder is designed for intermittent use.
Repeated welding within a short period of time
may cause the welder to overheat.
1. Turn pressure switch (A, Figure 14) to the zero
position.
B
A
D
2. Join blade ends together and locate unionin the
center between two electrodes. Lockblade in
positionby liftinglevers (Cand D, Fig. 14).
3. Set pressure switch (A)to blade widthaccording
to the scale.
4. Press weld button (8). Do not release untilthe
weld has been completed.
Annealing
1. Release the welded blade and clamp it again
between the front edge ofthe twojaws.
2. Annealing procedure willdepend on blade type:
Carbon Steel Blades
1. Press and jog the annealing switch button until
the weld is a "dullcherry"to "cherryred" color.
2. Allowthe blade to cool slowlybydecreasing the
jogg~ngfrequency.
Carbon
Steel Hard Back Blades
C
Fig. 14
.,
::::
DISTANCE BETWEEN JAWS
:'.
1. Heat the blade slowlyuntilthe weld becomes a
deep blue color.
2. Continue to heat byjoggingthe anneal button
untilthe widthof the blue color isone-half the
length of the band exposed between the jaws.
3.
Do not overheat or the temper ofthe band will
be damaged. Caution - Do not heat beyond
the "blue"stage. Ifthe band begins to show
any red color, itis too hot. Coolquicklyby
releasing the anneal button.
Correct annealing of Carbon Steel Hard
Back Blades
11

Bi-Metal Blades
1. Heat the blade slowly by jogging the annealing
switch button until the weld just begins to emit
light (dull red color). The desired color may
not always be visible in normal room light -
alwaysshadethe weld area.
2. Cool the weld quickly by releasing the annealing
button.
3.
Follow this procedure before and after grinding
bi-metal blades.
Blade Grinding
LIS: WARNING
Keep hands away from rotating grinding wheel!
Failure to comply may cause serious injury!
Always heed the indicator light
it warns that the grinder motor is running.
-when glowing,
After annealing, the blade must be ground to
remove excess metal or flash from the weld. With
the teeth facing out, grind the weld carefully. Do not
hitthe teeth, grind deeper than the weld, burn, or
overheat the weld area. Besureto remove flash
from the back edge of the blade. Any flash or "stub"
teeth which project beyondthe normal set or height
of the other teeth must be ground off.
Secondary Annealing
Anneal the weld 2-3 times again after grinding.
Welder Clean-Up
It is important that the welderjaws be kept clean at
all times. The jaws and inserts must be wiped or
scraped clean after every weld. Doing this will
ensure better welds by:
1. Holding proper alignment.
2. Preventing flash from becoming embedded in
the blade.
3. Preventing shorts or poor electrical contact.
12

Lubrication Schedule
1. Upper Blade Guide Shaft - lightly grease
weekly. Clean after every day's use.
2. Speed Change Handle - grease monthlywith a
light film on teeth andthreads.
3. Variable Pulley - found on end of pulley shaft.
Lubricatefitting using a light weight grease. .
4. Blade Tension Screw - grease monthly.
13

6799
6650
7330
6600
6602
6610
'3\
\'320 . .
.
~
~ ,'00
ID1320
'1 \'3'30 : I
~
9~90
gSOO
L
4010

--
15

Parts List for the VBS-2012 Bandsaw
PLEASE ORDER BY PART NUMBER ONLY
Control Panel Assembly
Index Part
No. No.
6600 VBS2012-6600 Push Button- On 1
6602 VBS2012-6602 Push Button- Off 1
6610 VBS2012-6610 Emergency Off Switch 1
Description
6650 VBS2012-6650 KeySwitch , 1
6710 VBS2012-6710 Magnetic Switch 2
6720 VBS2012-6720 Starter Overload 1
6742 VBS2012-6742 PowerOn Indicator Light 1
6745 VBS2012-6745 Voltage Reducer 1
6750 VBS2012-6750... Fuse . 2
6799 VBS2012-6799 Wiring Plate 1
Guide Post Assembly
1310 VBS1220A-131 Blade Guide Support.. 2
1320 VBS16-132 Blade Guide 4
1330 VBS1220M-133 BladeStop 2
1333 VBS2012-1333 Eccentric Shaft 1
G6201.BB-6201V Ball Bearing : 2
1350 VBS2012-1350 Blade Guide Post 1
1351 VBS2012-1351 Gear Bar 1
1360 VBS2012-1360 Guide Post Housing 1
1370 VBS2012-1370 Blade Guard - Left 1
1380 VBS2012-1380 Blade Guard - Right 1
1400 VBS2012-1400 Spring 2
1410 VBS2012-1410 Spring Housing 1
1450 VBS2012-1450 Post Elevating Gear 1
9015 VBS2012-9015 Guide Post Lock 1
9033 VBS2012-9033 Post Elevating Handwheel 1
9230 VBS2012-9023.. Handle 1
Size
Qty.
Work Table Assembly
1010 VBS2012-1
1020 VBS1220M-102 Table Support Frame 1
1030 VBS1220M-103 Table Bracket- Right 1
1040 VBS1220M-104 Table Bracket - Right 1
1060 TS-0680061 Washer 1/2" 2
1070 VBS2012-1070 Tube Screw 4
1080 VBS2012-1080 Blade Guard (not shown)... 2
1090 VBS1220M-109 Table Support Housing 1
1100 VBS1220M-110 Guide Support Housing 1
1550 VBS2012-1550 Rip Fence 1
8741 VBS2012-8741 Tilt Indicator - L&R 1
010 Work Table 1
16

8771 VBS2012-8771 Tilt Indicator -F&B 1
9013 VBS2012-9013 Rip Fence Lock 1
9700 VBS2012-9700 Indicating Needle 2
Motor Assembly
2000 VBS2012-2000 Motor 1
2010 VBS2012-2010 Motor Pulley 1
BA41...VB-A41 V-Belt 2
BA50... VB-A53 V-Belt 2
2020 VBS2012-2020 Motor SuspensionArm 2
Lower Wheel Assembly
3010 VBS1220A-301 Lower Wheel 1
3020 VBS1220A-302.. Rubber Tire... ... 1
VBS2012-301 LowerWheel wi Tire 1
3030 VBS2012-3030 Taper Sleeve 1
3040 VBS2012-3040 Wheel Lock Nut 1
Upper Wheel Assembly
3050 VBS1220A-305 Upper WheeL " 1
3020 VBS1220A-302 Rubber Tire 1
G6305. BB-6305 .. Ball Bearing.. 2
VBS2012-305 UpperWheel wi Tire and Bearings 1
3060 VBS2012-3060 UpperWheel Lock 1
3070 VBS2012-3070"'"'''''''''''' UpperWheel Nut 2
Blade Tracking Assembly
3080 VBS2012-3080 Slide Block Housing * 1
3090 VBS2012-3090 Slide Block Seat * 1
3100 VBS2012-3100 Slide Block Guide * '"'''''''''''''''''''''''''''''''''''' 2
3110 VBS2012-3110 Upper Wheel Slide * """""'"'''''''''''''''''''''''' 1
3111 VBS2012-3111 Slide Cover * 1
3112 VBS2012-3112 Slide Screw Shaft * """"""""""'''''''''''' 1
3113 VBS2012-3113 Slide Pin * 1
3120 VBS2012-3120 Wheel Elevating Shaft * 1
3121 VBS2012-3121 Spring * 1
3150 VBS2012-3150 Washer * 1
3180 VBS2012-3180 Indicator Ring * 3
* VBS2012-3080CP Slide Housing Complete 1
3190 VBS2012-3190 Tension Indicator 1
9030 VBS2012-9030 HandWheeL 1
8712 VBS2012-8712 Indicator Plate 1
3200 VBS2012-3200 Wheel Tracking Adjuster 1
3220 VBS2012-3220 Wheel Tracking Connector """""""""""""'''''' 1
3240 VBS2012-3240 Connector Washer 1
3250 VBS2012-3250 Connector Housing """"'''''''''''''''''''''''''''''''' 1
9060 VBS2012-9060 Tracking HandWheel '''''''''''''''''''''''''''''''' 1
9780 VBS2012-9780 Brush Bracket 1
9790 VBS2012-9790 Chip Brush 1
17

Gear Box Assembly
0500 VBS2012-0500 Gear Box * 1
0510 VBS2012-0510 Gear Box Cover * 1
0520 VBS2012-0520 Gear * 1
0530 VBS2012-0530 Screw Nut * 35mm 1
0540 VBS2012-0540 Gear * 1
0550 VBS2012-0550 Gear Shaft * 1
0560 VBS2012-0560 Shaft Cover * 1
0570 VBS2012-0570 Gear * 1
0581 VBS2012-0581 Main Shaft * 1
0590 VBS2012-0590.. Main Shaft Cover * 1
0600 VBS2012-0600 Speed Changing Shaft * 1
0610 VBS2012-0610 Speed ChangingArm * 1
0611 VBS2012-0611 Shaft Stop * 1
0612 VBS2012-0612 Spring * 1
0620 VBS2012-0620 Slide Block * 1
0621 VBS2012-0621 Slide Block Pin * 1
0624 VBS2012-0624 Key (not shown) * 1
0700 VBS2012-0700 Speed Change Lever * 1
0740 VBS2012-0740 Shaft Housing* 1
0790 VBS2012-0790 Speed Housing Ring * 1
9220 VBS2012-9220 Speed Lever Knob * 1
G6205. BB-6205 Ball Bearing * 3
G6206. BB-6206 . Ball Bearing * 1
G6304. BB-6304 Ball Bearing * 1
* VBS2012-0550CP Gear Box Assembly Complete 1
8422 VBS2012-8422 Gear Box Warning Label 1
Air Pump Assembly
4010 VBS2012-4010 Air Pump Housing * 1
4020 VBS2012-4020 Air Pump Cover * 1
4030 VBS2012-4030 Air Pump Shaft * 1
G6201. BB-6201 Ball Bearing * 2
4040 VBS2012-4040 Air Pump Pulley * 1
4050 VBS2012-4050 Air Pump Leaves * 4
4060 VBS2012-4160 Air Pump Housing* 1
4140 VBS2012-4140 Air Outlet * 1
4150 VBS2012-4150 Air Inlet * ... 1
4170 VBS2012-4170 Air Nozzle * 1
4180 VBS2012-4180 Air Nozzle Clip * 1
BM38.. VB-M39 V-Belt * 1
* VBS16-401CP Air Pump Assembly Complete 1
Main Body
5000 VBS2012-5000 ... Main Body 1
5100 VBS2012-5100 Rear Door - Larger 1
9310 VBS2012-9310 Hinge 6
9500 VBS2012-9500 Spring Plate 6
9590 VBS2012-9590 Handle 3
5101 VBS2012-5101 Rear Door - Smaller "'''''''' 1
5120 VBS2012-5120 Lower Door - Front 1
18

5140 VBS2012-5140.. UpperDoor- Frant 1
9300 VBS2012-9300 UpperDoorHinge . 2
9999 VBS2012-9999 Eye Bolt 1
Variable Speed Assembly
7000 VBS2012-7000 MotorSpringHousing* 1
7010 VBS2012-7010 Spring* 1
7020 VBS2012-7020 VariableSpeedDisk- UpperOutside* 1
7030 VBS2012-7030 VariableSpeedDisk- UpperInside* 1
7040 VBS2012-7040 VariableSpeed HousingTube * 1
G6007. BB-6007 BallBearing* .. 1
7050 VBS2012-7050 VariableSpeedDiskShaft* 1
G6205. BB-6205 BallBearing* 2
7060 VBS2012-7060 VariableSpeed Housing* 1
* VBS2012-7000CP VariableSpeedHousingAssemblyComplete. 1
7070 VBS2012-7070 Pulley 9" , 1
7080 VBS2012-7080.. Worm Gear 1
7090 VBS2012-7090 WormGear Housing 1
7100 VBS2012-7100 Gear Shaft 1
7120 VBS2012-7120 Arm ... 1
7170 VBS2012-7170 DetectorDiskHousing 1
7180 VBS2012-7180.. DetectorDisk 1
7190 VBS2012-7190 ScrewNut 1
8372 VBS2012-8372 VariableSpeedInstructionLabel 1
Variable Speed Shaft Assembly
7200 VBS2012-7200 Spring Housing * " 1
7210 VBS2012-721 0 Spring * 1
7220 VBS2012-7220...: VariableSpeedDisk- LowerOutside* 1
7230 VBS2012-7230 VariableSpeedDisk
7250 VBS2012-7250 VariableSpeedShaft* 1
G6007. BB-6007 BallBearing* """'''''''''''''''''''''''''''''''''''''''''' 1
G6204. BB-6204 BallBearing* .. 1
7260 VBS2012-7260 ShaftHousing* 1
* VBS2012-7200CP VariableSpeedHousingAssemblyComplete. , 1
7290 VBS20102-7290 Wheel Seat 1
7300 VBS2012-7300 Pulley 1
7310 VBS2012-7310 SpeedReadoutDetector 1
7320 VBS2012-7320 DetectorHousing 1
7330 VBS1220M-661 DigitalTachometer 1
9030 VBS2012-9030 HandWheel 1
BV875. VBS2012-BV875.. CogBelt 1
BA41...VB-A41 V-Belt 2
- LowerInside* 1
19

Work Lamp Assembly
6810 VBS2012-6810 Light Shield * 1
6820 VBS2012-6820 Shield Joint * 1
6830 VBS2012-6830 Brass Nut* 1
6840 VBS2012-6840 LampArm * " 1
6850 VBS2012-6850 Arm Joint * 1
6860 VBS2012-6860.. Arm Tube * 2
6870 VBS2012-6870 Tube Holder * 1
6880 VBS2012-6880 Arm Nut * 4
6890 VBS2012-6890 Tube Locker * 2
6900 VBS2012-6900 Arm Housing Adjuster * 1
6910 VBS2012-6910 HousingAdjust Screw* 1
6920 VBS2012-6920 LampArm Housing* 1
6930 VBS2012-6930 UpperArm Holder (RE:VBS2012-6920)* 1
6940 VBS2012-6940 LowerArm Holder (RE:VBS2012-6920)* 1
6950 VBS2012-6950 Lamp Socket * 1
9040 VBS2012-9040 Brass Handwheel * 1
* VBS2012-6950CP Work Lamp Assembly Complete 1
Welder/Grinder Assembly
6010 JWG34-601 Limit Switch * 2
6011 PR-EV-6011 Insulator * 1
6020 PR-EV-6020 Guide Block * 1
6021 PR-EV-6021 Spring Bracket * 1
6030 PR-EV-6030 Guide Casting * . 1
6040 PR-EV-6040 Housing * 1
6050 PR-EV-6050 Stationary Jaw * ... 1
6051 PR-EV-6051 Insulator * 1
6052 PR-EV-6052 Insulting Tube * 3
6053 PR-EV-6053 Insulating Washer * 3
6054 PR-EV-6054 Spacer * " 3
6060 PR-EV-6060 Eccentric Shaft * 2
6070 PR-EV-6070 Clamp Lever - Right * .. 1
6071 PR-EV-6071 Clamp Lever - Left * 1
9290 PR-EV-9290 Knob * 1
6100 PR-EV-6100 Clamp Support - Right * 1
6101 PR-EV-6101 Clamp Support- Left * 1
6110 PR-EV-6110 Clamp Plate - Right * " 1
6111 PR-EV-6111 Clamp Plate - Left * 1
6120 PR-EV-6120 Cam * . 2
6130 PR-EV-6130 Moving Jaw * 1
6150 JWG34-615 Weld Button * 1
6160 PR-HV-6160 MicroSwitch* 1
6161 PR-EV-6161 Switch Bracket* 1
6170 PR-EV-6170." PressureAdjust Knob* 1
6180 PR-EV-6180 Shaft * 1
6200 PR-EV-6200.. Cam * 1
6210 PR-EV-6210 :Weld Tension Arm * 1
6211 PR-EV-6211 Bushing * " 1
6220 PR-EV-6220 Spring - Short * 1
6230 PR-EV-6230 "... Spring - Long * ,1
6240 VBS1220M-624 " Transformer * 1
20

6241 PR-HV-6241 Mounting Bracket * 1
6250 PR-EV-6250 Switch * 1
6260 PR-EV-6260 . Grinder Motor * 1
6270 PR-EV-6270 Spacer * 1
6280 PR-EV-6280 Grinding Wheel * 1
6281 TS-0680021 Washer * 1/4" 1
6282 TS-1540041 Nut * 6mm 1
6290 VBS1220M-629 Grinder Guard * 1
6291 PR-EV-6291 Grinder Cover * 1
6330 PR-HV-6330 Name Plate * 1
6340 PR-EV-6340 Instruction Label * 1
6350 PR-EV-6420 Grinder Label * 1
6420 PR-HV-6420 Anneal Switch * 1
* VBS2012-WCP Welder Assembly Complete... 1
Shear Assembly
1910 PR-EV-1910 Spindle Bushing * 4
1920 PR-EV-1920 Spindle Lift * 1
1930 PR-EV-1930 Blade Shaft * 1
1940 PR-EV-1940 Vaned Iron Plate (Blade Stop) * 2
1950 PR-EV-1950 Lower Blade * 2
1960 PR-EV-1960 Upper Blade * 2
1970 PR-EV-1970 Joint Plate - Left * "'"'''''''''''''''''''''''''''''''''''' 1
1980 PR-EV-1980 Joint Plate- Right * 1
1990 PR-EV-1990 Handle Bar* 1
9210 PR-EV-9210 Knob * 1
* VBS2012-SCP ShearAssembly Complete 1
21

R
S
T
E
Electrical Schematic
A
A
it
A
1
2
3 ~ -/
32
l
-
4 -4
5 --- ?
6
---
b
--°
U ---/--1~
V -~/'/
~~B7 .0'-ilIlll IfLS2
PB3/ LSI
0 0 '-
-
PB4
w --~o SA ...r:F'BB
IO'~O
II
0 0---4\.J-<> cr--
I I
31 ~LS3
7i88881E-P81
f21 AbO
13
14
15
110
5A
,WELDER
16
17
18
PB1 - Saw Stop Switch
P82
-Saw Start Switch
PB3 - Weld Switch
PB4 - Anneal Switch
PB7 - Emergency Stop
PB8 - Main Power Key
LS1 - Auto Weld Stop Switch
LS2
- Safety Switch
LS3 - Safety Switch
SW1 - Grinder On-Off Switch
SW2 - Work Lamp On-Off Switch
22
Jumper Wire Settings
220V
1-U
2-V
3-W
4-5-6
10-11
14 - 15
16 - 17
440V
4-U
5-V
6-W
11- 12
13- 14
17- 18

NOTE

NOTE

NOTE