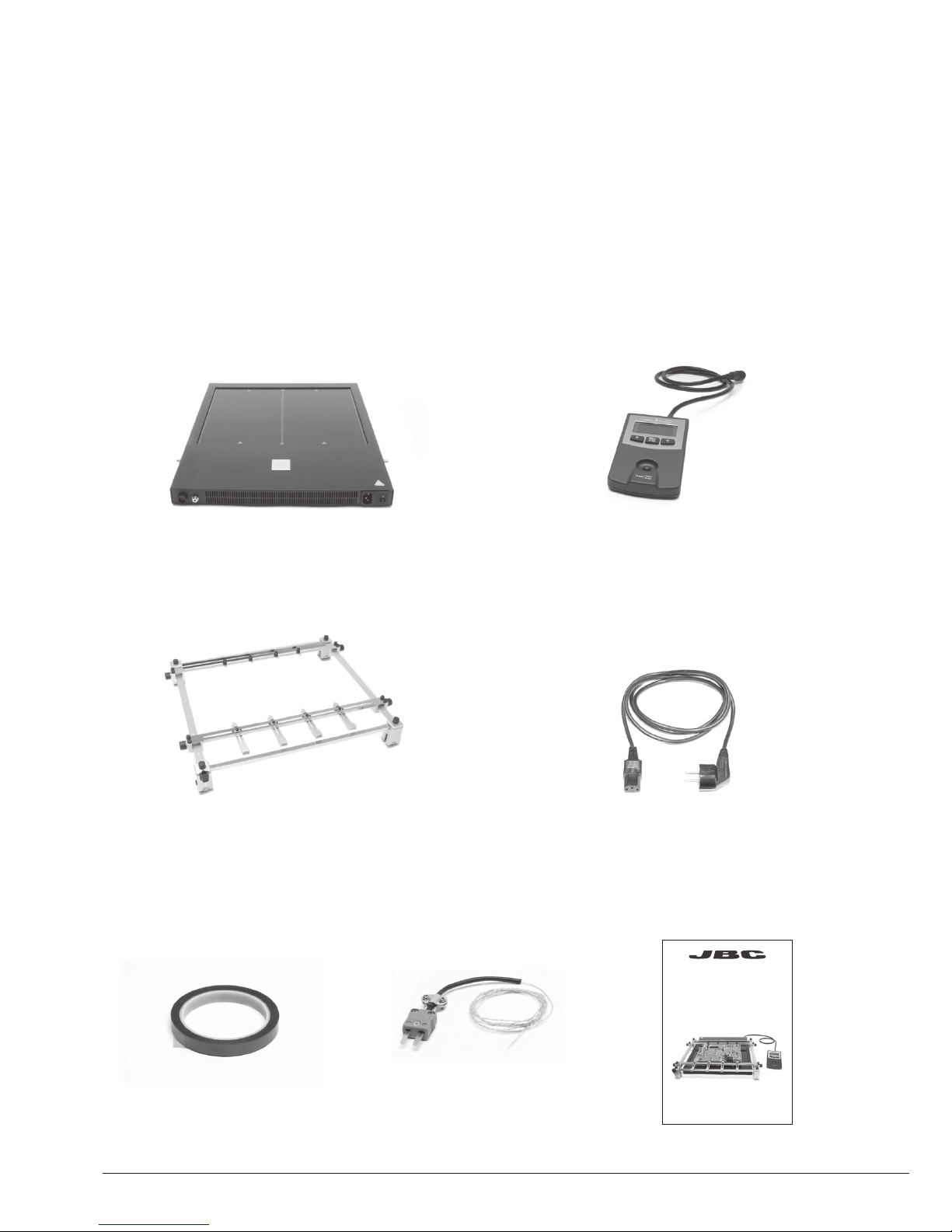
2
Packing List
The following items should be included:
Heater Unit Console
Power Cord .............................................. 1 unit
Ref. 0009417 (100V/120V)
0009401 (230V)
Thermocouple .............. 1 unit
Ref. PH218
Kapton Tape .................. 1 unit
Ref. PH217
Manual ............................ 1 unit
Ref. 0016815
Ref. PHB-KA
Convection Preheater Set
Convection Preheater ............................................................................................................................. 1 unit
Ref. PHB-1A (120V)
PHB-2A (230V)
PHB-9A (100V)
Convection Preheater Support ........... 1 unit
Ref. PHB-SA
INSTRUCTION MANUAL
www.jbctools.com
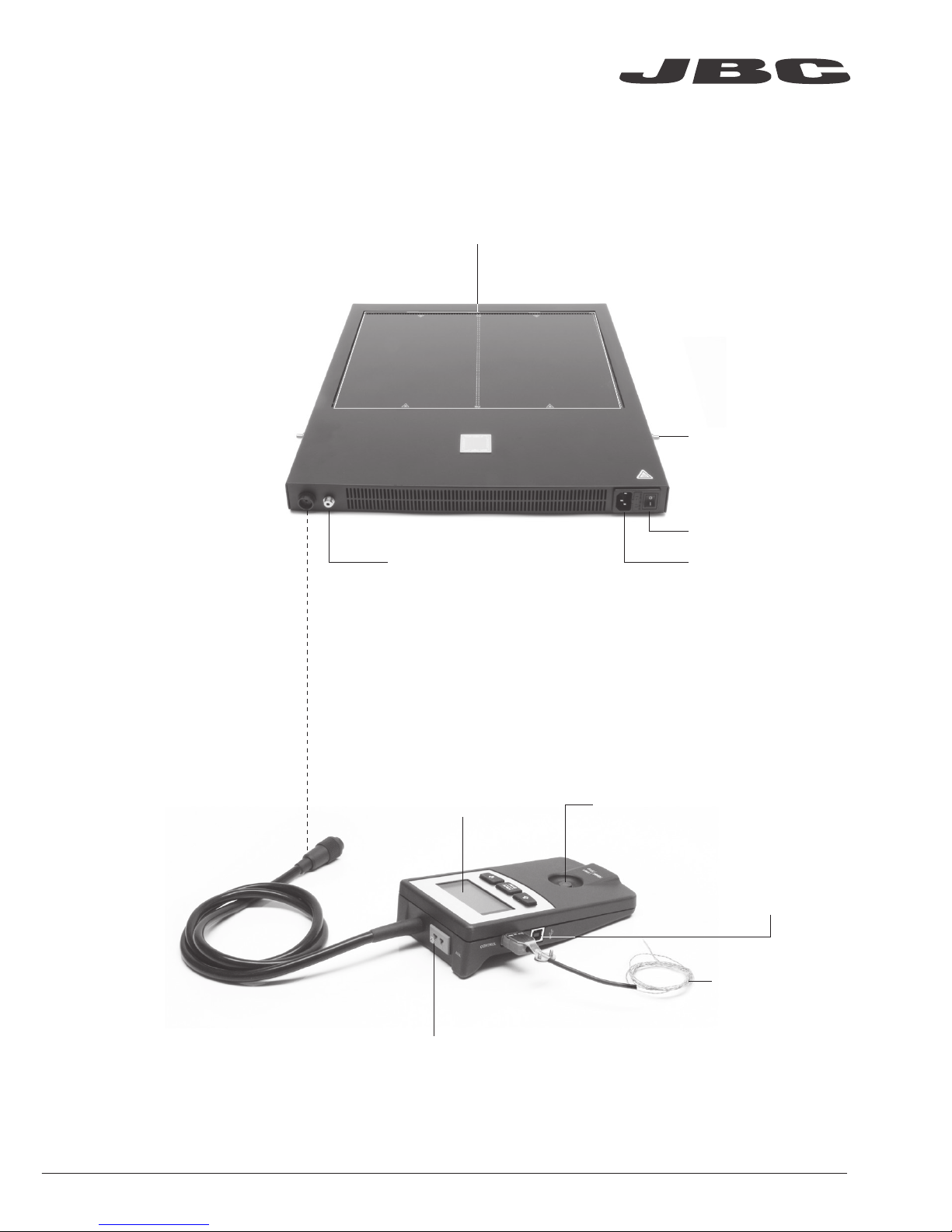
3
Features
Pedal socket (optional)
Ref. P-005
Heating Areas
Power socket
Power
Fixing brackets
for PHB-SA
Convection Preheater
Support
Heater Unit
Console
Control Unit Start / Stop
Auxiliary Thermocouple (Type K) Input
Thermocouple
(Type K)
Ref. PH218
USB-B
connector to PC:
Update software
Zone A
Zone B
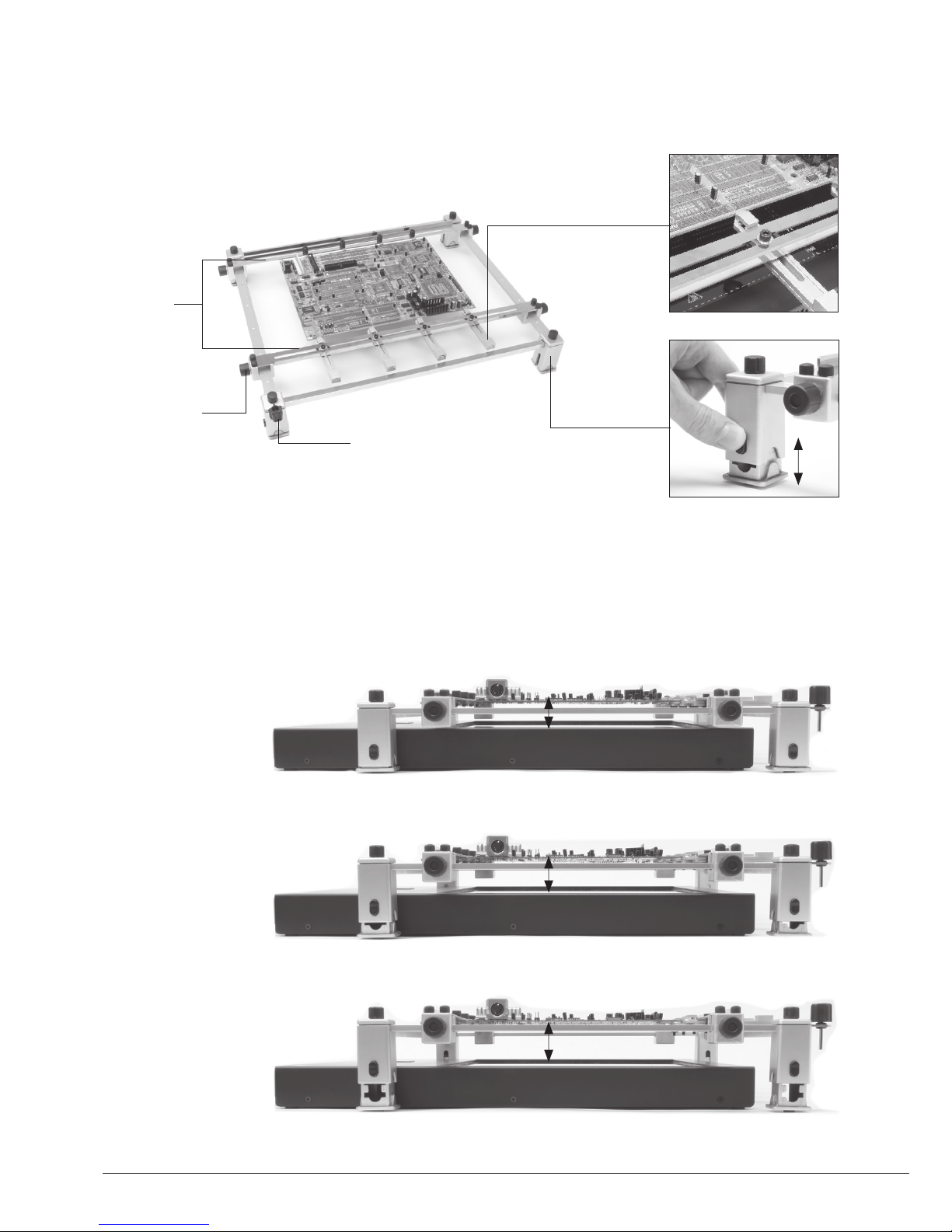
4
Height Adjustment
It allows adjustment for 3 heights between the PCB and the Heating Area of the PHB-A Heater Unit.
Low level
High level
Medium level
28 mm
38 mm
48 mm
PHB-SA Features
Adjustable slot clamps
for switching PCBs
Adjusting system
for changing height
Clamp knobs
Sliding
guides
Allen key
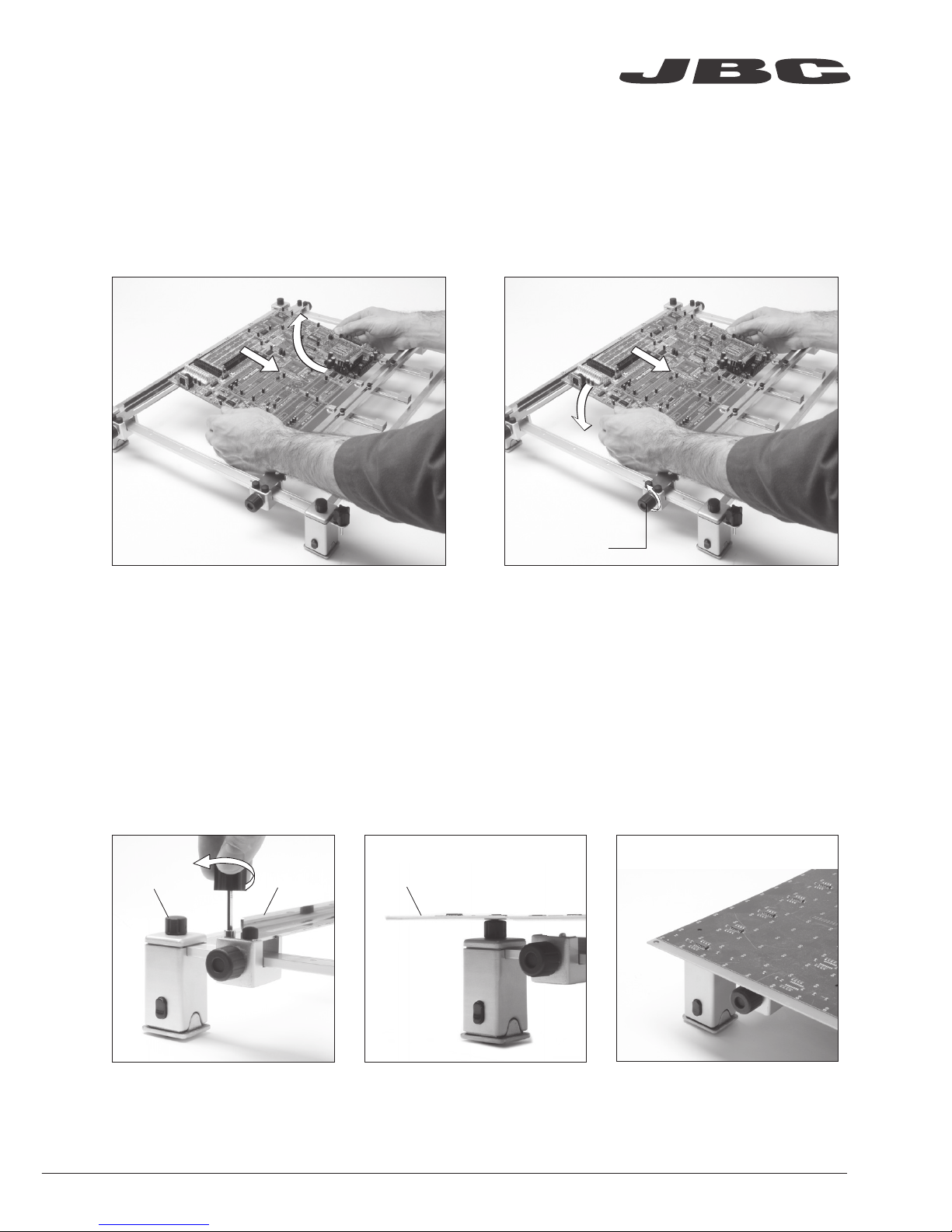
5
Changing PCBs of the same batch
Loosen one sliding guide, pull back and lift
out the PCB.
The support lets you place PCBs of the same batch so as to always heat the same area.
Use the sliding guides to change the PCBs.
Position it and tighten the sliding guide knobs.
Removing the PCB
Placing another PCB
Cap
Guide
PCB
Use the 4 caps to place larger PCBs than the PHB-SA Support or over 3mm thick.
1. Remove both guides by
untightening the 8 screws.
2. Place the PCB on the 4
rubber caps.
3. The PCB is ready to work.
Reworking large PCBs
Clamp knobs
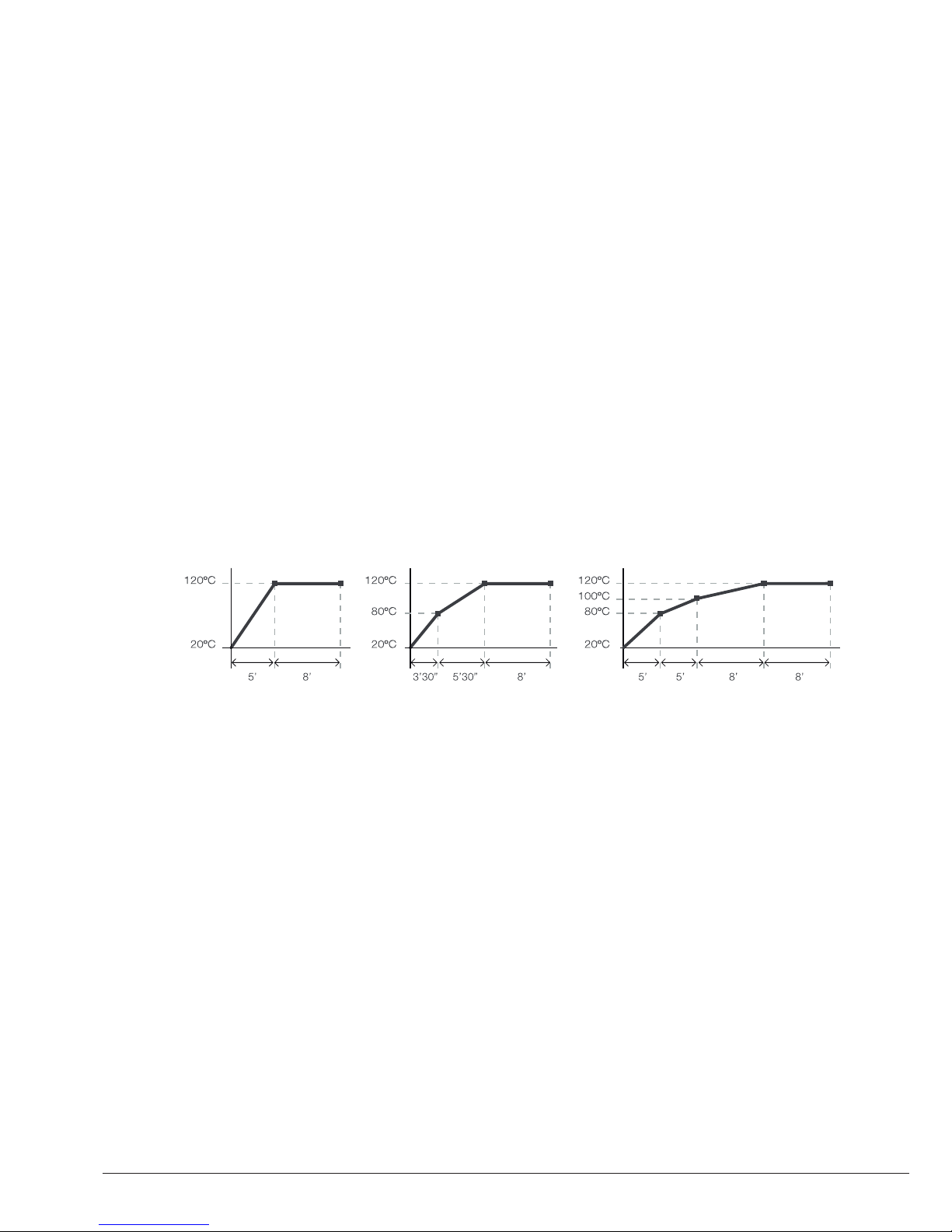
6
Profiles by Temperature
The usual way to run a profile is using the Thermocouple (TC) connected to the Control Input of the
console. JBC offers 3 predefined profiles (JBCset) and 20 profiles ready for you to personalize.
Why convection? Perfect heat distribution
Convection technology offers a uniform heat distribution over the whole working area of the
Preheater. This gradual heating system reduces the risk of thermal stress on the PCB.
Operation
JBCset profiles
There are 3 profiles predefined by JBC: A, B and C. The difference between them is the number
of steps: 2, 3 or 4. The thicker your PCB is and the more layers it contains, the more steps are
needed to obtain a gradual warming.
These profiles are not modifiable but they can be used as a template to create your own profiles.
JBCset A
2 steps
JBCset B
3 steps
JBCset C
4 steps
For repetitive jobs we recommend running profiles without the Thermocouple (TC). Once any
profile has been run to the end, the system has all the process data which you can save.
Once it is saved, you can run this profile without connecting the Thermocouple (TC). The heating
process will the same as long as the same working conditions are respected.
User profiles
You can create your own profiles from the JBCset profiles. On the work screen of the profile,
press the Enter button and choose the option Edit profile.
Power or Temperature Modes
The unit works at the selected power or temperature during the defined time. These parameters can
be modified from the work screen by pressing the Enter button and the Edit parameters menu.
To see the current temperature you must plug the Thermocouple (TC) into the Control connector.
PCB reference
specifications:
FR4 1,6mm thick
and 2 layers.
FR4 2,2mm thick
and 6 layers.
FR4 1,6mm thick
and 6 layers.
Profiles set using the low position of the PHB-SA Support (28 mm in height between the PCB and the heating area).
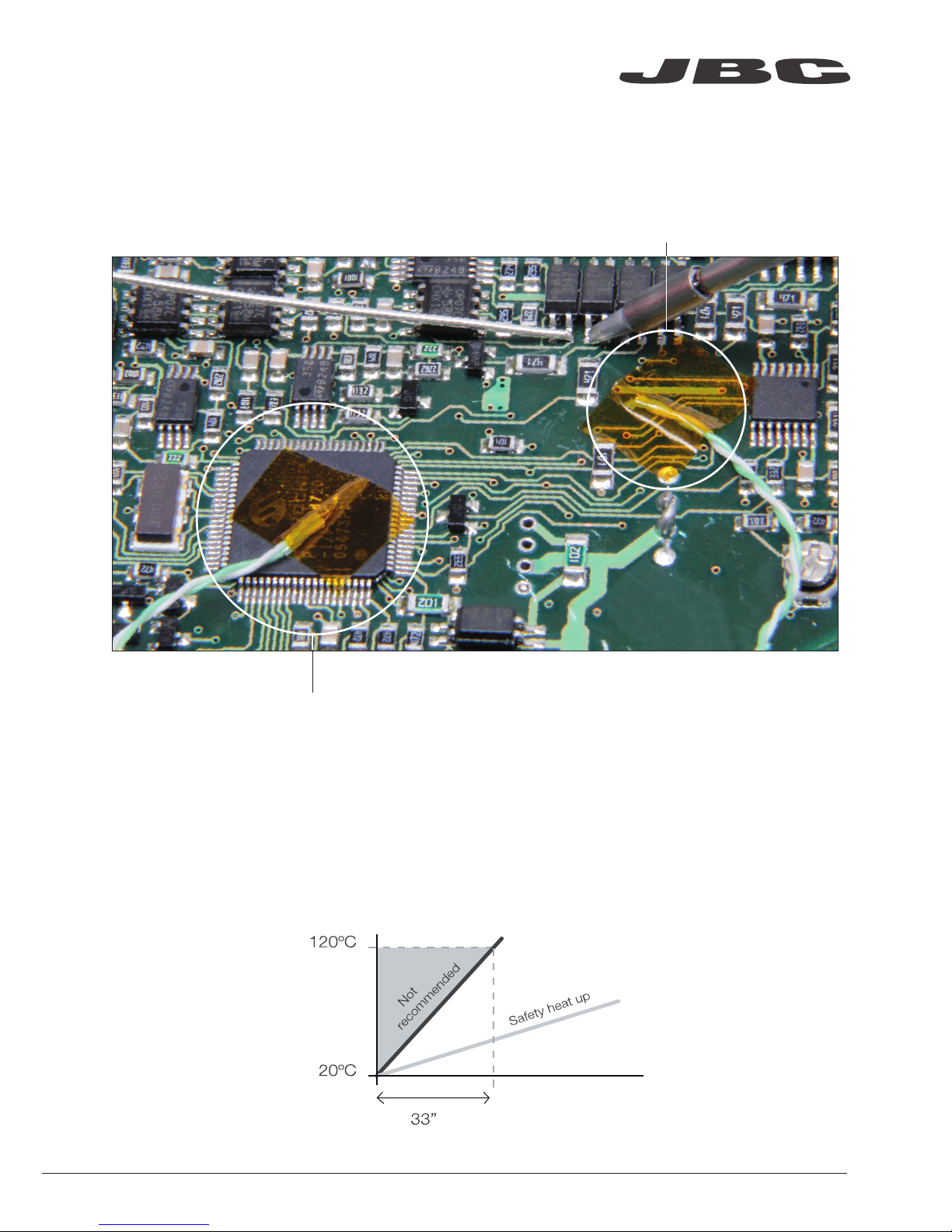
7
Recommended Guidelines
1. Place the Thermocouple (TC) as near as possible to the component being worked on.
2. If there are any sensitive components, use the Auxiliary Thermocouple as protection.
You can select the protection temperature in Station settings. If the selected temperature is
reached, the Heater Unit will stop the process and a warning message will be shown.
3. IPC* does not recommend exceeding ramp-up rates over 3 - 4 °C / sec (5 - 7 °F / sec) so as to
reduce the risk of thermal stress on the PCB.
* IPC was founded in the U.S. in 1957 as the Institute for Printed Circuits and is committed to becoming the
most recognized international industry association for the electronics manufacturing industry.
Fix the TC with Kapton Tape
Auxiliary Thermocouple (TC)