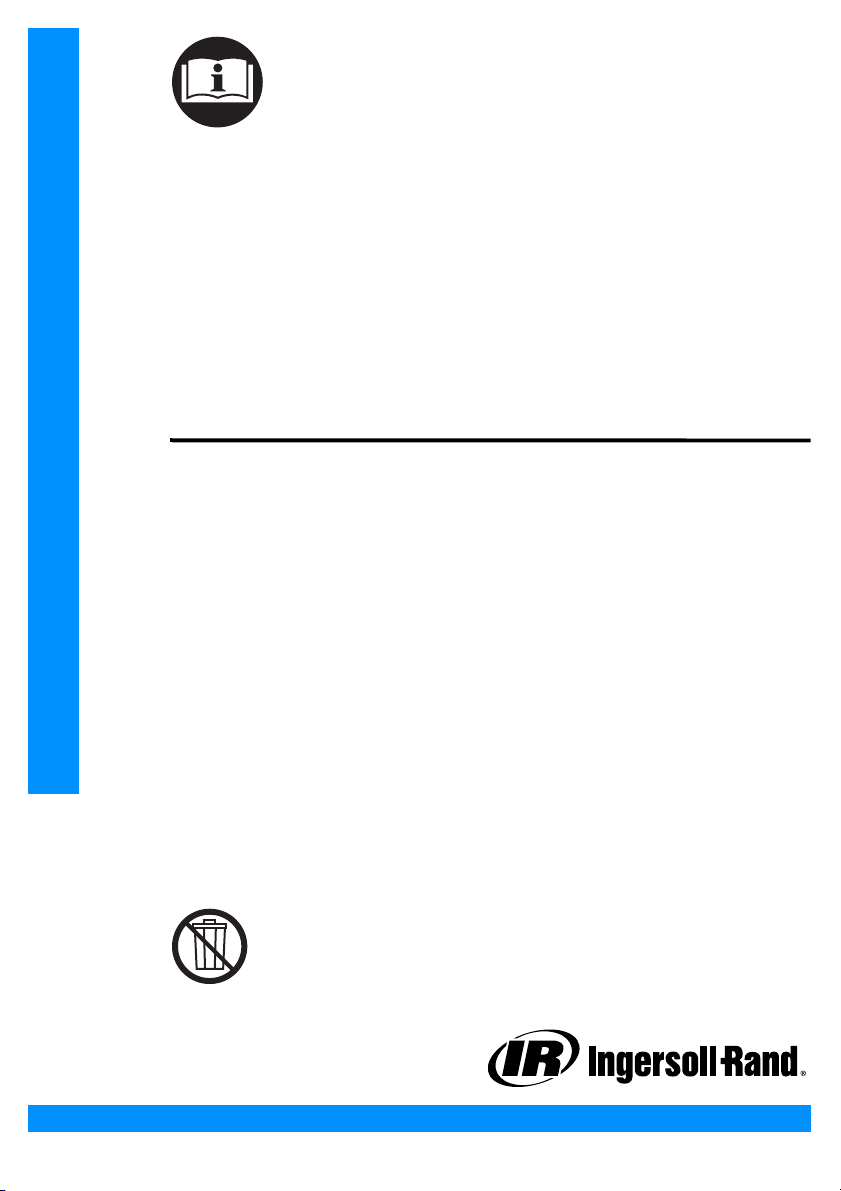
Form P6401
Edition 6
October 2005
CCN 03528635
Nonreversible and Reversible
MULTI–VANE® Geared Motors
92N and 92R Series
Operations and
Maintenance Information
Save These Instructions
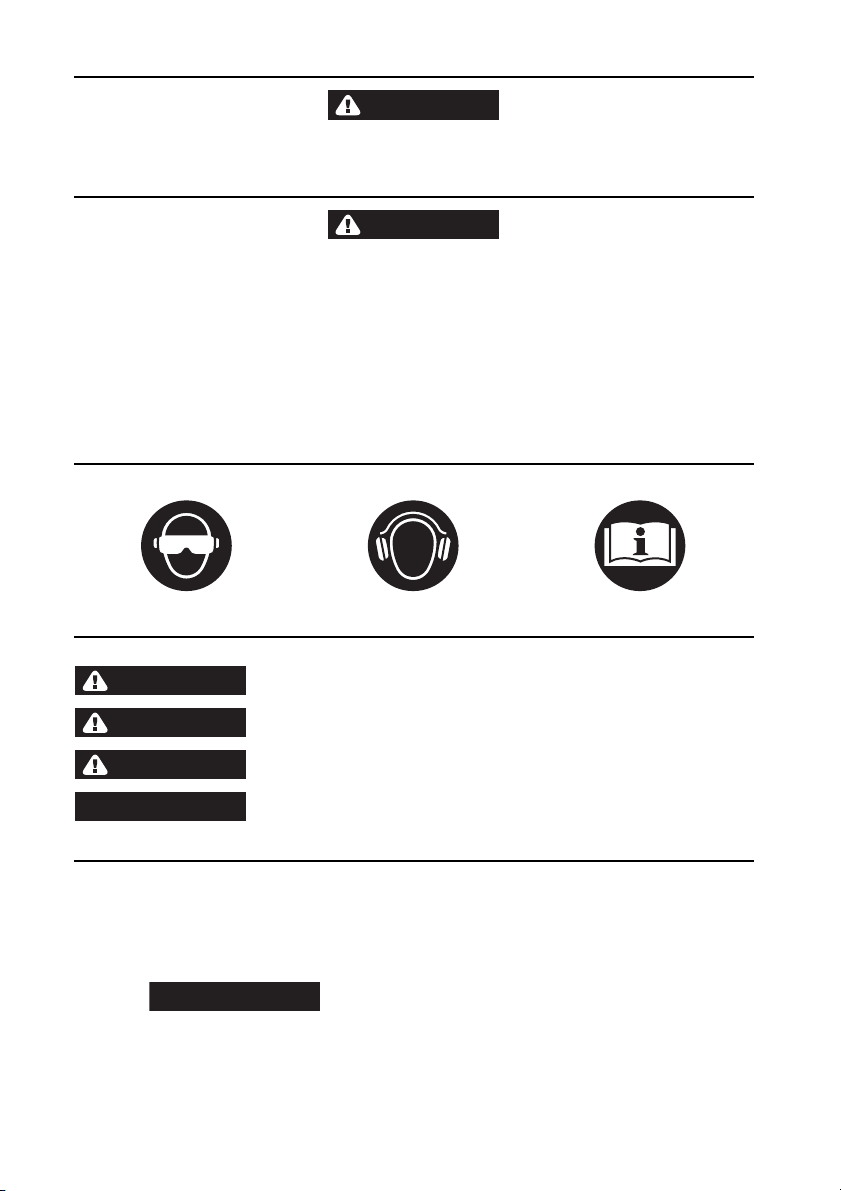
WARNING
General Product Safety Information
• Read and understand this manual before operating this motor.
• It is your responsibility to make this safety information available to others that will operate this motor.
• Failure to observe the following warnings could result in injury.
WARNING
• Always operate, inspect and maintain this motor in accordance with American National Standards Institute Safety
Code for Portable Air Tools (ANSI B186.1).
• For safety, top performance and maximum durability of parts, operate this motor at 90 psig (6.2 bar/620 kPa) air
pressure at the inlet with 1-1/4” (32 mm) air supply hose.
• Always turn off the air supply and disconnect the air supply hose before installing, removing or adjusting any
accessory on this motor.
• Do not use damaged, frayed or deteriorated air hoses and fittings.
• Keep hands, loose clothing and long hair away from rotating end of motor.
• Anticipate and be alert for sudden changes in motion during start up and operation of any motor.
• Motor shaft may continue to rotate briefly after the throttle is released.
• Do not lubricate motor with flammable or volatile liquids such as kerosene, diesel or jet fuel.
• Do not remove any labels. Replace any damaged label.
• Use accessories recommended by Ingersoll-Rand.
• This motor is not designed for working in explosive atmospheres.
• This motor is not insulated against electric shock.
Safety Symbol Identification
(Dwg. MHP2454) (Dwg. MHP2455) (Dwg. MHP0884)
Safety Information - Explanation of Safety Signal Words
DANGER
WARNING
CAUTION
NOTICE
Indicates an imminently hazardous situation which, if not avoided, will result in death or
serious injury.
Indicates a potentially hazardous situation which, if not avoided, could result in death or
serious injury.
Indicates a potentially hazardous situation which, if not avoided, may result in minor or
moderate injury or property damage.
Indicates information or a company policy that relates directly or indirectly to the safety of
personnel or protection of property.
Lubrication
Always use an air line lubricator with these motors. We
recommend the following Filter-Regulator-Lubricator Unit:
No. C31-08-600.
Install the Unit as close to the Motor as practical. Keep the
Lubricator filled with Ingersoll-Rand No. 50 Oil.
NOTICE
If a sight feed lubricator is used, adjust the lubricator to
feed 60 drops per minute for continuous duty operation.
Whenever the power unit is disassembled, work some
Ingersoll-Rand No. 28 Grease into the Rear Rotor Bearing
(5).
2 Form P6401-Edition 6
Use a good quality SAE 90 Gear Lubricant in the gear box.
The amount of lubricant required is dependent upon the size
of gear box and the mounting position of the Motor.
When lubricating the gear box, refer to Drawing TPB490
showing the various mounting positions and the fill plugs,
vent plug and drain plug. In each case, fill the gear chamber
up to the “Level” plug. If the Vent Plug (40) is not located at
the position indicated for a given mounting, relocate the Vent
Plug by interchanging it with the pipe plug at that location.
Whenever a Series 92NB or 92RB Motor is mounted with
the Motor Shaft (36) pointing toward the floor or ceiling,
you must install a gravity feed lubrication to make certain the
gears in the upper portion of the gear box get adequate
lubrication. To do this, remove one of the pipe plugs other
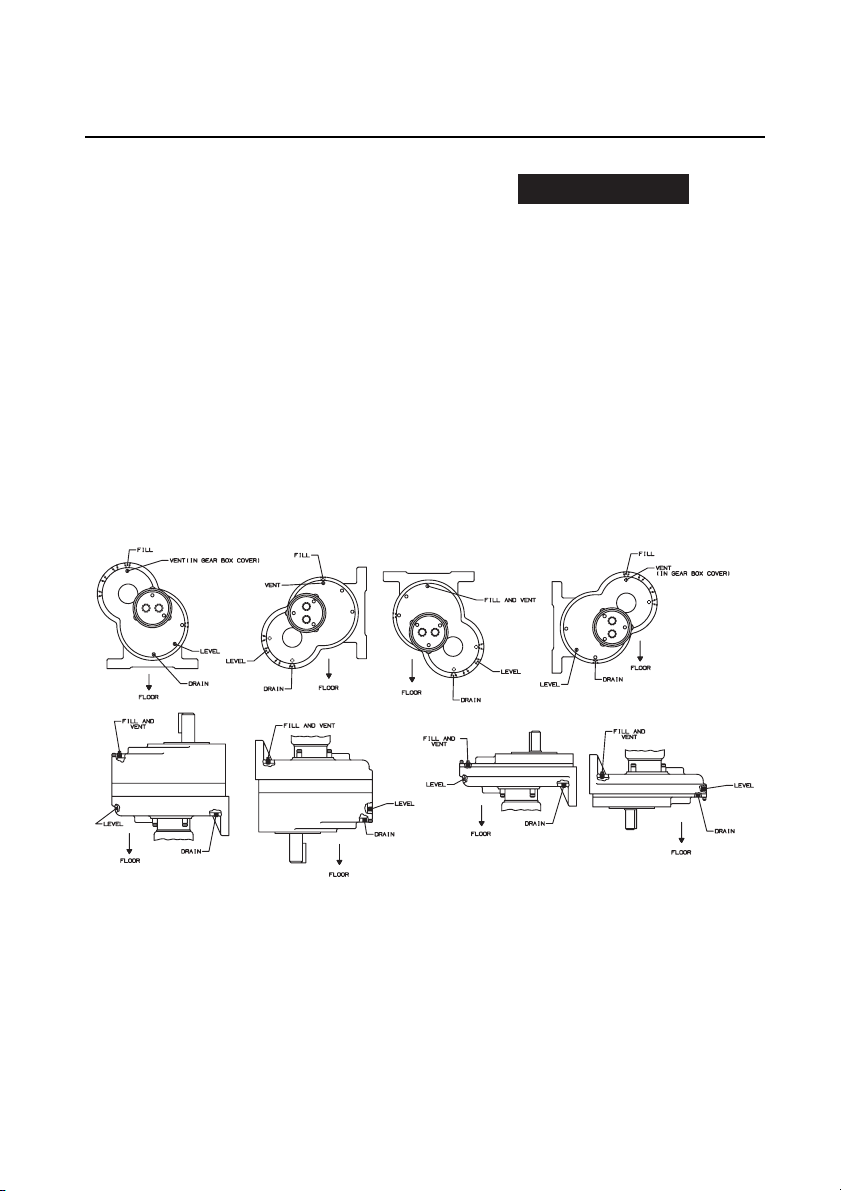
than the Vent plug from the upper side of the motor and
connect an oil line from a gravity feed reservoir. Connect an
overflow line to the Level Plug opening and run it to a pump
to return the lubricant to the gravity feed reservoir.
Direction of Shaft Rotation
Series 92N Non–reversible Motors are assembled at the
factory so that the Motor Shaft (36) rotates counterclockwise
when facing the end of the Shaft. When desired, the direction
of the shaft rotation can be changed as follows:
1. Stand the Motor upright on a workbench with the Motor
Housing Cover (1) upward and secure it in position by
clamping the base with a C–clamp.
2. Remove the four Housing Cover Cap Screws (2).
3. Being careful not to damage the Cylinder Seals (8A), pull
the Motor Housing Cover and the Motor Ho using (11) off
the Gear Box (18).
4. Grasp the Cylinder (8) with both hands and carefully work
the motor from the Gear Box.
5. While holding the Cylinder with one hand, drive against
the splined end of the Rotor (12) with a soft hammer until
the Front Rotor Bearing (13) comes free from the rotor
shaft.
6. Withdraw the Front Rotor Bearing, Front Rotor Bearing
Spacer Assembly (14) and Front End Plate (7).
7. Withdraw the Cylinder (8), turn it end–for–end, and slide
it back over the Rotor.
8. Install the Front End Plate, Front Rotor Bearing Spacer
Assembly and Front Rotor Bearing.
If the Motor is mounted in any position other than
that illustrated, contact an Ingersoll-Rand
Representative for oil level and venting recommendations.
NOTICE
Press against the inner ring of the Bearing when
pressing the Front Rotor Bearing on the rotor shaft.
9. Align the dowel hole in both End Plates and Cylinder, and
insert the Cylinder Dowel (9) so that it protrudes from the
Rear End Plate.
10. Place the Housing Cover Gasket (4) in the recess in the
Housing Cover so that the dowel notch in the Gasket is
aligned with the dowel hole in the Cover.
11. Set the motor assembly in the Cover so that the Cylinder
Dowel enters the dowel hole.
12. Slide the Motor Housing (11) over the Cylinder and
against the Motor Housing Cover.
13. Place the Gear Box Gasket (17) on the face of the Front
End Plate.
14. Pick up the entire assembly and being careful not to
damage the Cylinder Seals, work it into the pilot recess in
the gear box.
15. Install the Housing Cover Cap Screws and, with the
Motor running at a slow speed using air pressure of 30 to
40 psig (2.07 to 2.76 bar/207 to 276 kPa), alternately
tighten the Screws to 28 to 31 ft–lb. (38.0 to 42.0 Nm)
torque.
(Dwg. TPB490)
Form P6401 Edition 6 3
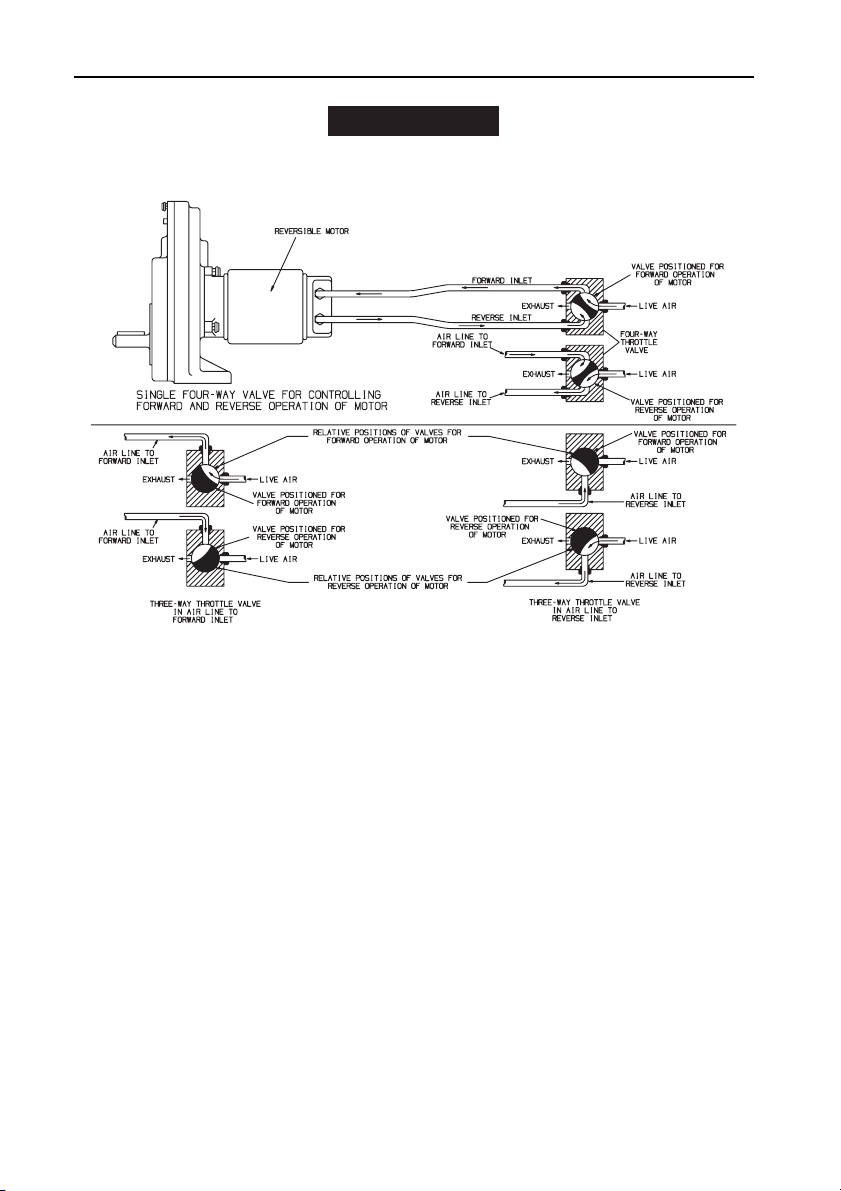
Reversible Motor Applicatons Air Flow Information
NOTICE
When these motors are used on applications requiring a reversible motor, a 4–way throttle valve or two 3–way throttle
valves must be used in the air supply line in accordance with the following schematic diagram (TPB491).
When the application requires a non–reversible motor, a 2–way inline valve can be used in the air supply line. In either
case, the inlet and outlet of the valve must be equal in size, and preferably one size larger, than the inlet of the motor.
(Dwg. TPB491)
4 Form P6401-Edition 6