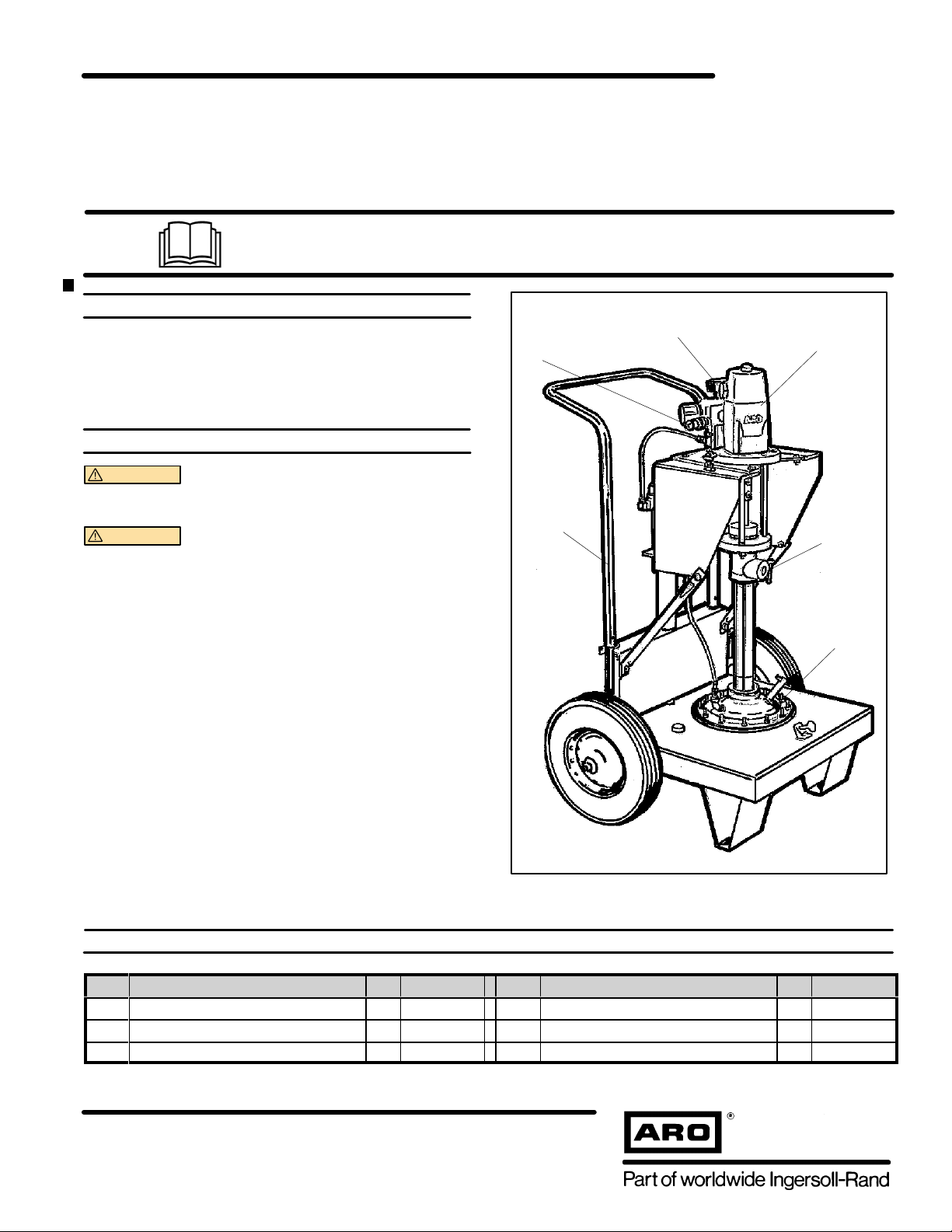
OPERAT
OR’S MANUAL
INCLUDING: OPERATION, INSTALLATION & MAINTENANCE
ALSO INCLUDEMANUALS: 67075 CART, 6711X-XPUMP, F252XX-X MODULE/AIR F-R-L & FM 3637-2 GEN
INFO SHEET
3” AIR MOTOR
21.7:1
RA
TIO
4” STROKE
650530–1
CARBON STEEL
PUMP
SYSTEM
650531–1
ST
AINLESS STEEL
650530–X
650531–X
RELEASED:
(REV
3–6–95
. A) IPP
READ THIS MANUAL CAREFULL
OPERA
TING OR SER
SERVICE KITS
• Use only genuine ARO replacement parts to assure compatible
pressure rating and longest service life.
• 637066-B for repair of Air Motor Section.
• 63729X-XXX for repair of Lower Pump 6710X-X.
GENERAL
WARNING DO NOT EXCEED MAXIMUM OPERATING
PRESSURE OF 3,262 P.S.I. (224.9 BAR) AT 150 P.S.I. (10.4
BAR) AIR INLET PRESSURE.
WARNING REFER TO GENERAL INFORMATION SHEET
FOR ADDITIONAL SAFETY PRECAUTIONS AND IMPORĆ
TANT INFORMATION.
By delivering a smooth, continuous bead of the proper size, an ARO
system helps the operator maintain both his production rate and proĆ
duce quality standards. Maintained quality standards assures that the
material benefits are realized. To further maximize operator production
time, the ARO System has a built-in lift feature for quick and easy
drum changeover.
ARO Systems are totally enclosed, sealing the material in the system
from air and moisture, preventing premature cure-out of the material.
This allows for either continuous or intermittent use of the system and
reduces the need for daily system clean-up.
Built-in lift capability allows for quick drum changeover and easy lifting
of pump assembly from container.
The 21.7:1 ratio is an expression of the relationship between the effecĆ
tive air motor area and the effective lower pump area. When 150 PSI
(10 bar) of air pressure is supplied to the air motor, the lower pump area
will develop a maximum of 3,262 PSI (224.9 bar) of fluid pressure (at
no flow) as the fluid control is opened, the flow rate will increase as the
air motor cycle rate increases to keep up with the demand
DESCRIPTION
Y BEFORE INST
VICING THIS EQUIPMENT
Pump Air
Cart/Lift
Air Inlet
1
Manifold
ALLING,
.
3
Material
Outlet
2
FIGURE 1
MAJOR COMPONENTS LIST
Item Description Qty Part No. Item Description Qty Part No.
1 Cart/Lift 1 67075 3 Basic Pump Assembly (650530-1) 1 67110-P43
2 Follower Plate (650530-1) 1 651840-1 Basic Pump Assembly (650531-1) 1 67111-P43
Follower Plate (650531-1) 1 651841-1
THE ARO CORPORA
%
(419) 636–4242 D F
E1995
THE ARO CORPORA
TION
AX (419) 636–21
D ONE ARO CENTER D BRYAN, OHIO 43506–0151
TION
D PRINTED IN U.S.A.
15

INSTALLATION
The 65053X-X Chop-Check Dispensing System comes completely
assembled. Remove unit from crate and place on a level surface.
Install material hose and dispensing device as required.
When the following instructions are observed, heavy paste materials
can be pumped directly from their original 5 gallon drum without air inĆ
OPERATING INSTRUCTIONS
OPERATING INSTRUCTIONS / INITIAL SETUP PROCEDURE
WARNING STAND CLEAR. When raising or lowering the
lift.
2
AIR CONTROLS
PUMP AIR
PUMP AIR
INLET
CART/LIFT
AIR INLET
OFF
FOLLOWER PLATE
AIR SUPPLY VALVE
FIGURE 2
TO RAISE LIFT, (THE FIRST TIME):
1. Take note of the pump/drum clearance above. Be certain the lift is
clear of any objects above the unit.
2. Adjust (Turn Needle Valve Knob Counter-Clockwise) air pressure to lift.
Connect the air supply (160 PSI MAX) to the air inlet.
3. Raise the lift high enough to clear the height of the drum. Stop the lift
upward travel by adjusting (Turn Needle Valve Clockwise until tight.)
Needle Valve.
REFER TO PAGE 3:
1. Once lift assembly and pump are in the ``UP" position, place and
center an opened 5 gallon drum of material on the lift base. Use the
REGULATOR
ON
clusion, or excessive waste. The follower plate creates an air tight seal
as well as clean-wiping action in its progressive downward movement
into the drum.
stops on the base to center 5 gallon drum. Tighten thumb screw to
secure drum.
2. Lubricate lower follower wiper plate seal with any type grease. (siliĆ
cone, vaseline, gear, etc.) This ensures a smooth fit into the pail as
well as prevents curing type compounds from bonding to seal.
3. Check vent plug on follower plate to be sure it easily threads in and
out. It is recommended to lubricate the threads of the plug to help
prevent possible set up of compound at this point. See 65184X-X
Operator's Manual.
TO LOWER LIFT:
WARNING
causing injury. Keep hands clear when aligning with containĆ
er.
NOTE: Be certain the Follower Plate vent plug has been removed
so that the air trapped between the follower and the material is allowed
to escape from this vent. Captured air between the follower plate and
drum will escape.
NOTE: The lift may hesitate momentarily before starting downward,
the air pressure inside the post air chamber must decrease before it
will begin to descend.
1. Disconnect air line from the lift air inlet. Adjust (Turn Needle Valve Knob
Counter-Clockwise) Needle Valve to Lower the pump end into drum.
2. Replace the vent plug once the material begins to ooze from the
vent opening.
3. Adjust (Turn pump air regulator knob Counter-Clockwise to prevent
over pressurization of pump.) Knob on pump air regulator.
4. Connect air line to pump air regulator and adjust (Turn pump air reguĆ
lator Clockwise) air until pump begins to cycle.
5. Trigger gun to prime pump with material.
PINCH HAZARD. Follower can descend quickly
TO RAISE LIFT, (NORMAL OPERATION):
1. Disconnect air line from pump air regulator and connect to lift air
inlet. Adjust the Follower Plate Air Valve pressure up to approxiĆ
mately 8 psig. DO NO OVERPRESSURIZE THE DRUM to avoid
damage.
NOTE: Air from this valve will only pass when the unit is being
raised.
2. Adjust (Turn Needle Valve Knob Counter-Clockwise) air pressure on lift.
3. Raise the lift high enough to clear the height of the drum. Stop the
lift upward travel adjusting needle valve knob Counter-Clockwise.
TO CHANGE DRUM:
NOTE: The Needle Valve Knob should be turned Clockwise to hold lift
in the ``UP" Position.
1. Unsrew thumb screw and remove old 5 gallon drum.
2. Place and center. a new drum into position. Remove cover. TightĆ
en thumb screw.
PAGE2OF4