
OPERATOR’S MANUAL
INCLUDING: OPERATION, INSTALLATION & MAINTENANCE
INCLUDE MANUAL: S-632 GENERAL INFORMATION MANUAL (PN 97999-624)
2” AIR MOTOR
2:1 RATIO
6” STROKE
It is the responsibility of the employer to place this information in the hands of the operator. Keep for future reference.
2” DIFFERENTIAL TRANSFER PUMP
(CARBON STEEL)
SEE CHART BELOW
READ THIS MANUAL CAREFULLY BEFORE INSTALLING,
OPERATING OR SERVICING THIS EQUIPMENT.
SERVICE KITS
650110-X
650115-X
RELEASED: 3-26-68
REVISED: 9-28-11
T)
(REV.
• Use only genuine AROR replacement parts to assure compatible
pressure rating and longest service life.
• 66098 for repair of 60702 air motor section.
• 637028 for repair of 66198 lower pump end (650110-C) and 66200
lower pump end (650115-C) (UHMW-PE / Polyethylene).
• 637029 for repair of 66198-1 lower pump end (650110-1C) and
66200-1 lower pump end (650115-1C) (PTFE / PTFE).
SPECIFICATIONS
Model Series 65011X-( )...................
Type Air Operated, Transfer Pump........................
Ratio 2:1.........................
Air Motor Diameter 2” (5.08 cm)..............
Stroke (double acting) 6” (15.24 cm)...........
Air Inlet (female) 1/4 - 18 N.P.T.F. - 1...............
Material Outlet (female) 1/2 - 14P.T.F.SAE Spec. Short
Material Inlet (female) (650115-X) 1 - 11-1/2 N.P.T.F....
Pump Construction Carbon Steel............
Pump Drum Size / Capacity
650110-C & 650110-1C 55 gallon..........
650115-C & 650115-1C 16 gallon..........
Dimensional Data see chart...............
Air Inlet Pressure Range 0 - 150 p.s.i. (0 - 10.3 bar)..........
Fluid Pressure Range 0 - 300 p.s.i. (0 - 20.7 bar)............
Cycles / Minute Rec’d @ Working Flow 120
Displacement In
3
Per Cycle 8.0........
Volume / Cycle 4.4 oz. (131 ml)..................
Cycles Per Gallon 28.9...............
Accessories Available 61113 mounting bracket
Noise Level @ 90 p.s.i. - 40 c.p.m . . . . . 81 db(A)
........
PERFORMANCE
............
Air Motor 60702
Air Inlet (not shown)
1/4 - 18 N.P.T.F. - 1 (female)
“A”
Material Outlet (female)
1/2 - 14 P.T.F. SAE Spec. Short
2 - 11-1/2 N.P.T. Bung Thread
“B”
LOWER
MODEL
650110-C 66198 53-3/32 (1349) 33-13/16 (859)
650110-1C 66198-1 53-3/32 (1349) 33-13/16 (859)
650115-C 66200 41-1/16 (1043) 21-25/32 (553)
650115-1C 66200-1 41-1/16 (1043) 21-25/32 (553)
PUMP
Lower Pump
(see chart below)
Material Inlet
“A”
(mm)
Inches
Figure 1
“B”
Inches
(mm)
The pump sound pressure level has been updated to an
Equivalent Continuous Sound Level (LAeq
ANSI SI.13-1971, CAGI-PNEUROP S5.1 using four microphone
locations.
INGERSOLL RAND COMPANY LTD
209 NORTH MAIN STREET – BRYAN, OHIO 43506
(800) 495-0276 FAX(800) 892-6276
www.ingersollrandproducts.com
) to meet the intent of
© 2011
CCN 81561318
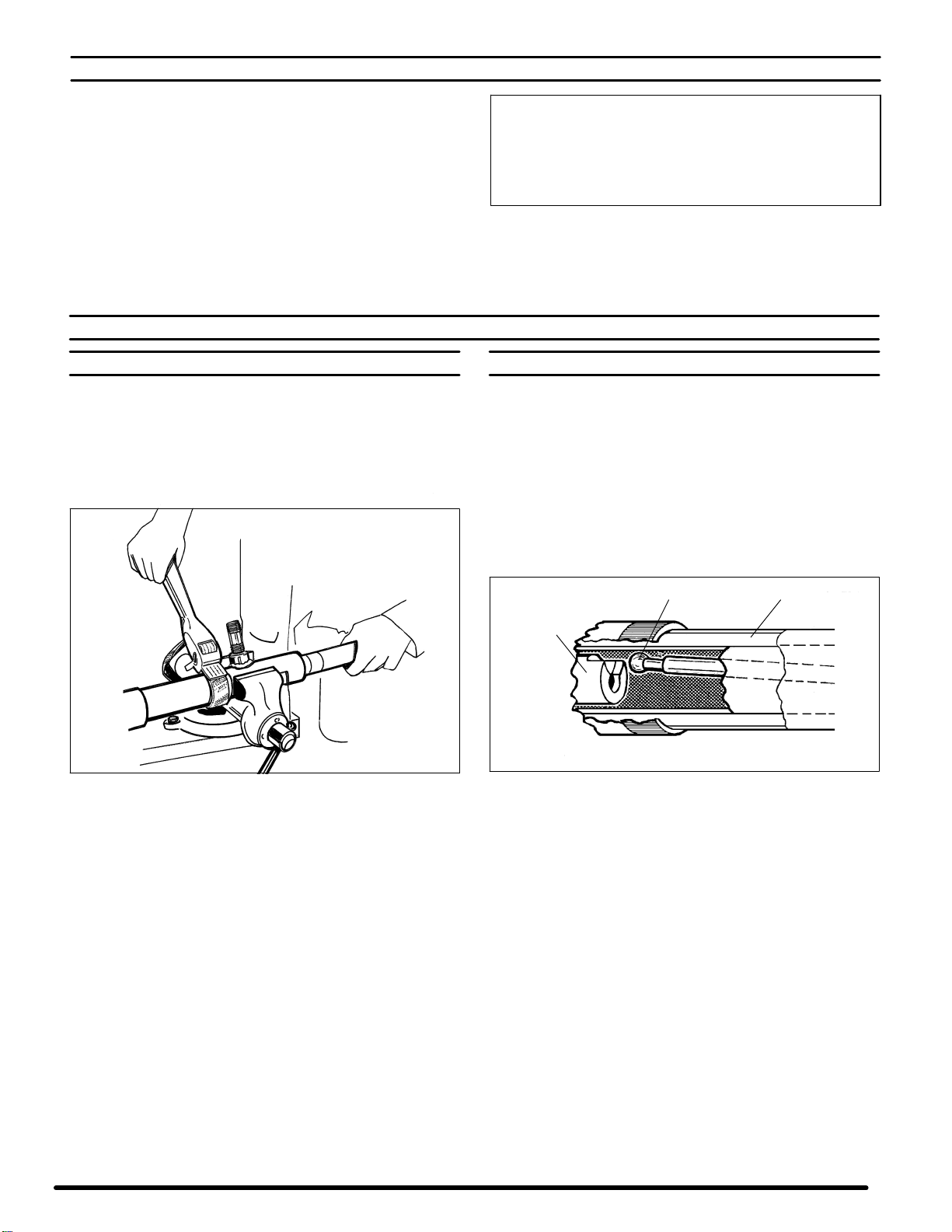
GENERAL DESCRIPTION
The ARO 2” differential, 2:1 ratio transfer pumps have been designed for
the application and transfer of a wide range of corrosive and non-corrosive materials. Refer to the lower pump parts list on page 4 for manufactured materials and packings available. These pumps may be directly
mountedin the 2” bung of a standard drum or when using a 61113 mounting bracket, the pump can be mounted on the wall or in an open head
drum.
The air motor is connected to the lower pump end by a spacer tube, this
protects the air motor section from possible contamination due to normal
wear and eventual leakage of material past the upper material piston
seals.
PUMP SERVICE PROCEDURES
PUMP DISASSEMBLY
RefertoFigure2.
NOTE: All threads are right hand.
1. Thread a 1/2” nipple into the material outlet.
2. Place the 2” differential pump assembly in a vise as shown. Rotate
the pump assembly so that the 1/2” nipple is resting against the vise.
CAUTION: Do not clamp the pump tightly.
INLET PRESSURE TO PUMP MOTOR
PUMP RATIO X
Pump ratio is an expression of the relationship between the pump motor area and the
lower pump end area. EXAMPLE: When 150 p.s.i. (10.3 bar) inlet pressure is supplied
to the motor of a 2:1 ratio pump it will develop a maximum of 300 p.s.i. (21 bar) fluid pressure (at no flow) - as the fluid control is opened, the flow rate will increase as the motor
cycle rate increases to keep up with the demand.
MAXIMUM PUMP
=
FLUID PRESSURE
Refer to General Information sheet for safety precautions and important
information.
PUMP REASSEMBLY
RefertoFigure3.
1. Place the 2” air motor in a vise with the needle valve or pipe nipple
resting against the jaws of the vise, as shown.
2. Insert the 90826 tip of the lower pump assembly into the 76216 separating tube of the air motor.
3. Insert the 90826 tip of the lower pump assembly through the outside
edge of the slot in the 76208 plunger tip, center the 90826 tip in the
76208 plunger tip and pull out until the 90826 tip is retained.
4. Thread the air motor into the material outlet body and tighten by using a strap wrench on the air motor 76216 separating tube.
Figure 2
3. Unthread the air motor from the material outlet body by using a strap
wrench on the air motor separating tube.
4. Push the connecting rod, in the lower pump assembly, to one side
and pull down until the air motor separates from the lower pump assembly.
5. The pump is now in two assemblies: air motor and lower pump assembly.
90826 76216
76208
Figure 3
Page2of8 650110-X

2” AIR MOTOR SERVICE PROCEDURES
2” AIR MOTOR DISASSEMBLY
RefertoFigure4.
NOTE: All threads are right hand.
1. Place the air motor in the vise with a needle valve or a 1/4” pipe nipple resting against the jaws of the vise, as shown.
2. Placea strap wrench around the (1) cap and remove the cap. NOTE:
If the (6) cylinder comes off with (1) cap, place the cap in a vise and
use a strap wrench around the cylinder and unscrew from cap.
NOTE: Do not squeeze or use pipe wrench on (6) cylinder.
3. Place a strap wrench around the (6) cylinder and unscrew and remove the cylinder.
4. Pull the (7) spacer and piston assembly and (15) plunger out of the
(18) pump body and lay aside.
5. Remove the (17) valve spring and (16) “O” ring from the (18) pump
body.
6. Place the (18) pump body in the vise and loosen the (21) lock ring
with a strap wrench.
7. Place a strap wrench around the (22) separating tube and unthread.
8. Remove the (20) washer and (19) “O” ring from the (18) pump body.
9. Clamp the flats of the (7) spacer and piston assembly in the vise. Remove the plunger tip from the (7) spacer and piston assembly.
NOTE: Do not remove the (13) plunger tip from the (15) plunger, unless replacing parts.
10. Removethe (12) gasket from the (13) plunger tip. NOTE: Do not mar
or damage o.d. of (15) plunger.
11. Remove the three (8) screws from the spacer and piston assembly.
12. Remove the (9) valve plate and (11) valve spacer.
Figure 4
S LoctiteR is a registered trademark of Henkel Loctite Corporation S
Page3of8650110-X