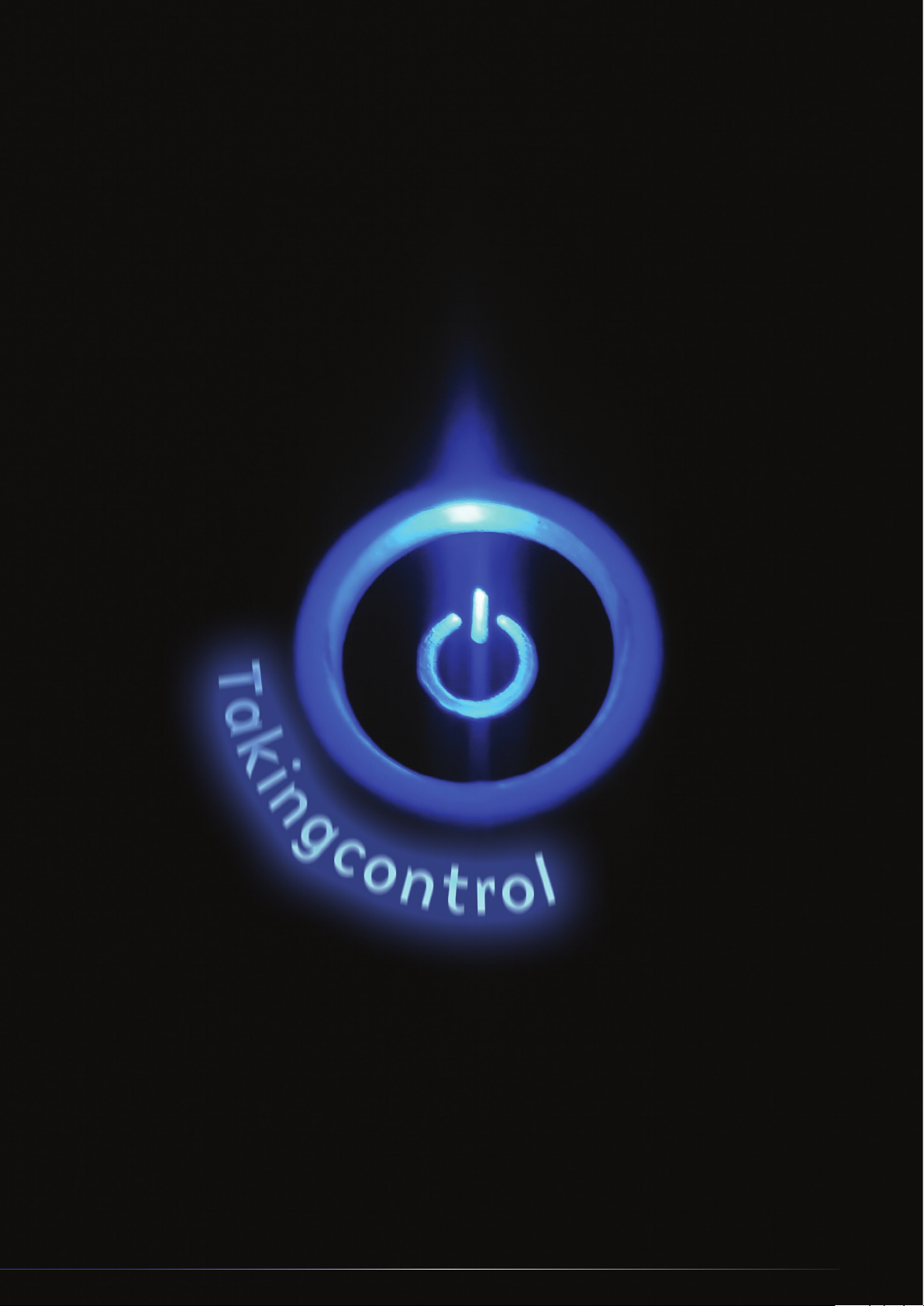
T
a
k
i
n
g
c
o
n
t
r
o
l
Reprinted from HydrocarbonENGINEERING February2008 www.hydrocarbonengineering.com
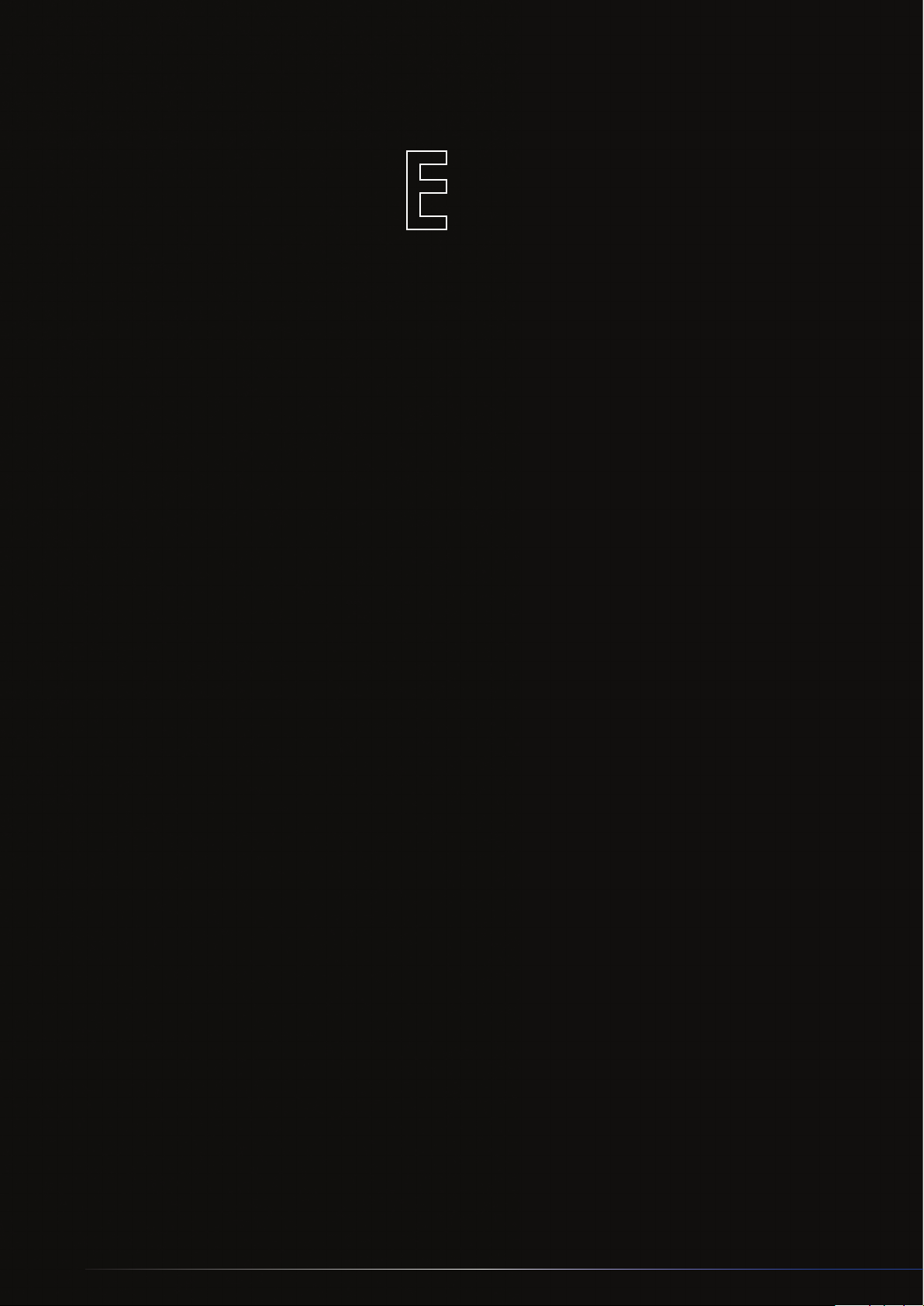
ven though Repsol YPF’s La Plata refinery in Argentina
is the country’s largest with an annual output of
200 000 bpd, the facility is challenged to meet
growing customer demand. It, along with sister
refineries in Lujan de Cuyo and Plaza Huincul, are at
near maximum production capacity, responding to one of the
fastest growing economies in the Americas. Economic growth
for Argentina is over 8%, and is expected to stay that way for the
foreseeable future.
Repsol YPF plans to capitalise on this growth by investing
nearly US$ 7 billion in Argentine operations through 2009 for
exploration and production activities, as well as logistics and
marketing. A portion of that funding will be going to the La Plata
refinery located 60 km from Buenos Aires, on the banks of the
Rio de la Plata. The operation is massive, with some 35 process
units occupying an area of 750 acres.
Located within the La Plata refinery complex is a critical
operation. It is the Departamento de Operaciones de Lubricantes
Juan Carlos Bondarenko,
ABB, Argentina,
discusses the
improvements made at
Argentina’s largest
refinery through
advanced
technology.
involved sophisticated process control. That was the route that
the company followed.
y Especialidades or DOLE plant, which
produces lubricants and specialties such
as asphalt, paraffins and derivatives. The
La Plata refinery also produces fuel oil,
diesel oil and gasoline. The lubricants
blending operation faced a multiple
marketing challenge regarding a product
portfolio extension, reduction of batch
sizes, and heavier customer restraints.
Additionally, it has a reputation for
continuous improvement as its operations
manager pursues methods to increase its
output.
The situation called for a creative
solution that was both timely and
cost effective. The best alternative
Application of advanced process
control
Repsol YPF decided to replace the existing control system with
a plant-wide control system from ABB, its Industrial IT System
800xA Extended Automation. This scalable, extended automation
system for process and production control, safety and production
monitoring is designed to extend the reach of traditional
automation systems beyond control of the process to achieve
production gains necessary to meet business targets.
Some of the key decision factors were the system’s object
technology, which can include aspects such as documentation,
production orders, raw material and laboratory analysis. It
operates with standards such as Microsoft technologies. There is
also enterprise connectivity to existing systems such as SAP, and
the fact that ABB provides a local presence and support for its
products and systems.
The system is unique as this scope is accessible from a
single user interface that is configured to present information and
provides interaction in a context appropriate to all user disciplines.
Extended automation objects created within the engineering
environment provide the foundation for the efficient development,
www.hydrocarbonengineering.com Reprinted from February2008 HydrocarbonENGINEERING