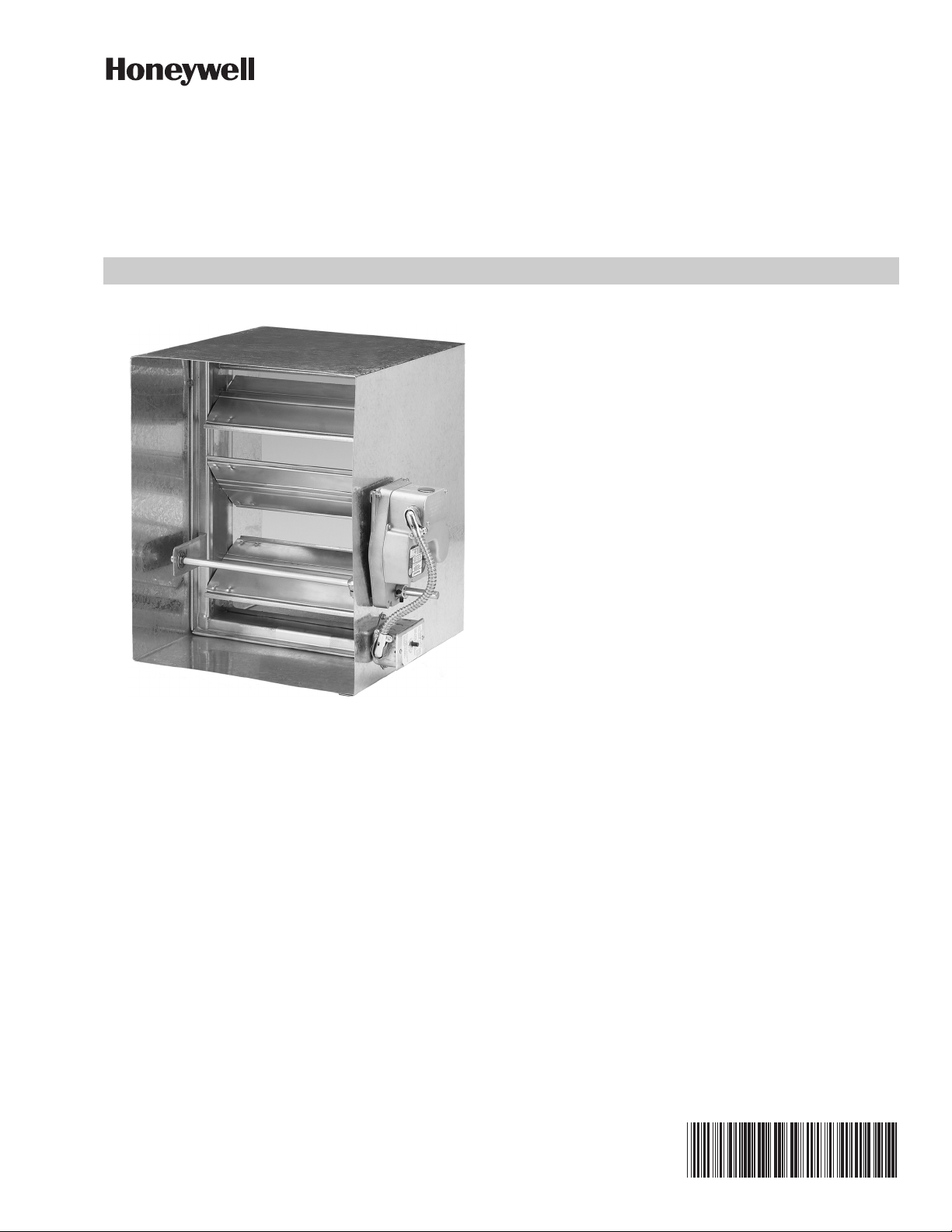
Fire and Smoke Damper Actuator
Field Replacement Guide
REPLACEMENT GUIDE
The following guidelines are crucial to keep fire and smoke
damper assemblies operating properly, and to stay in
adherence to standards and codes.
FIRE CODE REFERENCES AND
INFORMATION
Honeywell Fire and Smoke Actuators are designed to meet
both UL555 and UL555S safety requirements for
combined fire and smoke applications, if applicable.
The following maintenance guidelines are a summary of
the National Fire Protection Association (NFPA) Codes as
well as Air Movement and Control Association (AMCA) and
Honeywell manuals. We recommend that you become
familiar with NFPA 80, 90A, 92A & B, and 105 and AMCA
publication 503. Be aware that other codes, such,
International Building Code (IBC), regional, state and local
codes, may also apply to your area.
APPLICATION
Safety should never be left to chance. Honeywell fire and
smoke actuators are designed to meet both UL-555 and
UL555S 350°F safety requirements for fire and smoke
applications, if applicable. Fast-acting actuators close
dampers in 15 seconds, and the integral spring return
ensures the consistent, proper level of torque. For the
highest level of occupant safety, you can count on
Honeywell.
Fire and Smoke actuators and assemblies must function
properly during a fire or life-safety emergency. Honeywell
Fire and Smoke Actuators provide fast action when
timeliness is key in preventing the spread of fire and
smoke. Proper installation and periodic performance
testing are required to ensure fire and smoke damper
assemblies will fully function should an emergency occur.
REPLACEMENT GUIDELINES
Actuator Specifications
UL555 and UL555S require fire and smoke actuators to be
tested to 20,000 close and reopen cycles and close within
75 seconds. UL555 also requires them to be rated to either
250°F or 350°F. If UL does not apply to your region, please
omit.
Honeywell fire and smoke actuators are rated to 30,000
cycles, operate within 15 seconds, and are rated to 350°F.
Applications
Combined Fire and smoke dampers are used to maintain
fire barrier ratings when walls and floors are penetrated by
ductwork.
Smoke dampers are used to prevent the passage of smoke
through the HVAC system or from one side of a fire-rated
separation to the other. They may be dedicated to this
function or also function as HVAC dampers.
38-00001-02

FIRE AND SMOKE DAMPER ACTUATOR FIELD REPLACEMENT GUIDE
Damper Manufacturer’s Guidelines
When replacing actuators, it is important to follow the
guidelines that are provided by the damper manufacturer
for the damper assembly. When replacing a fire and smoke
actuator the replacement should be either like-for-like
with the original, factory-mounted actuator, or a
technically superior product where the total assembly has
passed UL testing with the damper manufacturer.
Please refer to the damper manufacturer’s guidelines for
details.
MAINTENANCE
INFORMATION
Fire and Smoke damper assemblies must undergo
periodic performance testing to be properly maintained
and to ensure they are functioning and will function in a
fire or life-safety emergency.
The NFPA codes require combined fire and smoke
dampers be tested and inspected at the time the system is
commissioned, after it has been balanced, and one year
after installation. Then they need to be tested and
inspected every 4 years, except in hospitals, where they
need to be tested and inspected every 6 years. See "Option
1” and “Option 2” in this section for detailed test
instructions.
AMCA suggests that smoke dampers be tested at least
semi-annually. Smoke dampers should be operated, and
the correct outputs should be observed, to verify
operation. These tests need to also be conducted under
standby power, if used.
c. Use the signal from the damper’s position indi-
cation device to confirm that the damper reaches
its fully-closed position.
d. Re-apply electrical power to re-open the damper.
e. Use the signal from the damper’s position indi-
cation device to confirm the damper reaches its
fully-open position.
Option 2: Dampers without position indication:
a. Visually confirm that the damper is fully-open
position.
b. Ensure that all obstructions, including hands,
are out of the path of the damper blades.
c. Remove electrical power or air pressure from the
actuator to allow the actuator’s spring return fea-
ture to close the damper.
d. Visually confirm that the damper closes com-
pletely.
e. Re-apply electrical power to re-open the damper.
f. Visually confirm that the damper is in the fully
open position.
3. If the damper is not operable, it must be repaired as
soon as possible. If the actuator has failed, replace it
with a UL approved actuator if required. See Table 1.
See Figs. 2-3 for mounting and installation information and Figs. 4-9 for wiring. After these repairs, the
damper should be tested again.
4. If there is a latch, verify that it is operable.
5. Perform any other damper manufacture recom-
mended maintenance such as lubrication.
6. Following the test and any repairs, document the
location of the damper, the date, the inspector, and
deficiencies or repairs. Keep the record for the life of
the damper, and have it available as you may need to
show it to an inspector.
Honeywell Fire and Smoke Actuators are found in
combination fire and smoke damper assemblies that use a
bi-metallic disc type thermostat to interrupt electrical
power to the actuator at a specified temperature. Once the
specified temperature is reached, power will be
interrupted and the spring return of the actuator will close
the damper. When these actuators are used in smoke
damper applications, they are usually controlled by smoke
detectors or fire alarms.
Periodic inspection includes:
1. Verify that there is full unobstructed access to the
damper
2. Test the damper with normal HVAC airflow and verify
that it opens following either Option 1 or Option 2.
There should be no interference due to rust, damaged frame or blades, or other moving parts.
Option 1: Dampers with Position Indication Wired to
indication Lights, or Control Panels:
Switches can be wired to local or remote control
panels or building automation systems (BAS) to
indicate that the damper is in the fully-open
position, fully-closed position, or neither.
a. Use the signal from the damper’s position indi-
cation device to confirm that the damper is in the
fully-open position.
b. Remove electrical power or air pressure from the
actuator to allow the actuator’s spring return feature to close the damper.
Fig. 1. Typical Fire and Smoke Damper Assembly.
Source: AMCA International: Guide for Commissioning
and Periodic Performance Testing of Fire, Smoke,
and other Life Safety Related Dampers, 2012.
38-00001—02 2
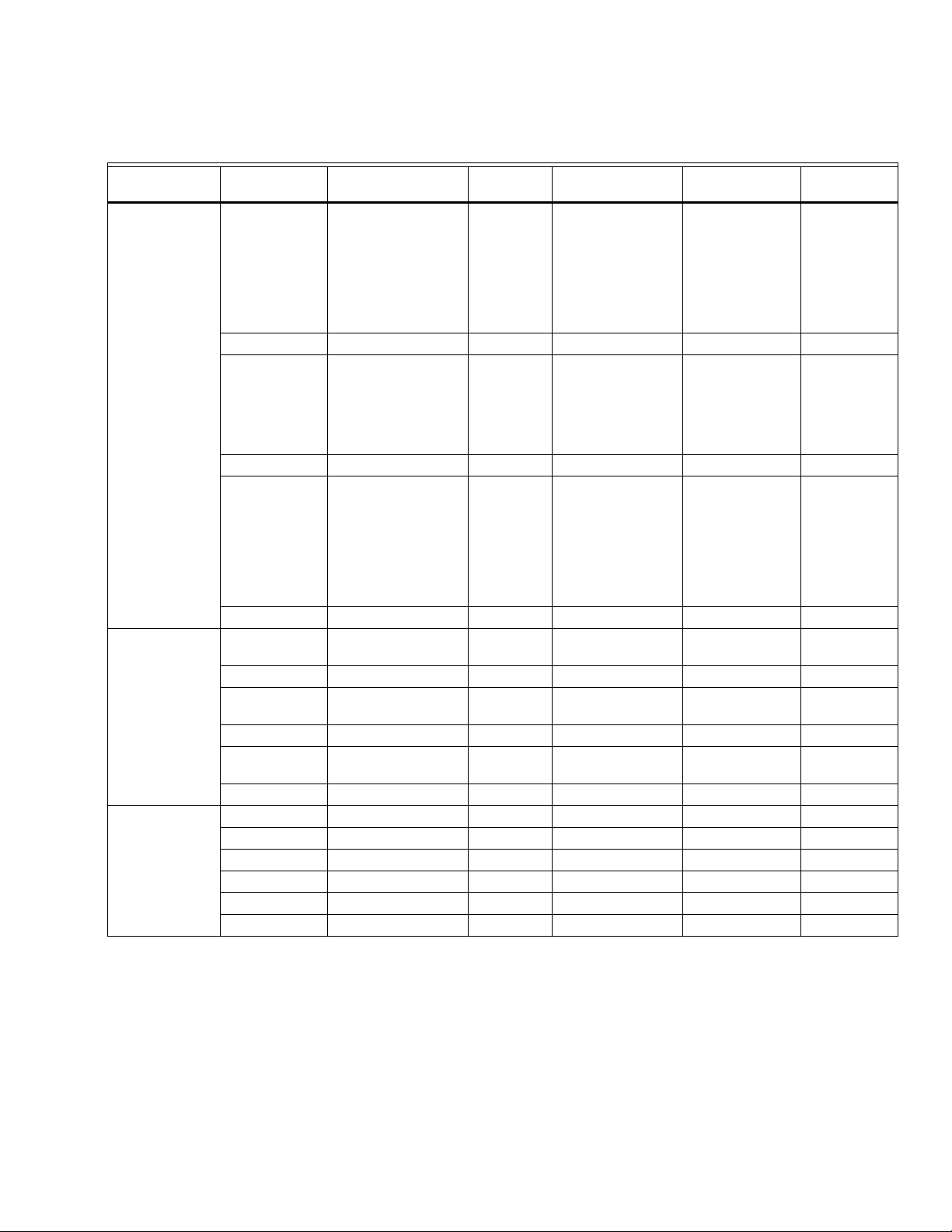
PRODUCT INFORMATION
FIRE AND SMOKE DAMPER ACTUATOR FIELD REPLACEMENT GUIDE
Tor que
30 lb-in
(3.4 Nm)
80 lb-in (9 Nm)
175 lb-in
(20 Nm)
Model
Number Voltage
120 Vac 0 ML4115A1009
MS4104F1010
MS4104F1210 120 Vac 2 Internal None FSLF120-S US None
MS4604F1010 230 Vac 0 ML4115C1007
MS4604F1210 230 Vac 2 Internal None FSLF230-S US None
MS8104F1010 24 Vac 0 ML8115A1005
MS8104F210 24 Vac 2 Internal None FSLF24-S US None
MS4109F1010
MS4109F1210 120 Vac 2 Internal None FSNF120-S US GND226.1U
MS4609F1010 230 Vac 0 MS4709F1014
MS4609F1210 230 Vac 2 Internal None FSNF230-S US GND326.1U
MS8109F1010 24 Vac 0 MS8209F1003
MS8109F1210 24 Vac 2 Internal None FSNF24-S US GND126.1U
MS4120F1006 120 Vac 0 None FSAF120 US GGD221.1U
MS4120F1204 120 Vac 2 Internal None FSAF120-S US None
MS4620F1005 230 Vac 0 None FSAF230 US GGD321.1U
MS4620F1203 230 Vac 2 Internal None FSAF230-S US None
MS8120F1002 24 Vac 0 None FSAF24 US GGD121.1U
MS8120F1200 24 Vac 2 Internal None FSAF24-S US None
120 Vac 0 MS4209F1007
SPST
Aux Switch
Legacy
Honeywell
ML4115A1017
ML4115B1008
ML4115B1016
ML4115H1002
ML4115J1009
ML4202F1000
ML4302F1008
ML4115C1015
ML4115D1006
ML4115D1014
ML4702F1009
ML4802F1007
ML8115A1013
ML8115B1004
ML8115B1012
ML8115H1008
ML8115J1005
ML8202F1006
ML8302F1004
MS4309F1005
MS4809F1012
MS8309F1001
Belimo
Cross
FSLF120 US None
FSLF230 US None
FSLF24 US None
FSNF120 US GND221.1U
FSNF230 US GND321.1U
FSNF24 US GND121.1U
Siemens
Cross
Table 1. Fire and Smoke Cross Reference.
3 38-00001—02

FIRE AND SMOKE DAMPER ACTUATOR FIELD REPLACEMENT GUIDE
M34622
2 (51)
1 (25)
90
°
0
°
11/16
(17)
6-3/8
(161)
8-15/16
(227)
4 (102)
2 (51)
1/16
(2)
3-1/4 (83)
5-1/8 (130)
9/16 (14)
INSTALLATION AND WIRING
M20051A
3-15/16 (100)
2 (50)
1-9/16
(40)
8-5/8
(220)
10-11/16
(271)
2-15/16 (75)1/4 (6)
Fig. 2. Dimensions for MS4104, MS4109, MS4604,
MS4609, MS8104, and MS8109 Series actuators.
See the following literature for further details and
mounting instructions:
• Product Data and Installation Instructions: 63-2740
• Specification data: 38-00006
Fig. 3. Dimensions for MSXX20F actuators.
See the following literature for further details and
mounting instructions:
• Product Data and Installation Instructions: 63-2584
• Specification Data: 63-2592
38-00001—02 4

Wiring
M34624
24 VAC
BLACK
RED
L1
( )
L2
( )
YELLOW
YELLOW
BLUE
7° AUXILIARY
SWITCH
85° AUXILIARY
SWITCH
BLUE
WHITE
BLACK
GREEN
L1
( )
L2
( )
YELLOW
YELLOW
BLUE
BLUE
7° AUXILIARY
SWITCH
85° AUXILIARY
SWITCH
120 VAC
M34625
M34626
BLUE
BROWN
GREEN
230 VAC
L1
( )
L2
( )
YELLOW
YELLOW
BLUE
BLUE
7° AUXILIARY
SWITCH
85° AUXILIARY
SWITCH
M20053B
24 VAC
BLACK
RED
GREEN
MS8120F
L1
( )
L2
( )
YELLOW
YELLOW
BLUE
7° AUXILIARY
SWITCH
85° AUXILIARY
SWITCH
BLUE
FIRE AND SMOKE DAMPER ACTUATOR FIELD REPLACEMENT GUIDE
For 30 lb-in and 80 lb-in (3.4 Nm, 9 Nm)
models:
Fig. 4. Typical 24 Vac wiring.
For 175 lb-in (20 Nm) models:
Fig. 7. Typical 24 Vac wiring
MS4120F
( )
L2
120 VAC
( )
L1
WHITE
BLACK
GREEN
Fig. 5. Typical 120 Vac wiring.
Fig. 6. Typical 230 Vac wiring.
7° AUXILIARY
85° AUXILIARY
M20056B
( )
L2
230 VAC
( )
L1
7° AUXILIARY
85° AUXILIARY
BLUE
SWITCH
SWITCH
BLUE
YELLOW
YELLOW
Fig. 8. Typical 120 Vac wiring.
MS4620F
BLUE
BROWN
GREEN
BLUE
SWITCH
SWITCH
BLUE
YELLOW
YELLOW
Fig. 9. Typical 230 Vac wiring.
M20057B
5 38-00001—02

FIRE AND SMOKE DAMPER ACTUATOR FIELD REPLACEMENT GUIDE
By using this Honeywell literature, you agree that Honeywell will have no liability for any damages arising out of your use or
modification to, the literature. You will defend and indemnify Honeywell, its affiliates and subsidiaries, from and against any
liability, cost, or damages, including attorneys’ fees, arising out of, or resulting from, any modification to the literature by you.
Home and Building Technologies
In the U.S.:
Honeywell
3992
® U.S. Registered Trademark
© 2016 Honeywell International Inc.
38-00001—02 M.S. Rev. 11-16
Printed in United States