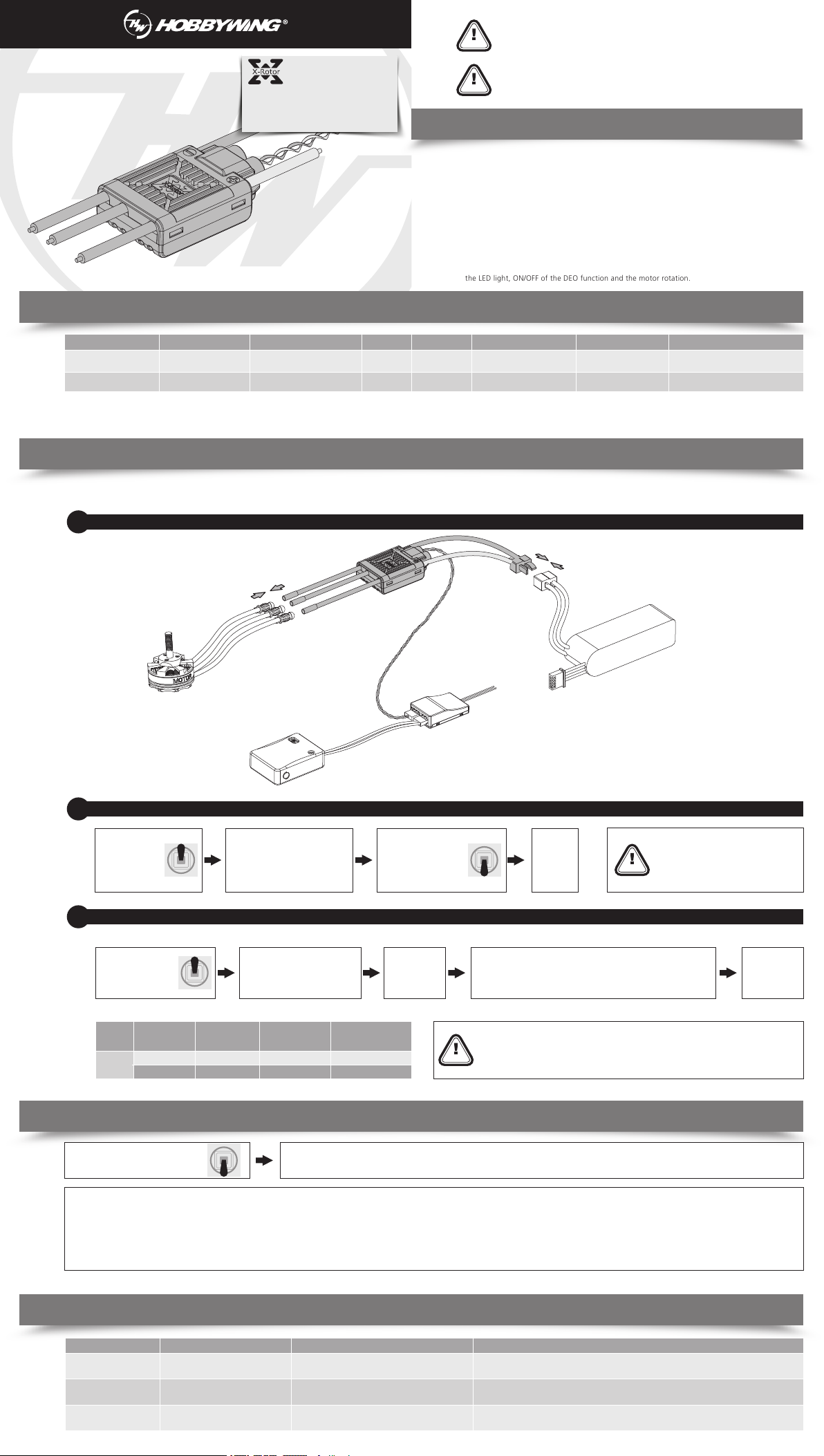
02
Specifications
USER MANUAL
Multi-Rotor
Brushless Electronic Speed Controller
XRotor Pro 40A • XRotor Pro 50A
Thank you for purchasing this HOBBYWING product! Brushless power systems can be
ATTENTION
CAUTIONS
Features
01
• Special core program for multi-rotor controllers greatly improves throttle response.
• DEO (Driving Efficiency Optimization) technology significantly improves throttle linearity and driving
efficiency.
• High intelligent and adaptive default settings like auto-adjusting timing meet almost all applications.
• The twisted-pair design of the throttle signal cable effectively reduces the crosstalk produced in
signal transmission and makes flight more stable.
• Compatible with various flight-control systems and supports a signal frequency of up to 621Hz.
(Note: all throttle signals over 500Hz are non-standard signals.)
• The high-light LED position on the XRotor Pro 50A ESC saves the trouble of mounting any extra
color light on multi-rotors.
• The DIP switches at the bottom of the XRotor Pro 50A ESC control the ESC ON/OFF status, color of
the LED light, ON/OFF of the DEO function and the motor rotation.
very dangerous. Any improper use may cause personal injury and damage to the
product and related devices. We strongly recommend reading through this user
manual before use. Because we have no control over the use, installation,
or maintenance of this product, no liability may be assumed for any damages or
losses resulting from the use of the product. We do not assume responsibility for any
losses caused by unauthorized modifications to our product.
Model Con. Current
XRotor Pro 40A
XRotor Pro 50A
Note: Version A (Wire Leaded) connects brushless motor via output wires, while Version B (COB-Connector On Board) with gold-plated connectors already directly soldered onto the printed circuit board of the
ESC, so Version B hasn't output wires.
03
User Guide
Throttle Calibration & ESC Programming
Users need to calibrate the throttle range when they start to use a new XRotor brushless ESC or another transmitter.
Motor Wiring
1
Throttle Range Calibration
2
Turn on the
transmitter, move
the throttle stick
to the top
position.
40A
50A
Motor
Peak Current (10s)
60A
70A
UBEC
Ensure the transmitter and receiver
are well bound, and then connect
the ESC to the battery.
(The receiver needs to be powered
by an extra power supply.)
BEC LiPo Programmable Item Weight Size
NO
NO
Electronic Speed Controller
Plug the UBEC cable into
the special battery (BATT)
channel or any other
unoccupied channel on
your receiver.
After the motor emits
two short “Beep-beep”,
move the throttle stick
to the bottom position
in 3 seconds.
3-6S
4-6S
Plug the throttle signal cable
into the throttle (TH) channel
on your receiver.
DEO(ON/OFF) and etc.
(See instructions below)
Receiver
DEO (ON/OFF)
Throttle
Calibration
completed
50g (Version A)
45g (Version B)
56g
Battery
IMPORTANT
We strongly recommend removing the
propellers for your own safety and the
safety of those around you before
performing calibration and programming
functions with this system.
66x21.8x11mm (Version A)
73.5x21.8x11mm (Version B)
48 x 30 x 15.5mm
ESC Programming
3
A) XRotor Pro 40A
Turn on the
transmitter, and then
move the throttle stick
to the top position.
B) XRotor Pro 50A
Dip
Switch
Option
04
Normal Start-up Process and Protections
Turn on the transmitter and move the
throttle stick to the bottom position.
• Start-up Protection: The ESC will shut down the motor if it fails to start the motor normally within 2 seconds by increasing the throttle value. In this case, you need to move the transmitter throttle stick back to
the bottom position and restart the motor. (Possible causes of this problem: poor connection/ disconnection between the ESC and motor wires, propellers are blocked, etc.)
• Over-load Protection: The ESC will cut off the power/output when the load suddenly increases to a very high value. Normal operation will not resume until the throttle stick is moved back to the neutral position.
The ESC will automatically attempt to restart when the motor and the ESC are out of sync.
• Throttle Signal Loss Protection: When the ESC detects loss of signal for over 0.25 second, it will cut off the output immediately to avoid an even greater loss which may be caused by the continuous high-speed
rotation of propellers or rotor blades. The ESC will resume the corresponding output after normal signals are received.
Trouble shooting
05
Switch #1
(LED Status)
On
Off
Connect the receiver to the
battery and ensure the transmitter
and receiver are well bound, and
then power on the ESC.
Switch #2
(LED Color)
Red
Green
Switch #3
(DEO Status)
The motor will
beep different
tones circularly.
Switch #4
(Motor Rotation)
On
Off
The motor will emit a long “beep —“1 second after the system is connected to the battery indicating the ESC is armed and the multi-rotor is ready to go.
CW
CCW
“Beep-beep-”Throttle Calibration; “Beep-beep-beep-”DEO ON;
“Beep-beep-beep-beep-” DEO OFF; If the throttle stick is moved to
the bottom position 3 seconds after you hear the corresponding
beeps, then the programming of that item is complete.
With the DEO ON, for better throttle linearity, the ESC will automatically brake and quickly
reduce the motor speed when decreasing the throttle amount. This can remarkably improve
the movement of the multi-rotors and the stability of its flight direction. Moreover, this also
IMPORTANT
improves the driving efficiency of the ESC and reduces its operating temperature.
Programming
is completed;
and the ESC is
ready.
Trouble
The ESC was unable
to start the motor.
The ESC was unable
to start the motor.
The ESC was unable
to start the motor.
Warning Tone
“Beep beep beep…”
(The motor beeps rapidly)
“Beep, beep, beep......”
(Time interval is 1 second)
“BB, BBB, BBBB”
(These tones are played circularly)
Possible Cause
The throttle stick is not at the bottom position.
No output signal from the throttle channel on
the receiver.
The“Normal / Reverse” direction of the throttle
channel on transmitter is incorrect.
Solution
Move the throttle stick to the bottom position or recalibrate the throttle range.
Check if the transmitter and receiver are well bound;
Check if the throttle wire has been properly plugged into the throttle channel on the receiver.
Refer to the transmitter instructions and correctly set the "Normal/ Reverse" direction of
the throttle channel.