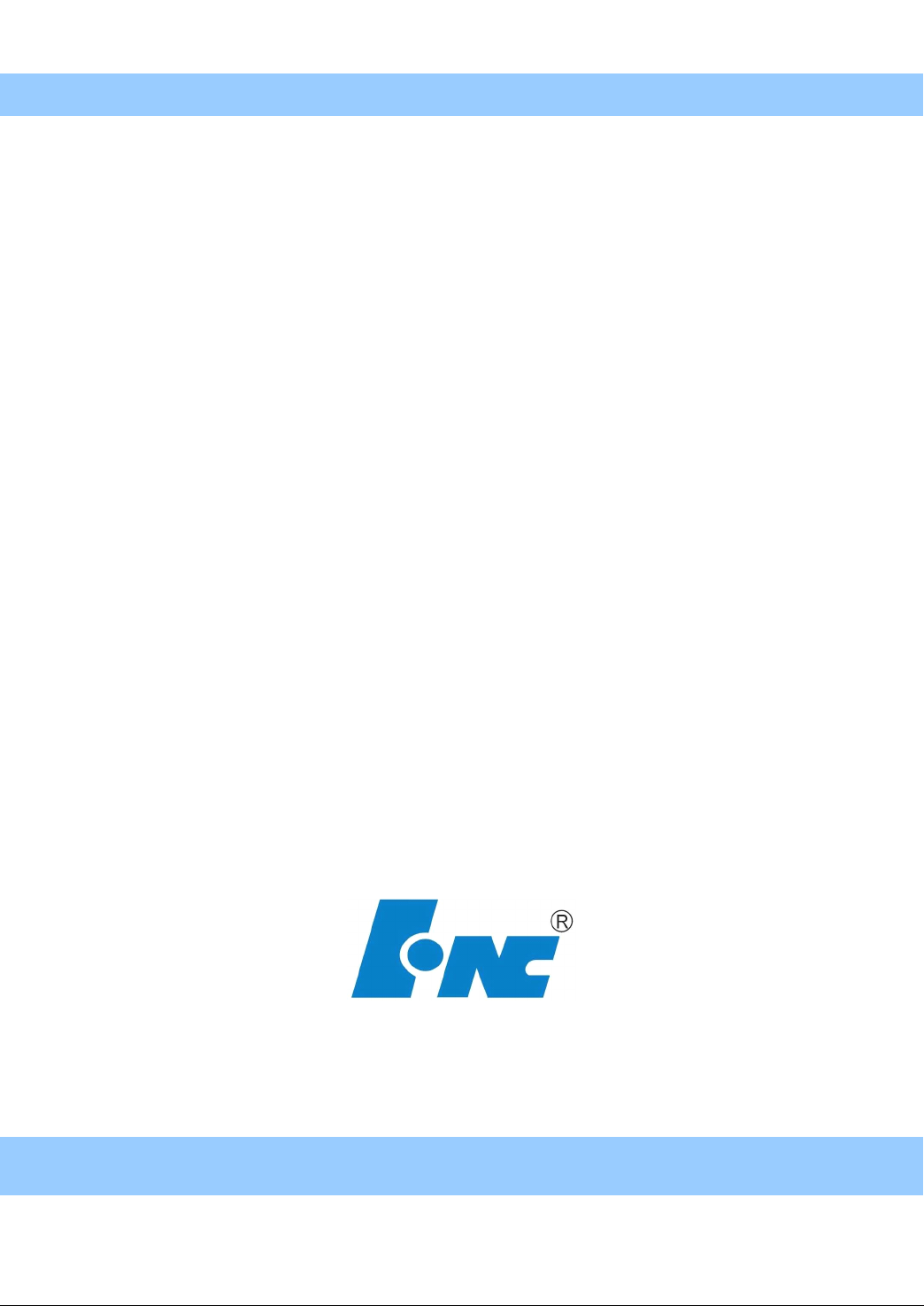
HNC-21/22
HNC-21/22
HNC-21/22
HNC-21/22 CNC
CNC
CNC
CNC Device
Device
Device
Device
Connection
Connection
Connection
Connection Manual
Manual
Manual
Manual
Wuhan
Wuhan
Wuhan
Wuhan Huazhong
Huazhong
Huazhong
Huazhong Numerical
V
2.0
V
2.0
V
V 2.0
2.0
20
10/11
20
10/11
20
20 10/11
10/11
Numerical
Numerical
Numerical Control
Control
Control
Control Co.
Co.
Co.
Co. Ltd
Ltd
Ltd
Ltd
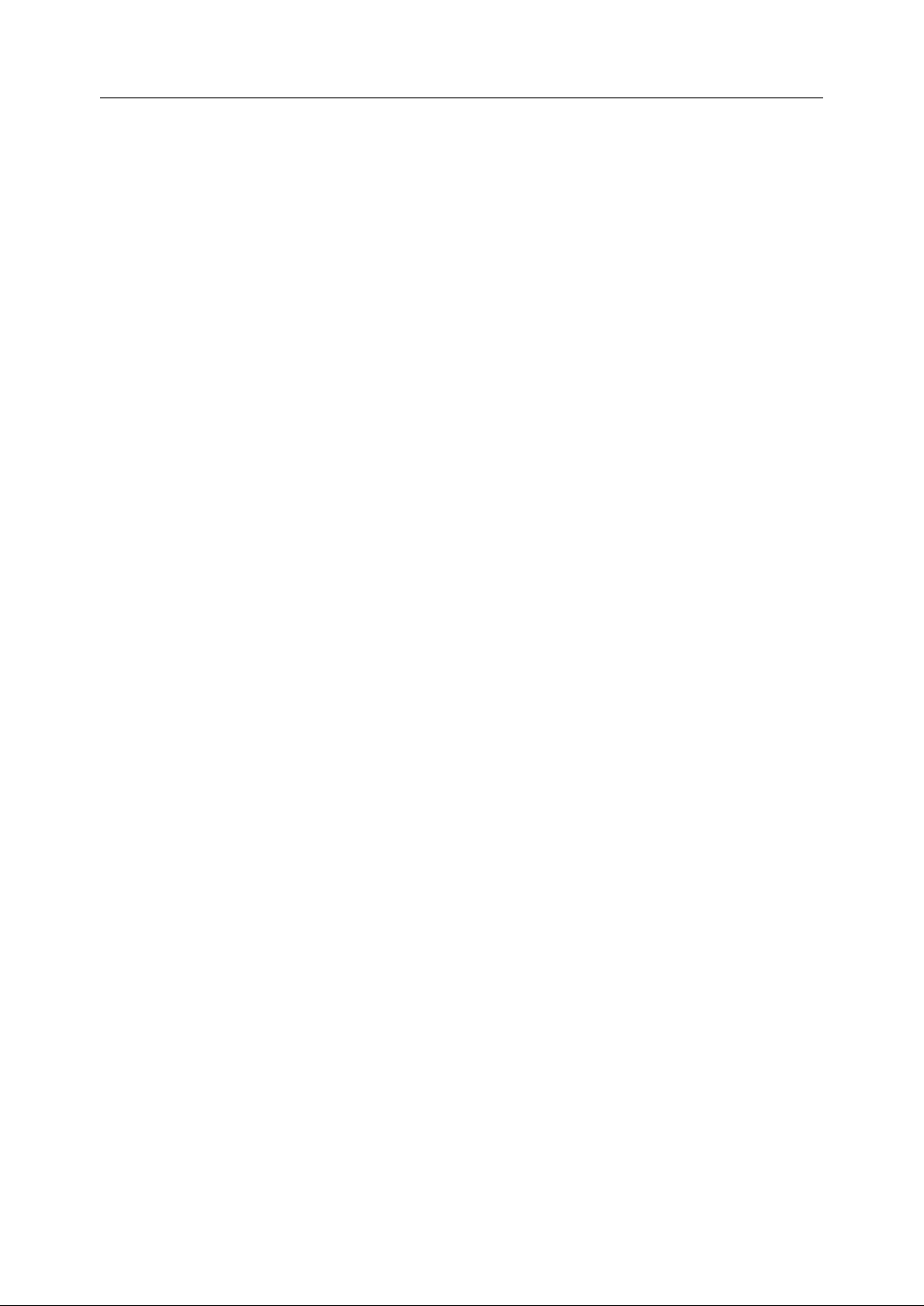
HNC-21/22 Connection Manual
Preface
Preface
Preface
Preface
This connection manual is for HNC-21/22 unit. It is recommended that the operator
read this manual before operating the machine.
The organization of this manual:
(1) Precaution
(2) Connection
(3) Parameters
(4) Commissioning
(5) Typical Design
(6) Appendix
i

HNC-21/22 Connection Manual
Introduction
Introduction
Introduction
Introduction
1.
HNC-
1.
1.
1. HNC-
HNC-21/22 (HNC- 21 /TD, HNC- 21 /M D, HNC-22/TD, HNC-22/MD ) possesses the
advanced open-structure, built-in industrial control computer, and high-performance
32-bit CPU. T here are 8.4’(HNC-21)/10.4’(HNC-22) LCD and standard panel for
machine tool engineering. It integrates feed axis interface, spindle interface,
handwheel unit interface, and built-in PLC ( Programmable Logic Circuits ) interface
as a whole. It supports the program storage form, and also supports the program
exchange through USB , DNC (Direct Numerical Control ) , Ethernet. According to its
high performance, compact structure, being easy to use, reliability, and reasonable
price, the Device is mainly suitable for numerical control of turning machines, milling
machines, and machining centers .
- Maximum coordinate axes: 6;
21/22
HNC-
21/22
HNC- 21/22
21/22
- Compatible with various pulsed AC servo drives, step motor drives;
- Standard panel for machine tool engineering is used . N o PLC input/output
interfaces are taken up. The color of machine control panel and the name of key
on the panel can be customized for different users.
- T here are 40 bit (extended to 60 bit) input interfaces , 32 bit optical isolated
output interfaces (extended to 48 bit), handwheel unit interface, analog spindle
control interface and spindle encoder interface.
- With 8.4’(HNC-21)/10.4’(HNC-22) LCD (the resolution is 640 × 480 ) , it is easy to
display the alarm message and simulation of tool - path.
- The program is written in ISO G code, compatible with any common CAD/CAM.
It can implement the linear interpolation, the circular interpolation, the helical
interpolation, the canned cycle, the rotation, the scale, the mirror image, the tool
compensation, the macro-program , etc.
- Machining a specified segment incrementally is especially suitable for machining
the compl icate moulds .
- The breakpoint can be saved and resumed , which provides the convenience and
safety for customers.
ii
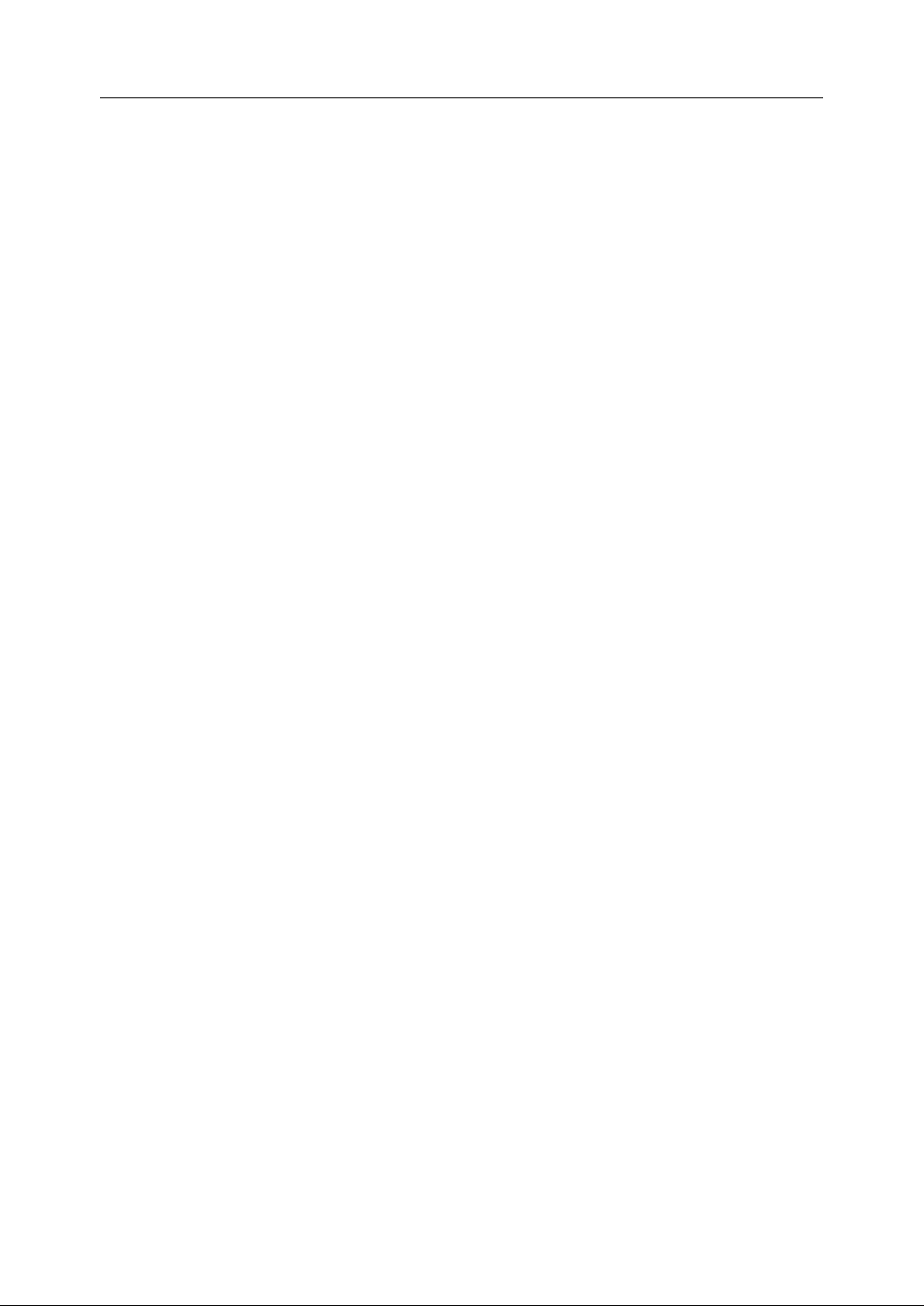
HNC-21/22 Connection Manual
- T he backlash and the uni-/ bi - directional pitch error compensation can improve
the machining precision effectively.
- It can save G code program up to 2GB.
- The data can be exchanged through RS232 or Ethernet .
- Flash RAM: 2GB is used to save the program (no cell is required).
- RAM: 32MB is used as a buffer for machining program .
Note: the default configuration of Flash RAM and RAM would not be notified
once again, if the size is increased.
- The dimension of device is 420 × 310 ×
2.
DNC
unit
2.
2.
2. DNC
DNC
DNC unit
(optional)
unit
(optional)
unit (optional)
(optional)
11
0 mm ( W × H × D).
DNC unit is a unit for interface switcher, which are DNC (RS-232) interface, PC
keyboard (PS2) interface, Ethernet interface .
Since there are DNC (RS-232) interface, PC keyboard (PS2) interface, and USB
interface on HNC-21, DNC unit is mainly used on HNC-22.
3.
Handwheel
3.
Handwheel
3.
3. Handwheel
Handwheel unit
unit
(optional)
unit
(optional)
unit (optional)
(optional)
- S tandard four -wire m anual pulse generator
- Four-axis switch
- Three kinds of magnification switch
- Emergency stop button
- Handwheel enabl e button
- Pilot lamps
4.
I/O
4.
I/O
4.
4. I/O
I/O Terminal
Terminal
Terminal
Terminal Board
Board
Board
Board
The I/O terminal board is connect ed to the optically isolated PLC inputs and outputs
through cables to facilitate wiring, commissioning and maintenance for the control
cabinet.
- 20-bit PLC inputs or 16-bit PLC outputs
- P ilot lamp on e ach input or output interface
- Both NPN and PNP interfaces are provided .
iii
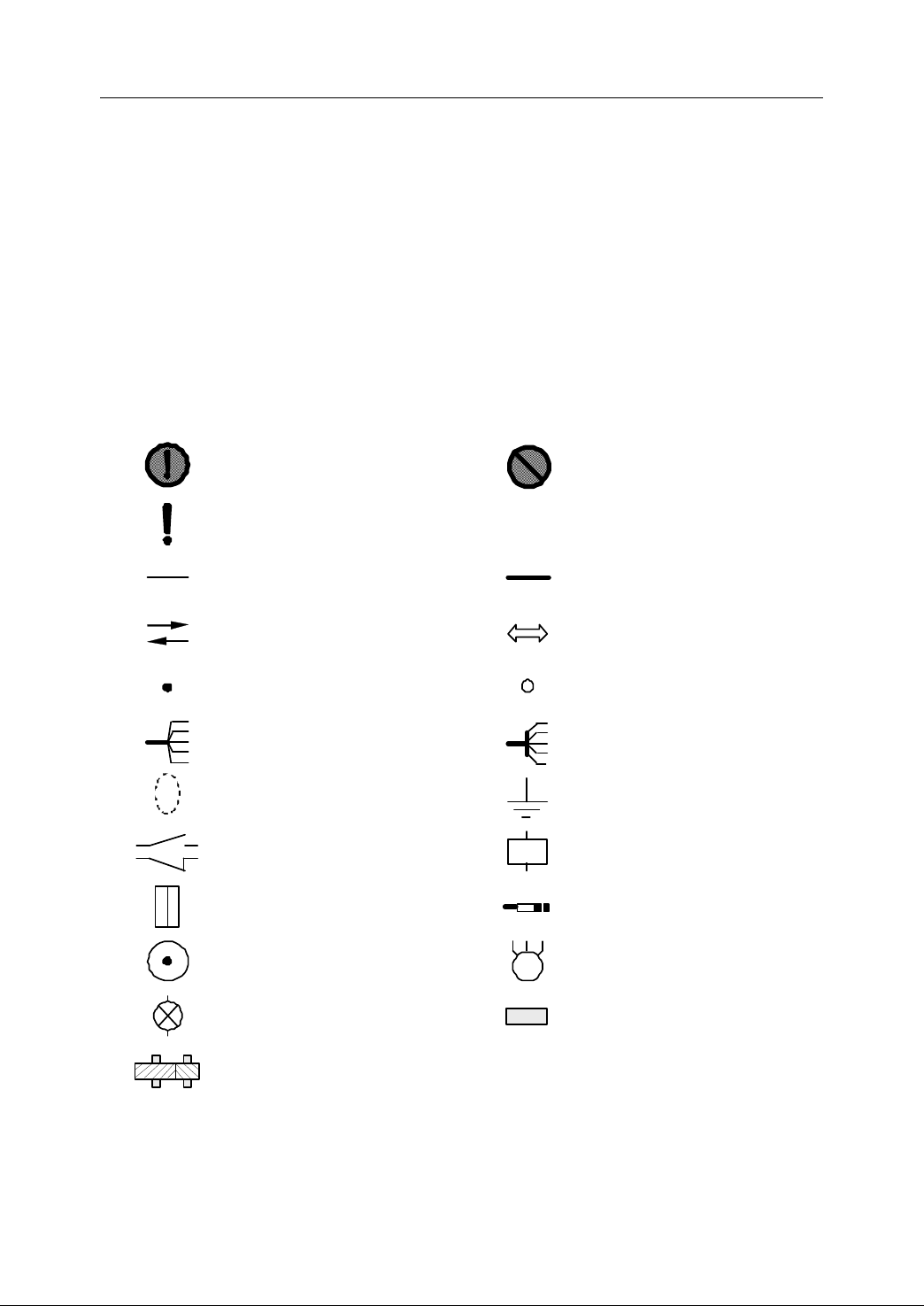
HNC-21/22 Connection Manual
5.
Relay
5.
Relay
5.
5. Relay
Relay Terminal
Terminal
Terminal
Terminal Board
Board
Board
Board (optional)
(optional)
(optional)
(optional)
I t is connect ed to the optically isolated PLC outputs through cables to facilitate wiring,
commissioning and maintenance for the control cabinet.
- 8 -bit PLC direct terminal out puts + 8-bit relay normally open contact point
outputs
- Two independent double-pole relays. Both normally open + normally closed
contact points are supported.
- P ilot lamp on e ach input or output interface .
II 图形符号系统 第 1 页 共 1 页
6.
Safety
6.
Safety
6.
6. Safety
Safety Placard
Placard
Placard
Placard
: m ust do.
; especially important
: line or boundary
: signal direction
: point connected
: cable bunched/diverged
: shielding layer
: passive NO and NC
: plug and socket
: encoder
【 】
: s h all not be done.
: default, initia l setting
: a set of cable
: exchange
: terminal
: cable bunched/diverged
: grounding
: coil
: transducer
: motor
: pilot lamp
: gearbox
iv
: mechanical linkage
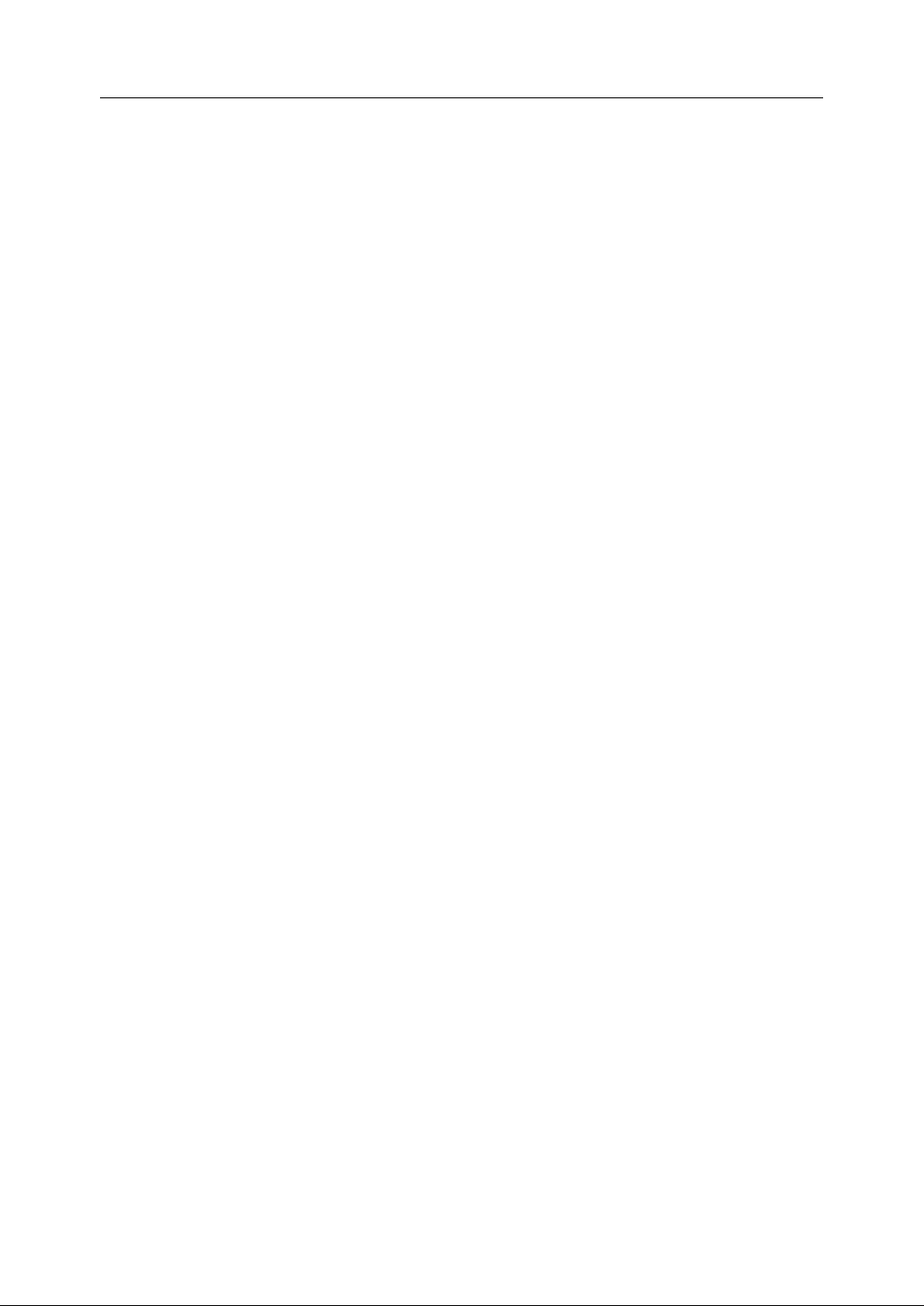
HNC-21/22 Connection Manual
Table
Table
Table
Table of
Preface .................................................................................................................................................................... i
Introduction ............................................................................................................................................................ ii
Table of Contents
1 Precaution .................................................................................................................................................... 1
1.1 Safety ...................................................................................................................... 2
1.2 Unpacking and Checking ........................................................................................ 6
1.3 Dimensions ............................................................................................................. 7
1.4 Installation .............................................................................................................. 8
1.5 Environmental Requirement ................................................................................. 10
2 Connection .................................................................................................................................................
2.1 Total Connection Diagram .................................................................................... 12
2.2 Interface ................................................................................................................ 13
2.3 Power Supply Connection .................................................................................... 17
2.4 Connection to DNC unit ....................................................................................... 20
2.5 Connection to Computer ....................................................................................... 21
2.6 PLC I/O Interface ................................................................................................. 24
2.7 Connection to Handwheel Unit ............................................................................. 36
of
Contents
of
Contents
of Contents
Contents
..................................................................................................................................................
1.1.1 Transportation and Storage ........................................................................ 2
1.1.2 Installation ..................................................................................................... 2
1.1.3 Wiring ............................................................................................................. 3
1.1.4 Commissioning ............................................................................................. 3
1.1.5 Operation ....................................................................................................... 4
1.1.6 Maintenance ................................................................................................. 4
1.1.7 Waste Treatment .......................................................................................... 5
1.1.8 General Instructions ..................................................................................... 5
1.2.1 List .................................................................................................................. 6
1.2.2 Product Type ................................................................................................. 6
1.5.1 Weather Condition ..................................................................................... 10
1.5.2 Elevation ...................................................................................................... 10
1.5.3 Transportation and Storage ...................................................................... 10
1.5.4 Mechanical Environment ........................................................................... 10
1.5.5 Environmental Pollution ............................................................................ 10
2.2.1 NC Device ................................................................................................... 13
2.2.2 DNC unit (optional) .................................................................................... 14
2.2.3 Handwheel unit (optional) ......................................................................... 14
2.2.4 I/O Terminal Boards (optional) ................................................................. 15
2.3.1 General Requirement ................................................................................ 17
2.3.2 Grounding .................................................................................................... 18
2.5.1 RS232 Interface ......................................................................................... 21
2.5.2 Ethernet Interface ....................................................................................... 21
2.6.1 Input interface ............................................................................................. 24
2.6.2 Output interface .......................................................................................... 27
2.6.3 Direct Connection to NC device ............................................................... 32
2.6.4 Connection to NC device through I/O terminal board ........................... 33
2.6.5 Description of PLC Address ..................................................................... 34
2.7.1 Handwheel Interface .................................................................................. 36
2.7.2 Connection to Standard Handwheel Unit ............................................... 37
v
11
v
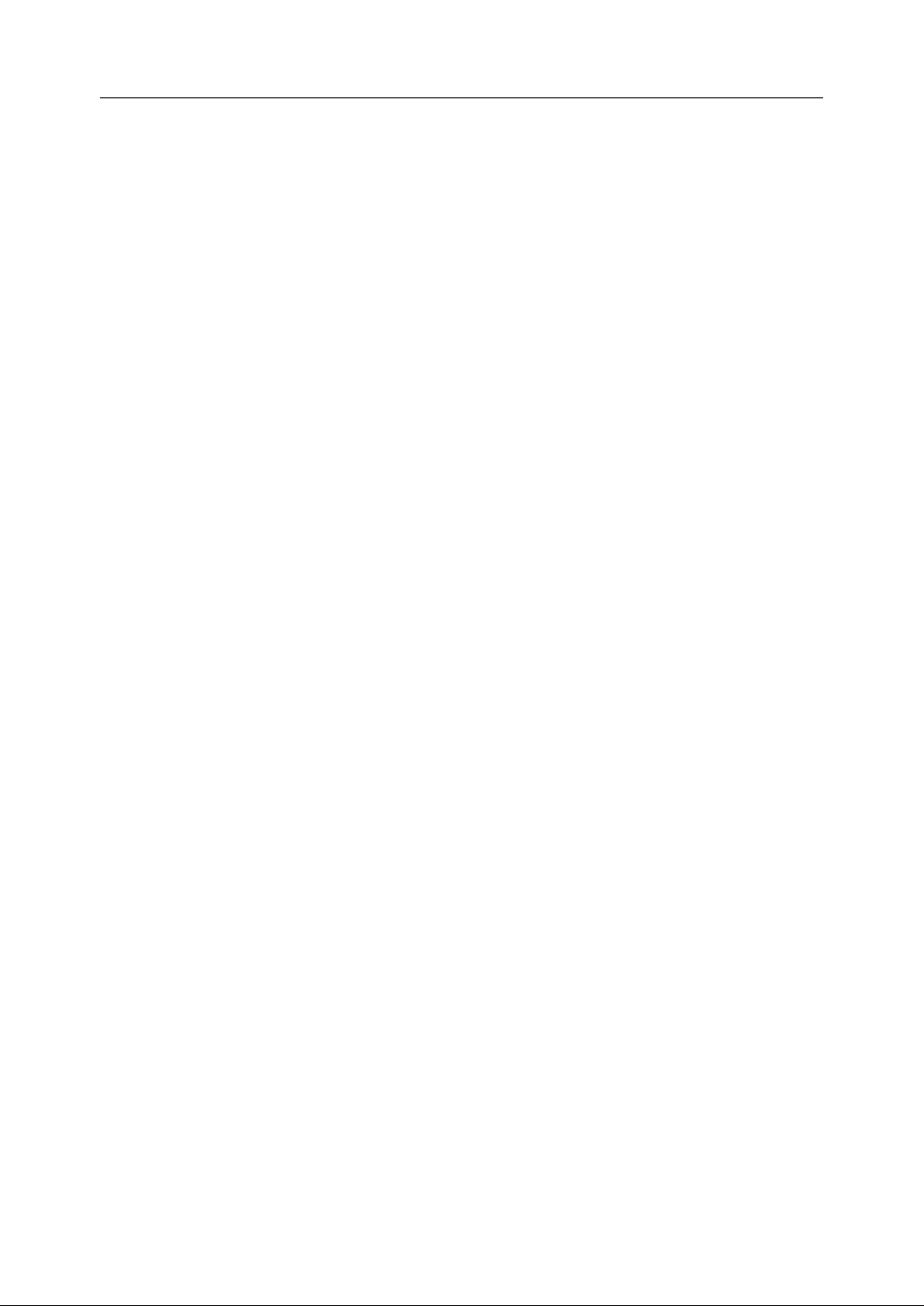
HNC-21/22 Connection Manual
2.7.3 Connection to Customized Handwheel Unit .......................................... 38
2.8 Connection to Spindle device ............................................................................... 39
2.8.1 Relevant Interfaces .................................................................................... 39
2.8.2 Spindle Start and Spindle Stop ................................................................ 40
2.8.3 Spindle Speed Control .............................................................................. 41
2.8.4 Spindle Orientation Control ...................................................................... 42
2.8.5 Spindle Gear Control ................................................................................. 43
2.8.6 Connection to Spindle Encoder ............................................................... 43
2.8.7 Connection Example ― AC Induction Motor ........................................... 44
2.8.8 Connection Example ― Spindle motor with driver .................................. 45
2.8.9 Parameters related to Spindle device ..................................................... 46
2.9 Connection to Feed Drive ..................................................................................... 47
2.9.1 Interface Description .................................................................................. 47
2.9.2 Connection to Stepper Motor Drive Unit ................................................. 48
2.9.3 Connection to Servo with pulse command ............................................. 50
2.10 Design of E-Stop and Overtravel Released .......................................................... 53
2.11 Design of Electromagnetic Compatibility ............................................................ 56
2.11.1 EMC of NC Device ..................................................................................... 56
2.11.2 Grounding .................................................................................................... 57
2.11.3 Check Interference from Power Network ............................................... 66
2.11.4 Anti-Interference ......................................................................................... 71
2.11.5 Prevention of Producing Interference ..................................................... 73
2.11.6 Summary of Design Guide ........................................................................ 79
3 Parameters
................................................................................................................................................
3.1 Overview .............................................................................................................. 84
3.2 Setting Parameters ................................................................................................ 85
3.3 Description of Parameters ..................................................................................... 86
3.3.1 Machine Parameters ................................................................................. 86
3.3.2 Axis Parameters ......................................................................................... 88
3.3.3 Servo Parameters ...................................................................................... 94
3.3.4 Axis Compensation Parameters .............................................................. 95
3.3.5 PMC User Parameters .............................................................................. 98
3.3.6 DNC Parameters ........................................................................................ 98
3.3.7 Quadrant Transition Parameters .............................................................. 99
4 Commissioning
........................................................................................................................................
4.1 Checking before Operation ................................................................................. 102
4.1.1 Inspection of Wiring ................................................................................. 102
4.1.2 Inspection of Power ................................................................................. 102
4.1.3 Inspection of Device ................................................................................ 103
4.2 Trial Operation .................................................................................................... 104
4.2.1 Power On .................................................................................................. 104
4.2.2 Setting Parameters .................................................................................. 104
4.2.3 Inspection of External Status .................................................................. 106
4.2.4 Servo Power On ....................................................................................... 108
4.3 PLC Commissioning ........................................................................................... 112
4.3.1 Main Elements of PLC Commissioning ................................................ 112
4.3.2 Process of PLC Commissioning ............................................................ 112
4.3.3 Methods for PLC Commissioning .......................................................... 113
4.4 Machine Commissioning .................................................................................... 114
4.4.1 Commissioning of Servo Parameters .................................................... 114
4.4.2 Machine Error Compensation ................................................................. 116
vi
83
101
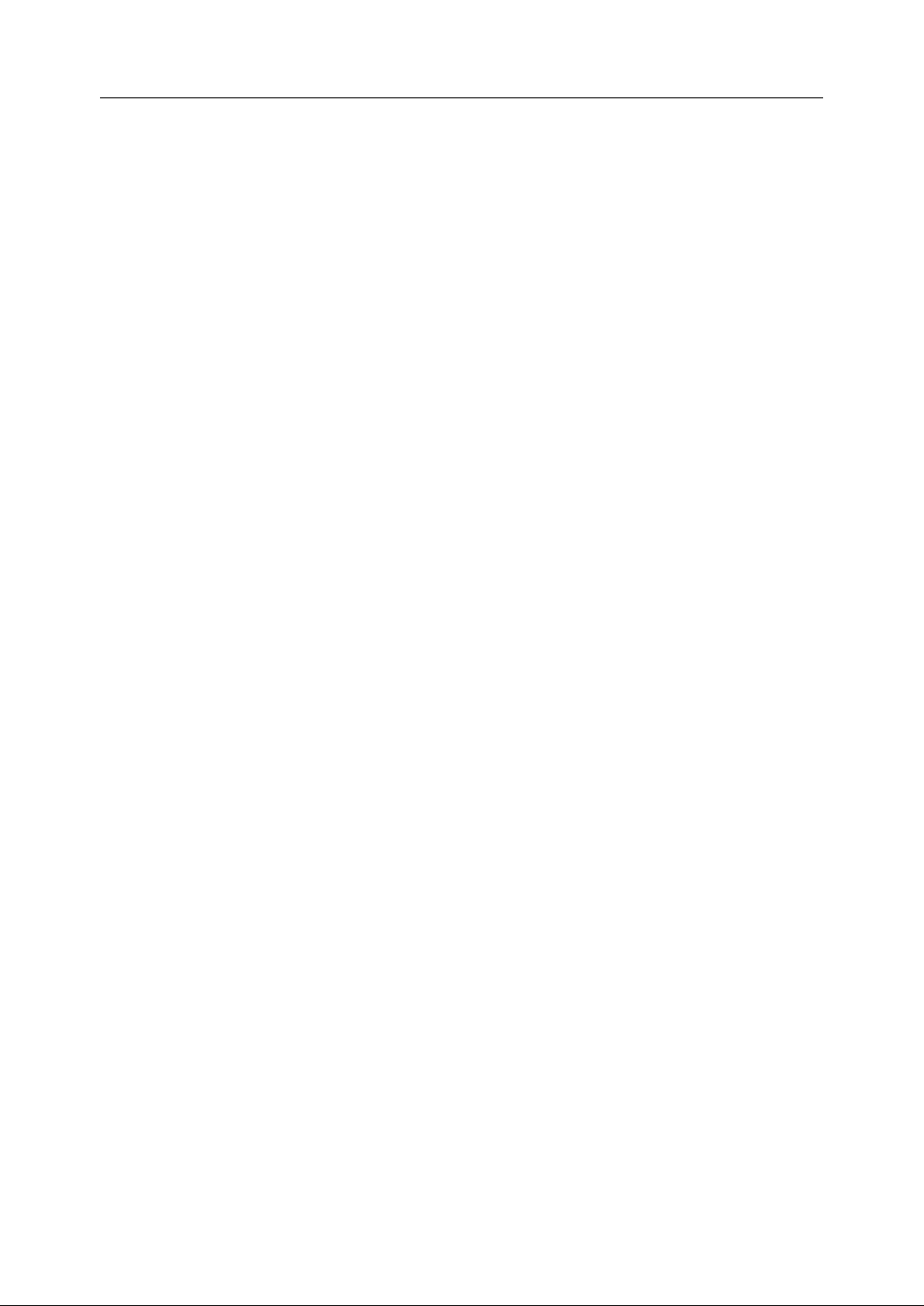
HNC-21/22 Connection Manual
4.5 Commissioning of Spindle D/A Parameters ....................................................... 120
5 Typical Design ......................................................................................................................................... 121
5.1 Overview ............................................................................................................ 122
5.2 Typical Design – NC Milling System ................................................................. 123
5.2.1 Brief Introduction ...................................................................................... 123
5.2.2 Overall Diagram ....................................................................................... 124
5.2.3 I/O Specification ....................................................................................... 124
5.2.4 Circuit Diagram ......................................................................................... 127
5.3 Typical Design – NC Turning System ................................................................ 135
5.3.1 Brief Introduction ...................................................................................... 135
5.3.2 Overall Diagram ....................................................................................... 135
5.3.3 I/O Specification ....................................................................................... 136
5.3.4 Circuit Diagram ......................................................................................... 138
6 Appendix .................................................................................................................................................. 144
6.1 Product Type ....................................................................................................... 145
6.2 Dimension ........................................................................................................... 146
6.2.1 NC Device ................................................................................................. 146
6.2.2 DNC Unit ................................................................................................... 147
6.2.3 Handwheel Unit ........................................................................................ 147
6.3 Interface Description .......................................................................................... 149
6.3.1 NC Device ................................................................................................. 149
6.3.2 DNC Unit (optional) .................................................................................. 154
6.3.3 Handwheel Unit (optional) ...................................................................... 154
6.4 Standard PLC I/O in milling system ................................................................... 156
6.5 Standard PLC I/O in turning system ................................................................... 158
vii
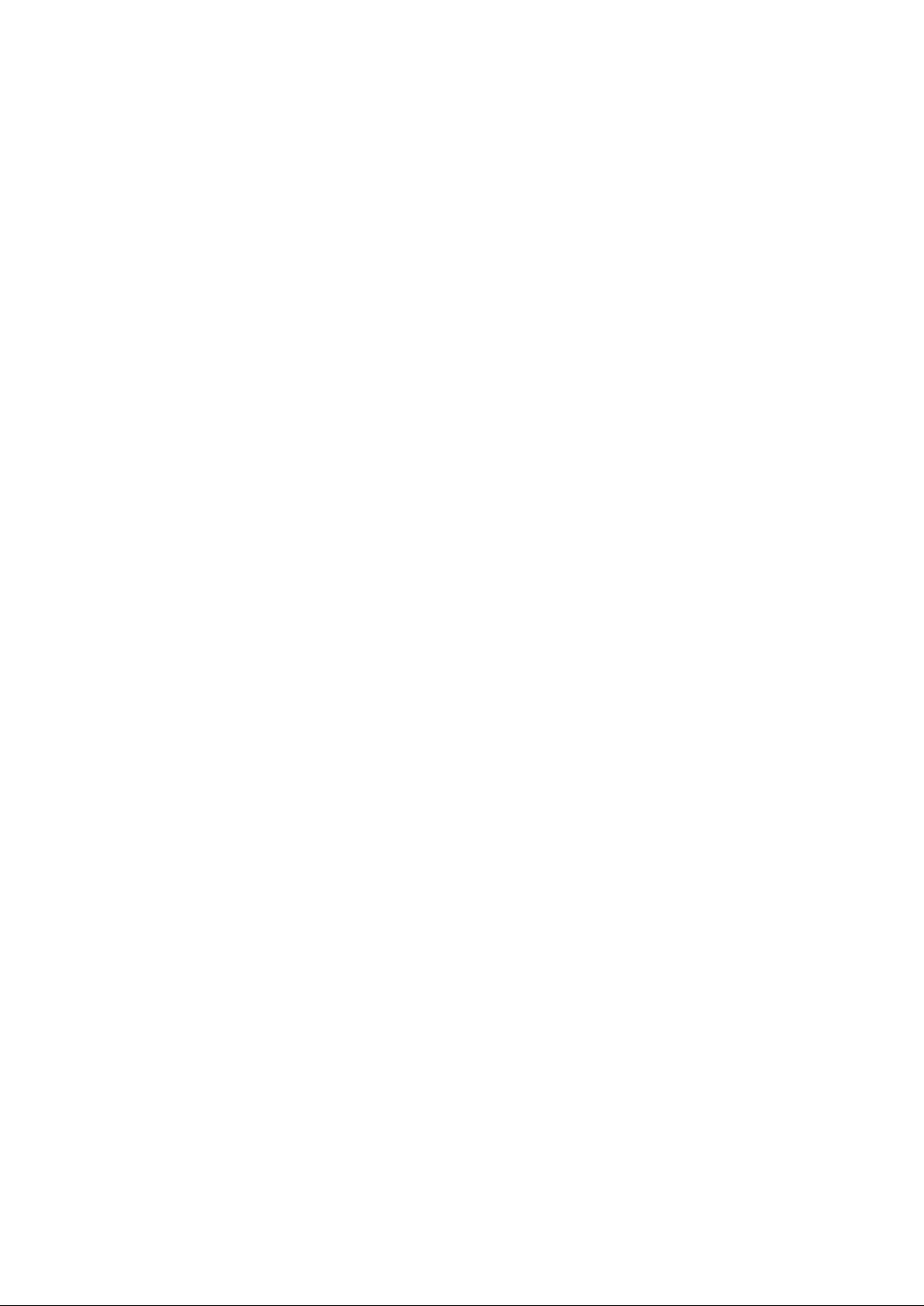
viii
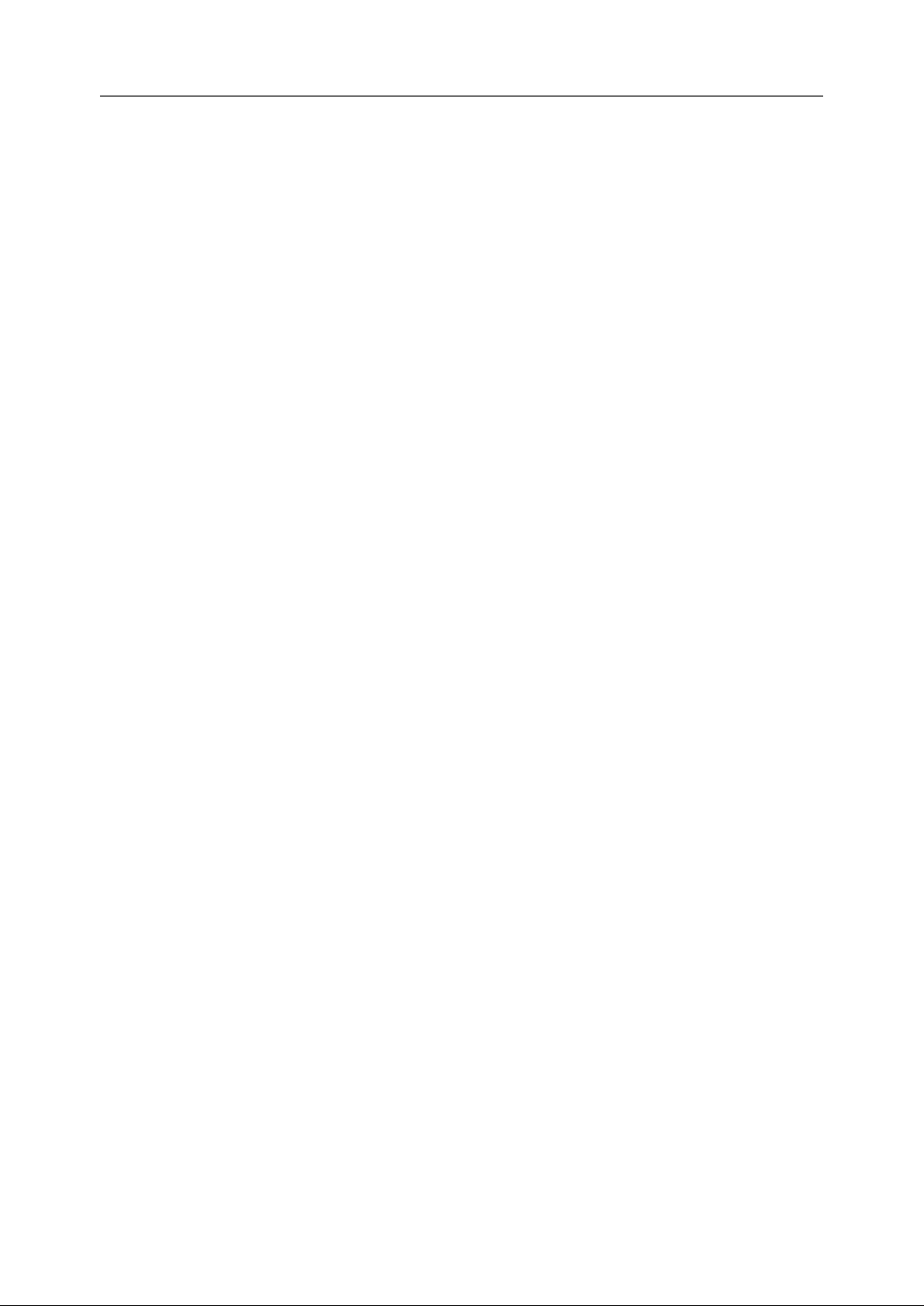
HNC-21/22 Connection Manual
1
Precaution
1
Precaution
1
1 Precaution
Precaution
To
protect the user and prevent damage to the machine, please read the following
precautions before attempting to use the machine.
1
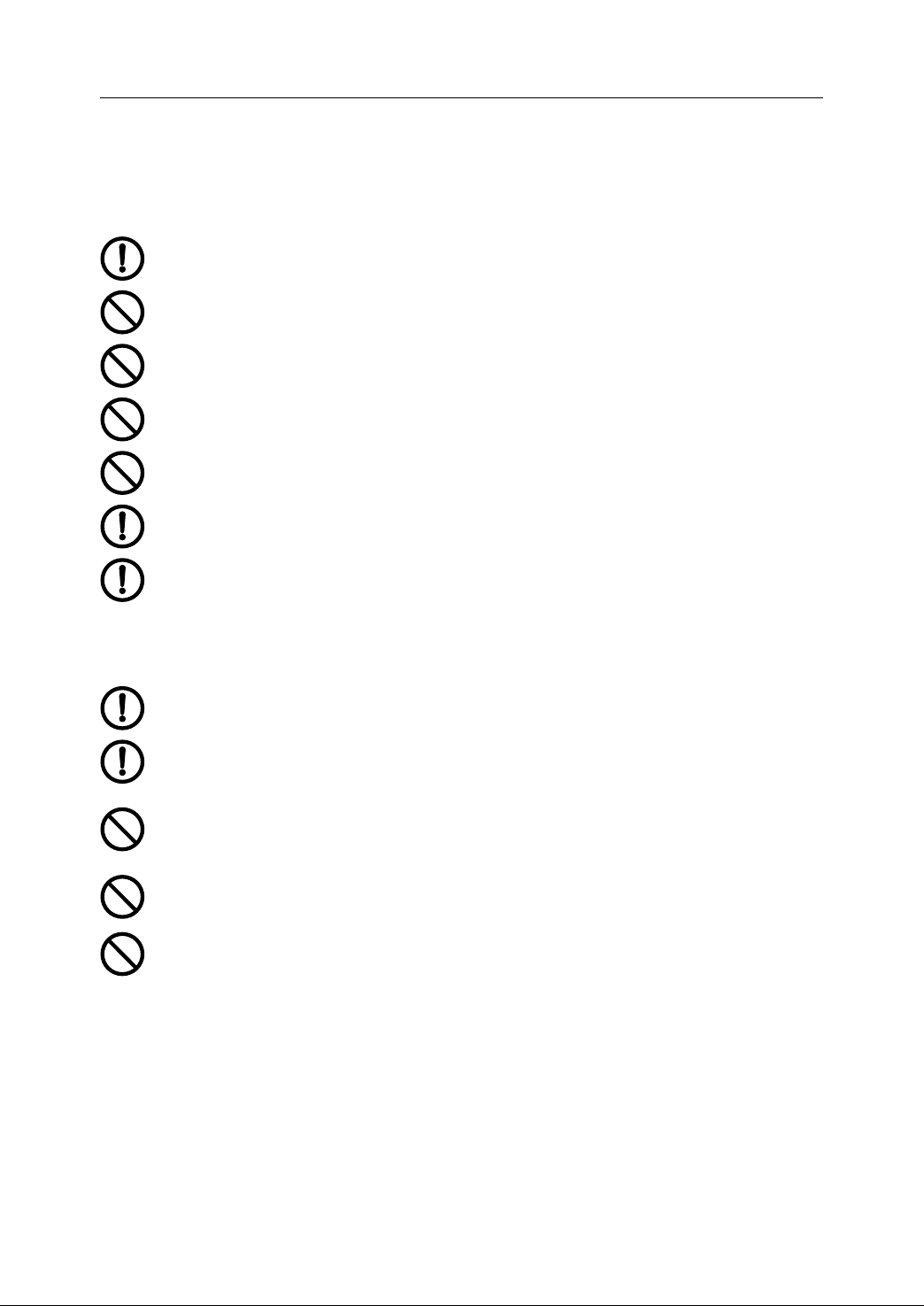
1. Precaution
1.1
Safety
1.1
Safety
1.1
1.1 Safety
Safety
1.1.1
1.1.1
1.1.1
1.1.1 Transportation
1.1.2
1.1.2
1.1.2
1.1.2 Installation
Transportation
Transportation
Transportation and
The product should be transported properly according to its weight.
The number of products stacked must not be more than what stipulated.
Do not climb up or stand on the product. Do not stack heavy things on it.
Dragging its cable to move or lift the product is not allowed.
Protect the front panel and screen from impact and cut.
Keep damp-proof while storing and transporting.
Let us know in time if the product has been stored overtime.
Installation
Installation
Installation
Because its casing is not of waterproof design, the product sh all be installed in
a cabinet to prevent from being rained on or directly sun-scorching.
and
Storage
and
Storage
and Storage
Storage
There sh all be enough space as required between the product and the cabinet
case or other devices.
The product sh all work in the environment with good ventilation, without
inflammable air, and without the erosion by corrosive material such as abrasive,
oil-mist, metal powder etc. Any conductor as metal or machine oil is prohibited
to get into the product.
Do not put the product near any inflammable or explosive matter.
The installation sh all be firm and without v ibration. Do not throw or strike the
product while installing. Neither a ny colliding against n or loading on the product
is allowed.
2
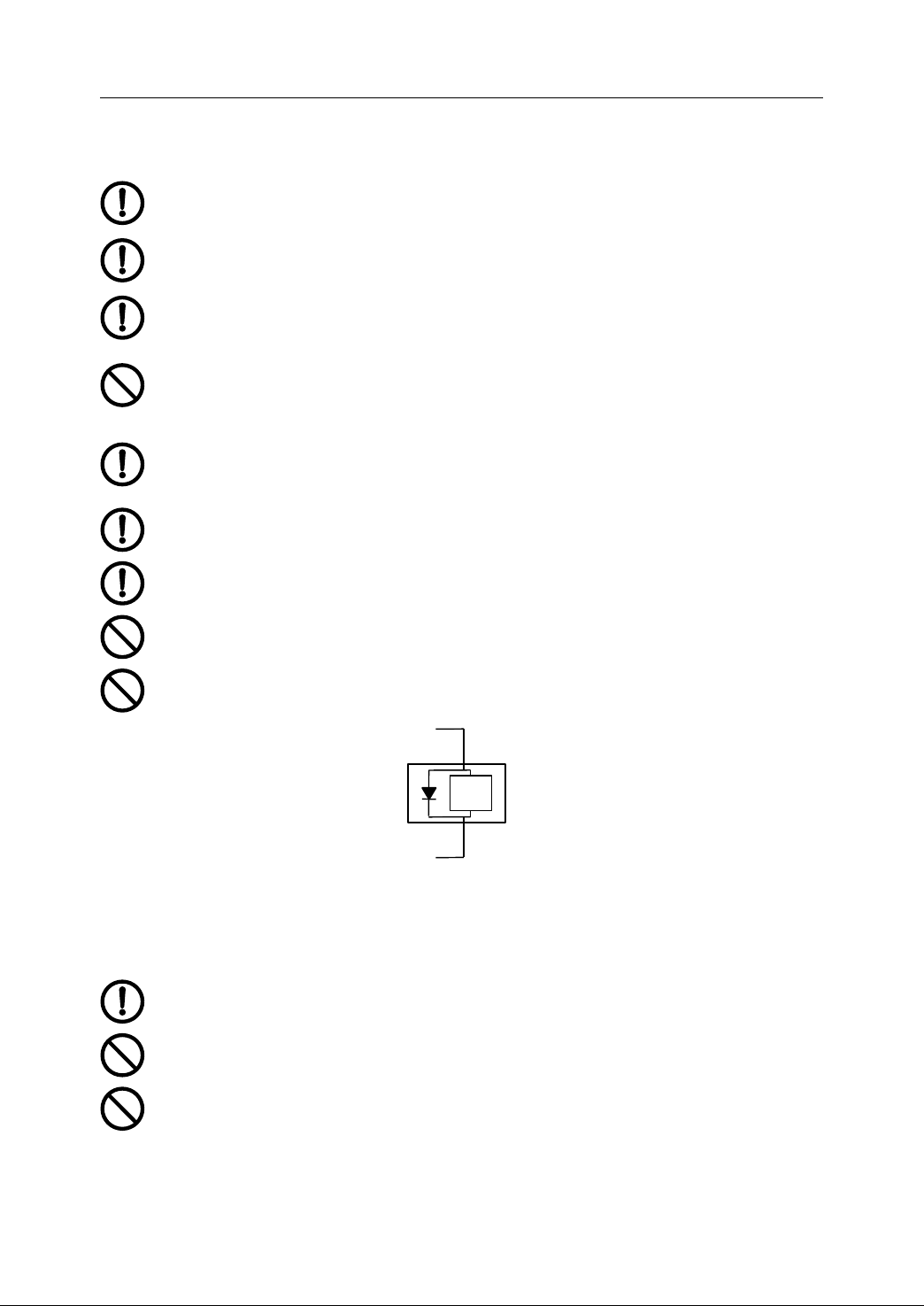
1. Precaution
1.1.3
1.1.3
1.1.3
1.1.3 Wiring
Wiring
Wiring
Wiring
Workers undertaking wiring or inspection must be qualified to do the jobs.
The NC device must be grounded reliably . T he earth-resistance must be less
than 4 ohm. Do not take the neutral as a ground . O therwise , the system may
not work normally and stably because of interference.
Wiring s hall be correct and firm to avoid wrong operation.
Do not transfer either the position signal from NC device to servo driver unit or
the position feedback signal from position frequency converter to servo driver
unit and NC device through terminals or sockets . O therwise , the NC device may
not work owing to interference.
Any voltage at terminals must have its correct value and polarities (+, -) as
mentioned in the manual . O therwise , the short circuit or permanent damage to
the machine may occur.
The surge-absorbed diode of DC relay controlled by PLC output signal from NC
device must be wired as shown in F igure 1-1 to prevent the damag e t o device.
A
perso n n el’s hands must be kept dry while touching the plugs or switches to
avoid getting an electric shock or resulting in device damage.
Any tear on electric wires is not allowed. The wires sh all not be squeezed to
avoid leakage or even short-circuit.
It is absolutely not allowed to insert or pull out any plug or open the NC cabinet
door with the power supply on.
1.1.4
1.1.4
1.1.4
1.1.4 Commissioning
1.1.5
1.1.5
1.1.5
1.1.5 Operation
Commissioning
Commissioning
Commissioning
Before putting the device in motion, check the parameter setting at first.
Incorrect settings would lead to unexpected results.
Set parameter in its permissible range. Oversetting may lead to unstable
operation or even the damag e to the device.
Check if the cables of servomotor and the encoder wires are corresponding to
each other.
Operation
Operation
Operation
PLC output
Relay coil
DC+24V
Figure 1 1 the surge-absorbed diode
3
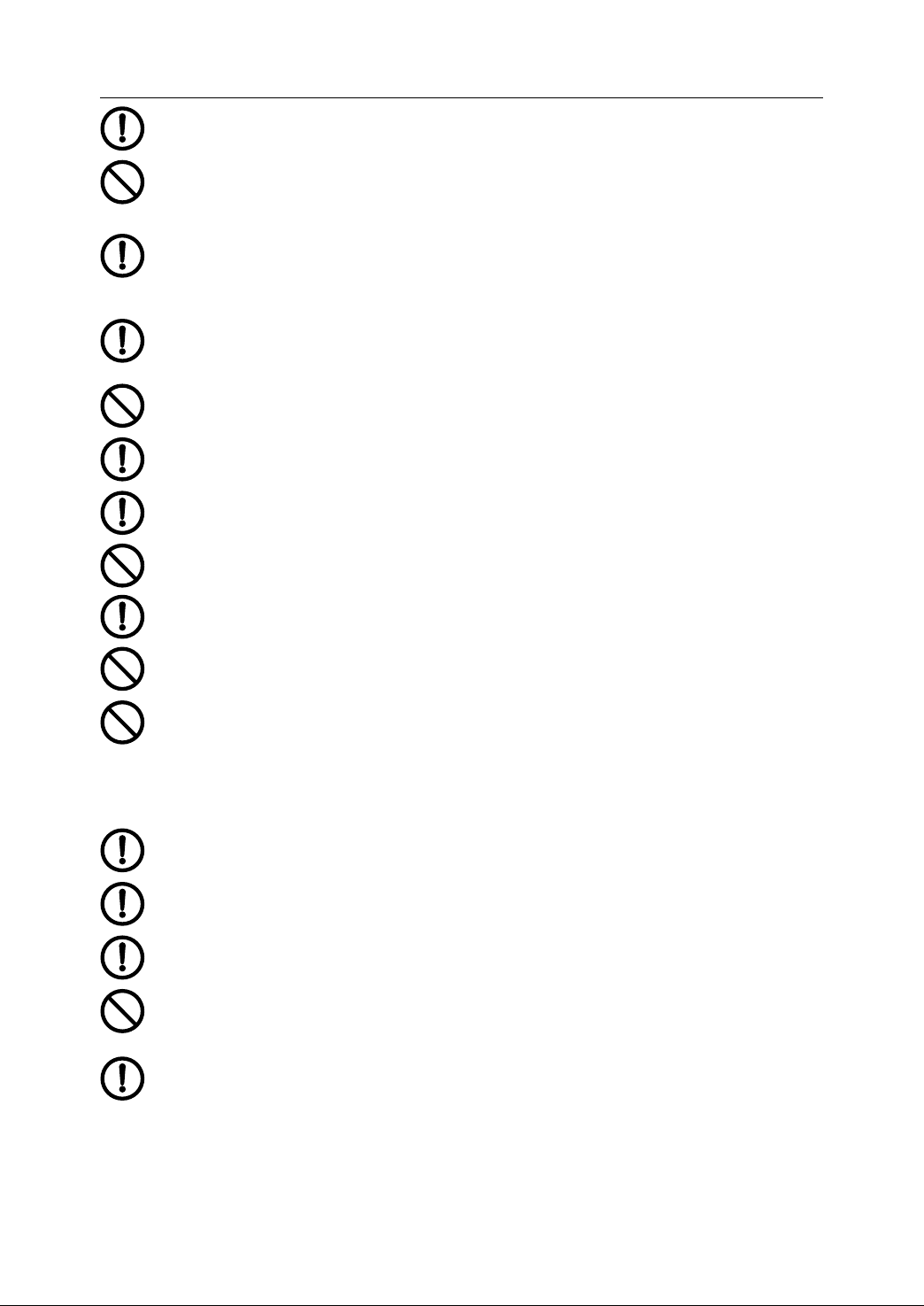
1. Precaution
Personnel to operate the device must be competent for their work.
Before plugging in to get the main source, make sure that the main switch is off
to avoid accidental start -up .
While doing electrical design, it sh all take into account that the emergency stop
button of NC device could cut the power supplies for servo motion, spindle
motion and motions of all other moving parts when the system accidents occur.
For example, cut off the power supply (section 2. 9 for details ).
While designing or modifying the PLC programs, make sure that the operation
signal has been off before the reset alarm signal . For example, the spindle
rotation signal must be off before resetting the spindle alarm signal .
Do not refit the device.
To
prevent from or reduce the influence of electromagnetic interference on NC
device, refer to section 2.10 E lectromagnetic Compatibility Design.
To
reduce the electromagnetic interference, a low-pass filter can be added i f
there are electronic devices .
Do not turn on and off the system frequently . T he interval between on and off
operations must be at least 3 minutes.
T he operator’s hands must be kept dry, clean and no greasy dirt during
operation . It is suggested to keep the clear protection film on the panel.
Do not press the keys hard . It is not allowed to strike at the keyboard with
wrench or other sharp-edged and hard articles.
Operators shall not leave the machine while operating the devices.
1.1.6
1.1.6
1.1.6
1.1.6 Maintenance
Maintenance
Maintenance
Maintenance
Power supply sh all be turned off before checking, replacing or installing parts or
elements.
When short-circuit or overload happens, do not turn on the power again un less
checking and fixing the breakdown.
When alarm has happened, do not restart the device un less the accident is
cleared off.
Do not install or operate the device if it is damaged or lack of p arts and
elements.
The aging of electrolytic capacitors may lead to low performance.
damages arising from there, the electrolytic capacitors should be replaced,
under the normal operation conditions, every ten years. Please c ontact with us
at any time to solve the relevant problems.
To
avoid the
4

1. Precaution
1.1.7
1.1.7
1.1.7
1.1.7 Waste
1.1.8
1.1.8
1.1.8
1.1.8 General
Waste
Waste
Waste Treatment
Treat the wastes as ordinary industrial wastes.
General
General
General Instructions
While putting the device in operation, install the cover plate and safety
equipment perfectly and operate the device as mentioned in manuals.
Read over chapter 2.10 Electrical Design in detail and notice all the
emphasized points.
Treatment
Treatment
Treatment
Instructions
Instructions
Instructions
5
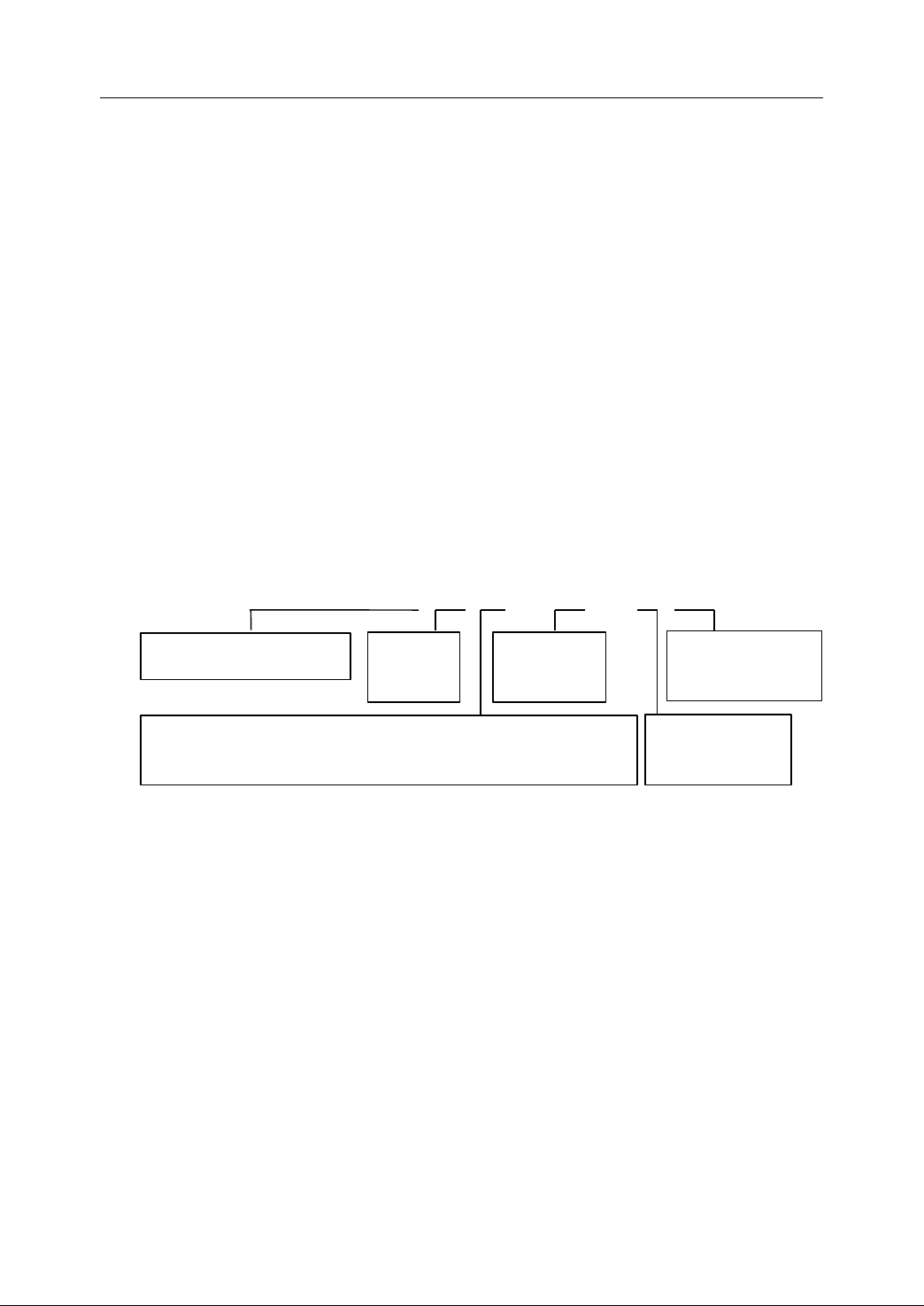
1. Precaution
1.2
Unpacking
1.2
Unpacking
1.2
1.2 Unpacking
Unpacking and
and
and
and Checking
Checking
Checking
Checking
1.2.1
1.2.1
1.2.1
1.2.1 List
After unpacking, please make sure that :
- The product is what you ordered.
- No damage occurs during transportation.
- The received components included the accessories are complete and without
Please Contact us in time if any problem exists .
1.2.2
1.2.2
1.2.2
1.2.2 Product
The following is the description of HNC- 21 .
List
List
List
damage.
Product
Product
Product Type
21: NC of standard type
22: NC of advanced type
Type
Type
Type
HNC
HNC
HNC
HNC –
–
–
– 21
21
21
21 M
Unit Type
M: Milling
T:
Turning
M
D
–
M
D
M D
D –
32
–
32
– 32
32 –
Storage Size
MB
–
H
–
– H
02
H
02
H 02
02
Memory Size
Flash RAM – MB
Hard disk -- GB
T
ype of feed axis
D: pulse interface for pulse servo or step per motor driver
Figure 1 2 Description of HNC-21
6
Memory type:
F: Flash RAM
H: IDE hard disk
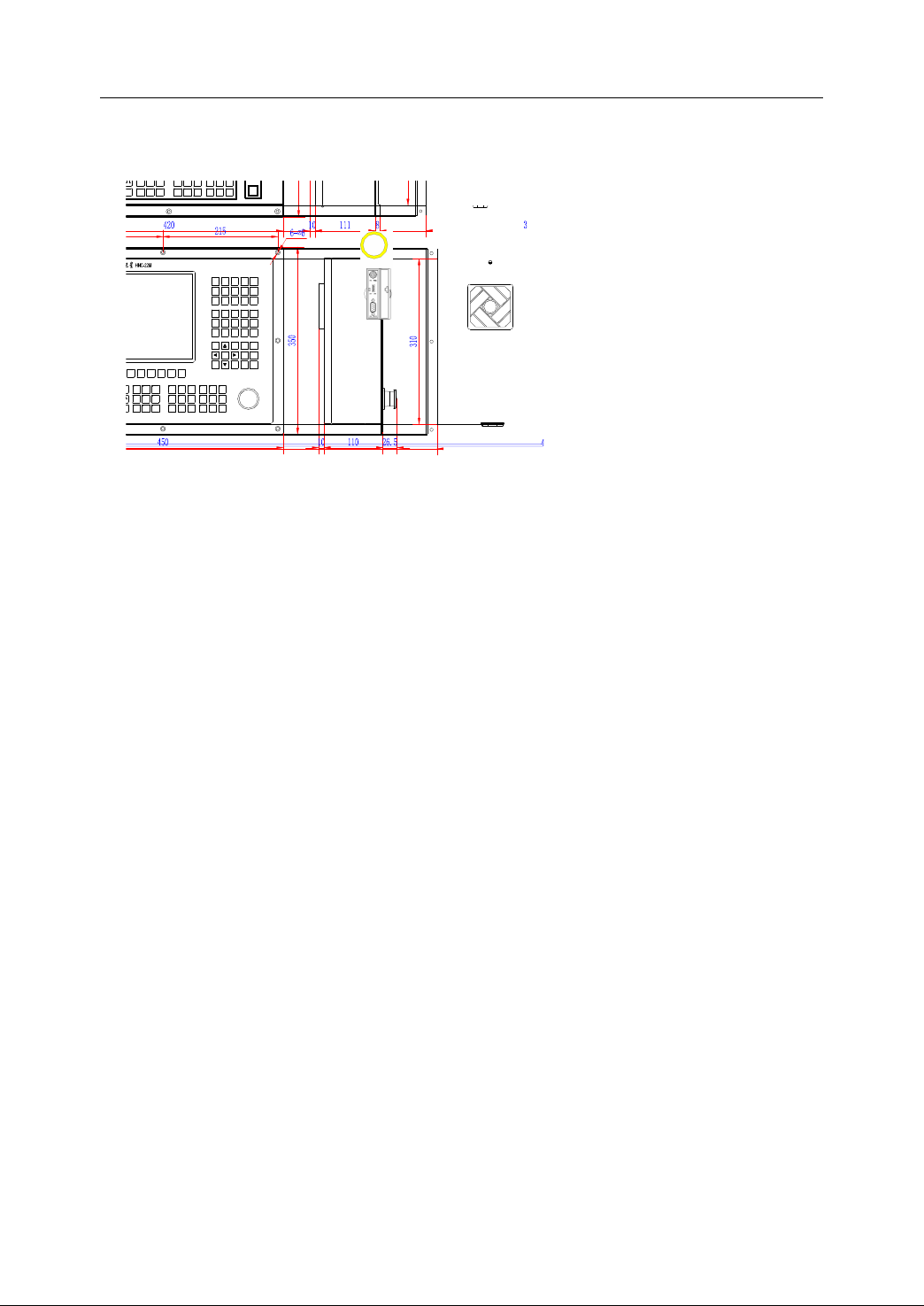
1.3
Esc
Tab
GECYBZ
QRFH
S T
%
SP
\:;
[8]^
6 7
2 3 4
BS
Enter
Upper
-
=+/
0
.
Del
Alt
Pgdn
+X
+Z
快进
-X
+4TH -Y
-4TH+Y-Z
循环
启动
进给
保持
V
J K
W L
P N
O
X
A
D
M
"
5
#
1
*
9
Pgup
+-
100%
100%
- +
快速修调主轴
制动
刀具
松/紧主轴修调
+-
100%
进给修调主轴
反转
主轴
定向
回 零
1000
冷却
开停
主轴正转机床锁住主轴
停止
主轴
冲动
换刀
允许
I
U
主轴
停止
主轴
冲动
换刀
允许
主轴
正转
主轴
定向
冷却
开停
F5F4 F6
主轴
反转
主轴
制动
进给
修调
-
快速
修调
- +
+
100%
100%
-Z
-X
刀具
松/紧主轴修调
-
F8F7 F9
+
100%
+4TH
F10
+X
-4TH+Y
快进
+Z-Y
PgDn
EnterAlt
SP
[8]^
6 75
#
+
PgUp
*9/
.
0
Upper
Shift
Del
=
-
BS
R
W
:1"
2 3
;
I
U
M
D
V
J K
H
S T
4
\
%
P
L
F
Q
O
N
Tab
CXA B
Y Z G
E
Esc
Dimensions
1.3
Dimensions
1.3
1.3 Dimensions
Dimensions
1. Precaution
Figure 1 3 Dimension of HNC-21/22
7
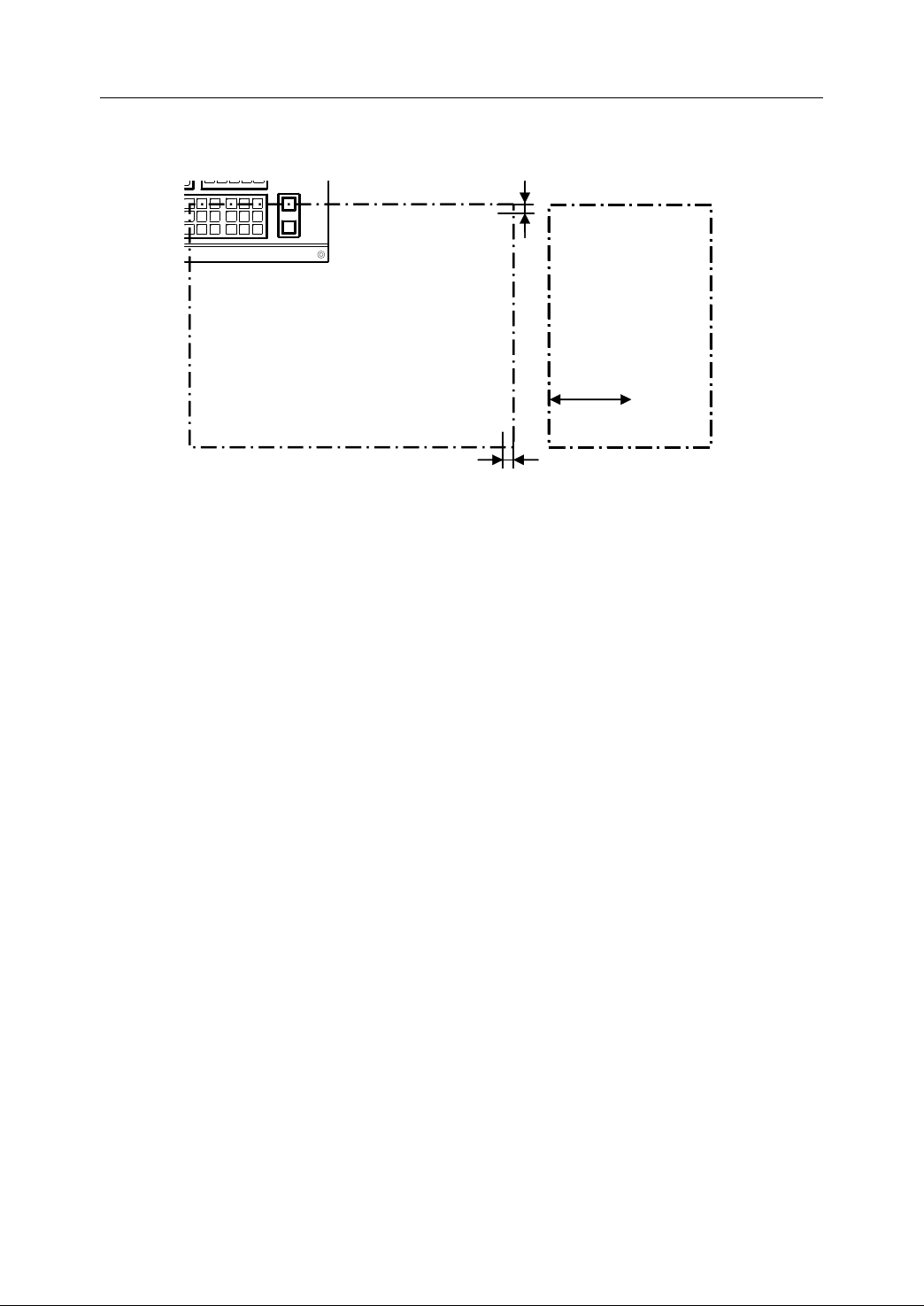
1. Precaution
Esc
Tab
GECYBZ
Q
RFH
S T
%
SP
\:;
[8]^
6 7
2 3 4
BS
Enter
Upper
-
=+/
0
.
Del
Alt
Pgdn
+X
+Z
快进
-X
+4TH -Y
-4TH+Y-Z
循环
启动
进给
保持
V
J K
W L
P N
O
X
A
D
M
"
5
#
1
*
9
Pgup
+-
100%
100%
- +
+-
100%
I
U
1.4
Installation
1.4
Installation
1.4
1.4 Installation
Installation
Figure 1 4 Dimension of Installation (HNC-21 as an example)
Please note the following items when designing the cabinet (control cabinet, console,
and pendant box) .
1. As shown in Fig ure 1-4 , it needs to have at least a 100mm-space between NC
device and the rare wall of the cabinet to facilitate plugging the cables and heat
radiation .
2. The cabinet structure must be of IP54 protection class. S ome requirements
should be met :
1) The material used to make the cabinet must bear any mechanical, chemical,
or heat stress and the moisture influence normally happened .
2) It needs to stick the adhesive tape along the door crack to eliminate the
gap .
3) The cable entrances must be sealed properly, so that it can be unsealed
easily if necessary .
4) Fans or heat exchanger must be equipped to radiate the heat from cabinet .
5) If fans are used, the air filters are required at both inlets and outlets .
6) Be careful not to let the dust come into the cabinet through heat dissipation
holes. Dust or other materials such as cutting lubricant, mist can get into the
device and attach itself to circuit board to make the insulation aging and
even lead to circuit damage. Therefore, it needs to know the environment
and the direction of air discharge; the warm air stream should be directed
8
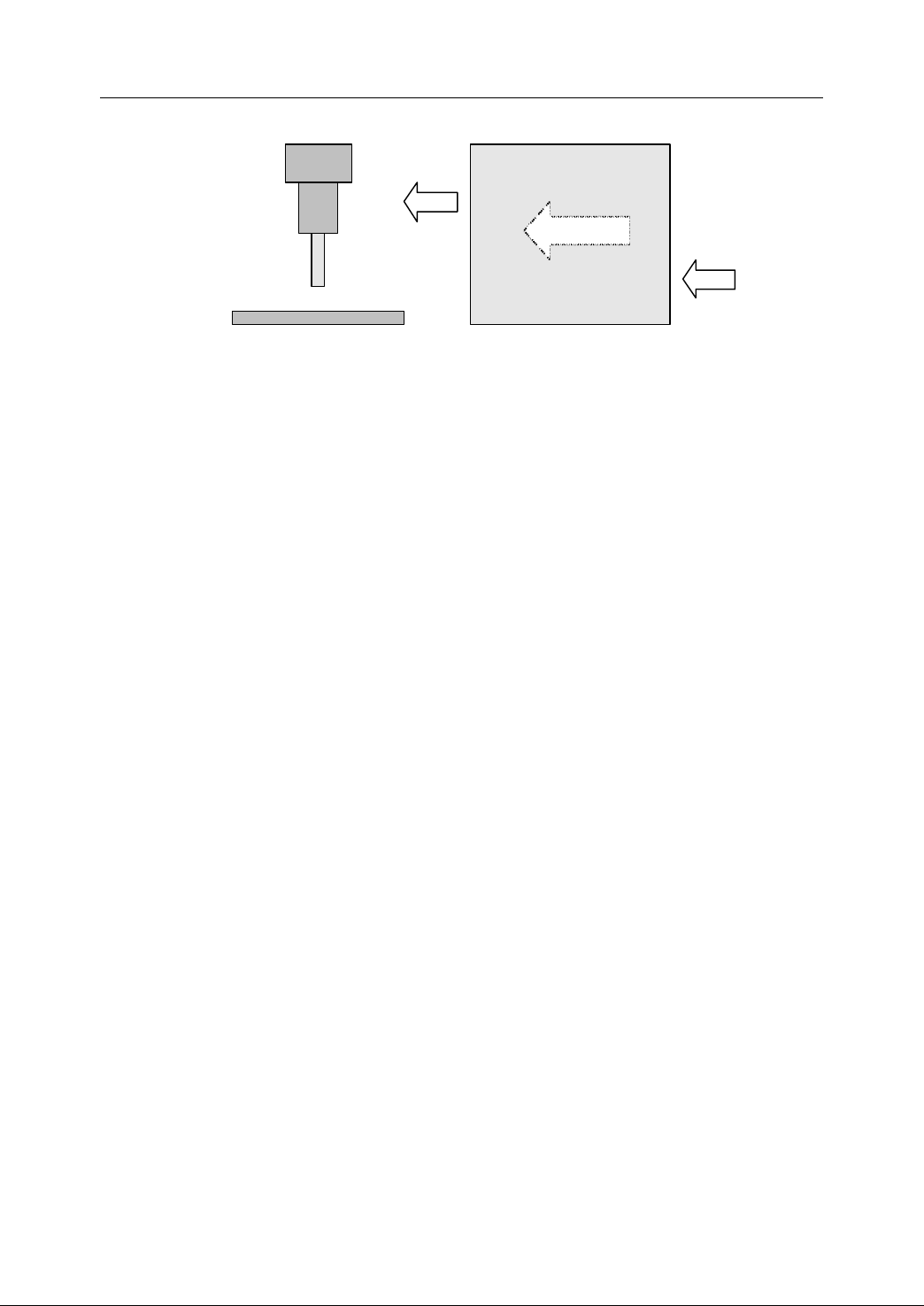
1. Precaution
against the pollution source, as shown in Fig ure 1-5.
Figure 1 5 Air flow direction in NC cabinet
3. Temperature in the cabinet shall not be higher than 50 ℃ . Alternatively, more
effective steps shall be applied to dissipate the heat.
4. The control panel must be placed where the coolant or other liquid does not
reach .
5.
To
reduce electromagnetic interference, k eep cables or electric components
having supply voltage higher than 50V apart from NC device at least 100mm .
6. The NC device should be installed where the commissioning and maintenance
can be done conveniently .
9
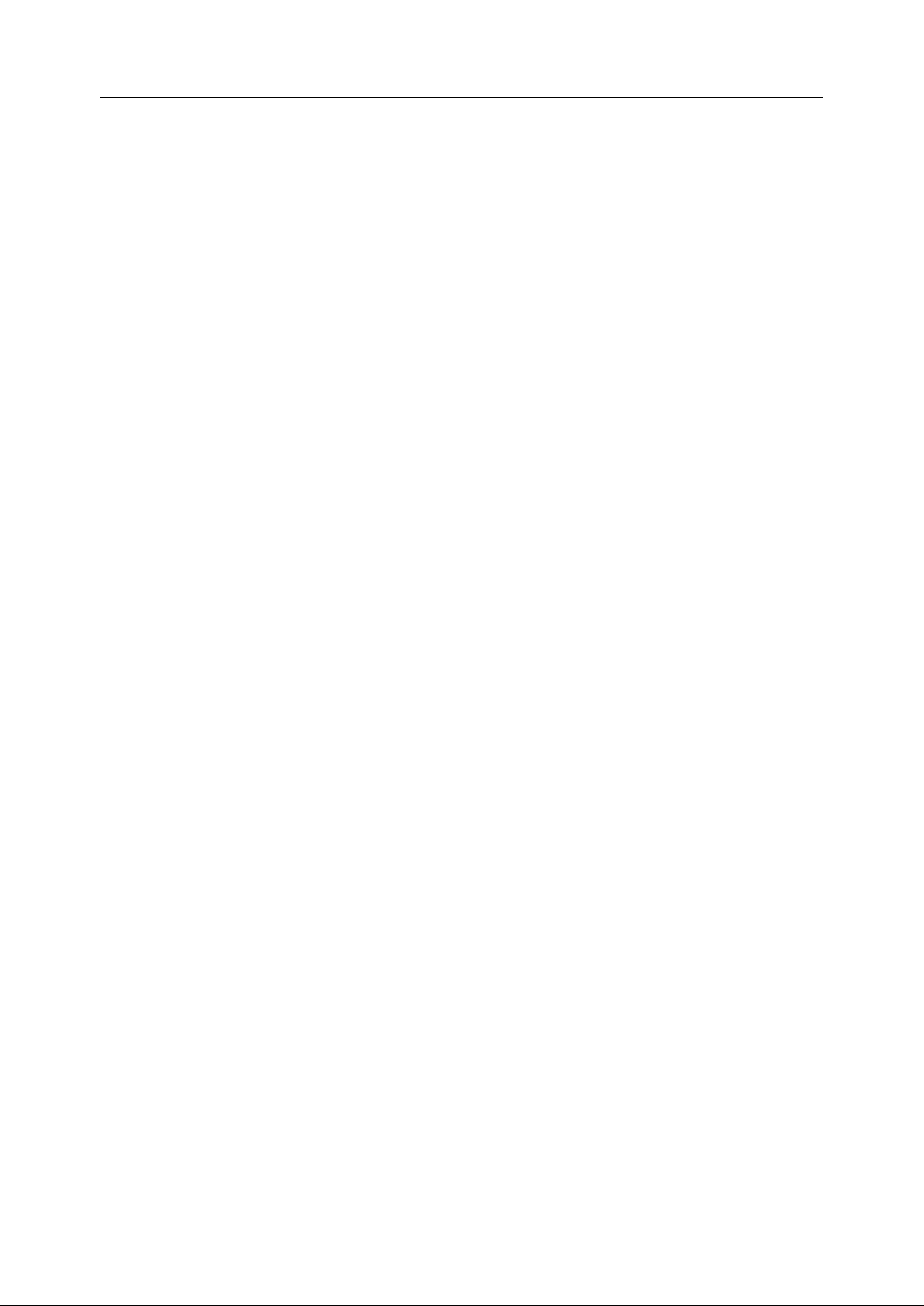
1. Precaution
1.5
Environmental
1.5
Environmental
1.5
1.5 Environmental
Environmental Requirement
Requirement
Requirement
Requirement
1.5.1
1.5.1
1.5.1
1.5.1 Weather
The NC device works normally in the environment shown as follows.
- A mbient temperature : 0 ~ 40 ℃
- R elative humidity : 30% ~ 95% ( without dew )
- A tmospheric pressure : 86 ~ 106k Pa
1.5.2
1.5.2
1.5.2
1.5.2 Elevation
The NC device works normally with an elevation of less than 1000 m.
1.5.3
1.5.3
1.5.3
1.5.3 Transportation
It is proper to transport and store the NC device within a temperature range of
(-40 ℃ ~ +55 ℃ ). The device can survive up to 70 ℃ in a short-term, less than 24
hours, transportation or storage. It is necessary to adopt moisture-proof, shockproof
and impact-resistant measures to avoid damage .
Weather
Weather
Weather Condition
Elevation
Elevation
Elevation
Transportation
Transportation
Transportation and
Condition
Condition
Condition
and
Storage
and
Storage
and Storage
Storage
1.5.4
1.5.4
1.5.4
1.5.4 Mechanical
The NC device sh all be installed far from any shock resource to prevent from the
influence of shock, impulse and impact. If the device has to be installed near these
resources, additional measures are necessary to ensure the NC device against
resonance, and the vibration amplitude must be less than 0.05mm (frequency range:
5-55 Hz) .
1.5.5
1.5.5
1.5.5
1.5.5 Environmental
While transporting, storing or operating, keep the NC device out of the strong
microwave radiation and the strong electromagnetic interference. Do not let
excessive pollutants (dust, acid, corrosive gas, salty matter) intrude into NC device.
The device should not work in an environment accompanied with strong vibratio n.
10
Mechanical
Mechanical
Mechanical Environment
Environmental
Environmental
Environmental Pollution
Environment
Environment
Environment
Pollution
Pollution
Pollution
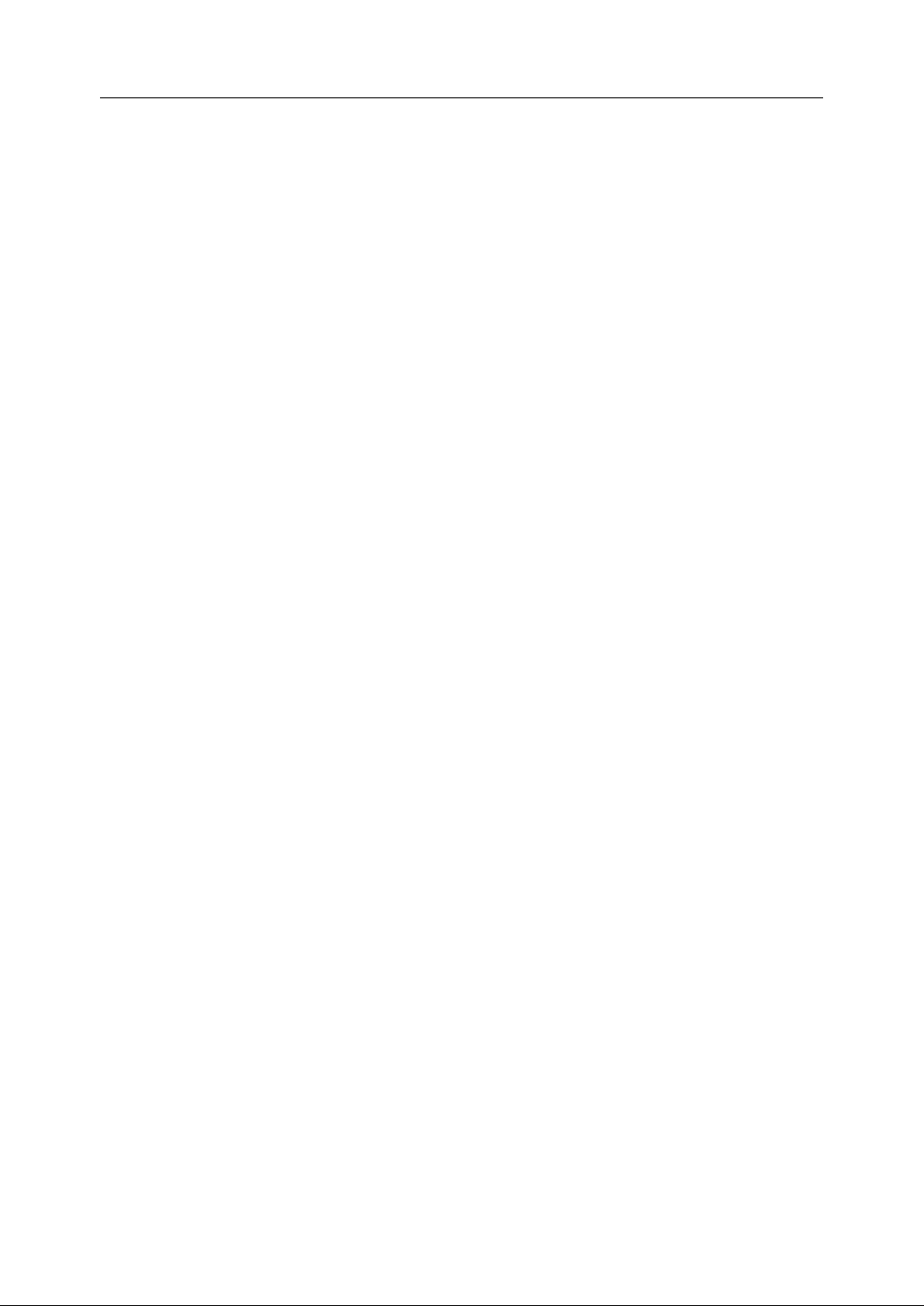
HNC- 21/22 Connection Manual
2
Connection
2
Connection
2
2 Connection
Connection
Thi s chapter would introduce:
-
Total
connection diagram
- I nterface
- Power supply connection
- Connection to DNC
- Connection to computer
- I/O on NC device
- Connection to handwheel unit
- Connection to spindle device
- Connection to feed drive
- Design of E-Stop and Overtravel Released
- Design of Electromagnetic Compatibility
11

2. Connection
XS1
XS
30 -
XS3
5
XS2
XS
8
XS3
XS
9
XS5
XS
10 - XS12
XS
7
XS20 - XS22
2.1
Total
2.1
Total
2.1
2.1 Total
Total Connection
This section shows the total connection diagram of HNC-21/22.
Connection
Connection
Connection Diagram
Diagram
Diagram
Diagram
[Note]
[Note]
[Note]
[Note]
(1) As it is shown Fig ure 2 - 1, HNC- 21/22 controls various types of feed units
(2) PLC I/O (maximum: 60/48) can be connected through XS10-XS12 (input),
(3) The interface to connect to the third axis on HNC-21 or the fourth axis on
(4) The interfaces XS12 and XS22 which provide 20/16 I/O are optional.
(5) Ethernet interface XS3 is optional.
Figure 2 1
through XS 30 -XS3 5. Up to six different types of feed device can be connected.
XS20-XS22 (output).
HNC-22 is optional.
Total
Connection Diagram of HNC-21/22
12
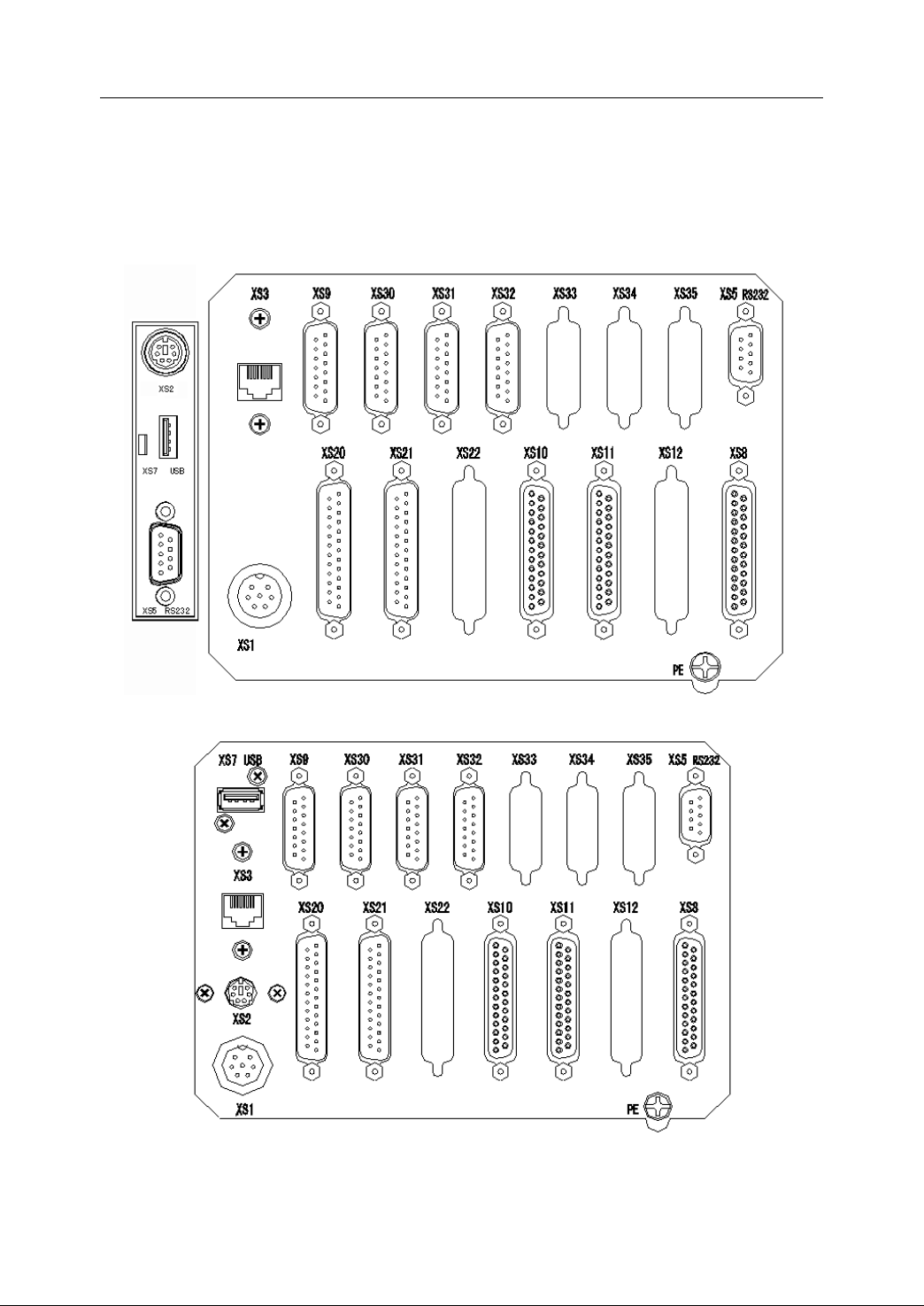
2.2
Interface
2.2
Interface
2.2
2.2 Interface
Interface
2. Connection
2.2.1
2.2.1
2.2.1
2.2.1 NC
Th is section shows the interface of HNC-21.
NC
Device
NC
Device
NC Device
Device
Figure 2 2 Interface of HNC-21
Figure 2 3 Interface of HNC-22
13
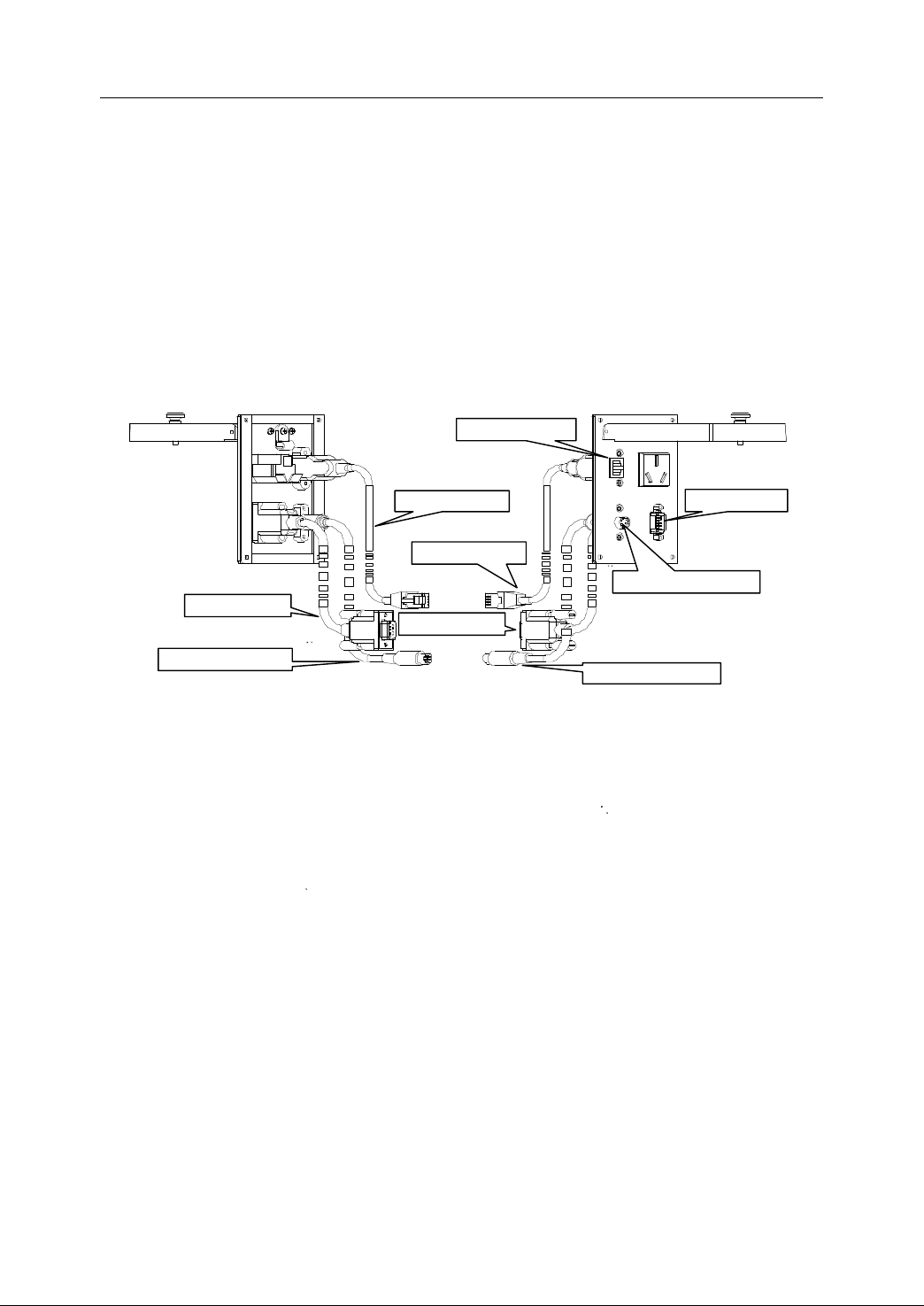
2. Connection
XS1: Power supply interface XS2: Keyboard interface
XS3: Ethernet interface XS5: RS232 interface
XS7: USB interface XS8: Handwheel unit interface
XS9: Spindle control interface X10~X12: PLC inputs interface
X20~X22: PLC outputs interface X30~X35: feed axis control interface
2.2.2
2.2.2
2.2.2
2.2.2 DNC
There are RS232, PC keyboard and E thernet interfaces on DNC unit . The following
Fig ure 2-4 shows the interface of DNC unit .
As it is shown in Figure 2-4, the interfaces are used to connect with PC or other
devices, and the switchers are used to connect with HNC-21/22. The interfaces on
DNC unit correspond with the interfaces shown in Figure 2-2 or Figure 2-3.
DNC
DNC
DNC unit
unit
unit
unit (optional)
(optional)
(optional)
(optional)
Figure 2 4 Interface of DNC unit
2.2.3
2.2.3
2.2.3
2.2.3 Handwheel
As it is shown in Figure 2-5, t he handwheel unit is equipped with the emergency stop
button, pilot lamps, axis switch (OFF, X,
and the manual pulse generator. It is connected to XS8 of HNC-21/22.
14
Handwheel
Handwheel
Handwheel unit
unit
unit
unit (optional)
(optional)
(optional)
(optional)
Y,
Z), m agnification switch (X1, X10, X100) ,
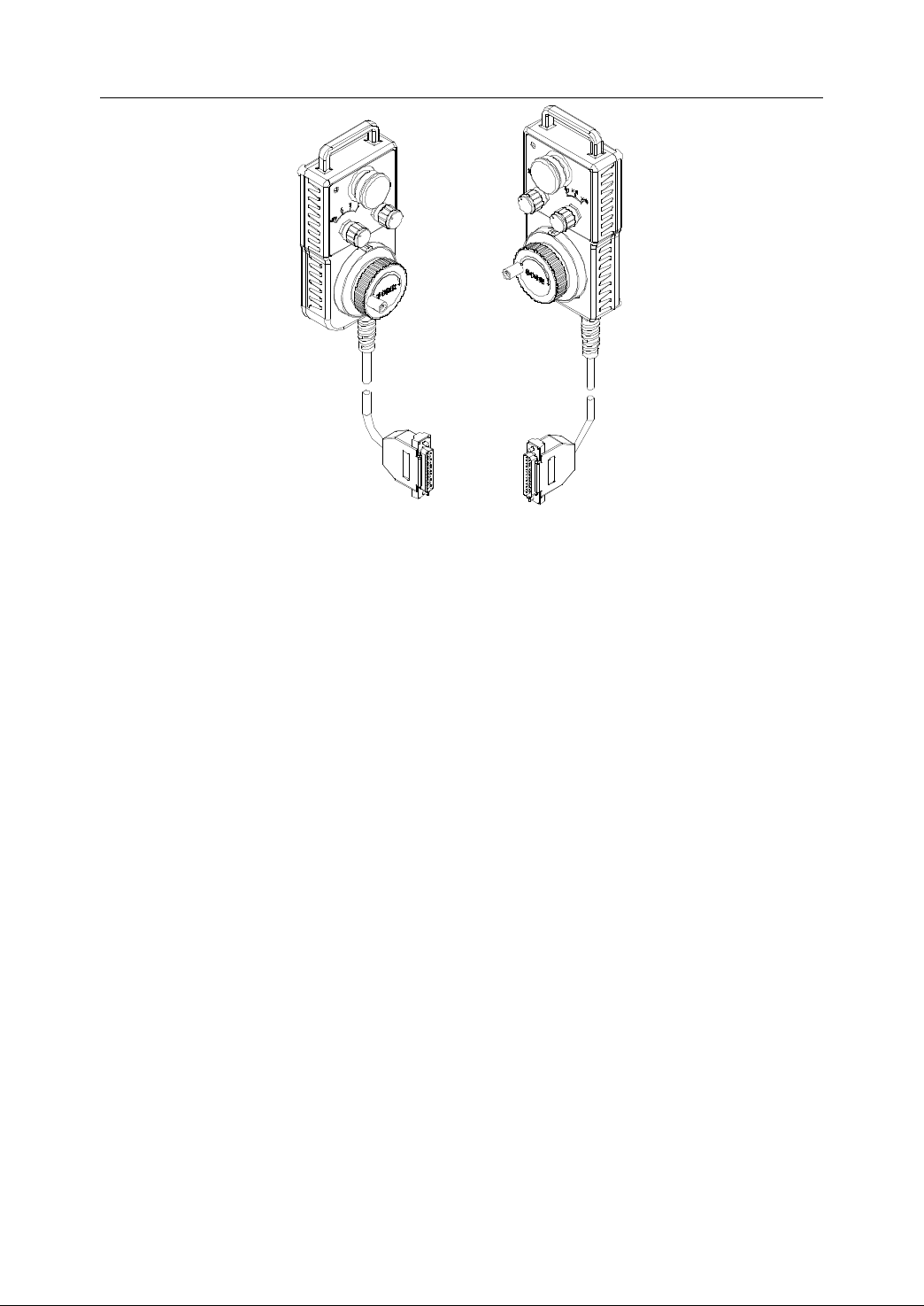
Figure 2 5 Interface of Handwheel unit
2. Connection
2.2.4
2.2.4
2.2.4
2.2.4 I/O
There are two kinds of I/O terminal boards – input terminal boards and output
terminal boards. They are usually used as a switcher unit to connect XS 10, XS11,
XS12, XS20, XS21, and XS22 of HNC-21 /22 .
Each input terminal board or output terminal board contains both NPN and PNP
terminals.
E ach input terminal board contains 20 bit input terminals . Each output terminal
board contains 16 bit output terminals, 2 bit emergency-stop terminal, and 2 bit
overtravel terminal.
- I nput terminal board
I/O
Terminal
I/O
Terminal
I/O Terminal
Terminal Boards
Boards
Boards
Boards (optional)
(optional)
(optional)
(optional)
15
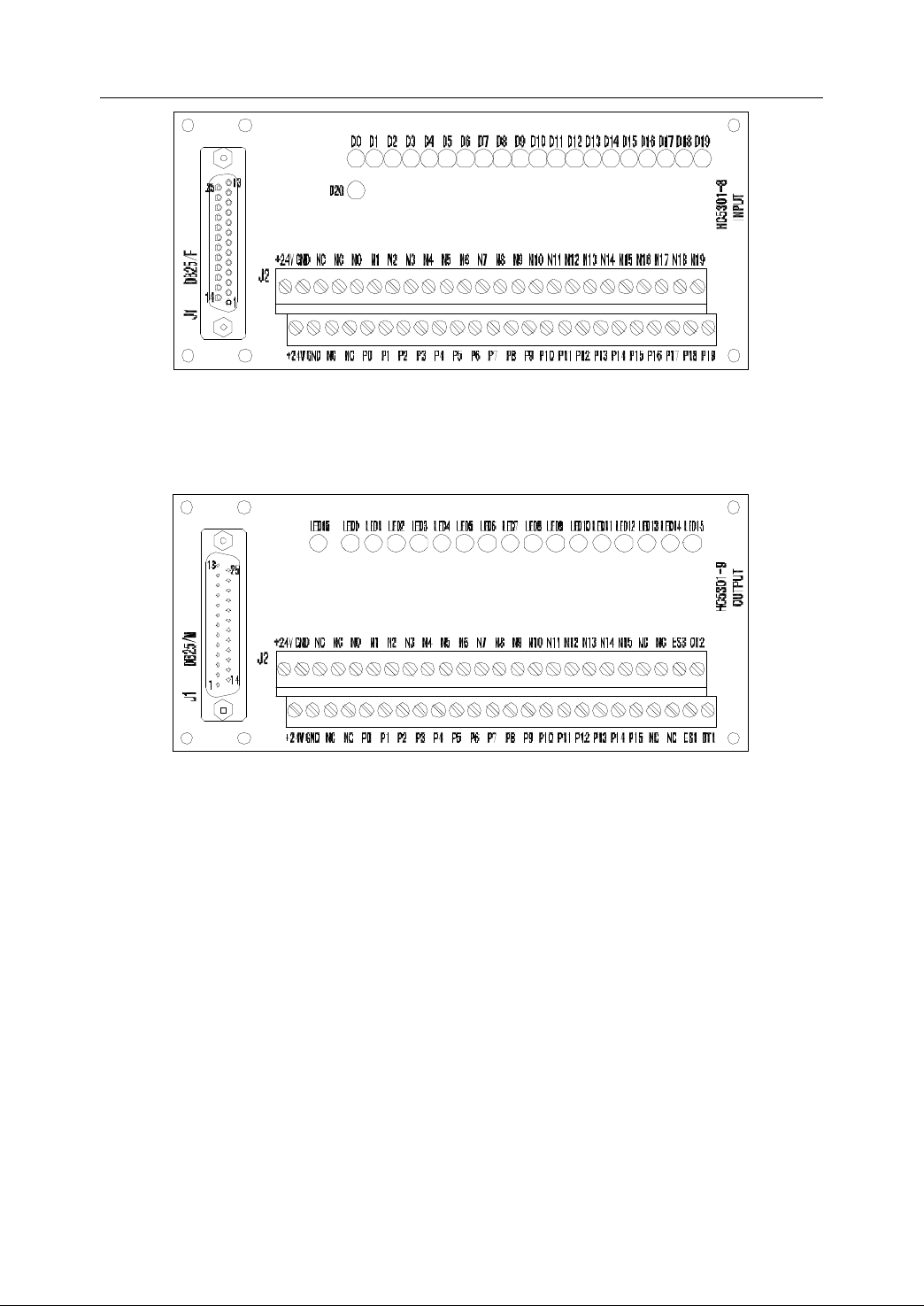
2. Connection
- O utput terminal board
Figure 2 6 Input terminal board
Figure 2 7 Output terminal board
16
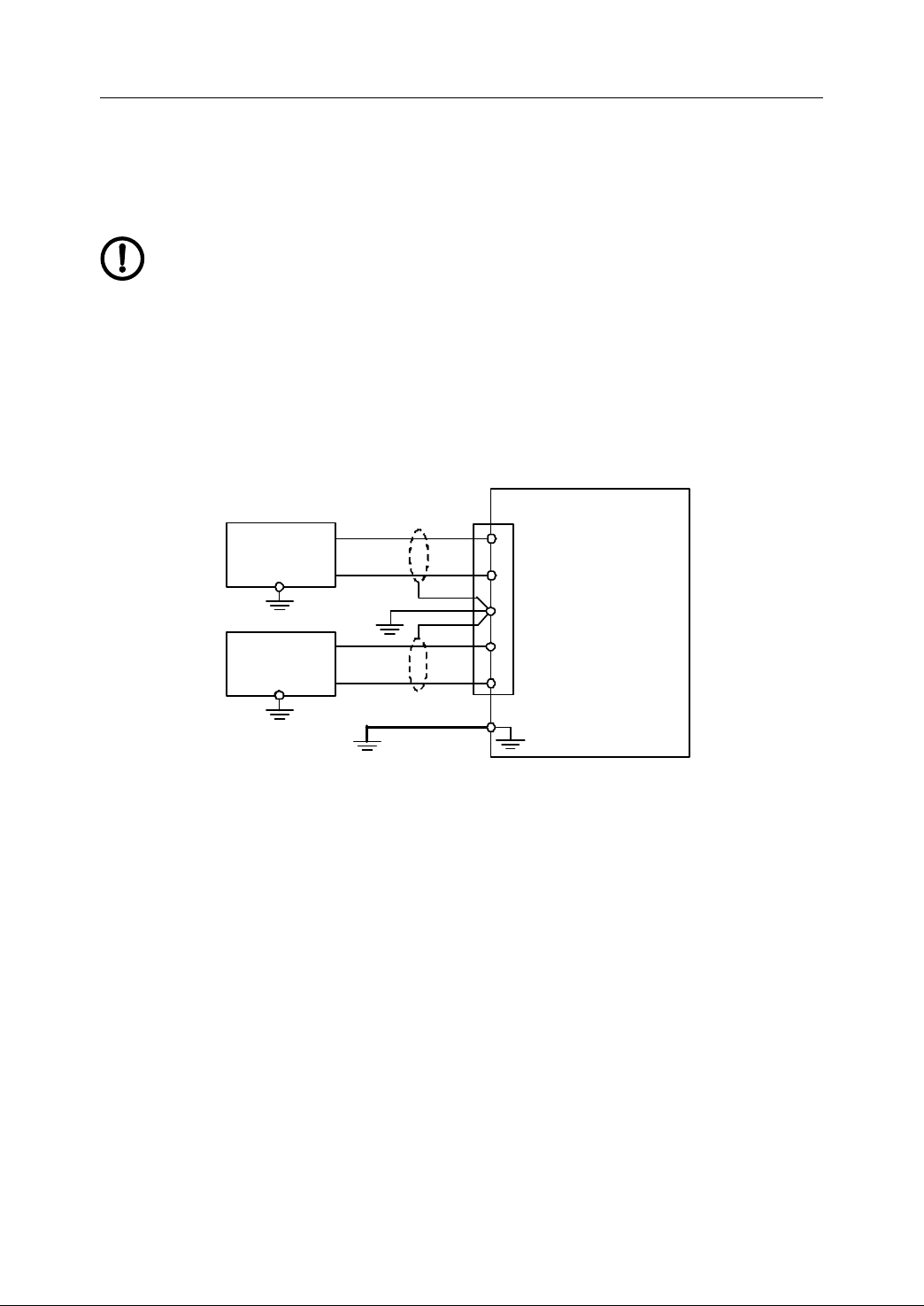
2.3
Power
2.3
Power
2.3
2.3 Power
Power Supply
Supply
Supply
Supply Connection
Connection
Connection
Connection
2. Connection
2.3.1
2.3.1
2.3.1
2.3.1 General
If the external supply 1 is of AC 24V, an independent power supply for NC device is
suggested to use (refer to Fig ure 2 -8 ) .
General
General
General Requirement
NC device (External supply 1) : AC24V , or DC24V/100W;
PLC power (External supply 2): DC24V, no less than 50W;
Cables: Shielded cables or twisted cables ;
Requirement
Requirement
Requirement
Figure 2 8 Power Supply 1
It is suggested to use a switch supply of DC 24V for the external supply 2. It is
proper to increase the supply capacity in case there are many DC 24V relays
controlled by PLC outputs, or to have an additional power supply, having a common
ground with the external supply 2. If the brake of Z axis (spindle) and
electromagnetic valves also require DC 24V supply , try to use another supply (not
the external supply 2) to prevent NC device from interference induced by loads with
large inductance .
I f the external supply 1 is of DC 24V , it is allowed to have a shared switching supply,
having capacity of no less than 1 45 W for both the external supply 1 and the external
supply 2 (refer to Fig ure 2 -9 ) .
17
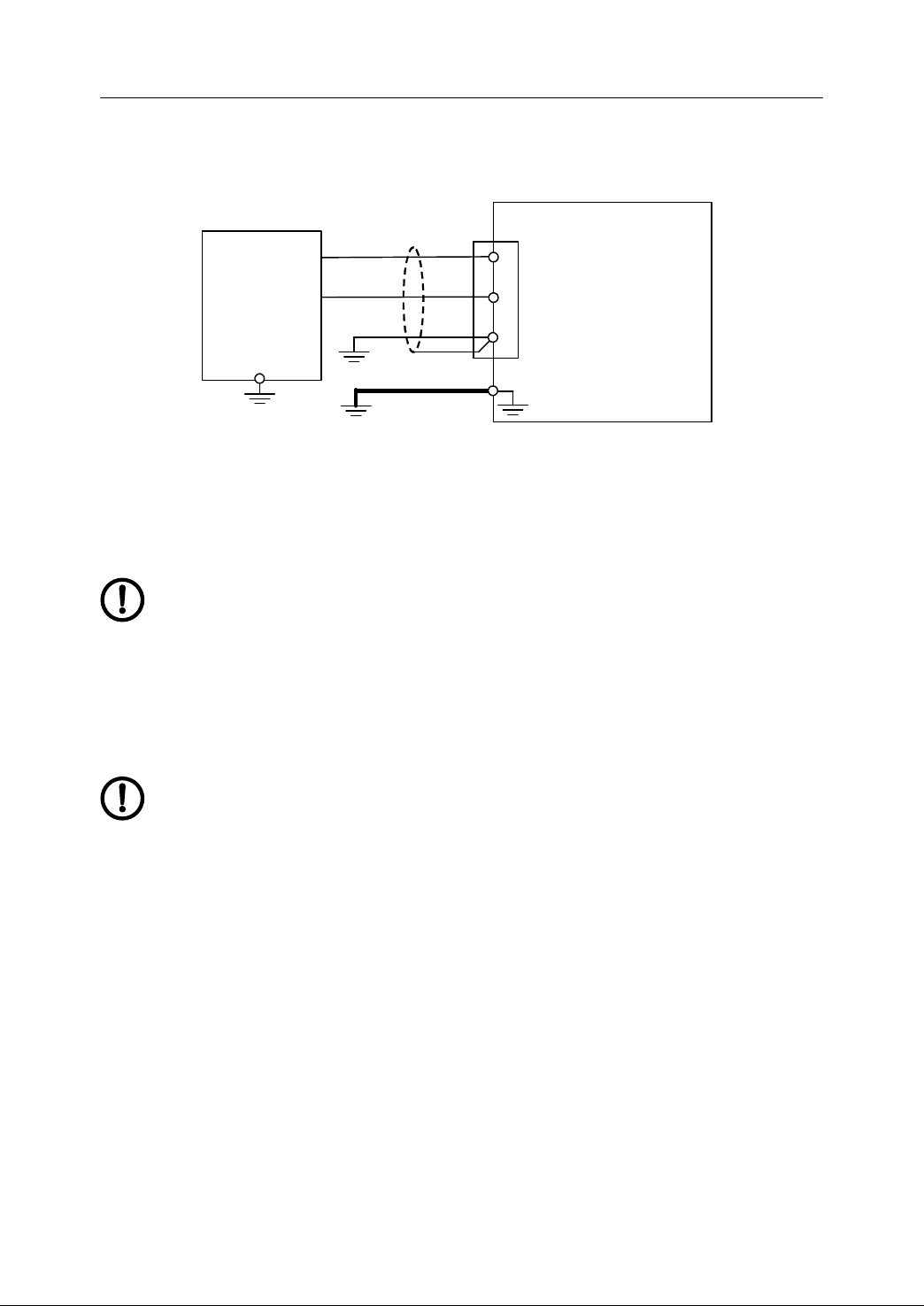
2. Connection
As shown in Fig ure 2 -10 , the external supplies 1 and 2 provide power for PLC
elements and manual pulse generator of handwheel unit through the interface XS8
on NC device .
Figure 2 9 Power Supply 2
2.3.2
2.3.2
2.3.2
2.3.2 Grounding
- Protective Grounding
Grounding
Grounding
Grounding
T he ground wire of power supply (pin 6 of XS1) is connected with PE
interface of NC device. An additional copper ground wire at le ast 2.5 mm
shall be taken as the ground wire and connected with PE interface of NC
unit , since the ground wire of the power cable is thin.
- Signal Grounding
The pin 4 of XS1 (DC 24VG) is connected to pin 1, 2, 14, and 15 of XS10,
XS11, XS12, XS20, XS21, and XS2 2 . Moreover, t o reduce the current
passing the pin 4 (DC 24V G ) of XS1 and to raise the anti-interference ability
of PLC signals , those pins (1, 2, 14, 15) sh all be connected to the ground of
external supply DC 24V (Figure 2-10).
2
18

2. Connection
XS10
, 11
,12
XS20 ,21
,22
P ower s upply 2
DC 24V ≥ 1 50W
Figure 2 10 Signal grounding
In case some electrical components (such as relays, pilots in buttons,
approach switches, and Hall switches) to control or receive signals from
I/O have their independent power supply, the supply should have common
ground with the supply of these inputs and outputs, Otherwise , NC device
can not control those electrical components or receive signal from th o se
component s reliably .
19
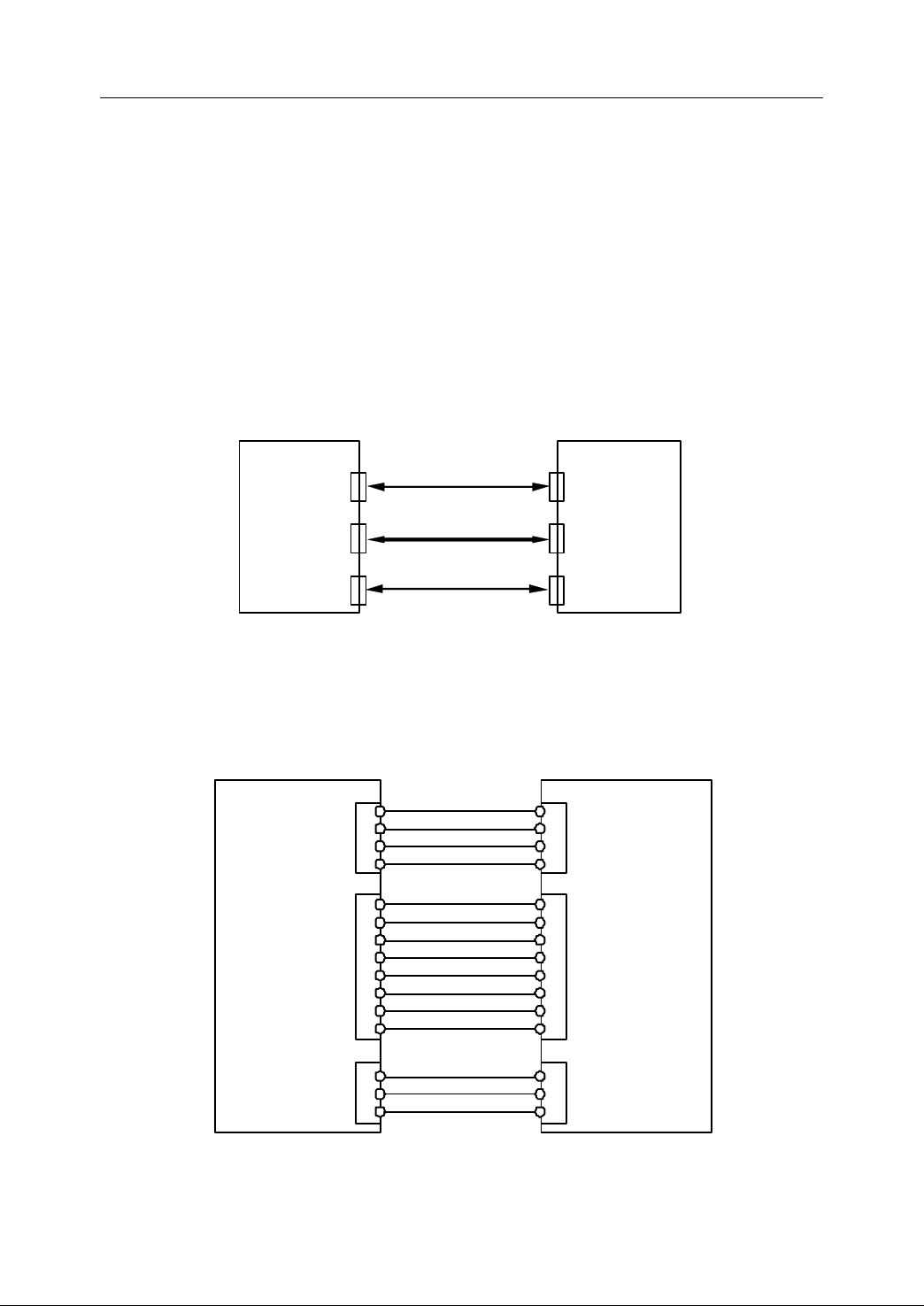
2. Connection
DNC
DNC
DNC
DNC
unit
unit
unit
unit
NC device
NC device
NC device
NC device
2.4
Connection
2.4
Connection
2.4
2.4 Connection
Connection to
to
DNC
to
DNC
to DNC
DNC unit
unit
unit
unit
DNC unit is a unit for interface switcher, which are DNC (RS-232) interface, PC
keyboard (PS2) interface, Ethernet interface .
Since there are DNC (RS-232) interface, PC keyboard (PS2) interface, and USB
interface on HNC-21, DNC unit is mainly used on HNC-22.
The following figure is the connection between DNC unit and NC device.
Figure 2
11
Connection between DNC and NC unit
The distance between DNC unit and NC device should not be longer than one meter.
The following figure shows the detailed connection between DNC and NC unit.
Figure 2 12 Detailed connection between DNC and NC unit
20