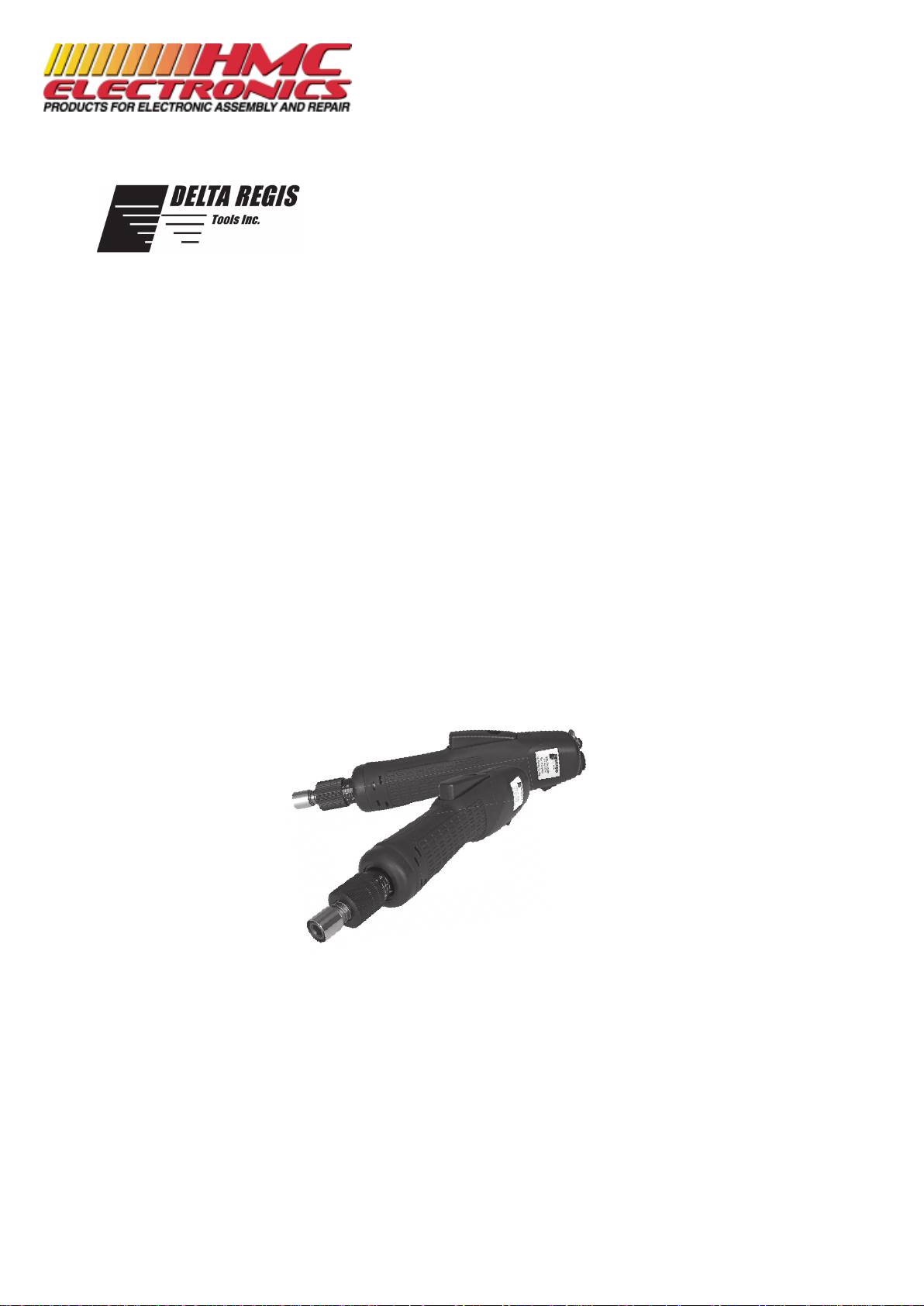
Documentation Provided By HMC Electronics
33 Springdale Ave. Canton, MA 02021
http://www.hmcelectronics.com
(800) 482-4440
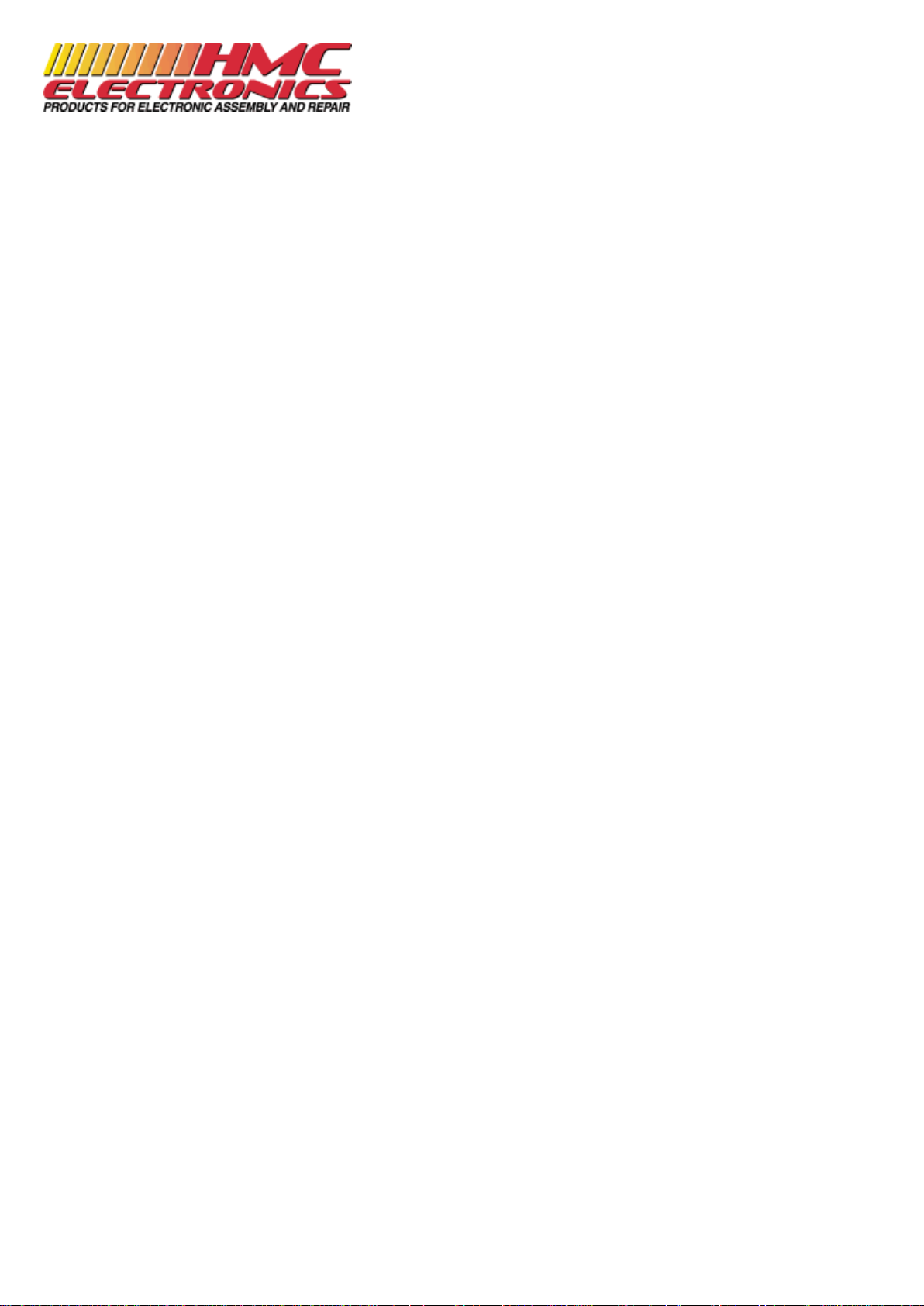
attempt to repair this tool unless you are a qualifi ed technician. When using electric tools, basic safety precautions should
always be followed to reduce the risk of fi re, electric shock and personal injury. Read all instructions before using the tool.
2-1 Grounded tools must be plugged into an outlet properly installed and grounded in accordance with all codes and
ordinances. Never remove the grounding prong or modify the plug in any way. Do not use any adaptor plugs. Check
with a qualifi ed electrician if you are in doubt as to whether the outlet is properly grounded. If the tools should
electrically malfunction or break down, grounding provides a low resistance path to carry electricity away from the
2-2 Avoid body contact with grounded parts such as pipes, metal structures or other electrical products. There is an
2-3 Don’t expose power tools to rain or wet conditions. Water entering a power tool will increase the risk of electrical
2-4 Don’t abuse the cord. Never use the cord to carry the tools or pull the plug from an outlet by the cord. Keep the cord
away from heat, oil, sharp edges, and moving parts. Replace damaged cords immediately. Damaged cords increase
the risk of electric shock.
2-5 When operating a power tool outside, use an outdoor extension marked ‘W-A’ or ‘W’. These cords are rated for outdoor
3-1 Stay alert, watch what you are doing, and use common sense when operating a power tool. Do not use tools when
tired or under the infl uence of drugs, alcohol, or medication. A momentary lack of attention while operating a power
tool may result in serious personal injury.
3-2 Dress properly. Do not wear loose clothing or jewelry. Contain long hair. Keep hair, clothing, and gloves away from
3-3 Avoid accidental starting. Make sure the trigger switch is off before plugging the tool in. Carrying tools with the
trigger held on or plugging in tools with the trigger switch on invites accidents.
3-4 Remove adjusting keys or wrenches before turning on the tool. A wrench or key that is left attached to a rotating part
of the tool may result in personal injury.
3-5 Do not overreach. Keep a proper footing and balance at all times. Proper footing and balance enables better control
of the tool in unexpected situations.
3-6 Use safety equipment. Always wear eye protection. Dust mask, non-slip safety shoes, hardhat, or hearing protection
Documentation Provided By HMC Electronics
33 Springdale Ave. Canton, MA 02021
http://www.hmcelectronics.com
(800) 482-4440

4-1 Use clamps or other practical means to secure and support the workpiece to a stable platform. Holding the work by
4-2 Do not force tool. Use the correct tool for your application. The correct tool will do the job better and safer at the rate
for which it is designed.
4-3 Do not use the tool if the switch does not turn it on or off. Any tool that cannot be controlled with the switch is
dangerous and must be repaired.
4-4 Disconnect the plug from the power source before making any adjustments, changing accessories, or storing the tool.
Such preventative safety measures reduce the risk of starting the tool accidentally.
4-5 Store idle tools out of reach of children and other untrained persons. Tools are dangerous in the hands of untrained
4-6 Maintain tools with care. Check for misalignment or binding of moving parts, breakage of parts, and any other
condition that may affect the tools operation. If damaged, have the tool serviced before using. Many accidents are
caused by poorly maintained tools.
4-7 Use only accessories that are recommended by the manufacturer for your model. Accessories that may be suitable for
one tool may become hazardous when used on another tool.
5-1 Tool service must be performed only by qualifi ed repair personnel. Service or maintenance performed by unqualifi ed
5-2 When servicing a tool, use only identical replacement parts. Use of unauthorized parts or failure to follow
5-3 Check for damaged parts. Before further use, any guard or part that is damaged should be carefully checked to
determine that it will operate properly and perform its intended function. Check for alignment of moving parts,
The use of other than genuine Delta Regis Tools, Inc. replacement parts may result in decreased tool performance and
6-1 When changing a screwdriver bit, make certain that the Forward/Reverse switch is in the ‘OFF’ position and the tool is
6-2 Do not allow chemicals such as acetone, benzene, thinner, trichloroethylene ketone, or other similar chemicals to
come in contact with the screwdriver housing as damage will result.
6-3 Do not drop or abuse the screwdriver.
6-4 Do not adjust the torque setting higher than 8 on the torque scale.
6-5 This tool is intended for a duty cycle of 0.8 seconds ‘ON’ and 3.2 seconds ‘OFF’.
6-6 Do not tighten more than 800 tapping screws per hour (M3 x 5mm).
6-7 This screwdriver is not intended to drive wood screws.
6-8 Do not operate the Forward/Reverse switch while the motor is running.
6-9 Ensure that the controller power switch is off before connecting the screwdriver cable.
6-10 When not in use and when changing accessories, make certain that the tool is unplugged.
6-11 Whenever a tool is not being used, move the Forward/Reverse switch to the ‘OFF’ position and unplug the power
Documentation Provided By HMC Electronics
33 Springdale Ave. Canton, MA 02021
http://www.hmcelectronics.com
(800) 482-4440

1.5 – 10.6 0.17 – 1.2 1.7 – 12
3.0 – 14 0.34 – 1.58 3.5 - 16
6 - 21 0.69 - 2.37 6.9 - 24.2 750 450 600 260
7 - 26.4 0.79 - 2.98 8.1 - 30.4 530 300 600 260
14 - 42 1.6 - 4.7 17.3 - 47.9
• Specifi cations are applicable to push-start versions
• All models are intended for use with one of the following controllers: ECT300; ECT320; ECT345; ECT326*; ECT326V*
* RPM indicated is free speed based on using ECT326/326V Controller
• Connect the cord to the driver and power supply. Take care to align the key and the pins on the connectors.
• Plug the power supply/controller into the appropriate power outlet.
• Turn on the power supply/controller by pressing the power switch. Select the HI or LO speed via the speed selection
• Retract the sleeve on the bit holder.
• Insert the desired ¼” hex power bit.
• It is recommended to grip the tool with the forefi nger on the trigger. This orientation allows the thumb to control
the forward/reverse switch. It also allows more contact between the operator’s palm and the tool – this is especially
• Squeeze the trigger and hold until the clutch reacts and the tool shuts down.
• If using a push-to-start model, apply adequate downwards force to start the tool and hold until the clutch reacts and
• The preset torque will not be reached if the trigger is released before the clutch activates.
• Ensure that enough downwards force is applied to prevent the screwdriver bit from camming out of the fastener.
• Torque is set by turning the torque adjusting nut on the nose of the driver.
• Torque is increased as the nut covers increasingly higher numbers on the scale.
• The numbers on the scale are for reference only and are not an indication of actual torque.
• Drivers should be calibrated on a torque tester suited for measuring the torque of power drivers. There should be a
(ie. soft, medium, or hard joint).
Documentation Provided By HMC Electronics
33 Springdale Ave. Canton, MA 02021
http://www.hmcelectronics.com
(800) 482-4440

• Once the desired torque has been set, you can prevent tampering by securing it with an optional torque locking
• Based on a new tool the torque output may decline after about one months useage. The decline will become minor
and stabilized afterwards. To ensure required torque output, the user should check torque output periodically with a
torque meter and adjust as required.
You have a sophisticated tool for the installation of your hardware. Protect it by suspending it with a balancer and tool
• Initiate a preventative maintenance plan. Contact our technical support staff for assistance.
2. It is recommended that the screwdriver be serviced and carbon brushes be changed every fi ve to six months. Brushes
should be replaced when 1/3 of length (2-3 mm depending on model) has worn. Life of the brushes depends on the
operating frequency and torque output.
3. To avoid motor overheating, do not drive more than 10-15 screws per minute.
4. If the screwdriver is used more than 8 hours per day, service should be performed more frequently.
2. All repairs and maintenance of this tool must be performed by an authorized service center.
3. Delta Regis Tools, Inc. is not responsible for modifi cations made to the tool by others.
4. Repairs should be made only by authorized, trained personnel. Consult your nearest Delta Regis Tools authorized
5. It is the responsibility of the employer to inform all operators of the information in this manual.
TO BE REPAIRED BY QUALIFIED, TRAINED PERSONNEL ONLY.
of the brush aligns with the curve of the commutator.
DO NOT OVER TIGHTEN CAPS!
install torque locking sleeve.
Turn to adjust torque. Higher values on
scale indicate higher torque. Numbers
on the scale are for reference only and
are not a torque indication.
Three position switch with center position
being OFF. The OFF position is recommended
Documentation Provided By HMC Electronics
33 Springdale Ave. Canton, MA 02021
http://www.hmcelectronics.com
(800) 482-4440