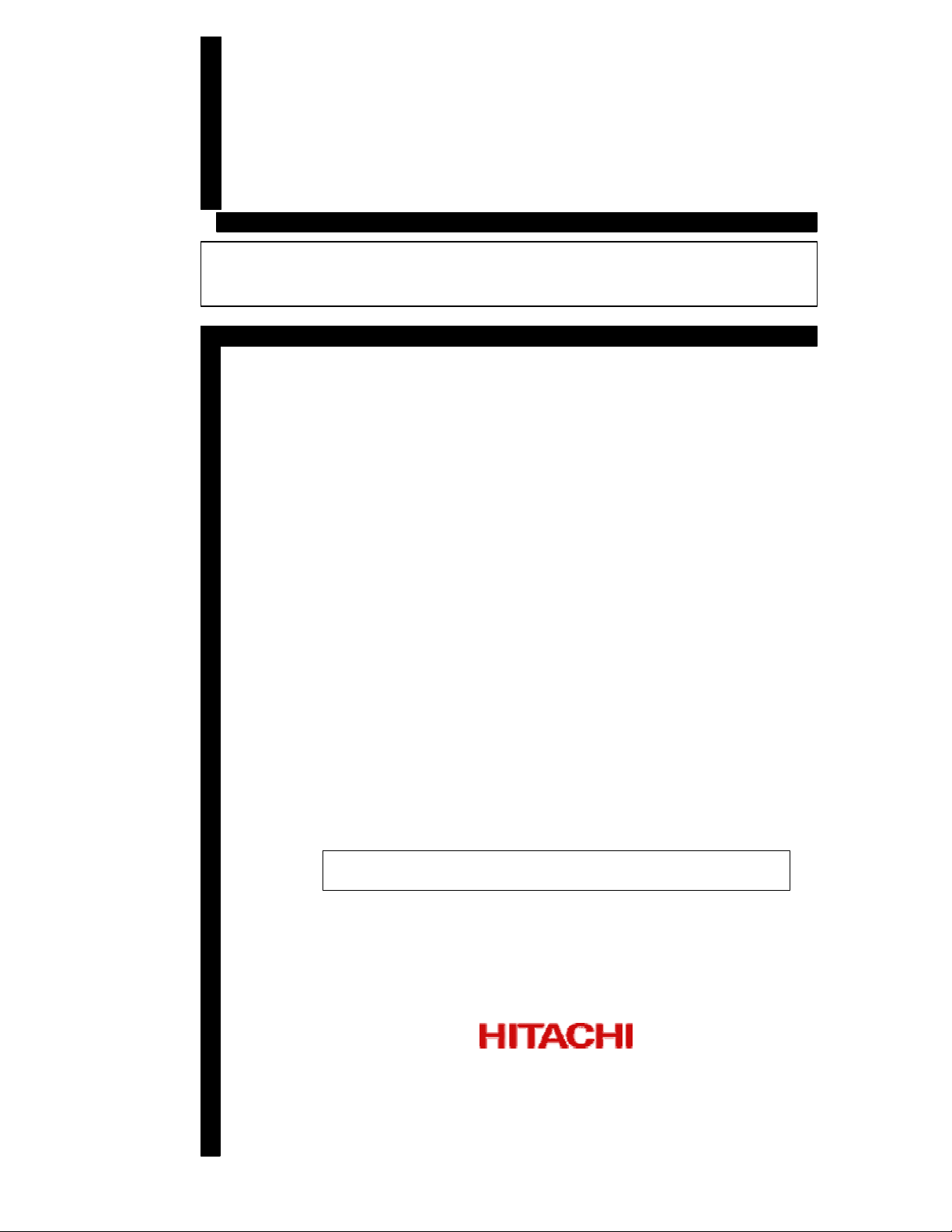
HITACHI INVERTER
PID CONTROL
USERS’ GUIDE
After reading this manual, keep it for future reference
Hitachi America, Ltd.
HAL100PID
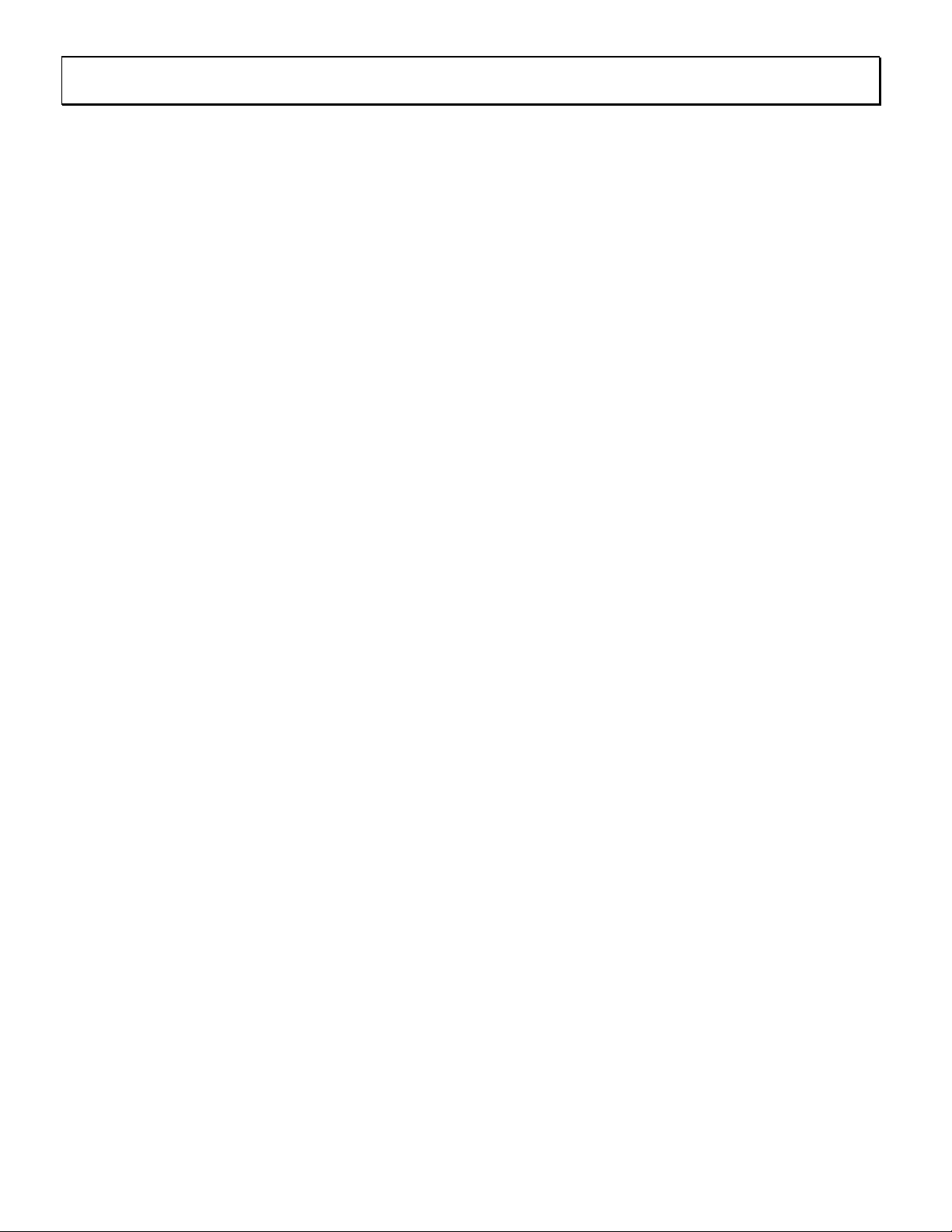
CONTENTS
1. OVERVIEW 3
2. PID CONTROL ON SJ100/L100 INVERTERS 3
2-1 PID Control 3
(1) P : Proportional Control 4
(2) I : Integral Control 5
(3) D : Differential Control 5
(4) PID Control 5
2-2 PID Gain Adjustments & Control Characteristics 6
3. HOW TO USE 7
3-1 Structure & Parameters 7
(1) Control Mode 7
(2) Parameters 7
(3) Deviation Calculation 8
(4) Target Input 8
(5) Feedback Input & Setting PID Performance Area 8
(6) Scale Conversion 9
3-2 Summary of Parameters for PID Control 9
3-3 Examples of Set Up 11
(1) Parameter Set Up under Frequency Control Mode 11
(2) PID Set Up (Target & Feedback) 11
(3) Scale Conversion Factor Setting 12
(4) Target Input by Digital Input Signal 12
(5) PID Mode Selection 12
3-4 Example of Each Gain Adjustment (Kp & Ti) 13
(1) Adjustment of Proportional Gain (Kp) 13
(2) Adjustment of Integration time (Ti) & Readjustment of Kp 13
3-5 General Cautions 13
4. EXAMPLES OF ACTUAL APPLICATION 14
4-1 Constant Flow Control 14
4-2 Constant Temperature Control 15
5. INDEX 16
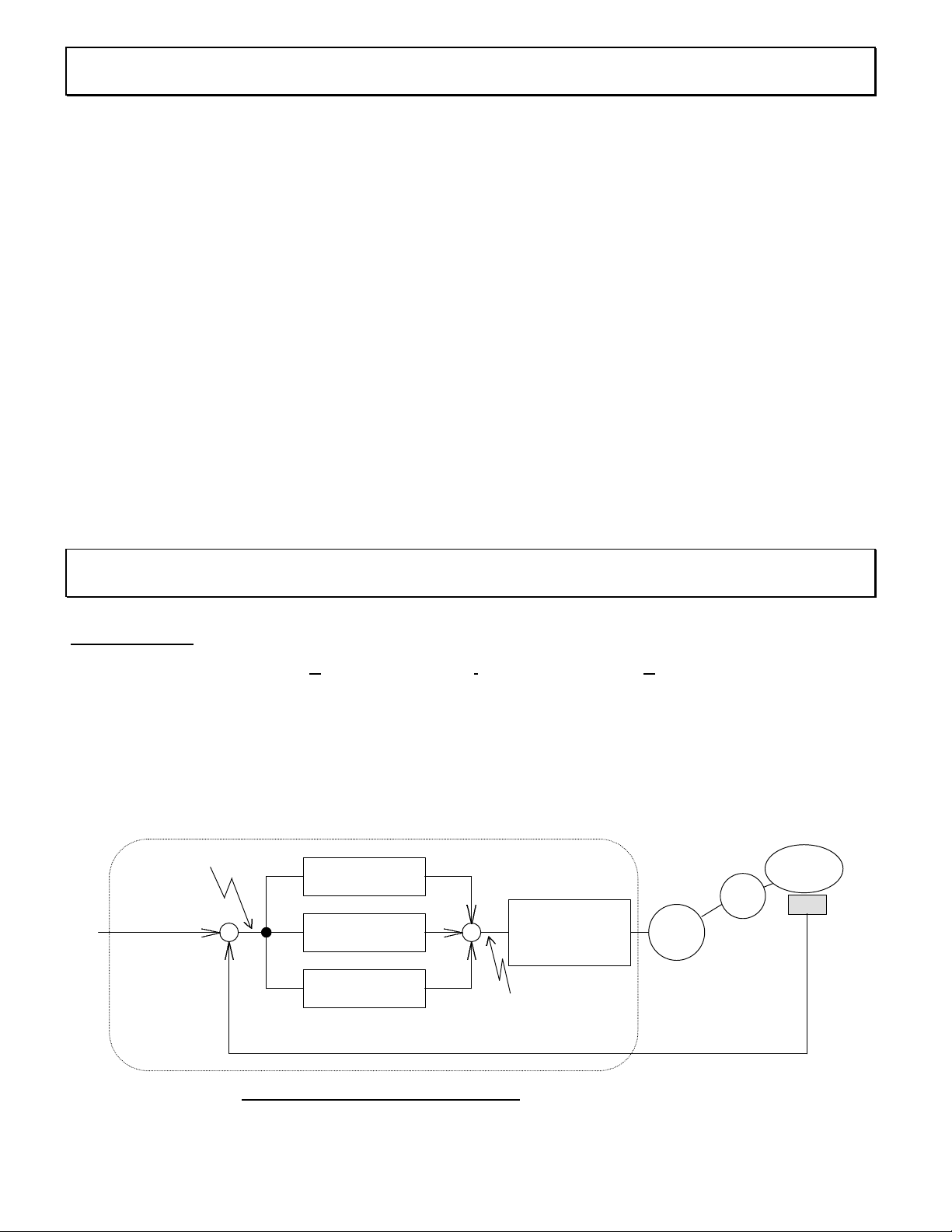
1. OVERVIEW
Fig. 2-1 PID Control block diagram
SJ100/L100 series inverters have an integrated PID control function as standard. They can be used for
controls, such as constant flow control for fan & pump applications, and they have the following features.
l Target signal can be given not only by the digital operator but also by an external digital signal, which can
be set to 16 different targets. Furthermore, it can also be given by an analog input signal (0 - 10V or 4 20mA).
l Feedback signal can be given to SJ100/L100 by analog voltage input (10V max.)or by analog current
input (20mA max.).
l For the feedback signal, the performance area can be defined individually. For example 0 - 5V, 4 - 20mA
or others.
l Using a scale conversion function, you can get actual values of target value and/or feedback value for air
flows, water flows or temperature on the display.
Please read this guide book to use the convenient PID function of the SJ100/L100 series inverters correctly
and without any trouble.
2. PID CONTROL ON SJ100/L100
2-1 PID Control
“P” in PID stands for Proportional, “I” for Integral, and “D” for Differential. The combination of
these controls is called PID control. PID control is widely used in various fields, such as the process
control of air flow, water flow, pressure, temperature and others. It controls the output frequency of the
inverter according to PID calculation, which is based on the deviation between target and feedback. The
inverter adjusts its output frequency to correct the deviation. This control block diagram is shown in Fig. 21 below.
Target
deviation
P : Proportional
operation
I : Integral
operation
D : Differential
operation
Inverter
Frequency
command
Fan, pump, etc.
Load
Motor
Sensor &
Transducer
control
of
Feedback (Flow, Pressure or temperature etc.)
Integrated into SJ100/L100
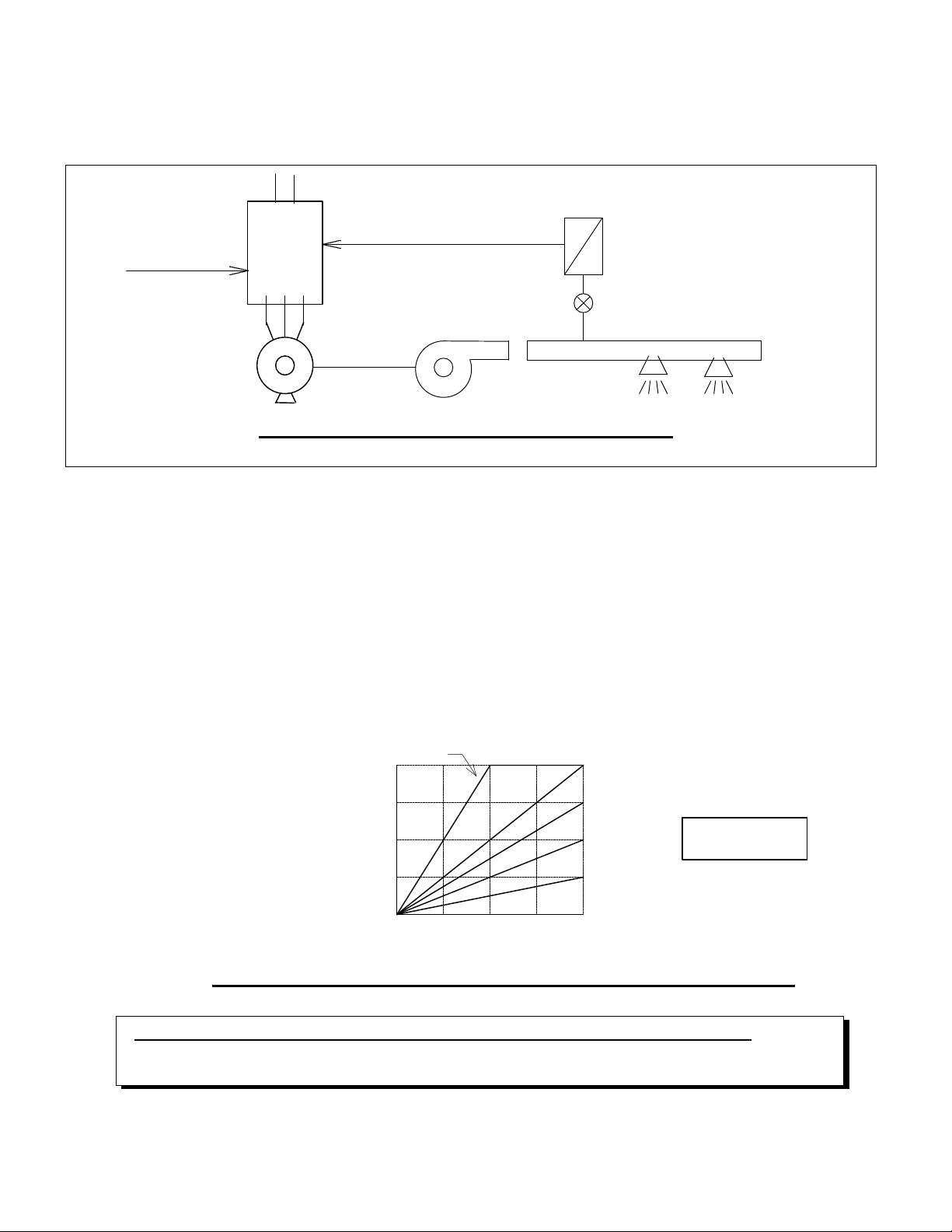
SJ100/L100 series inverters have integrated PID control, which is indicated by the dotted line in Fig. 2-1.
Fig. 2-2 Wiring example for flow control application
4 bit of digital
Max. frequency <---
You can use PID control by setting a target value and providing a feedback signal.
The example in Fig. 2-2 shows a connection diagram for ventilation flow control in a fan application.
SJ100/
Target
input signal
Feedback
(DC0-10V, 4-20mA)
Transducer
Flow volume sensor
Fan
Motor
(1) P : Proportional Control
This controls the output frequency so that output frequency and deviation have a proportional relation.
The coefficient of deviation and output frequency (expressed in %) is called Proportional Gain (Kp). This
parameter can be set under function [A71].
Fig. 2-3 shows the relationship between deviation and output frequency. If you set a high value of Kp,
the response of the system to a rapid change in deviation is fast. However, if Kp is too high, the system
can become unstable.
frequency
Deviation(%)
Fig. 2-3 Relation between deviation and output frequency of SJ100/L100
100% of output frequency of above figure is equivalent to maximum output frequency.
Kp can be chosen between 0.2 and 5.0 in function [A71].
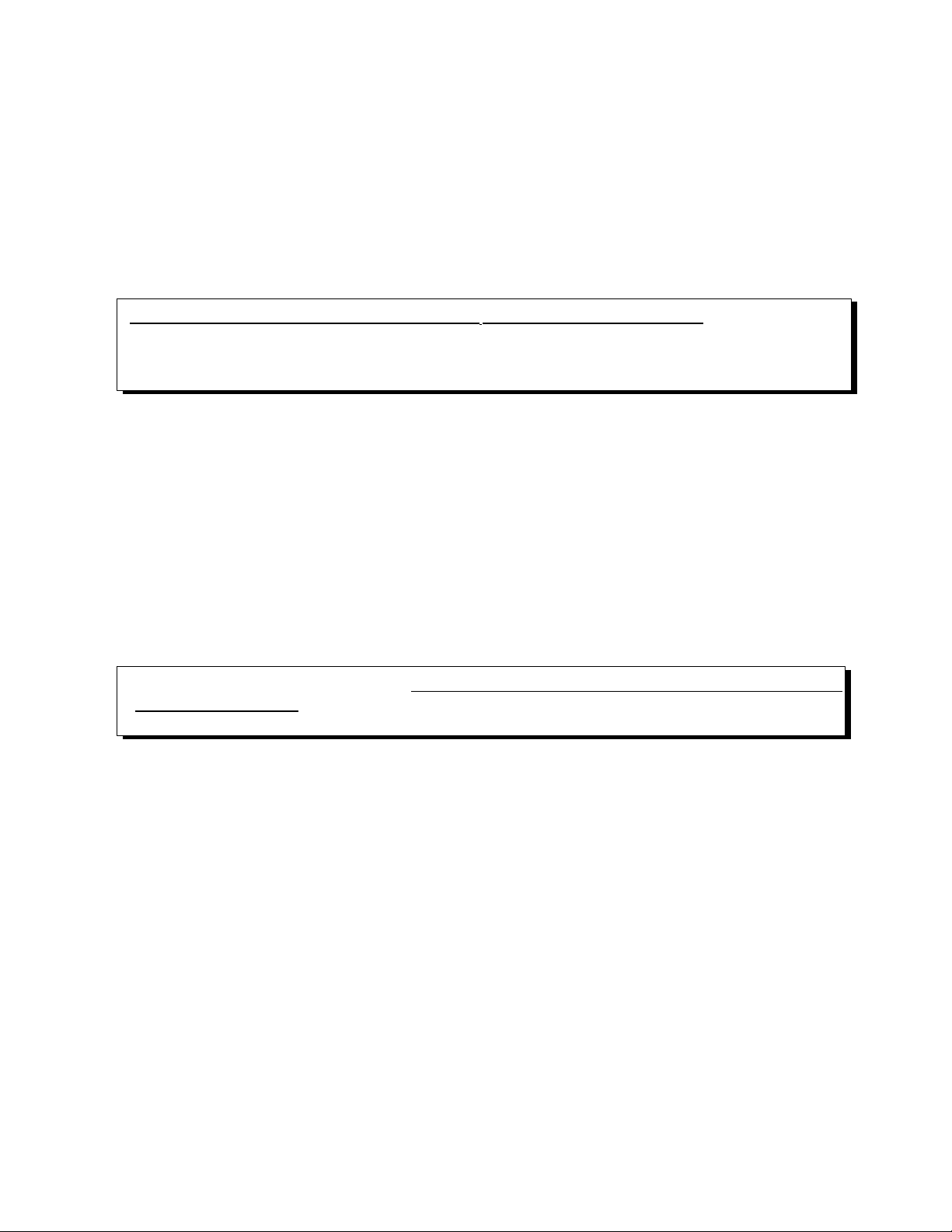
(2) I: Integral Control
This is a control to correct the output frequency by integrating the deviation. In the case of
proportional adjustment, a large deviation will result in a large output frequency adjustment, but if the
deviation is small, then the resulting adjustment of output frequency will also be small. However, you
cannot make the deviation zero. Integral performance compensates this problem.
Integral correction of output frequency is performed by accumulating the deviation over time, so that
eventually, the deviation is brought to zero. Integration Gain (Ki) is a coefficient that determines how
often the deviation is to be integrated. The reciprocal of integration gain is Integration Time Constant
(Ti : Ti=1/Ki).
You must set the integration time constant (Ti) on the SJ100/L100 inverter. You can set the
time between 0.5 second and 150 seconds. When “0.0” seconds is set, NO integral control
will be performed.
(3) D : Differential Control
This is a control to correct the output frequency by differentiating the deviation. Since P control is
based on the current deviation and I control is based on the past deviation, there will always be a delay in
the control system. Differential control compensates for this problem.
Differential correction of the output frequency is performed in proportion to the rate of change of the
deviation. Therefore, D control corrects the output frequency rapidly when there is a rapid change in the
deviation. Differentiation Gain (Kd) is a coefficient to determine how often the deviation is to be
differentiated.
You can set Kd between 0 and 100. Gain is (Fmax / 10) * set value of [A74] versus change in
deviation per second.
(4) PID Control
PID control is a combined Proportional, Integral and Differential control. You can achieve the best
control by adjusting the three factors, P-gain, I-gain and D-gain. Smooth control may be achieved without
any hunting by P-control; you can correct steady-state deviation by I-control; and by D-control, you can
achieve a quick response to sudden disturbances which can influence the feedback value. A large
deviation can be suppressed by P-control. A small deviation can be corrected by I-control.
(Note) Since D-control is performed based on the differentiation of
deviation, it is a very sensitive control. Therefore, it may also
react to extraneous signals and noise, and can easily lead to
unstable system control. D-control is not normally required for the
control of processes such as flow, pressure and temperature.