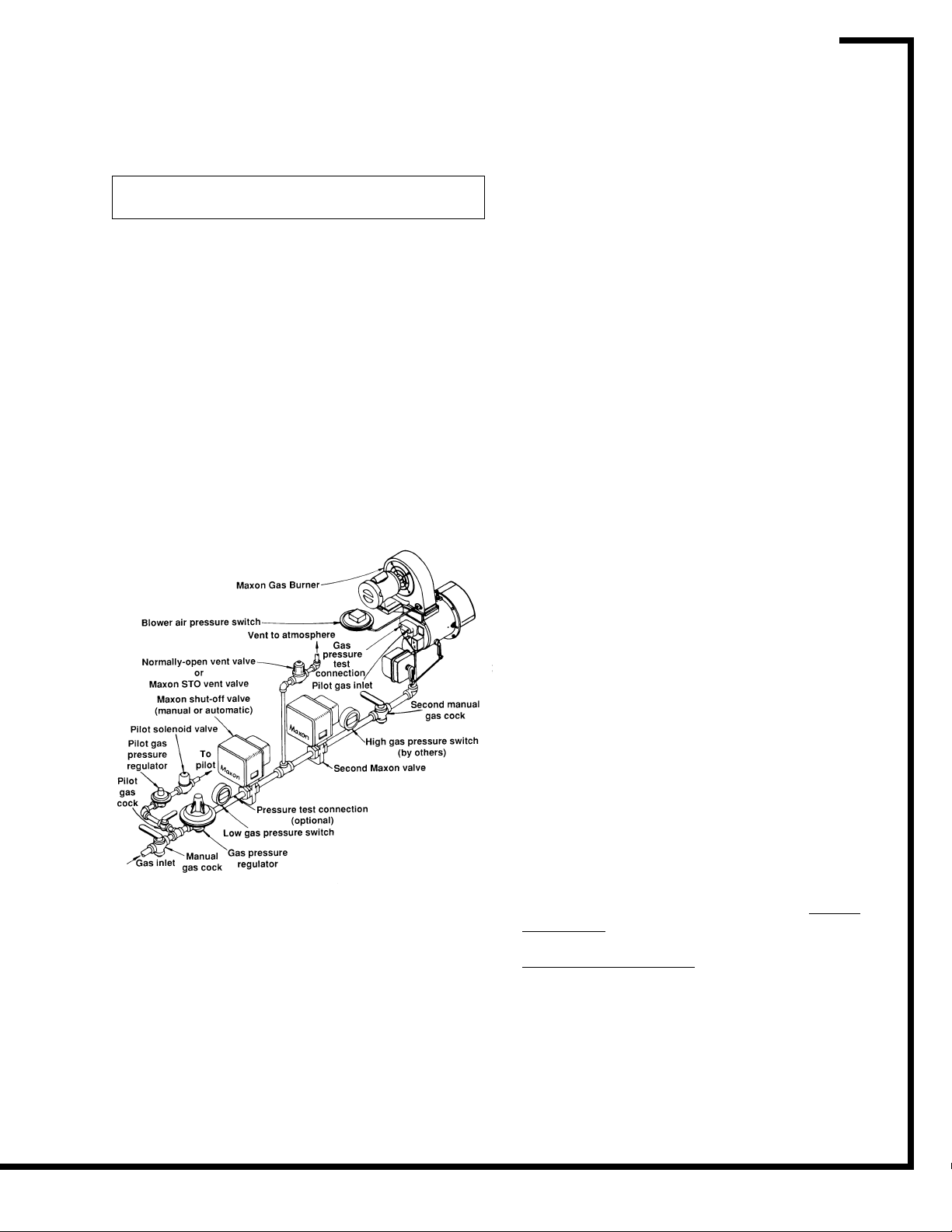
Installation Instructions
Page 2100-S-1“400”, “200” OVENPAK® Burners
General Instructions
Important: Do not discard packing material until
all loose items are accounted for.
To prevent damage in transit, the spark ignitor,
discharge sleeve, mounting gaskets, flame rod and
connecting linkage components may be packed
separately and shipped loose with your new Maxon
OVENPAK® Burner.
The burner itself is normally only a part of your
complete combustion system. Additional pipe train
accessories and control components will be required
for a complete system installation. The sketch below
shows a typical gas train as might be used with
OVENPAK® gas fired burners.
Piping Layout as sometimes required by
insurance and standards groups
Block and Bleed gas train arrangement illustrated
with Model “400” OVENPAK
Model “400” OVENPAK
supply (except for EB versions, which require a
separate combustion air blower). They also serve as
a fuel flow control and fuel/air mixing device. Model
“200” OVENPAK® Burners serve as a mixing device
and usually have an externally-mounted gas control
valve.
Burner should not be exposed to direct radiant
heat or positioned where it might draw in inert gases.
If such conditions exist, consider filters, relocation
and/or use of the EB version and external air supply.
Electrical service must match the voltage, phase
and cycle of all electrical system components and be
®
Burner
®
Burners provide the air
compatible with burner nameplate ratings. Insure that
all normal control safeguards are satisfied. Combustion air blower should continue to run after shutdown
to allow burner to cool.
Gas supply piping must be large enough to
maintain the required fuel pressures cataloged for the
particular burner size used with burner operating at
full rated capacity.
Anything more than minimal distance or piping
turns may necessitate oversizing piping runs to keep
pressure drops within acceptable ranges.
Inlet pipe leading to any burner should be at least
four pipe diameters in length. If multiple burners are
fed from a single gas train, care should be taken to
minimize pressure drop and give maximum uniformity.
Clean fuel lines are essential to prevent blockage
of pipe train components or burner gas ports.
Main Shut-Off Cock should be upstream of both
the main gas regulator and pilot line take-off. Use it to
shut off fuel to both pilot and main burner during shutdown periods of more than a few hours.
The fuel throttling valve contained within a Maxon
burner is not intended for tight shut-off.
Main gas regulator is essential to maintain a
uniform system supply pressure. If one pipe train
supplies multiple burners, provide a separate regulator in the branch leading to each burner system.
Size the regulator for full system capacity at the
required pressure, carefully considering pipe train
losses. Follow the instructions attached to the regulator during installation and be sure to remove any
shipping pin or block.
Pilot take-off should be upstream of the main gas
regulator, but downstream of the main gas cock. It
should normally include its own pilot gas regulator, a
solenoid valve and shut-off cock. A pilot adjustable
orifice at the pilot inlet simplifies adjustment.
Pilot piping must be large enough to provide for
the full flow and pressures shown in the catalog for
your particular burner size.
Fuel Shut-Off Valves (when properly connected to
a control system) shut the fuel supply off when a
hazardous operating condition is sensed. Manual
reset valves require operator attendance each time
the system is started up (or restarted after a trip-out).
Motorized shut-off valves permit automatic startrestart when used with an appropriate control system.
Test connections are essential for burner adjustment. They should be provided immediately downstream of the regulator and are included in the burner
itself. Test connections must be plugged except
when readings are being taken.
4/98
Maxon practices a policy of continuous product improvement. It reserves the right to alter specifications without prior notice.
INDUSTRIAL COMBUSTION EQUIPMENT AND VALVES
m
CORPORATION
MUNCIE, INDIANA, USA

Page 2100-S-2
“400”, “200” OVENPAK® Burners
Installation Instructions
Horizontal mounting is preferred, but burner may
be mounted in any position suitable for automatic
control motor and UV scanner (if used).
OVENPAK
through an oven wall or insulated air duct. Cut opening approximately 1" larger in diameter than discharge
sleeve to allow for thermal expansion of sleeve.
Burner mounting requires four studs and a flat
mounting surface perfectly centered on the discharge
sleeve.
After placing burner in position over studs, add lock
washers and nuts, then draw up hand-tight only.
Check that burner is seated evenly all around the
flange, filling any gaps to prevent air leakage, then
tighten all nuts firmly.
For proper performance of any burner, air inlet and
motor should be surrounded by clean, fresh, cool air.
Burner and pipe manifold support will be required to support weight of the burner and connected
pipe train components. Air control motors, in particular, require additional support. Maxon connecting
base and linkage assemblies are designed to position
the control motors to work with the burner, not to
support their weight.
The Packaged Model “400” OVENPAK
requires external auxiliary support provided by the
user. The support configuration may be similar to the
leg support or knee bracket support illustrated below.
®
Burners will typically be installed
®
Burner
Additional burner support may be required in
conjunction with a stiffener plate when mounting
OVENPAK® Burner (weighing 100-350 pounds)
through typical thin wall of heater/oven panels.
For push-through systems, use Maxon special
back pressure gasket between stiffener plate and
discharge sleeve flange and use (2) ring gaskets
between discharge sleeve flange and burner casting
to prevent back flow of high temperature air. Fill area
D (see sketch below) with no more than 2" of high
temperature packing (too little will overheat mounting;
too much will overheat sleeve).
Typical discharge sleeve mounting
recommendations
“400”
OVENPAK
Burners
®
Suggested supporting arrangements for
Packaged Model “400” OVENPAK
®
Burners:
For pull-through systems, spacers may be
installed on stud bolts and area D left empty to admit
cooling air past the sleeve.
WARNING: Welding of burner flange to stiffener
plate may cause warpage of burner flange and
require additional seal material to prevent
leakage.
Four lock screws permit centering of mixing cone
within burner body and sleeve.
m
CORPORATION
MUNCIE, INDIANA, USA
Maxon practices a policy of continuous product improvement. It reserves the right to alter specifications without prior notice.
INDUSTRIAL COMBUSTION EQUIPMENT AND VALVES
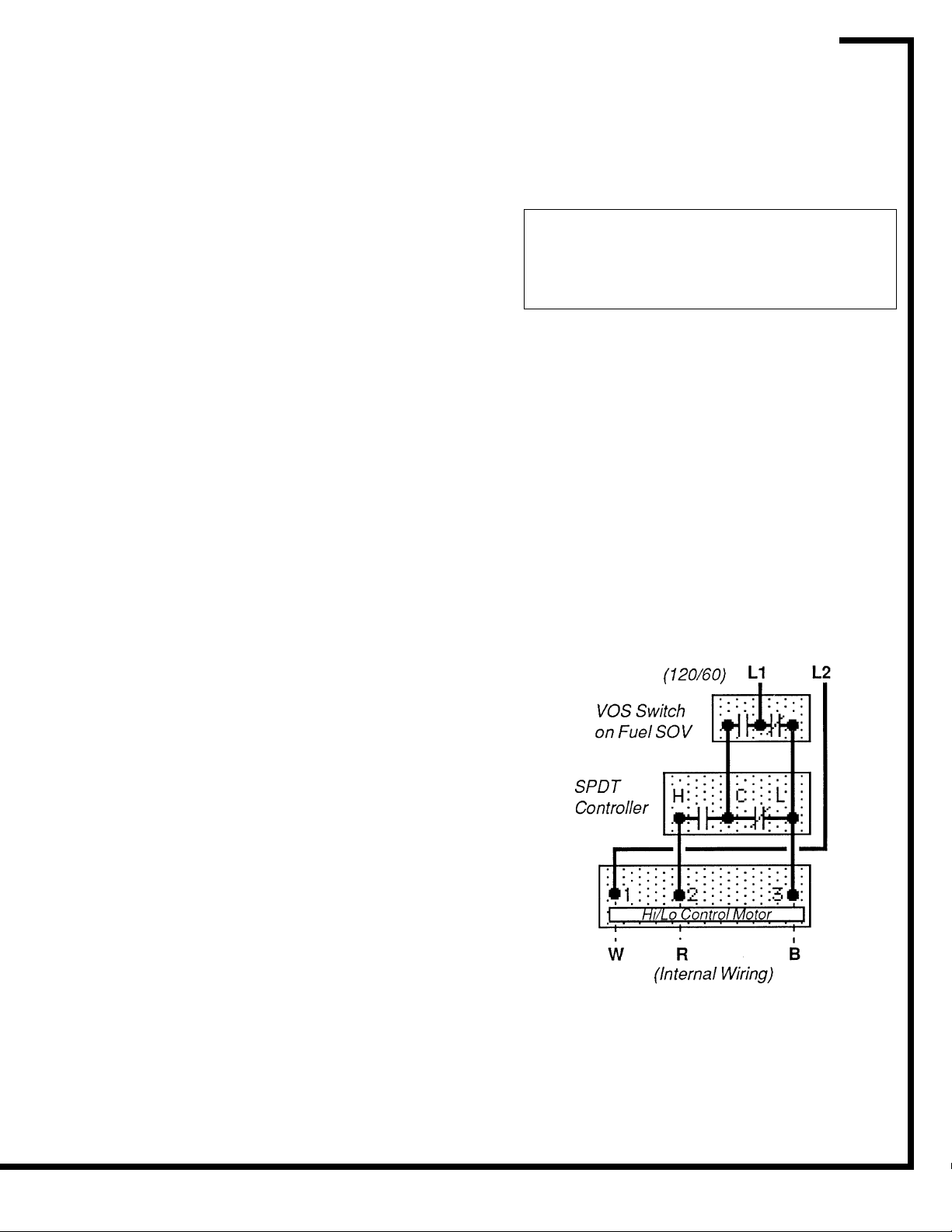
“400”, “200” OVENPAK® Burners
Installation Instructions
Page 2100-S-3
For “400” OVENPAK® Burners: Lock screws
should be drawn up hand-tight, then backed out onehalf turn to allow for cone expansion. They must be
re-checked after start-up, and loosened if necessary
to prevent deformation of cone. See start-up instructions for details. Over-tightening lock screws can
lead to cone distortion and greatly reduce cone
and discharge sleeve life.
Discharge sleeve must be flush with, or extend
beyond, interior wall. Maxon can supply a special 12"
long discharge sleeve, but higher noise levels may
result, particularly when firing on propane.
An external viewing port should be provided for
flame observation, preferably in such a position that
burner pilot and main flame can both be seen.
Flame sensing can be accomplished by either
flame rod or UV scanner. When UV scanner is used,
it should be kept as close to burner as feasible. Heat
block, if used, may affect signal strength with some
brands of scanners.
For “400” OVENPAK® Burners, field conversion
from a flame rod version to a UV scanner version and
vice versa may require additional parts in the burner.
Contact Maxon for requirements.
Alternate fuels may require correction of supply
pressures.
If OVENPAK® Burner is equipped with Maxon Hi/Lo
Control Motor, low-fire start wiring can be accomplished as shown in the sketch below.
Maxon assumes no responsibility for the use or
misuse of the layouts shown. Specific piping
and wiring diagrams should always be submitted to the appropriate agencies for approval on
each application.
Multi-burner installations require special consid-
erations if supplied by a common pipe train and/or air
supply. Air and Gas Balancing Valves should be
used for improved heating uniformity; Gas Swing-
Check Valves should be installed as close as possible to each burner inlet for dependable lightoff (gas
manifold may otherwise act as a reservoir, preventing
lightoff during trial-for-ignition period).
Control system’s circuitry must not allow main
Fuel Shut-Off Valve to be opened unless combustion
air is on, and must de-energize valve upon loss of
combustion air pressure, along with the other usual
system interlocks. Motor starter is to be interlocked
with valve, whether or not a combustion air pressure
switch is used.
4/98
Maxon practices a policy of continuous product improvement. It reserves the right to alter specifications without prior notice.
INDUSTRIAL COMBUSTION EQUIPMENT AND VALVES
m
CORPORATION
MUNCIE, INDIANA, USA