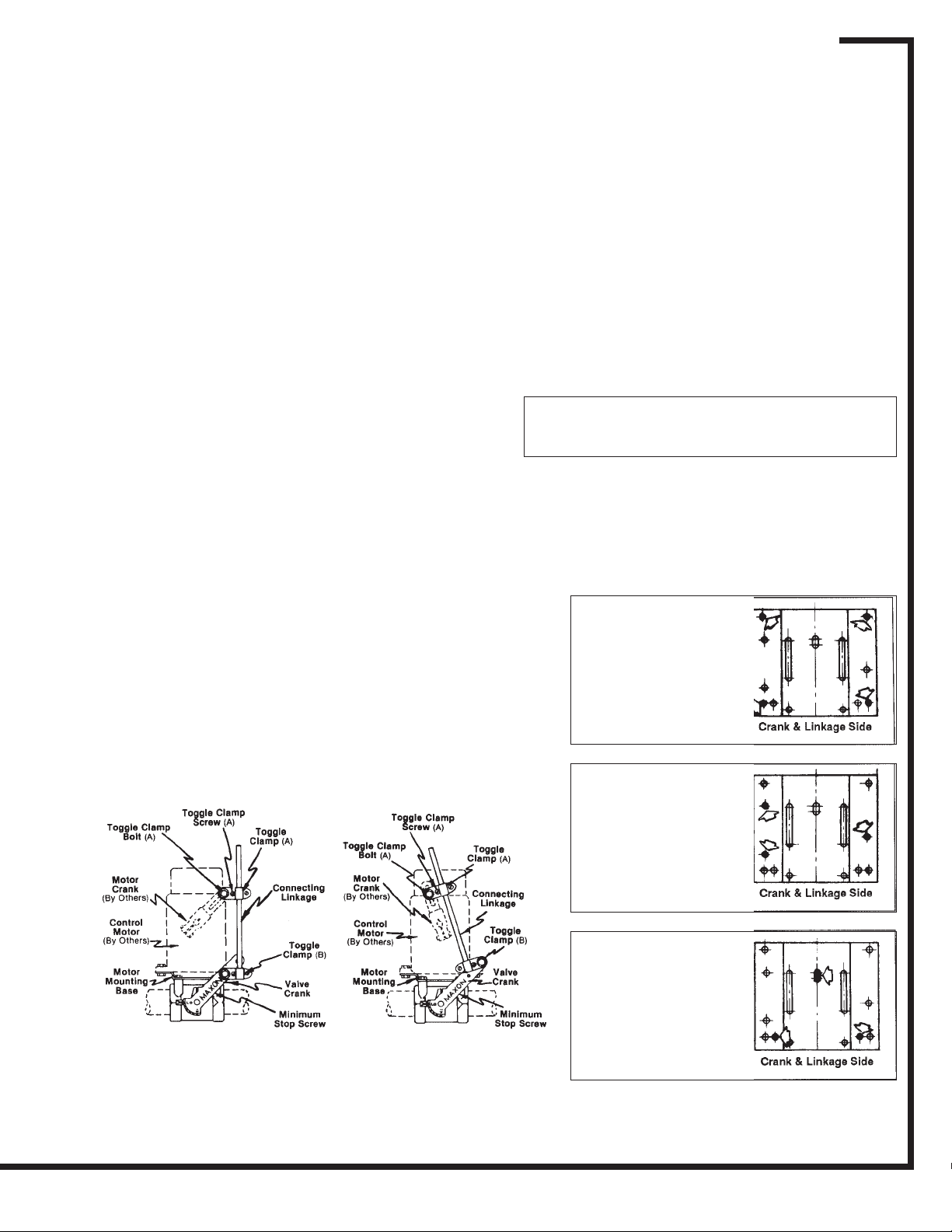
Flow Control Valves Page 7000-S-1
Installation Instructions
– Support weight of piping independently. Do not
place any Maxon Flow Control Valve in a piping
bind. Provide pipe hangers and/or special support
for related manifolds.
– Maxon connecting base and linkage assemblies
are designed to locate and/or position the
control operator for its interaction with the Flow
Control Valve assembly. They are not intended to
support the weight of the control motor. Special
provisions will be required to support the weight of
the control operators.
– Use of pipe heavier than schedule #40 can
cause interference with butterfly-type Flow Control
Valves and restrict the valve from full opening.
– Flow Control Valves provide the means to
adjust fluid and/or gas flows. They should be
installed with at least four pipe diameter lengths of
straight pipe before and after the valve. This
lessens the chance of internal flow turbulence being
set-up in the piping manifolds and control valve.
– Check fluid flow direction through “-P” and “-O”
poppet-type valves. It must flow only in direction
matching the arrow cast into valve body. If necessary, valve body may be rotated per instructions
given on page 7016.
– Install flow control valves carefully and maintain
adequate dimensional clearance to allow full
stroke and travel of the valve’s control linkage.
Internal drive mechanisms within a control motor
may be damaged if linkage is restricted as to cause
binding in high or low flow position.
CAUTION: All Flow Control Valves are designed
for throttling service only and are not intended
for tight shut-off.
– Main system shut-off should always use a
manual “leak-tight” upstream fuel cock.
Mounting Instructions for motor operator on Series “CV” Flow Contr ol Valves
For those Series “CV” Valve assemblies furnished with
connecting base and linkage, the accompanying diagrams
illustrate mounting procedures relative to each specific type
operator.
First, mount your control motor to connecting base in
accordance with diagrams at right.
Secondly, determine if your electric operator travels
through 90° or 180° rotations. Then arrange connecting
linkage and motor crank arm as shown below for your
specific operator.
Honeywell
#M644, M744,
M941 or M944
(7616BR Crank)
Mount with four short bolts
and nuts at indicated holes.
90° Control Motor 160° – 180° Control Motor
Maxon practices a policy of continuous product improvement. It reserves the right to alter specifications without prior notice.
11/90
INDUSTRIAL COMBUSTION EQUIPMENT AND VALVES
Barber-Colman
EA50
Mount with three short bolts
and nuts at indicated holes.
Penn/Johnson
M80, M81
(MD3-600 Crank)
Mount with two short bolts
and nuts and long bolt
screwed into operator base
through slotted hole.
m
CORPORATION
MUNCIE, INDIANA, USA

Flow Control Valves Page 7000-S-1
Installation Instructions
– Support weight of piping independently. Do not
place any Maxon Flow Control Valve in a piping
bind. Provide pipe hangers and/or special support
for related manifolds.
– Maxon connecting base and linkage assemblies
are designed to locate and/or position the
control operator for its interaction with the Flow
Control Valve assembly. They are not intended to
support the weight of the control motor. Special
provisions will be required to support the weight of
the control operators.
– Use of pipe heavier than schedule #40 can
cause interference with butterfly-type Flow Control
Valves and restrict the valve from full opening.
– Flow Control Valves provide the means to
adjust fluid and/or gas flows. They should be
installed with at least four pipe diameter lengths of
straight pipe before and after the valve. This
lessens the chance of internal flow turbulence being
set-up in the piping manifolds and control valve.
– Check fluid flow direction through “-P” and “-O”
poppet-type valves. It must flow only in direction
matching the arrow cast into valve body. If necessary, valve body may be rotated per instructions
given on page 7016.
– Install flow control valves carefully and maintain
adequate dimensional clearance to allow full
stroke and travel of the valve’s control linkage.
Internal drive mechanisms within a control motor
may be damaged if linkage is restricted as to cause
binding in high or low flow position.
CAUTION: All Flow Control Valves are designed
for throttling service only and are not intended
for tight shut-off.
– Main system shut-off should always use a
manual “leak-tight” upstream fuel cock.
Mounting Instructions for motor operator on Series “CV” Flow Contr ol Valves
For those Series “CV” Valve assemblies furnished with
connecting base and linkage, the accompanying diagrams
illustrate mounting procedures relative to each specific type
operator.
First, mount your control motor to connecting base in
accordance with diagrams at right.
Secondly, determine if your electric operator travels
through 90° or 180° rotations. Then arrange connecting
linkage and motor crank arm as shown below for your
specific operator.
Honeywell
#M644, M744,
M941 or M944
(7616BR Crank)
Mount with four short bolts
and nuts at indicated holes.
Crank & Linkage Side
11/90
Barber-Colman
EA50
Mount with three short bolts
and nuts at indicated holes.
Penn/Johnson
M80, M81
(MD3-600 Crank)
Mount with two short bolts
and nuts and long bolt
90° Control Motor 160° – 180° Control Motor
Maxon practices a policy of continuous product improvement. It reserves the right to alter specifications without prior notice.
screwed into operator base
through slotted hole.
INDUSTRIAL COMBUSTION EQUIPMENT AND VALVES
Crank & Linkage Side
Crank & Linkage Side
m
CORPORATION
MUNCIE, INDIANA, USA

Page 7000-S-2 Flow Control Valves
Adjusting Instructions
Notice: Only generalized instructions can be provided
here. Detailed adjusting instructions are provided with
each individual Maxon burner and/or mixer system.
General Instructions
Important: Do not discard packing materials
until all loose items are accounted for.
To prevent damage in transit, some connecting
base and linkage components may be packed
separately and shipped loose with your new Maxon
Flow Control Valve.
The Flow Control Valve is normally only a part of
your complete combustion system. Additional pipe
train accessories and control components may be
required for a complete system installation.
Read complete instructions before proceeding,
and familiarize yourself with all the system’s
equipment components. Verify that your equipment
has been installed in accordance with the original
manufacturer’s current instructions.
CAUTION: Initial adjustment and light-off of
burner systems should be undertaken only by
trained and experienced personnel familiar with
combustion systems, with control/safety
circuitry, and with knowledge of the overall
installation. Instructions provided by the
company and/or individuals responsible for the
manufacture and/or overall installation of
complete system incorporating Maxon burners
take precedence over these provided by Maxon.
If Maxon instructions conflict with any codes or
regulations, contact Maxon Corporation before
attempting start-up.
For initial adjustment and/or burner start-up:
1. Close all burner fuel valves and cocks. Make
preliminary adjustments to fuel gas regulators.
2. Check all electric circuitry. Verify that all
control devices and interlocks are operable and
functioning within their respective settings/
ranges. Be sure all air and fuel manifolds are
tight and that test ports are plugged if not being
used.
3. Check that any air handling dampers are
properly positioned and locked into operating
positions.
4. Disconnect the automatic control motor’s
linkage from your control valve’s operating crank
arm by loosening the control motor’s connecting
rod from the burner’s toggle linkage.
Initial adjustment should only be
accomplished during a “manual” control
mode.
5. Start all system-related fans and blowers.
Check for proper motor rotation and impeller
direction. Verify that all control interlocks are
working. Allow air handling equipment to run for
adequate purge of your manifolds.
CAUTION: Do not by-pass control panel timers
typically controlling sequential operations.
6. With MICRO-RATIO
air and fuel valves, the minimum differential
pressure setting is initially established with
the air valve only.
A. By disconnecting the linkage between the air
butterfly valve and interconnected fuel
valve(s), the minimum and maximum limits of
travel on the air valve may be determined.
For example, a combustion system may
need the air valve to be 15° open for the
“minimum” setting and the “maximum”
requirements are satisfied with the air valve
open to 60°. By marking these points on the
air valve’s indicating strip, you are ready to
reconnect the SYNCHRO Fuel Valve’s
linkage to the air valve.
B. The next step involves adjusting the
connecting linkage between the air valve
and the fuel valve(s) so that each fuel valve
travels its full quadrant range (i.e. from
minimum to maximum), while the air valve
swings from its pre-determined minimum and
maximum positions.
C. With Series “CV” Valves and Series “Q”
adjustable-gradient Flow Control Valves,
the minimum flow position is set by their
minimum stop screw. This adjustable stop is
located on the side of the screw carrier of
Series “Q” Valves and at the base of crank
arm of Series “CV” Valves. Screwing “in” on
the minimum stop screw produces a physical
stop on the quadrant’s travel that prohibits
valve from being completely closed off.
®
Valve combinations of
m
CORPORATION
MUNCIE, INDIANA, USA
Maxon practices a policy of continuous product improvement. It reserves the right to alter specifications without prior notice.
INDUSTRIAL COMBUSTION EQUIPMENT AND VALVES