
Seal Replacement for
Bubble Tight Dampers
HBTR-151 & HBTR-451
Blade seal may deteriorate over time due to aging,
wear or mechanical damage. Site conditions such as
radiation, grit, or chemical agents may degrade the
elastomer used.
Standard seal material is solid silicone rubber, 50
Shore A durometer.
A. Operating torque increase with material
thickness, as does the ability to withstand
differential pressure across the damper
blade.
B. Stiffer material (higher durometer) increases
operating torque and degrades material
compliance to frame.
C. Rubber materials vary greatly in their
coefficient of friction and their “stickiness”.
Materials with the same durometer may
not perform with same torque and sealing
capability.
The amount of seal overlap to the damper frame is
critical. At axle penetration, seal should just contact
frame so it does not fold. Seal blade perimeter at
right angle to axle should overlap frame so as to
increase the angular range of blade travel. That
is, blade may not stop in exactly the same spot
everytime, depending on installed actuator.
Seal may cover the whole blade surface or have
center cut out to conserve material.
Standard caulk is silicone rubber and is used
to insure that air does not bypass around blade
fasteners.
Seal Preparation
If seal is being cut in field, a fine sanding pad running
PARALLEL to the seal edge can smooth rough
places and blend uneven surfaces (see below). It
is important that seal edge have sharp right angle
corners and have no nicks, cuts or roughness.
Procedure
A. Decontaminate, sterilize or clean damper
before replacing seal. This damper is often
specified for uses that could be hazardous
to one’s health.
B. Close damper. Remove nuts around blade
perimeter and along axle.
C. Use hammer and punch on axle bolt ends to
loosen and remove blade cover plate with
seal. Be careful not to scrape or gouge
frame inside perimeter.
D. Pull off seal. Remove any remaining silicone
caulk.
E. Caulk perimeter of blade cover with small
(1/8 in.) bead. Be sure to caulk OUTSIDE of
blade perimeter studs.
F. Install seal onto perimeter studs, making
sure to orient the shorter seal axis and axle
bolt holes along the axle centerline.
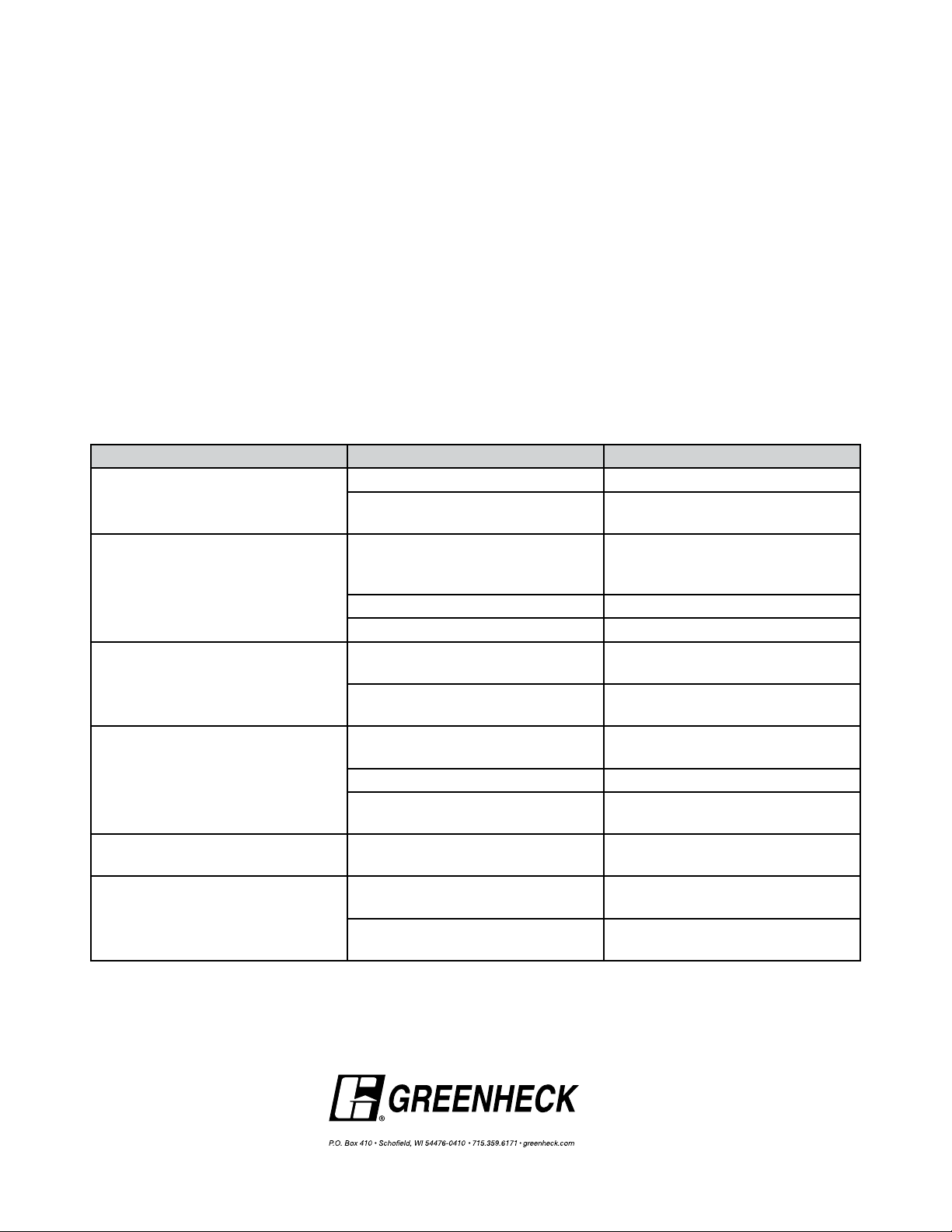
Procedure....
G. Lay damper horizontally with the axle on
down side. Insert blade cover with seal. On
larger dampers, it is sometimes easier to
orient damper vertically, open blade and
insert blade cover and seal. Rock blade
cover to engage axle studs. Install several
fasteners to hold blade cover in place.
H. Position damper so blade studs are
accessible and install nuts. If nuts are
stainless steel, apply anti-sieze compound
to studs to prevent galling fastener threads.
I. DO NOT OVERTIGHTEN NUTS ON
PERIMETER STUDS as seal can and will
be squeezed out excessively. Seal should
extend approximately 0.5 inches at axle
Trouble Shooting Guide
Problem Possible Cause Remedy
Insufficient tightening of perimeter nuts Tighten nuts until seal gap closes
Visual see through near axle
Small leak at seal perimeter
Damper not closing completely
Damper will not open
Leakage around blade fasteners
Blowing through seal perimeter
Perimeter nuts too tight causing
excessive squeeze
Roughness or cut across seal perimeter Sand seal perimeter edge smooth. If
Insufficient tightening of perimeter nuts Tighten nuts until seal gap closes
Dirt on seal or frame Remove dirt
Insufficient actuator torque Replace actuator or increase air
Blade stops not correctly adjusted
(HTBR-451 only)
Insufficient actuator torque Replace actuator or increase air
Higher seal durometer used Replace with correct material
Stuffing boxes too tight Loosen stuffing box clamps to reduce
Seal not caulked outside perimeter
studs
Excessive differential pressure across
blade
Insufficient seal overlap
perimeter and 0.625-0.75 inches at right
angles to axle. Tighten nuts starting at axle,
alternating side-to-side, and working out to
blade tips.
J. Close damper. Blade tip-to-frame web
distance at top & bottom should be the
same, + 0.5 in. Adjust blade stops as
necessary.
K. Open and close damper blade several times
so blade seal seats and aligns. Wipe off
any excess caulk. Inspect for visual gaps.
If possible, pressurize one side of damper
and use Leak Detect Solution to inspect for
leakage. Adjust per Trouble Shooting Guide.
Loosen perimeter nuts so seal relaxes
near axle, this will require disassembly
of damper. See figure on page 1.
pressure supply if pneumatic
Adjust blade stops
pressure supply if pneumatic
friction
Loosen, caulk and retighten seal
Reduce applied pressure
Tighten perimeter nuts to squeeze out
seal
Copyright © 2012 Greenheck Fan Corporation
Bubble Tight Seal Replacement Rev. 1 Feb 2012