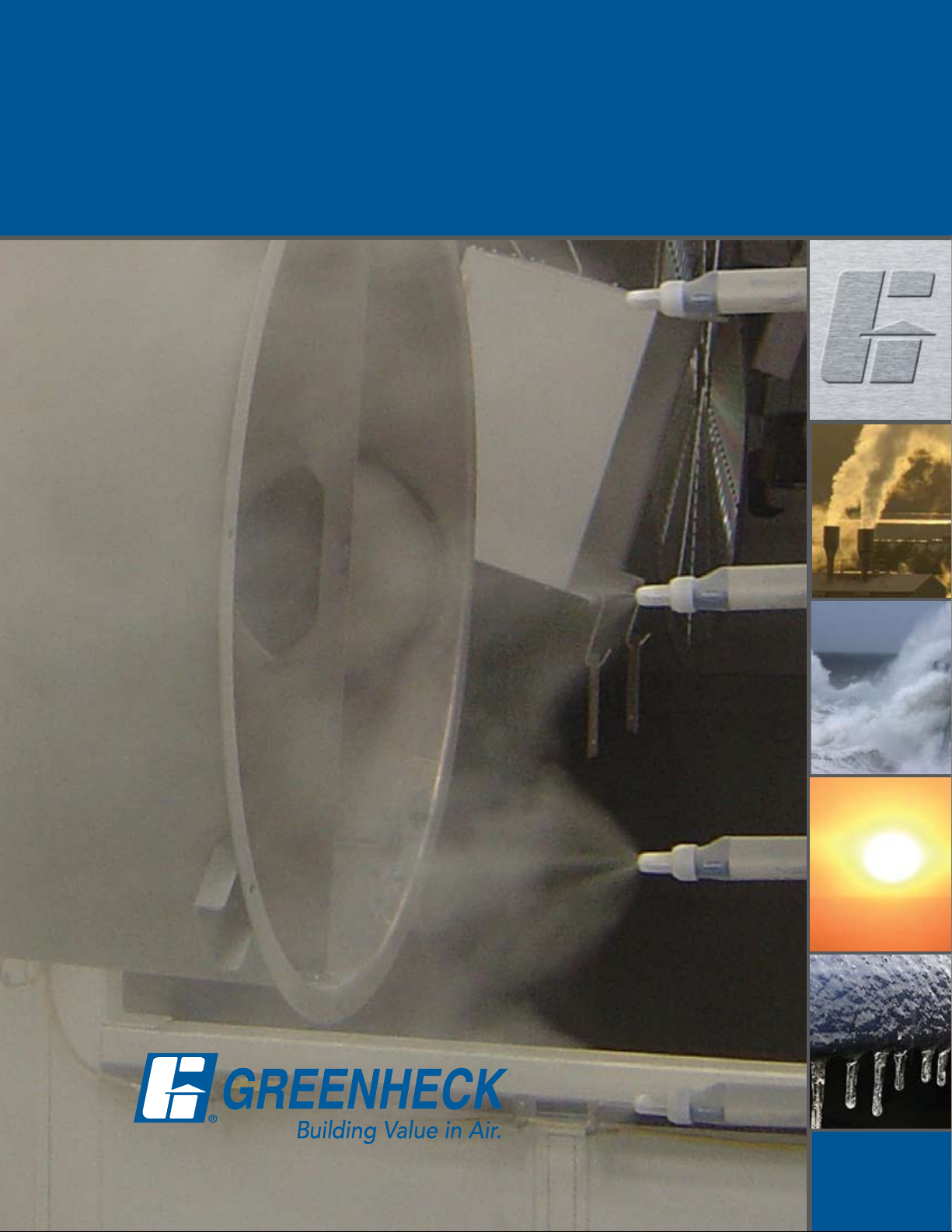
Coatings for Extreme Applications
Perma-Z
Hi-Pro-Z
July
2008
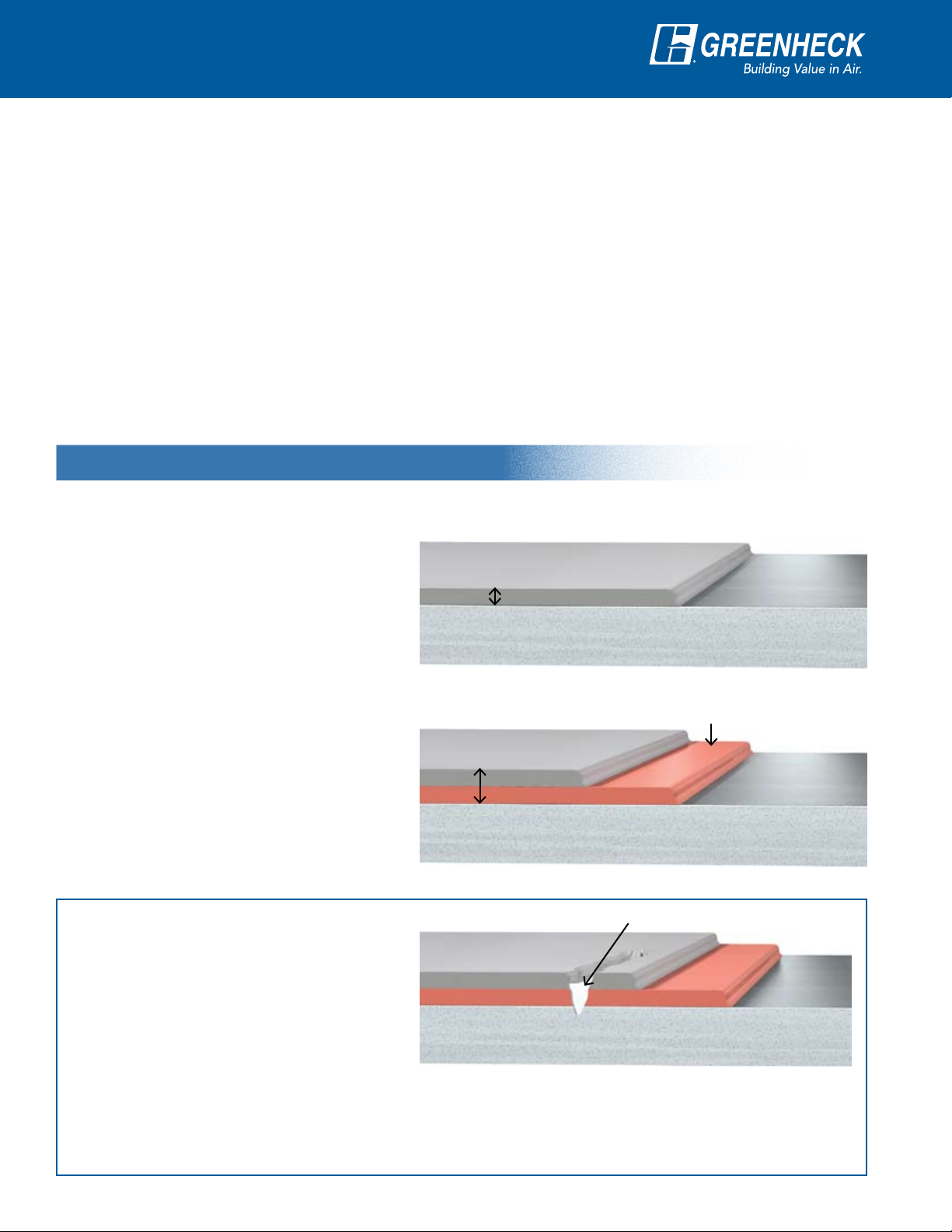
Page Header
The Zinc Advantage
In 1972, Greenheck took the lead as the first
commercial and industrial fan manufacturer to
introduce electrostatic powder coatings. Today,
Greenheck continues to lead by being the first to
offer a superior zinc-rich powder basecoat and
powder coating finish.
This zinc-rich basecoat technology is used
extensively outside the HVAC industry to protect
bridge beams, automotive components and other
heavy-gauge steel products. Now, this advanced
technology is exclusively available on Greenheck
welded steel products.
Greenheck’s coating process starts with a minimum
of five wash stages to treat all components prior
Two Coat System
When compared to a traditional single coat
application, the benefits of the two coat
system include:
An automatic powder coat application •
produces uniform coverage and unmatched
paint quality.
One Coat Process
to painting. Cleaner parts result in better coating
adhesion and durability. We then use an advanced
two coat powder application method that includes
a basecoat of zinc-rich powder and a topcoat of
Greenheck’s Permatector™ or Hi-Pro Polyester. The
combination of these two topcoats over our new zincrich basecoat results in the two new coatings Perma-Z
and Hi-Pro-Z. These oven cured coatings provide
superior corrosion resistance along with a tough,
uniform finish to combat the most extreme conditions.
To help determine what process and coating may
be right for your specific environment, refer to the
performance tested guide provided on page three.
Topcoat
Standard
2-3 mils
Base Steel
Surface Preparation
The double coat thickness provides superior •
durability and protection from air and water.
The zinc-rich basecoat includes an epoxy •
component that provides additional corrosion
protection.
The zinc-rich basecoat provides chemical •
protection of exposed steel to prevent
corrosion.
The Zinc Advantage
The zinc-rich basecoat actively and
passively protects the base steel if the
coating becomes damaged and the
steel is exposed to air and water.
The zinc-rich basecoat has a lower
electrochemical potential than the base
steel. As a result, the steel is actively held in a neutral state when exposed to a corrosive environment—the
driving force of corrosion is halted. A protective layer forms over the damaged surface as a by-product of
the chemical reaction and passively protects the exposed steel from further corrosion due to air and water.
Two Coat Process
Topcoat
4-6 mils Total
Base Steel
Protective Layer
Damaged Surface
If scratched or chipped the zinc donates electrons
to the iron, producing immediate corrosion protection.
Zinc-rich Primer
(70% zinc)
Surface Preparation
Advanced
2