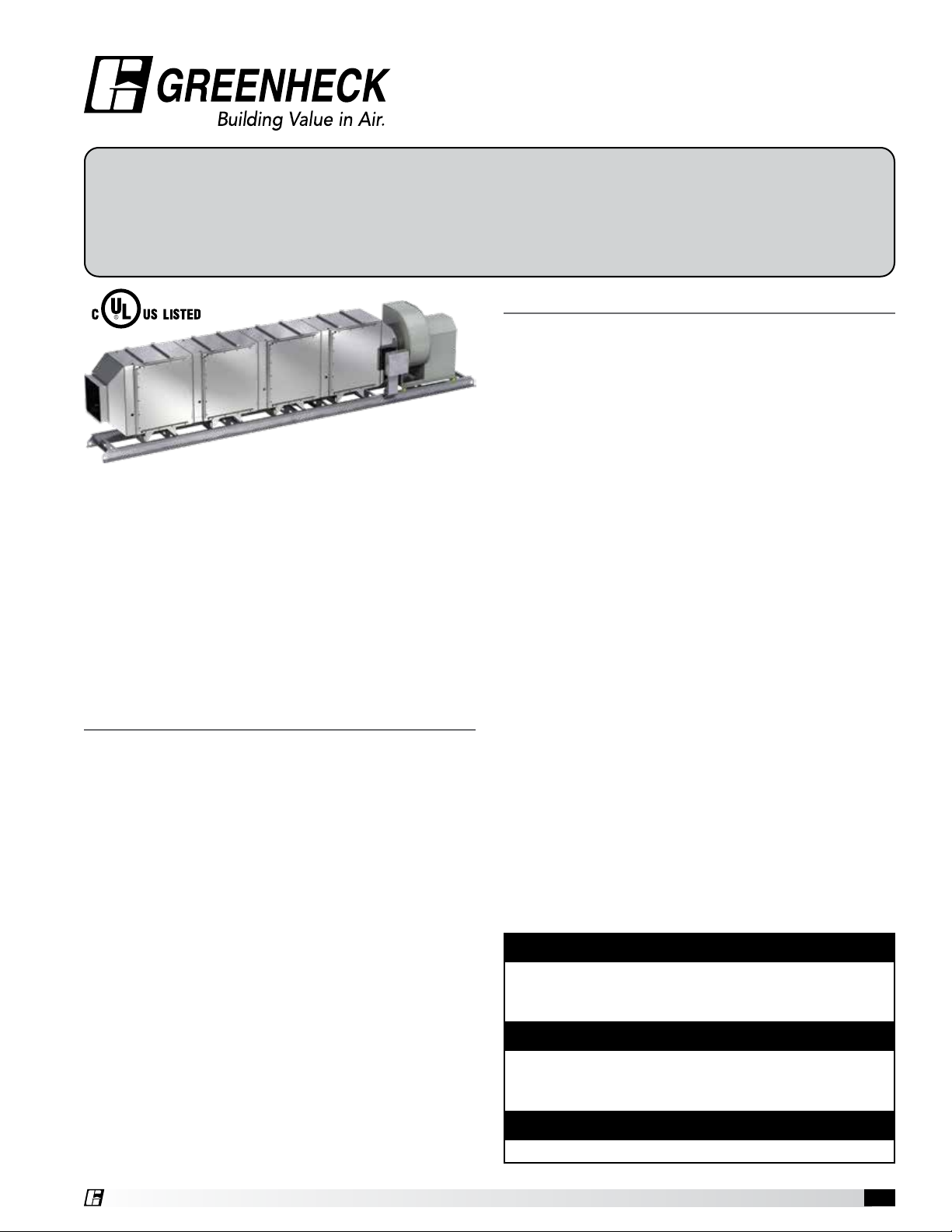
Document 479927
Grease Trapper
®
Kitchen Exhaust Pollution Control Unit
Installation, Operation and Maintenance Manual
Please read and save these instructions for future reference. Read carefully before attempting to assemble, install,
operate or maintain the product described. Protect yourself and others by observing all safety information. Failure
to comply with these instructions will result in voiding of the product warranty and may result in personal injury
and/or property damage.
General Safety Information
Only qualified personnel should install this system.
Personnel should have a clear understanding of these
instructions and should be aware of general safety
precautions. Improper installation can result in electric
shock, possible injury due to coming in contact with
Unit certified to UL 8782
The Grease Trapper Pollution Control Unit is a preengineered mechanical filtration pollution control unit
with integral exhaust fan (available without exhaust fan
as an option). The unit is designed to remove grease
and odor molecules from the kitchen exhaust airstream.
This installation manual covers procedures for receiving,
installing, and maintaining the filtered section of the unit.
For additional instructions and maintenance information
on the integral exhaust fan, when applicable, refer to
the fan nameplate to determine model type and visit
greenheck.com to download the corresponding manual.
Table of Contents
Receiving, Unpacking, Handling, Storage ........ 2
Grease Trapper System Function ............... 3
System Components ......................... 3
PCU Field Assembly
Unit Modules ............................. 4
Attaching Fan ............................ 5
Installation
Rigging and Placing Equipment .............. 6
Ductwork, Electrical & Plumbing Connections ..6-7
Remote Filter Status Indicator Panel .......... 7
Filter Installation .......................... 7
Fire System .............................. 7
Operation
Start-Up ................................ 8
Remote Filter Status Indicator ............... 8
Filter Replacement ........................ 8
Carbon Tray Replacement .................. 8
Maintenance
Regular Scheduled Maintenance ............. 9
Replacement Filter - Parts Ordering ........... 9
Unit Layout - Elevation Views ................. 10
Wiring Diagrams ........................... 11
Our Commitment ........................... 12
moving parts, as well as other potential hazards. Other
considerations may be required if high winds or seismic
activity are present. If more information is needed,
contact a licensed professional engineer before moving
forward.
• Follow all local electrical and safety codes, as well as
the National Electrical Code (NEC), and the National
Fire Protection Agency (NFPA), where applicable.
Follow the Canadian Electric Code (CEC) in Canada.
• The rotation of the fan wheel is critical. It must be free
to rotate without striking or rubbing any stationary
objects.
• Fan motor must be securely and adequately
grounded.
• Do not spin fan wheel faster than maximum cataloged
fan rpm. Adjustments to fan speed significantly effects
motor load. If the fan RPM is changed, the motor
current should be checked to make sure it is not
exceeding the motor nameplate amps.
• Do not allow the power cable to kink or come in
contact with oil, grease, hot surfaces or chemicals.
Replace cord immediately if damaged.
• Verify that the power source is compatible with the
equipment.
• Never open access doors to a duct while the fan is
running.
DANGER
Always disconnect power before working on or near a
fan. Lock and tag the disconnect switch or breaker to
prevent accidental power up.
CAUTION
When servicing the fan, motor may be hot enough
to cause pain or injury. Allow motor to cool before
servicing.
CAUTION
Precaution should be taken in explosive atmospheres.
Grease Trapper Kitchen Exhaust Pollution Control Unit 1
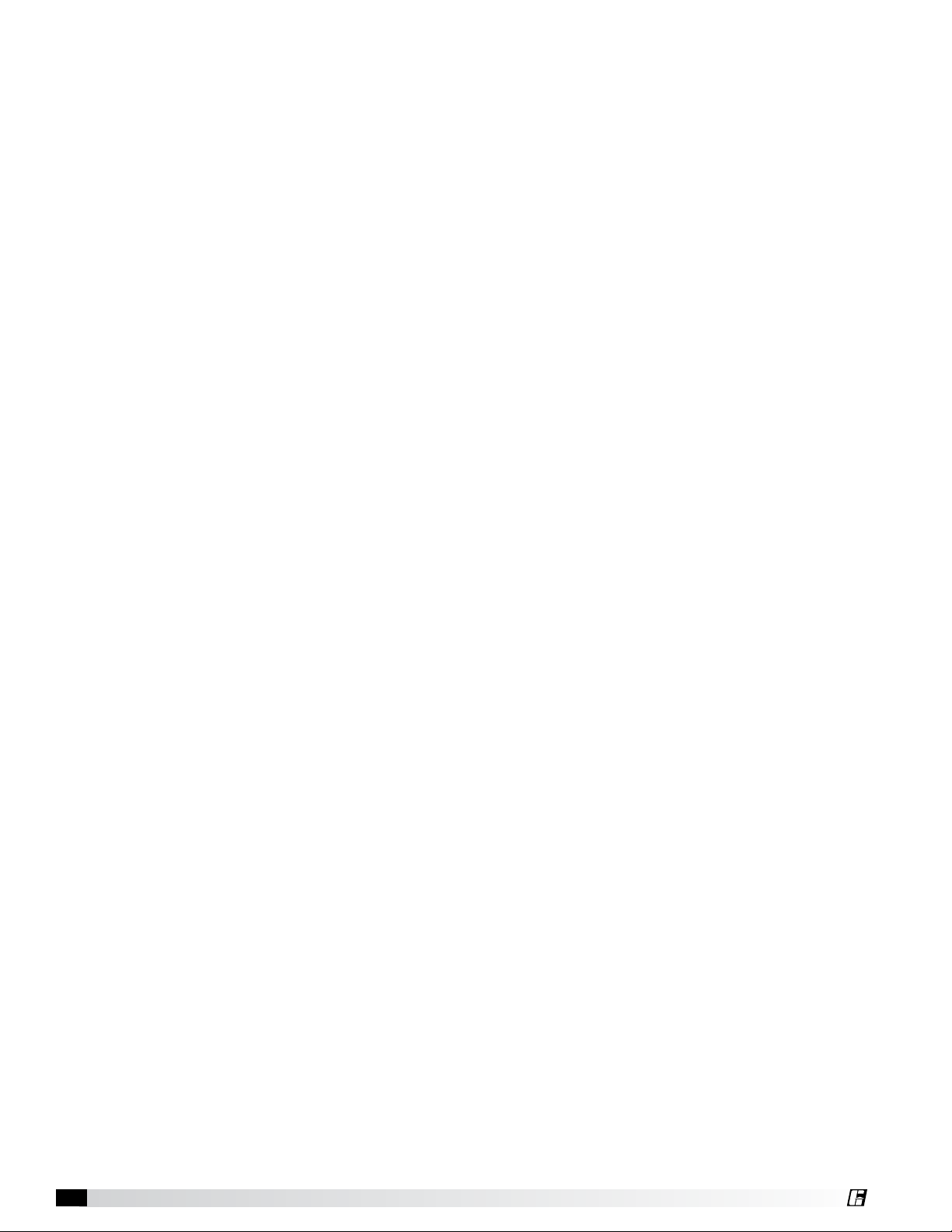
Receiving
Upon receiving the product, check to make sure all
items are accounted for by referencing items shown
on the packing list. Inspect each crate for shipping
damage before accepting delivery. Notify the carrier if
any damage is noticed. The carrier will make a notation
on the delivery receipt acknowledging any damage
to the product. All damage should be noted on all the
copies of the bill of lading which is countersigned by
the delivering carrier. A Carrier Inspection Report should
be filled out by the carrier upon arrival and filed with
the Traffic Department. If damaged upon arrival, file
claim with carrier. Any physical damage to the unit after
acceptance is not the responsibility of manufacturer.
Unpacking
Verify that all required parts and the correct quantity
of each item have been received. If any items are
missing, report shortages to your local representative to
arrange for obtaining missing parts. Sometimes it is not
possible that all items for the unit be shipped together
due to availability of transportation and truck space.
Confirmation of shipment(s) must be limited to only
items on the bill of lading. Remove all other shipping/
packing materials including fan tie down straps.
Handling
Units are to be rigged and moved by the lifting brackets
provided or by the skid when a forklift is used. Location
of brackets varies by model and size. Handle in such
a manner as to keep from scratching or chipping the
coating. Damaged finish may reduce ability of unit to
resist corrosion.
Storage
Units are protected against damage during shipment. If
the unit cannot be installed and operated immediately,
precautions need to be taken to prevent deterioration of
the unit during storage. The user assumes responsibility
of the unit and accessories while in storage. The
manufacturer will not be responsible for damage during
storage. These suggestions are provided solely as a
convenience to the user.
INDOOR - The ideal environment for the storage of
units and accessories is indoors, above grade, in a
low humidity atmosphere which is sealed to prevent
the entry of blowing dust, rain, or snow. Temperatures
should be evenly maintained between 30°F (-1°C) and
110°F (43°C) (wide temperature swings may cause
condensation and “sweating” of metal parts). All
accessories must be stored indoors in a clean,
dry atmosphere.
Remove any accumulations of dirt, water, ice, or snow
and wipe dry before moving to indoor storage. To avoid
“sweating” of metal parts allow cold parts to reach room
temperature. To dry parts and packages, use a portable
electric heater to get rid of any moisture buildup. Leave
coverings loose to permit air circulation and to allow for
periodic inspection.
OUTDOOR - Units designed for outdoor applications
may be stored outdoors, if absolutely necessary. Roads
or aisles for portable cranes and hauling equipment are
needed.
The unit should be placed on a level surface to prevent
water from leaking into it. The unit should be elevated
on an adequate number of wooden blocks so that it is
above water and snow levels and has enough blocking
to prevent it from settling into soft ground. Locate parts
far enough apart to permit air circulation, sunlight,
and space for periodic inspection. To minimize water
accumulation, place all unit parts on blocking supports
so that rain water will run off.
Do not cover parts with plastic film or tarps as these
cause condensation of moisture from the air passing
through heating and cooling cycles.
Inspection and Maintenance
during Storage
While in storage, inspect fans once per month. Keep a
record of inspection and maintenance performed.
If moisture or dirt accumulations are found on parts,
the source should be located and eliminated. At each
inspection, rotate the fan wheel by hand ten to fifteen
revolutions to distribute lubricant on motor. Every three
months, the fan motor should be energized. Fans with
special coatings may require special techniques for
touch-up or repair.
Machined parts coated with rust preventive should be
restored to good condition promptly if signs of rust
occur. Immediately remove the original rust preventive
coating with petroleum solvent and clean with lint-free
cloths. Polish any remaining rust from surface with
crocus cloth or fine emery paper and oil. Do not destroy
the continuity of the surfaces. Wipe thoroughly clean
with Tectyl® 506 (Ashland Inc.) or the equivalent. For
hard to reach internal surfaces or for occasional use,
consider using Tectyl® 511M Rust Preventive or WD-40
or the equivalent.
Removing from Storage
As units are removed from storage to be installed
in their final location, they should be protected and
maintained in a similar fashion, until the equipment goes
into operation. Prior to installing the unit and system
components, inspect the unit assembly to make sure it
is in working order.
1. Check all fasteners, set screws on the fan, wheel,
bearings, drive, motor base, and accessories for
tightness.
2. Rotate the fan wheel(s), where applicable, by hand
and assure no parts are rubbing.
®
Grease Trapper Kitchen Exhaust Pollution Control Unit2
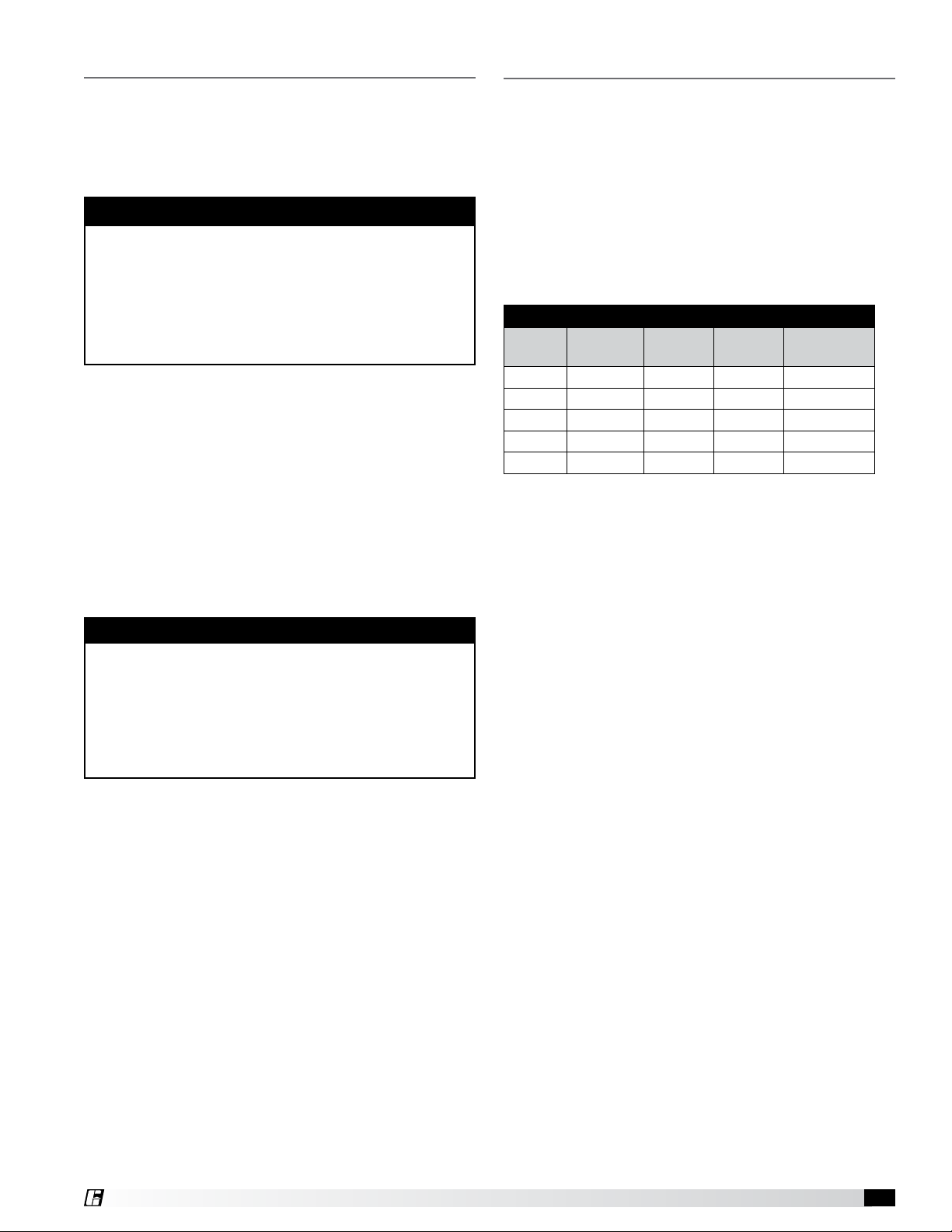
Grease Trapper System Function
System Components
Grease Trapper is a 3-stage mechanical air filtration unit,
with an additional carbon filter module. It is designed for
two specific functions:
1. Remove grease particulate from kitchen exhaust.
2. Remove odor molecules from kitchen exhaust.
NOTE
• Grease Trapper must be connected to a listed
exhaust hood assembly and must be installed in
accordance with local building codes, NFPA 96
and NEC.
• The unit must be installed with a minimum 12 inch
clearance to combustible materials on top of unit,
and six inches on the sides and bottom.
Filter stages 1, 2 and 3 are mechanical air filters of
progressive filtration efficiency that retain the grease
particles.
Each filter stage is monitored by an individual pressure
switch that signals when a particular filter stage needs
replacing. The pressure switches are located inside
the Pressure Switch Enclosure located by the fan.
When a filter stage requires replacement, a signal from
the pressure switch enclosure lights an indicator light
located on the Remote Filter Status Indicator Panel.
The remote status indicator must be field mounted in an
area convenient for monitoring by the cook staff.
Unit Body
The unit body is shipped on a common mounting
rail ready for installation. If the unit was ordered with
an exhaust fan, the fan will also be mounted on the
unit. If unit must be disassembled in the field, refer to
instructions on page 4.
Filters
Filter quantity for each filter stage is based on unit size.
A consistent quantity of filters is provided for each stage
of filtration.
Filter Quantity
Housing
30 3 3 3 6
45 4 4 4 10
60 6 6 6 14
90 8 8 8 20
120 12 12 12 28
Module 1
Metal Mesh
Module 2
MERV 8
Module 3
MERV 15
Module 4
Carbon Filters
Remote Filter Status Indicator Panel (see page 7)
At time of delivery, a remote status indicator panel is
shipped loose. This item must be mounted remotely in
the cooking area prior to unit start-up.
NOTE
Grease Trapper is designed to remove submicron,
airborne particulate generated from cooking
processes. This system is NOT INTENDED to
eliminate regular hood and ductwork cleaning and
service. Improper care and maintenance of this
system and associated hoods and ductwork may
present a fire hazard.
Grease Trapper Kitchen Exhaust Pollution Control Unit 3
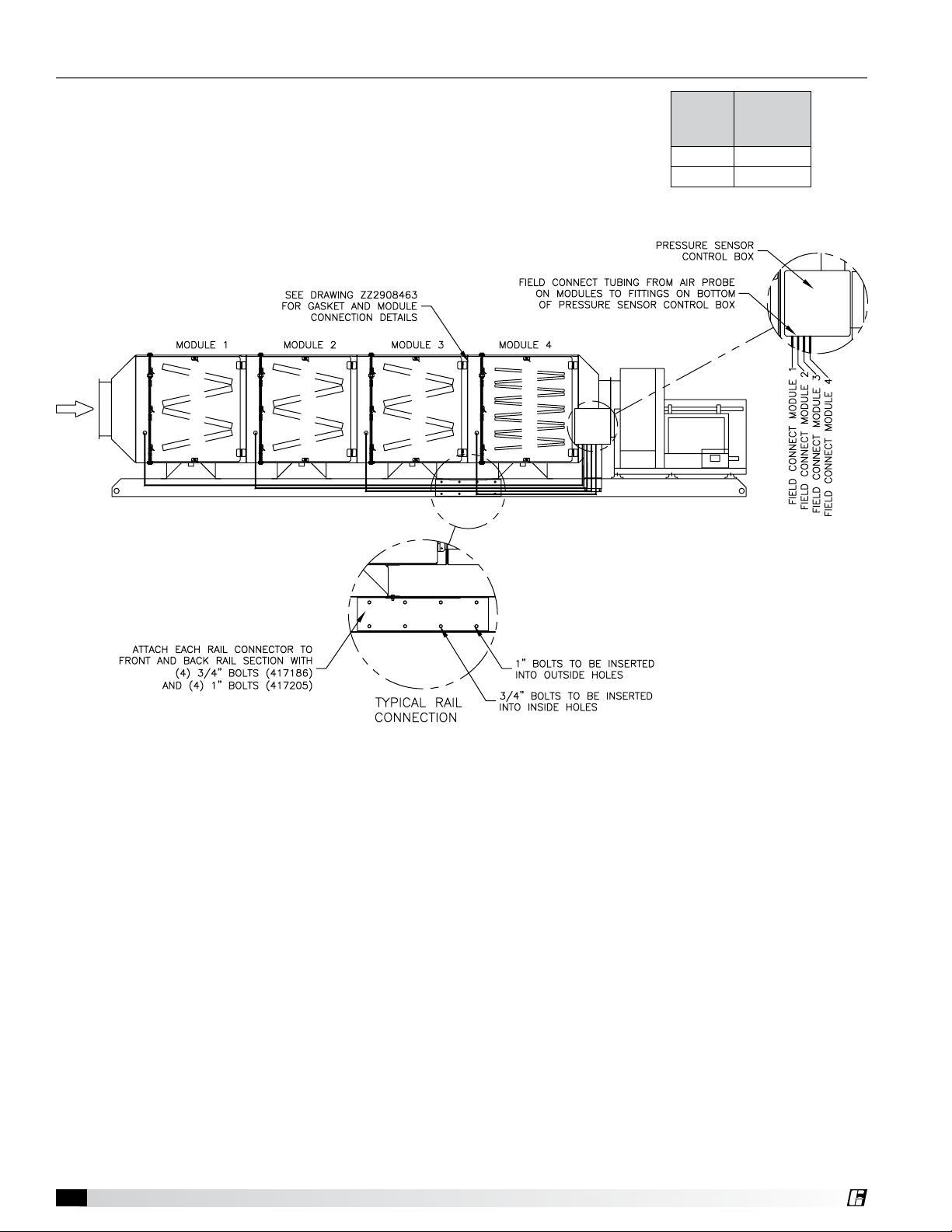
PCU Field Assembly - if applicable
If unit is shipped in sections, each section will need to be assembled in the field.
Unit Modules
1. Remove (4) 5/16 inch mechanical fasteners that attach each module to
the rails.
2. Remove 5/16 inch mechanical fasteners that attach each module to the next
adjacent module. PCU housing size can be found in the model number on tag on
side of unit.
AIRFLOW
AIR
PRESSURE
SWITCH
CONTROL
BOX
Housing
Size
Number of
Mechanical
Fasteners
30, 45 4
60, 90 6
Grease Trapper Kitchen Exhaust Pollution Control Unit4